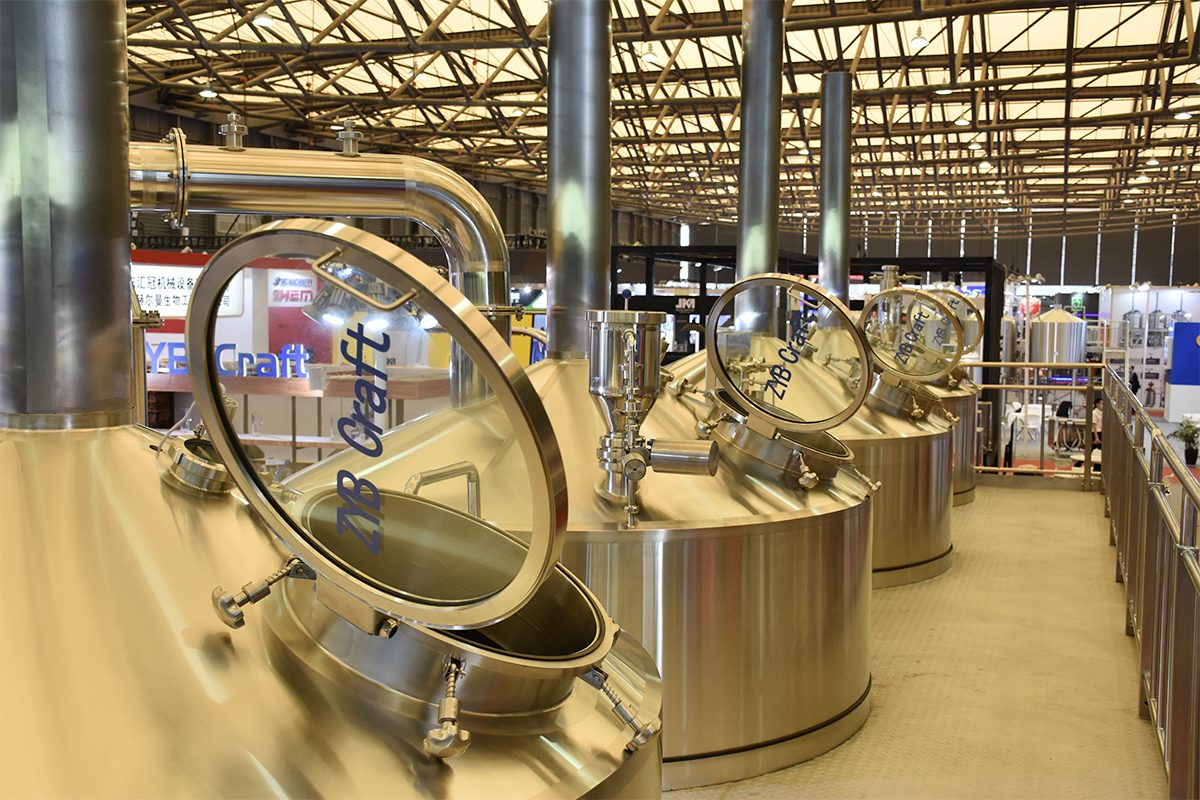
Automatic VS Manual Brewing Systems: Comprehensive Analysis
In the ever-evolving landscape of commercial brewing, the choice between automatic and manual brewing systems is critical for breweries aiming to balance efficiency, consistency, and craftsmanship. As the demand for craft beer continues to grow, breweries are faced with the challenge of scaling production while maintaining the quality that their customers expect. Automatic brewing systems offer streamlined processes and reproducibility, while manual systems emphasize traditional methods and artisanal craftsmanship. This article delves into the intricacies of both systems, comparing their advantages, disadvantages, and impact on the brewing process, to help commercial brewers make informed decisions that align with their business goals.
Complete Guide
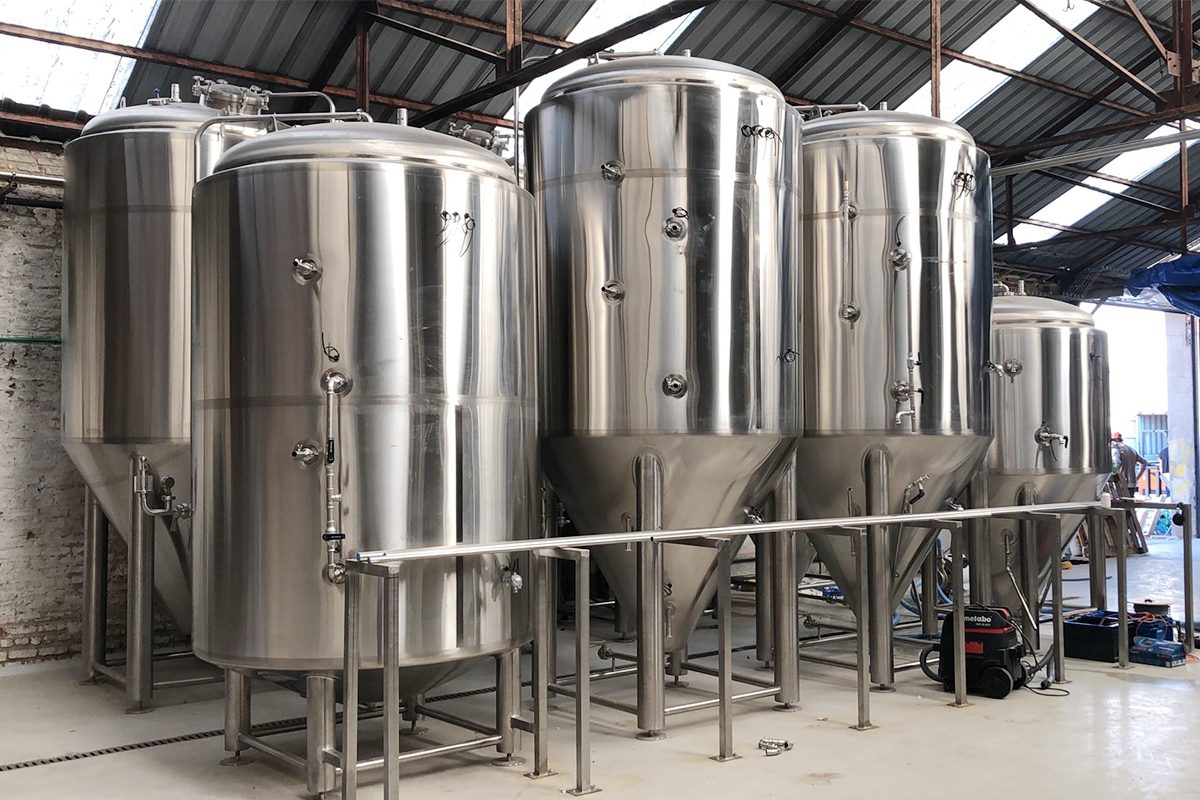
Introduction of Brewing Systems
Brewing systems are the backbone of both craft and commercial beer production, encompassing the equipment and processes that transform raw ingredients into the beloved beverage enjoyed by many. At its core, a brewing system is a collection of tools and machinery that facilitate the various stages of brewing, including mashing, boiling, fermentation, and conditioning. These systems can range from simple setups for homebrewers to sophisticated, fully automated machines used in large-scale commercial breweries.
The importance of brewing systems cannot be overstated, as they play a critical role in determining the quality, consistency, and efficiency of the brewing process. In craft brewing, where the emphasis is often on unique flavors and artisanal techniques, the choice of brewing system can significantly impact the final product. Manual systems allow brewers to exercise creativity and precision, enabling them to experiment with different ingredients and methods to create distinctive beers that reflect their style.
In the commercial brewing arena, where production volumes are higher and consistency is paramount, the choice between automatic and manual systems can affect not only the quality of the beer but also the operational efficiency and profitability of the brewery. Automatic brewing systems are designed to streamline processes, minimize labor costs, and enhance reproducibility, ensuring that each batch meets the desired specifications. Conversely, manual systems may require more hands-on involvement, but they often result in a more engaging experience for brewers and can lead to unique flavor profiles that set a brand apart in a competitive market.
Understanding the nuances of brewing systems is essential for any brewer, whether operating on a small craft scale or managing a large commercial operation. As the craft beer movement continues to grow, the choice of brewing system will remain a vital consideration in producing exceptional beers that satisfy consumer demand and reflect the brewer’s artistry.
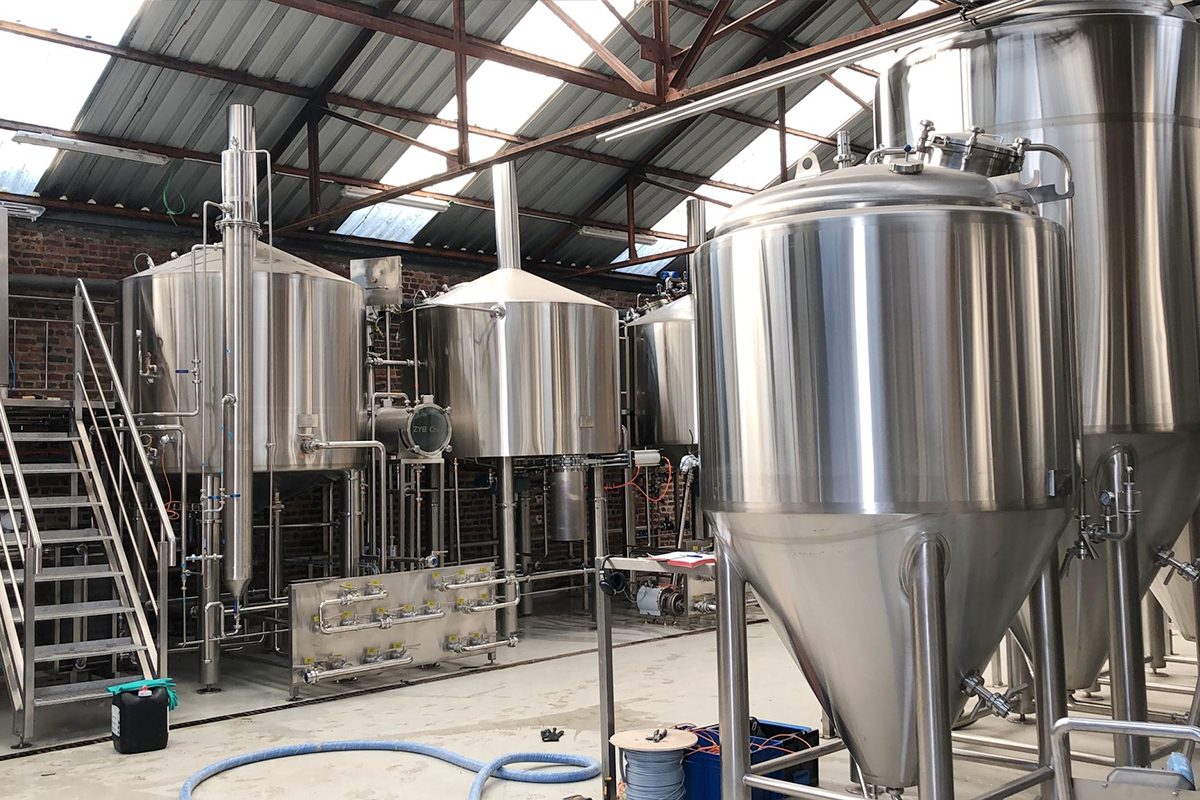
Overview of Brewing Systems
The history of brewing systems dates back thousands of years, with evidence of beer production found in ancient Mesopotamia, where Sumerians created rudimentary brewing methods using simple ingredients like barley and water. Early brewing practices were manual and labor-intensive, relying on basic equipment such as clay pots and open fires. These traditional methods were passed down through generations, forming the foundation of brewing as both a domestic and communal activity.
As societies evolved, so did the brewing process. The Middle Ages saw the establishment of monasteries that refined brewing techniques, leading to more structured methods and the introduction of hops for flavor preservation. By the 18th century, the Industrial Revolution brought significant advancements, including the use of steam power and improved brewing equipment, allowing for larger production capacities and the birth of commercial breweries.
The transition from manual to automated brewing systems began in the late 20th century, driven by technological innovations and the demand for efficiency in an increasingly competitive market. Early automated systems primarily focused on streamlining specific stages of the brewing process, such as temperature control during mashing and fermentation. These advancements allowed brewers to achieve greater consistency in their products while reducing labor costs.
Modern automatic brewing systems incorporate sophisticated technology, including computer controls, sensors, and software that enable real-time monitoring and adjustments throughout the brewing process. This evolution has not only improved efficiency and quality but also allowed breweries to scale their operations without compromising on flavor or craftsmanship. As the brewing landscape continues to change, both manual and automated systems coexist, each offering unique advantages that cater to the diverse needs of craft and commercial brewers alike.
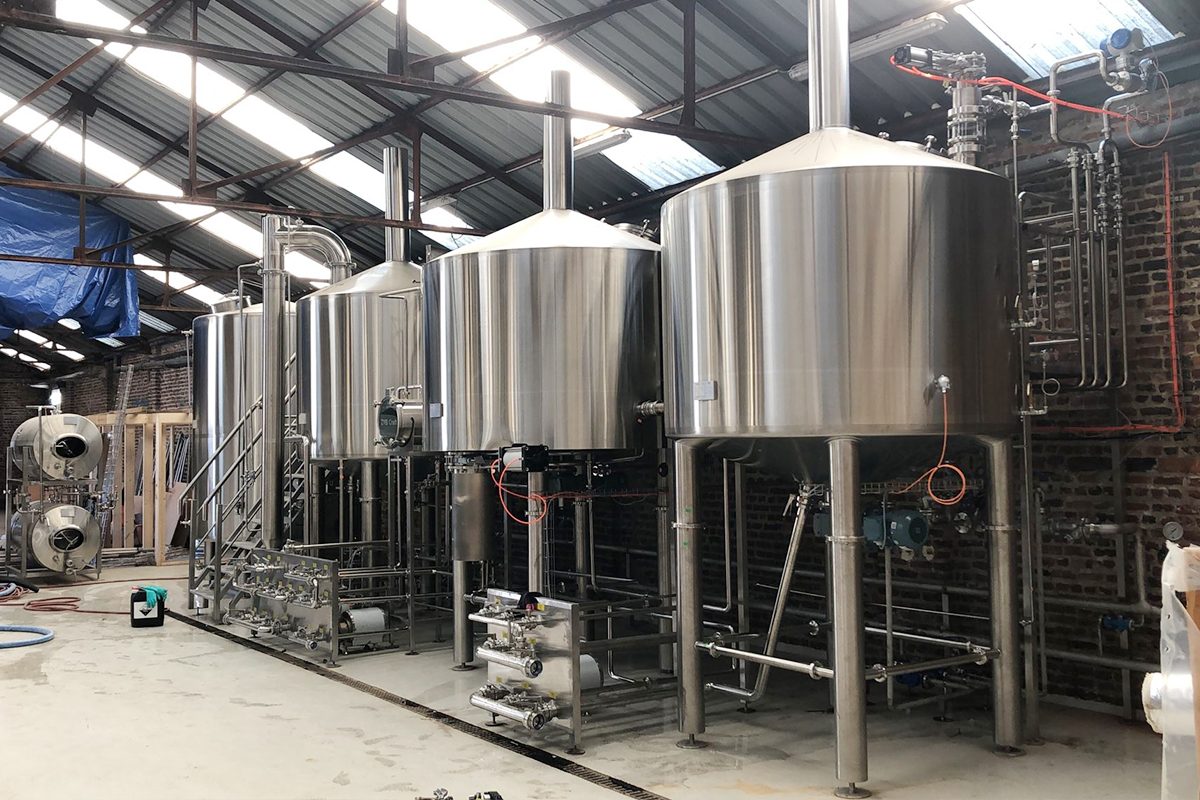
Manual Brewing Systems
Manual brewing systems refer to traditional brewing setups that require significant hands-on involvement from the brewer. These systems typically consist of essential equipment such as mash tuns, kettles, fermentation vessels, and cooling systems. Unlike automated systems, manual brewing relies on the brewer’s skills, knowledge, and techniques to control the brewing process. This approach often emphasizes craftsmanship and artisanal practices, allowing for greater experimentation with ingredients and methods.
Manual brewing systems can vary in complexity, ranging from simple homebrewing setups to more sophisticated arrangements used by craft breweries. They are characterized by their flexibility, enabling brewers to make real-time adjustments based on sensory evaluations throughout the brewing process.
Brewing Process
The brewing process in manual systems generally involves several key stages:
- Mashing: Grains are steeped in hot water, converting starches into fermentable sugars. The temperature and duration of mashing can be adjusted based on the desired beer style.
- Boiling: The wort (the liquid extracted from the mash) is brought to a boil. Hops are added during this stage for bitterness, flavor, and aroma. The boiling time and hop varieties can significantly influence the beer’s characteristics.
- Cooling: After boiling, the wort must be cooled rapidly to yeast-pitching temperatures to avoid contamination. This is typically done using a wort chiller.
- Fermentation: The cooled wort is transferred to fermentation vessels, where yeast is added. The fermentation process can take several days to weeks, depending on the beer style. Brewers monitor the fermentation closely, making adjustments as needed.
- Conditioning and Packaging: After fermentation, the beer is conditioned to develop flavors. This can involve additional processes like dry hopping or carbonation before the beer is packaged for distribution.
Advantages
- Control: Manual brewing allows brewers to have complete control over every aspect of the process. This flexibility enables them to experiment with different techniques, ingredients, and recipes.
- Craftsmanship: Many brewers appreciate the hands-on nature of manual brewing, which fosters a deeper connection to their craft and allows for creative expression.
- Unique Flavors: The ability to adjust variables during brewing often results in distinctive flavors and aromas, setting craft beers apart in a crowded market.
- Lower Initial Costs: Manual brewing systems typically require less upfront investment compared to automated systems, making them more accessible for small breweries and homebrewers.
Disadvantages
- Labor-Intensive: Manual brewing demands significant time and physical effort, which can lead to increased labor costs, especially in commercial settings.
- Inconsistency: Variability in brewing conditions, such as temperature fluctuations or human error, can lead to inconsistent results, making it challenging to replicate specific flavors across batches.
- Skill Requirement: Successful manual brewing requires a deep understanding of brewing science and techniques, which may pose a barrier for novice brewers.
- Time Consumption: The manual process can be slower compared to automated systems, potentially limiting production capacity for commercial breweries aiming to scale operations.
Manual brewing systems offer a unique blend of creativity, control, and craftsmanship, making them a popular choice among craft brewers. However, the labor-intensive nature and potential for inconsistency present challenges that must be carefully managed to achieve desired outcomes.
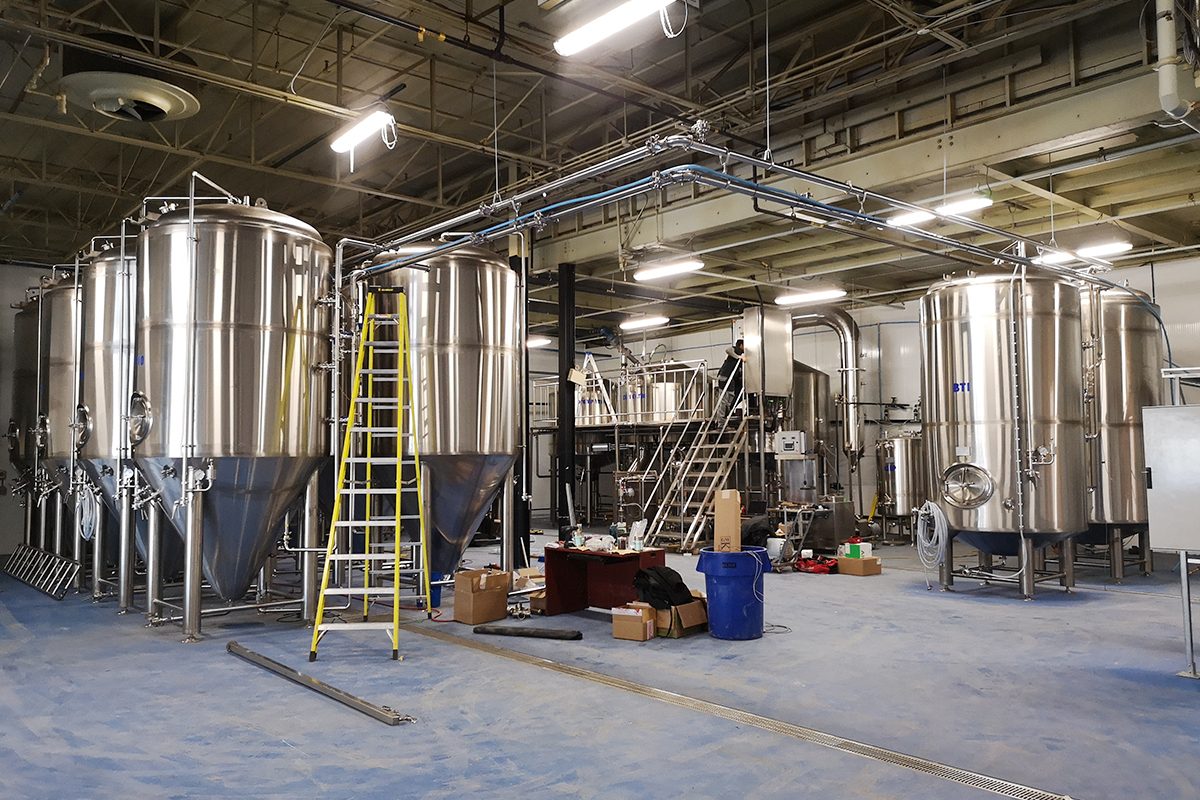
Automatic Brewing Systems
Automatic brewing systems are advanced setups that utilize technology and automation to streamline the brewing process. These systems typically integrate various components, including mash tuns, fermentation tanks, and control panels, allowing brewers to program and monitor the entire brewing process with minimal manual intervention. Automatic systems can range from compact, all-in-one machines suitable for small-scale operations to large, complex systems designed for commercial breweries, often equipped with sensors, data logging, and software for precise control.
These systems enhance efficiency by automating repetitive tasks, allowing brewers to focus on recipe development and quality control rather than the intricacies of the brewing process.
Brewing Process
The brewing process in automatic systems is typically outlined in several stages, facilitated by software that monitors and adjusts parameters:
- Mashing: Automated systems manage the mashing process by controlling temperature and time based on pre-programmed settings. This precision ensures optimal enzyme activity for sugar conversion.
- Boiling: The wort is automatically heated to boiling, with hops added at specific intervals. Automated timers can be set to manage hop additions accurately.
- Cooling: After boiling, automated wort chillers quickly bring the temperature down to yeast-pitching levels. Sensors ensure that the wort reaches the desired temperature without delay.
- Fermentation: The cooled wort is transferred to fermentation tanks where yeast is added. Automated monitoring systems track fermentation parameters such as temperature and specific gravity, alerting brewers to any deviations from the plan.
- Conditioning and Packaging: Once fermentation is complete, the beer can be conditioned and carbonated with minimal manual handling. Automated bottling or canning lines further enhance efficiency in the packaging process.
Advantages
- Consistency: Automatic systems provide uniform results by minimizing variability in the brewing process, ensuring each batch meets quality standards.
- Efficiency: Automation reduces labor costs and time spent on repetitive tasks, allowing for higher production rates.
- Precision: Advanced monitoring and control features enable precise adjustments to brewing parameters, enhancing the quality of the final product.
- Data Logging: Many systems offer data collection capabilities, allowing brewers to analyze and optimize their processes over time.
Disadvantages
- Initial Investment: The upfront cost for automatic brewing systems can be significantly higher than manual setups, which may deter smaller breweries.
- Less Hands-On Experience: For brewers who value craftsmanship, automation can lead to a disconnection from the brewing process and a reduction in the artisanal experience.
- Dependency on Technology: Automated systems can be susceptible to technical failures, requiring maintenance and technical expertise to resolve issues effectively.
- Limited Customization: While some systems offer programmable options, there may be constraints on making spontaneous changes during the brewing process compared to manual systems.
Automatic brewing systems represent a significant advancement in the brewing industry, offering numerous benefits that cater to the demands of modern commercial brewing while presenting challenges that require careful consideration.
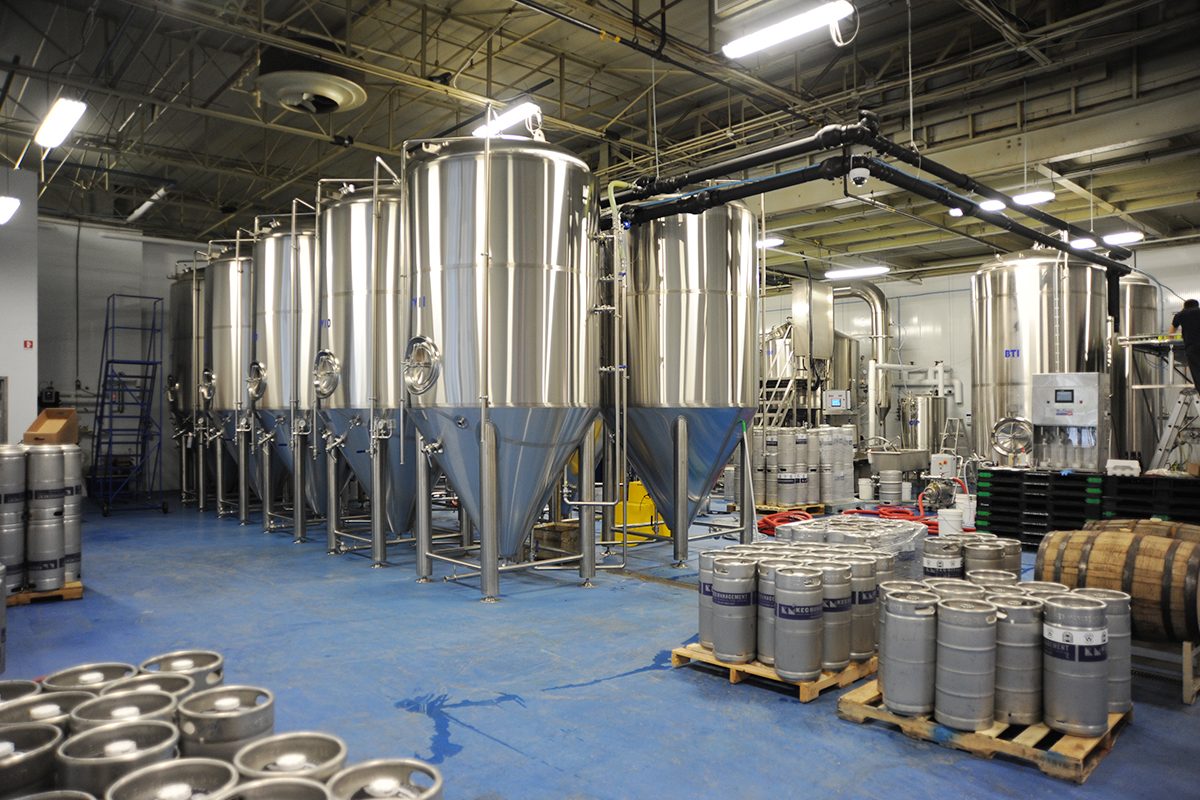
Comparative Analysis
When choosing between automatic and manual brewing systems, several key factors must be considered. This comparative analysis examines the quality of beer produced, cost considerations, time investment, learning curve and skill development, flexibility and customization, and environmental impact.
Quality of Beer Produced
Both manual and automatic brewing systems can produce high-quality beer, but the methods of achieving consistency differ. Manual brewing allows for a hands-on approach, enabling brewers to make real-time adjustments based on sensory evaluations. This can lead to unique flavors and artisanal qualities. However, the variability in human input can sometimes result in inconsistencies between batches.
Automatic systems, on the other hand, excel in reproducibility. The precision of automated controls minimizes the risk of human error, resulting in uniform batches. For commercial breweries where consistency is paramount, automatic systems are often preferred. Nonetheless, the craft of brewing can sometimes be perceived as less personal in fully automated environments, potentially impacting the distinctiveness of the beer.
Cost Considerations
The initial investment for manual brewing systems is generally lower, especially for smaller setups. Homebrewers or small craft breweries can start with basic equipment and gradually scale up. However, as production demands increase, manual systems may require additional labor and time, which can lead to higher operational costs.
Automatic brewing systems typically entail a higher upfront cost due to advanced technology and integrated components. While the investment may be significant, the efficiency gained can offset operational costs over time. Automated systems can also reduce labor needs, allowing breweries to allocate resources to other areas, such as marketing or recipe development.
Time Investment
Manual brewing requires a substantial time commitment, with brewers actively involved in each stage of the process. This hands-on approach can be rewarding, but it limits the number of batches that can be produced in a given timeframe. As demand increases, manual systems may struggle to keep pace.
Automatic systems are designed for efficiency, significantly reducing the time needed for brewing processes. Once programmed, these systems can operate with minimal supervision, allowing brewers to focus on other aspects of the business. This time-saving capability is especially beneficial for larger commercial operations where meeting demand is crucial.
Learning Curve and Skill Development
Manual brewing often requires a steeper learning curve, as brewers must develop a thorough understanding of the brewing process, ingredient interactions, and sensory evaluation. This knowledge fosters skill development and can enhance a brewer’s expertise, leading to greater creativity and innovation.
In contrast, automatic brewing systems can simplify the brewing process, making it accessible for beginners or those with limited experience. However, reliance on technology may reduce the depth of understanding needed to troubleshoot issues or innovate new recipes. Brewers using automatic systems may miss out on the hands-on experience that builds craftsmanship.
Flexibility and Customization
Manual brewing systems excel in flexibility, allowing brewers to experiment with ingredients, techniques, and styles. This adaptability is particularly valuable for craft brewers who prioritize unique and diverse offerings. Manual systems encourage creativity and can accommodate small-batch experiments.
Automatic brewing systems, while efficient, may have limitations in customization. Many systems are designed for specific recipes and processes, which can constrain experimentation. However, advanced models offer programmable settings that allow for some degree of flexibility. Still, the hands-on nature of manual systems remains unmatched in terms of adaptability.
Environmental Impact
The environmental impact of brewing systems varies based on efficiency and resource usage. Manual brewing may result in higher resource consumption, as processes are often less optimized. However, smaller-scale operations might focus on sustainable practices that mitigate environmental concerns.
Automatic systems tend to be more efficient, utilizing technology to optimize water and energy usage. Many modern automatic brewers incorporate eco-friendly features, such as heat recovery and efficient cooling systems, which can significantly reduce their carbon footprint. For commercial breweries looking to improve sustainability, investing in automatic systems can align with environmental goals.
The choice between automatic and manual brewing systems ultimately depends on a brewery’s specific needs, goals, and philosophy. Understanding these comparative factors can help brewers make informed decisions that best suit their operations.
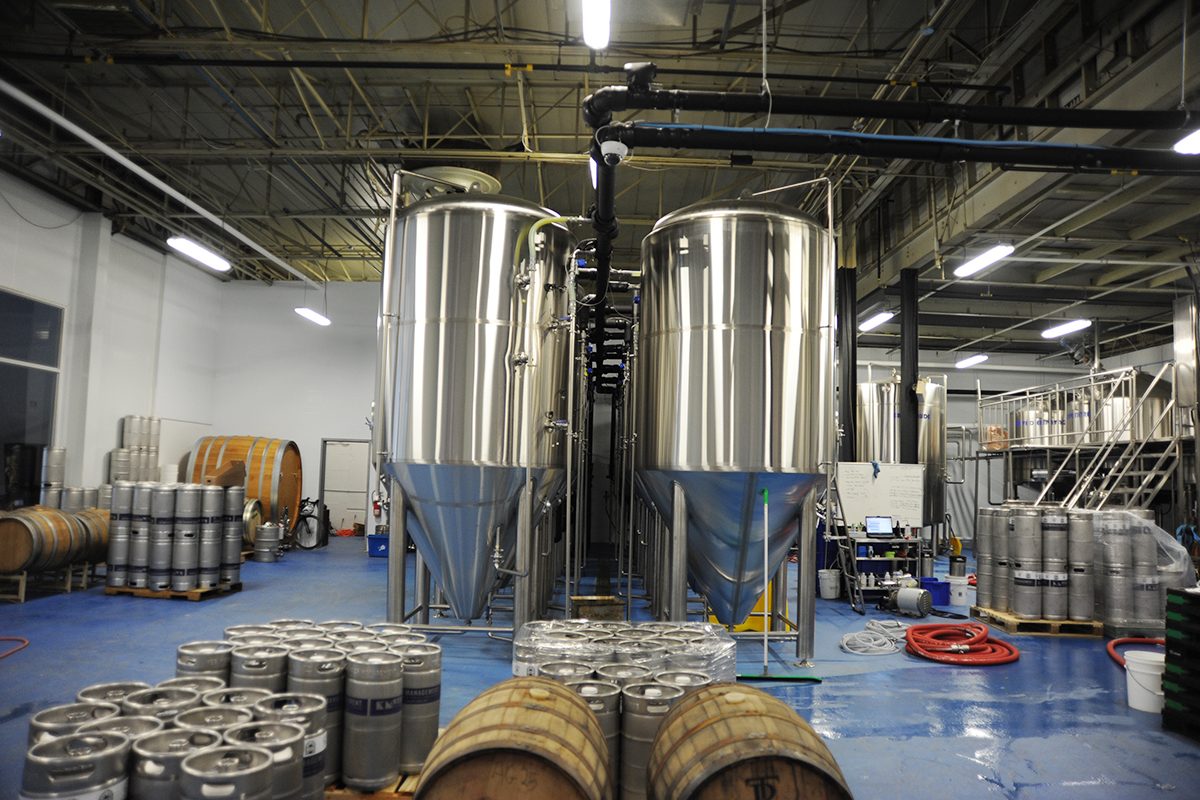
Summary
In the debate between automatic and manual brewing systems, each approach presents distinct advantages and challenges that cater to different brewing needs. Manual brewing systems offer hands-on control, allowing brewers to experiment with techniques and ingredients, which can lead to unique flavors and artisanal qualities. However, they require significant time and labor investment, along with a steeper learning curve. In contrast, automatic brewing systems enhance efficiency and consistency, minimizing human error and significantly reducing production time. While the initial investment is higher, the long-term savings in labor and operational costs can be substantial. Ultimately, the choice between these systems depends on a brewery’s specific goals, production scale, and desired level of involvement in the brewing process. By carefully considering these factors, brewers can select the system that best aligns with their vision and operational needs, ensuring the production of high-quality beer that meets market demands.
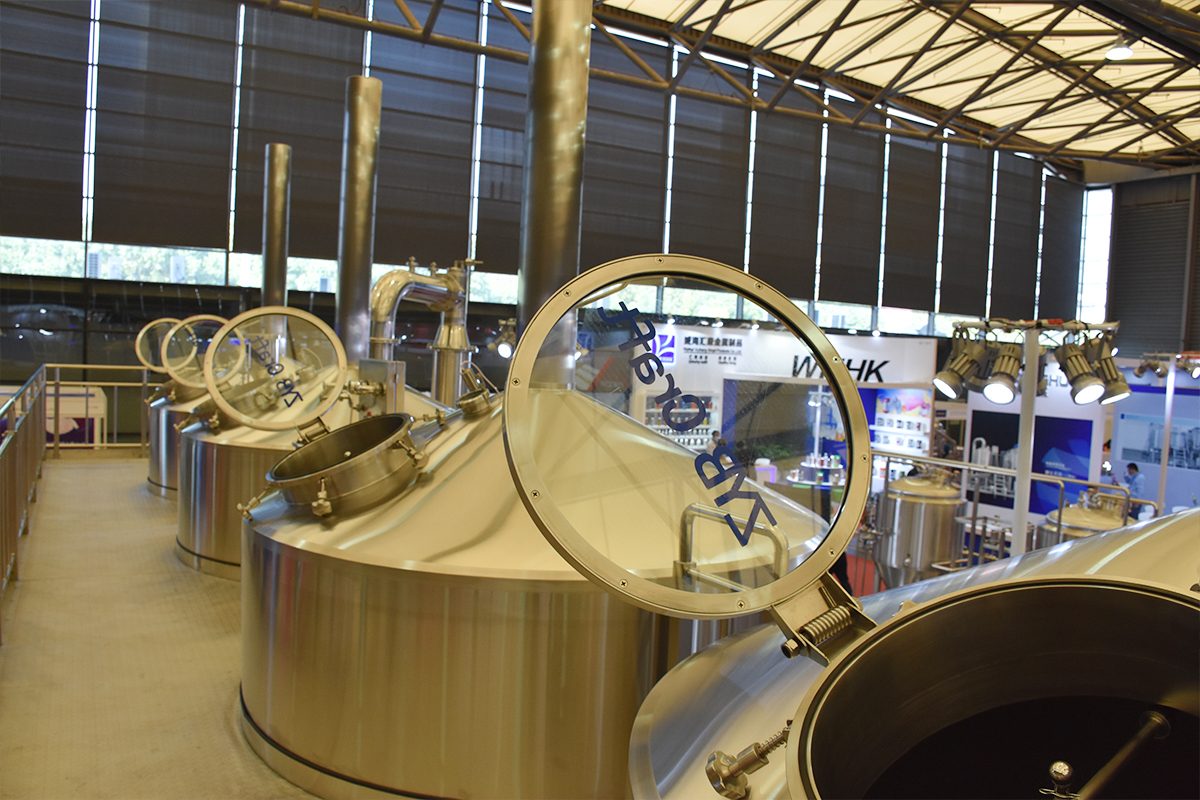
Get Turnkey Brewery Solutions
When choosing between automatic and manual brewing systems, it’s essential to consider how turnkey brewery solutions can streamline the process. A turnkey solution provides a comprehensive package that includes everything needed to start brewing, from brewery equipment and installation to training and support. ZYB Craft offers a variety of options tailored to your specific brewing needs, whether you prefer the hands-on approach of manual systems or the efficiency of automated setups.
With our turnkey solutions, you benefit from expert guidance throughout the entire process, ensuring that your brewery is equipped with the latest technology and optimized for production. This not only accelerates your time to market but also enhances operational efficiency. Additionally, our solutions are designed to grow with your business, allowing for easy scalability as demand increases. By investing in a turnkey brewery solution, you can focus on crafting exceptional beers while we handle the complexities of setup and integration.