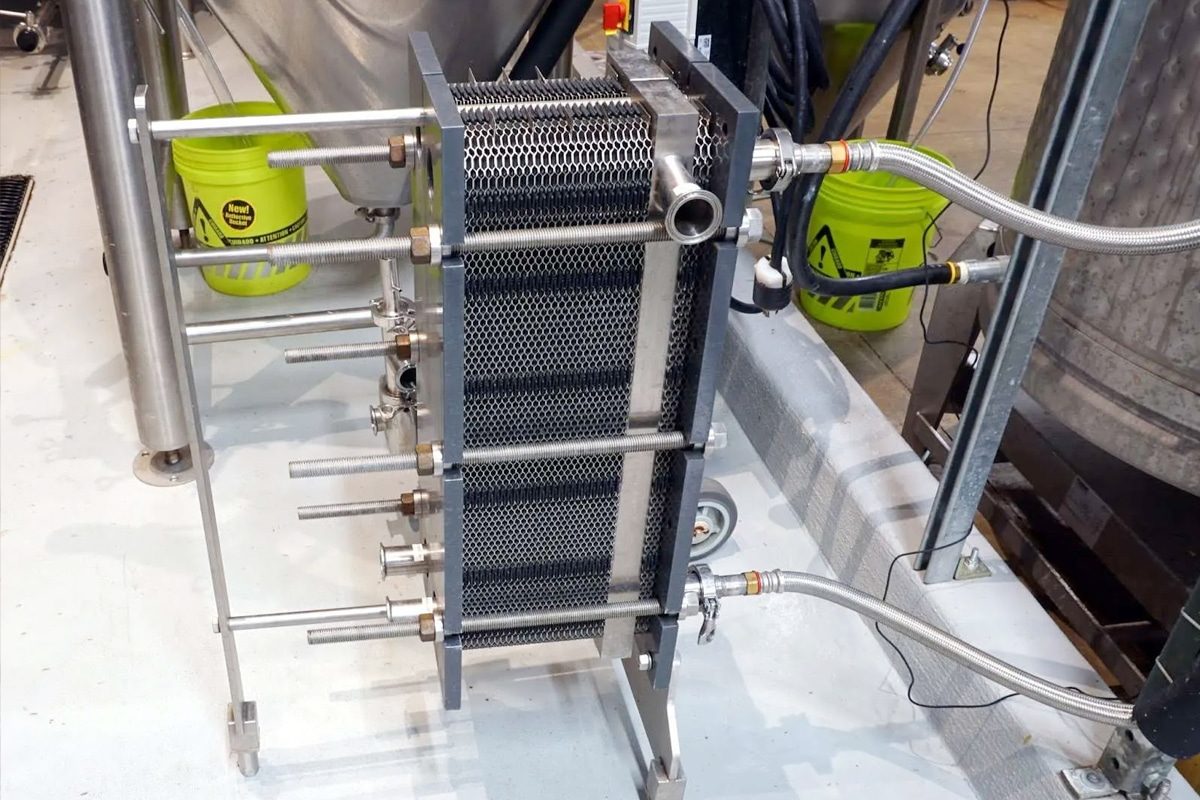
What Types of Heat Exchangers Are Used in Brewery?
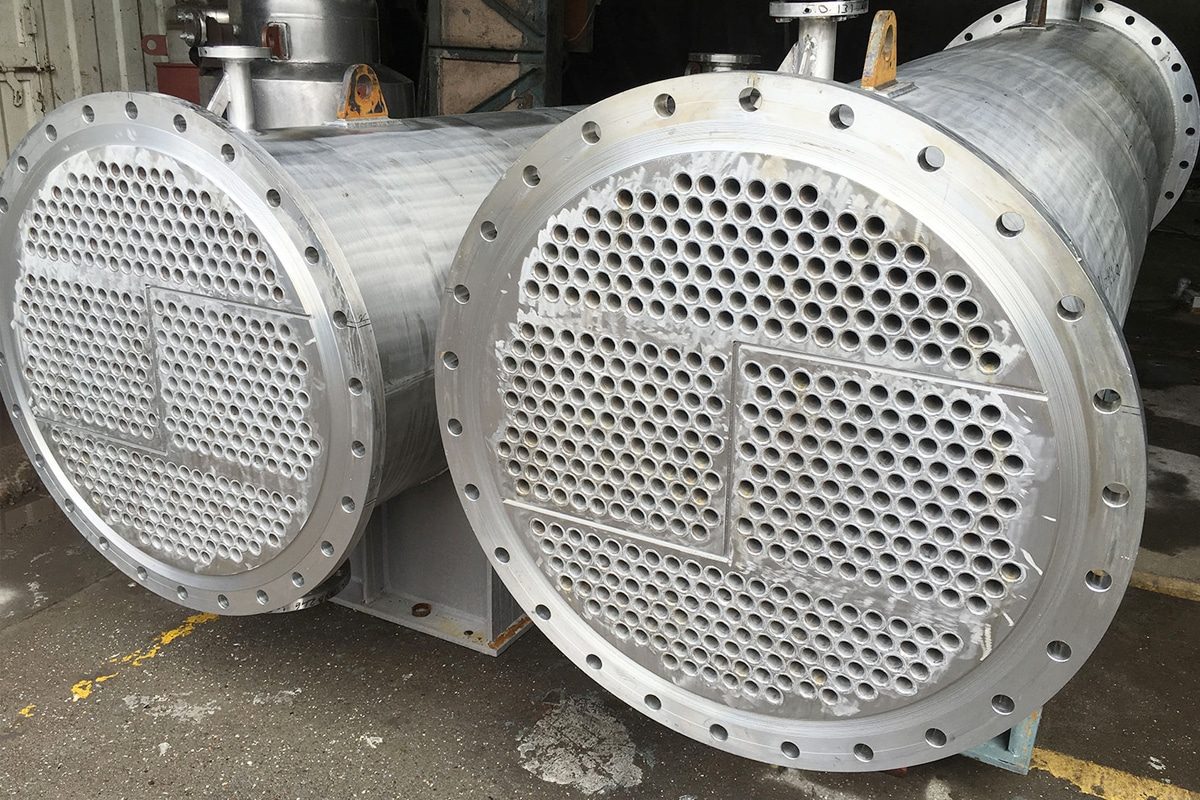
The Role of Heat Exchangers in Different Brewing Stages
Wort Cooling
Process Description
- Boiling Completion: After the wort is boiled, it needs to be cooled down from boiling temperatures (around 100°C) to the optimal fermentation temperature (typically between 15-20°C for ales and 10-15°C for lagers).
- Heat Exchanger Use: Plate heat exchangers are commonly used for this purpose due to their efficiency and compact design. The hot wort flows through the plates while cold water flows in the opposite direction, allowing heat to transfer from the wort to the water.
- Temperature Control: The cooled wort is then transferred to fermentation vessels, while the heated water can be reused elsewhere in the brewing process, enhancing energy efficiency.
Fermentation Temperature Control
Process Description
- Fermentation Vessels: Fermentation tanks are often equipped with cooling jackets through which a cooling fluid (usually glycol) circulates.
- Heat Exchanger Use: Shell and tube or plate heat exchangers are used to regulate the temperature of the glycol before it circulates through the cooling jackets.
- Temperature Monitoring: Continuous monitoring systems ensure that the fermentation temperature remains within the desired range, optimizing yeast performance and flavor development.
Heating Water for Mashing and Sparging
Mashing
- Process Description: During mashing, milled grains are mixed with hot water to convert starches into fermentable sugars. The temperature of the water (usually between 65-75°C) is crucial for enzymatic activity.
- Heat Exchanger Use: Shell and tube heat exchangers are typically used to heat the water to the precise temperature required for mashing.
Sparging
- Process Description: Sparging involves rinsing the grain bed with hot water to extract additional sugars after mashing.
- Heat Exchanger Use: Plate heat exchangers can be employed to heat the sparge water to the required temperature (usually around 77-79°C), ensuring efficient extraction of sugars from the grain bed.
Pasteurization
Process Description
- Flash Pasteurization: The beer is rapidly heated to a high temperature (usually around 72-75°C) for a short period and then quickly cooled.
- Heat Exchanger Use: Plate or tubular heat exchangers are often used for this purpose. The beer flows through the heat exchanger where it is heated to the pasteurization temperature and then immediately cooled.
- Energy Efficiency: The heat from the hot beer can be transferred to the incoming cold beer, making the process energy-efficient.
Cleaning and Sterilization
Process Description
- CIP (Clean-In-Place): CIP systems use heated cleaning solutions (such as caustic soda or acid) that are circulated through the equipment to remove residues and microbial contaminants.
- Heat Exchanger Use: Plate heat exchangers are commonly used to heat the cleaning solutions to the required temperatures (usually between 70-80°C).
- Sterilization: For sterilization, equipment may need to be exposed to even higher temperatures, which can be achieved using heat exchangers to heat water or steam.
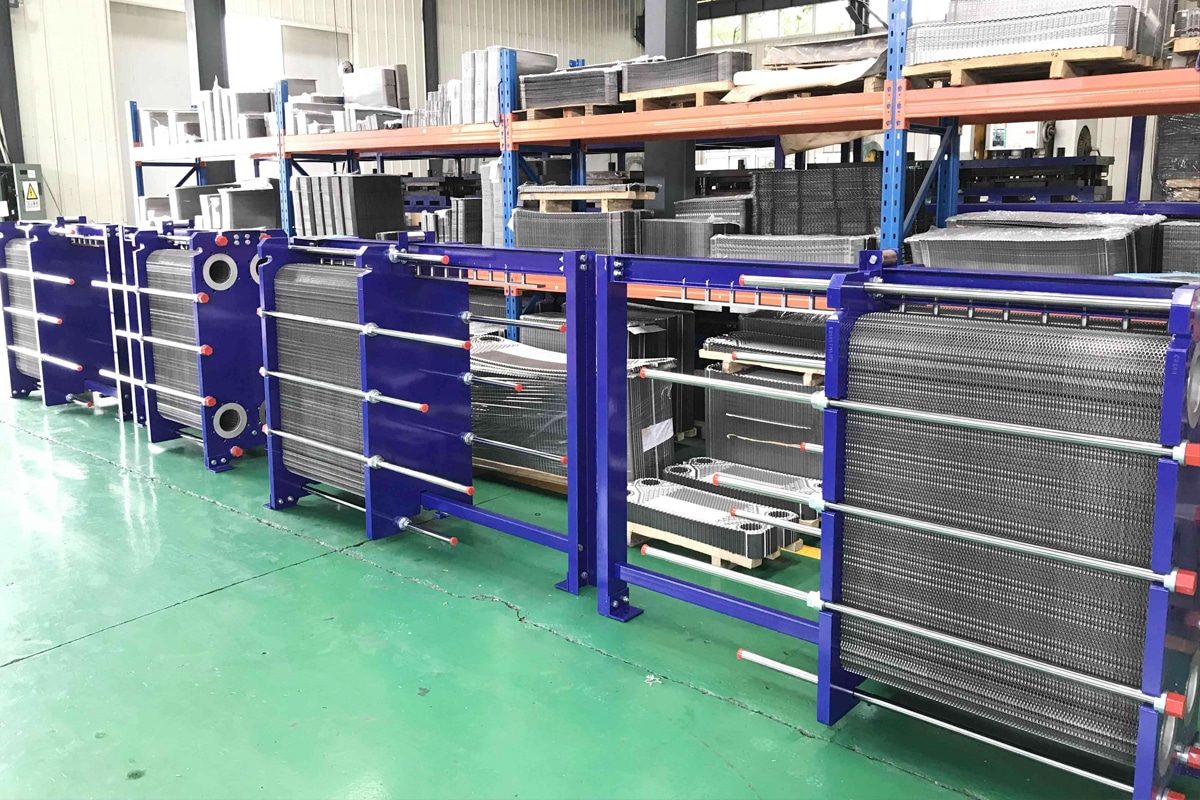
Types of Heat Exchangers in Breweries
Plate Heat Exchangers
Structure and Function
Applications in Brewing
- Wort Cooling: Rapid cooling of hot wort before fermentation.
- Heating and Cooling of Process Water: Temperature control of water used in various brewing stages.
Advantages
- High Efficiency: Large surface area provides excellent heat transfer rates.
- Compact Design: Takes up less space compared to other types of heat exchangers.
- Flexibility: Plates can be added or removed to adjust capacity.
- Easy Maintenance: Plates can be individually removed for cleaning and inspection.
Disadvantages
- Fouling: Narrow channels can be prone to fouling, reducing efficiency.
- Pressure Drop: High-pressure drops can occur due to the narrow flow paths.
Shell and Tube Heat Exchangers
Structure and Function
Applications in Brewing
- Heat Recovery: Recovery of heat from hot streams to preheat incoming cold fluids.
- Cooling Systems: Used in cooling systems for fermentation tanks and other brewing equipment.
Advantages
- Durability: Robust construction suitable for high-pressure applications.
- Versatility: Can handle a wide range of temperatures and pressures.
- Scalability: Easy to scale up by adding more tubes or using larger shells.
Disadvantages
- Size: Larger and heavier compared to other heat exchangers, requiring more space.
- Maintenance: More complex to clean and maintain due to the tube bundle configuration.
Double Pipe Heat Exchangers
Structure and Function
Applications in Brewing
- Small Batch Processes: Ideal for small-scale brewing operations or pilot plants.
- Supplementary Heating/Cooling: Used for additional heating or cooling needs.
Advantages
- Simple Design: Easy to construct and maintain.
- Cost-Effective: Lower initial cost compared to other heat exchangers.
- Flexibility: Can be used for both heating and cooling applications.
Disadvantages
- Limited Capacity: Suitable for smaller-scale operations due to limited heat transfer area.
- Efficiency: Less efficient than plate or shell and tube heat exchangers.
Immersion Coil Heat Exchangers
Structure and Function
Applications in Brewing
- Fermentation Temperature Control: Used to regulate temperatures in fermentation tanks.
- Heating and Cooling of Liquids: Direct heating or cooling of liquids in storage tanks.
Advantages
- Direct Contact: Efficient heat transfer due to direct contact between the coil and the fluid.
- Compact Design: This takes up less space as the coil is immersed in the fluid.
Disadvantages
- Maintenance: Difficult to clean the coils without removing them from the tank.
- Limited Applications: Primarily suitable for applications where the coil can be directly immersed.
Shell and Coil Heat Exchangers
Structure and Function
Applications in Brewing
- Heat Recovery: Recovery of heat from hot streams to preheat incoming fluids.
- Temperature Control: Used in cooling and heating systems for various brewing processes.
Advantages
- High Efficiency: The helical coil provides a large surface area for efficient heat transfer.
- Compact Design: More compact than shell and tube heat exchangers.
- Versatility: Suitable for a wide range of temperatures and pressures.
Disadvantages
- Cleaning Complexity: More challenging to clean due to the helical coil configuration.
- Pressure Drop: Higher pressure drops can occur, especially in long coils.
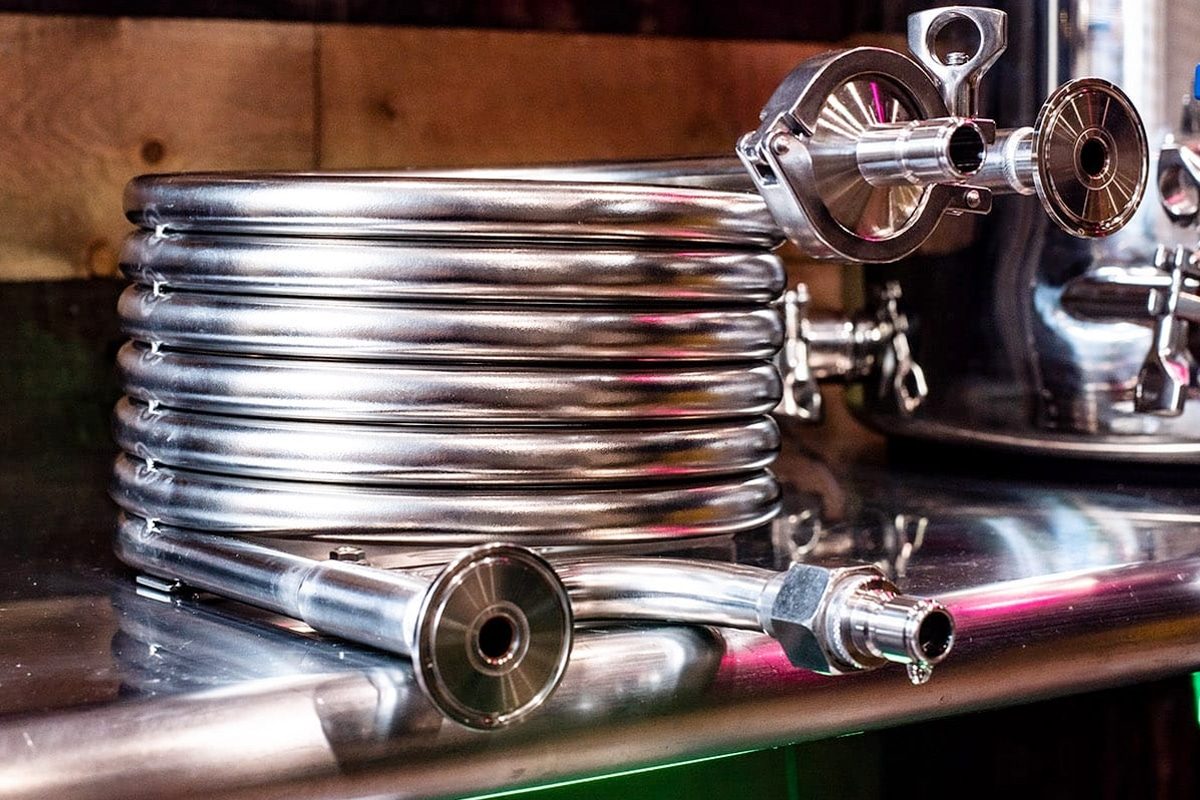
Factors Influencing the Choice of Heat Exchangers
Efficiency Requirements
Efficiency is a paramount consideration when selecting a heat exchanger, as it directly impacts the brewing process’s overall performance and energy consumption.
- Heat Transfer Efficiency: The ability of the heat exchanger to transfer heat from one fluid to another efficiently is crucial. Plate heat exchangers are known for their high heat transfer efficiency due to the large surface area of the plates.
- Energy Recovery: Efficient heat exchangers can recover and reuse heat within the process, such as using the heat from hot wort to preheat cold water, thereby reducing energy consumption and operational costs.
- Thermal Performance: The thermal performance should match the specific requirements of different brewing stages, such as rapid wort cooling or maintaining stable fermentation temperatures.
Scale of Operation
The scale of the brewery operation significantly influences the choice of heat exchanger.
- Small-Scale Breweries: Smaller operations may benefit from more compact and simpler designs like double pipe or immersion coil heat exchangers, which are cost-effective and easier to manage.
- Large-Scale Breweries: Larger operations typically require high-capacity heat exchangers like shell and tube or large plate heat exchangers to handle the significant volumes of fluids involved and ensure efficient heat transfer across multiple brewing stages.
Space Constraints
The physical space available in the brewery can limit the types of heat exchangers that can be installed.
- Compact Designs: Plate heat exchangers and immersion coil heat exchangers are generally more compact and suitable for breweries with limited space.
- Larger Footprints: Shell and tube heat exchangers, while efficient and versatile, typically require more space and may not be suitable for breweries with tight spatial constraints.
Temperature Requirements
Different brewing stages require precise temperature control, influencing the choice of heat exchanger based on its ability to achieve and maintain these temperatures.
- High-Temperature Applications: Processes like wort boiling and pasteurization require heat exchangers capable of handling high temperatures and significant temperature differences.
- Low-Temperature Applications: Cooling processes, such as wort cooling and fermentation temperature control, need heat exchangers that can efficiently operate at lower temperatures and provide rapid cooling.
Maintenance and Cleaning
Regular maintenance and cleaning can ensure the longevity and efficiency of heat exchangers in a brewery environment.
- Ease of Cleaning: Plate heat exchangers offer easy access to individual plates for cleaning and maintenance, which is beneficial in preventing fouling and maintaining efficiency.
- Maintenance Complexity: Shell and tube and shell and coil heat exchangers may require more complex maintenance procedures due to their design, which can complicate cleaning operations.
Cost Considerations
Cost is a critical factor that includes both the initial investment and the ongoing operational costs of the heat exchanger.
- Initial Investment: The upfront cost of heat exchangers varies, with plate heat exchangers generally being more expensive initially but offering high efficiency and ease of maintenance.
- Operational Costs: Efficient heat exchangers can reduce energy costs over time by improving heat recovery and reducing the need for additional heating or cooling.
- Total Cost of Ownership: It’s important to consider the total cost of ownership, including maintenance, repairs, and energy consumption, rather than just the initial purchase price.
Material Compatibility
The materials used in the construction of heat exchangers must be compatible with the brewing fluids to prevent contamination and ensure durability.
- Corrosion Resistance: Stainless steel is commonly used in brewery heat exchangers due to its excellent corrosion resistance and compatibility with brewing ingredients.
- Durability: The materials should withstand the operational conditions of the brewery, including temperature fluctuations and potential chemical exposure during cleaning processes.
- Food Safety: Materials must comply with food safety regulations to ensure that no harmful substances leach into the beer during the brewing process.
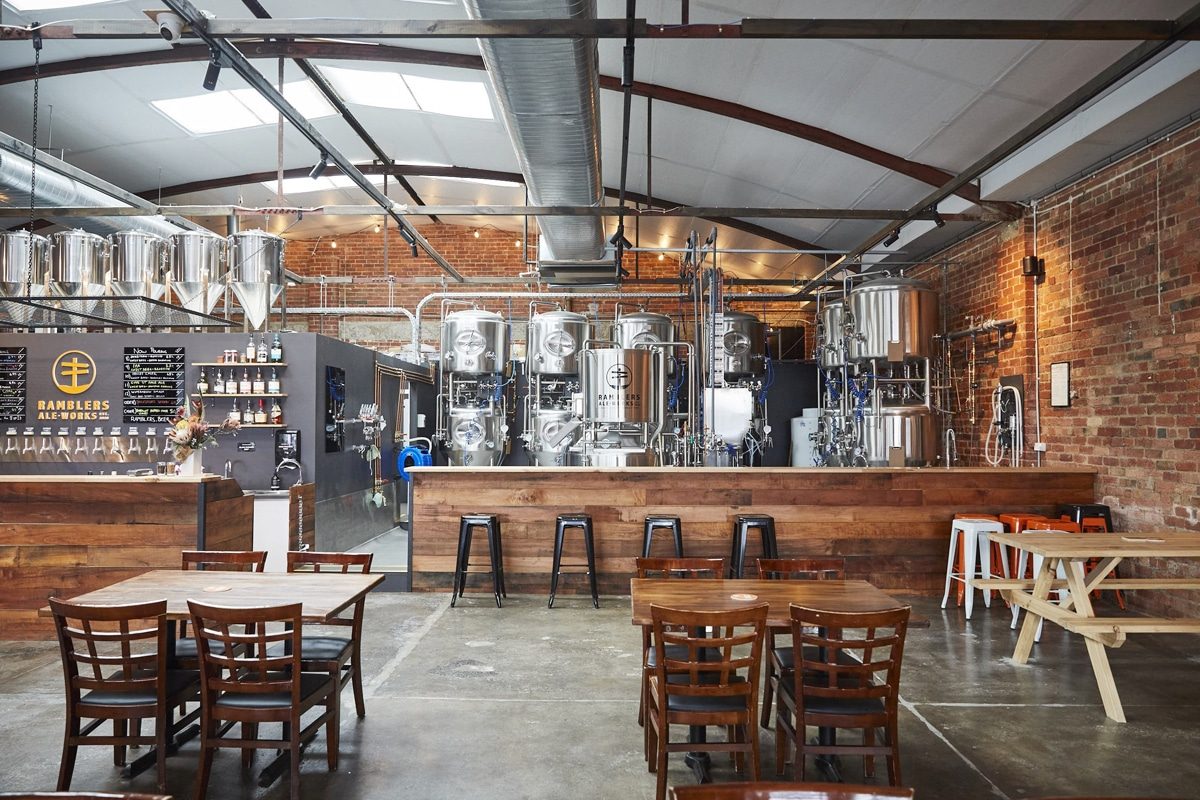
Summary
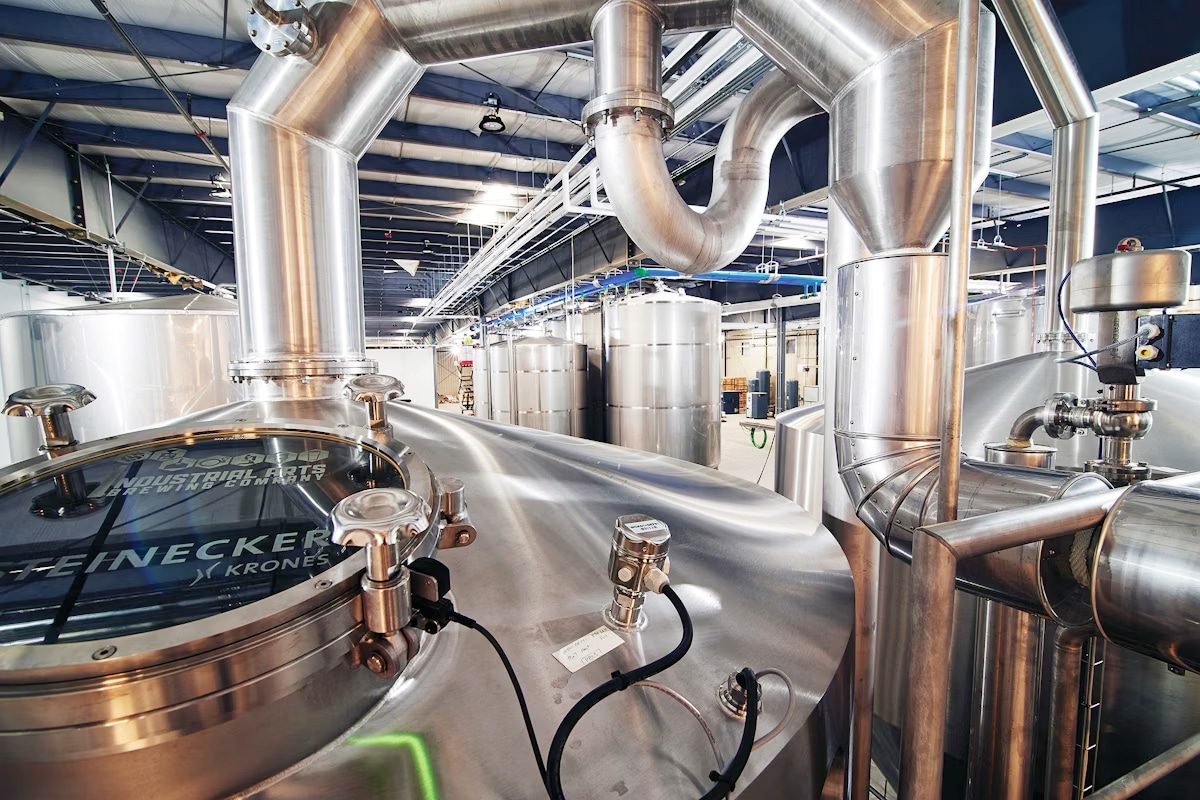