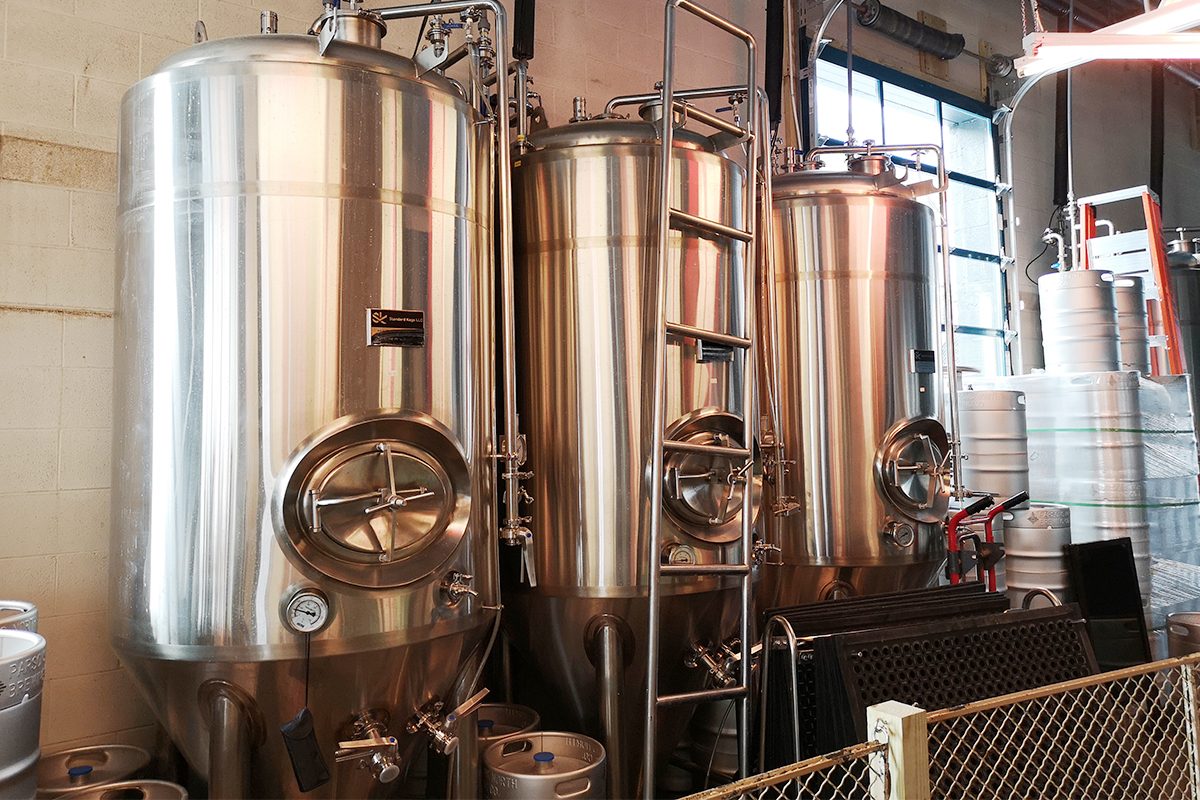
What Is The Role of Cooling Jackets in Fermentation Tanks?
In the brewing process, temperature control is a critical factor that directly influences the quality and consistency of the final product. Fermentation, where yeast converts sugars into alcohol, generates heat as a by-product. This heat can lead to undesirable flavors, stalled fermentation, or even spoiled batches if not managed properly. Integrated into fermentation tanks, cooling jackets play a vital role in regulating temperature by dissipating excess heat and maintaining the optimal environment for yeast activity. This article explores the role of cooling jackets in fermentation tanks, highlighting their function, benefits, and impact on the brewing process.
Complete Guide
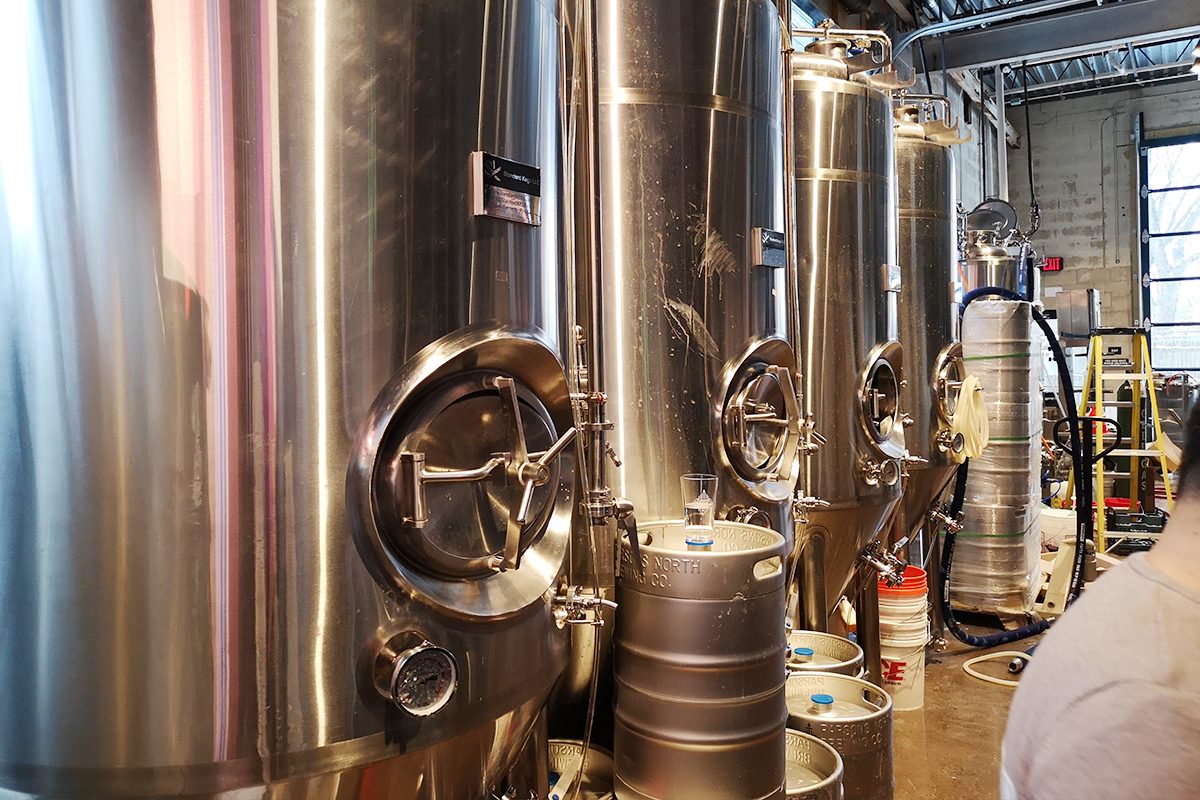
Introduction to Fermentation and Temperature Control
The fermentation is a critical phase where yeast converts fermentable sugars into alcohol, carbon dioxide, and various flavor compounds that define the character of the beer. This biochemical process is highly sensitive to temperature, with even slight variations capable of significantly altering the final product’s taste, aroma, and quality. Proper temperature control during fermentation ensures that the yeast remains active and healthy, helping to achieve a consistent and efficient fermentation process.
Temperature influences yeast metabolism, impacting the production of alcohol and other by-products such as esters, phenols, and higher alcohols. For instance, cooler temperatures tend to produce cleaner, crisper flavors, typical of lagers, while warmer temperatures encourage the development of fruity and spicy notes, often found in ales. Without adequate temperature control, undesirable flavors can emerge, and fermentation may become unpredictable, leading to inconsistent batches.
To address these challenges, professional brewery solution providers like ZYB Craft emphasize the importance of temperature regulation systems, particularly cooling jackets in fermentation tanks. The cooling jacket maintains the precise temperature required for optimal fermentation, ensuring the yeast is operating within the ideal range. By dissipating excess heat generated during fermentation, cooling jackets help maintain a stable environment, allowing brewers to produce high-quality, consistent beer batch after batch.
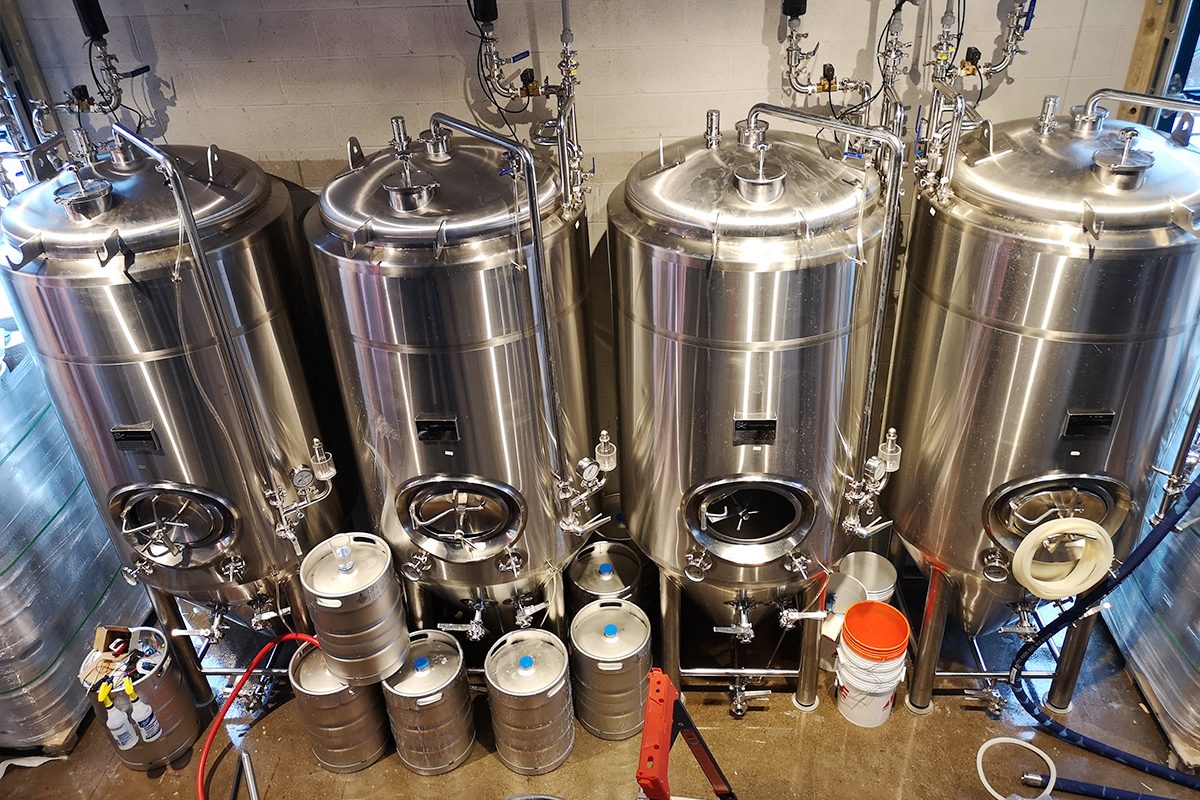
What Are Cooling Jackets
Cooling jackets are essential components integrated into the design of fermentation tanks, particularly in professional brewing environments. These jackets are typically made of stainless steel and consist of a double-walled structure that surrounds the tank. The space between the inner and outer walls forms a channel through which a cooling medium, such as glycol or chilled water, is circulated. This system allows for precise control of the temperature inside the tank, ensuring that the fermentation process occurs under optimal conditions.
The primary function of cooling jackets is to regulate the temperature within the fermentation tank by removing excess heat generated during the fermentation process. As yeast ferments sugar into alcohol, it produces heat as a by-product. Without proper temperature management, this heat can cause the fermentation to become too vigorous, leading to undesirable flavors, off-aromas, and even the risk of yeast stress or death. Cooling jackets help maintain a stable temperature, providing a consistent environment for yeast to thrive and perform its function efficiently.
There are various designs of cooling jackets, including dimpled jackets, which create small channels for the cooling medium to flow through, and serpentine coils, which provide localized cooling by circulating the medium through coiled tubes. Each design offers different levels of cooling efficiency, allowing brewers to choose the system that best suits their specific needs.
Understanding the function and benefits of cooling jackets can help design fermentation tanks to provide a high-quality fermentation system. By integrating effective cooling solutions, ZYB Craft helps brewers achieve consistent results, optimize fermentation, and produce beer that meets the highest standards of quality.
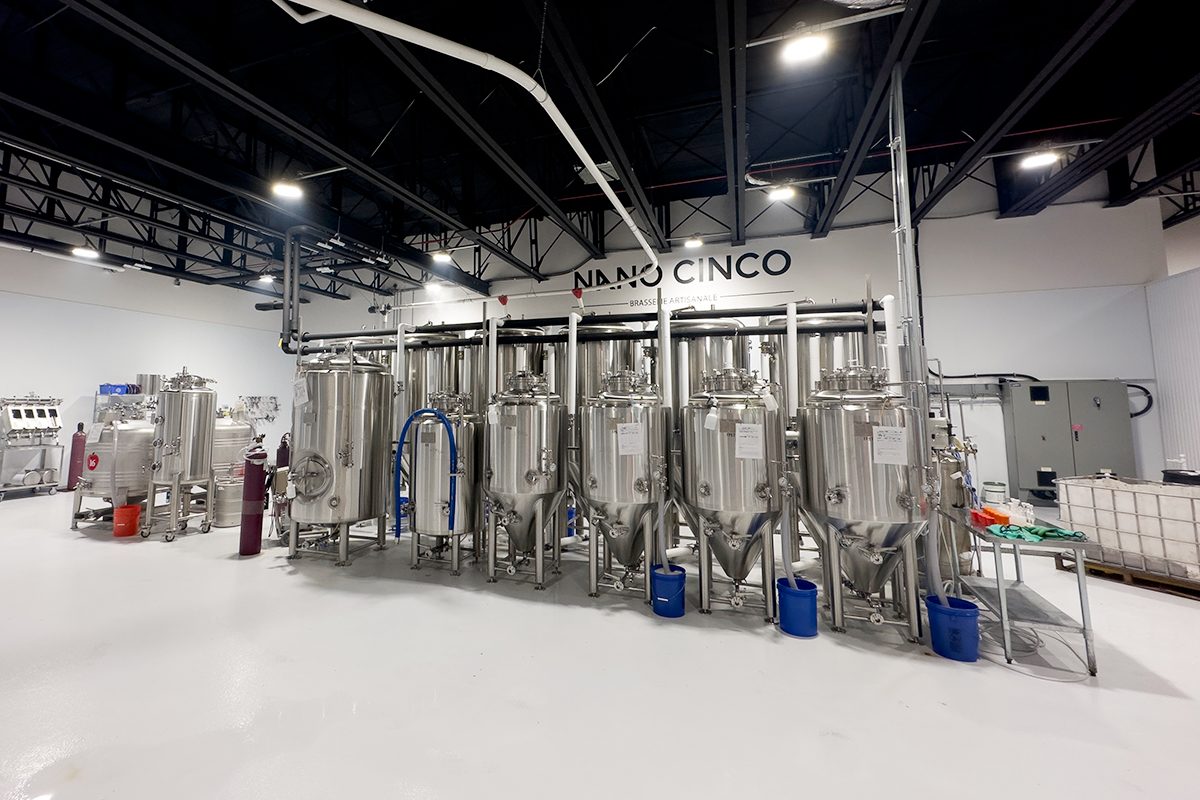
How Cooling Jackets Work
Cooling jackets operate by circulating a cooling medium, typically glycol or chilled water, through a network of channels or coils embedded within the tank’s exterior walls. The cooling medium absorbs excess heat generated during fermentation and dissipates it, maintaining the fermenting liquid at the desired temperature. This process is crucial because fermentation naturally produces heat, and without proper cooling, temperatures can rise to levels that adversely affect yeast performance and the quality of the final product.
Key Components of Cooling Jacket Systems
- Cooling Medium: The cooling medium is the substance that flows through the jacket’s channels to absorb and carry away heat. Glycol, mixed with water, is commonly used due to its low freezing point and efficiency in maintaining a stable temperature. Chilled water is another option, particularly in systems where the fermentation temperature is above the freezing point of water.
- Circulation System: A circulation system is essential for moving the cooling medium through the jacket. This typically includes a pump that drives the cooling medium from a central cooling source, such as a glycol chiller or refrigeration unit, through the jacket and back to the cooling source. Continuous circulation ensures that heat is consistently removed from the fermentation tank.
- Temperature Sensors: Temperature sensors are strategically placed inside the fermentation tank to monitor the temperature of the fermenting liquid in real time. These sensors are connected to a control system, providing data that helps regulate the flow of the cooling medium to maintain the desired temperature.
- Control System: The control system is the brain of the cooling jacket operation. It interprets data from the temperature sensors and adjusts the flow of the cooling medium accordingly. Advanced control systems are often automated, allowing for precise and consistent temperature management without the need for manual intervention. This is particularly beneficial in large-scale operations where maintaining a consistent fermentation temperature is crucial.
Understanding how a cooling jacket works allows for the design of a fermentation system that meets the specific needs of each brewing operation. By integrating an effective cooling solution, breweries are able to achieve precise temperature control, optimize fermentation, and consistently produce high-quality beer.
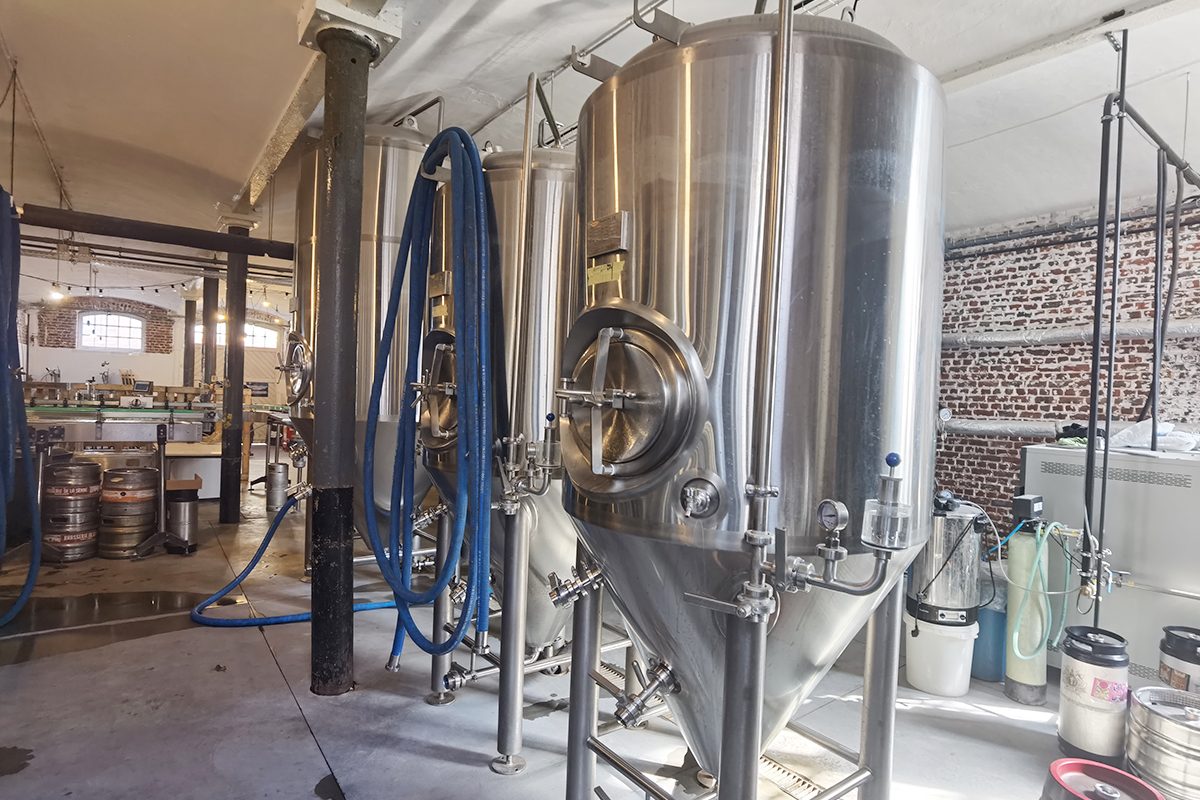
Types of Cooling Jackets
Cooling jackets come in various designs, each tailored to meet the specific needs of different fermentation processes. Understanding the types of cooling jackets available can help brewers optimize temperature control and ensure consistent, high-quality brewing results. Below are the most common types of cooling jackets used in fermentation tanks:
Dimpled Jackets
- Design: Dimpled jackets are among the most popular types of cooling jackets used in fermentation tanks. They feature a double-wall construction with a series of small, round indentations or dimples pressed into the stainless steel surface. These dimples create pockets that allow the cooling medium to flow evenly across the tank’s surface.
- Advantages: The primary benefit of dimpled jackets is their ability to provide uniform cooling across the entire surface of the tank. This design ensures that heat is dissipated efficiently, maintaining a consistent temperature throughout the fermentation process. Dimpled jackets are highly durable, easy to clean, and suitable for both small and large-scale fermentation tanks.
- Applications: Dimpled jackets are widely used in commercial breweries where precise temperature control is critical. They are ideal for maintaining the consistent temperature needed for large batches of beer, ensuring uniformity and quality.
Serpentine Coils
- Design: Serpentine coils consist of flexible, tubular coils that are wrapped around the exterior or interior of the fermentation tank. These coils circulate the cooling medium directly through them, allowing for localized cooling of the fermenting liquid.
- Advantages: Serpentine coils offer versatility in installation and can be easily adapted to tanks of various shapes and sizes. They provide targeted cooling, making them especially useful in tanks with irregular shapes or when specific areas of the tank require more cooling than others. They are also relatively easy to retrofit into existing tanks.
- Applications: Serpentine coils are often used in smaller breweries or for specialized fermentations where precision cooling is required. They are a cost-effective option for brewers looking to upgrade their fermentation systems without investing in entirely new tanks.
Full Immersion Jackets
- Design: Full immersion jackets cover the entire surface area of the fermentation tank, providing maximum contact between the cooling medium and the tank wall. This design ensures the most efficient and comprehensive cooling possible.
- Advantages: Full immersion jackets offer unparalleled temperature control, making them ideal for large-scale operations where maintaining a consistent fermentation temperature is essential. This type of cooling jacket is particularly effective in preventing temperature gradients within the tank, ensuring that the entire volume of liquid is kept at a uniform temperature.
- Applications: Full immersion jackets are commonly used in large breweries, distilleries, and wineries, where precision and consistency are paramount. These jackets are ideal for high-capacity fermentation tanks and are often part of sophisticated, automated temperature control systems.
External Panel Jackets
- Design: External panel jackets are flat, external plates that are welded or clamped onto the outer surface of the fermentation tank. These plates are designed to channel the cooling medium across the surface of the tank, offering a different approach to cooling compared to dimpled jackets or serpentine coils.
- Advantages: External panel jackets provide a larger cooling surface area, making them highly efficient for large tanks. They are also relatively easy to install and maintain, offering a practical solution for brewers looking to enhance their existing fermentation systems. Additionally, their design allows for easy access to the tank’s interior for cleaning and maintenance.
- Applications: External panel jackets are often used in industrial-scale breweries and wineries, where large volumes of liquid require precise temperature control. Their robust design makes them suitable for long-term use in demanding production environments.
Modular Cooling Jackets
- Design: Modular cooling jackets are composed of multiple interconnected panels or segments that can be easily installed or removed as needed. This modularity allows brewers to customize the cooling capacity of their tanks according to the specific requirements of each fermentation process.
- Advantages: The primary advantage of modular cooling jackets is their flexibility. Brewers can adjust the number of panels or segments to achieve the desired level of cooling, making these jackets ideal for operations with varying batch sizes or production scales. They are also easier to repair or replace than traditional, single-piece jackets.
- Applications: Modular cooling jackets are particularly useful in craft breweries or experimental brewing facilities where batch sizes and fermentation requirements may frequently change. They offer a versatile and scalable solution for temperature control.
Understanding the different types of cooling jackets can help provide a customized solution that meets the different needs of brewers. Whether optimizing temperature control for a small craft brewery or a large industrial operation, selecting the appropriate type of cooling jacket ensures that the fermentation process runs smoothly, leading to consistent, high-quality beer.
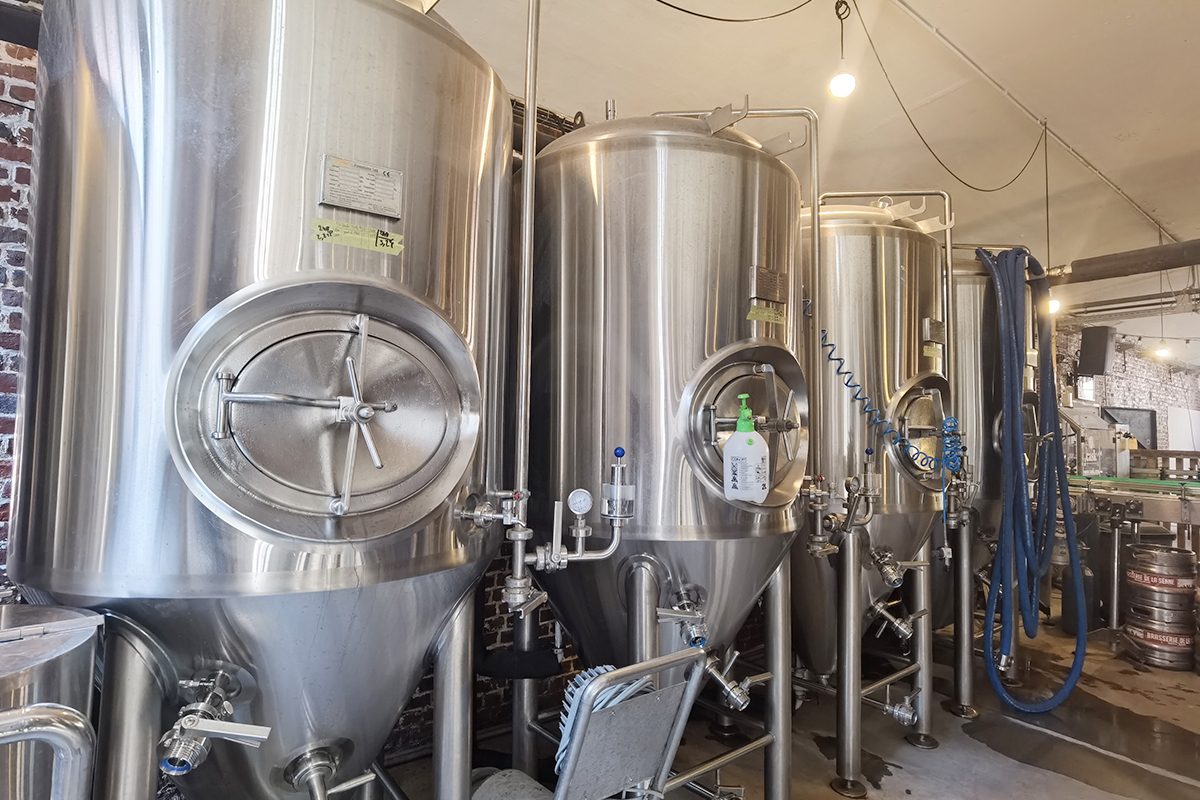
Design Considerations for Cooling Jackets
When designing cooling jackets for fermentation tanks, several critical factors must be considered to ensure optimal performance and efficiency.
Tank Size and Shape
The size and shape of the fermentation tank significantly influence the design of the cooling jacket. Larger tanks require more extensive cooling surfaces to manage the greater volume of liquid and the associated heat generated during fermentation. The shape of the tank, whether cylindrical, conical, or irregular, also affects how the cooling jacket is applied. For instance, conical fermenters often require jackets that cover both the sides and the cone to ensure even temperature distribution throughout the entire tank.
Cooling Medium
Choosing the appropriate cooling medium is a key consideration. Glycol-water mixtures are commonly used due to their efficiency in absorbing heat and their ability to remain in a liquid state at lower temperatures. The cooling medium’s properties will determine the flow rate and the cooling system’s overall efficiency. It’s important to select a medium that is compatible with the specific fermentation temperature range required by the brewing process.
Jacket Configuration
Different jacket configurations offer varying levels of cooling efficiency and control. Dimple jackets provide a uniform cooling surface, making them ideal for large tanks, while serpentine coils offer more localized cooling, which can be advantageous in smaller or irregularly shaped tanks. The choice of configuration should align with the brewery’s specific cooling needs, the desired level of control, and the tank’s physical characteristics.
Insulation
Proper insulation of the fermentation tank helps increase the effectiveness of the cooling jacket. Insulation helps prevent external heat from affecting the fermentation temperature and reduces the cooling system’s workload. When designing the cooling jacket, it’s important to ensure that the tank is adequately insulated, particularly in environments where ambient temperatures fluctuate significantly.
Flow Rate and Distribution
The flow rate of the cooling medium through the jacket must be carefully calibrated to match the heat load generated by the fermentation process. An insufficient flow rate can lead to hot spots within the tank, while an excessive flow rate can result in unnecessary energy consumption. The distribution of the cooling medium should also be even across the entire jacket to avoid temperature gradients that could impact the consistency of the fermentation.
Temperature Control Systems
The integration of advanced temperature control systems allows precise management of the fermentation process. Automated control systems that monitor and adjust the temperature in real time offer significant advantages in maintaining consistent fermentation conditions. These systems should be designed to work seamlessly with the cooling jacket, ensuring that any temperature fluctuations are quickly corrected.
Maintenance and Accessibility
Maintenance needs to be considered when designing cooling jackets to improve long-term reliability and efficiency. The system should be easy to clean, inspect, and repair without requiring extensive downtime. Features such as removable panels or access points for inspection can greatly facilitate routine maintenance and help prevent potential issues from escalating.
Scalability and Flexibility
Breweries often expand their production capacity over time, so scalability is an important consideration in the design of cooling jackets. Modular designs that allow for easy expansion or reconfiguration can provide flexibility for future growth. Additionally, the system should be adaptable to different types of fermentation processes, offering versatility for brewers who may produce a variety of beer styles.
Energy Efficiency
Energy efficiency is a major concern in the design of cooling jackets, especially for large-scale operations. The system should be designed to minimize energy consumption while maximizing cooling performance. This can be achieved through the selection of efficient pumps, the use of advanced control systems, and the optimization of the jacket’s thermal conductivity.
Compliance with Industry Standards
Cooling jackets must be designed in compliance with industry standards and regulations, particularly those related to food safety and hygiene. Materials used in the construction of the jackets should be food-grade and resistant to corrosion. The design should also facilitate easy cleaning and sterilization to prevent contamination and ensure that the fermentation process meets the highest standards of quality.
Considering these design factors can help create a cooling jacket system that provides precise temperature control, energy efficiency, and long-term reliability. By carefully addressing each of these aspects, ZYB Craft can provide brewers with customized solutions that enhance the fermentation process and contribute to the consistent production of high-quality beer.
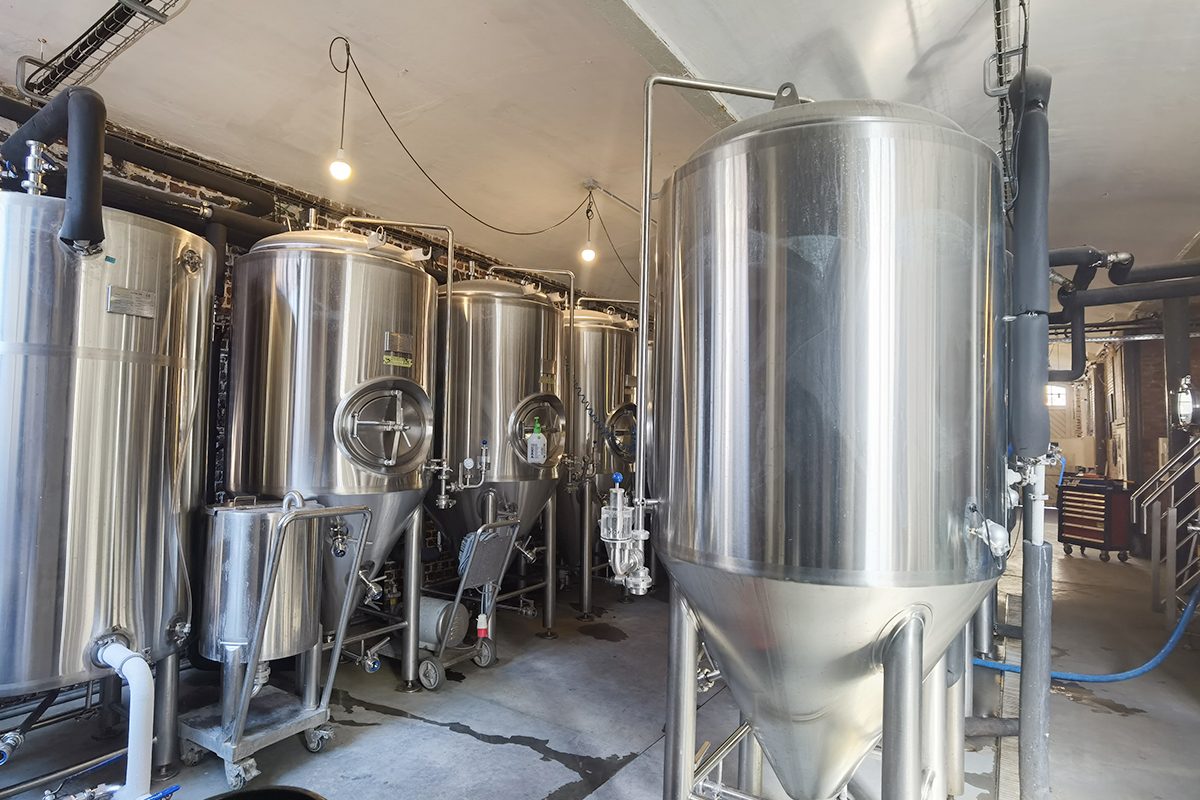
Advantages of Using Cooling Jackets
Cooling jackets are an indispensable component in modern fermentation tanks, providing brewers with the ability to precisely control the fermentation environment. Here are the key advantages of using cooling jackets in fermentation tanks:
Precise Temperature Control
Cooling jackets allow brewers to maintain the exact temperature required for optimal yeast performance during fermentation. By circulating a cooling medium through the jacket, brewers can dissipate excess heat generated during the fermentation process, keeping the temperature within a narrow, controlled range. This precision can help produce consistent, high-quality beer, as even small temperature changes can significantly affect the flavor, aroma, and overall character of the final product.
Enhanced Yeast Performance
Yeast health and activity are directly influenced by the fermentation temperature. Cooling jackets ensure that the temperature remains within the yeast’s optimal range, promoting healthy fermentation and preventing issues such as off-flavors, incomplete fermentation, or yeast stress. This results in more efficient sugar conversion and a cleaner, more desirable flavor profile in the beer.
Consistency Across Batches
For commercial breweries, consistency is key to maintaining product quality and customer satisfaction. Cooling jackets help ensure that each batch of beer is fermented under identical conditions, minimizing variations between batches. This uniformity is essential for brands that rely on producing the same high-quality product every time, regardless of production scale.
Energy Efficiency
Cooling jackets are an energy-efficient solution for temperature control in fermentation tanks. Unlike air conditioning or refrigeration systems that cool the entire space, cooling jackets target only the fermentation tank, reducing energy consumption. This localized cooling approach minimizes energy waste and lowers operational costs, making it a cost-effective solution for breweries of all sizes.
Versatility and Flexibility
Cooling jackets can be customized to fit tanks of various sizes and shapes, offering flexibility for different brewing setups. Whether a brewery operates small-scale craft fermenters or large industrial tanks, cooling jackets can be designed to meet specific requirements. This adaptability makes them suitable for a wide range of fermentation processes, from ales and lagers to specialty beers that require precise temperature control.
Improved Product Quality
By maintaining a stable and controlled fermentation environment, cooling jackets contribute to the overall quality of the beer. They help prevent the formation of undesirable by-products, such as diacetyl and fusel alcohols, which can negatively impact the taste and aroma of the beer. With proper temperature control, brewers can achieve the desired flavor profile and consistency, resulting in a superior final product.
Reduced Risk of Contamination
Cooling jackets, being an external temperature control solution, do not come into direct contact with the fermenting liquid. This reduces the risk of contamination, as the cooling medium is contained within the jacket’s channels. The design of cooling jackets also facilitates easy cleaning and sanitization, further minimizing the potential for microbial contamination and ensuring the safety and purity of the beer.
Scalability
As breweries grow and expand their production capacities, cooling jackets offer scalability to meet increased demands. Modular cooling jacket systems can be easily adapted or expanded to accommodate larger tanks or additional fermentation vessels. This level of control can help produce complex and high-quality beers that require specific fermentation conditions.
Optimized Fermentation Control
Cooling jackets provide brewers with greater control over the entire fermentation process. From the initial temperature ramp-up to the final conditioning phase, cooling jackets allow for precise adjustments to maintain the desired temperature profile. This level of control is especially important for producing complex and high-quality beers that require specific fermentation conditions.
Sustainability and Environmental Impact
By reducing energy consumption and improving process efficiency, cooling jackets contribute to the sustainability of brewing operations. Lower energy usage not only cuts costs but also reduces the brewery’s carbon footprint, making cooling jackets an environmentally friendly solution. This aligns with the growing demand for sustainable practices in the brewing industry and helps breweries meet their sustainability goals.
For ZYB Craft, understanding the advantages of using cooling jackets in fermentation tanks is crucial for providing brewers with solutions that enhance their operations. From precise temperature control and improved product quality to energy efficiency and scalability, cooling jackets offer numerous benefits that contribute to the success and sustainability of modern breweries. By integrating these systems into their brewing setups, ZYB Craft’s clients can achieve consistent, high-quality results, ensuring their beer meets the highest standards with every batch.
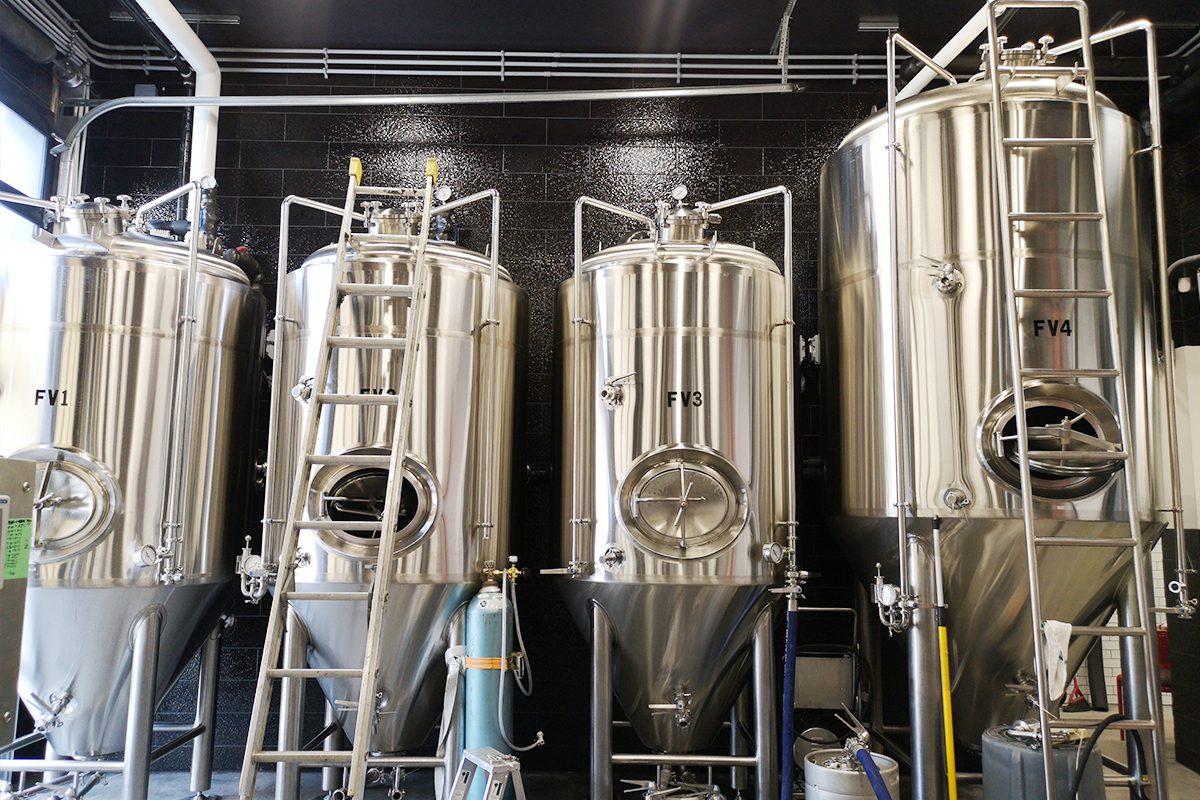
Challenges and Considerations
When implementing cooling jackets in fermentation tanks, several challenges and considerations must be addressed to ensure optimal performance and efficiency. Here are the key challenges and considerations:
Initial Cost and Installation
One of the primary challenges of incorporating cooling jackets into fermentation tanks is the initial cost. High-quality cooling jackets, especially those designed for large or custom tanks, can represent a significant investment. Additionally, the installation process can be complex, particularly in existing facilities where retrofitting may be required. The cost and complexity of installation must be carefully weighed against the long-term benefits of improved temperature control and product consistency.
Maintenance Requirements
Cooling jackets require regular maintenance to ensure they function efficiently. This includes checking for leaks, monitoring the performance of the circulation system, and ensuring that the temperature control system is calibrated correctly. Neglecting maintenance can lead to issues such as reduced cooling efficiency, hot spots within the tank, or even system failures. Breweries must be prepared to invest time and resources into maintaining their cooling jacket systems to avoid these problems.
Compatibility with Fermentation Tanks
Not all fermentation tanks are immediately compatible with cooling jackets. In some cases, modifications may be necessary to ensure that the jacket fits properly and functions as intended. For example, older tanks or those made from materials other than stainless steel may require additional work to accommodate a cooling jacket. This can increase the overall cost and complexity of the system, so compatibility needs to be considered during the planning phase.
Energy Consumption
While cooling jackets are generally more energy-efficient than other temperature control methods, they still require a significant amount of energy to operate, particularly in large-scale operations. The energy consumption of the cooling system is influenced by factors such as the size of the tank, the temperature differential that needs to be maintained, and the efficiency of the cooling medium. Breweries need to carefully consider the energy requirements of their cooling jackets to ensure that they do not inadvertently increase their operational costs or environmental impact.
Temperature Control Challenges
Achieving precise temperature control can be challenging, particularly in larger tanks or when dealing with complex fermentation processes. Factors such as uneven cooling distribution, variations in the flow rate of the cooling medium, and external temperature fluctuations can all impact the effectiveness of the cooling jacket. Breweries must ensure that their temperature control systems are sophisticated enough to manage these variables and maintain a consistent fermentation temperature.
Impact on the Fermentation Process
While cooling jackets are designed to enhance the fermentation process, they can also introduce potential challenges if not properly managed. For example, overly aggressive cooling can cause the temperature to drop too quickly, shocking the yeast and potentially halting fermentation. Conversely, insufficient cooling can lead to overheating and the production of off-flavors. Brewers need to carefully monitor and adjust the cooling process to avoid these issues and ensure that fermentation proceeds smoothly.
System Scalability
As breweries grow and expand their production capabilities, the scalability of their cooling systems becomes a critical consideration. Cooling jackets must be designed with future growth in mind, ensuring that they can be easily adapted or expanded to accommodate larger tanks or additional fermentation vessels. Failure to plan for scalability can result in costly upgrades or the need to replace the cooling system entirely as production demands increase.
Environmental Considerations
The environmental impact of cooling jackets, particularly in terms of energy consumption and the use of cooling mediums, is an important consideration for breweries committed to sustainability. While cooling jackets are generally more energy-efficient than other methods, they still require careful management to minimize their environmental footprint. Breweries should consider using eco-friendly cooling mediums and investing in energy-efficient equipment to reduce their impact on the environment.
Design Customization
Customization of cooling jackets to fit specific tanks and brewing processes can be a complex task. Each brewery has unique requirements based on the types of beer produced, the size and shape of the tanks, and the specific fermentation conditions needed. Designing a cooling jacket that meets all these requirements can be challenging and may require collaboration between the brewery and the equipment provider. This customization process can also extend the timeline for implementation, which must be considered during planning.
Regulatory Compliance
Cooling jackets, like all brewery equipment, must meet specific regulatory standards, particularly concerning food safety and hygiene. Ensuring that the materials used in the cooling jacket are food-grade and that the system is designed to prevent contamination is essential. Compliance with industry standards not only ensures the safety and quality of the beer but also protects the brewery from potential legal and regulatory issues.
By carefully planning and managing the implementation of cooling jackets, breweries can overcome these challenges and reap the benefits of precise temperature control, improved product quality, and energy efficiency.
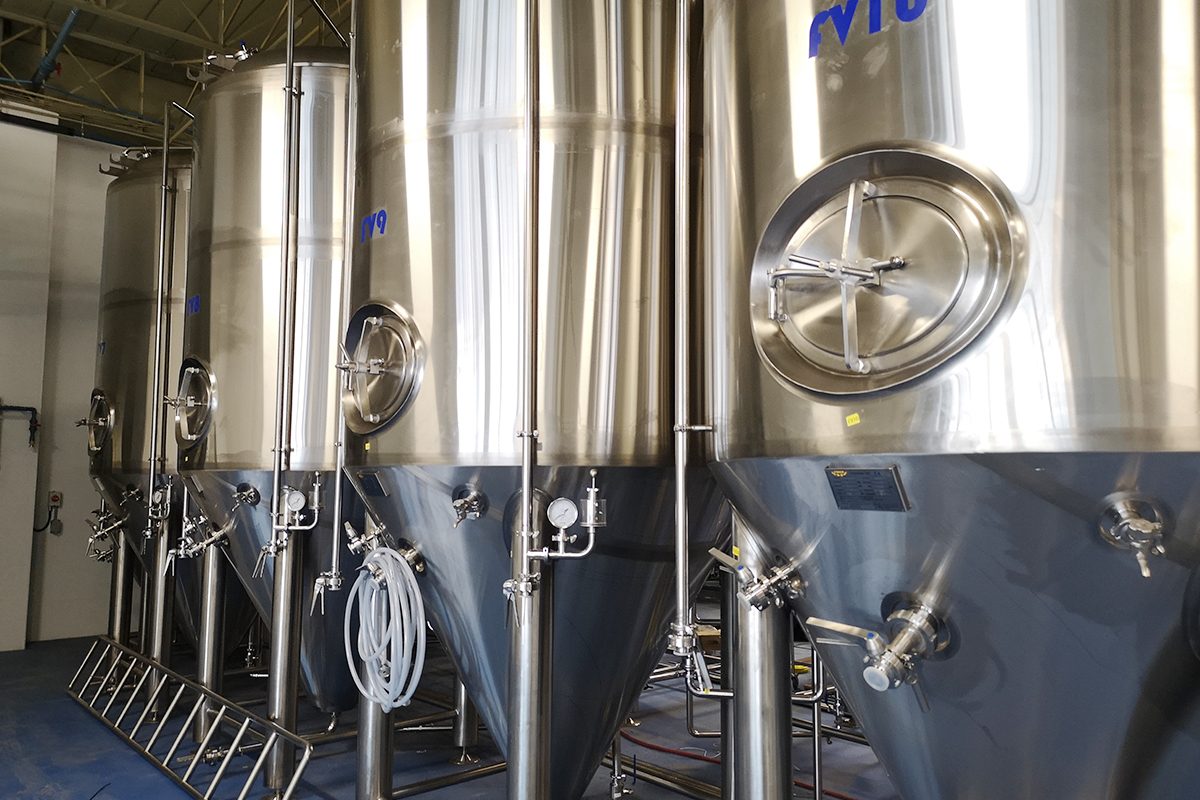
Summary
Cooling jackets play a vital role in the fermentation process, providing precise temperature control to produce consistent, high-quality beer. By circulating a cooling medium through the jacket, excess heat generated during fermentation is effectively dissipated, maintaining an optimal environment for yeast activity. This temperature regulation not only ensures the consistency of each batch but also enhances the flavor, aroma, and overall quality of the final product. While the initial investment and maintenance requirements of cooling jackets can be significant, their benefits in terms of energy efficiency, scalability, and improved product quality make them indispensable for modern breweries.
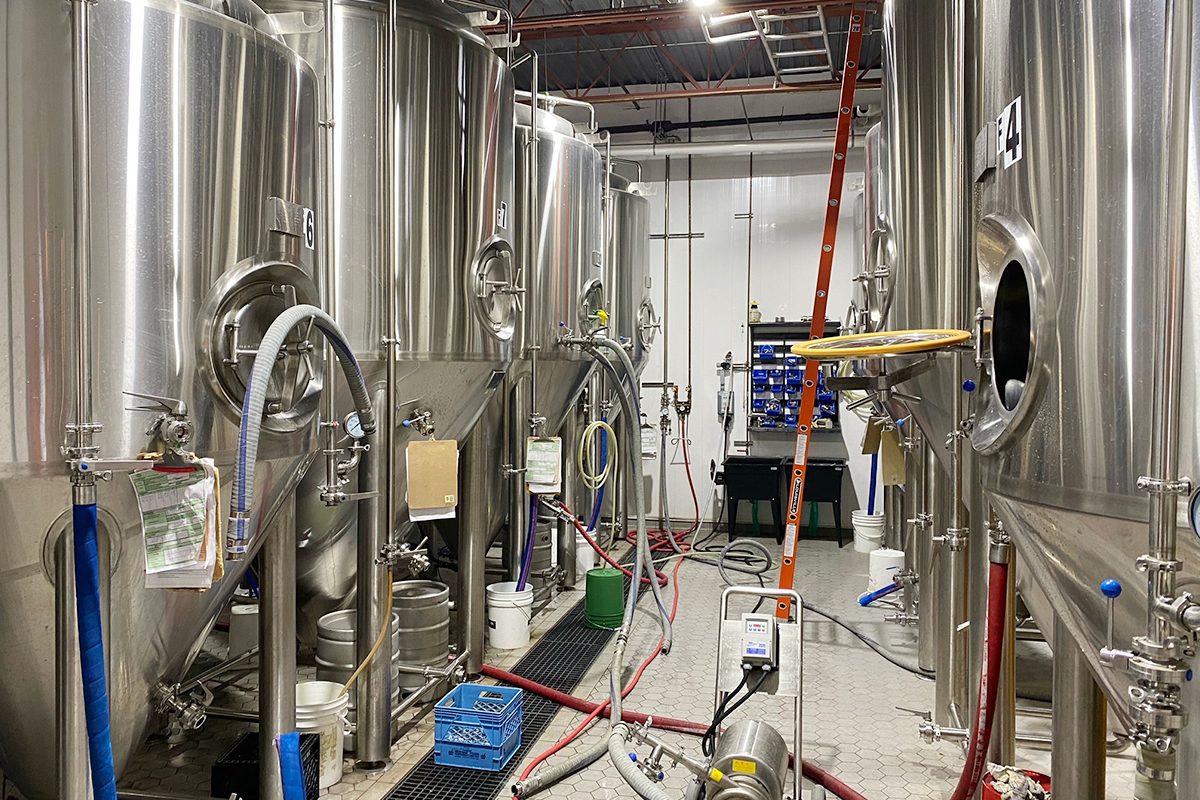
Get Turnkey Brewery Solutions
At ZYB Craft, we understand that every brewery has unique needs, which is why we offer comprehensive turnkey brewery solutions that include expertly designed fermentation systems with integrated cooling jackets. Our turnkey approach ensures that every aspect of your brewing operation is optimized for efficiency, quality, and consistency. From the initial design phase to installation and ongoing support, we work closely with you to develop a customized solution that meets your specific production goals.
Our cooling jacket systems are tailored to your fermentation tanks, providing precise temperature control for consistent, high-quality beer. Whether you’re starting a new brewery or expanding an existing one, ZYB Craft’s turnkey solutions streamline the entire process, minimizing downtime and maximizing your brewing potential. With our expertise and commitment to excellence, you can trust that your brewery will be equipped with the best technology and support, enabling you to focus on what you do best—crafting exceptional beer.