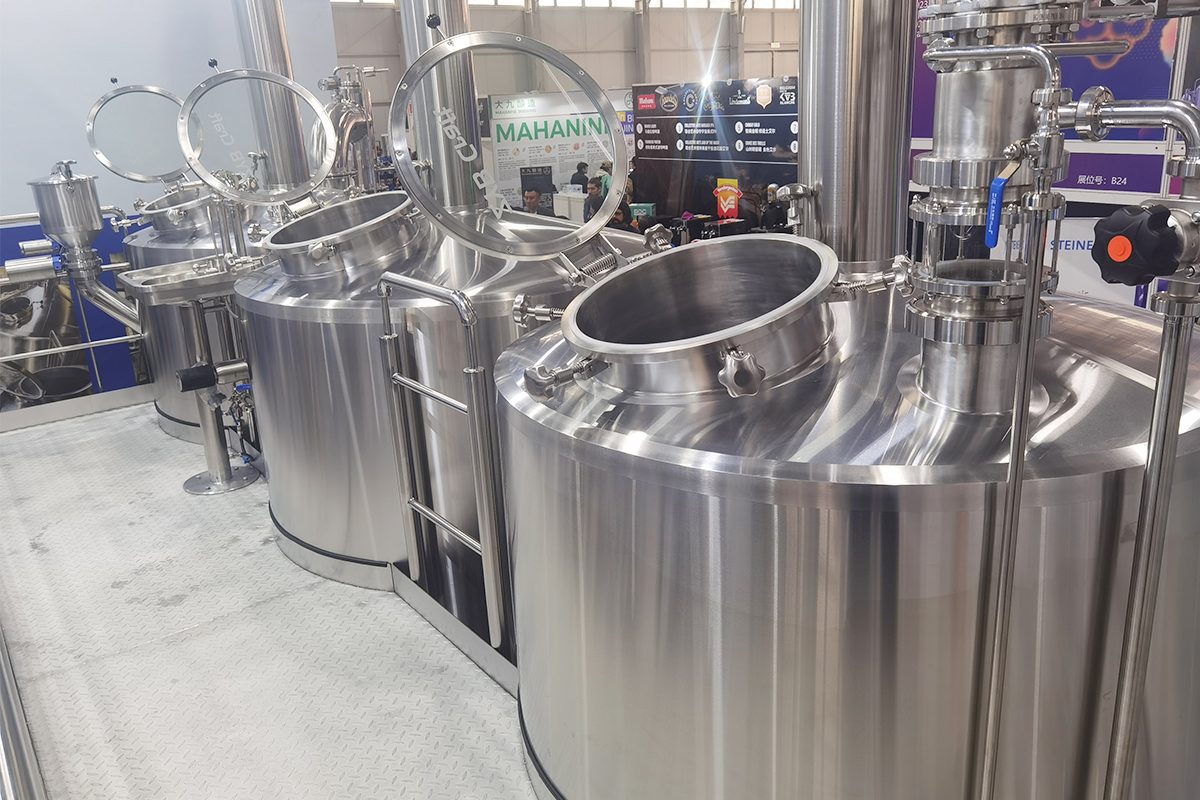
How To Choose The Right Heat Source For Brewhouse?
Choosing the right heat source for a brewhouse is a critical decision that significantly impacts the brewing process, efficiency, and overall quality of the beer produced. With various options available—from direct fire and electric heating to steam—each heat source offers unique advantages and challenges. The right choice not only influences energy consumption and operational costs but also affects the consistency and flavor profile of the final product. As breweries strive for efficiency and sustainability, understanding the intricacies of each heating method becomes essential. This article aims to guide brewers in selecting the most suitable heat source for their specific needs, balancing performance, cost, and environmental considerations.
Complete Guide
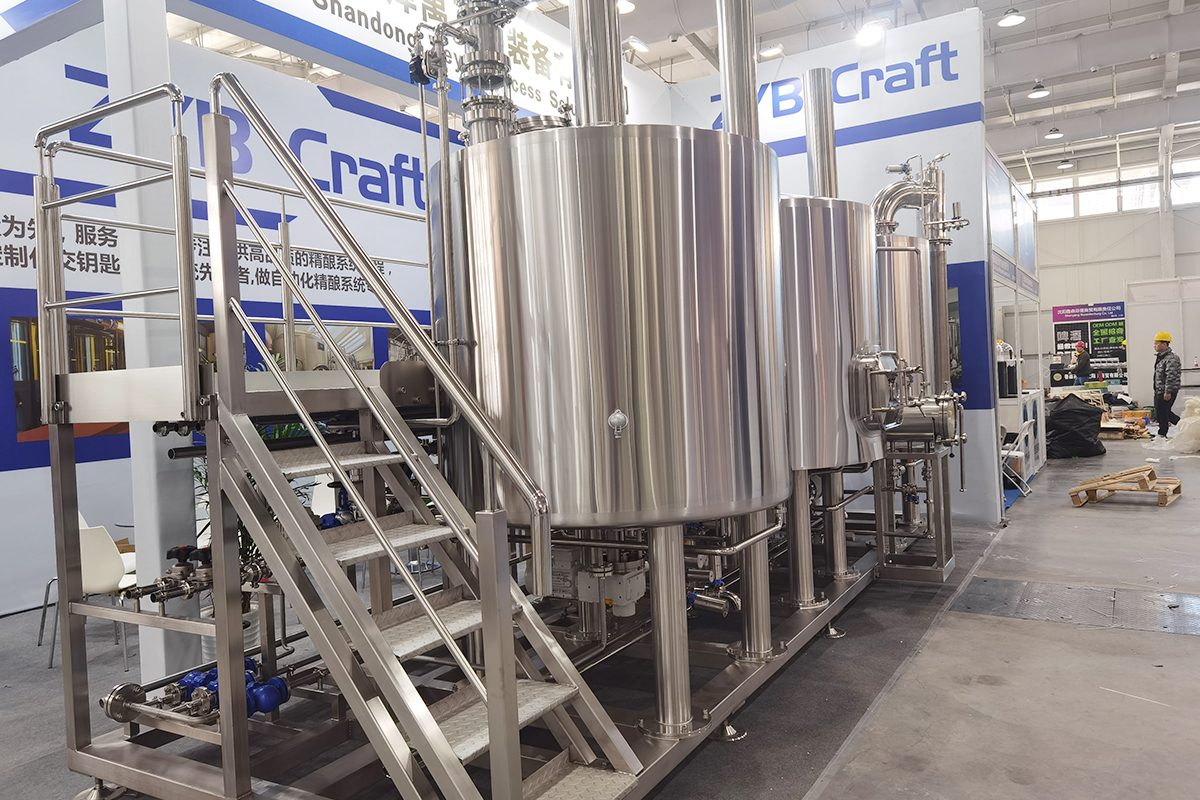
Understanding Brewing Process Requirements
Overview of the Brewing Process
The brewing process consists of several critical stages that transform raw ingredients into beer. The primary stages include mashing, boiling, and fermentation, each requiring specific temperature control and heat management.
- Mashing: This initial stage involves mixing crushed grains (malt) with hot water to extract fermentable sugars. The temperature during mashing typically ranges from 150℉ to 160℉ (65℃ to 71℃), depending on the desired beer style. Enzymes in the malt convert starches into sugars, creating a sweet liquid known as wort.
- Boiling: After mashing, the wort is boiled to sterilize it and extract flavors from hops. This stage usually occurs at temperatures around 210℉ (99℃). Boiling not only contributes bitterness and aroma from hops but also facilitates the evaporation of unwanted volatile compounds, helping to clarify the beer.
- Fermentation: Once the wort cools to the appropriate fermentation temperature (typically between 60℉ to 75℉ or 15℃ to 24℃ for ales), yeast is added to convert sugars into alcohol and carbon dioxide. Temperature control during fermentation is crucial, as it affects yeast activity and flavor development. Too high or too low temperatures can lead to undesirable off-flavors and slow fermentation rates.
Heat Requirements for Each Stage
Each stage of brewing has distinct heat requirements:
- Mashing: Consistent heat is needed to maintain the mashing temperature for the duration of the process, usually 60 to 90 minutes. Effective heat sources ensure that the temperature remains stable, facilitating optimal enzymatic activity.
- Boiling: This stage requires high heat for a specific duration, typically lasting 60 to 90 minutes. An effective heat source must deliver a rapid and consistent boil to achieve desired hop utilization and evaporate excess water.
- Fermentation: While not requiring constant heat like the previous stages, maintaining an optimal fermentation temperature is critical. Heat sources may be used for cooling systems or temperature control jackets to manage the temperature during fermentation, ensuring yeast operates efficiently.
The Significance of Temperature Control
Temperature control is paramount throughout the brewing process. Each stage has an optimal temperature range that must be maintained to achieve desired results. In mashing, precise temperatures influence the efficiency of sugar extraction and the overall mouthfeel of the beer. During boiling, temperature stability affects hop utilization and clarity. In fermentation, temperature fluctuations can lead to off-flavors, affect yeast health, and influence the beer’s final characteristics.
Understanding the heat requirements and temperature control for each brewing stage is essential for selecting the appropriate heat source. The right choice not only enhances efficiency and consistency but also contributes to the quality and complexity of the final beer product.
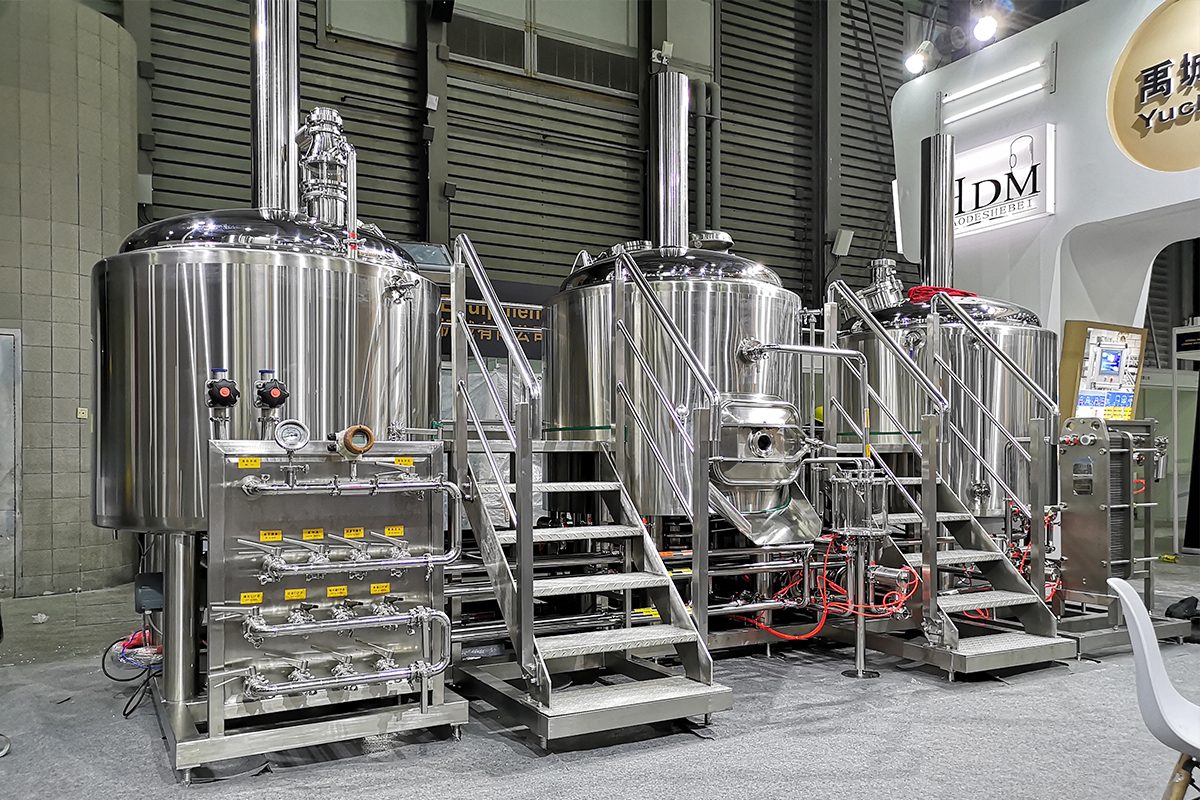
Importance of Heat Sources in Brewing
Heat sources are fundamental to the brewing process, directly influencing key stages such as mashing, boiling, and fermentation. The right heat source ensures optimal temperature control, which helps extract sugars and achieve desired flavor characteristics during the mashing process. Additionally, during the boiling stage, the heat source promotes the evaporation of undesirable compounds while isomerizing the hops, thereby contributing to the development of bitterness and aroma in the beer.
Efficient heat transfer maintains consistent brewing cycles, reduces energy costs, and minimizes downtime. A reliable heat source also supports the fermentation process by maintaining the ideal temperature for yeast activity, impacting fermentation speed and the development of flavors. Ultimately, the choice of heat source affects not only operational efficiency and cost-effectiveness but also the quality and characteristics of the final product, making it a pivotal aspect of brewery design and function.
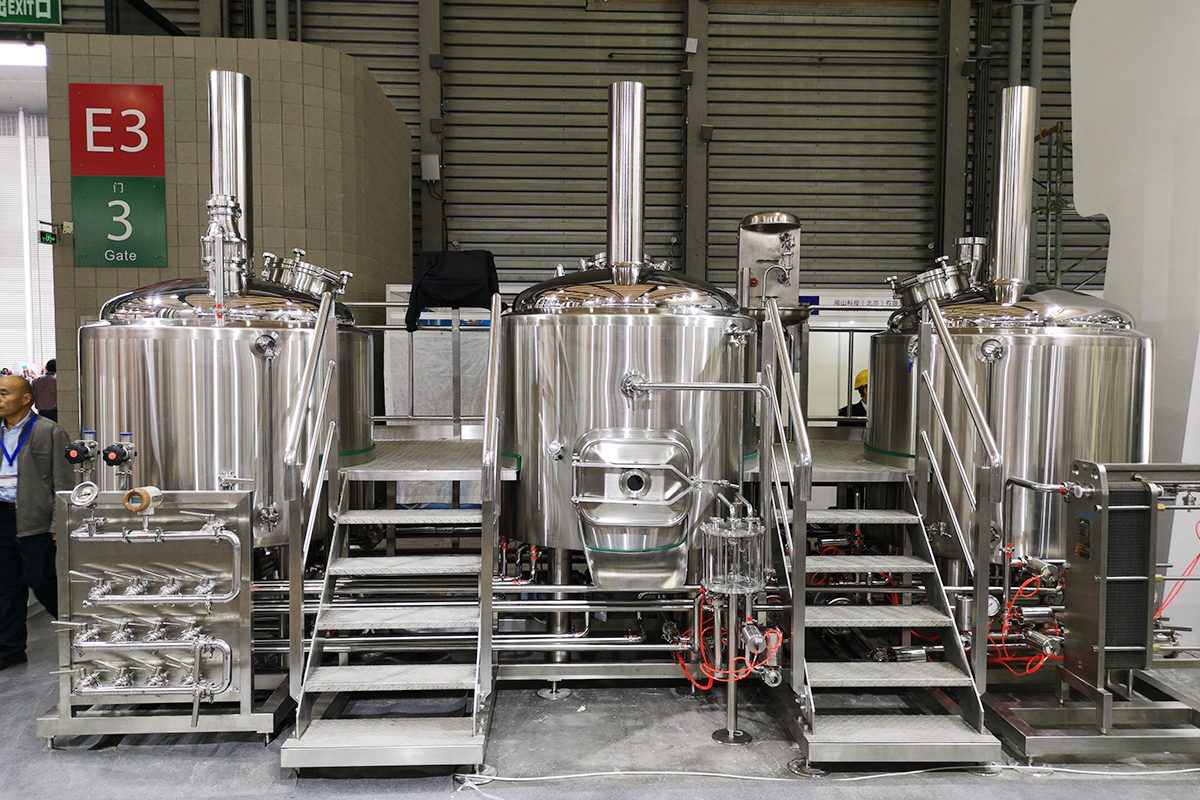
Types of Heat Sources
Choosing the right heat source for a brewhouse involves understanding the different options available. Here, we explore three primary types of heat sources: Direct Fire Heating, Steam Heating, and Electric Heating.
Direct Fire Heating
Direct fire heating utilizes an open flame or gas burner to directly heat the brewing vessels. This method is common in many traditional breweries, where natural gas or propane is burned to produce heat.
Pros
- Cost-Effective: Generally lower initial equipment costs compared to other heating methods.
- Quick Heating: Provides rapid temperature increases, allowing for efficient mashing and boiling processes.
- Simplicity: Straightforward installation and operation with fewer mechanical components.
Cons
- Uneven Heating: Potential for hot spots in the brewing vessel, which may lead to scorching or caramelization of the wort.
- Safety Concerns: Open flames pose safety risks and require careful monitoring and safety measures.
- Emissions: Produces combustion gases that may require proper ventilation and can impact air quality.
Steam Heating
Steam heating involves generating steam in a boiler and transferring that heat to the brewing vessel via a heat exchanger or direct steam injection. This method is widely used in commercial breweries due to its efficiency and effectiveness.
Pros
- Consistent Heat: Provides uniform heating throughout the brewing process, minimizing the risk of hot spots.
- Efficiency: Steam can transfer heat efficiently, leading to reduced energy costs in the long term.
- Versatility: Suitable for various brewing processes, including mashing, boiling, and cleaning.
Cons
- Initial Investment: Higher upfront costs for steam generation equipment and installation.
- Complexity: Requires more sophisticated control systems and regular maintenance of steam boilers.
- Space Requirements: Steam systems may require additional space for boilers and associated equipment.
Electric Heating
Electric heating utilizes electric elements to heat the brewing vessels. This method is becoming increasingly popular due to advancements in electric heating technology and the desire for cleaner energy sources.
Pros
- Precise Control: Offers excellent temperature control, allowing brewers to adjust settings accurately and maintain consistent temperatures.
- Clean Operation: Produces no emissions at the point of use, improving air quality and reducing the need for ventilation.
- Low Maintenance: Generally requires less maintenance compared to gas or steam systems, with fewer mechanical components.
Cons
- Higher Operating Costs: Depending on local energy rates, operating costs may be higher compared to gas or steam options.
- Limited Heating Capacity: Electric systems may have limitations in heating capacity for larger brewing operations, requiring careful sizing and design.
- Dependence on Power Supply: Reliance on a stable electrical supply can be a drawback, especially in areas with unreliable power.
By understanding the characteristics, advantages, and disadvantages of each heat source, brewers can make informed decisions that align with their specific needs and operational goals. If you plan to learn more about the different types of heating types you can read the article “Brewhouse Heating Options: Electric VS Steam VS Direct Fire”.
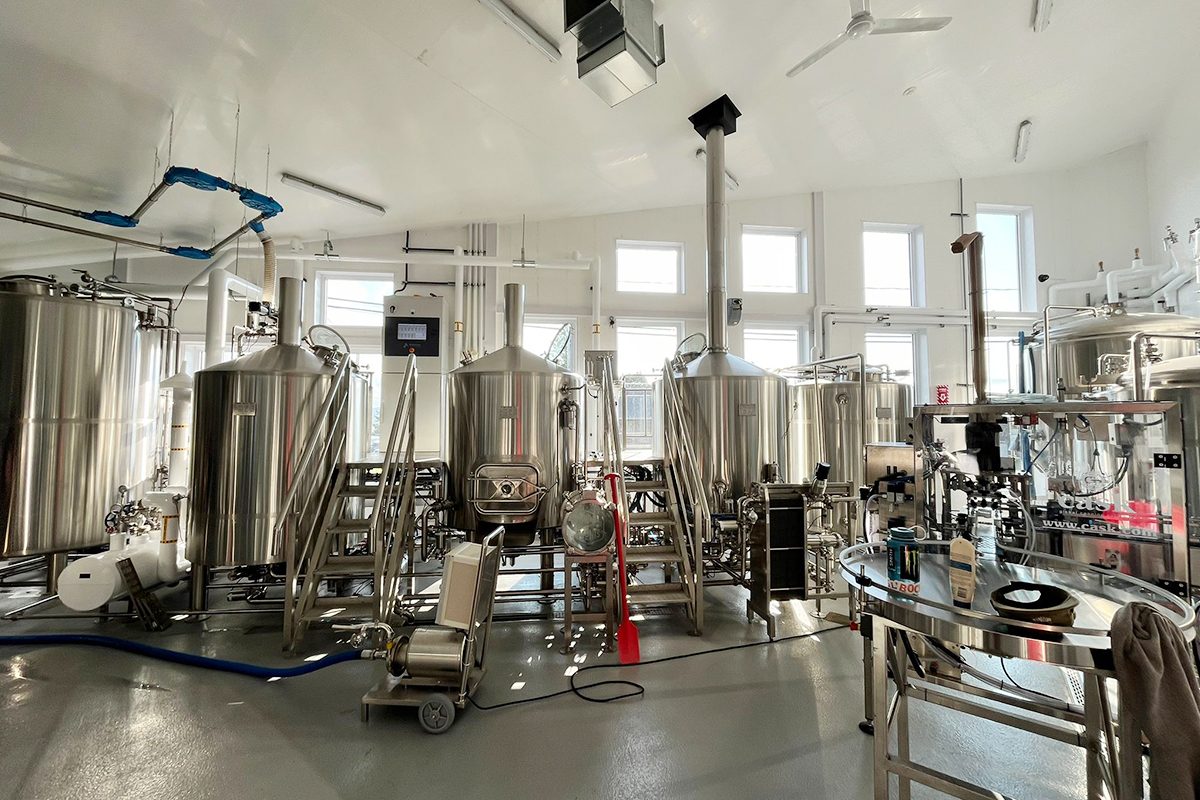
Factors to Consider When Choosing a Heat Source
When selecting the right heat source for a brewhouse, several critical factors must be taken into account to ensure optimal performance, cost-effectiveness, and safety. Here are the key considerations:
Brewery Size and Production Volume
The scale of the brewery significantly influences the choice of heat source. Larger breweries with high production volumes may require robust systems that can deliver consistent and substantial heat output. Smaller operations, on the other hand, might benefit from more compact and efficient heating solutions that match their lower volume needs. Understanding production capacity helps determine the appropriate heat source type and size.
Energy Efficiency
Energy efficiency is a vital consideration, as it directly impacts operating costs. Evaluating the thermal efficiency of different heat sources can lead to substantial savings over time. Options that provide quick heat transfer and minimal energy waste should be prioritized to reduce overall energy consumption and enhance profitability.
Space and Infrastructure
The available space within the brewery can limit the choice of heat source. For example, steam systems require boilers and associated infrastructure, which may take up significant space. Electric heating might be more suitable for smaller breweries, while direct fire systems could necessitate ventilation solutions. Assessing existing infrastructure and space constraints can help achieve effective planning.
Initial Investment VS Long-term Costs
While the initial investment is a crucial factor, it should be weighed against long-term operational costs. Some systems may have lower upfront costs but higher ongoing expenses, while others might require a larger initial investment but offer significant savings over time. Conducting a comprehensive cost analysis can help make a well-informed decision that balances immediate financial outlay with future savings.
Control and Precision
The ability to control and maintain precise temperatures makes for efficient brewing. Heat sources that offer advanced temperature control features allow for greater consistency in the brewing process, which is essential for producing high-quality beer. Systems that can adapt quickly to changes in brewing conditions can enhance product quality and reduce waste.
Environmental Impact
As sustainability becomes increasingly important in the brewing industry, the environmental impact of the chosen heat source must be considered. Options that utilize renewable energy or have a lower carbon footprint can enhance a brewery’s reputation and align with consumer preferences for eco-friendly practices. Evaluating emissions, resource use, and compliance with environmental regulations is crucial.
Flexibility and Scalability
Breweries may experience changes in production volume due to market demand. Therefore, the chosen heat source should be flexible and scalable to adapt to changing needs. Systems that allow for easy upgrades or modifications can support growth and help breweries respond to fluctuations in demand without significant additional investment.
Safety and Compliance
Safety is paramount in any brewing operation. Each heat source comes with its own set of safety considerations, including the risk of fires, explosions, or equipment malfunctions. Understanding the regulatory requirements and compliance standards for each heat source can help ensure safe operation and avoid potential liability. Implementing safety measures, regular maintenance, and employee training can mitigate risks associated with various heating methods.
By carefully considering these factors, brewers can make an informed decision when choosing a heat source that aligns with their operational needs, financial constraints, and long-term goals.
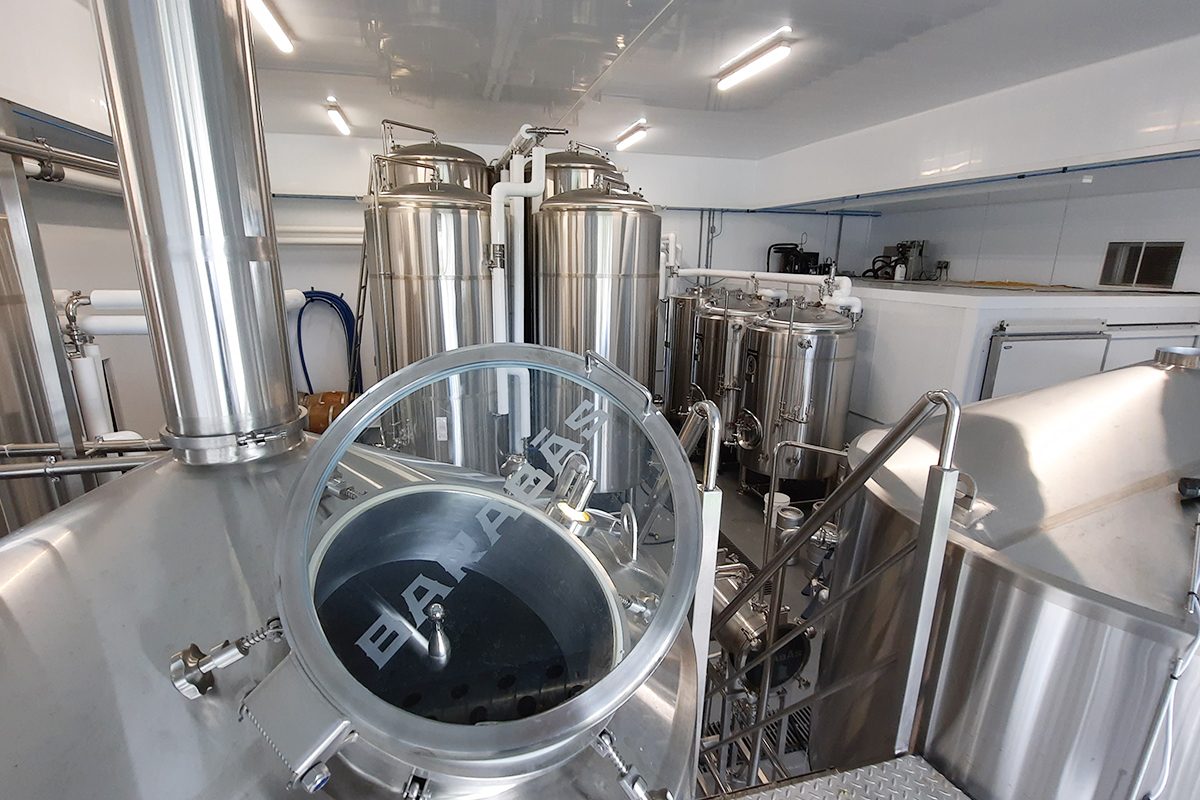
Cost Analysis
When choosing a heat source for a brewhouse, a thorough cost analysis can ensure long-term financial viability. This analysis should encompass three main components: initial investment, operating costs, and return on investment.
Initial Investment
The initial investment includes all costs associated with purchasing and installing the heat source. This can vary significantly depending on the type of heating system selected. For example, direct fire systems may have lower upfront costs, while steam heating systems typically require more significant investment due to the need for boilers and associated infrastructure. Electric heating systems can also vary, depending on the power requirements and control systems. It’s crucial to account for not just the equipment costs, but also installation, necessary modifications to existing infrastructure, and any required permits.
Operating Costs
Operating costs refer to the ongoing expenses related to running the heat source. This includes energy costs, maintenance, and repairs. Different heat sources have varying efficiencies, which directly affect energy consumption. For instance, steam heating may have lower operational costs over time due to its efficiency, while direct fire may lead to higher fuel expenses. Additionally, maintenance costs can vary based on the complexity of the system; more sophisticated setups may require more frequent servicing and part replacements. Evaluating these ongoing costs helps understand the long-term financial impact.
Return on Investment
Return on investment (ROI) is a critical metric that helps determine the financial feasibility of a heat source. ROI can be calculated by comparing the initial investment and operating costs against the expected increases in production efficiency and quality improvements in the final product. A more efficient heat source may lead to reduced energy costs and faster brewing cycles, enhancing productivity and profitability. Assessing the ROI allows brewers to make informed decisions that align with their financial goals and operational needs, ensuring a sustainable and profitable brewing operation.
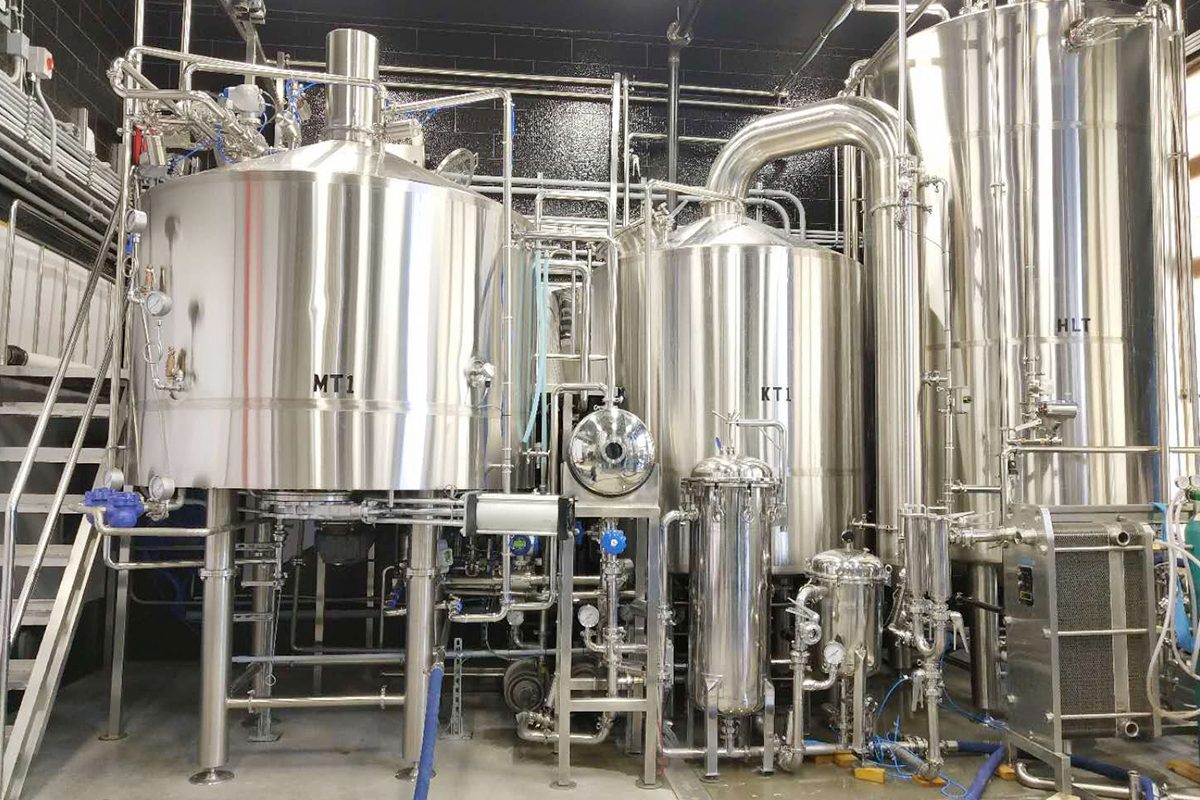
Summary
Choosing the right heat source for a brewhouse is a pivotal decision that influences both the brewing process and the quality of the final product. Factors such as brewery size, energy efficiency, space availability, and safety compliance play critical roles in this choice. Each heat source—whether direct fire, steam, or electric—has distinct advantages and drawbacks, affecting initial investment, operating costs, and return on investment. Effective temperature control is essential for ensuring consistent brewing results while considering the environmental impact that aligns with modern sustainability goals. By thoroughly analyzing these factors, brewers can make informed decisions that not only enhance production efficiency but also contribute to the overall success and growth of their operations. Ultimately, selecting the appropriate heat source is an investment in the future of the brewery, enabling the production of high-quality beer while optimizing operational performance.
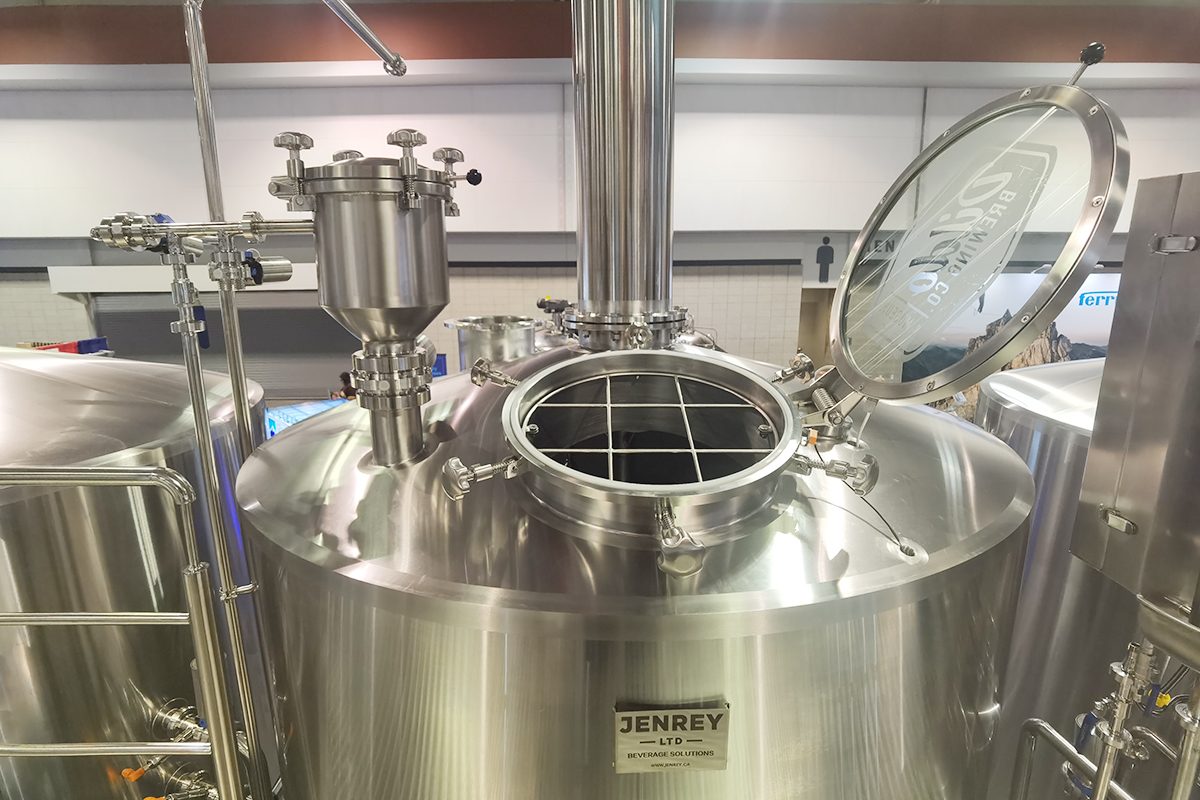
Get Turnkey Brewery Solutions
When choosing the right heat source for your brewhouse, consider partnering with ZYB Craft for comprehensive turnkey brewery solutions. Our approach encompasses everything from initial consultation and design to installation and ongoing support, ensuring a seamless transition from concept to production. We specialize in customizing heat source options to meet your specific brewing requirements, whether you’re looking for energy-efficient systems or high-capacity solutions.
Our turnkey solutions include integrated brewery equipment, precise temperature control systems, and reliable heat sources tailored to your production scale. By providing a complete package, we simplify the decision-making process, allowing you to focus on what matters most—crafting exceptional beer. With our expertise and commitment to quality, you can rest assured that your brewery will operate efficiently and effectively, maximizing both productivity and profitability. Let ZYB Craft help you create the perfect brewing environment with our tailored solutions designed for success.