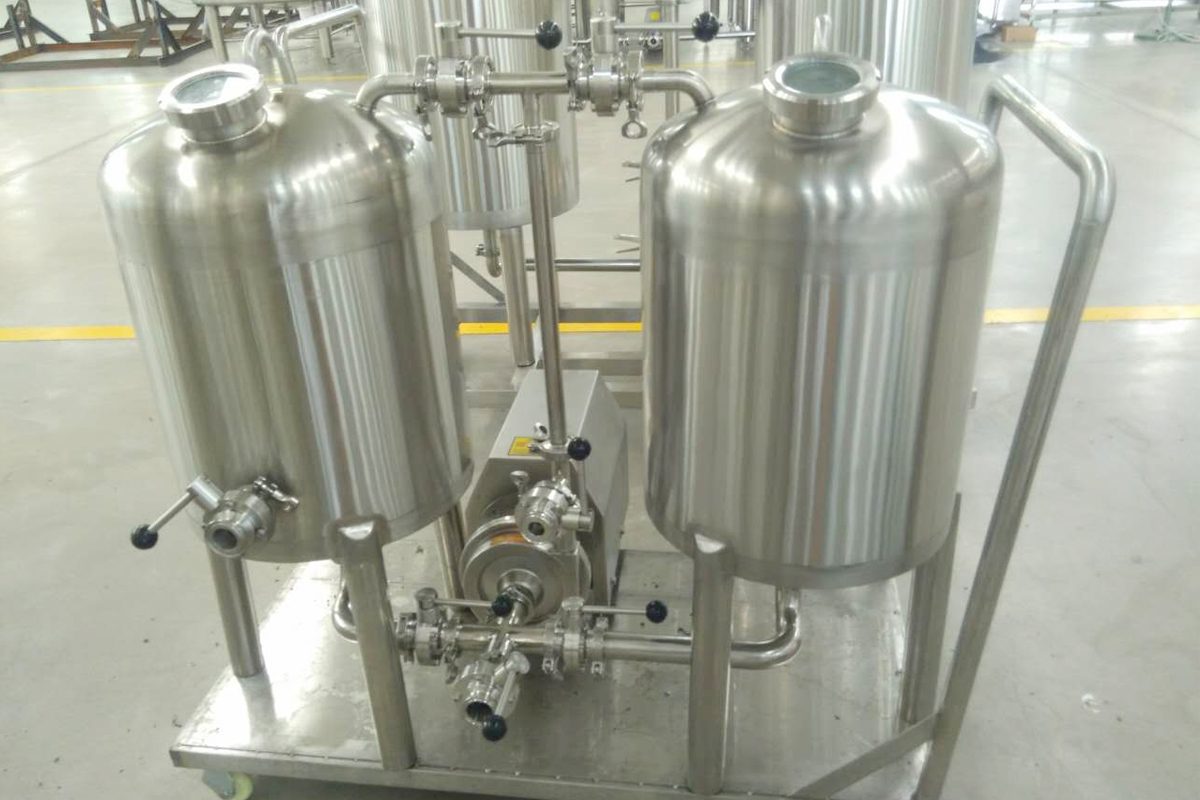
What You Need To Know When Considering CIP Systems
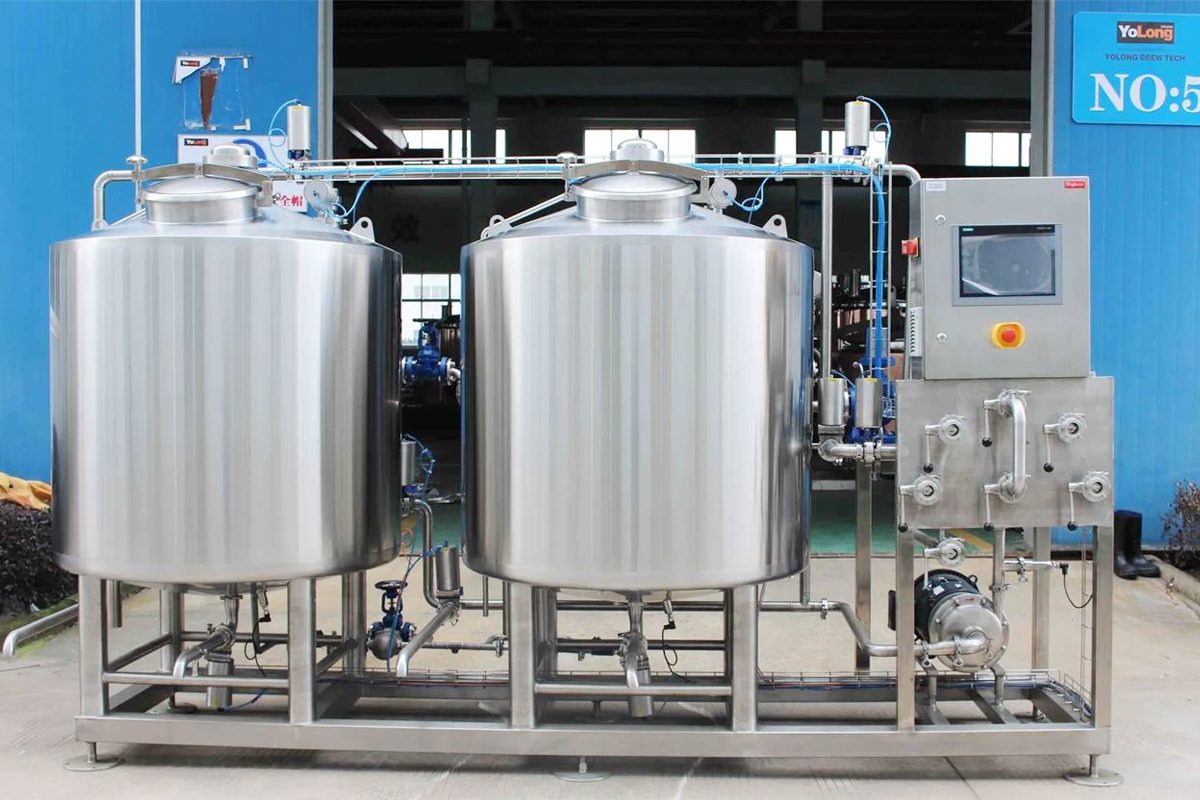
Understanding CIP Systems
Definition and Functionality
Components of a CIP System
Supply Tanks
Supply tanks can hold a variety of cleaning and sanitizing solutions used in the CIP process. Typically, a CIP system includes separate tanks for:
- Water Tank: Used for the initial and final rinses to remove loose debris and residual cleaning agents.
- Detergent Tank: Contains the detergent solution that helps dissolve and remove soils, fats, proteins, and other residues.
- Sanitizer Tank: Holds the sanitizing solution that eliminates microbial contaminants, ensuring the equipment is safe for subsequent production.
Supply Pumps
Return Pumps
Control Systems
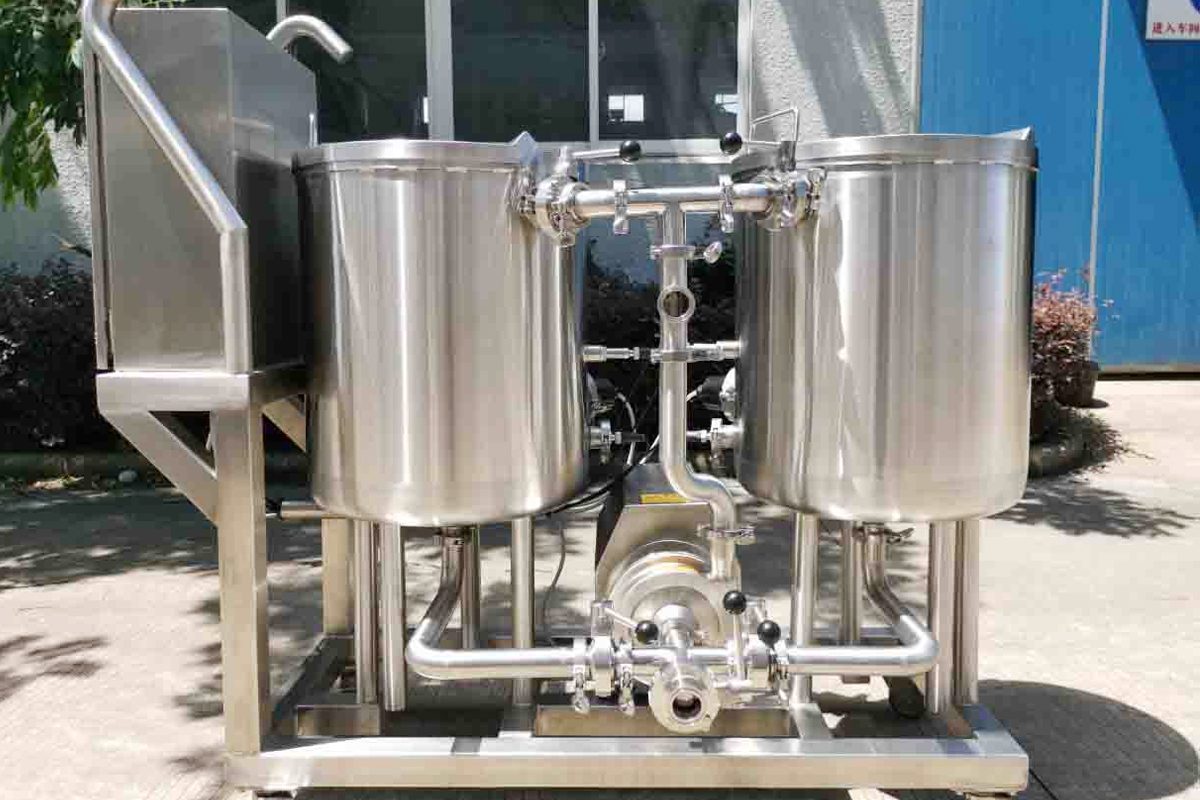
Importance of CIP Systems
Consistent Cleaning
Efficiency
Compliance
Resource Management
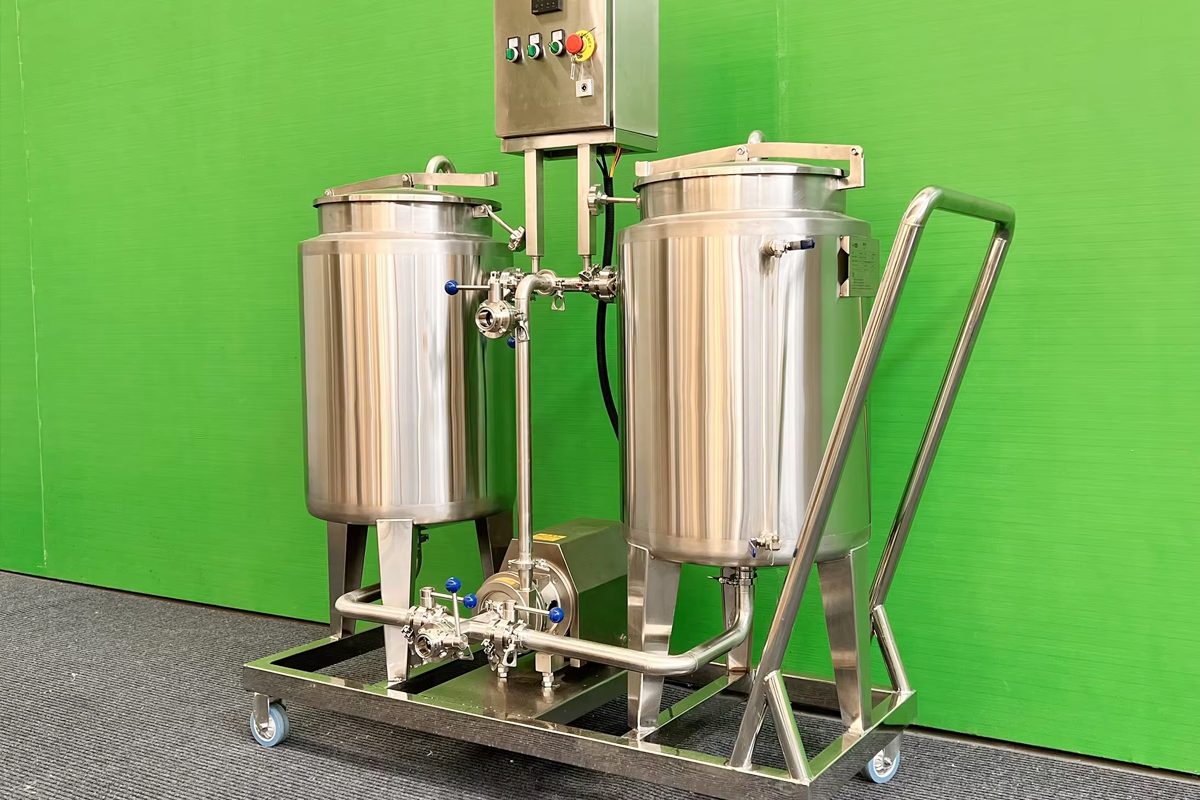
Types of CIP Systems
Single-Use CIP Systems
- Elimination of Cross-Contamination: Since fresh solutions are used for each cycle, there is no risk of carrying over contaminants from one cleaning cycle to the next.
- Simplified Validation: With no need to validate the effectiveness of solution recovery and reuse, validation processes can be more straightforward.
- Flexibility: These systems can be quickly adapted to different cleaning requirements or production shifts, making them ideal for facilities with diverse product lines.
Recoverable CIP Systems
- Resource Efficiency: By reusing cleaning solutions, these systems reduce the consumption of water, chemicals, and energy, resulting in lower operational costs.
- Environmental Benefits: Reduced resource use translates to a smaller environmental footprint, making recoverable systems an environmentally friendly option.
- Cost Savings: The reuse of cleaning solutions can lead to significant cost savings over time, especially in large-scale operations.
Automated VS Manual CIP Systems
Automated CIP Systems
Automated CIP systems are equipped with advanced control systems that manage the entire cleaning process, from the preparation of cleaning solutions to the final rinse. These systems use sensors and programmable logic controllers (PLCs) to monitor and control parameters such as temperature, flow rate, and chemical concentration. Automated systems offer several key benefits:
- Consistency: Automation ensures that each cleaning cycle follows the same protocol, resulting in consistent and repeatable cleaning results.
- Efficiency: Automated systems can operate without direct human intervention, reducing labor costs and minimizing the risk of human error.
- Data Logging and Reporting: These systems can record detailed data on each cleaning cycle, providing valuable information for validation and compliance purposes.
Manual CIP Systems
Manual CIP systems require human intervention to control and monitor the cleaning process. Operators manually prepare cleaning solutions, adjust flow rates and temperatures, and monitor the progress of the cleaning cycle. While manual systems are less expensive to install and can be more flexible in certain applications, they have some limitations:
- Labor-Intensive: Manual systems require more labor and oversight, which can increase operational costs and the risk of human error.
- Inconsistency: Variations in manual operations can lead to inconsistencies in cleaning results, potentially compromising product quality and safety.
- Limited Data Collection: Manual systems may not provide the same level of data logging and reporting as automated systems, making it more challenging to demonstrate compliance.
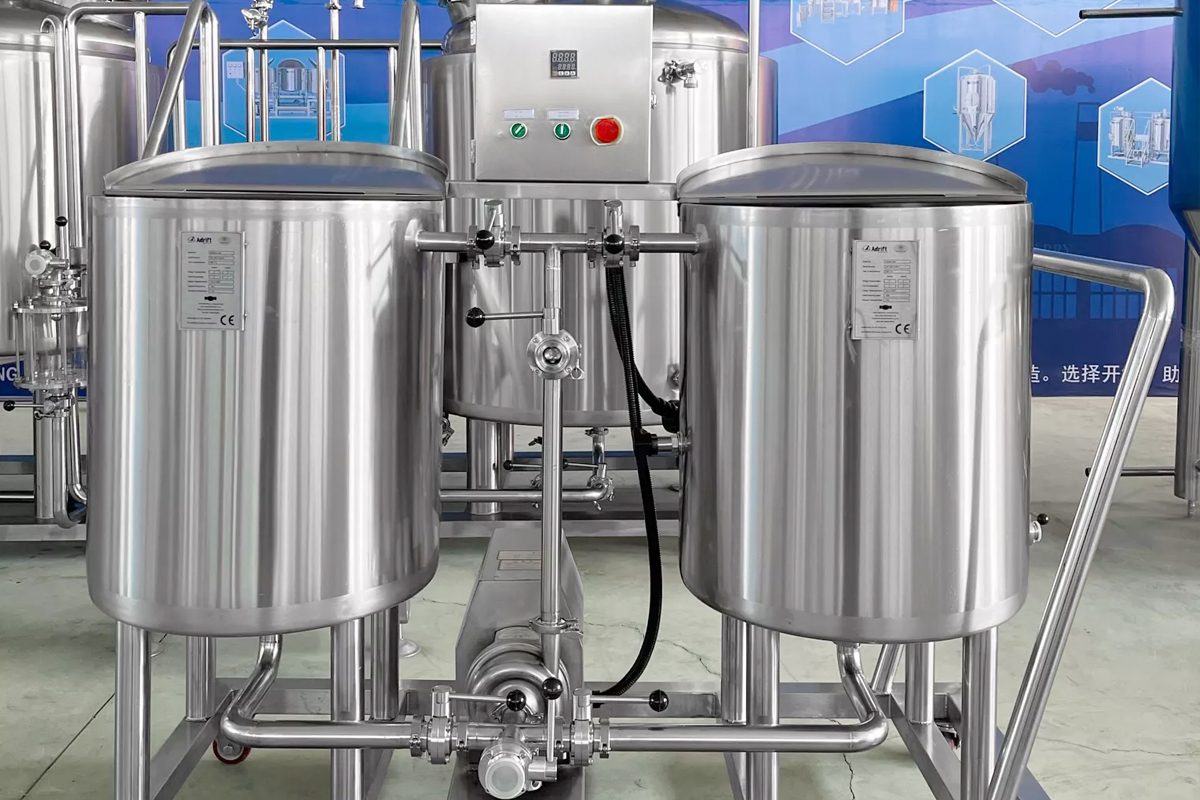
Benefits and Challenges of CIP Systems
Benefits of CIP Systems
- Consistent and Repeatable Cleaning: CIP systems provide a standardized cleaning process that ensures consistent and repeatable results. The automation of cleaning procedures eliminates variability, ensuring that equipment is cleaned to the same high standard every time. This consistency maintains product quality and safety because it reduces the risk of contamination and cross-contamination.
- Operational Efficiency: One of the most significant benefits of CIP systems is their ability to clean equipment without disassembly, significantly reducing downtime. Automated CIP systems can be programmed to run during off-hours, minimizing the impact on production schedules. This efficiency leads to increased productivity and optimal use of resources.
- Resource Conservation: Modern CIP systems are designed to use water, chemicals, and energy efficiently. Recoverable CIP systems, in particular, recycle cleaning solutions, reducing the overall consumption of resources. This not only lowers operational costs but also aligns with environmental sustainability goals by minimizing waste and resource depletion.
- Enhanced Safety: CIP systems minimize the need for manual cleaning, reducing the risk of worker exposure to hazardous chemicals and the potential for workplace injuries. Automated systems further enhance safety by controlling and monitoring chemical dosing and process parameters, ensuring safe and accurate cleaning.
- Regulatory Compliance and Documentation: CIP systems help facilities comply with stringent hygiene and safety regulations. Automated systems can provide detailed records of each cleaning cycle, including parameters such as temperature, flow rate, and chemical concentrations. This data is invaluable for validation, audits, and ensuring compliance with industry standards.
Challenges of CIP Systems
- High Initial Investment: The installation of a CIP system can involve significant upfront costs, including the purchase of equipment, installation, and integration with existing systems. The need for specialized components, such as pumps, heat exchangers, and control systems, can add to the expense. However, these initial costs can often be offset by long-term savings in labor, resources, and efficiency.
- Complexity and Maintenance: CIP systems can be complex, requiring careful design and configuration to ensure optimal performance. Regular maintenance is necessary to keep the system operating effectively, including the calibration of sensors, inspection of pumps, and verification of chemical concentrations. Facilities must also have trained personnel to manage and troubleshoot the system, adding to the operational complexity.
- Chemical Compatibility and Safety: The selection of cleaning agents must consider the compatibility with equipment materials and the products being processed. Incompatible chemicals can cause corrosion, damage equipment, or leave residues that compromise product quality. Additionally, handling and storing cleaning chemicals require strict safety protocols to prevent accidents and ensure worker safety.
- Waste Management: While CIP systems are designed to be resource-efficient, the disposal of used cleaning solutions and waste materials still needs careful management. Facilities must comply with environmental regulations regarding the discharge of chemicals and wastewater. This can involve additional costs and logistical considerations, such as treatment facilities or disposal services.
- Space Requirements: CIP systems, especially those with multiple tanks and complex piping, can require a significant amount of space. Facilities must plan for adequate space to accommodate the system, including considerations for access, maintenance, and future expansion. Space constraints can sometimes limit the scalability or configuration options of the system.

Design Considerations for CIP Systems
System Layout and Piping Design
The layout of a CIP system is fundamental to its effectiveness and efficiency. The design should ensure complete coverage of all equipment surfaces, minimize dead zones where cleaning agents might not reach, and facilitate the easy drainage of cleaning solutions.
- Piping Design: Piping should be designed to promote the smooth and efficient flow of cleaning solutions. Properly sized piping can maintain the desired flow rate and avoid pressure drops. The design should also minimize bends and fittings, which can create areas where soils and contaminants might accumulate.
- Spray Devices and Nozzles: The placement and type of spray devices, such as spray balls or nozzles, are critical for effective cleaning. These devices must be positioned to ensure that all internal surfaces of the equipment are thoroughly cleaned, with particular attention to challenging areas like corners and crevices.
- Accessibility: The system layout should allow easy access for maintenance and inspection. Components like tanks, pumps, and valves should be positioned to facilitate routine checks and repairs.
Selection of Cleaning Agents
Selecting the right cleaning agent allows for effective cleaning and ensures equipment and personnel safety.
- Type of Soils: The selection of cleaning agents depends on the type of residues or soils to be removed, such as fats, proteins, sugars, or mineral deposits. The nature of the soil will determine whether alkaline, acidic, enzymatic, or other specialized cleaning agents are required.
- Compatibility: Cleaning agents must be compatible with the materials of the equipment to prevent corrosion or damage. The selection should also consider the compatibility with the products being processed to avoid cross-contamination or residue issues.
- Environmental and Safety Considerations: The environmental impact and safety profile of the cleaning agents should be considered. This includes factors such as biodegradability, toxicity, and the potential for hazardous reactions. Facilities should also ensure proper handling and storage of chemicals to maintain safety.
Temperature and Flow Rate Control
Temperature and flow rate are critical parameters that influence the effectiveness of the cleaning process.
- Temperature Control: The temperature of the cleaning solutions can significantly affect their cleaning power. For example, higher temperatures can enhance the efficacy of alkaline cleaners and sanitizers. However, it is essential to consider the thermal stability of both the cleaning agents and the equipment materials.
- Flow Rate: Adequate flow rates are necessary to create the mechanical action required to remove soils from surfaces. The flow rate must be carefully controlled to ensure sufficient turbulence for effective cleaning without causing damage to the equipment.
- Heating Systems: Incorporating heat exchangers or other heating systems in the CIP design can help maintain the desired temperature throughout the cleaning cycle, ensuring consistent results.
Material Compatibility
The materials used in the construction of the CIP system and the equipment being cleaned must be compatible with the cleaning agents and the process conditions.
- Corrosion Resistance: Stainless steel is commonly used in CIP systems due to its corrosion resistance and durability. However, other materials, such as certain plastics or specialized alloys, may be required depending on the specific chemical and thermal conditions.
- Surface Finish: The surface finish of equipment can affect the cleaning process. Smooth, polished surfaces are easier to clean and less likely to harbor contaminants compared to rough or pitted surfaces. The design should ensure that all surfaces are appropriately finished to facilitate effective cleaning.
Automation and Control
Automation and control systems can help manage the complexity of the CIP process and ensure consistent, reliable cleaning.
- Control Systems: Modern CIP systems are equipped with advanced control systems that automate the cleaning process. These systems manage the timing and sequencing of cleaning cycles, control the flow rates and temperatures, and monitor the concentrations of cleaning agents.
- Sensors and Monitoring: Sensors are used to monitor critical parameters such as temperature, pressure, flow rate, and chemical concentration. Real-time monitoring allows for adjustments to be made during the cleaning process, ensuring optimal performance and compliance with hygiene standards.
- Data Logging and Reporting: Automation systems often include data logging capabilities, which record details of each cleaning cycle. This data helps validate cleaning processes, ensure compliance with regulatory requirements, and optimize system performance.
- Integration with Plant Systems: CIP systems can be integrated with the facility’s overall automation and control systems, allowing for centralized monitoring and control. This integration can enhance operational efficiency and provide a comprehensive view of the facility’s cleaning and production processes.
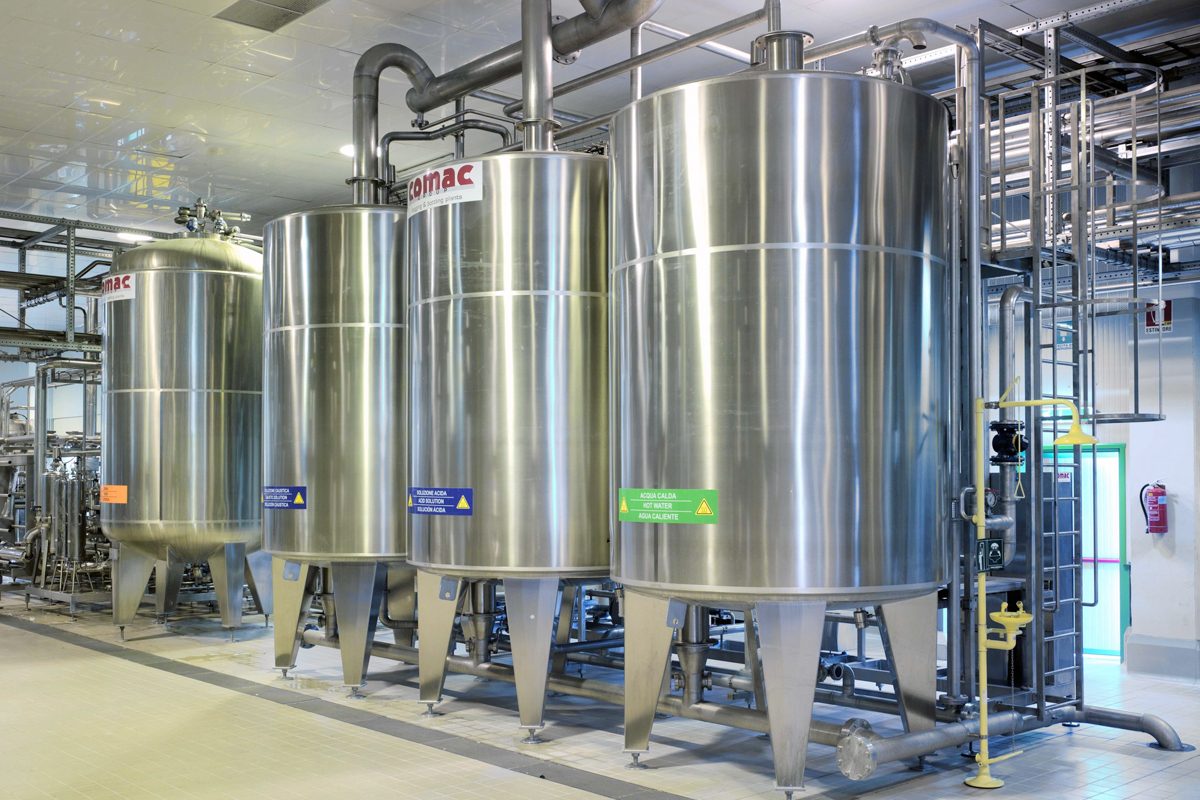
Best Practices for Implementing CIP Systems
Assess Cleaning Requirements
Before implementing a CIP system, it is crucial to conduct a thorough assessment of your facility’s specific cleaning requirements. This involves understanding the types of residues and soils that need to be removed, the equipment and surfaces involved, and the desired level of cleanliness.
- Identify Contaminants: Determine the nature of contaminants, such as organic residues, mineral deposits, or microbial contaminants. This will guide the selection of appropriate cleaning agents and processes.
- Set Cleaning Standards: Define the required cleanliness standards based on regulatory requirements and industry best practices. This includes determining acceptable levels of microbial contamination and residue presence.
- Frequency and Scope: Establish how often cleaning cycles need to be performed and which parts of the facility or equipment require CIP. This helps in designing a system that meets operational needs without unnecessary complexity.
Design for Flexibility
Flexibility in a CIP system design allows it to accommodate changes in production processes, product lines, and cleaning requirements. A flexible CIP system can adapt to different cleaning scenarios and future expansions.
- Modular Design: Consider a modular approach, where components such as tanks, pumps, and piping can be easily reconfigured or expanded. This design allows for adjustments as the facility’s needs evolve.
- Multiple Cleaning Programs: Implement a system capable of handling multiple cleaning programs with varying parameters such as temperature, flow rate, and chemical concentration. This capability is essential for facilities that produce a wide range of products or have different equipment types.
- Scalability: Ensure the system can scale up or down depending on production volume changes. This might involve designing for additional capacity or integrating with other systems.
Optimize Resource Usage
Optimizing the use of water, chemicals, and energy not only reduces operational costs but also supports environmental sustainability. An efficient CIP system conserves resources while maintaining effective cleaning.
- Water and Chemical Efficiency: Use sensors and control systems to accurately measure and control the amount of water and chemicals used. Implementing techniques such as counter-current rinsing can reduce water usage.
- Energy Management: Optimize heating and cooling processes to minimize energy consumption. Use energy-efficient equipment and consider recovering heat from hot rinse water for use elsewhere in the facility.
- Recycling and Reuse: Design the system to allow for the recycling and reuse of cleaning solutions where feasible. Implement filtration and treatment processes to maintain the quality of recycled solutions.
Regular Maintenance
Regular maintenance helps ensure your CIP system operates efficiently and reliably. Proactive maintenance can prevent system failures, ensure consistent cleaning performance, and extend the life of equipment.
- Scheduled Inspections: Conduct regular inspections of all CIP components, including tanks, pumps, valves, sensors, and piping. Look for signs of wear, corrosion, or buildup that could affect performance.
- Calibration and Validation: Regularly calibrate sensors and control systems to ensure accurate measurements of critical parameters. Validate the cleaning processes to verify they meet established standards and requirements.
- System Cleaning and Decontamination: Periodically perform thorough cleaning and decontamination of the CIP system itself to prevent cross-contamination and buildup of residues within the system.
Training and Education
Proper training and education aid in the successful operation and maintenance of a CIP system. All personnel involved in the cleaning process should be well-trained and knowledgeable about the system’s operation, safety protocols, and best practices.
- Operator Training: Provide comprehensive training for operators on the use of the CIP system, including starting and stopping procedures, setting parameters, and monitoring system performance.
- Safety Training: Educate staff on the safe handling of cleaning chemicals, emergency procedures, and the proper use of personal protective equipment (PPE). Emphasize the importance of safety in preventing accidents and exposures.
- Continuous Education: Offer ongoing education and training opportunities to keep staff updated on new technologies, regulatory changes, and improvements in cleaning processes. Encourage a culture of continuous improvement and knowledge sharing.
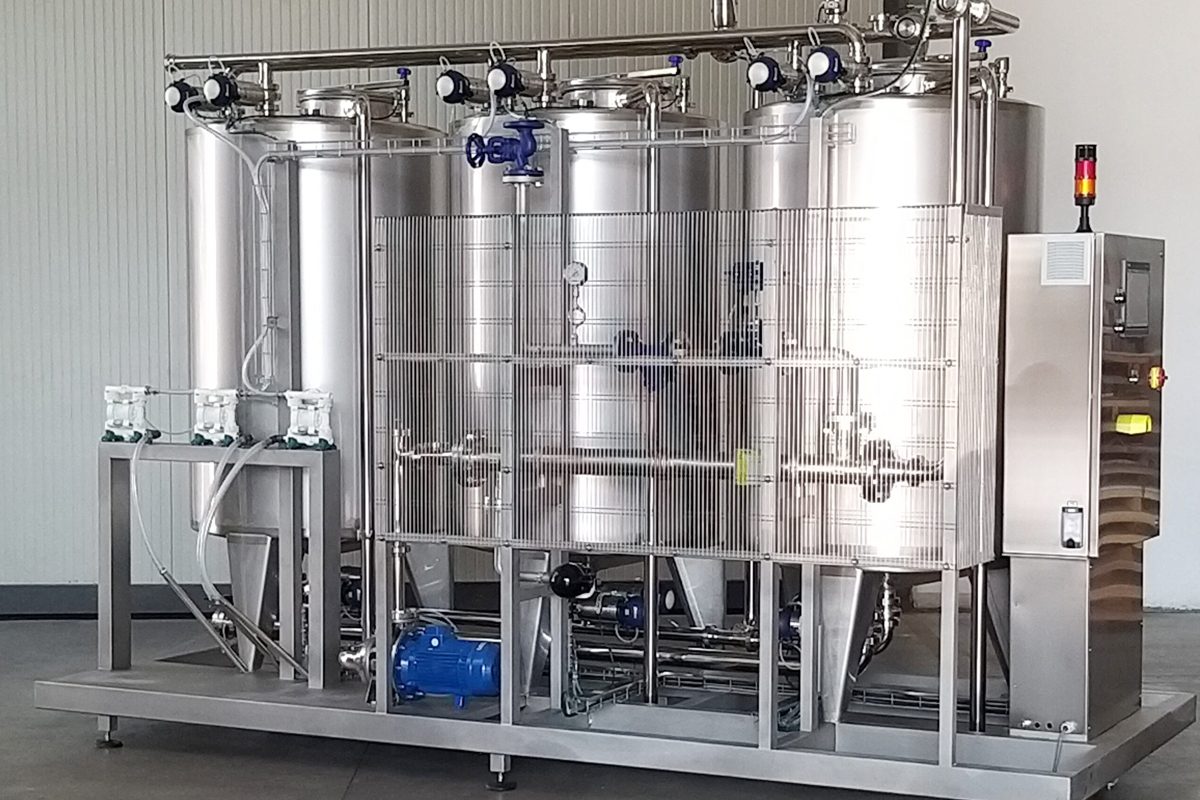
Summary
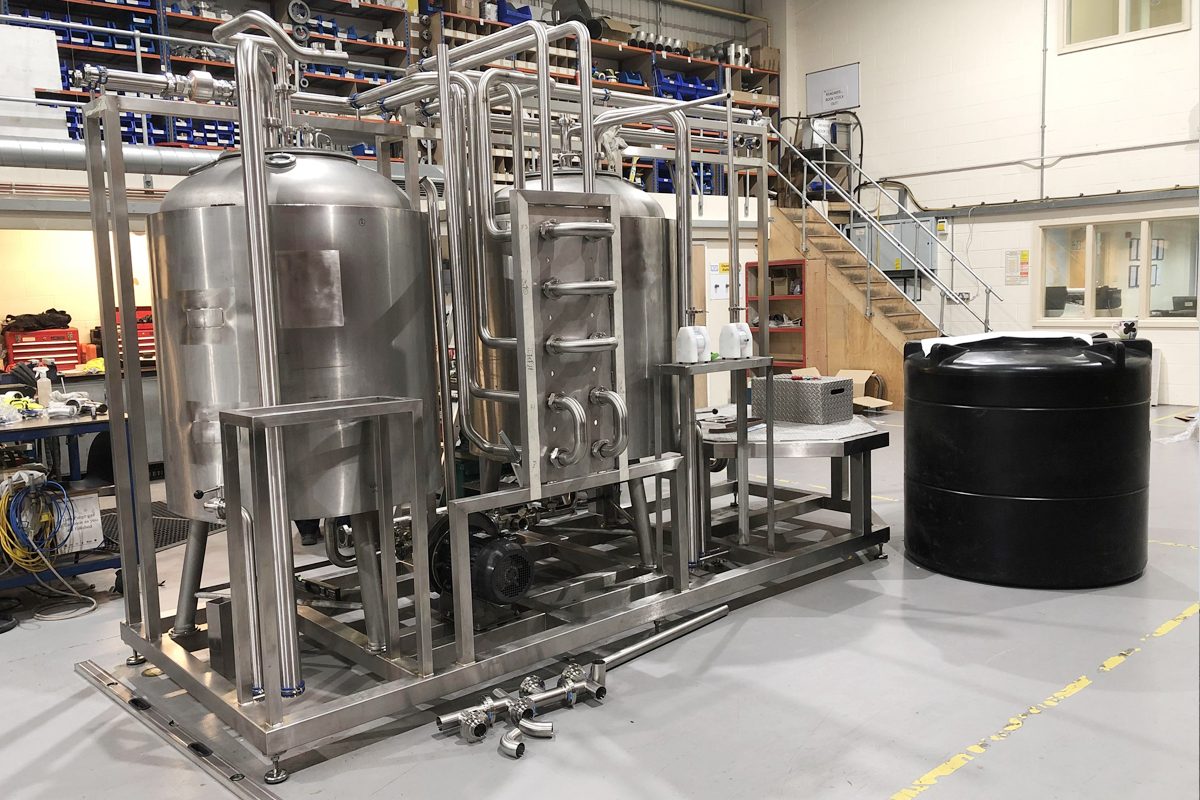