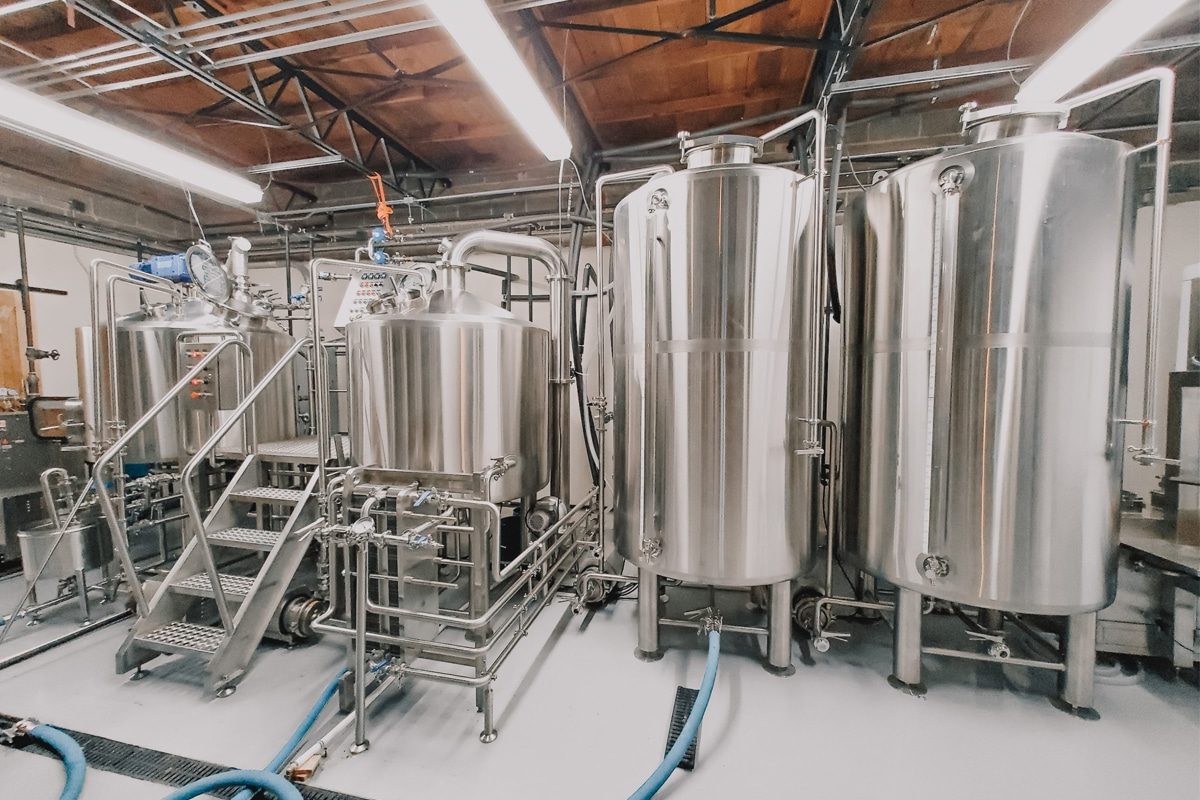
Use Cold Liquor Tank To Cool Wort—Pros & Cons
Brewing beer is an art, a subtle interplay of ingredients, processes, and equipment, all working in harmony to create the perfect beer. Of the many critical steps in the brewing process, cooling the wort is the most important. Wort is the sweet liquid extracted from mashed barley malt and needs to be effectively cooled before fermentation. In pursuit of optimal beer quality, brewers employ a variety of techniques, among which the use of cold wine tanks has become an important method. In this wide-ranging exploration, we’ll take a closer look at the world of wort cooling using cold liquid tanks, breaking down the pros and cons that brewers face in their pursuit of precision and excellence.
Complete Guide
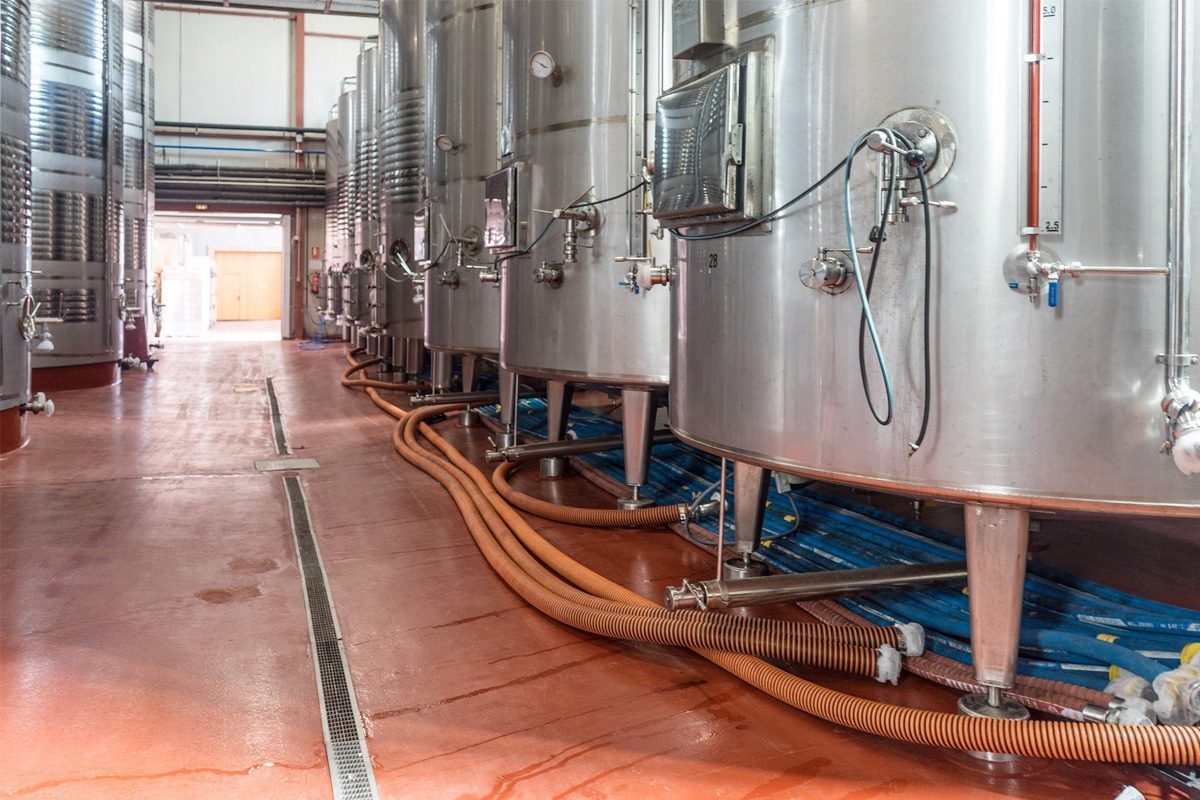
Understanding The Cold Liquor Tank
Definition And Function
Cold liquid tanks (CLT) are an indispensable asset in the complex modern brewing process. These specialized containers are designed to store and cool the water used in the brewing process. The main function of CLT is to act as a source of chilled water used to reduce the temperature of the hot wort after the mashing process. This critical role makes the cold brew tank central to thermal management in the brewery, influencing the final quality and characteristics of the beer produced.
Design And Components
The construction of the cold liquid tank consists of several complete components carefully integrated to ensure optimal functionality. Typically, a CLT includes solid insulation to maintain low temperatures, a cooling jacket to facilitate heat exchange, a temperature control system, and the usual ancillary equipment such as pumps and heat exchangers.
The insulation acts as a thermal barrier, maintaining the low temperatures required to store water. The cooling jacket surrounding the tank allows for efficient heat exchange, allowing the chilled water in the tank to effectively absorb heat from the hot wort.
Temperature control mechanisms, often automated, allow brewers to fine-tune the cooling process to ensure the wort reaches the ideal fermentation temperature. In some setups, heat exchangers are integrated into the CLT, capable of recovering heat from the wort to further optimize energy efficiency in the brewing process.
Wort Cooling Function
During the brewing process, after the wort is extracted and separated from the grains, it is exposed to high temperatures unsuitable for yeast fermentation. This is the important role of the cold wine tank. Chilled water from the CLT is circulated through the heat exchange system and comes into contact with the hot wort. This interaction promotes the transfer of heat from the wort to the cooler water, gradually lowering the temperature of the wort to the desired level conducive to fermentation.
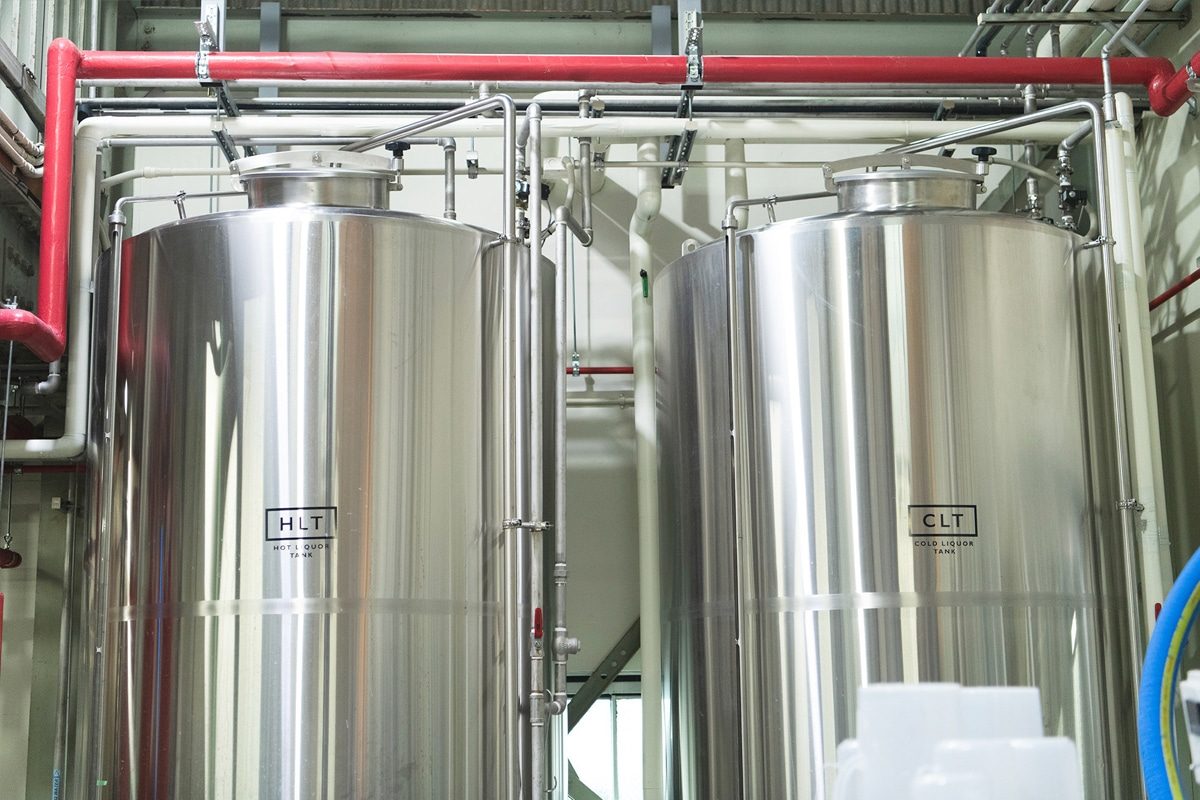
Pros of Using a Cold Liquor Tank
Precision And Control
One of the outstanding advantages of using a Cold Liquor Tank (CLT) is that it provides unparalleled precision in wort cooling. Brewers have fine control over the temperature of the cold liquid, allowing them to carefully regulate how quickly the wort is cooled. This meticulous control ensures that the wort always reaches the optimal fermentation temperature, helping to improve the overall quality and flavor profile of the beer.
Energy Efficiency And Heat Recovery
Integrating the cold liquid tank with a heat exchanger allows the heat of the wort to be recovered during the cooling process. The recovered heat can be reused in the brewing process, increasing overall energy efficiency. By harnessing and reusing thermal energy, brewers can not only reduce operating costs but also align their practices with sustainable brewing, minimizing environmental impact.
Process Flexibility And Consistency
Using a cold liquid tank allows brewers to standardize and simplify wort cooling procedures. This standardization ensures batch-to-batch consistency, a key factor in delivering consistent, high-quality products to consumers. The flexibility provided by CLT allows brewers to fine-tune and adjust cooling parameters to accommodate recipe changes while maintaining a consistent cooling process.
Minimize Contamination Risk
The cold liquid tank operates in a closed system, minimizing the risk of contamination during the cooling process. This closed-loop system helps maintain the hygiene and purity of the wort, protecting it from potential microbial threats. Ensuring a contamination-free environment makes a significant contribution to the overall quality and safety of the final beer product.
Improve Wort Quality
The controlled and gradual cooling facilitated by CLT helps improve wort quality. The gentle cooling process helps preserve the delicate flavors and aromas produced during the brewing process, which ultimately affects the final taste of the beer. Brewers can take advantage of cold wine tanks to produce a more refined, nuanced product.
Improve Wort Clarity
The gradual cooling promoted by CLT helps precipitate unwanted proteins and solids from the wort. This gradual settling improves the clarity of the wort and provides the basis for a visually appealing refined beer.
Improve Batch-To-Batch Consistency
Cold liquid tanks play a key role in achieving consistent cooling of multiple batches. The reliability and repeatability of the cooling process contribute to a standardized production environment. Brewers can confidently replicate successful brewing parameters, ensuring each batch of beer maintains desired characteristics and meets quality standards.
Operational Efficiency
The precision and efficiency provided by CLT translate into time savings during the brewing process. Controlled cooling allows for faster, more predictable transitions between brewing stages, helping to improve overall operational efficiency. Reducing processing time can be a key factor in meeting production demands and optimizing resource utilization.
Enhance Operational Control
The addition of a cold liquid tank gives brewers increased operational control. By having dedicated cooling vessels, breweries can streamline processes, optimize production schedules, and fine-tune cooling parameters to suit specific beer styles or recipes.
Brewery Size Adaptability
Cold liquid tanks can be adapted to a variety of brewery sizes. Whether in a small craft brewery or a large production facility, CLT’s modular nature allows for scalability. Breweries can adjust the size and capacity of the CLT to meet their specific production requirements, providing a flexible solution that matches the changing needs of the brewery.
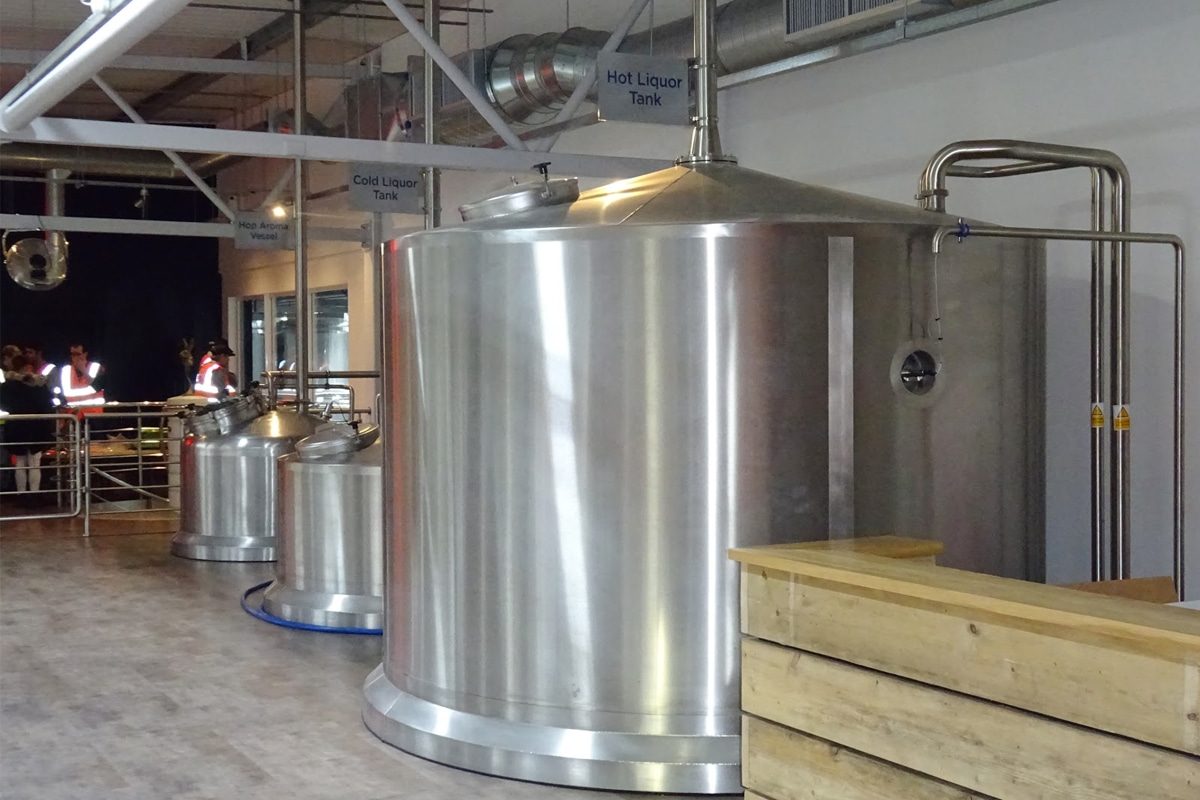
Cons of Using a Cold Liquor Tank
Initial Capital Investment
One of the major disadvantages of implementing a cold liquid tank (CLT) is the large initial capital investment required. Purchasing storage tanks, installing related equipment, and integrating control systems can place a significant financial burden on a brewery, especially a small brewery with a limited budget.
Space Limitations And Footprint
Cold liquid tanks typically have a large footprint and require a significant amount of space within the brewing facility. In smaller or cramped breweries, space optimization is critical, and the size of the CLT can create challenges in layout and efficient use of available space.
Maintenance Complexity
The complexity of cold liquid tanks and their complex cooling systems and associated components means stringent maintenance requirements. Regular maintenance helps ensure optimal performance and prevent potential problems that could affect the quality of your chilled wort. Maintenance complexity increases operating expenses and requires skilled personnel to perform maintenance.
Energy Consumption
While cold liquid tanks help improve energy efficiency through heat recovery, the cooling process itself can require significant amounts of electricity. Breweries must carefully weigh the environmental impact and energy consumption costs against the benefits of using CLT. High energy consumption increases operating costs and environmental concerns.
Operational Complexity
Integrating a cold liquid tank into the brewing process creates additional complexities. Managing tank operations, monitoring temperature controls, ensuring proper circulation, and troubleshooting potential problems add to the complexity of the operation. Breweries may need specialized training for employees to handle CLT effectively.
Risk of Mechanical Failure
Like any mechanical system, cold liquid tanks are prone to failure. Technical issues, such as pump failure or temperature control system problems, can disrupt the wort cooling process and affect the entire brewing operation. Breweries must have contingency plans in place to address potential mechanical failures promptly.
Limited Adaptability to Certain Beers
The controlled and gradual cooling promoted by CLT, while beneficial for many beer styles, may not be ideal for certain beers that require a rapid or specific cooling profile. Breweries brewing a variety of beer styles may want to consider alternative cooling methods for certain recipes.
Dependence on Infrastructure
The effective operation of cold liquid tanks relies on supporting infrastructure, such as a reliable power supply, efficient water circulation system, and sufficient maintenance resources. Any disruptions or deficiencies in this infrastructure may impact the performance of the CLT and thus the brewing process.
Adaptation Challenges For Small Breweries
The size and dimensions of cold wine tanks may not be suitable for small breweries with limited production volumes. The investment in CLT and the space it takes up may not be commensurate with the size and production capabilities of a small brewing facility, making it less practical for some setups.
Limited Flexibility For Process Changes
Once installed, making major modifications or changes to the cold liquid tank setup can be challenging. This limitation in flexibility can create limitations in adapting to changes in brewing technology, throughput, or operational requirements.
Environmental Considerations
The production and operation of cold liquid tanks involve the use of materials and resources. Breweries committed to sustainable practices may need to evaluate the environmental impacts of manufacturing and operating CLT, considering factors such as raw material extraction, manufacturing processes, and end-of-life disposal.
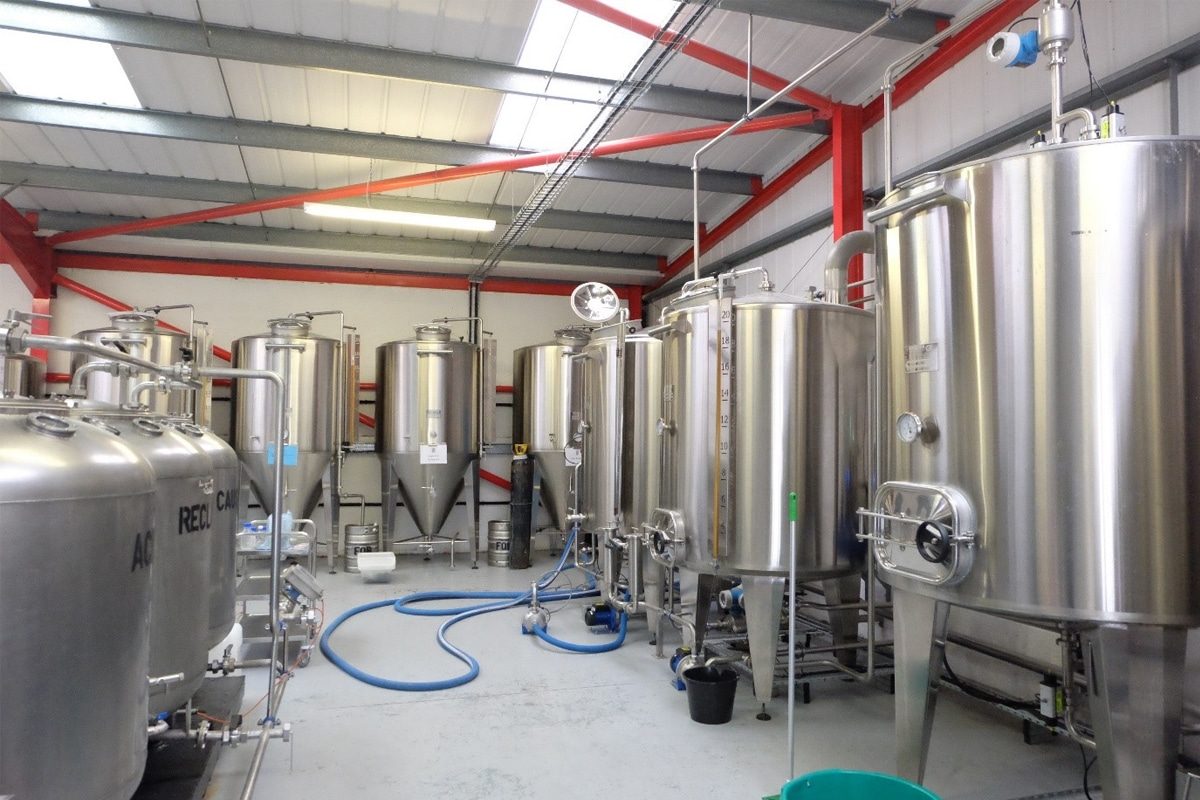
How Much Cold Liquor Tank Do You Need?
Determining the proper size and capacity of the cold liquid tank (CLT) is a critical decision for breweries looking for optimal efficiency in their wort cooling process. Correct sizing ensures the CLT meets the needs of the brewing operation, balancing production requirements with considerations of space, energy consumption, and overall cost-effectiveness. Here’s a closer look at the factors to consider when deciding how many cold liquid tanks you need:
Batch Size
The size of the CLT should align with the brewery’s typical batch size. Larger batch sizes necessitate a proportionally larger CLT to ensure an adequate supply of chilled water for efficient wort cooling. Understanding the average production volume is foundational in determining the optimal capacity.
Cooling Time Requirements
Consider the desired cooling time for the wort. A larger CLT allows for faster cooling due to a greater volume of chilled water available. However, it’s essential to strike a balance, as excessively rapid cooling may impact beer quality. Evaluate the cooling requirements for your specific brewing process and find a capacity that optimally balances speed and precision.
Temperature Differential
The temperature difference between the hot wort and the chilled water is a critical factor. A larger temperature differential allows for quicker cooling. However, the achievable difference between them may be influenced by the design and efficiency of the CLT’s cooling system. Consult with brewing engineers to calculate the required temperature difference for your specific process and adjust CLT size accordingly.
Heat Recovery Considerations
If your brewery employs heat exchangers to recover heat from the wort, the CLT capacity should accommodate the additional thermal load. The heat recovered can be repurposed for various brewing processes, contributing to energy efficiency. Ensure that the CLT is sized to support both the wort cooling requirements and potential heat recovery systems.
Frequency of Brewing
Consider how frequently brewing operations occur. Breweries with high production frequencies may benefit from a larger CLT that can handle continuous cooling cycles without compromising performance. Conversely, smaller breweries with less frequent brewing may find a smaller CLT more suitable for their needs.
Space Constraints
While a larger CLT might offer advantages in terms of cooling capacity, it’s essential to assess the available space within the brewery. Balancing the desired capacity with the physical footprint of the CLT ensures optimal space utilization and efficient integration into the brewing facility.
Future Expansion Plans
Anticipate future growth and expansion. Investing in a CLT with scalability in mind allows the brewery to accommodate increased production volumes without the need for immediate equipment upgrades. This forward-thinking approach ensures that the CLT remains a viable and cost-effective solution as the brewery evolves.
Water Quality and Availability
The characteristics of the water source used for cooling can impact CLT performance. Analyze factors such as water temperature variations and quality fluctuations. A larger CLT may provide buffering capacity to handle variations in water conditions, ensuring consistent cooling results.
In conclusion, determining the appropriate size of a Cold Liquor Tank is a nuanced process that requires a thorough understanding of the brewery’s production requirements, cooling objectives, and future aspirations. Collaborating with brewing engineers and experts can provide valuable insights and ensure that the chosen CLT size aligns seamlessly with the brewery’s unique needs.
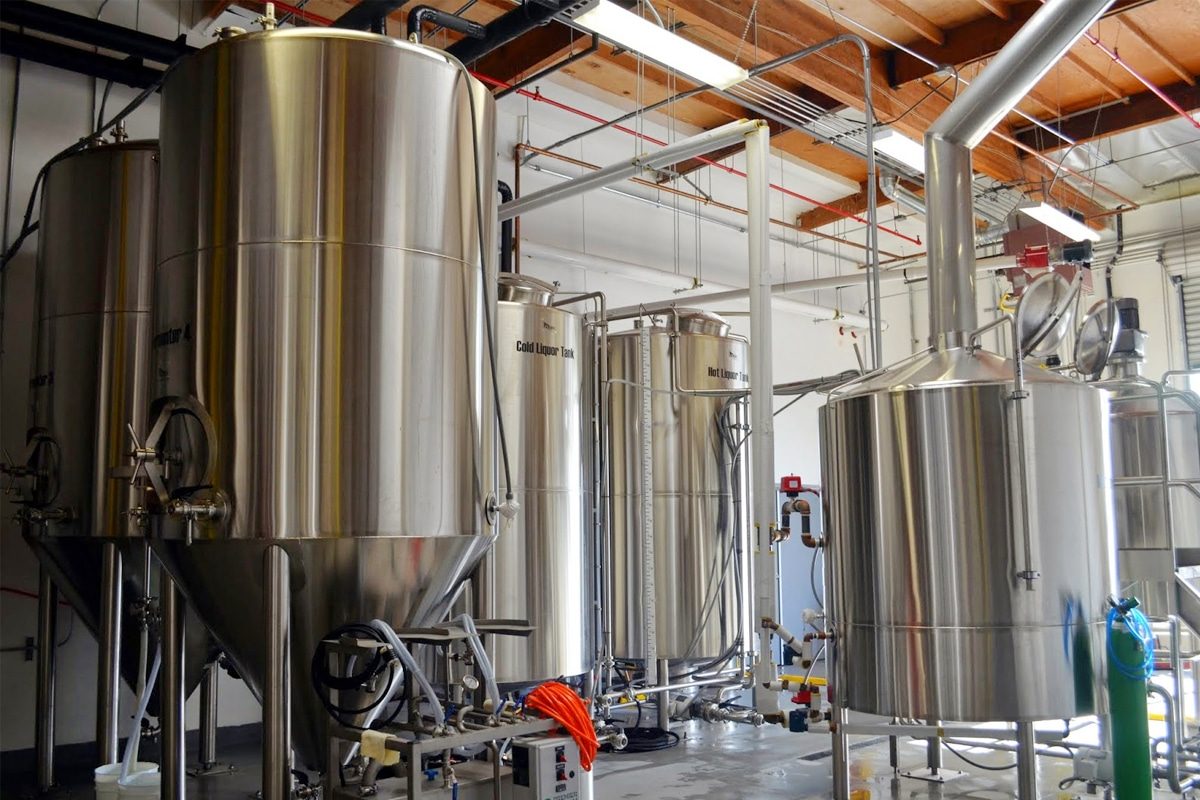
Striking The Balance: Optimizing Cold Liquor Tank Size for Wort Cooling
Determining the ideal size for a Cold Liquor Tank (CLT) is akin to orchestrating a delicate symphony in the brewing process. Striking the right balance ensures efficient wort cooling, operational smoothness, and cost-effectiveness. Here, we delve into the considerations and strategies for optimizing CLT size to achieve the perfect harmony:
Understanding Production Dynamics
Tailoring the CLT size to the brewery’s production dynamics is paramount. Assess the average batch size, production frequency, and overall demand to determine the capacity required. A nuanced understanding of production nuances lays the foundation for an appropriately sized CLT.
Analyzing Cooling Time Objectives
The desired cooling time for the wort influences CLT size. A larger CLT facilitates faster cooling due to a greater volume of chilled water. However, brewers must carefully calibrate the size to strike a balance between speed and precision. Maintaining an optimal cooling rate is crucial for preserving beer quality and flavor profiles.
Evaluating Heat Recovery Potential
Breweries employing heat exchangers for heat recovery need a CLT that accommodates this additional thermal load. Integrating systems for heat exchange enhances energy efficiency but necessitates a CLT size that aligns with both wort cooling requirements and heat recovery objectives.
Considering Space Constraints
Balancing CLT capacity with the available space within the brewery is essential. Opting for a size that maximizes efficiency without compromising floor space ensures a harmonious integration into the brewing facility. The layout should promote operational fluidity while accommodating the required CLT size.
Adapting to Seasonal Variations
Breweries in regions with seasonal variations in water temperature should consider the impact on CLT performance. A larger CLT can provide a buffer against fluctuations, ensuring consistent cooling results even when external factors pose challenges.
Scaling for Future Growth
Anticipating future growth and expansion is a strategic consideration. Choosing a CLT with scalability allows the brewery to evolve without necessitating immediate equipment upgrades. Future-proofing investments by selecting a CLT that aligns with expansion plans ensures long-term viability.
Strategic Water Source Management
The quality and characteristics of the water source used for cooling play a pivotal role. Larger CLTs can provide flexibility in handling variations in water quality and temperature. Assessing water source parameters ensures that the CLT is equipped to adapt to diverse conditions.
Collaborating with Brewing Experts
Collaborating with brewing engineers and industry experts adds a layer of expertise to the decision-making process. Their insights can help navigate complexities, optimize CLT size, and fine-tune the brewing system for peak performance. Professional guidance ensures that the CLT is a tailored solution aligned with the brewery’s unique requirements.
In the symphony of brewing, where precision and efficiency dance in tandem, the Cold Liquor Tank plays a crucial role. Striking the right balance in CLT size requires a thoughtful blend of production insights, cooling objectives, and future vision. By carefully orchestrating these elements, brewers can ensure that the Cold Liquor Tank becomes a harmonious conductor, orchestrating the perfect cooling cadence for the creation of exceptional beer.
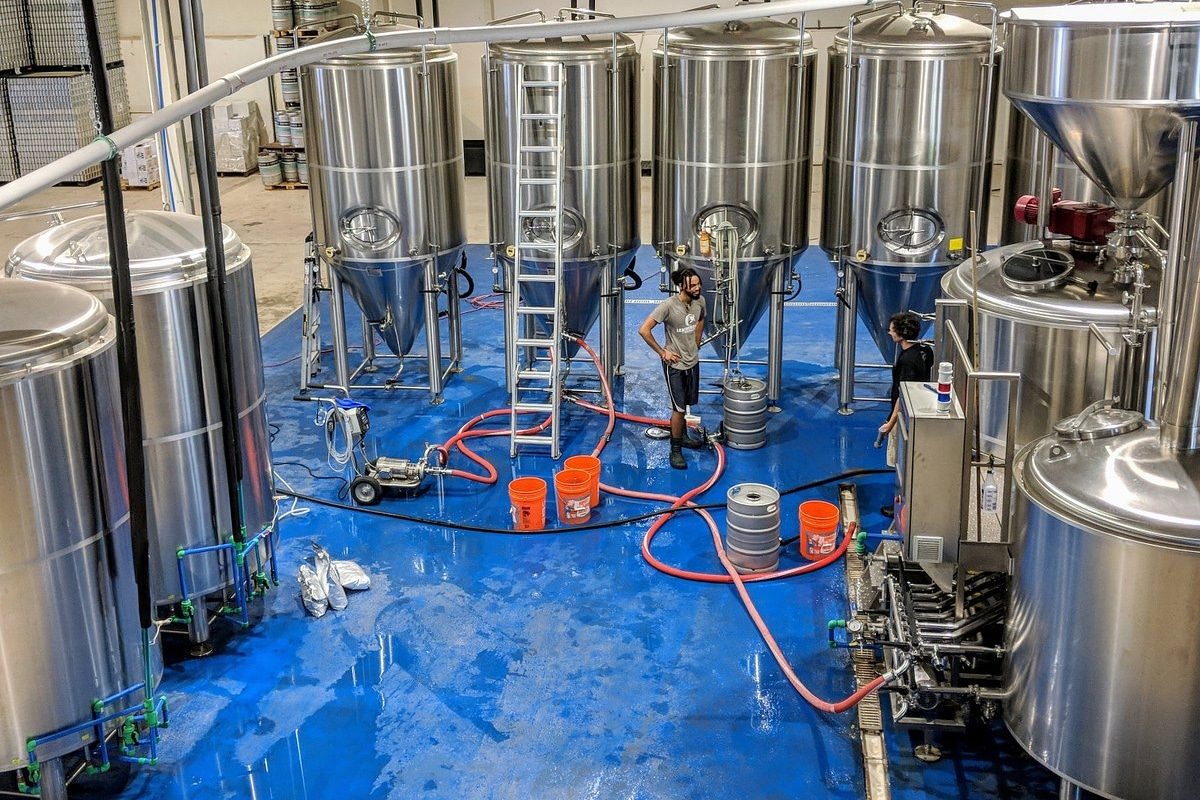
Summary
The utilization of Cold Liquor Tanks (CLTs) in wort cooling presents a dichotomy of advantages and challenges in the brewing landscape. These tanks offer brewers unparalleled precision, energy efficiency through heat recovery, and process consistency. However, the initial capital investment, maintenance complexities, and space requirements pose significant considerations. Striking the right balance in CLT size involves understanding production dynamics, heat recovery potential, and adaptation to varying water source characteristics.
In this delicate orchestration of brewing techniques, the choice of employing a Cold Liquor Tank necessitates a thoughtful evaluation of trade-offs. Breweries must navigate between the advantages of precise cooling control and the considerations of cost, space, and operational complexities to craft a wort cooling strategy aligned with their unique brewing objectives.
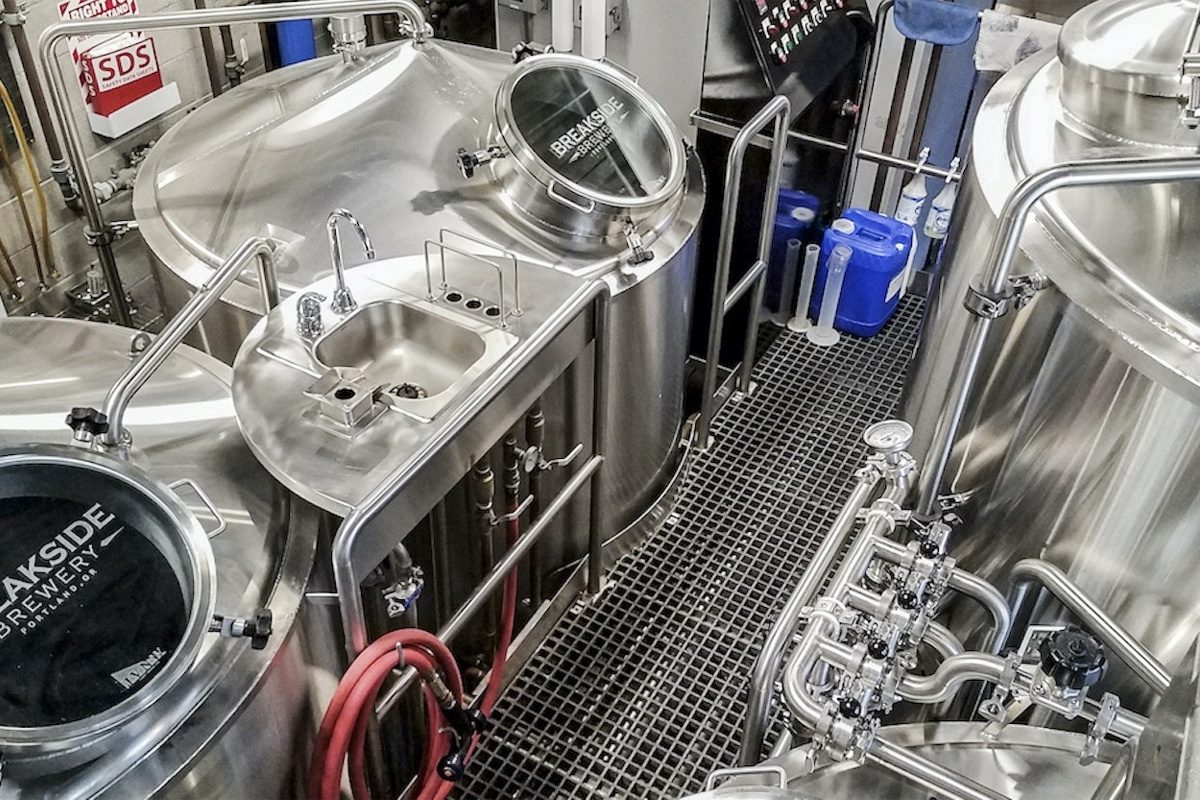
Get A Turnkey Brewery Solution
Embarking on the journey of creating exceptional beer involves a meticulous blend of artistry and technology. For those seeking a comprehensive and seamless brewing experience, considering a Turnkey Brewery Solution becomes paramount. ZYB Craft stands as a beacon in the brewing industry, offering expertise and innovation to guide brewers through the intricacies of implementing Cold Liquor Tanks (CLTs) for wort cooling. Contact ZYB Craft today to embark on a journey towards brewing excellence with a Turnkey Brewery Solution tailored to your unique needs.