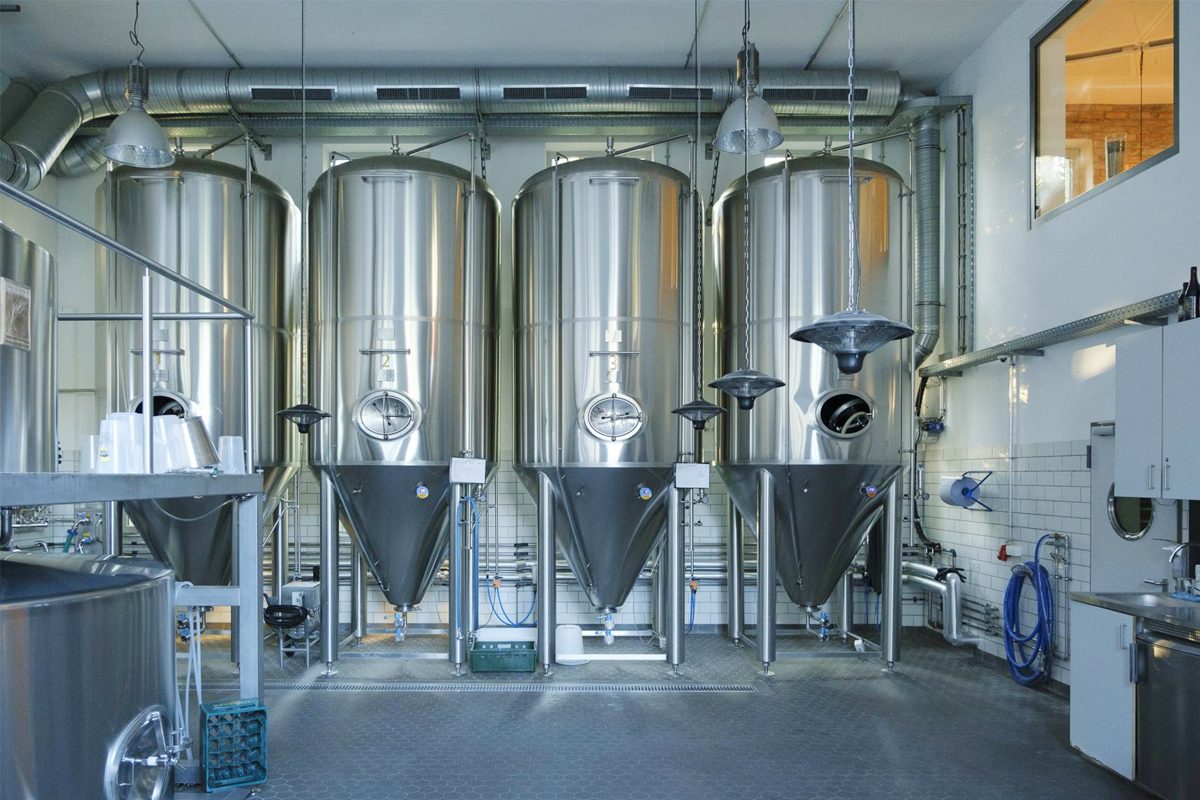
The Role of Flow Meters in Breweries
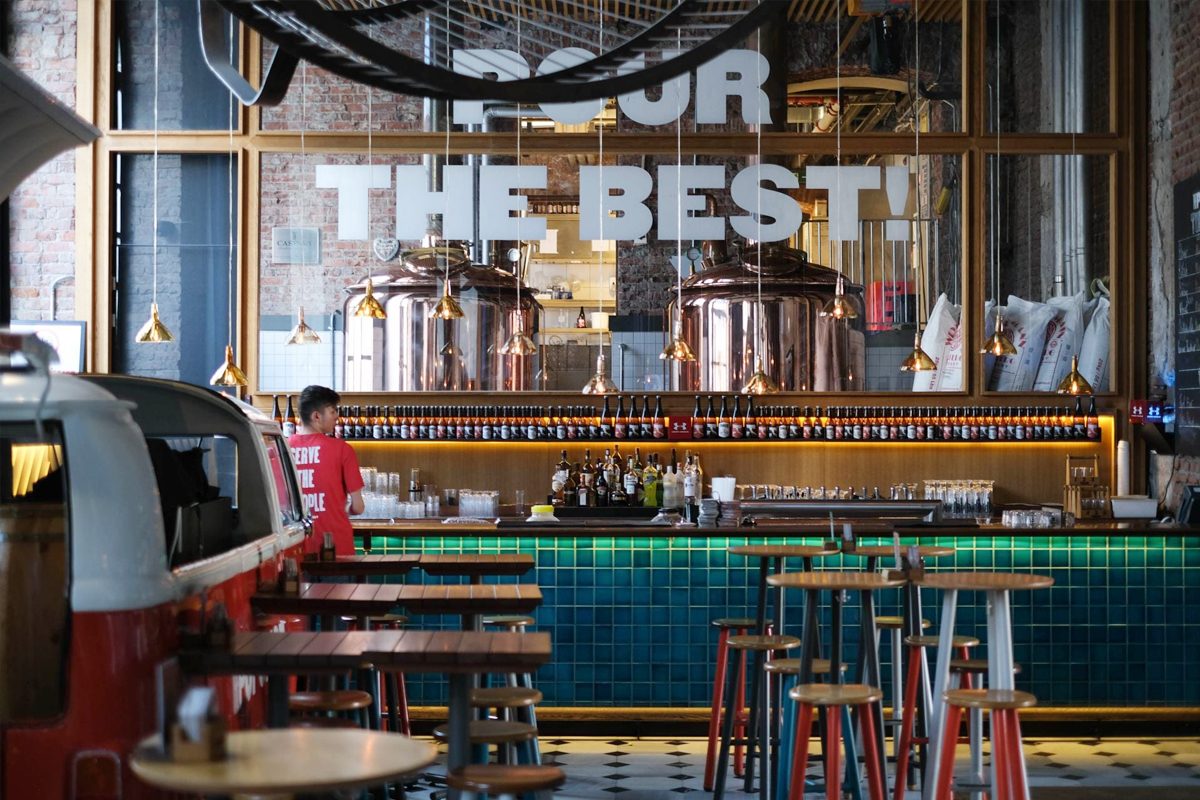
Understanding Flow Meters
What is a Flow Meter?
How Flow Meters Work
Flow meters function by detecting the velocity, pressure, or displacement of the liquid or gas passing through them and converting these readings into flow rate data. The working principle varies depending on the type of meter:
- Magnetic Flow Meters: These generate a magnetic field and measure the voltage induced by the movement of conductive liquids, such as wort or beer, through the field. The voltage is proportional to the flow rate.
- Coriolis Flow Meters: These rely on the Coriolis effect, where the deflection of a vibrating tube corresponds to the mass flow of liquid. These meters are ideal for measuring viscous ingredients or high-density fluids like yeast slurry.
- Ultrasonic Flow Meters: Using sound waves, these meters measure the time or frequency shift of sound waves traveling through the liquid, providing a non-contact method for precise flow measurement.
- Turbine Flow Meters: A mechanical rotor spins as liquid flows through, with the rotational speed correlating to the flow rate.
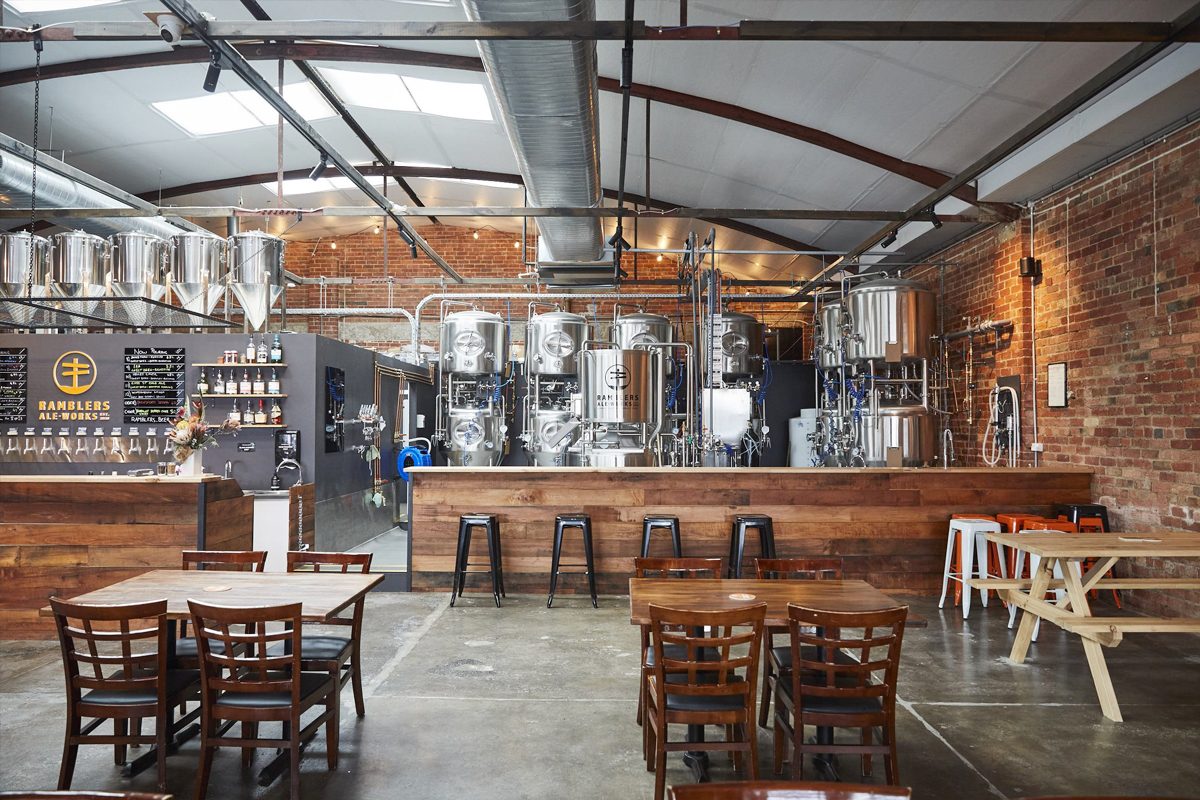
Importance of Flow Meters in Breweries
Accurate Measurement and Control of Water Usage
Managing Wort Flow
Controlling Ingredient Additions
Carbonation and CO2 Flow Control
Cleaning and Sanitization
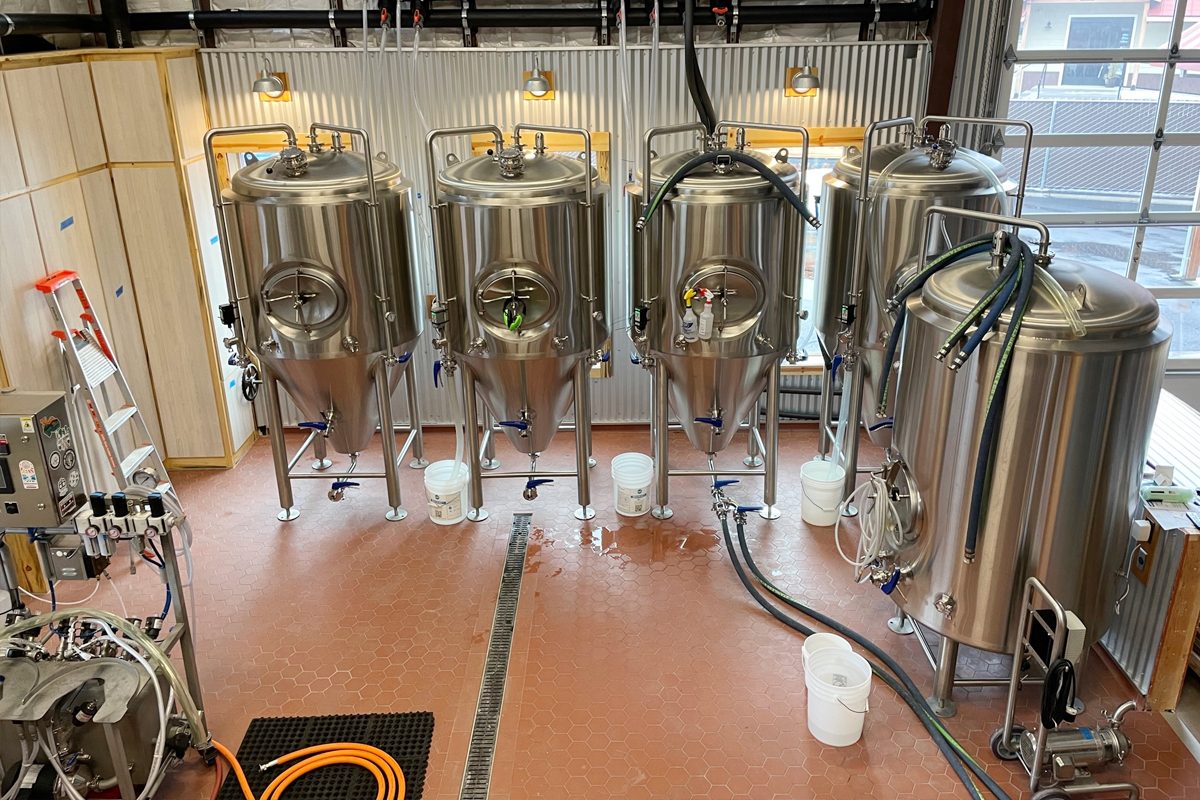
Types of Flow Meters Used in Breweries
Magnetic Flow Meters
Magnetic flow meters, also known as mag meters, are ideal for measuring conductive liquids such as wort and water. They operate by creating a magnetic field inside the pipe, generating a voltage as the liquid flows through it. The voltage is directly proportional to the flow rate, providing highly accurate readings.
- Application: Suitable for measuring water usage, wort transfer, and other conductive fluids.
- Advantages: High accuracy, no moving parts (reducing maintenance), and minimal risk of contamination.
- Considerations: Only works with conductive liquids, so it’s not suitable for measuring gases or non-conductive fluids like oils.
Coriolis Flow Meters
Coriolis flow meters measure the mass flow of liquids by detecting the impact of the Coriolis effect on vibrating tubes. These meters are particularly useful for measuring the mass and density of liquids, providing valuable data for precise ingredient management.
- Application: Ideal for measuring high-viscosity fluids like malt extracts or syrup, or when mass flow is required.
- Advantages: Extremely accurate, can measure both mass flow and density, suitable for viscous liquids.
- Considerations: Expensive and may require calibration to maintain accuracy.
Turbine Flow Meters
Turbine flow meters use a mechanical rotor that spins as liquid flows through the device. The speed of the rotor is directly proportional to the flow rate, allowing the volume of liquid to be calculated.
- Application: Commonly used to measure water and CO2 flow during brewing and carbonation.
- Advantages: Simple design, affordable, and effective for low-viscosity liquids.
- Considerations: Requires regular maintenance, as moving parts can wear out over time. Debris in the liquid can also affect accuracy.
Ultrasonic Flow Meters
Ultrasonic flow meters measure the flow of liquids using sound waves. They are non-invasive, meaning the sensors attach to the outside of the pipe without coming into contact with the liquid. There are two main types: transit-time ultrasonic meters, which measure the time it takes for sound waves to travel between sensors, and Doppler ultrasonic meters, which measure the frequency shift of reflected sound waves.
- Application: Used for monitoring water flow, cleaning solutions, and liquids where hygiene is a priority.
- Advantages: No moving parts, low maintenance, non-invasive design prevents contamination.
- Considerations: May struggle with liquids containing solid particles or bubbles, which can interfere with sound waves.
Positive Displacement Flow Meters
Positive displacement (PD) flow meters measure the flow by trapping a known amount of liquid in chambers and counting how often the chambers fill and empty. These meters are known for their precision, even with thick or viscous liquids.
- Application: Suitable for measuring thick liquids like syrups and malt extracts, as well as low-flow applications.
- Advantages: Extremely accurate, ideal for dosing small quantities of liquids.
- Considerations: Requires regular cleaning and maintenance due to the presence of mechanical components.
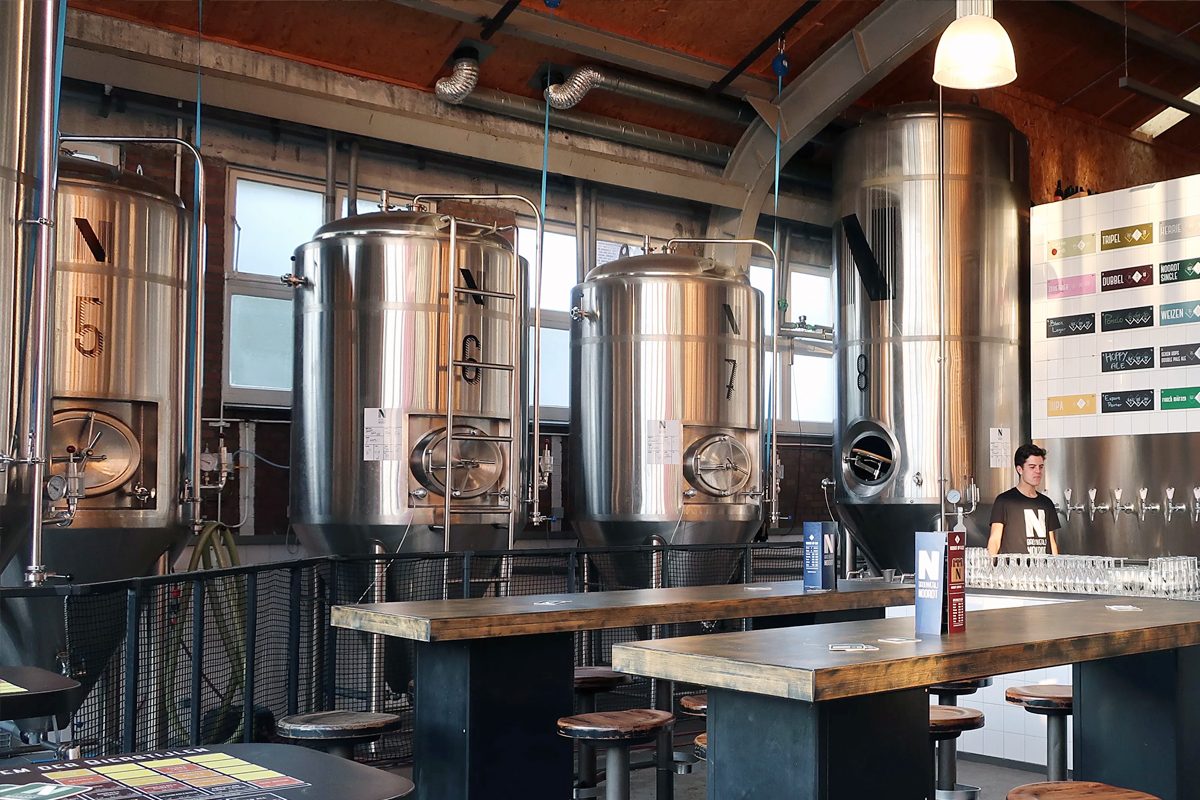
Applications of Flow Meters in Different Stages of Brewing
Mashing and Lautering
In the mashing process, water is mixed with milled malt to extract fermentable sugars, creating a mash. Accurate control of water flow into the mash tun is crucial, as it ensures the proper grain-to-water ratio, which directly affects the sugar extraction and beer quality. Flow meters also regulate the hot water flow used during lautering, where the wort is separated from the spent grain.
- Flow Meter Role: Ensure precise water addition during mashing, and control sparge water flow for efficient wort extraction.
- Impact: Optimizes sugar yield, improves wort clarity, and ensures consistency across batches.
Boiling and Hopping
After lautering, the wort is transferred to the brew kettle for boiling. This stage sterilizes the wort, removes unwanted compounds, and concentrates the flavors. During boiling, hops are added at specific intervals to impart bitterness, aroma, and flavor to the beer.
- Flow Meter Role: Monitor the transfer of wort into the brew kettle, and control the flow of hop extracts or hop additions.
- Impact: Maintains consistency in bitterness and flavor by ensuring precise hop additions and effective boiling times.
Fermentation
During fermentation, yeast converts the sugars in the wort into alcohol and carbon dioxide (CO2), creating beer. The wort must be transferred smoothly to the fermentation tank to avoid contamination or aeration issues. In addition, CO2 produced during fermentation must be properly monitored and controlled.
- Flow Meter Role: Regulate wort flow into fermentation tanks, monitor and control the CO2 flow for venting or carbonation purposes.
- Impact: Ensures optimal fermentation conditions, prevents contamination, and maintains product quality.
Packaging
In the final stage, the beer is packaged into bottles, cans, or kegs. Flow meters help ensure that each container is filled with the correct volume of beer, reducing waste and maintaining consistency. Additionally, precise monitoring of CO2 during carbonation ensures that the beer has the right amount of fizz.
- Flow Meter Role: Measure beer flow during filling, and monitor CO2 flow to maintain consistent carbonation levels.
- Impact: Minimizes product loss, ensures accurate filling and enhances customer satisfaction with consistent carbonation and taste.
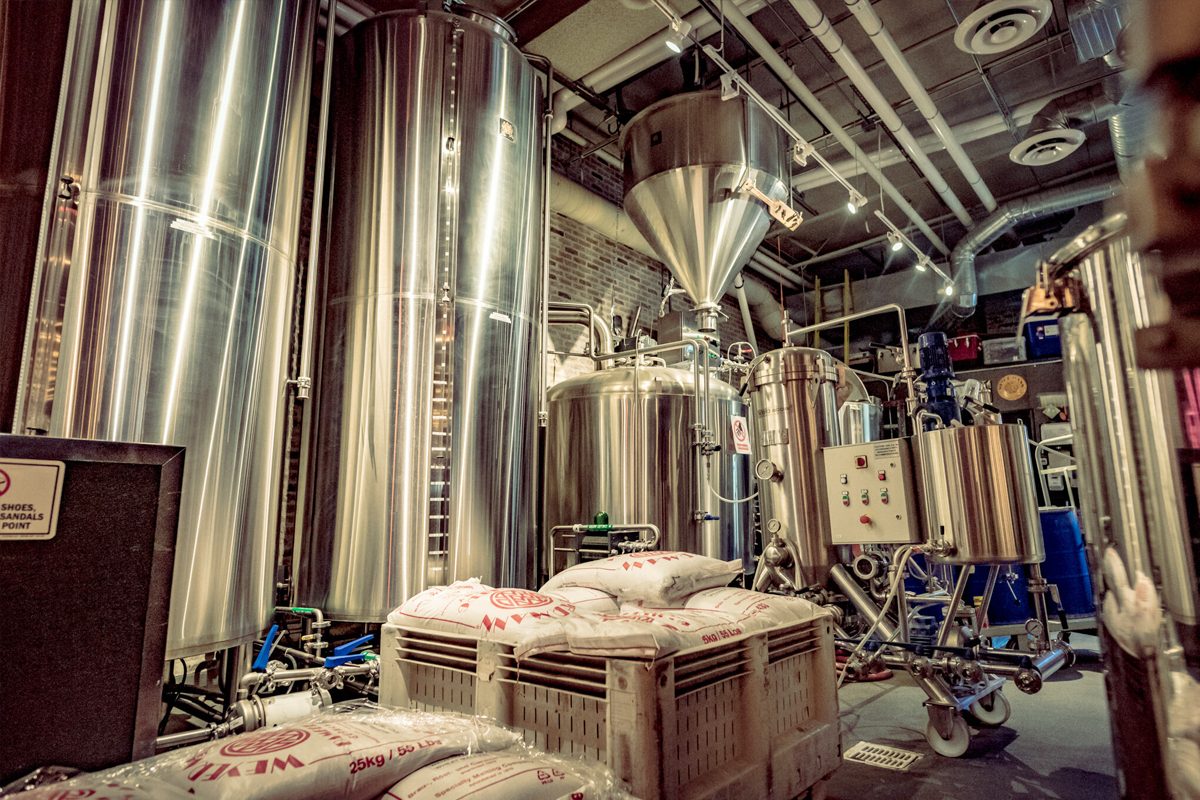
Advantages of Using Flow Meters in Breweries
Accuracy and Consistency
Brewing is a meticulous process where even minor deviations can impact the final product’s flavor, appearance, and quality. Flow meters provide precise control over the volume of liquids and gases used during each stage, from water intake to ingredient additions and carbonation.
- Impact: Flow meters ensure each batch meets the same quality standards, providing customers with consistent beer flavor and texture.
- Example: Accurate measurement of hop extracts ensures bitterness remains consistent across batches.
Improved Process Efficiency
By accurately controlling the flow of liquids and gases, flow meters reduce downtime and bottlenecks. Flow meters allow brewers to maintain optimal production speeds, ensuring smooth transfers between brewing stages, such as wort transfer or beer filling, without delays.
- Impact: Optimizes production schedules, reduces time between brewing steps, and maximizes equipment utilization.
- Example: Real-time monitoring of wort flow helps prevent interruptions and keeps the process on schedule.
Reduction of Waste and Cost Savings
Precise flow measurement helps breweries minimize the overuse of water, CO2, ingredients, and cleaning agents, preventing waste and lowering operational costs. Flow meters also reduce product loss during packaging by ensuring accurate fills.
- Impact: Supports sustainable practices by reducing water and resource consumption while lowering operating expenses.
- Example: Accurate CO2 control during carbonation ensures minimal gas usage without compromising beer quality.
Real-Time Monitoring and Automation
Modern breweries are adopting automation to improve efficiency and consistency. Many flow meters are equipped with data logging and remote monitoring capabilities, allowing brewers to oversee operations from a central control system. This enables quick adjustments based on real-time data, reducing the need for manual interventions.
- Impact: Enhances productivity by automating routine tasks and allowing for quick responses to potential issues.
- Example: Automated wort flow monitoring prevents over-aeration by adjusting flow rates as needed in real-time.
Regulatory Compliance
Breweries must comply with strict health, safety, and environmental regulations. Flow meters help ensure that cleaning and sanitization processes are effective by verifying that the proper amount of cleaning agents is used. They also ensure accurate CO2 usage, aiding in environmental compliance by minimizing emissions and waste.
- Impact: Reduces the risk of contamination, ensures safe production practices, and helps breweries meet environmental and safety standards.
- Example: Accurate flow monitoring during tank cleaning ensures compliance with food safety regulations.
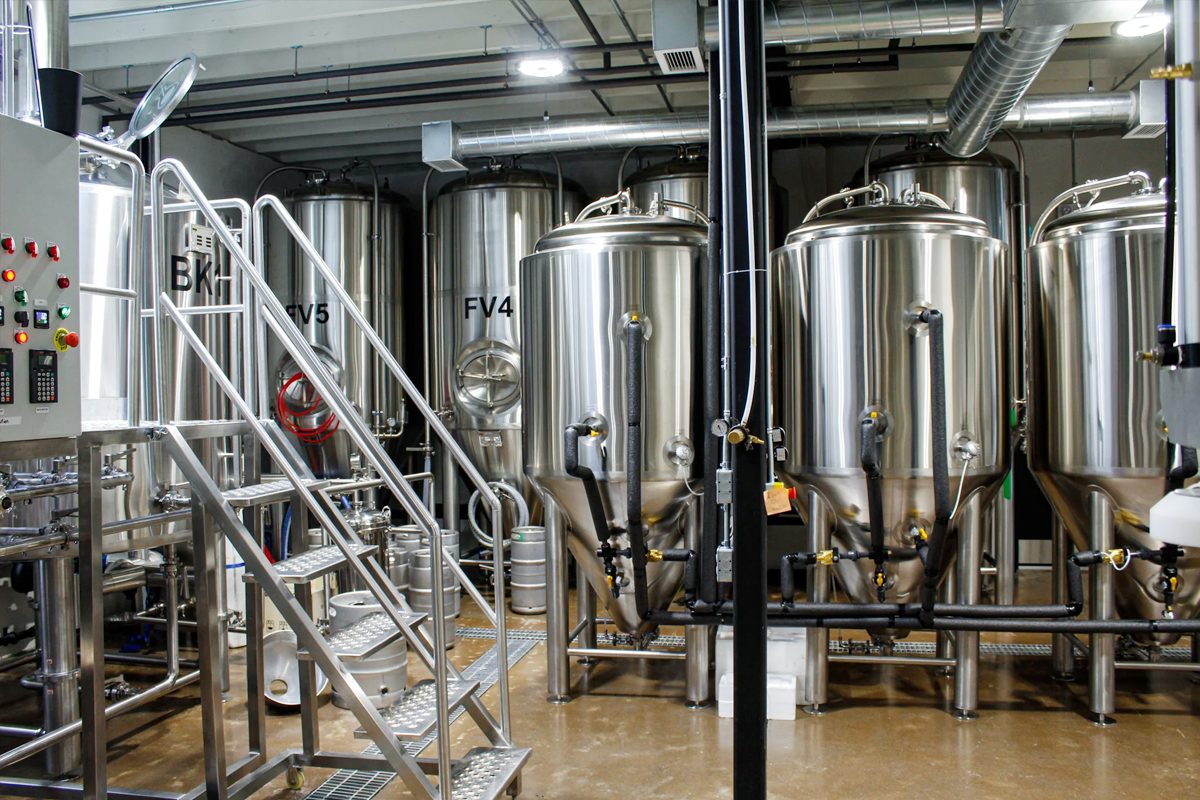
Challenges of Using Flow Meters in Breweries
Installation Complexity
Installing flow meters requires precise planning to ensure compatibility with existing brewing systems. Factors such as pipe size, flow direction, and required straight-pipe runs can affect installation. Some flow meters need specific orientations to function accurately, which may involve modifications to the brewery’s infrastructure.
- Impact: Poor installation can lead to inaccurate readings or inefficient operations, potentially disrupting production schedules.
- Solution: Working with experienced providers, such as ZYB Craft, ensures proper installation and integration with existing equipment.
Calibration and Maintenance
Flow meters require regular calibration to maintain accuracy, especially in high-demand brewing environments. Over time, some meters, such as turbine flow meters, may experience wear and tear, requiring maintenance to avoid disruptions.
- Impact: Failing to calibrate or maintain flow meters can result in inaccurate measurements, affecting product quality.
- Solution: Scheduling regular maintenance and calibration helps maintain accuracy and minimizes downtime. Selecting low-maintenance meters like magnetic or ultrasonic types can reduce the need for frequent servicing.
Cost Considerations
High-precision flow meters, such as Coriolis meters, can be expensive, particularly for smaller breweries with limited budgets. Installation, calibration, and maintenance also add to the total cost of ownership. Brewers must balance the benefits of improved accuracy and efficiency with the initial investment and ongoing costs.
- Impact: The high cost of advanced flow meters can be a barrier for smaller breweries or those with tight budgets.
- Solution: ZYB Craft helps breweries identify cost-effective solutions by matching the right flow meter to each application, balancing performance with affordability.
Fluid Properties and Compatibility
Not all flow meters are suitable for every fluid. For example, magnetic flow meters work only with conductive liquids like wort, while turbine meters may not perform well with unfiltered fluids containing solids. Selecting the wrong type of flow meter can lead to inaccurate measurements or equipment damage.
- Impact: Using incompatible flow meters can cause disruptions, affect product quality, and increase maintenance needs.
- Solution: ZYB Craft provides expert advice on selecting flow meters based on fluid properties, ensuring compatibility with brewing processes.
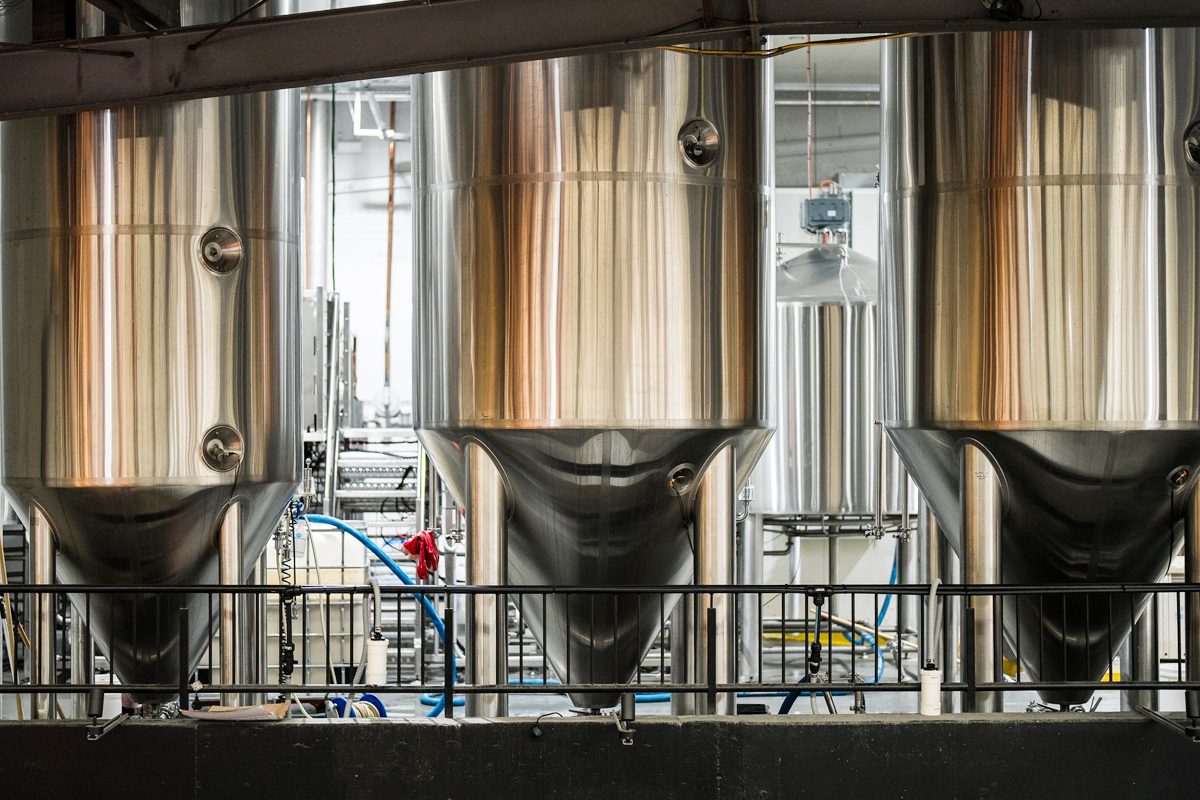
Selecting the Right Flow Meter for a Brewery
Fluid Type and Properties
The properties of the fluid—such as viscosity, conductivity, and the presence of solids—determine which flow meter will work best. For instance, magnetic flow meters are ideal for conductive liquids like wort, while ultrasonic flow meters excel in measuring clean, particle-free liquids like water or cleaning solutions. Turbine meters work well for gases such as CO2, but they may struggle with viscous liquids or fluids containing debris.
- Impact: Selecting the wrong meter can lead to inaccurate measurements and operational disruptions.
- Solution: Evaluate the nature of each fluid in the brewery process to match it with a suitable flow meter.
Accuracy Requirements
Different brewery processes require varying levels of precision. Accurate measurements are crucial for ingredient dosing, CO2 flow during carbonation, and beer packaging, while slightly lower accuracy may suffice for water usage. Coriolis meters, known for their high accuracy, are ideal for mass-based ingredient measurements, whereas magnetic meters ensure precision in wort transfer.
- Impact: Insufficient accuracy can affect product consistency and quality, leading to batch rejections.
- Solution: We help breweries assess their precision needs and recommend the appropriate meter for each task.
Operational Conditions
Temperature, pressure, and flow variability impact the performance of flow meters. Breweries operate under a range of conditions—such as high temperatures during boiling and varying pressures during fermentation and carbonation. Some flow meters, like ultrasonic meters, handle high temperatures effectively, while others may need special adjustments or materials to perform under challenging conditions.
- Impact: Using incompatible meters can lead to breakdowns or inaccurate readings, disrupting operations.
- Solution: Select meters designed to withstand the brewery’s operational environment.
Maintenance and Longevity
Flow meters with moving parts, such as turbine meters, may require frequent maintenance due to wear and tear. Conversely, non-intrusive meters, like magnetic or ultrasonic meters, have fewer maintenance needs and longer lifespans. Breweries with tight production schedules benefit from low-maintenance meters that minimize downtime.
- Impact: Frequent maintenance increases costs and disrupts production.
- Solution: We provide durable, low-maintenance flow meters, reducing the need for servicing while ensuring continuous operation.
Integration with Automation Systems
Modern breweries increasingly rely on automation to enhance efficiency and consistency. Flow meters with digital interfaces can seamlessly integrate with brewery management systems, enabling remote monitoring, real-time data collection, and process control. This integration supports predictive maintenance, helping identify potential issues before they affect production.
- Impact: Lack of integration may hinder process optimization and increase manual labor.
- Solution: We offer flow meters compatible with automation systems, providing breweries with the tools to monitor and optimize their processes.
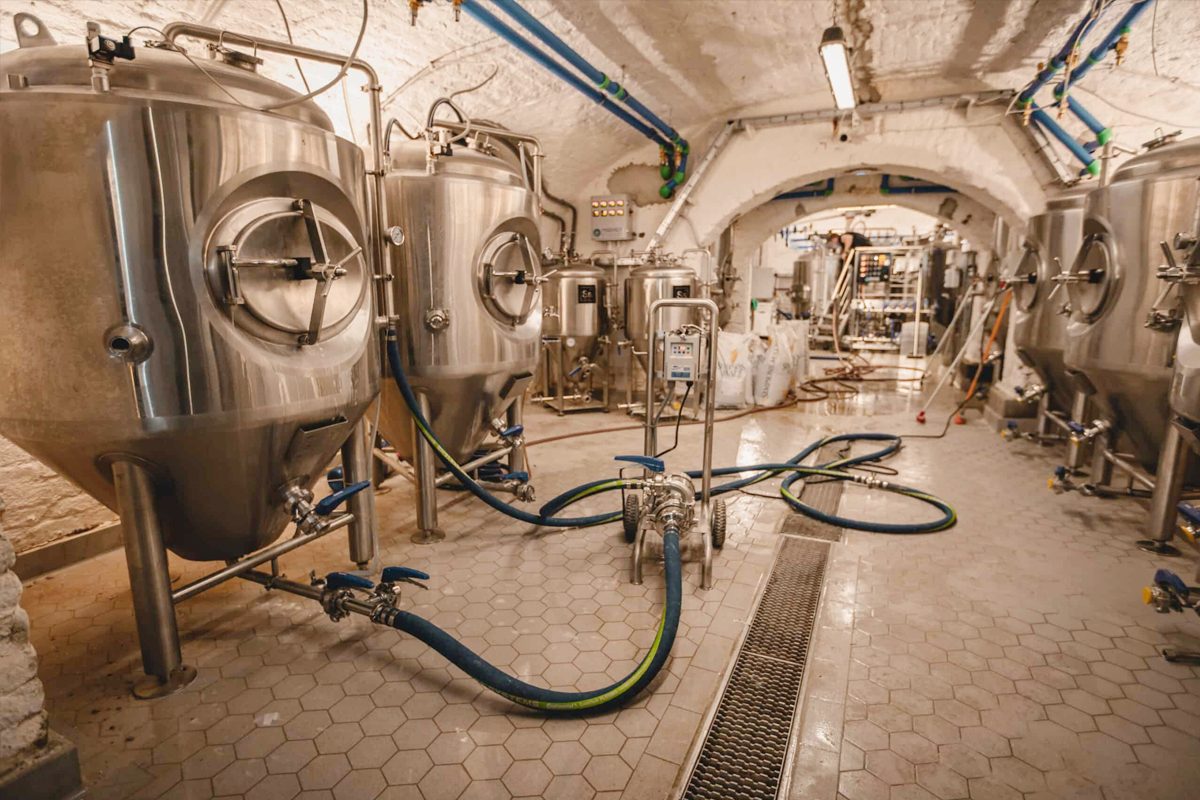
Summary
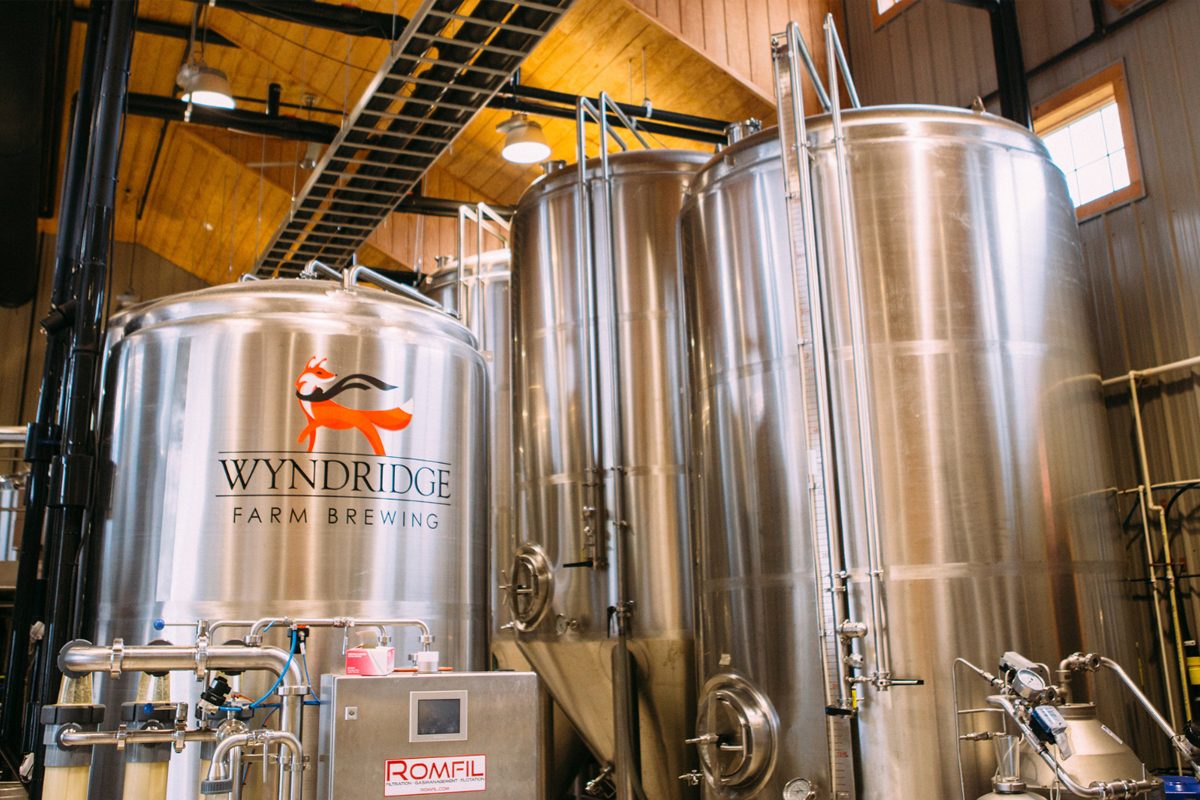