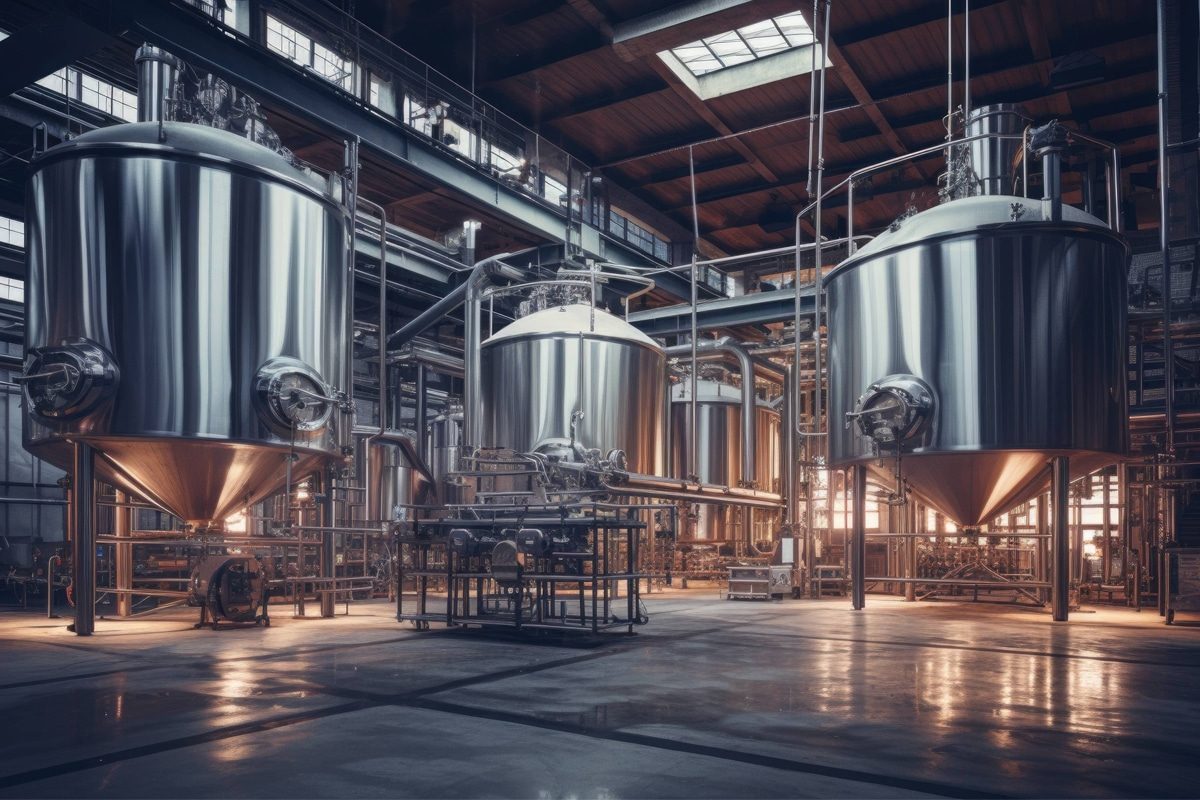
What Are The Risks of Corrosion in Brewery Equipment?
Corrosion is a critical challenge in the brewing industry, where maintaining the quality and safety of the final product is paramount. Brewery equipment, which includes brewhouse equipment, fermentation tanks, bright tanks, piping systems, heat exchangers, and storage vessels, is typically made from metals like stainless steel and copper. Despite their durability, these materials are susceptible to various forms of corrosion. Corrosion not only compromises the structural integrity of the equipment but also poses significant risks to product quality and safety. It can lead to the contamination of beer with metal ions, alter flavors, and cause microbial contamination. Moreover, corrosion can result in costly equipment failures, production downtime, and increased maintenance expenses. Understanding the types and causes of corrosion, along with effective prevention and mitigation strategies, is essential for breweries to ensure continuous, high-quality production and to safeguard their investment in sophisticated brewing systems.
Complete Guide
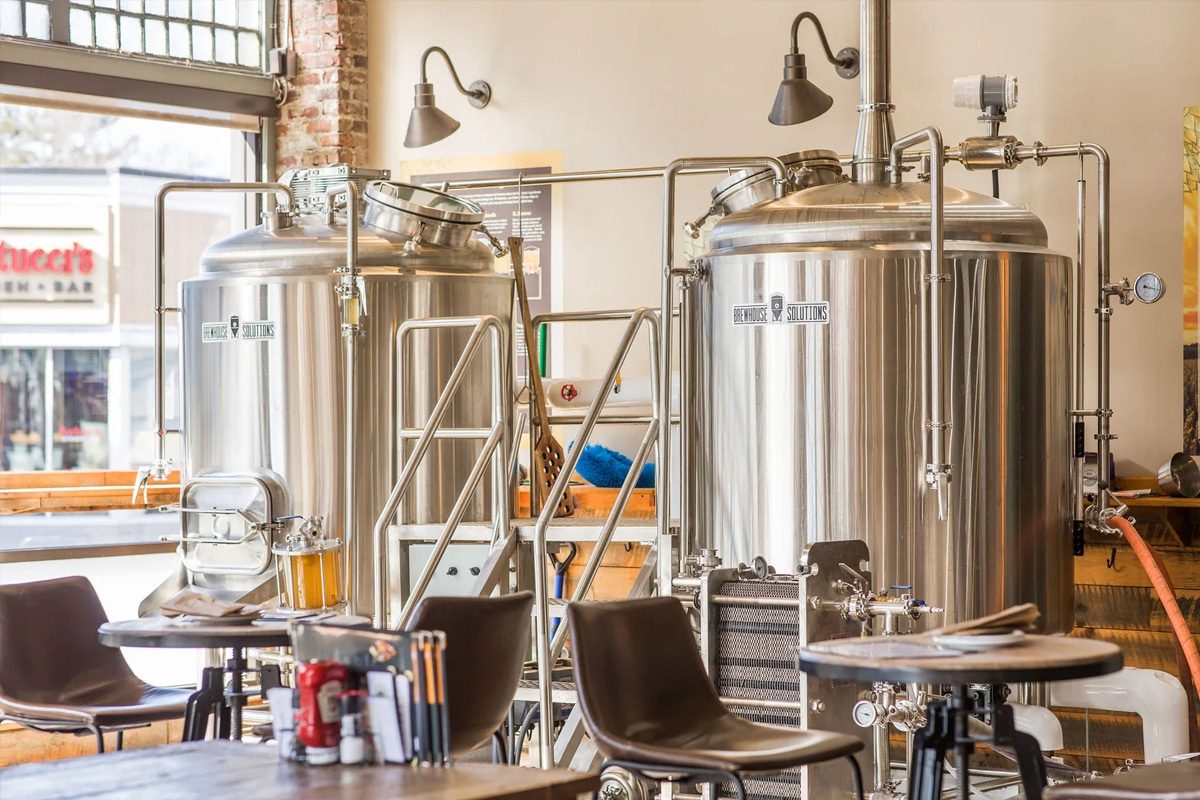
Understanding Corrosion
Corrosion is a natural process that gradually deteriorates metals through chemical reactions with their environment. In the context of breweries, corrosion can have severe implications for equipment longevity, product quality, and operational efficiency. To effectively combat corrosion, a brewery needs to understand the various types and causes unique to the brewery environment.
Types of Corrosion
- Uniform Corrosion: Uniform corrosion occurs evenly across the surface of the metal, leading to a general thinning over time. This type of corrosion is predictable and often less severe than localized forms because it affects the entire surface uniformly. However, it can still weaken equipment if not monitored and managed.
- Pitting Corrosion: Pitting corrosion is a localized form of corrosion that leads to the formation of small, deep pits or holes in the metal. These pits can penetrate deeply and cause significant damage even if the overall loss of metal is minimal. Pitting is particularly dangerous because it can go unnoticed until it causes equipment failure.
- Crevice Corrosion: This form of corrosion occurs in confined spaces where the solution can become stagnant, such as under gaskets, washers, or lap joints. Crevice corrosion is problematic because it can be difficult to detect and can rapidly progress once initiated.
- Stress Corrosion Cracking (SCC): SCC results from the combined effect of tensile stress and a corrosive environment, leading to the formation of cracks. These cracks can grow rapidly under stress and cause sudden, catastrophic failure of equipment. SCC is particularly concerning in high-stress areas like welds and bends.
- Galvanic Corrosion: Galvanic corrosion occurs when two dissimilar metals are in electrical contact in the presence of an electrolyte, leading to accelerated corrosion of the more reactive metal. This is common in breweries where different metals are used nearby, such as in piping systems and fittings.
- Microbiologically Influenced Corrosion (MIC): MIC is caused by the presence of microorganisms, such as bacteria and fungi, which can create localized environments that accelerate corrosion. These microbes can form biofilms on metal surfaces, leading to pitting and other localized corrosion.
Causes of Corrosion in Brewery Equipment
- Water Quality: Water is a major component in brewing and cleaning processes. Its quality, including pH, hardness, and the presence of dissolved gases and minerals, significantly impacts corrosion rates. Hard water with high mineral content can accelerate scaling and corrosion, while soft water can be equally corrosive due to its aggressive nature.
- Cleaning and Sanitizing Agents: Breweries use a variety of cleaning and sanitizing agents to maintain hygiene. Many of these chemicals, such as acidic and alkaline cleaners, can be highly corrosive if not properly managed. The residues left by these agents can also contribute to ongoing corrosion if not thoroughly rinsed.
- Organic Acids: During fermentation, organic acids such as acetic and lactic acid are produced. These acids can lower the pH and create a more corrosive environment, especially in areas where the acids can accumulate and concentrate, such as in crevices and around seals.
- Dissolved Oxygen and Carbon Dioxide: Oxygen and carbon dioxide are involved in the brewing process but can also contribute to corrosion. Oxygen, particularly, can lead to the oxidation of metal surfaces, while carbon dioxide can combine with water to form carbonic acid, which is corrosive to many metals.
- High Temperatures: Elevated temperatures can accelerate the rate of chemical reactions, including those that cause corrosion. Many brewery processes involve high temperatures, such as boiling and pasteurization, which can exacerbate corrosion, especially in heat exchangers and boilers.
- Mechanical Stresses: Equipment in breweries is often subjected to mechanical stresses from pressure, vibration, and operational wear and tear. These stresses can create or exacerbate conditions for stress corrosion cracking and other forms of mechanical-assisted corrosion.
By understanding these types and causes of corrosion, breweries can implement targeted strategies to prevent and mitigate corrosion, thereby ensuring the longevity and reliability of their equipment, maintaining product quality, and safeguarding their operational efficiency.
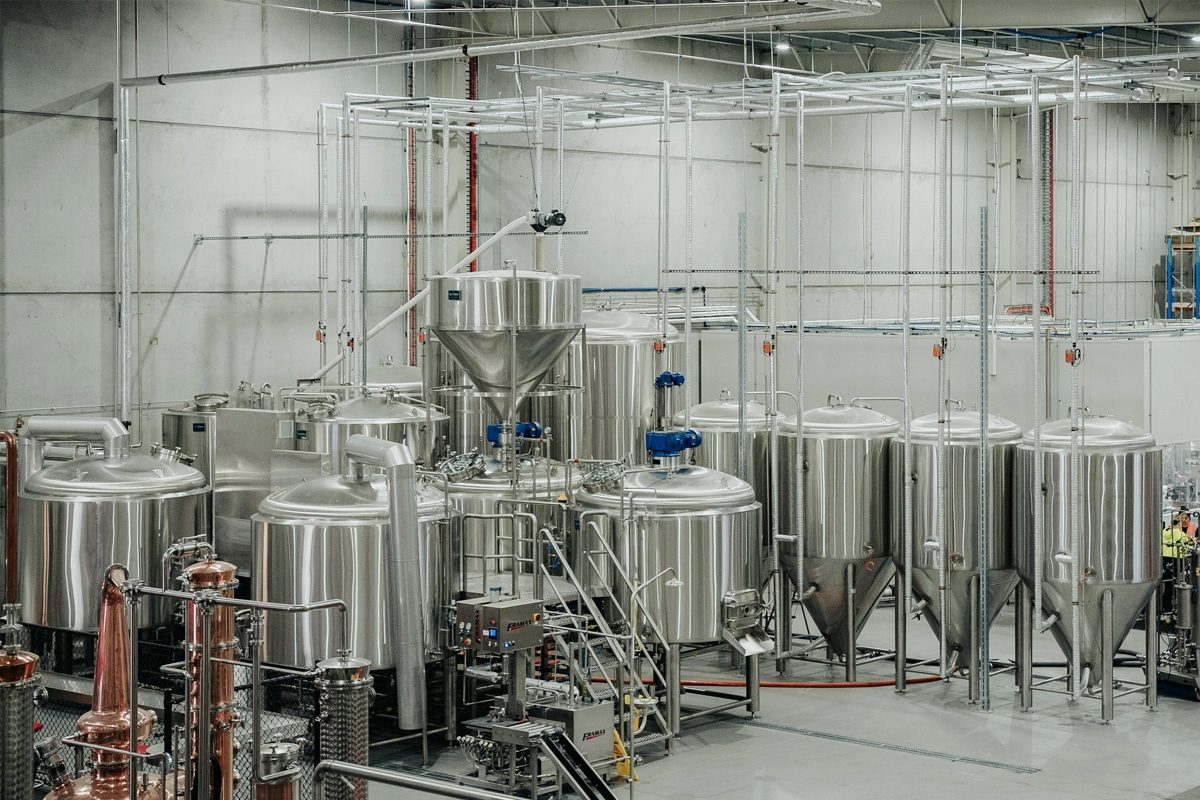
Risks Posed by Corrosion in Brewery Equipment
Corrosion in brewery equipment presents multiple risks that can significantly impact the brewing process, product quality, and overall operational efficiency. The primary risks can be categorized into three main areas: product contamination, structural integrity and equipment failure, and economic impact. Understanding these risks can help implement effective corrosion management strategies.
Product Contamination
- Metal Ion Leaching: Corrosion can cause metal ions such as iron, copper, and nickel to leach into the beer. These metal ions can adversely affect the taste, aroma, and appearance of the beer. For instance, iron can impart a metallic taste, while copper ions can catalyze oxidation reactions that result in off-flavors and haziness.
- Microbial Contamination: Corroded surfaces are often rough and pitted, providing ideal environments for microbial colonization. Bacteria and other microorganisms can thrive in these areas, leading to potential contamination of the beer. Microbial contamination can result in spoilage, and off-flavors, and pose health risks to consumers.
- Chemical Residue: The presence of corrosion can lead to the accumulation of chemical residues from cleaning and sanitizing agents. These residues can contaminate the beer, affecting its flavor profile and safety. Making sure to rinse thoroughly after cleaning can prevent this type of contamination.
Structural Integrity and Equipment Failure
- Leaks and Ruptures: Corrosion can weaken the walls of tanks, pipes, and other equipment, leading to leaks or even catastrophic ruptures. Such failures can cause loss of product, pose safety hazards to workers, and require extensive repairs. Leaks can also lead to environmental contamination if not promptly addressed.
- Reduced Pressure Resistance: Pressure vessels and piping systems in breweries must withstand high pressures during various stages of the brewing process. Corrosion-induced thinning reduces the ability of these components to handle pressure, increasing the risk of blowouts and other dangerous failures.
- Mechanical Failure: Stress corrosion cracking (SCC) and other forms of localized corrosion can lead to sudden and unexpected mechanical failures. For example, a small crack in a critical weld can propagate rapidly under stress, leading to a complete failure of the component.
Economic Impact
- Maintenance and Replacement Costs: The financial burden of addressing corrosion is substantial. Regular maintenance to mitigate corrosion and the premature replacement of corroded equipment can be costly. This includes direct costs such as materials and labor, as well as indirect costs like production downtime.
- Production Downtime: Equipment failure due to corrosion can halt production, leading to delays and loss of revenue. For breweries, maintaining continuous production can meet market demand and ensure profitability. Unplanned shutdowns can disrupt the supply chain and negatively impact sales.
- Quality Control Issues: Corrosion-related contamination and equipment failures can lead to quality control issues, resulting in inconsistent product quality. This can damage a brewery’s reputation, lead to customer dissatisfaction, and potentially result in product recalls.
- Loss of Revenue: The cumulative effects of corrosion, including product contamination, equipment failure, and production downtime, can significantly impact a brewery’s financial performance. In severe cases, persistent corrosion issues can threaten the viability of the business.
Corrosion in brewery equipment poses severe risks that affect product quality, safety, and economic performance. By understanding these risks, product contamination, structural integrity and equipment failure, and economic impact, breweries can implement effective strategies to manage and mitigate corrosion. Investing in high-quality materials, regular maintenance, and advanced monitoring technologies can help breweries protect their equipment, ensure consistent product quality, and maintain profitability in a competitive industry.
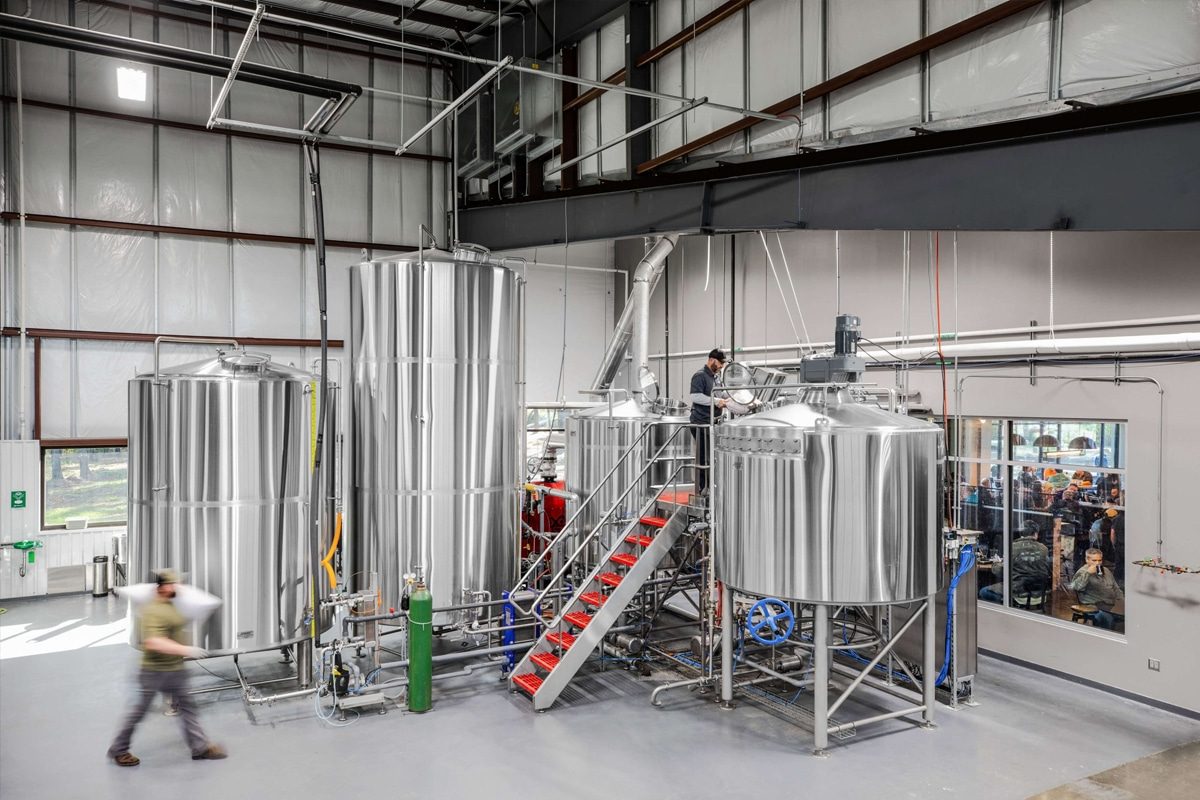
Preventing and Mitigating Corrosion in Breweries
Effective prevention and mitigation of corrosion in brewery equipment require a multifaceted approach. This section outlines key strategies, including material selection, design considerations, maintenance practices, chemical treatment, and environmental control.
Material Selection
- Stainless Steel: Stainless steel, especially grades 304 and 316, is the most commonly used material in breweries due to its excellent corrosion resistance and durability. Grade 316 stainless steel contains molybdenum, which enhances its resistance to pitting and crevice corrosion, making it suitable for more aggressive environments.
- Copper: Copper is traditionally used in brewing kettles for its excellent thermal conductivity and antimicrobial properties. However, it is more prone to corrosion, particularly in the presence of acidic environments. Regular maintenance and protective coatings can extend their lifespan.
- Protective Coatings: Applying protective coatings, such as passivation layers on stainless steel or food-grade epoxy coatings, can provide an additional barrier against corrosive agents. These coatings must be compliant with food safety standards and regularly inspected for integrity.
- Alternative Materials: In some cases, non-metallic materials like high-performance polymers and ceramics can be used for certain components to eliminate the risk of metal corrosion. These materials are often used in fittings, gaskets, and seals.
Design Considerations
- Minimize Crevices: Equipment should be designed to minimize crevices and other confined spaces where corrosive agents can accumulate. Smooth, continuous welds and seamless construction are preferable to reduce the risk of crevice corrosion.
- Drainage and Ventilation: Proper drainage systems should be in place to prevent the accumulation of standing water, which can lead to localized corrosion. Adequate ventilation is also crucial to reduce humidity and the buildup of corrosive gases like CO2.
- Cathodic Protection: In situations where dissimilar metals must be used, implementing cathodic protection systems can prevent galvanic corrosion. Sacrificial anodes or impressed current systems can be employed to protect the more reactive metal.
- Ease of Cleaning: Designing equipment with accessibility in mind allows for thorough cleaning and maintenance. CIP (clean-in-place) systems should be integrated into the design to ensure effective cleaning without the need for disassembly.
Maintenance Practices
- Regular Inspection: Regular inspections are critical for the early detection of corrosion. Techniques such as visual inspections, ultrasonic testing, and radiographic testing can identify thinning, pitting, and other forms of corrosion before they lead to equipment failure.
- Cleaning Protocols: Implementing stringent cleaning protocols helps prevent the buildup of residues that can cause corrosion. Using non-corrosive cleaning agents and ensuring thorough rinsing after cleaning is essential.
- Routine Maintenance: Routine maintenance schedules should include tasks such as descaling, reapplying protective coatings, and replacing worn components. Keeping detailed maintenance records helps in tracking the condition of equipment over time.
- Water Quality Management: Ensuring the quality of water used in the brewing and cleaning processes is vital. Water treatment systems like reverse osmosis, deionization, and the use of corrosion inhibitors can help control pH, hardness, and mineral content.
Chemical Treatment
- Corrosion Inhibitors: Adding corrosion inhibitors to cleaning and sanitizing solutions can help protect metal surfaces. These inhibitors form a protective film on the metal, reducing its interaction with corrosive agents.
- pH Control: Maintaining optimal pH levels in brewing and cleaning solutions can mitigate corrosive reactions. Buffer solutions and pH stabilizers help maintain the desired pH levels, reducing the risk of acid-induced corrosion.
- Descaling Agents: Using descaling agents to remove mineral buildup from equipment surfaces helps prevent scaling and corrosion. These agents should be chosen based on their compatibility with the equipment materials.
Environmental Control
- Temperature Control: Maintaining moderate temperatures in the brewing environment helps reduce the rate of corrosive reactions. Insulating equipment and using temperature control systems can prevent temperature extremes.
- Humidity Control: Reducing humidity levels in areas where equipment is stored or used helps prevent corrosion, particularly for equipment that is not constantly in use. Dehumidifiers and proper ventilation systems are effective tools for humidity control.
- Ventilation: Ensuring adequate ventilation in brewing areas helps remove corrosive gases like CO2 and prevents the accumulation of moisture. Proper air circulation is essential to maintaining a non-corrosive environment.
Preventing and mitigating corrosion in brewery equipment requires a comprehensive approach that includes careful material selection, thoughtful design considerations, rigorous maintenance practices, effective chemical treatments, and strict environmental control. By implementing these strategies, breweries can protect their equipment, ensure consistent product quality, and maintain efficient and safe operations. Proactive corrosion management not only extends the lifespan of brewery equipment but also contributes to the overall success and profitability of the brewery.
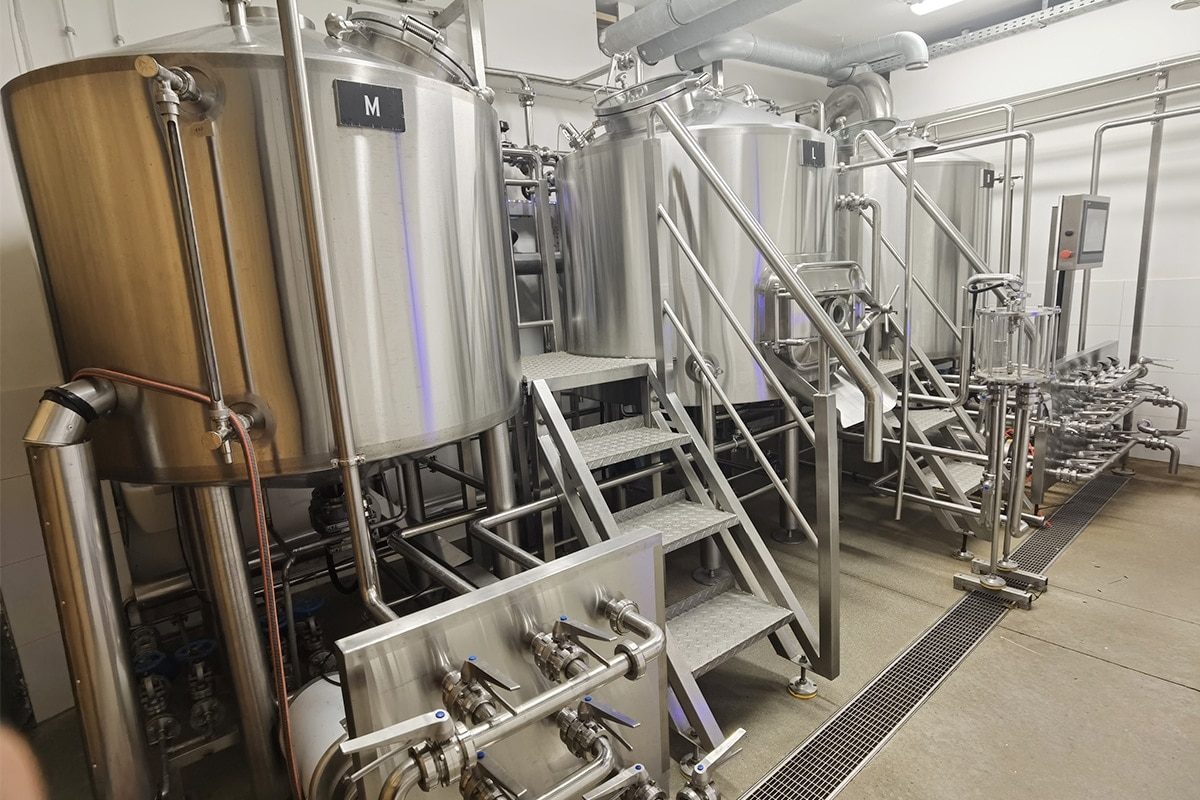
Summarize
Corrosion in brewery equipment poses significant risks that can impact product quality, operational efficiency, and financial performance. Key risks include product contamination through metal ion leaching and microbial growth, structural integrity issues leading to equipment failure, and substantial economic impacts due to maintenance costs and production downtime. Effective prevention and mitigation strategies can effectively address these risks.
Breweries should focus on selecting corrosion-resistant materials like stainless steel, designing equipment to minimize corrosion-prone areas, implementing rigorous maintenance and inspection protocols, using chemical treatments to protect metal surfaces, and controlling environmental factors like humidity and temperature. By understanding and addressing the multifaceted risks of corrosion, breweries can ensure the longevity of their equipment, maintain high product standards, and protect their bottom line. In the highly competitive beer industry, proactive corrosion management helps maintain the quality and efficiency of brewery operations.

Get A Turnkey Brewery Solutions
When facing the challenges of corrosion in brewery equipment, partnering with a professional brewery solution provider like ZYB Craft can make a significant difference. ZYB Craft offers comprehensive turnkey brewery solutions designed to address and mitigate the risks of corrosion effectively. Our expertise encompasses selecting the highest quality, corrosion-resistant materials, and designing equipment with minimal crevices and optimal drainage to prevent corrosion hotspots. We provide state-of-the-art cleaning and maintenance protocols tailored to the unique needs of each brewery, ensuring long-term equipment reliability and product quality.
With ZYB Craft’s turnkey solutions, breweries can benefit from advanced corrosion monitoring systems, regular maintenance schedules, and the application of protective coatings and corrosion inhibitors. Our solutions are not only technologically advanced but also economically efficient, helping breweries reduce downtime, maintenance costs, and potential product contamination. Trust ZYB Craft to deliver a robust, corrosion-resistant brewery setup that guarantees consistent performance and high-quality beer production.