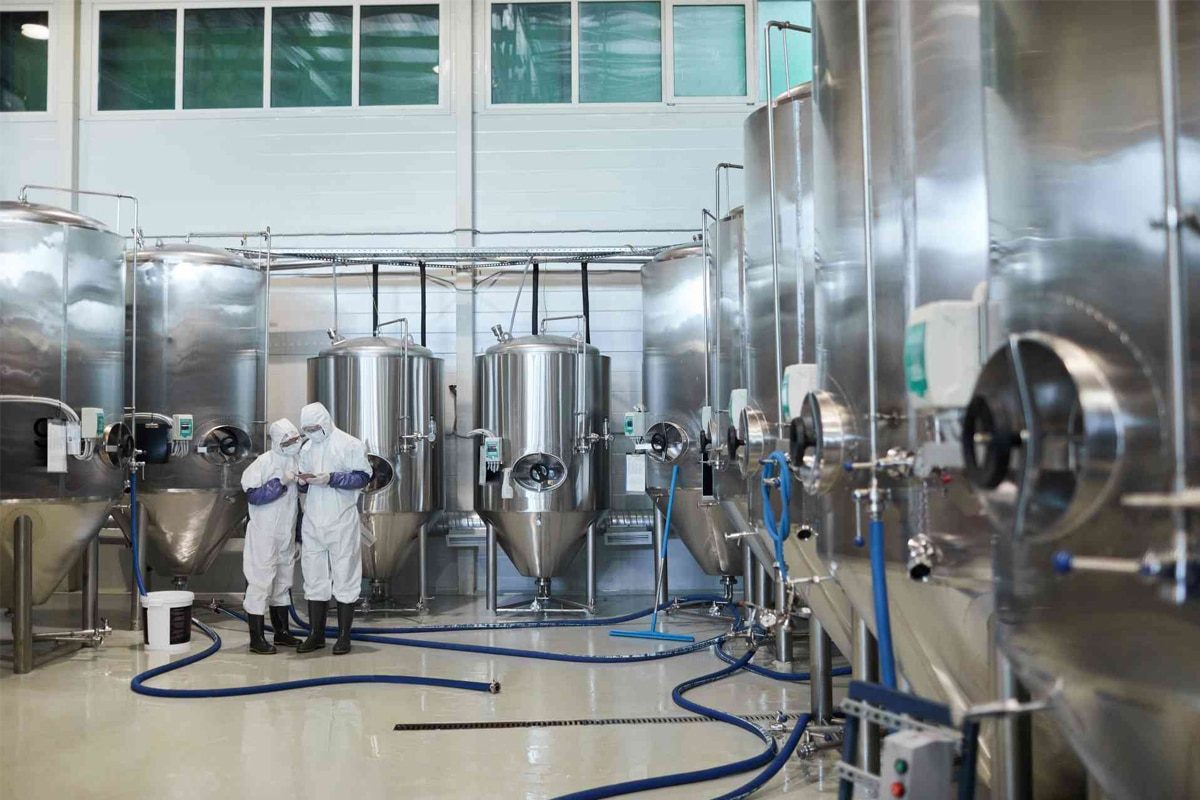
Uncovering Brewery Hazards: Keeping Your Brewing Operation Safe
Entering the beer factory, you will encounter a world full of bubbling fermentation tanks and aromatic beer, which proves the art and accuracy behind each product. However, in the creativity and craftsmanship, there is a less charming reality: there are many dangers during the brewing process. From the processing of raw materials to the operation of complex machinery, the beer factory is full of risks that need attention and caution. In this article, we have deeply studied the complexity of the harm of the beer factory and discussed the various dangers faced by the front-line workers of beer production. By understanding these hazards and implementing strong security measures, the beer plant can protect its employees, maintain quality standards, and ensure the sustainable success of its craftsmanship.
Complete Guide
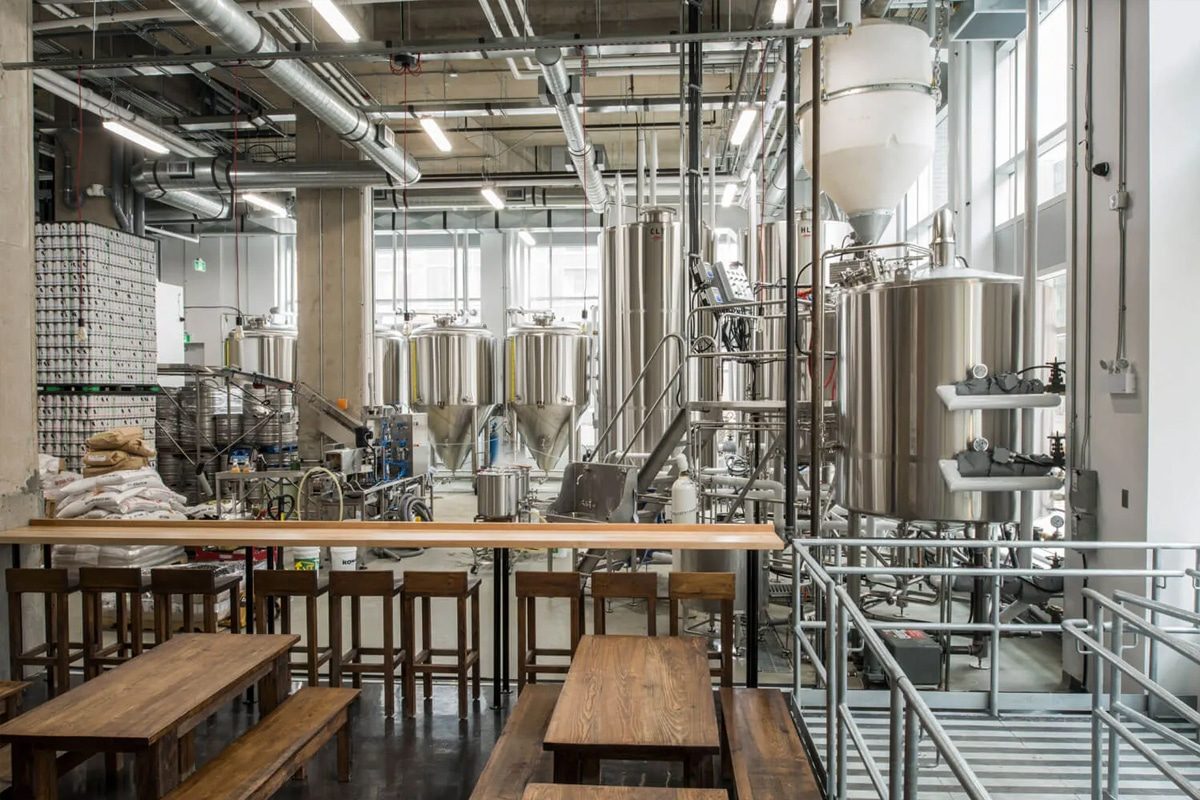
Rural and material treatment danger
In the intricate brewing dance, the entire journey starts with the selection and processing of raw materials. From grain to beer and yeast, each component will bring unique harm to the brewing process.
Grain treatment danger
- Grain Dust: Grain grinding will produce dust particles in the air. If it is ignited, it will bring huge explosive risks. Inhaling grain dust can also cause respiratory diseases, such as asthma and bronchitis. Proper ventilation and dust control measures can reduce this risk.
- Counteracting Space: There may be a risk of confinement space for storing grain, including the risk of suffocation due to gases such as carbon dioxide. Sufficient ventilation and closed space protocol must be implemented to ensure the safety of workers.
Beer and yeast harm
- Skin Stimulus: The exposure to exposure to beer can cause skin irritation and allergic reactions. When dealing with beer flowers, you should wear appropriate personal protection equipment (PPE), including gloves and long sleeves to prevent skin exposure.
- Carbon Dioxide Exposure: During the fermentation process, yeast will produce carbon dioxide (CO2), and carbon dioxide will accumulate in a poorly ventilated area and replace oxygen, leading to suffocation. Proper ventilation and monitoring systems help prevent carbon dioxide accumulation and ensure a safe working environment.
Storage and processing risk
- Heavy Object Handling: If you do not follow the correct handling technology, carrying valley bags and mobile devices may cause muscle and bone injury. Training for safety lifting practice and mechanical auxiliary equipment can help reduce this risk.
- Storage Conditions: Improper storage of raw materials may lead to corruption and pollution. Grain should be stored in dry and ventilated places to prevent molds from growing, and beer flowers should be stored in sealed containers to maintain their freshness and aroma.
There are many dangers in the treatment of the raw materials of brewerys, and they must be carefully managed to ensure the safety of workers and the quality of the final product. By implementing appropriate processing procedures, training, and security measures, the beer factory can minimize risks and create a safer working environment for all employees participating in the brewing process.
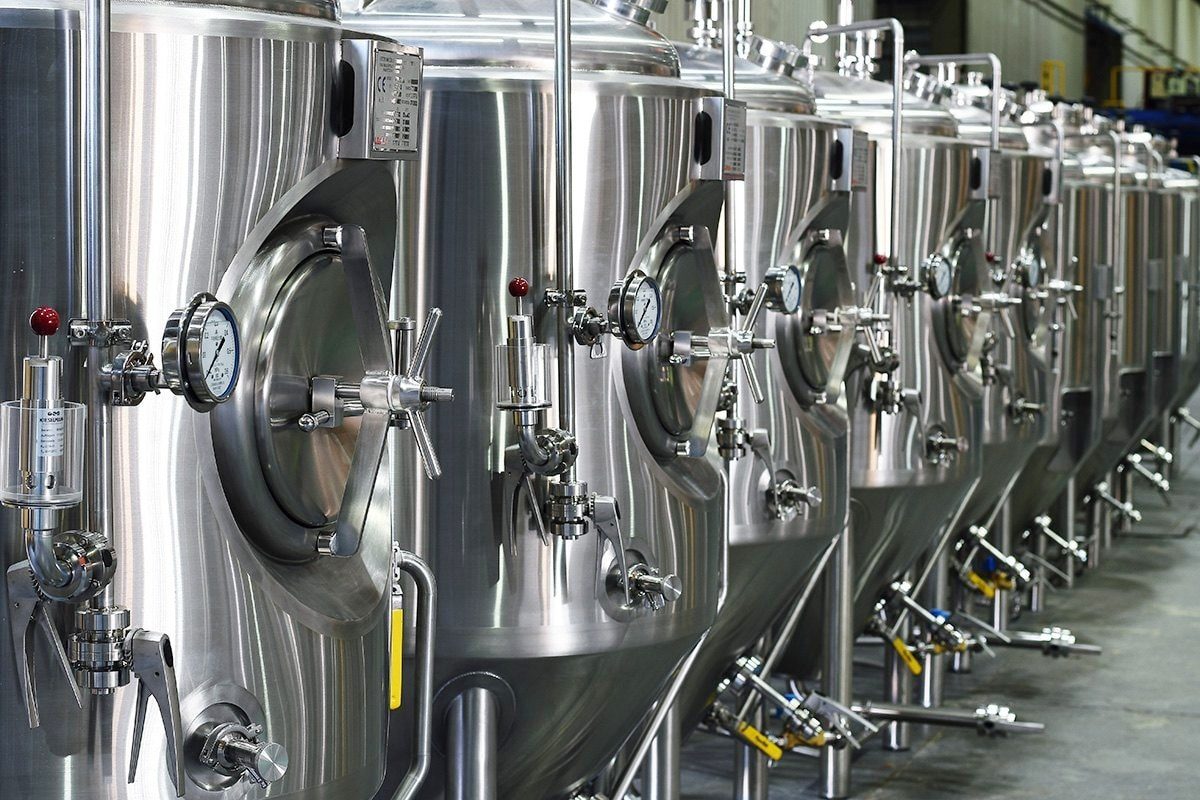
Mechanical and equipment dangerous
In the limited range of beer plants, machinery, and equipment are the pillars of production, which promotes the transformation of raw materials into our well-known drink -beer. However, in the gears and tumbling water tanks, many risks need to be carefully considered and managed.
Pressure container risk
- Stress Risk: steam boilers, fermentation tanks, and small barrels are operated under high pressure. Failure to monitor and maintain stress may lead to catastrophic accidents, including container rupture and explosion.
- Boiler Safety: Especially steam boilers, you need to pay close attention to the safety protocol to prevent over-pressure. Regular inspections, pressure-leaking valves, and compliance with boiler specifications and standards help maintain workers’ safety.
Heat source and burning
- Hot Liquid and Surface: brewing involves heating a large amount of liquid, increasing the risk of workers’ burns and burns. Appropriate training and the use of heat protection equipment can reduce these dangers.
- Steaming Harm: steam pipelines and equipment will release high-temperature steam, which will cause burns after contact. The safety valve and pressure leakage system should be installed to prevent steam accumulation and ensure the safety of workers.
Mechanical danger
- Sports Parts: Brewery equipment (such as pumps, conveyors, and bottle lines) contains many motion components, which can cause squeezing and entanglement hazards. There should be a protective device and a locking device to prevent accidental contact and ensure the safety of workers.
- Powering Line Safety: Due to the mechanical high-speed operation, the bottling line is particularly prone to mechanical danger. Appropriate training, regular maintenance, and obeying the lock/listing program can prevent accidents.
Electrical danger
- Electrical Equipment: Beerles seriously relies on electrical equipment in various processes, including brewing, bottling, and packaging. Wiring errors, damage to equipment, and a humid environment will increase the risk of electric shock and fire. Regular inspections, correct grounding, and compliance with electrical safety standards can improve the safety of workers.
The harm of machinery and equipment is inherent in the operation of the beer factory, and it needs to pay attention to reducing risks to effectively reduce risks. Through the implementation of strong security agreements, comprehensive training, and regular equipment inspections, beer factories can create a safer working environment for employees and ensure that their operations continue to succeed.
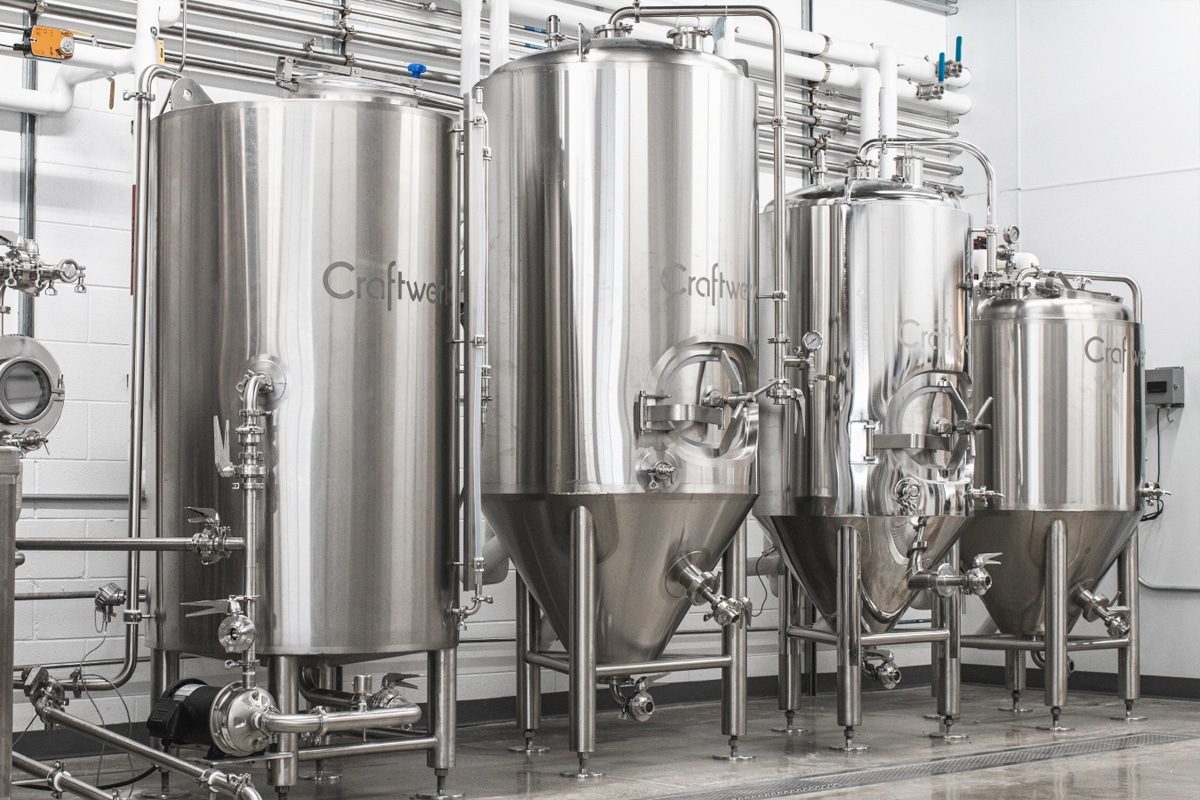
Chemical Exposure and Handling Hazards
Within the intricate tapestry of brewery operations, the use of chemicals plays a vital role in maintaining cleanliness, ensuring product quality, and facilitating the brewing process. However, the handling and management of these chemicals present significant hazards that demand careful attention and adherence to safety protocols.
Cleaning Agents
- Caustic Solutions: Brewery sanitation often involves the use of caustic cleaning solutions to remove organic residues and bacteria from equipment and surfaces. However, these solutions can cause severe chemical burns and eye damage if they come into contact with the skin or eyes. Proper handling procedures, including the use of appropriate personal protective equipment (PPE) such as gloves and goggles, are essential to minimize the risk of exposure.
- Acidic Cleaners: Acidic cleaning agents may also be used to remove mineral deposits and sanitize equipment. Like caustic solutions, they can cause burns and respiratory irritation if mishandled. Workers should be trained in the safe use and handling of acidic cleaners, and adequate ventilation should be provided to prevent the buildup of fumes.
Disinfectants and Sanitizers
- Quaternary Ammonium Compounds (Quats): Quats are commonly used as disinfectants and sanitizers in breweries due to their effectiveness against a wide range of microorganisms. However, prolonged exposure to quats can cause skin irritation and respiratory sensitization. Workers should use these chemicals in well-ventilated areas and wear appropriate PPE to minimize exposure.
- Iodophors: Iodophor sanitizers are another popular choice for brewery sanitation, but they can cause skin irritation and allergic reactions in some individuals. Workers with sensitivities to iodophors should be provided with alternative sanitizing options, and all workers should receive training in proper handling procedures.
Chemical Additives
- Fining Agents: Fining agents such as gelatin, isinglass, and PVPP (polyvinylpolypyrrolidone) are used to clarify beer and remove undesirable compounds. While these additives are generally considered safe for use in brewing, they may pose risks if mishandled. Workers should be trained in the proper use and dosage of fining agents to prevent overexposure.
- Stabilizers: Stabilizers such as potassium metabisulfite and potassium sorbate are used to inhibit microbial growth and prevent oxidation in beer. However, these chemicals can cause allergic reactions and respiratory irritation in sensitive individuals. Proper ventilation and PPE should be used when handling stabilizers to minimize exposure.
Chemical Storage and Handling
- Proper Labeling: All chemicals used in the brewery should be properly labeled with their contents, hazards, and handling instructions. Workers should be trained to read and understand chemical labels to prevent accidents and minimize the risk of exposure.
- Storage Considerations: Chemicals should be stored in designated areas away from food and beverage storage areas. Flammable and combustible chemicals should be stored by local regulations, and incompatible chemicals should be stored separately to prevent reactions.
Chemical exposure and handling hazards are significant concerns in brewery operations. By implementing robust safety protocols, providing comprehensive training, and ensuring the proper use of personal protective equipment, breweries can minimize the risks associated with chemical handling and create a safer working environment for all employees.
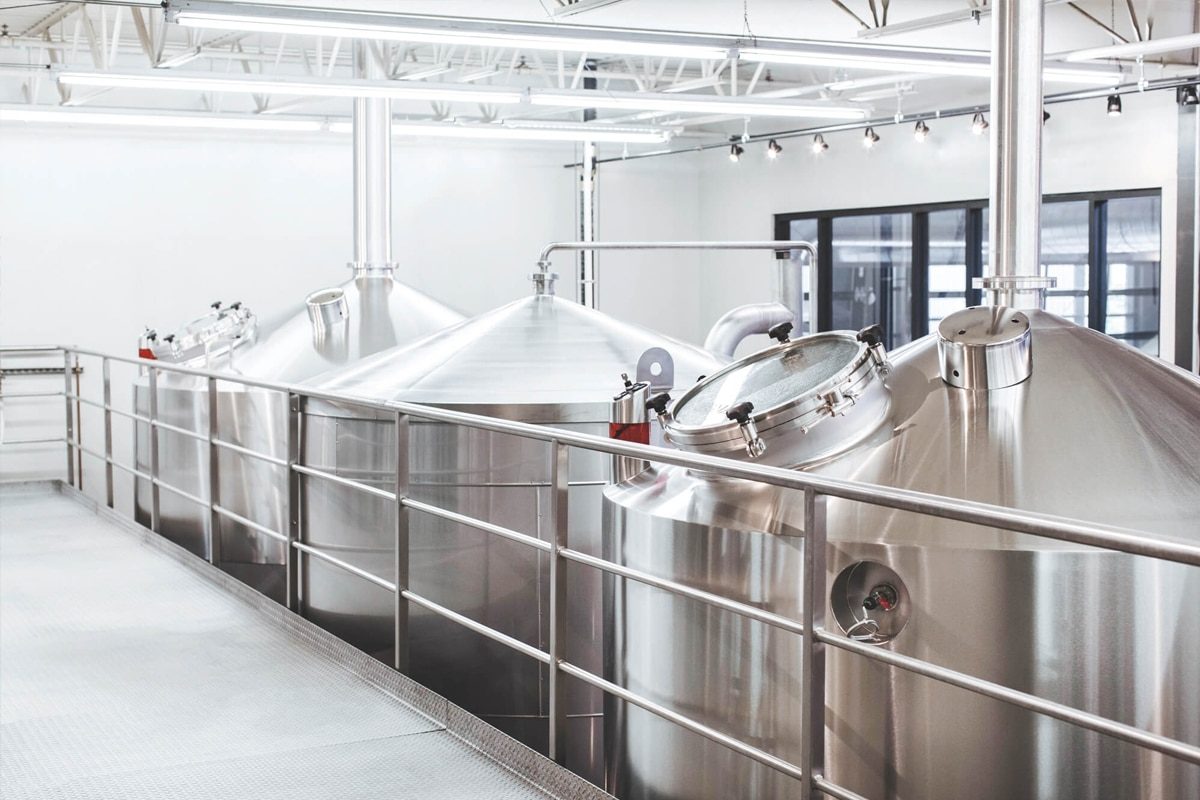
Environmental and Ergonomic Hazards
In the dynamic world of brewery operations, environmental and ergonomic hazards present unique challenges that require careful consideration and proactive management. From the temperature-controlled confines of fermentation tanks to the repetitive motions of bottling lines, these hazards can impact the health and safety of brewery workers if not properly addressed.
Temperature and Humidity Control
- Mold and Bacteria Growth: Breweries often operate in environments with fluctuating temperatures and humidity levels, creating ideal conditions for mold and bacteria growth. Proper ventilation, cleaning, and hygiene habits help prevent pollution and ensure that the quality of the product is consistent.
- Heat Stress: Workers may be exposed to high temperatures during brewing processes, leading to heat-related illnesses such as heat exhaustion and heat stroke. Pinded water, rest time and cooling measures for the workplace help prevent heat stress and protect workers’ health.
Slip, Trip, and Fall Hazards
- Wet and Slippery Surfaces: Spills of water, wort, or cleaning solutions can create slippery surfaces, increasing the risk of slips, trips, and falls. Proper housekeeping practices, including prompt cleanup of spills and the use of non-slip flooring materials, are essential for preventing accidents.
- Elevated Work Areas: Brewery facilities may have elevated platforms and catwalks for equipment access. Fall protection measures such as guardrails, handrails, and harnesses should be implemented to prevent falls from height and protect workers from injury.
Manual Handling and Ergonomics
- Heavy Lifting: Brewery workers are often required to lift and move heavy sacks of grain, kegs, and equipment, increasing the risk of musculoskeletal injuries. Proper lifting techniques, mechanical aids, and ergonomic training can help reduce strain and prevent injuries.
- Repetitive Tasks: Workers engaged in repetitive tasks such as bottling and packaging may develop ergonomic-related injuries over time, including carpal tunnel syndrome and tendonitis. Job rotation, ergonomic workstation design, and the use of assistive devices can help mitigate these risks and promote worker health and well-being.
Noise Exposure
- Equipment Noise: Brewery operations involve the use of various machinery and equipment, which can generate high levels of noise. Prolonged exposure to loud noise can lead to hearing loss and other auditory problems. Engineering controls, such as soundproofing and noise-reducing equipment, should be implemented to minimize noise exposure and protect worker hearing.
Environmental and ergonomic hazards are integral aspects of brewery operations that must be carefully managed to ensure the health and safety of brewery workers. By implementing robust safety protocols, providing comprehensive training, and prioritizing worker well-being, breweries can create a safer and more sustainable workplace for all employees.
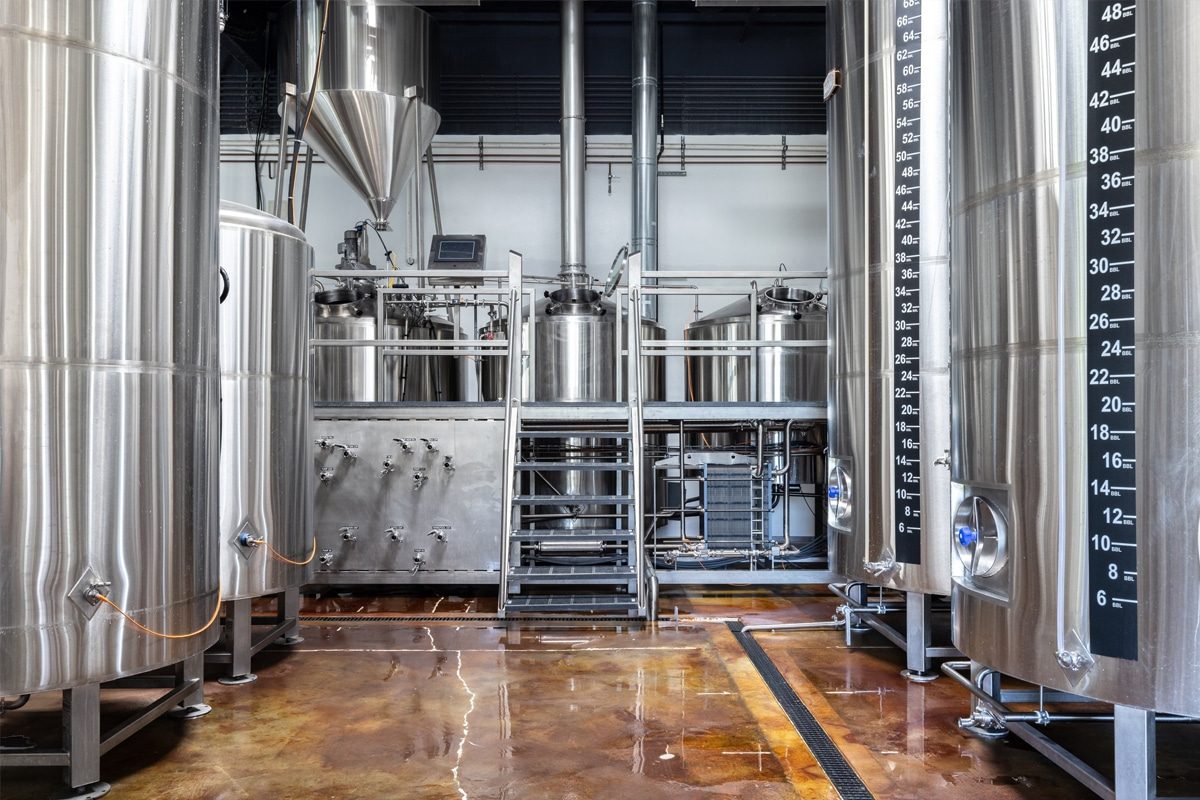
Electrical Hazards
In the rhythmic operation of machinery, electrical hazards have vaguely become a silent threat in the operation of the brewery. From powering pumps and motors to illuminating workspaces, electricity is indispensable in modern breweries. However, improper installation, maintenance lapses, and worker negligence can turn this vital resource into a source of danger. Understanding and mitigating electrical hazards are paramount to ensuring the safety and efficiency of brewery operations.
Electrical Equipment
- Faulty Wiring: Improper wiring practices or damaged electrical cables can lead to short circuits, electrical fires, and electric shock hazards. Regular inspections and maintenance of electrical systems help identify and correct them before the upgrade of potential issues.
- Overloading: Overloading electrical circuits with excessive loads can cause overheating and increase the risk of electrical fires. Breweries must ensure that electrical circuits are properly sized and that loads are distributed evenly to prevent overload conditions.
- Wet Conditions: Brewery environments often involve exposure to moisture and liquids, which can increase the risk of electrical shock. GFCI (Ground Fault Circuit Interrupter) outlets and equipment with waterproof enclosures should be used in areas where water exposure is likely.
Worker Safety
- Electric Shock: Direct contact with live electrical circuits or equipment can result in electric shock, which can cause severe injuries or even fatalities. Workers should receive training in electrical safety procedures and be aware of the location of electrical disconnects and emergency shutdown procedures.
- Arc Flash: Arc flash, a sudden release of energy due to an electrical fault, can produce intense heat, light, and pressure waves capable of causing severe burns and injuries. Workers should wear appropriate personal protective equipment (PPE), such as arc flash suits and face shields when working on or near energized electrical equipment.
- Lockout/Tagout: Lockout/tagout procedures should be implemented to ensure that electrical equipment is de-energized and safely isolated before maintenance or repair work begins. Workers should be trained in lockout/tagout procedures and provided with the necessary tools and equipment to perform these tasks safely.
Emergency Preparedness
- Emergency Response: Breweries should have clear emergency response procedures in place to address electrical accidents and incidents. This includes procedures for administering first aid, evacuating the area, and contacting emergency services.
- Fire Safety: Electrical faults can lead to electrical fires, which can spread rapidly and pose a significant threat to brewery operations and personnel. Breweries should have adequate fire detection and suppression systems in place, as well as regular fire drills to ensure that workers are prepared to respond effectively in the event of a fire.
Electrical hazards are a critical concern in brewery operations that require proactive management and adherence to safety protocols. By prioritizing electrical safety, breweries can minimize the risk of accidents and injuries, ensuring the well-being of their workers and the continuity of their operations.
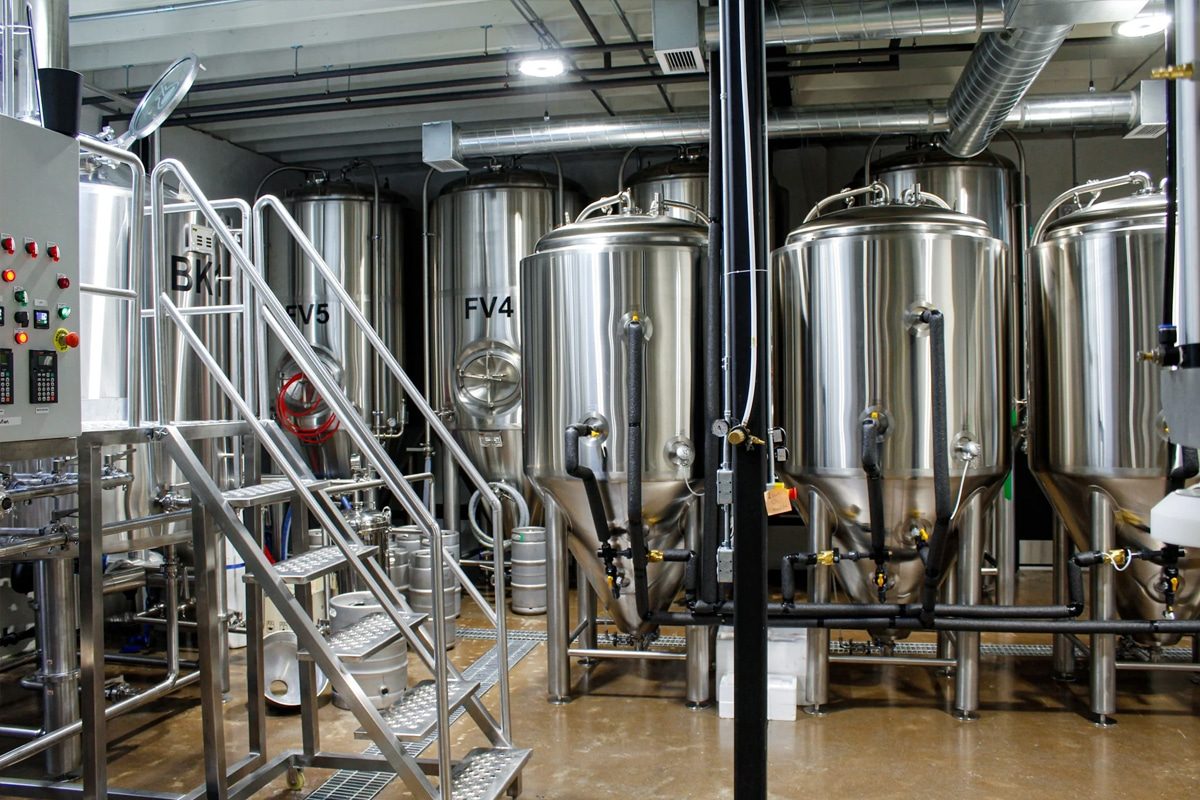
Summarize
The hazards encountered in brewery operations span a diverse range, from the handling of raw materials to the operation of machinery and electrical systems. Grain dust inhalation, chemical exposure, and heat stress pose risks to worker health, while machinery malfunctions, electrical hazards, and environmental factors such as slippery surfaces and noise exposure threaten safety. Additionally, ergonomic strains and repetitive tasks contribute to musculoskeletal injuries over time. To mitigate these risks, breweries must prioritize safety protocols, employee training, and the use of appropriate personal protective equipment. Regular inspections, maintenance, and adherence to industry standards are essential for ensuring a safe working environment. By addressing these hazards comprehensively, breweries can safeguard the well-being of their workforce, maintain product quality, and uphold operational efficiency in the dynamic world of brewing.
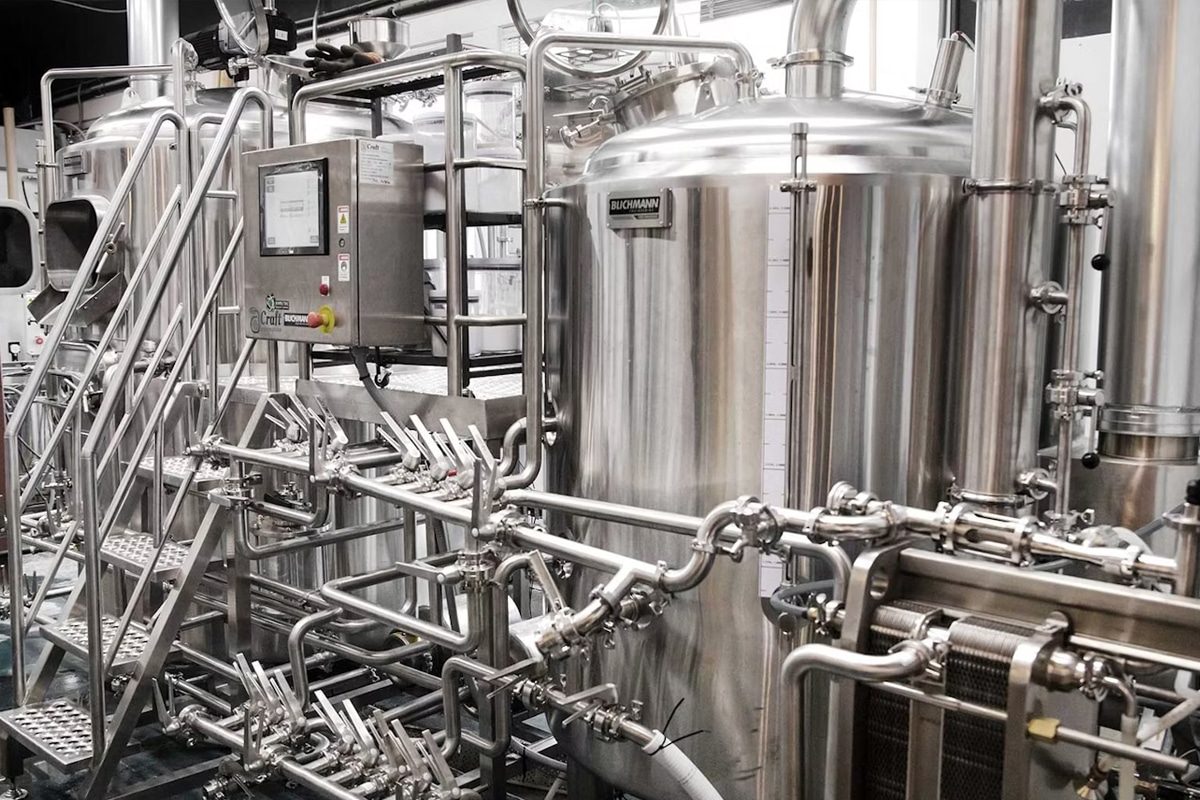
Get Turnkey Brewery Solutions with ZYB Craft
Navigating the hazards inherent in brewery operations requires comprehensive solutions that prioritize safety, efficiency, and quality. With ZYB Craft, a leading provider of professional brewhouse solutions, breweries can access turnkey solutions designed to address the diverse range of risks encountered in brewing environments.
ZYB Craft offers a holistic approach to brewery safety, encompassing state-of-the-art equipment, expert guidance, and tailored solutions to meet the unique needs of each brewery. From grain handling systems designed to minimize dust exposure to advanced control panels that ensure precise temperature and pressure control, ZYB Craft’s solutions are engineered to mitigate hazards and optimize operational performance.
Moreover, ZYB Craft’s team of experienced professionals provides ongoing support and training to brewery personnel, empowering them to operate equipment safely and efficiently. By partnering with ZYB Craft, breweries can not only mitigate risks but also enhance productivity, quality, and overall safety in their operations.