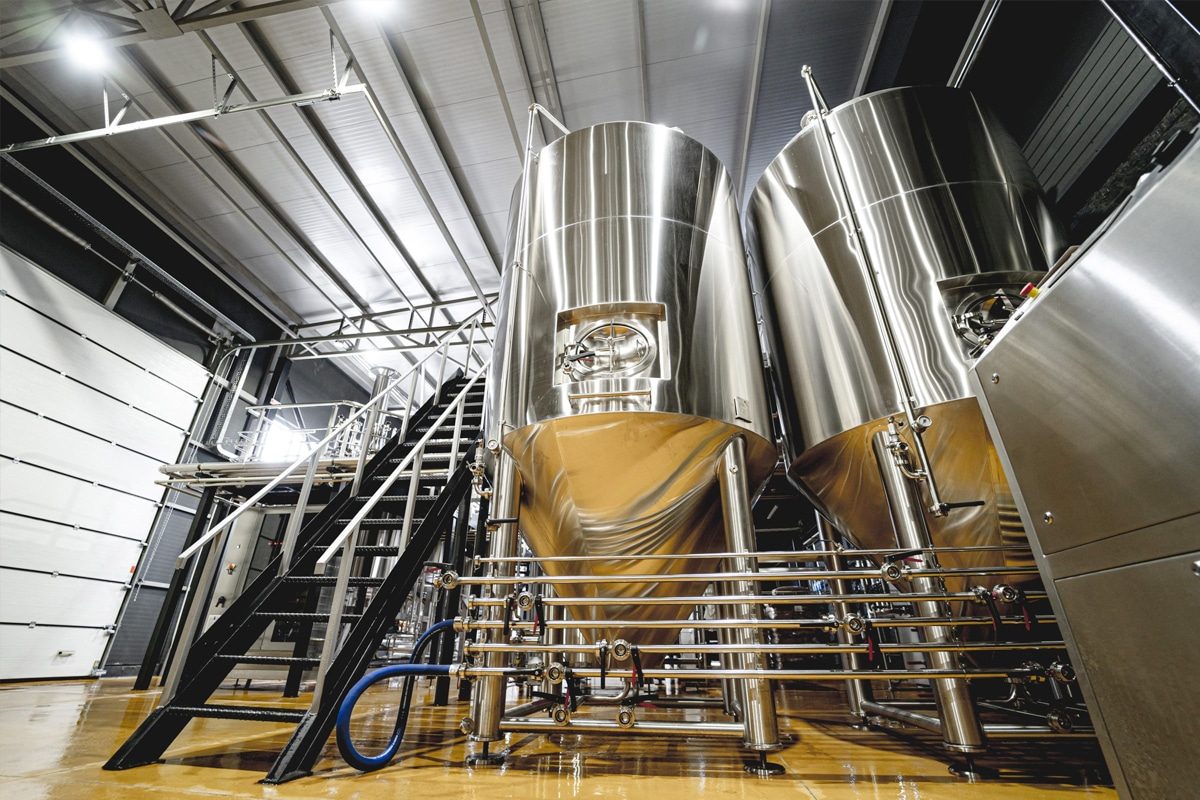
What Are The Potential Problems With Custom-Built Brewery Equipment?
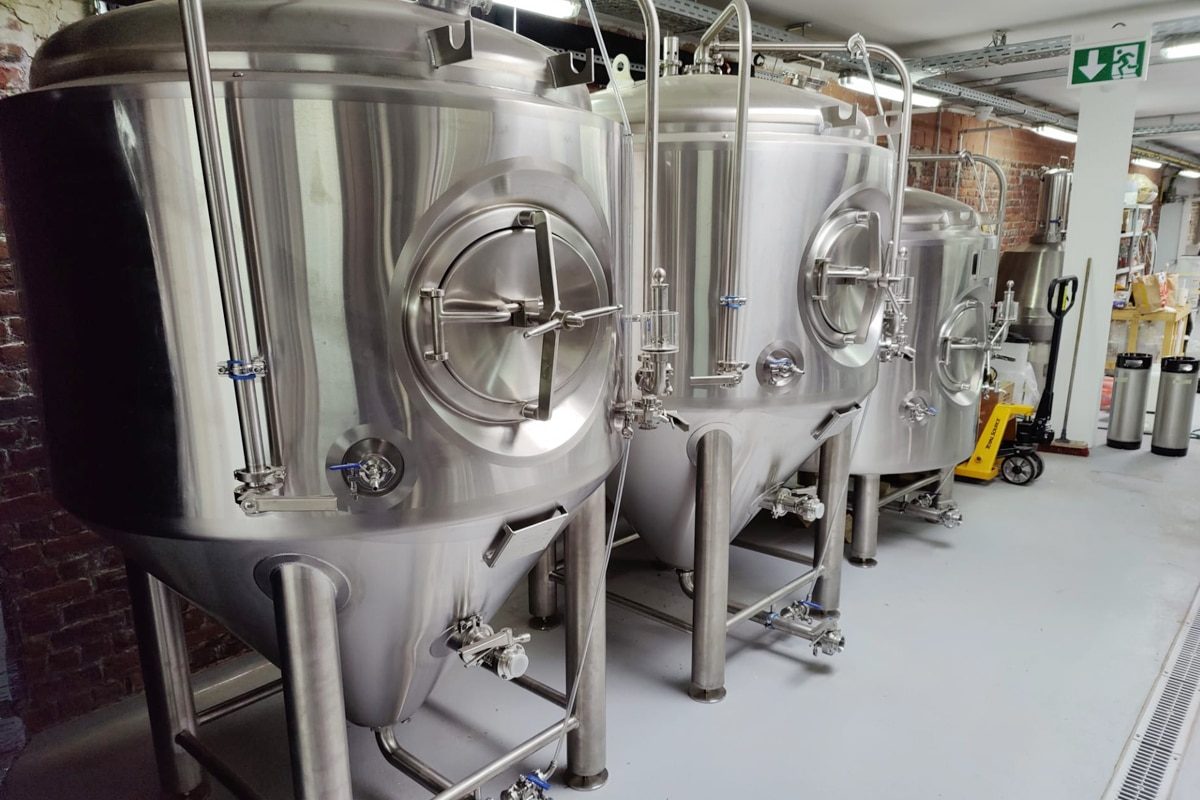
High Initial Costs
Design and Engineering Fees
The first major expense incurred in the development of custom-built brewery equipment is the design and engineering phase. This process involves several critical steps:
- Needs Assessment
- Consultations: Initial consultations with brewers to understand their specific needs and preferences are necessary. These consultations often involve multiple meetings to gather detailed requirements and to ensure that the custom equipment will meet the desired specifications.
- Site Analysis: Analyzing the brewery’s layout and existing infrastructure to determine how the new equipment will be integrated. This may include site visits and surveys.
- Design Development
- Conceptual Design: Creating initial design concepts and schematics. This stage involves significant creative and technical input to ensure the equipment will function as intended.
- Detailed Engineering: Once the conceptual designs are approved, detailed engineering begins. This involves creating precise technical drawings, 3D models, and specifications for every component of the equipment.
- Prototyping and Testing
- Prototype Development: For complex equipment, developing prototypes may be necessary to test functionality and make necessary adjustments. This stage can be both time-consuming and costly.
- Testing and Validation: Rigorous testing is required to ensure the design meets all operational, safety, and regulatory standards. Any issues identified during testing must be addressed, which can further increase costs.
Material Costs
Material costs represent another significant portion of the initial investment in custom-built brewery equipment. These costs can vary widely depending on several factors:
- Quality and Type of Materials
- Stainless Steel: High-grade stainless steel is commonly used in brewery equipment due to its durability, resistance to corrosion, and ease of cleaning. However, the cost of stainless steel can be significantly higher than other materials.
- Specialty Metals: In some cases, specialty metals or alloys may be required for specific parts of the equipment, further increasing material costs.
- Customization Requirements
- Unique Components: Custom-built equipment often requires components that are not standard. These unique parts may need to be specially manufactured, which can increase material costs.
- Precision Fabrication: High precision in the fabrication of custom components ensures proper fit and function. Achieving this precision often involves additional material costs.
- Supplier and Sourcing
- Supplier Selection: The choice of supplier can also impact material costs. While some suppliers offer competitive pricing, others may charge premium rates for high-quality or specialized materials.
- Logistics: Shipping and handling of materials, especially for large or heavy components, add to the overall material costs. This is particularly relevant for breweries located in remote areas.
Manufacturing Costs
The manufacturing phase of custom-built brewery equipment involves translating the detailed designs and materials into functional machinery. This phase can be particularly costly due to several factors:
- Labor Costs
- Skilled Labor: Manufacturing custom equipment requires highly skilled labor, including welders, machinists, and assembly technicians. These professionals command higher wages due to their expertise and the precision required.
- Labor Intensity: The bespoke nature of custom equipment means that the manufacturing process is more labor-intensive compared to mass-produced equipment. Each component often requires more time and attention to detail.
- Fabrication Techniques
- Specialized Processes: Custom equipment may involve specialized fabrication techniques, such as precision welding, custom machining, and complex assembly procedures. These processes are typically more expensive than standard manufacturing techniques.
- Quality Control: Ensuring the highest standards of quality involves extensive quality control measures, including inspections and testing at various stages of the manufacturing process. These measures add to the overall manufacturing costs.
- Production Volume
- Low Volume Production: Custom-built equipment is usually produced in lower volumes compared to standard equipment. The lack of economies of scale means that the cost per unit is higher. Manufacturers must allocate resources specifically for these small production runs, which increases costs.
- Customization Adjustments: Any changes or adjustments requested during the manufacturing process can lead to additional costs. Custom equipment often requires iterative modifications to meet the exact specifications, further driving up expenses.
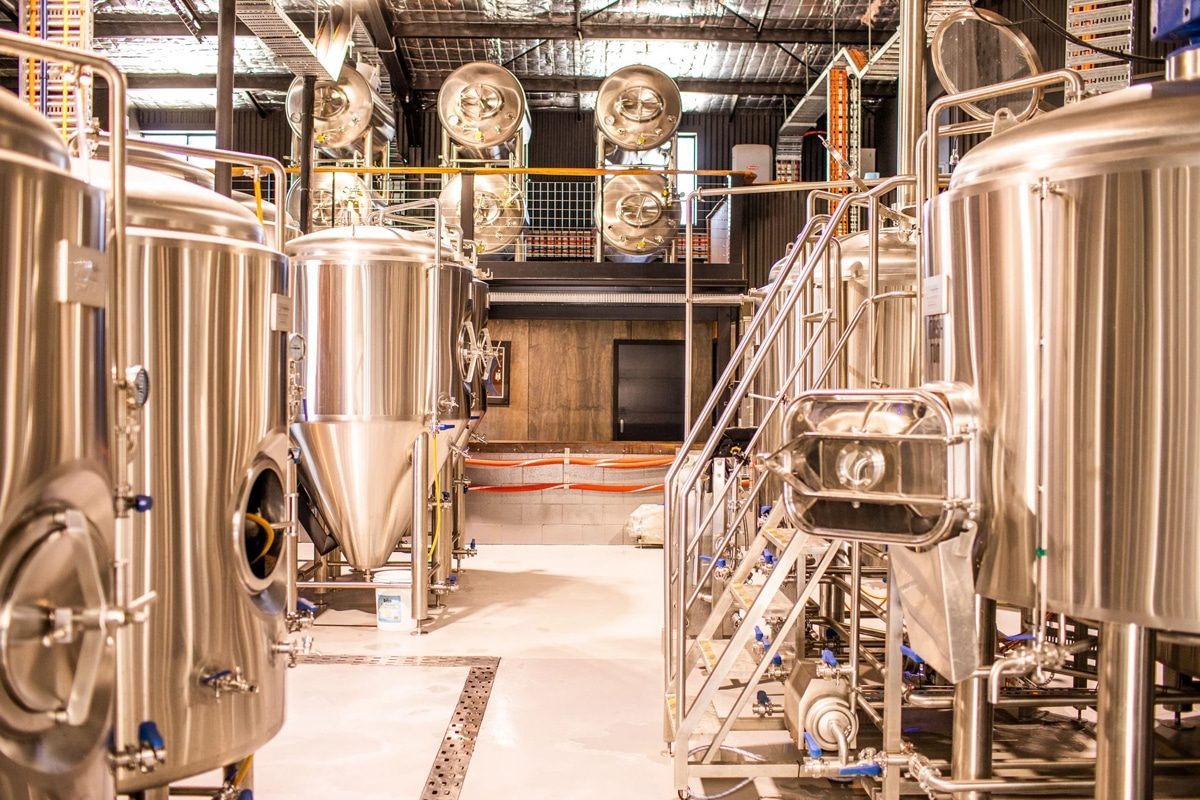
Extended Lead Times
Design Phase
The design phase is the first and one of the most time-consuming stages in developing custom-built brewery equipment. This phase involves several intricate steps that ensure the equipment will meet the brewery’s specific requirements:
- Needs Assessment
- Detailed Consultations: Extensive discussions with the brewery team to understand their unique needs, preferences, and brewing processes. This stage requires multiple meetings and thorough documentation of specifications.
- Site Analysis: Conducting detailed analyses of the brewery’s current layout and infrastructure to ensure the new equipment can be integrated seamlessly. This often involves site visits, measurements, and possibly 3D modeling of the space.
- Conceptual Design
- Initial Concepts: Creating initial design concepts that align with the brewery’s requirements. These concepts are usually reviewed and refined multiple times, involving feedback from the brewery team.
- Technical Specifications: Develop detailed technical specifications that outline the functionality, dimensions, and materials for the equipment. This step requires collaboration with engineers and technical experts.
- Detailed Engineering
- Engineering Drawings: Producing comprehensive engineering drawings and 3D models of the equipment. These documents must be precise and detailed to guide the manufacturing process.
- Prototype Development (if necessary): In some cases, a prototype may be developed to test specific features or functions of the equipment. Prototyping can significantly add time to the design phase but is vital in helping to ensure that the final product meets all requirements.
Manufacturing Delays
Once the design phase is complete, the project moves into the manufacturing stage. Custom-built equipment often faces longer manufacturing times compared to off-the-shelf solutions due to several factors:
- Custom Fabrication
- Unique Components: Custom equipment requires the fabrication of unique components that are not readily available. These components often need to be manufactured from scratch, which is a time-consuming process.
- High Precision: The bespoke nature of custom equipment demands high precision in manufacturing. Achieving this precision can take longer than mass-producing standard components.
- Skilled Labor
- Specialized Skills: Custom equipment manufacturing relies on highly skilled labor, including specialized welders, machinists, and assembly technicians. The availability of such skilled labor can impact manufacturing timelines.
- Labor Intensity: Custom projects are typically more labor-intensive, requiring meticulous attention to detail and often involving manual processes that take longer to complete.
- Quality Control
- Rigorous Testing: Ensuring the highest quality and performance standards involves extensive quality control measures. Each component must be tested and inspected thoroughly, which can add significant time to the manufacturing process.
- Iterative Adjustments: During manufacturing, unforeseen issues may arise that require adjustments or reworking of parts. These iterative adjustments can further delay the timeline.
Shipping and Installation
The final stages of bringing custom-built brewery equipment to operational status are shipping and installation. These stages, while seemingly straightforward, can also introduce delays:
- Shipping
- Logistics Planning: Coordinating the logistics of shipping custom equipment can be complex, especially if the equipment is large, heavy, or requires special handling. Detailed planning is necessary to ensure safe and timely delivery.
- Customs and Regulations: For international shipments, navigating customs and regulatory requirements can add to the shipping time. Delays at borders or ports due to paperwork or inspections are common.
- Installation
- Site Preparation: Preparing the site for installation may involve significant work, including structural modifications, utility upgrades, and ensuring the area meets safety standards.
- Complex Assembly: Custom equipment often requires on-site assembly by skilled technicians. This assembly process can be complex and time-consuming, requiring precise alignment and connection of various components.
- Integration with Existing Systems: Ensuring the new equipment integrates seamlessly with existing systems can be challenging. This step may involve software integration, connectivity checks, and testing to ensure everything works harmoniously.
- Commissioning and Testing
- Initial Testing: After installation, initial testing is necessary to ensure the equipment operates correctly. This includes running the equipment through various scenarios to check for functionality and performance.
- Training: Staff training on the new equipment is essential and can add to the overall time required before the equipment becomes fully operational.
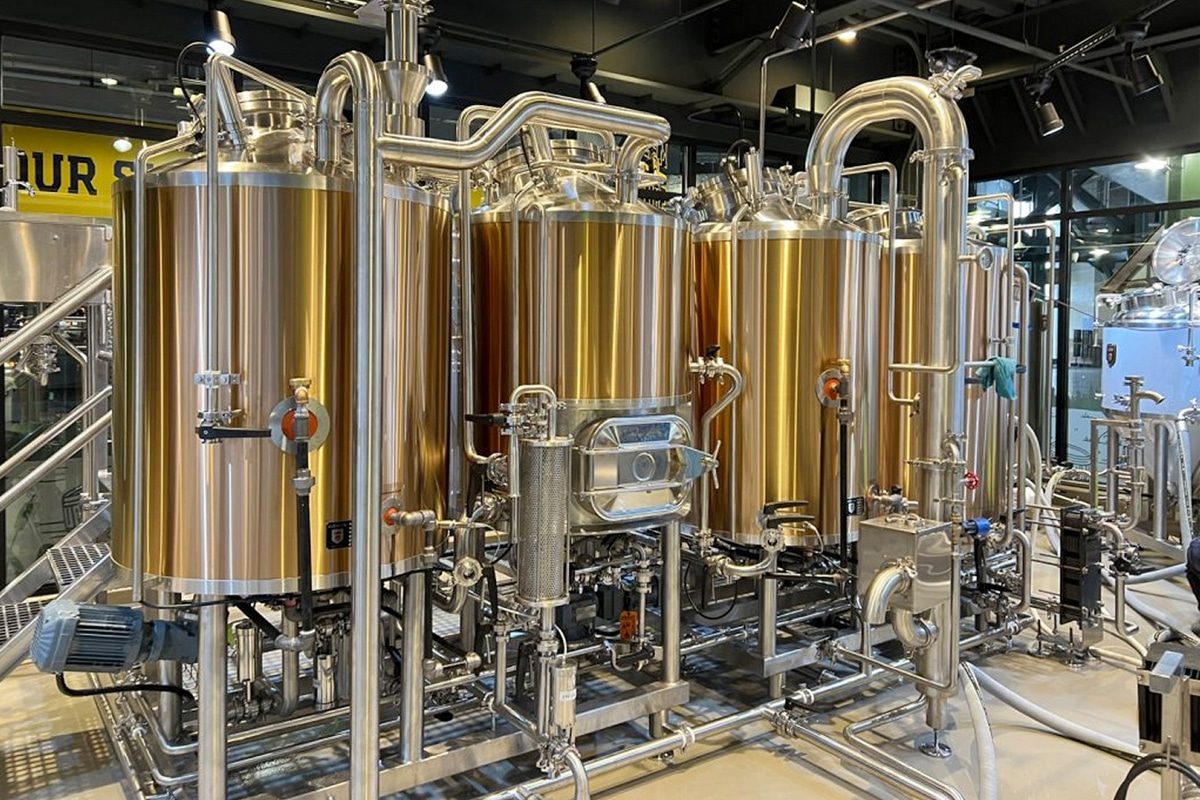
Design and Engineering Challenges
Inconsistent Performance
Inconsistent performance is a critical issue that can affect the quality and consistency of the beer produced. Several factors contribute to this problem:
- Variability in Design Execution
- Component Quality: Custom-built equipment relies on various components that must work together seamlessly. Any variation in the quality or specifications of these components can lead to inconsistencies in performance. For example, variances in pump flow rates or heating element efficiency can cause fluctuations in brewing processes.
- Precision and Tolerances: Custom equipment must be manufactured to exact specifications. Any deviation from these specifications during fabrication can lead to performance issues. Precise tolerances help maintain consistent temperature, pressure, and flow.
- Operational Challenges
- Calibration Issues: Custom equipment often requires precise calibration to function correctly. Inaccurate calibration can lead to variations in measurements, such as temperature or volume, which can affect the brewing process.
- Staff Training: Operators must be thoroughly trained to use custom equipment. Inadequate training can result in operational errors, further contributing to inconsistent performance.
- Integration Problems
- System Compatibility: Integrating custom-built equipment with existing systems can be challenging. Compatibility issues can arise, causing disruptions in the brewing process. For example, a new custom fermentation tank might not integrate smoothly with existing control systems, leading to inconsistent fermentation results.
Higher Energy Consumption
Energy efficiency is a crucial factor for breweries, affecting both operational costs and environmental impact. Custom-built equipment can sometimes lead to higher energy consumption due to several reasons:
- Inefficient Design
- Suboptimal Insulation: Poor insulation in tanks, pipes, and other components can result in significant energy losses. Effective insulation maintains the required temperature during brewing and fermentation.
- Inefficient Heating and Cooling Systems: Custom-built systems may lack the efficiency of standardized solutions. For instance, custom heating elements or cooling jackets may not be optimized for energy efficiency, leading to higher energy usage.
- Over-Specification
- Oversized Equipment: Custom equipment designed to handle peak production capacities may be oversized for regular operations. This can result in unnecessary energy consumption during periods of lower production.
- Redundant Features: Custom designs sometimes include additional features or redundancies that consume extra energy without providing significant benefits.
- Operational Practices
- Energy Management: Without proper energy management practices, custom equipment can lead to inefficient energy use. This includes monitoring energy consumption, optimizing operational schedules, and maintaining equipment regularly.
Increased Waste
Waste generation is a significant concern in the brewing industry, impacting both sustainability and cost efficiency. Custom-built brewery equipment can contribute to increased waste in various ways:
- Material Waste
- Fabrication Scrap: Custom fabrication processes often produce more scrap and waste material compared to standardized manufacturing. Specialized components may require more precise cuts or unique materials, leading to higher waste during production.
- Spare Parts: Custom equipment may require unique spare parts that are not readily available, leading to the disposal of otherwise usable equipment when parts are unavailable.
- Process Inefficiencies
- Batch Variability: Inconsistent performance can result in batch variability, leading to higher rates of off-spec products that must be discarded. For example, variations in fermentation temperature can cause flavor inconsistencies, resulting in wasted batches.
- Cleaning and Maintenance: Custom equipment may require more frequent or intensive cleaning and maintenance, generating additional waste in terms of cleaning agents and water usage.
- Resource Utilization
- Water and Energy Waste: Inefficient use of water and energy during brewing processes contributes to overall waste. Custom equipment that is not optimized for resource efficiency can exacerbate this issue.
- Raw Material Loss: Inefficiencies in the brewing process, such as poor mash tun performance or ineffective wort separation, can lead to higher losses of raw materials like malt and hops.
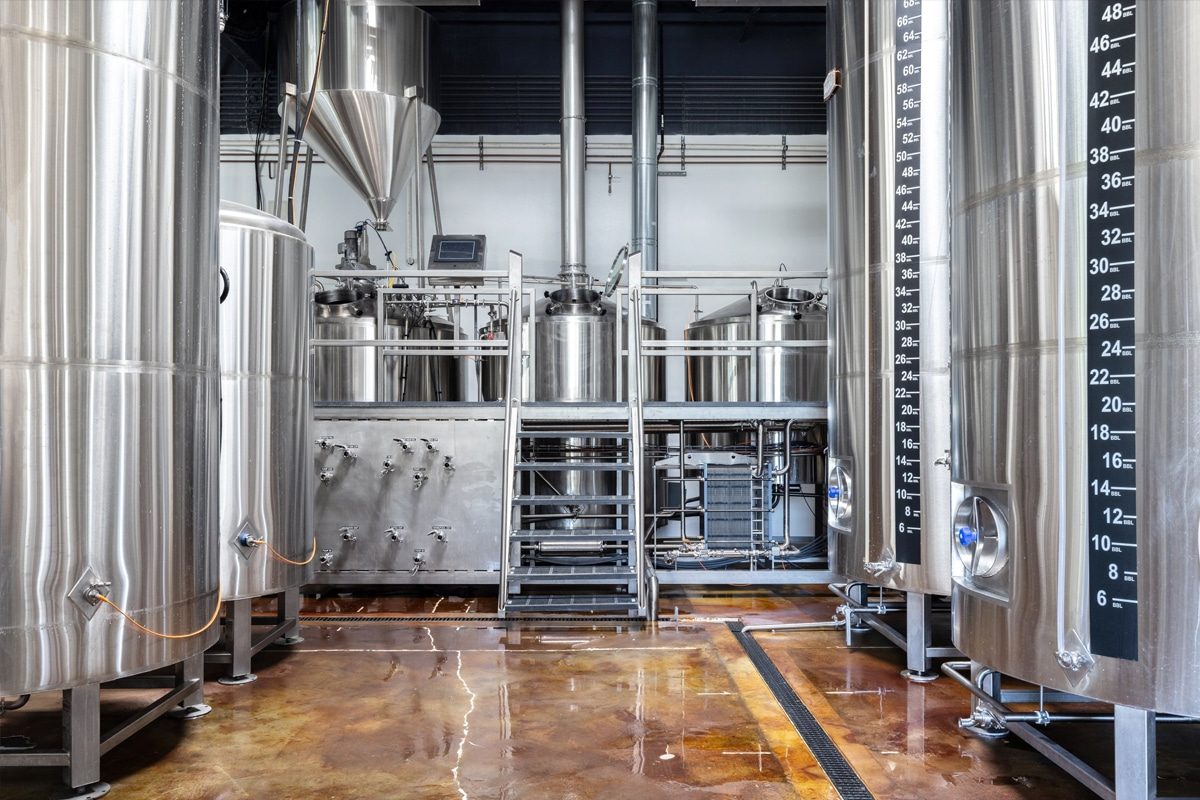
Integration Issues
Software Compatibility
Software compatibility is a critical aspect of integrating custom-built brewery equipment. Modern breweries rely heavily on automation and software systems to monitor and control brewing processes. When new custom equipment is introduced, ensuring it is compatible with existing software systems is essential but can be problematic.
- Proprietary Systems
- Vendor-Specific Software: Custom-built equipment often comes with proprietary software designed by the manufacturer. Integrating this software with existing brewery management systems can be challenging if the systems are not compatible or if they use different protocols.
- Licensing Issues: Proprietary software might require specific licenses or subscriptions, adding to the complexity and cost of integration.
- Data Integration
- Data Formats: Different equipment might use various data formats for recording and transmitting information. Ensuring these formats are compatible and can be integrated into a unified system is crucial for accurate data analysis and process control.
- Real-Time Monitoring: Custom equipment needs to integrate seamlessly with real-time monitoring systems. Any lag or incompatibility can result in delayed responses and affect the quality of the brewing process.
- System Updates and Maintenance
- Software Updates: Keeping all systems up-to-date can be challenging if custom equipment relies on specific software versions that are not aligned with the broader system updates.
- Technical Support: Custom equipment might require specialized technical support, which can be harder to coordinate and integrate with existing IT support structures.
Physical Integration
Physical integration involves incorporating custom-built equipment into the existing brewery layout and infrastructure. This process can be complex and disruptive, requiring careful planning and execution.
- Space Constraints
- Footprint and Layout: Custom equipment might have a different footprint compared to standard equipment, requiring modifications to the existing layout. This can involve relocating other equipment or even structural changes to the facility.
- Access and Clearance: Ensuring there is adequate space for installation, maintenance, and operation of the new equipment is critical. Lack of sufficient clearance can lead to operational inefficiencies and safety hazards.
- Utility Connections
- Plumbing and Electrical: Custom equipment might require specific plumbing and electrical connections that differ from standard configurations. Integrating these connections can involve significant modifications to the existing utility infrastructure.
- HVAC Systems: Adjustments to heating, ventilation, and air conditioning systems might be necessary to accommodate the new equipment, especially if it has different heat or humidity requirements.
- Structural Modifications
- Support Structures: Heavy or large custom equipment may require reinforced floors or additional support structures. This can involve extensive construction work and additional costs.
- Vibration and Noise: New equipment might introduce vibrations or noise levels that affect other operations or equipment. Mitigating these impacts might require additional insulation or isolation measures.
Process Adjustments
Introducing custom-built equipment often necessitates adjustments to existing brewing processes. These adjustments can be disruptive and require time and resources to implement effectively.
- Operational Procedures:
- Training: Staff need to be trained on the operation and maintenance of the new equipment. This training can be time-consuming and might temporarily reduce productivity.
- Standard Operating Procedures (SOPs): Existing SOPs might need to be revised to incorporate the new equipment. This includes updating documentation and ensuring all staff are familiar with the changes.
- Process Optimization:
- Calibration and Testing: Custom equipment typically requires calibration and testing to ensure it operates correctly within the existing process. This phase can uncover unforeseen issues that need to be addressed before full-scale operation.
- Performance Monitoring: Continuous monitoring and adjustment are necessary to optimize the new equipment’s performance and ensure it aligns with the overall brewing process.
- Product Consistency:
- Quality Control: Integrating new equipment can affect product consistency. Rigorous quality control measures are necessary to ensure that the introduction of custom equipment does not negatively impact the final product.
- Recipe Adjustments: Existing recipes might need to be adjusted to accommodate changes in the brewing process introduced by the new equipment. This can involve extensive testing and validation.
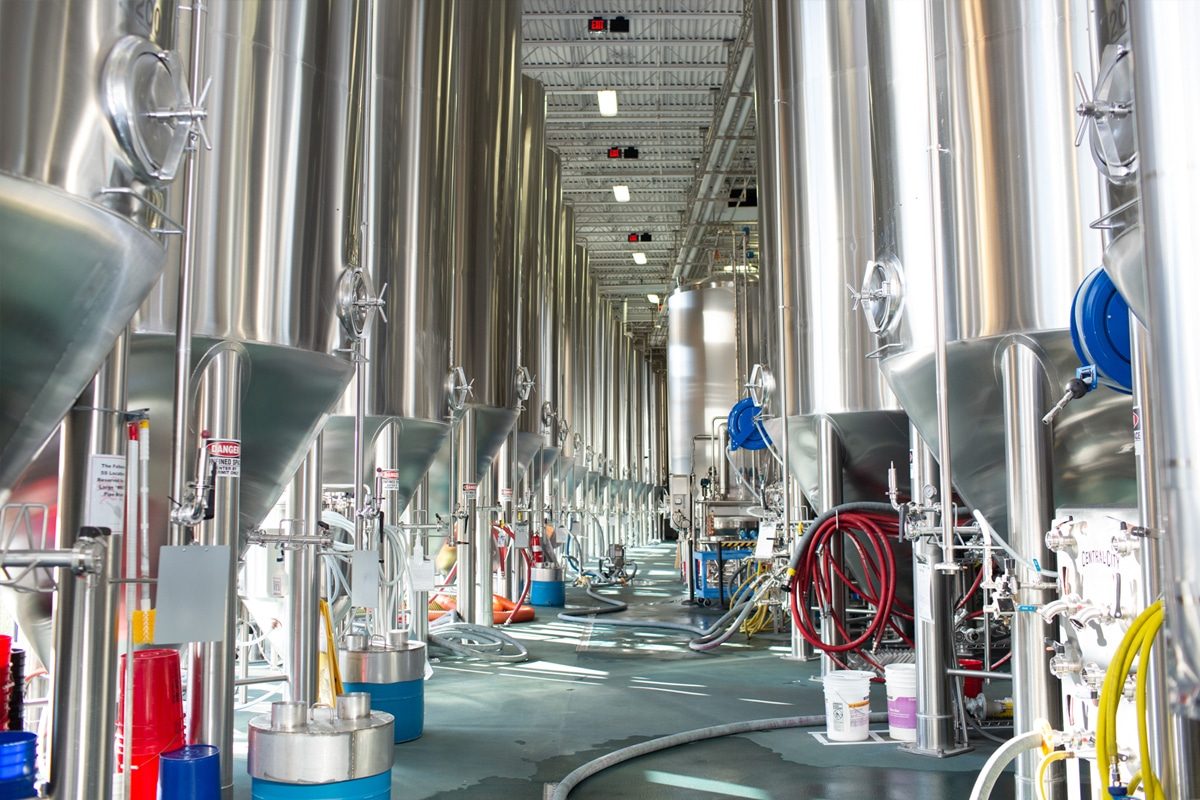
Limited Supplier Support
Longer Downtimes
Downtime in a brewery can be costly, affecting production schedules and potentially leading to revenue losses. Custom-built equipment, with its unique components and specifications, often experiences longer downtimes due to several factors:
- Specialized Parts Availability
- Custom Components: Custom equipment typically uses specialized parts that are not readily available in the market. When these parts fail or need replacement, the lead time to procure them can be significantly longer compared to standard parts.
- Supplier Dependence: Breweries may become heavily dependent on the original equipment manufacturer (OEM) for spare parts. If the supplier has limited stock or is located far away, obtaining the necessary components can take weeks or even months.
- Complex Repairs
- Unique Designs: Custom equipment often incorporates unique design elements that require specialized knowledge to repair. General maintenance staff may not have the expertise needed, necessitating the involvement of the OEM or specialized technicians.
- Diagnostic Delays: Identifying and diagnosing issues in custom-built equipment can be more time-consuming due to its bespoke nature. Standard diagnostic tools and procedures may not be applicable, requiring custom approaches.
- Service Availability
- Limited Field Technicians: The OEM may have a limited number of field technicians capable of servicing the custom equipment. Scheduling a visit from a technician can be delayed if they are not locally based or if their schedule is already full.
- Response Times: Limited supplier support often means longer response times for service requests. This delay can exacerbate the duration of downtimes, further impacting production.
Higher Maintenance Costs
Maintaining custom-built brewery equipment can be significantly more expensive compared to standard equipment. Several factors contribute to these higher maintenance costs:
- Specialized Maintenance
- Custom Maintenance Plans: Custom equipment requires bespoke maintenance plans tailored to its unique specifications. Developing and implementing these plans can be more complex and costly.
- Higher Expertise Requirements: Maintenance staff need specialized training and skills to service custom equipment effectively. This specialization often commands higher wages and can increase overall labor costs.
- OEM Dependency
- Exclusive Service Agreements: Breweries may be tied to exclusive service agreements with the OEM, which can be more expensive than using local maintenance providers. These agreements often include premium charges for parts and labor.
- Travel Costs: If the OEM’s technicians need to travel long distances to service the equipment, travel and accommodation expenses can add to the overall maintenance costs.
- Custom Parts
- Higher Part Costs: Custom parts are typically more expensive than standard parts due to their specialized nature and lower production volumes. This cost is further compounded if the parts are sourced internationally, involving import duties and shipping fees.
- Frequent Replacements: Unique parts may not have been tested as extensively as standard parts, leading to higher failure rates and more frequent replacements.
Training Requirements
Effective operation and maintenance of custom-built brewery equipment necessitate extensive training for brewery staff. The unique features and functionalities of custom equipment can pose several training challenges:
- Initial Training
- Comprehensive Onboarding: Staff need thorough training on the specific operations, safety procedures, and maintenance requirements of the custom equipment. This training is often provided by the OEM and can be time-consuming and costly.
- Training Materials: Developing detailed training materials, such as manuals, videos, and hands-on guides, is essential for effective learning but can involve significant effort and resources.
- Ongoing Training
- Continuous Updates: As custom equipment is upgraded or modified, continuous training is necessary to keep staff updated on new procedures and functionalities. This requires a sustained commitment to training programs.
- Skills Retention: Regular refresher courses are needed to ensure that skills and knowledge are retained over time, especially if the equipment is not used frequently or if there is staff turnover.
- Specialized Skill Sets
- Technical Expertise: Custom equipment may require staff to develop specialized technical skills that are not common in standard brewery operations. This includes advanced troubleshooting, calibration, and repair techniques.
- Cross-Training: To ensure operational continuity, multiple staff members should be cross-trained on the custom equipment. This redundancy helps mitigate the risk of key personnel being unavailable due to illness, vacation, or turnover.
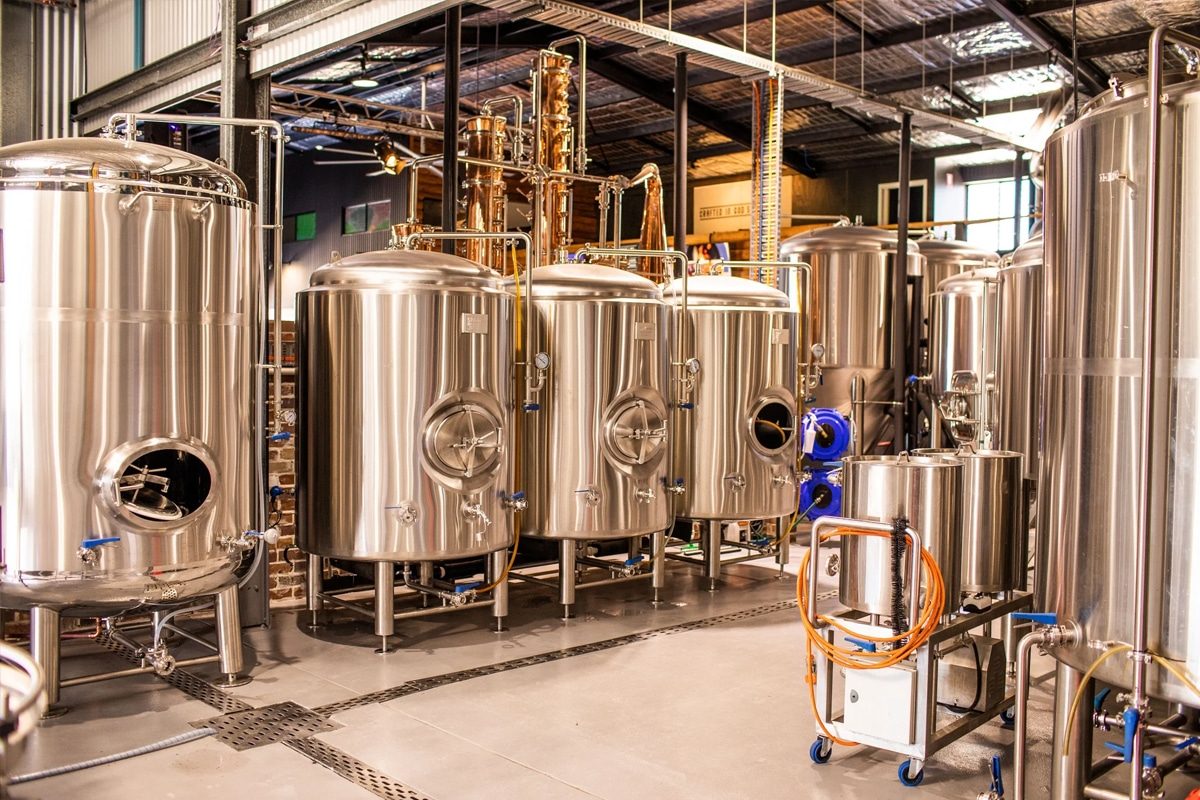
Maintenance and Repairs
Specialized Knowledge
Maintaining and repairing custom-built brewery equipment requires specialized knowledge and expertise, which can pose several challenges:
- Technical Expertise
- Unique Systems: Custom equipment is tailored to specific processes and may incorporate unique technologies and configurations. Technicians need in-depth knowledge of these systems to perform effective maintenance and repairs.
- Training Requirements: Breweries must invest in comprehensive training programs to equip their staff with the necessary skills. This training often needs to be provided by the equipment manufacturer, involving significant time and financial resources.
- Troubleshooting Skills
- Diagnostic Tools: Standard diagnostic tools and techniques may not apply to custom equipment. Technicians must be familiar with specialized diagnostic procedures to identify and resolve issues accurately.
- Experience: Effective troubleshooting requires hands-on experience with the specific equipment. Building this experience can take time, during which the brewery might face higher risks of prolonged downtimes due to slower problem resolution.
- Knowledge Retention
- Staff Turnover: High staff turnover can lead to a loss of specialized knowledge, necessitating continuous training efforts. Ensuring that multiple staff members are trained on the custom equipment can help mitigate this risk.
- Documentation: Maintaining detailed documentation of all maintenance and repair procedures is crucial for knowledge retention. This includes creating comprehensive manuals and logs of past issues and solutions.
Custom Parts
Custom-built equipment often utilizes unique components that are not readily available in the market, leading to several challenges related to parts procurement and management:
- Sourcing Difficulties
- Limited Availability: Custom parts are typically manufactured in limited quantities, making them harder to source. Breweries may need to rely on the original equipment manufacturer (OEM) for replacement parts, which can result in long lead times.
- Supplier Dependence: Breweries may become dependent on a single supplier for custom parts. Any disruption in the supplier’s operations, such as manufacturing delays or logistical issues, can significantly impact the brewery’s maintenance schedule.
- Higher Costs
- Manufacturing Costs: Custom parts often have higher production costs due to their specialized nature and lower production volumes. These costs are typically passed on to the brewery, increasing maintenance expenses.
- Shipping and Import Fees: If parts need to be sourced from international suppliers, additional costs such as shipping, import duties, and taxes can further escalate the total expenditure.
- Inventory Management
- Stocking Parts: Maintaining an inventory of critical custom parts can help mitigate delays but involves significant upfront investment. Breweries must balance the cost of stocking parts against the risk of extended downtimes.
- Inventory Turnover: Low turnover of custom parts can lead to inventory obsolescence, where stocked parts become outdated or incompatible with upgraded equipment. Effective inventory management strategies are essential to address this issue.
Routine Maintenance
Routine maintenance of custom brewery equipment ensures optimal performance and longevity. However, the unique nature of custom equipment can complicate routine maintenance activities:
- Customized Maintenance Plans
- Specific Requirements: Custom equipment may have unique maintenance requirements that differ from standard brewery equipment. Developing tailored maintenance plans that address these specific needs is crucial.
- Frequency and Scope: The frequency and scope of maintenance activities may need to be adjusted based on the equipment’s unique operational demands. This can include more frequent inspections, specialized cleaning procedures, and custom calibration routines.
- Resource Allocation
- Dedicated Personnel: Effective routine maintenance requires dedicated personnel with the necessary expertise to handle custom equipment. Allocating these resources can strain the brewery’s workforce, especially in smaller operations.
- Time and Effort: Custom equipment may require more time and effort to maintain due to its complexity. This includes longer inspection periods, more detailed cleaning processes, and intricate calibration tasks.
- Preventive Maintenance
- Predictive Tools: Implementing predictive maintenance tools and techniques can help identify potential issues before they lead to equipment failure. This requires investment in advanced monitoring systems and data analysis capabilities.
- Scheduled Downtimes: Planning and scheduling maintenance activities to minimize operational disruptions is crucial. This involves coordinating maintenance schedules with production plans to ensure minimal impact on brewing operations.
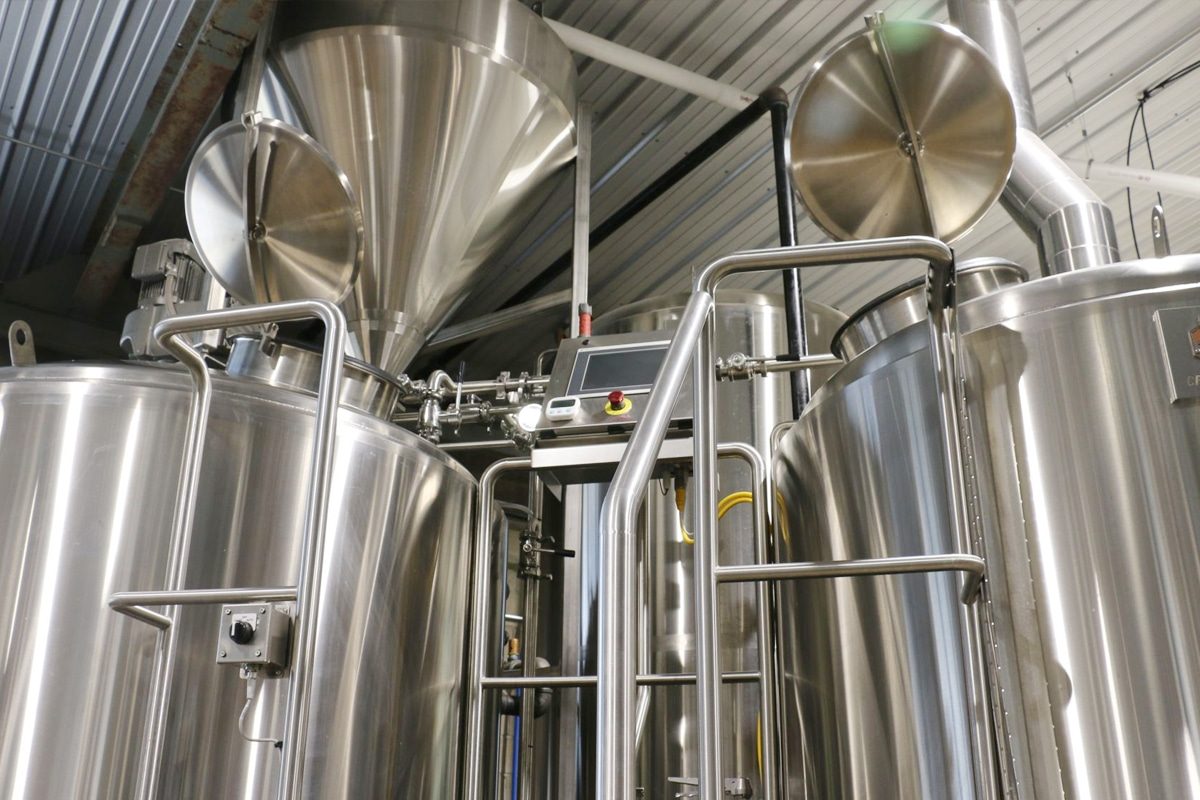
Scalability Issues
Capacity Limitations
Capacity limitations are a fundamental scalability issue that breweries encounter with custom-built equipment:
- Fixed Production Volumes
- Initial Design Constraints: Custom-built equipment is often designed to meet specific production volumes based on current needs. As demand grows, these fixed capacities can become a bottleneck, limiting the brewery’s ability to increase output without significant investment in additional equipment.
- Upgrading Challenges: Unlike modular systems, which can be easily expanded by adding more units, custom equipment often requires comprehensive redesigns to scale up. This can be both time-consuming and costly.
- Economic Viability
- Cost per Unit: Smaller breweries with custom equipment might find it economically challenging to produce larger volumes cost-effectively. The initial investment in custom-built systems does not easily scale, leading to higher costs per unit of production.
- Capital Expenditure: Expanding capacity with custom-built equipment typically involves significant capital expenditure. Securing the necessary funding can be a major hurdle, especially for small to mid-sized breweries.
- Operational Efficiency
- Optimal Utilization: Custom equipment is designed for specific operational parameters. Scaling up production can lead to inefficiencies if the equipment is not optimized for higher volumes, potentially resulting in increased waste or energy consumption.
Adaptability
Adaptability is another critical scalability issue with custom-built brewery equipment. As market trends and consumer preferences evolve, the ability to adapt to new brewing processes or products becomes essential:
- Process Flexibility
- Rigid Design: Custom-built equipment is often optimized for specific brewing processes. Adapting these systems to new processes, such as different beer styles or brewing methods, can be difficult and may require significant modifications.
- Limited Versatility: Equipment designed for particular specifications may not be versatile enough to handle variations in raw materials, brewing techniques, or product formulations. This lack of flexibility can hinder innovation and product diversification.
- Technological Integration
- New Technologies: Integrating new technologies into existing custom systems can be challenging. Custom equipment might not be compatible with the latest brewing innovations or automation technologies, limiting the brewery’s ability to modernize operations.
- Upgrade Pathways: Establishing clear upgrade pathways is essential for adaptability. Custom equipment should be designed with potential upgrades in mind, allowing for incremental improvements rather than complete overhauls.
- Regulatory Compliance
- Changing Regulations: Adapting to new regulatory requirements can be particularly challenging with custom-built equipment. Ensuring compliance may require retrofitting or redesigning existing systems, which can be both time-consuming and costly.
- Quality Standards: Maintaining consistent quality standards while adapting to new processes or products is crucial. Custom equipment needs to be flexible enough to ensure quality control across different production scenarios.
Space Constraints
Space constraints are a practical scalability issue that can significantly impact the expansion potential of a brewery using custom-built equipment:
- Physical Footprint
- Initial Space Utilization: Custom-built equipment is designed to fit specific spaces within the brewery. As operations expand, finding additional space for new equipment without disrupting existing workflows can be challenging.
- Space Optimization: Efficiently utilizing available space becomes more difficult with custom equipment, which may not be as compact or easily reconfigurable as standardized systems.
- Facility Expansion
- Infrastructure Limitations: Expanding a brewery’s physical infrastructure to accommodate additional custom equipment can involve significant construction work, including modifications to the building’s layout, plumbing, and electrical systems.
- Zoning and Permits: Facility expansion may also require navigating zoning laws and obtaining necessary permits, adding complexity and potential delays to scalability plans.
- Operational Disruptions
- Installation Impact: Installing new custom equipment in limited spaces can disrupt ongoing operations. Careful planning is required to minimize downtime and ensure that production can continue smoothly during expansion activities.
- Workflow Adjustments: Integrating new equipment into existing workflows may necessitate adjustments to operational procedures, which can impact productivity and efficiency during the transition period.
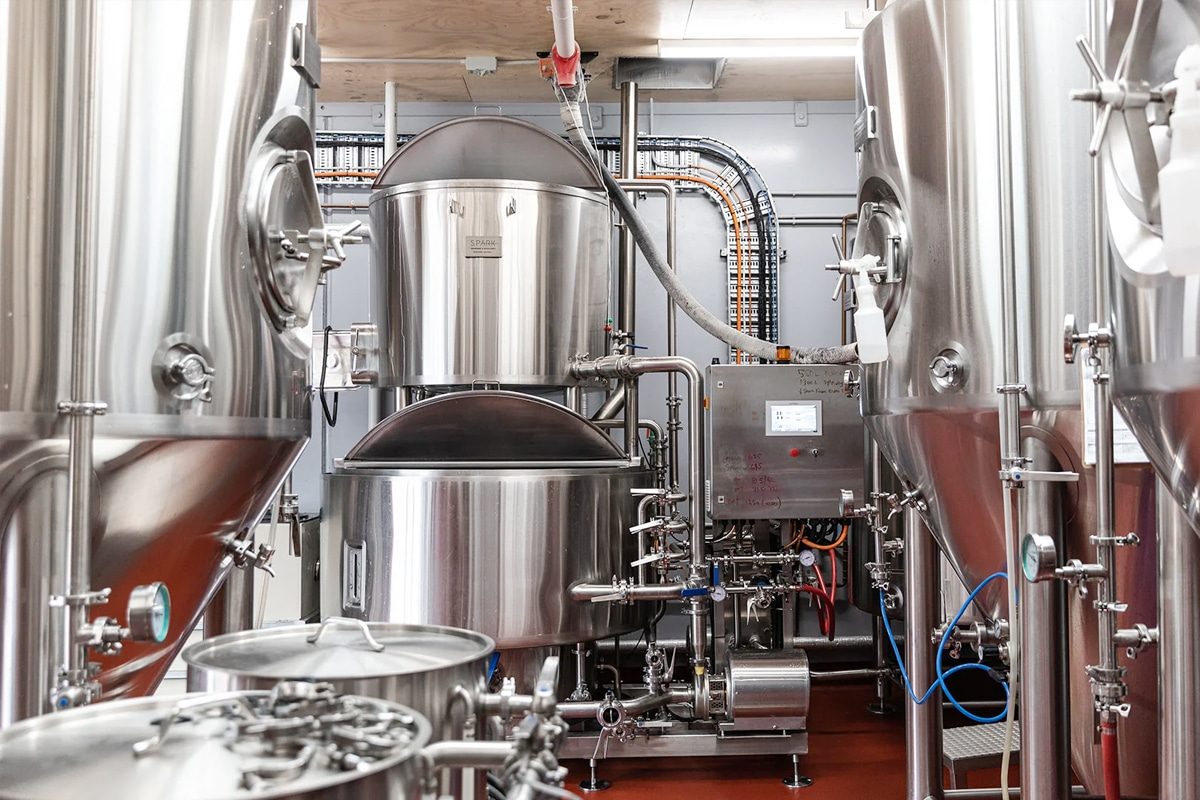
Quality Control Risks
Calibration Issues
Calibration is vital for the accurate and reliable operation of brewery equipment, ensuring that all measurements and processes are consistent and precise. However, custom-built equipment can present several calibration challenges:
- Unique Components
- Specialized Calibration Needs: Custom-built systems often use unique sensors and instruments that require specific calibration procedures. Standard calibration tools and techniques may not be applicable, leading to potential inaccuracies.
- Lack of Standardization: Unlike off-the-shelf equipment, custom-built systems may not adhere to industry-standard specifications, complicating the calibration process and increasing the risk of errors.
- Infrequent Calibration
- Maintenance Overlook: Regular calibration is crucial, but custom equipment might not be calibrated as frequently due to its specialized nature or the perceived complexity of the task. This can lead to a drift in measurements and compromised quality control.
- Resource Constraints: Smaller breweries may lack the specialized personnel or tools required for regular and precise calibration, further exacerbating the risk of calibration issues.
- Environmental Factors
- Operational Conditions: Custom equipment operating in environments with significant temperature and humidity variations can experience calibration drift. Ensuring consistent calibration under varying conditions is challenging but necessary for maintaining accuracy.
Process Variability
Process variability is a significant quality control risk that can affect the consistency and predictability of brewing operations. Custom-built equipment can introduce variability in several ways:
- Design-Specific Variability
- Customized Designs: The unique design of custom equipment can lead to inherent variability in operational parameters, such as temperature, pressure, and flow rates. These variations can impact the consistency of the brewing process and the final product.
- Component Interactions: Custom systems often involve complex interactions between various components. Any variability in one part can affect the overall process, leading to inconsistent product quality.
- Integration Challenges
- System Compatibility: Integrating custom-built equipment with existing systems can introduce compatibility issues, resulting in process disruptions and variability. Ensuring seamless integration requires careful planning and coordination.
- Operational Adjustments: Custom equipment may necessitate changes in standard operating procedures, which can lead to variability if not properly managed and standardized across the operation.
- Human Factors
- Operator Variability: The human element in operating custom equipment can introduce variability. Differences in operator experience, training, and adherence to procedures can affect the consistency of the brewing process.
Testing and Validation
Testing and validation are critical to ensuring that custom-built brewery equipment performs reliably and meets quality standards. However, custom equipment presents unique challenges in this area:
- Customized Testing Protocols
- Protocol Development: Custom-built systems may require the development of specific testing protocols tailored to their unique features and functionalities. This can be a resource-intensive process, requiring significant time and expertise.
- Baseline Establishment: Establishing baseline performance metrics for custom equipment can be challenging due to the lack of standardized benchmarks. Rigorous initial testing is essential to define these baselines.
- Continuous Validation
- Ongoing Assessment: Custom equipment must undergo continuous validation to ensure it maintains performance over time. This involves regular testing and adjustments to account for wear and tear, environmental changes, and other factors.
- Regulatory Compliance: Ensuring compliance with industry standards and regulations requires thorough and ongoing validation processes. Custom equipment must meet all relevant regulatory requirements to avoid legal and operational issues.
- Data Management
- Record Keeping: Maintaining detailed records of all testing and validation activities is crucial for tracking performance and identifying issues. This data is essential for troubleshooting and continuous improvement.
- Analysis and Reporting: Effective data analysis tools and techniques are needed to interpret testing and validation results. This helps in making informed decisions and implementing necessary adjustments.
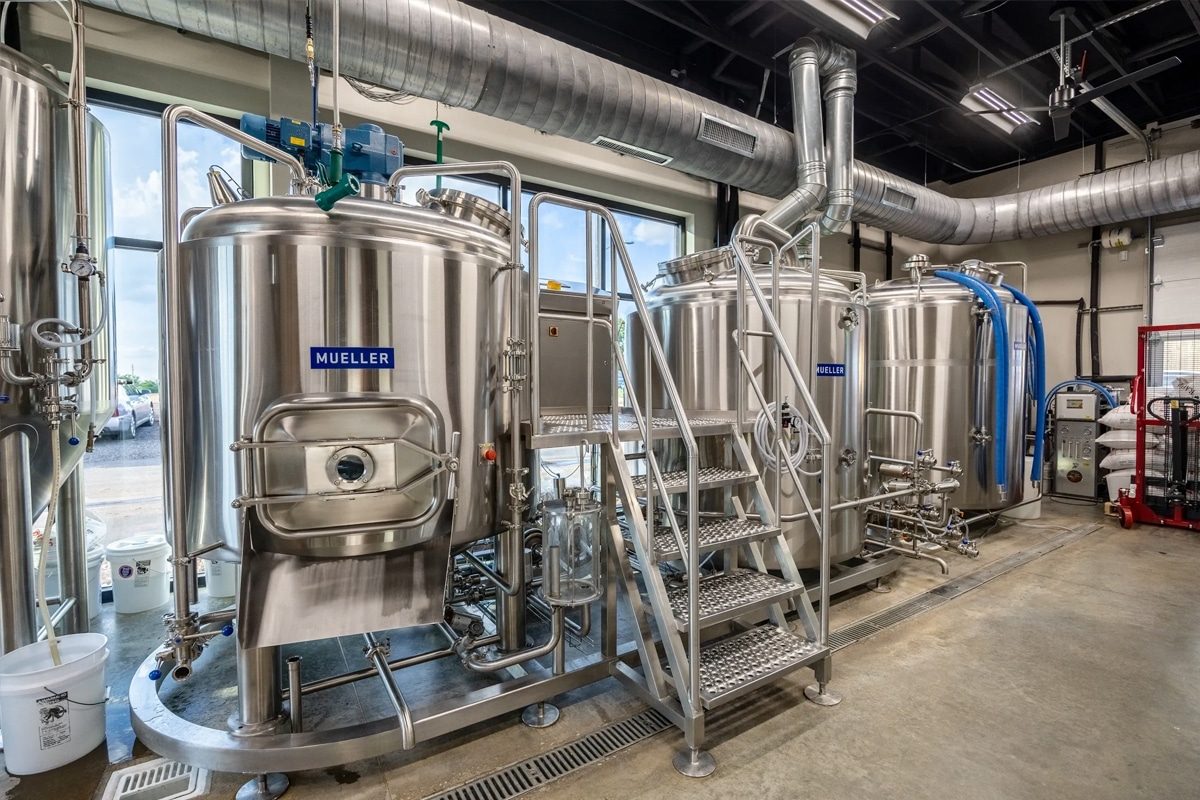
Regulatory Compliance
Safety Standards
Safety standards are designed to protect brewery workers, consumers, and the environment from potential hazards associated with brewing operations. Custom-built brewery equipment can present several challenges in meeting these standards:
- Design Considerations
- Unique Configurations: Custom-built equipment often features unique designs that may not conform to standard safety guidelines. Ensuring these designs meet all relevant safety standards requires thorough risk assessments and possibly additional safety features.
- Structural Integrity: Custom systems must be designed to handle specific pressures, temperatures, and mechanical stresses. Any miscalculation can lead to equipment failure, posing safety risks.
- Certification Requirements
- Complex Certification Processes: Obtaining safety certifications for custom-built equipment can be more complex and time-consuming compared to standard equipment. Custom designs may need to undergo extensive testing to demonstrate compliance with safety regulations.
- Specialized Documentation: Detailed documentation of the equipment’s design, materials, and construction processes is often required for certification. Compiling this information can be challenging, especially for one-of-a-kind systems.
- Ongoing Safety Monitoring
- Regular Inspections: Custom-built equipment may require more frequent and detailed safety inspections to ensure ongoing compliance. This can increase the operational burden and cost for breweries.
- Training Requirements: Employees need specialized training to safely operate and maintain custom equipment. Ensuring all staff are adequately trained can be a logistical challenge.
Hygiene Requirements
In the brewing industry, hygiene helps prevent contamination and ensure the safety and quality of the final product. Custom-built equipment can introduce specific hygiene challenges:
- Cleaning and Sanitation
- Complex Designs: Custom equipment may have intricate designs with hard-to-reach areas, making effective cleaning and sanitation difficult. Any residual contaminants can lead to product spoilage or health risks.
- Specialized Cleaning Protocols: Standard cleaning procedures may not be effective for custom equipment, requiring the development of specialized protocols. This adds complexity and potential for oversight.
- Material Selection
- Food-Grade Materials: Ensuring that all materials used in custom-built equipment are food-grade and resistant to corrosion and microbial growth is essential. Non-compliant materials can compromise hygiene and lead to contamination.
- Compatibility with Cleaning Agents: Custom equipment must be compatible with industry-standard cleaning and sanitizing agents. Incompatibility can lead to equipment damage or ineffective sanitation.
- Validation and Monitoring
- Sanitation Validation: Custom equipment requires thorough validation of cleaning and sanitation processes to ensure they are effective. This involves rigorous testing and regular monitoring.
- Continuous Monitoring: Implementing continuous monitoring systems to detect potential hygiene issues in real time can help maintain high hygiene standards, but it adds to the complexity and cost.
Environmental Regulations
Environmental regulations govern the impact of brewery operations on air, water, and soil quality. Custom-built equipment can complicate compliance with these regulations:
- Wastewater Management
- Effluent Treatment Systems: Custom-built equipment must include effective wastewater treatment systems to ensure that effluents meet regulatory discharge limits. Designing and maintaining these systems can be complex and costly.
- Variable Effluent Quality: Custom equipment might produce effluents with variable compositions, requiring adaptive and robust treatment solutions.
- Energy Efficiency
- Optimized Energy Use: Custom equipment might not be optimized for energy efficiency, leading to higher energy consumption and increased environmental impact. Retrofitting or redesigning equipment to improve energy efficiency can be challenging.
- Renewable Energy Integration: Integrating renewable energy sources with custom-built systems may require additional modifications, increasing complexity and cost.
- Waste Reduction
- Solid Waste Management: Custom processes can generate unique waste streams that need specialized handling and disposal methods to comply with environmental regulations.
- Recycling and Reuse: Designing custom equipment to facilitate recycling and reuse of materials can help reduce environmental impact but requires careful planning and additional resources.
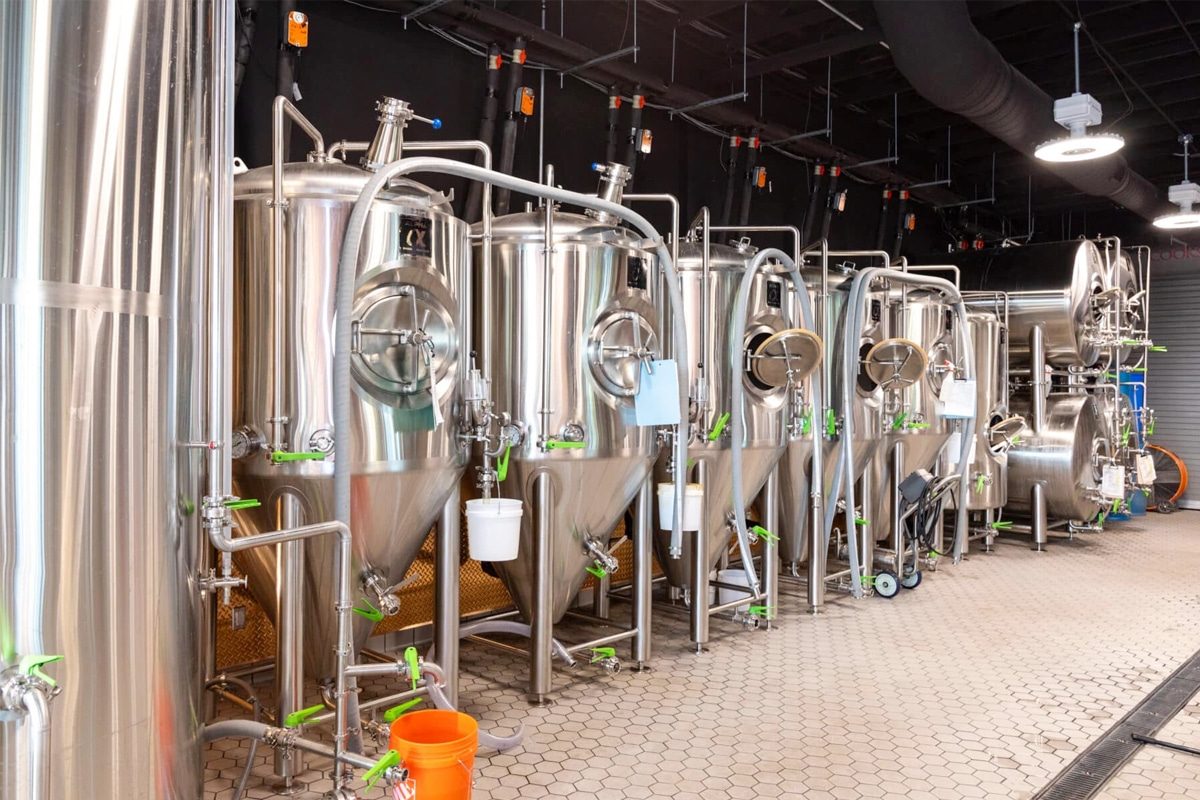
Resale Value
Specificity
Custom-built brewery equipment is designed to meet the unique requirements of a particular brewery. While this specificity can provide significant operational advantages, it poses challenges when it comes to resale:
- Limited Buyer Pool
- Tailored Designs: The customized nature of the equipment means it may not be suitable for other breweries with different production processes or scales. This limits the potential buyer pool to those with similar needs.
- Compatibility Issues: Custom equipment might be designed to integrate seamlessly with existing systems in the original brewery. For prospective buyers, adapting this equipment to fit their operations can be complex and costly.
- Unique Features
- Specialized Components: Custom-built equipment often includes unique components or features that are not commonly found in standard models. These specialized aspects can deter buyers who are unfamiliar with them or do not have the specific needs that the equipment was designed to address.
- Operational Constraints: Potential buyers may be concerned about the flexibility of custom equipment to adapt to their production requirements, leading to hesitancy in purchasing such systems.
Depreciation
Depreciation significantly impacts the resale value of any equipment, and custom-built brewery systems are no exception. Several factors contribute to the accelerated depreciation of custom-built equipment:
- Initial High Investment
- High Upfront Costs: Custom-built equipment often involves a higher initial investment compared to standard off-the-shelf equipment. This higher base cost can result in a steeper depreciation curve as the value decreases over time.
- Unique Design Costs: The costs associated with the unique design and engineering of custom equipment can also contribute to higher initial depreciation rates, as these elements may not hold their value well in the secondary market.
- Technological Obsolescence
- Rapid Advancements: The brewing industry, like many others, sees continuous technological advancements. Custom-built equipment may quickly become outdated as new technologies and more efficient systems are developed.
- Maintenance Costs: Older custom equipment may require more maintenance and repairs, further decreasing its attractiveness and value in the resale market.
- Market Perception
- Uncertain Longevity: Potential buyers might perceive custom-built equipment as riskier due to the uncertainty about its longevity and reliability, contributing to higher depreciation rates.
- Limited Warranties: Custom equipment may come with limited warranties, which can deter buyers and reduce the perceived value of the equipment.
Market Demand
Market demand plays a crucial role in determining the resale value of custom-built brewery equipment. Several factors influence demand in the secondary market:
- Industry Trends
- Market Preferences: The brewing industry’s preferences can shift over time, affecting the demand for specific types of equipment. Custom-built systems that were once highly desirable may fall out of favor as new brewing trends and technologies emerge.
- Production Scale Changes: Changes in the scale of production within the industry can also impact demand. Smaller craft breweries, for example, might not have the resources or need for large-scale custom equipment.
- Economic Factors
- Economic Climate: The overall economic environment influences capital investment decisions. During economic downturns, breweries may be less likely to invest in custom equipment, leading to lower demand and resale values.
- Financing Availability: Access to financing can affect the ability of potential buyers to purchase high-cost custom equipment. Limited financing options can reduce market demand and, consequently, resale values.
- Secondary Market Dynamics
- Supply and Demand Balance: The availability of similar equipment on the secondary market affects resale value. A surplus of custom equipment for sale can drive prices down, while limited availability can maintain higher prices.
- Buyer Sophistication: The level of sophistication and experience of buyers in the secondary market can influence demand. Buyers with specific technical knowledge and needs may be more willing to invest in custom-built equipment.
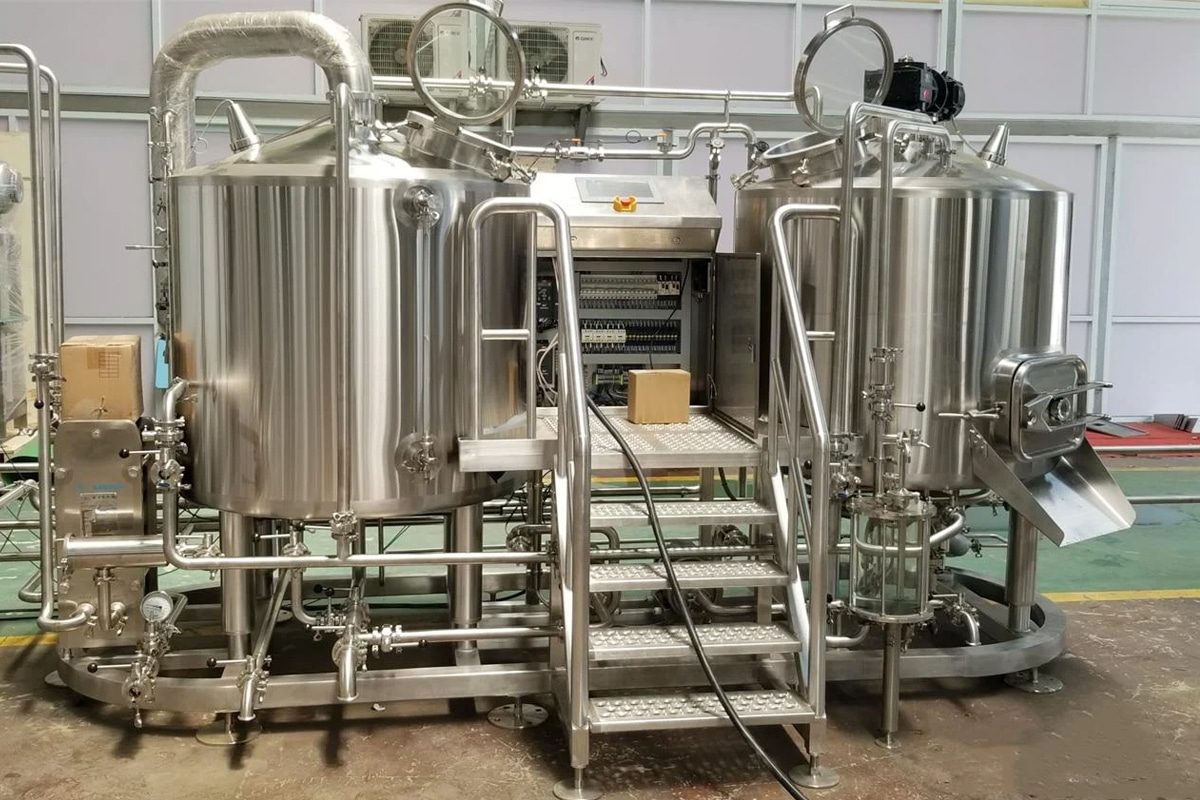
Strategies to Mitigate Problems
Thorough Planning and Design
Effective planning and meticulous design are foundational to mitigating potential problems with custom-built brewery equipment. This involves several key steps:
- Detailed Requirements Analysis:
- Operational Needs Assessment: Clearly define the specific needs of the brewery, including production capacity, type of products, and space constraints. Engage all relevant stakeholders to gather comprehensive requirements.
- Future-Proofing: Consider future growth and potential changes in production processes. Design equipment with scalability and adaptability in mind to accommodate future needs.
- Collaborative Design Process:
- Expert Consultation: Collaborate with experienced engineers and brewing consultants to develop a robust design. Their expertise can help identify potential design flaws and optimize the equipment for efficiency and safety.
- Iterative Prototyping: Use prototyping and simulation tools to test and refine the design before finalizing. This iterative process helps to identify and resolve issues early in the design phase.
- Regulatory Compliance:
- Standards and Certifications: Ensure the design adheres to all relevant safety, hygiene, and environmental standards. Plan for necessary certifications and approvals to avoid compliance issues later.
Vendor Selection and Relationships
Selecting the right supplier and cultivating strong relationships contributes to the successful implementation and operation of custom equipment:
- Vendor Evaluation:
- Experience and Expertise: Choose vendors with proven experience in designing and manufacturing custom brewery equipment. Review their past projects and client testimonials.
- Technical Capabilities: Assess the vendor’s technical capabilities, including their ability to handle complex designs, provide innovative solutions, and meet quality standards.
- Communication and Collaboration:
- Open Communication Channels: Establish clear and open communication channels with the vendor. Regular updates and feedback sessions can ensure that the project stays on track and any issues are promptly addressed.
- Collaborative Approach: Foster a collaborative relationship where both parties work together to address challenges and refine the design and implementation processes.
- Long-Term Support:
- Maintenance and Service Agreements: Negotiate comprehensive maintenance and service agreements to ensure ongoing support for the equipment. This includes regular maintenance, troubleshooting, and emergency repairs.
- Training and Documentation: Ensure the vendor provides detailed documentation and training for brewery staff to operate and maintain the equipment effectively.
Comprehensive Testing and Quality Control
Implementing rigorous testing and quality control measures can help ensure custom equipment operates reliably and meets quality standards:
- Pre-Installation Testing:
- Factory Acceptance Testing (FAT): Conduct thorough testing at the vendor’s facility to ensure the equipment meets all specifications and functions correctly. Address any issues before shipping.
- Performance Benchmarks: Establish clear performance benchmarks and test the equipment against these criteria to ensure it can meet production demands.
- On-Site Testing and Validation:
- Site Acceptance Testing (SAT): Perform detailed testing upon installation at the brewery to validate that the equipment integrates seamlessly with existing systems and operates as expected.
- Process Validation: Continuously monitor and validate the brewing process to ensure consistent quality and identify any deviations or inefficiencies.
- Continuous Quality Control:
- Ongoing Monitoring: Implement real-time monitoring systems to track equipment performance and process parameters. This helps in the early detection of potential issues and allows for timely corrective actions.
- Regular Audits: Conduct regular quality audits and inspections to ensure compliance with operational standards and regulatory requirements.
Staff Training and Support
Equipping brewery staff with the necessary skills and knowledge to operate and maintain custom-built equipment is vital for minimizing operational risks:
- Comprehensive Training Programs:
- Initial Training: Provide thorough training sessions for all relevant staff members on the operation, maintenance, and troubleshooting of the custom equipment. This should include both theoretical knowledge and hands-on practice.
- Ongoing Training: Offer continuous training programs to keep staff updated on new procedures, technologies, and best practices. This can include refresher courses and advanced training for specific roles.
- Support Resources:
- Detailed Manuals: Ensure that detailed operation and maintenance manuals are readily available. These should include step-by-step guides, troubleshooting tips, and safety protocols.
- Technical Support: Provide access to technical support from the vendor or an in-house team to assist with any issues that arise. This support should be available during critical production times.
Flexible Design for Scalability
Designing custom-built equipment with flexibility and scalability in mind can help accommodate future growth and changes in production processes:
- Modular Design:
- Expandable Systems: Implement a modular design approach that allows for easy expansion of production capacity. Modular components can be added or upgraded as needed without significant disruption.
- Interchangeable Parts: Use interchangeable parts and standardized components where possible to facilitate easy upgrades and replacements.
- Adaptability:
- Versatile Functionality: Design equipment to handle a variety of brewing processes and product types. This versatility can help the brewery adapt to market changes and new product development.
- Future-Proofing: Anticipate future technological advancements and industry trends. Ensure that the equipment can be easily upgraded to incorporate new technologies and improve efficiency.
Budgeting for Contingencies
Effective financial planning, including budgeting for contingencies, is essential to manage the risks associated with custom-built brewery equipment:
- Detailed Budget Planning:
- Comprehensive Cost Analysis: Conduct a thorough cost analysis that includes not only the initial purchase and installation costs but also long-term operational expenses such as maintenance, repairs, and energy consumption.
- Contingency Fund: Allocate a contingency fund to cover unexpected costs. This fund can help manage unforeseen issues such as design changes, equipment failures, or regulatory compliance upgrades.
- Financial Flexibility:
- Flexible Financing Options: Explore flexible financing options that can accommodate changes in project scope or unexpected financial needs. This might include lines of credit, leasing options, or phased payment plans.
- Cost Monitoring: Continuously monitor project costs and compare them against the budget. Implement cost-control measures to prevent overruns and ensure financial stability.
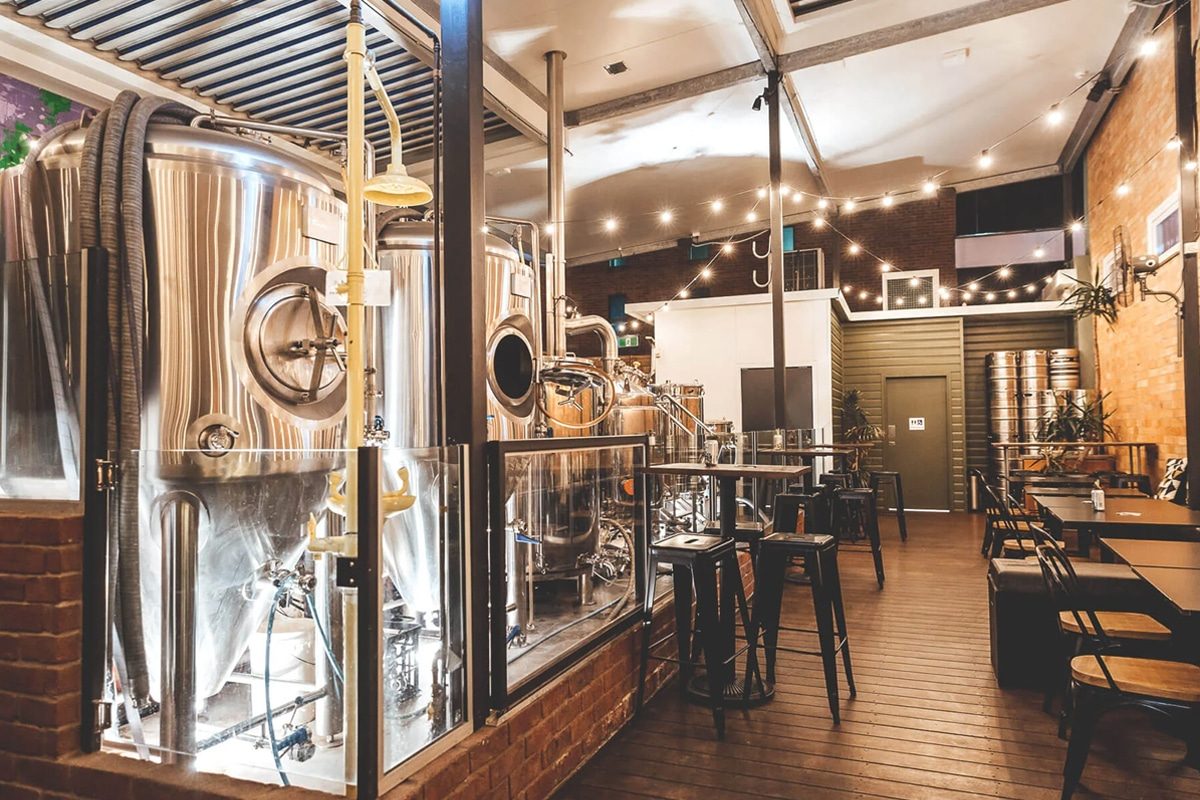
Summary
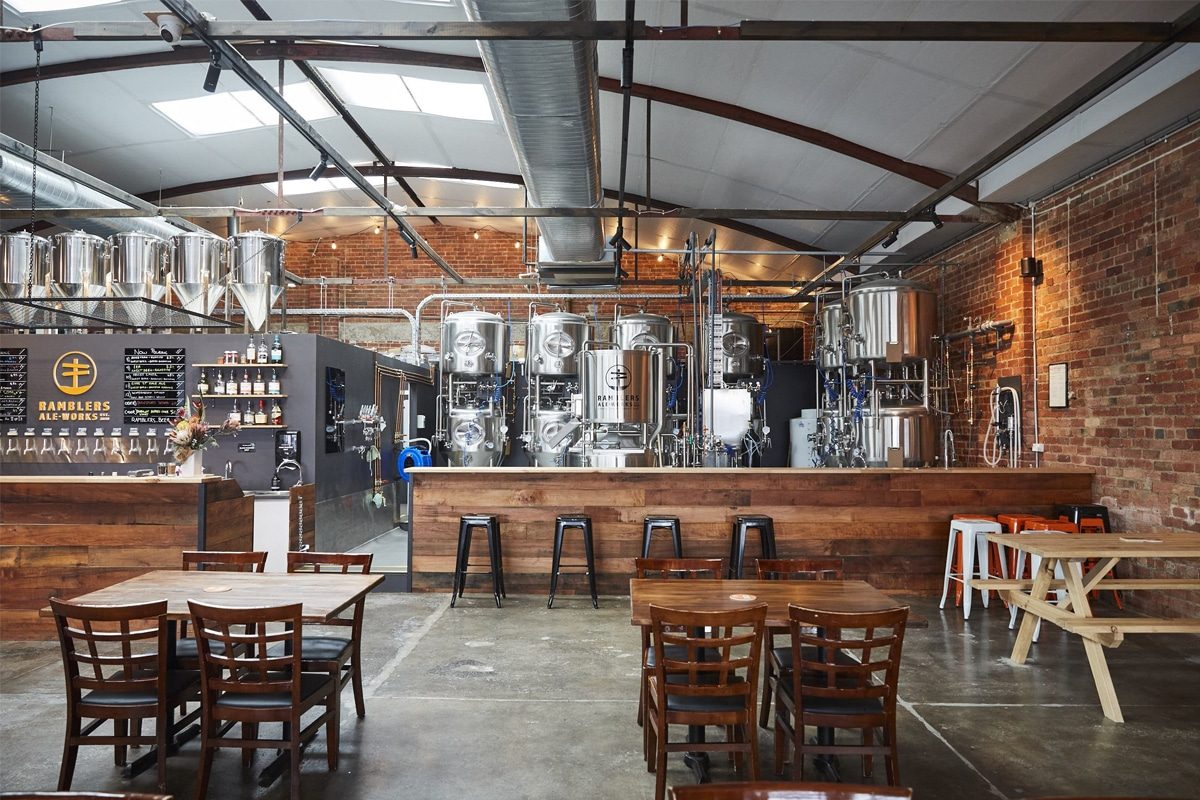