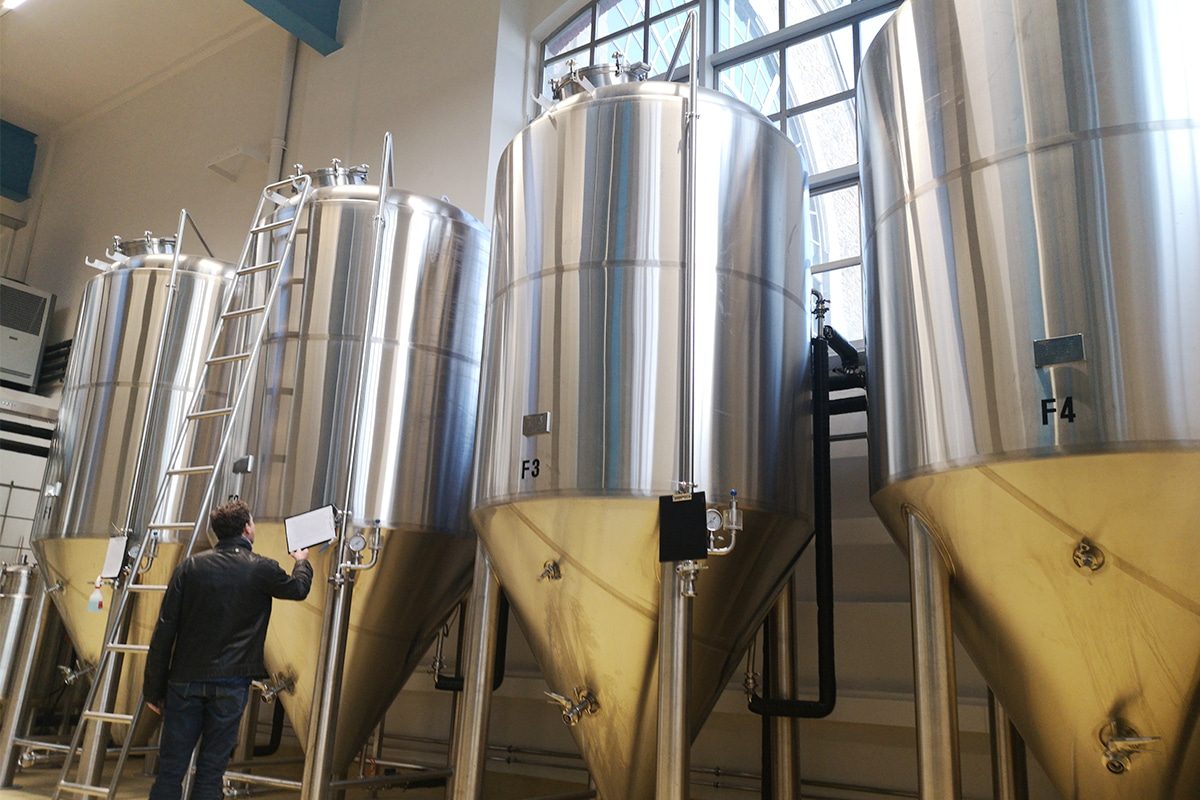
The Risks of Using Second-Hand or Refurbished Brewery Equipment
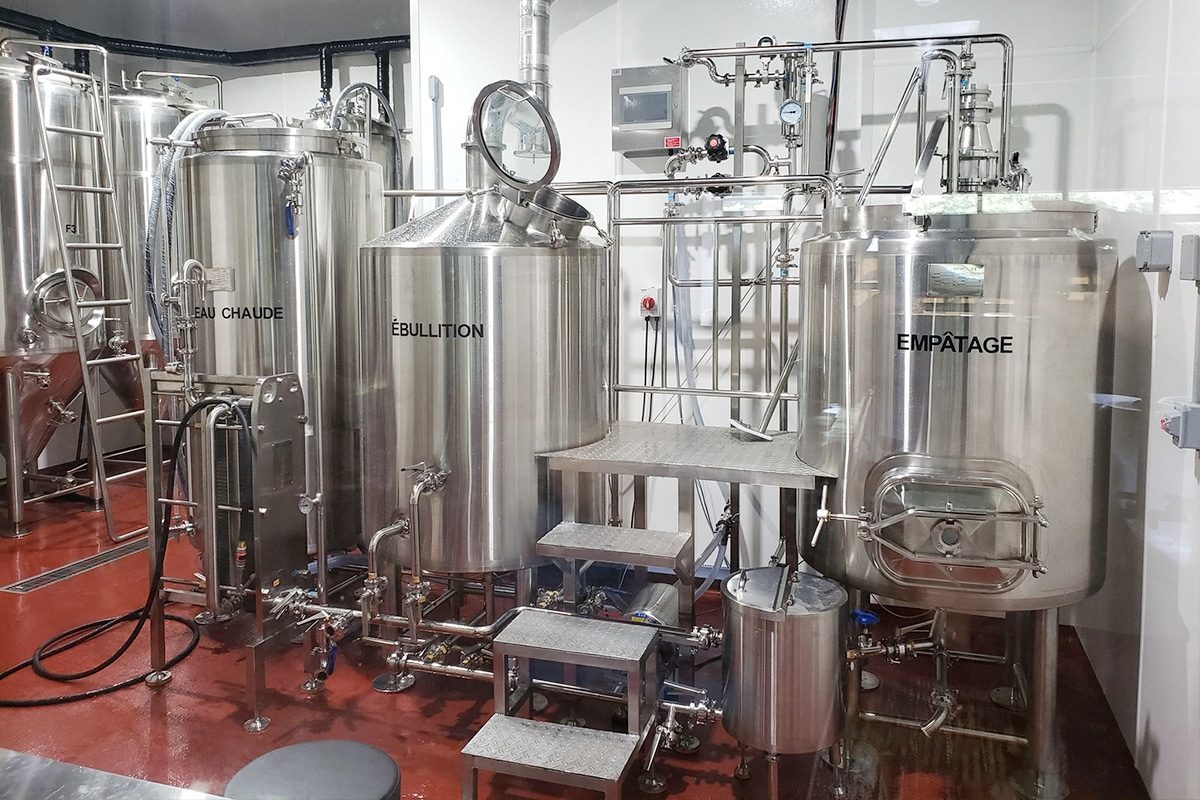
Quality and Performance Issues
Wear and Tear
Mechanical Degradation
Metal Fatigue
Inconsistent Performance
Heating and Cooling Variability
Reduced Efficiency
Reduced efficiency is a common problem with second-hand equipment. This inefficiency can manifest in several ways:
- Energy Consumption: Older equipment tends to be less energy-efficient. For example, outdated heating systems may consume more energy to achieve the same results as newer models. This increased energy consumption not only raises operating costs but also impacts the brewery’s environmental footprint.
- Operational Downtime: Frequent breakdowns and repairs required for older equipment can lead to increased downtime, disrupting the brewing schedule and reducing overall productivity. Every hour of downtime is an hour of lost production, which can be particularly costly for small and medium-sized breweries.
- Productivity: Inefficient equipment may also result in lower throughput, meaning it takes longer to produce each batch of beer. This reduced productivity can limit a brewery’s ability to scale operations and meet growing demand.
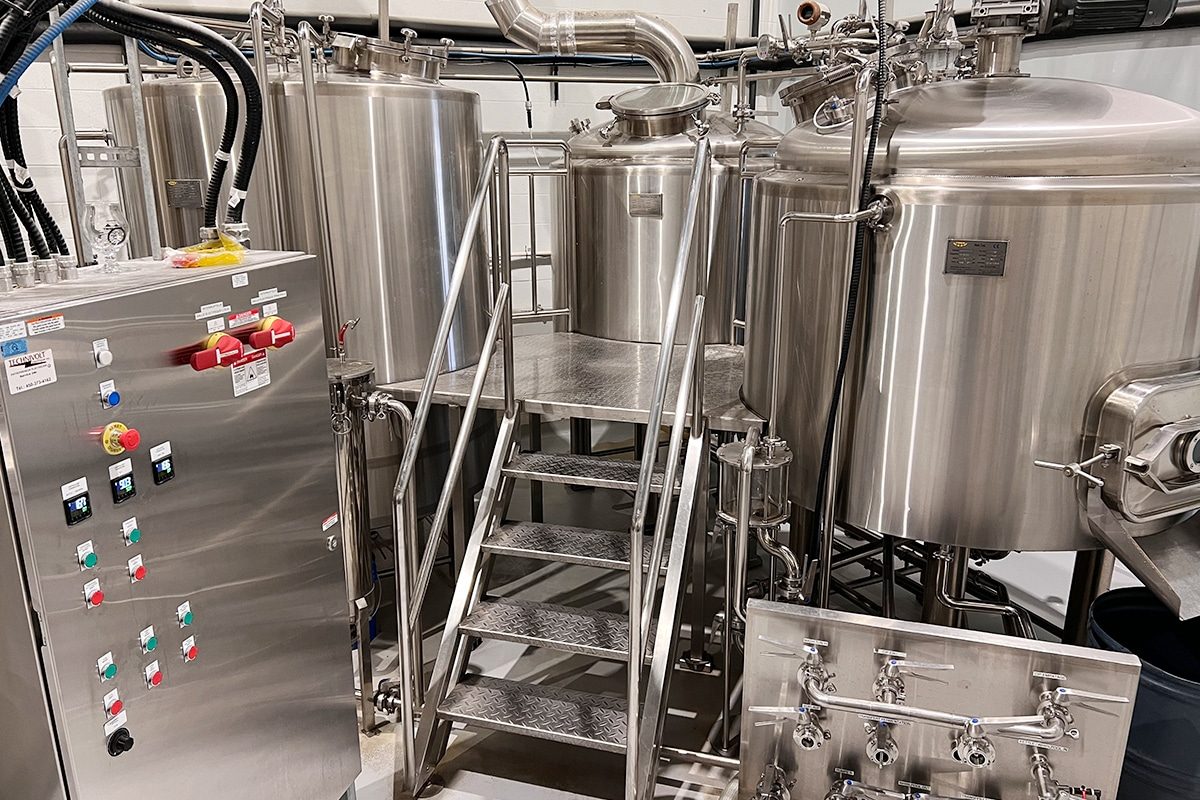
Sanitation and Hygiene Concerns
Contamination Risks
Contamination risks are a primary concern when using second-hand or refurbished equipment. Any residual organic matter left from previous brewing processes can serve as a breeding ground for bacteria, wild yeast, and mold. These microorganisms can spoil batches, lead to off-flavors, and even cause health hazards. The complexity and scale of modern brewing equipment mean that thorough cleaning is challenging, and remnants from prior use can easily be overlooked.
- Chemical Residues: In addition to organic matter, chemical residues from cleaning agents or previous brewing processes can linger on used equipment. These residues can interact with new ingredients, leading to undesirable chemical reactions or tainting the flavor of the beer.
Microbial Infections
Microbial infections pose a serious threat to the brewing process. Equipment that harbors bacteria, wild yeast, or mold can introduce these microorganisms into the beer, leading to spoilage and inconsistent flavors. The risk is particularly high for equipment with scratches, dents, or other imperfections that provide niches for microbes to thrive.
- Wild Yeast and Bacteria: Wild yeast and bacteria can outcompete the brewer’s yeast, leading to unintended fermentation processes. This can result in sour or otherwise off-flavored beer that deviates significantly from the intended product.
Residual Contaminants
Residual contaminants are often found in second-hand equipment, especially if it was not properly cleaned or stored after its previous use. These contaminants can include leftover wort, yeast, hops, and other brewing materials that can spoil new batches.
- Difficult-to-Clean Areas: Certain parts of the equipment, such as heat exchangers and complex valve systems, are particularly prone to harboring residual contaminants. These areas can be difficult to clean thoroughly, making it challenging to ensure that all traces of previous use are eliminated.
Biofilm Formation
Biofilm formation is a significant concern with used brewing equipment. Biofilms are colonies of microorganisms that adhere to surfaces and are surrounded by a protective matrix. These biofilms are notoriously difficult to remove and can resist standard cleaning procedures.
- Resistance to Cleaning: Biofilms can be resistant to many common sanitizers and cleaning agents. Once established, they can continuously shed microorganisms into the brewing process, leading to recurring contamination issues.
- Hidden Biofilms: Biofilms can form in places that are hard to inspect, such as inside pipes, on the inner surfaces of tanks, and within heat exchangers. Their hidden nature makes them a persistent threat that is challenging to eradicate.
Persistent Infections
Persistent infections occur when microorganisms that are difficult to eliminate take hold in the brewing equipment. These infections can lead to chronic contamination problems, repeatedly spoiling batches and undermining the consistency and quality of the beer.
- Recurrent Contamination: Persistent infections can cause recurrent contamination, leading to continuous quality control issues and financial losses. This can be particularly damaging for small breweries with limited resources to combat ongoing contamination problems.
- Cost of Remediation: Addressing persistent infections often requires extensive cleaning, potentially including chemical treatments and physical scrubbing, or even replacing infected parts of the equipment. These remediation efforts can be costly and time-consuming.
Mitigation Strategies
To mitigate these sanitation and hygiene concerns, brewers considering second-hand or refurbished equipment should implement rigorous cleaning and maintenance protocols. This includes:
- Thorough Inspection: Inspect all equipment for signs of wear, damage, and contamination before use. Look for areas that are difficult to clean and ensure they are properly sanitized.
- Rigorous Cleaning Regimen: Employ a comprehensive cleaning regimen using appropriate chemicals and sanitizers. Consider using high-temperature steam cleaning to address areas prone to biofilm formation.
- Regular Maintenance: Regularly maintain and inspect equipment to catch potential issues early. Replace worn or damaged parts promptly to prevent contamination risks.
- Professional Assessment: Engage professional services to assess and certify the cleanliness and safety of second-hand equipment, ensuring it meets industry standards.
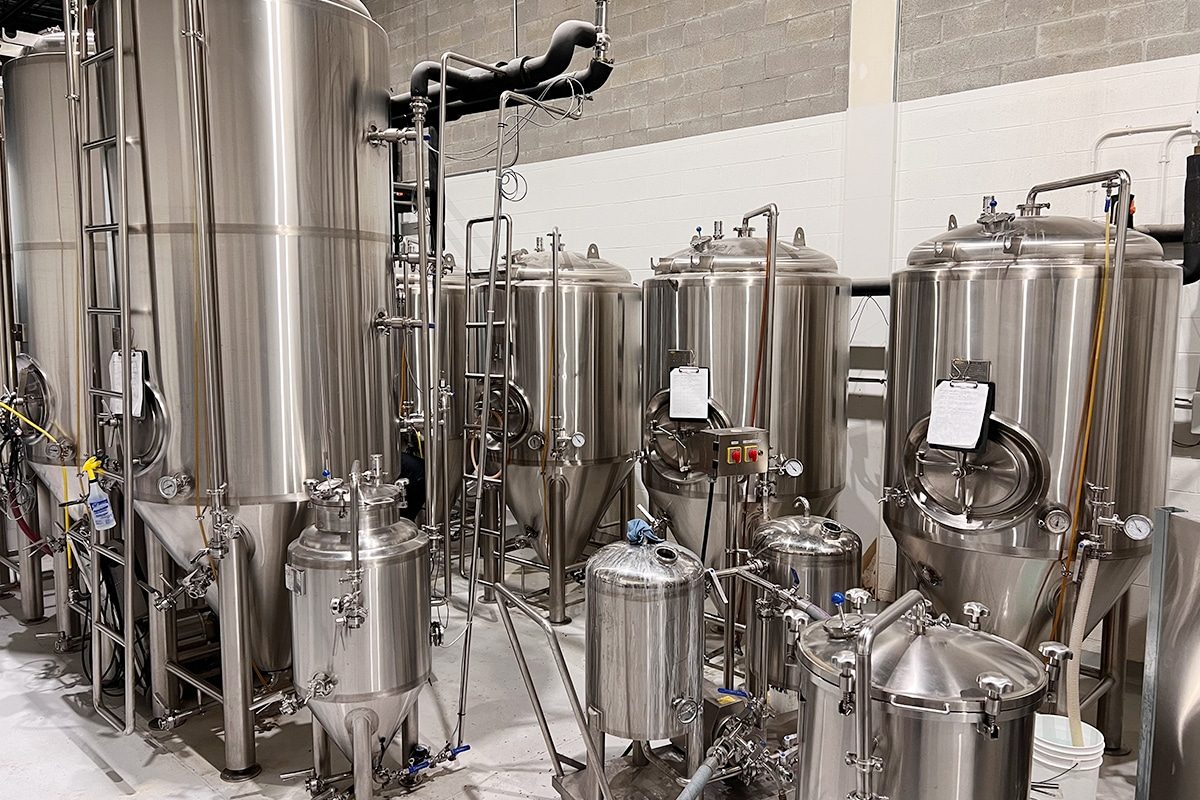
Compatibility and Integration Challenges
Technical Compatibility
Technical compatibility is a primary concern when incorporating second-hand equipment into an existing brewery. Differences in specifications, operating systems, and control interfaces can hinder smooth integration and lead to operational inefficiencies.
- Compatibility Checks: Before purchasing second-hand equipment, brewers must carefully assess its compatibility with their existing infrastructure. This includes evaluating electrical requirements, plumbing configurations, and compatibility with control systems.
- Customization Needs: In some cases, modifications or customizations may be necessary to achieve compatibility. This can involve retrofitting equipment with new fittings, adapting piping systems, or rewiring electrical components.
Mismatched Connections
Mismatched connections between second-hand equipment and existing infrastructure can complicate integration efforts. Variations in fitting sizes, thread types, and connection points can require additional time and resources to resolve.
- Adapter Requirements: Adapters or reducers may be needed to bridge the gap between incompatible connections. However, relying on adapters can introduce points of failure and compromise system reliability.
- Custom Fabrication: In cases where off-the-shelf adapters are not available, custom fabrication may be necessary. This adds complexity and cost to the integration process and can extend project timelines.
Inconsistent Sizing
Differences in equipment sizing between second-hand and existing equipment can pose significant challenges during integration. Mismatched sizes can affect fluid flow rates, mixing efficiency, and overall system performance.
- Sizing Discrepancies: Second-hand equipment may have different capacities or dimensions compared to existing components. For example, a larger fermentation tank may require modifications to accommodate the increased volume, such as changes to piping or tank supports.
- Impact on Process Efficiency: Inconsistent sizing can disrupt the brewing process, leading to inefficiencies and potential product quality issues. Brewers must carefully evaluate sizing discrepancies and develop strategies to mitigate their impact.
Software and Automation
Modern brewing equipment often includes sophisticated software and automation systems that streamline operations and improve process control. However, second-hand or refurbished equipment may lack these features, posing challenges for integration and automation.
- Lack of Automation: Older equipment may rely on manual controls or outdated automation technology. This can result in increased labor requirements and reduced process efficiency compared to fully automated systems.
- Compatibility Issues: Integrating legacy equipment with modern automation systems can be challenging due to differences in communication protocols and software interfaces. Compatibility issues may require custom programming or hardware modifications to resolve.
Integration Challenges
Integration challenges encompass a range of issues related to incorporating second-hand equipment into an existing brewery environment. These challenges can arise from technical, logistical, and operational factors, requiring careful planning and execution to overcome.
- Equipment Layout: Second-hand equipment must be integrated into the existing brewery layout in a way that optimizes space utilization and workflow efficiency. This may involve reconfiguring equipment placement or redesigning process flows to accommodate new components.
- Workflow Alignment: Integration efforts should aim to align workflow processes seamlessly across all equipment, minimizing bottlenecks and maximizing throughput. This requires careful coordination and communication between brewing staff and equipment suppliers.
- Testing and Commissioning: After installation, thorough testing and commissioning are essential to ensure the integrated system operates as intended. This includes functional testing, performance validation, and operator training to familiarize brewery staff with the new equipment.
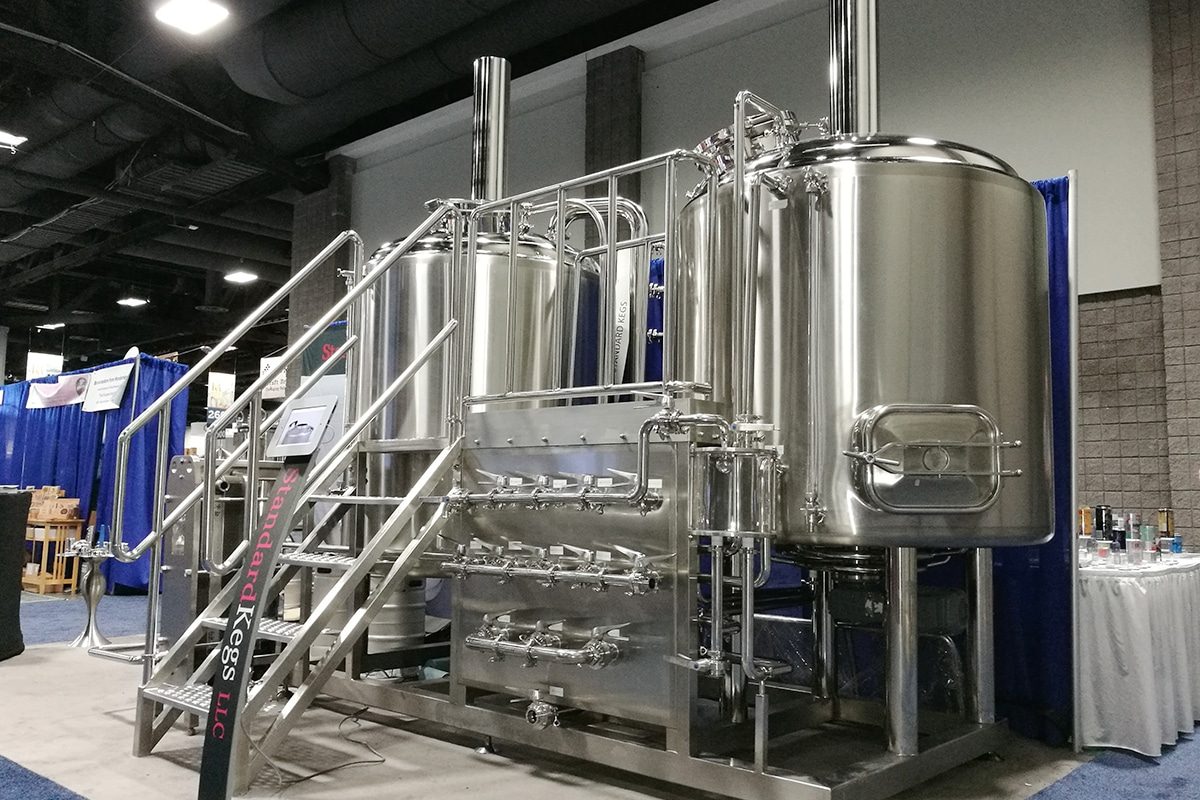
Warranty and Support Limitations
Lack of Warranty
Lack of warranty coverage is a significant drawback of purchasing second-hand equipment. Unlike new equipment, which typically comes with manufacturer warranties that provide financial protection against defects and malfunctions, second-hand equipment often lacks such coverage.
- Financial Risk: Without a warranty, breweries assume the full financial risk associated with any mechanical failures or defects that arise post-purchase. This can result in unexpected repair or replacement costs that strain the brewery’s budget and impact profitability.
- Reliability Concerns: The absence of a warranty raises concerns about the reliability and durability of the equipment. Breweries must consider the potential consequences of equipment failure on production schedules, product quality, and customer satisfaction.
Limited Manufacturer Support
Second-hand equipment may come with limited manufacturer support, particularly if the equipment is outdated or no longer supported by the original manufacturer. This lack of support can present numerous challenges for breweries seeking technical assistance and spare parts.
- Difficulty Obtaining Parts: Older equipment may have discontinued or hard-to-find parts, making it challenging to source replacements in the event of a breakdown. Breweries may need to explore alternative sources or consider aftermarket parts, which can be costly and may compromise equipment performance.
- Technical Assistance: Limited manufacturer support can also hinder breweries’ ability to access technical assistance and troubleshooting expertise. In the absence of manufacturer guidance, breweries may need to rely on in-house expertise or third-party service providers, leading to delays in resolving equipment issues.
Mitigation Strategies
To mitigate the risks associated with warranty and support limitations, breweries should consider the following strategies:
- Thorough Equipment Inspection: Conduct a comprehensive inspection of the second-hand equipment before purchase to identify any existing issues or potential areas of concern.
- Budget for Maintenance and Repairs: Allocate a portion of the equipment budget to cover ongoing maintenance, repairs, and potential replacements. This proactive approach helps mitigate the financial impact of unforeseen equipment failures.
- Diversify Spare Parts Inventory: Stockpile essential spare parts and components to minimize downtime in the event of equipment breakdowns. By maintaining a diverse inventory, breweries can reduce reliance on manufacturer support and expedite repairs.
- Establish Relationships with Suppliers: Cultivate relationships with equipment suppliers, aftermarket parts vendors, and technical service providers to access alternative sources of support and expertise.
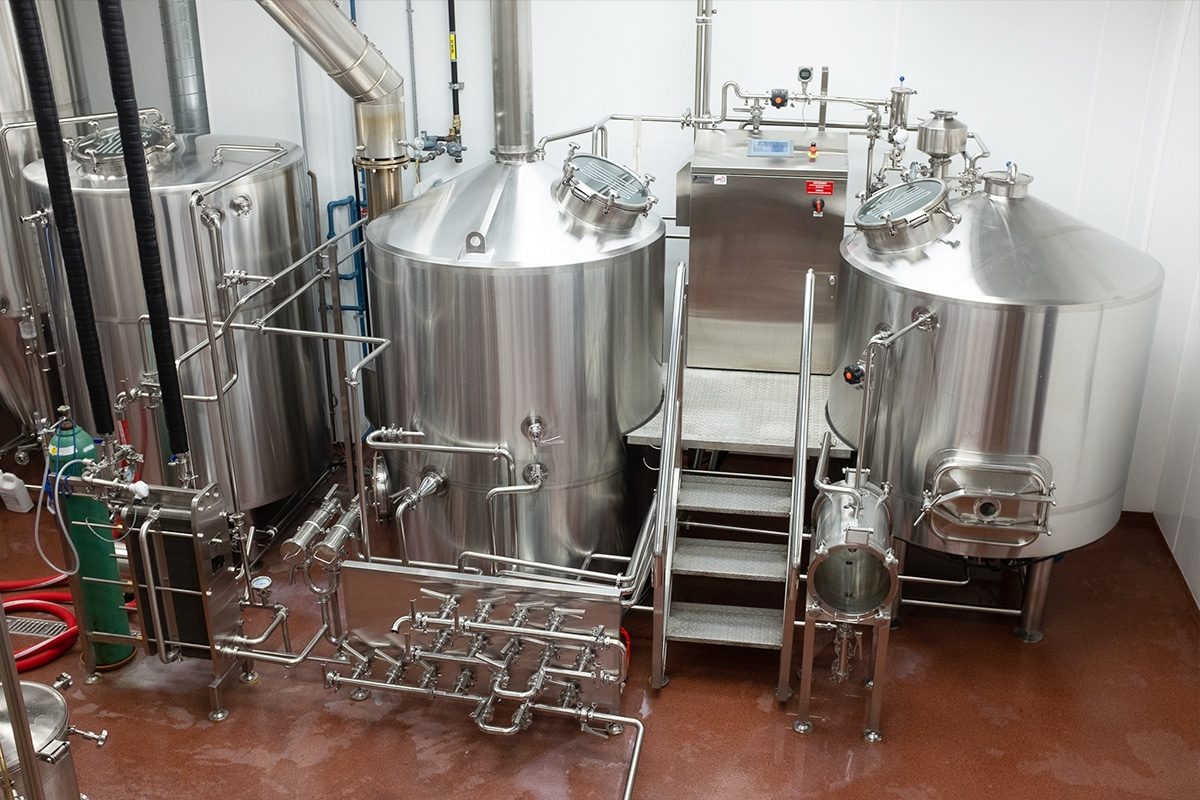
Financial Considerations
Hidden Costs
Hidden costs associated with second-hand brewery equipment can quickly accumulate and impact the overall financial viability of the investment. These costs may include unforeseen repairs, maintenance expenses, and additional modifications required to bring the equipment up to operational standards.
- Unexpected Repairs: Second-hand equipment may have underlying issues or wear-and-tear that are not immediately apparent. Breweries may incur unexpected repair costs shortly after purchase, requiring unplanned expenditures and impacting cash flow.
- Maintenance Expenses: Older equipment typically requires more frequent maintenance to ensure optimal performance and longevity. Breweries must budget for ongoing maintenance expenses, including routine servicing, replacement parts, and consumables.
- Modifications and Upgrades: Integrating second-hand equipment into an existing brewery setup may necessitate modifications or upgrades to enhance compatibility, efficiency, or safety. These modifications can incur additional costs and prolong the implementation timeline.
Energy Efficiency
Energy efficiency is a critical consideration in brewery operations, as energy costs constitute a significant portion of the overall operating expenses. Second-hand equipment may be less energy-efficient than newer models, leading to increased energy consumption and higher utility bills.
- Increased Energy Consumption: Older equipment often lacks modern energy-saving features and may operate less efficiently than newer models. Breweries may experience higher energy consumption, resulting in elevated operational costs over time.
- Environmental Impact: Inefficient equipment not only affects the brewery’s bottom line but also has a greater environmental impact. Breweries committed to sustainability may face challenges in reducing their carbon footprint and achieving their environmental goals.
Depreciation and Resale Value
The depreciation and resale value of second-hand brewery equipment can have significant implications for the brewery’s financial planning and asset management. Second-hand equipment generally depreciates faster and has a lower resale value compared to new equipment.
- Lower Resale Value: Second-hand equipment typically commands a lower resale value than new equipment due to factors such as age, wear and tear, and technological obsolescence. Breweries may struggle to recoup their initial investment when selling used equipment.
- Accelerated Depreciation: Second-hand equipment depreciates faster than new equipment, impacting the brewery’s balance sheet and financial performance. Accelerated depreciation may necessitate earlier equipment replacements or upgrades, requiring additional capital expenditure.
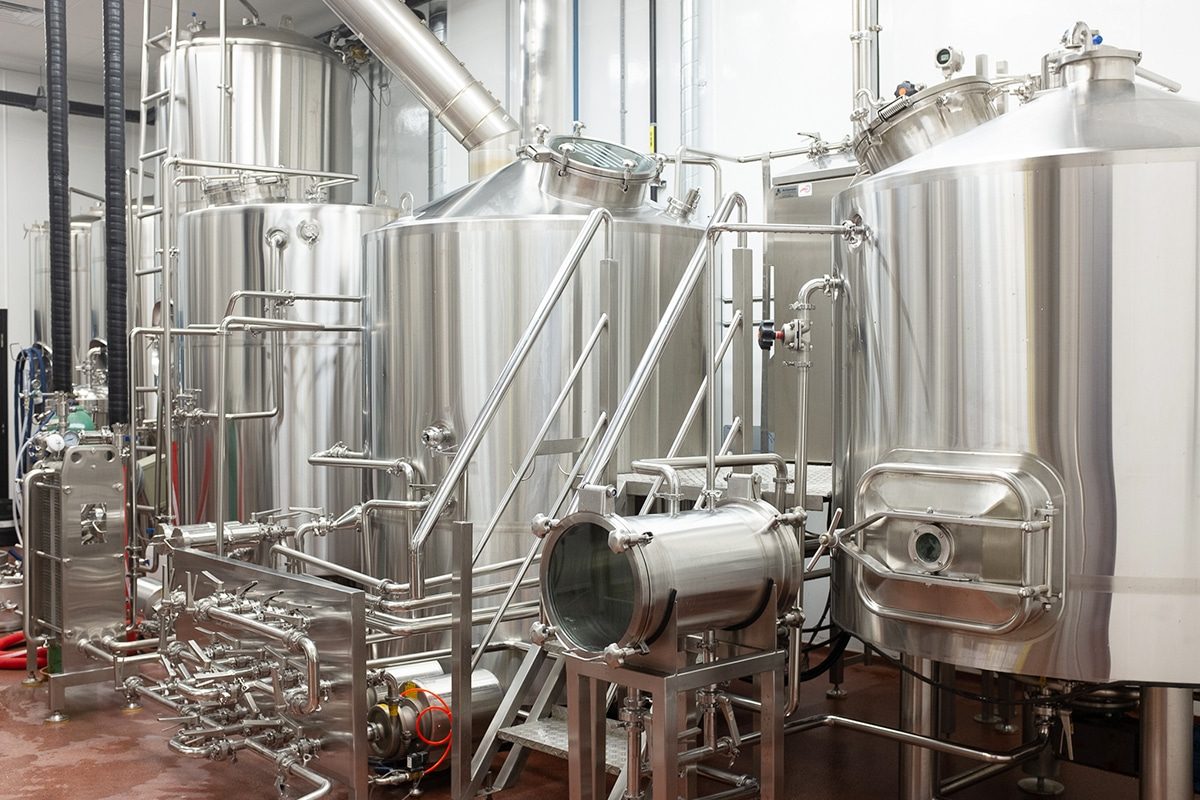
Regulatory and Compliance Risks
Safety Standards
Safety standards dictate the minimum requirements for equipment design, construction, and operation to ensure the safety of brewery workers and the integrity of the brewing process. Failure to meet these standards can result in accidents, injuries, and legal liabilities.
- Equipment Safety: Second-hand equipment may not meet current safety standards, particularly if it is outdated or poorly maintained. Breweries must assess the safety features of second-hand equipment and take necessary measures to address any deficiencies.
- Risk Assessments: Conduct comprehensive risk assessments to identify potential hazards associated with second-hand equipment and implement appropriate risk mitigation measures. This includes safeguarding against mechanical failures, electrical hazards, and ergonomic risks.
Compliance Issues
Compliance issues arise when second-hand equipment fails to meet regulatory requirements or industry standards. Non-compliance can lead to regulatory sanctions, fines, and operational disruptions.
- Regulatory Oversight: Regulatory bodies closely monitor brewery operations to ensure compliance with safety, sanitation, and environmental regulations. Breweries using second-hand equipment must demonstrate compliance with applicable regulatory requirements.
- Documentation Requirements: Maintain thorough documentation of equipment inspections, maintenance activities, and compliance certifications to demonstrate regulatory compliance and facilitate inspections.
Worker Safety
Ensuring worker safety is a top priority for breweries. Second-hand equipment that is poorly maintained or lacks essential safety features can pose significant risks to brewery personnel.
- Training and Education: Provide comprehensive training and education to brewery staff on the safe operation of second-hand equipment, hazard identification, and emergency procedures.
- Personal Protective Equipment (PPE): Equip brewery workers with appropriate PPE, including safety goggles, gloves, and hearing protection, to mitigate the risk of injuries during equipment operation and maintenance.
Licensing and Inspections
Breweries must obtain the necessary licenses and permits to operate legally and comply with local health and safety regulations. Using second-hand equipment can complicate the licensing process and subject breweries to increased scrutiny during inspections.
- Regulatory Compliance: Ensure that second-hand equipment meets regulatory requirements and standards before applying for licenses and permits. Non-compliance can lead to delays in obtaining approvals and approvals.
- Inspection Preparedness: Prepare for regulatory inspections by maintaining accurate records, addressing identified deficiencies, and implementing corrective actions as necessary.
Inspection Challenges
Inspecting second-hand equipment for compliance with regulatory standards can pose challenges, particularly if the equipment is outdated or lacks documentation of its history and maintenance.
- Documentation Verification: Verify the authenticity and accuracy of documentation provided by equipment sellers, including maintenance records, compliance certifications, and inspection reports.
- Technical Assessment: Engage qualified professionals to conduct technical assessments and inspections of second-hand equipment to identify potential safety hazards and compliance issues.
Potential Non-Compliance
Failure to comply with regulatory requirements can result in non-compliance, leading to regulatory sanctions, fines, and reputational damage.
- Regulatory Enforcement: Regulatory bodies may impose penalties for non-compliance, including fines, warnings, and enforcement actions. Breweries must take proactive measures to address identified deficiencies and mitigate compliance risks.
- Reputational Damage: Non-compliance can tarnish the brewery’s reputation and erode consumer trust. Breweries must prioritize regulatory compliance to uphold their commitment to safety, quality, and integrity.
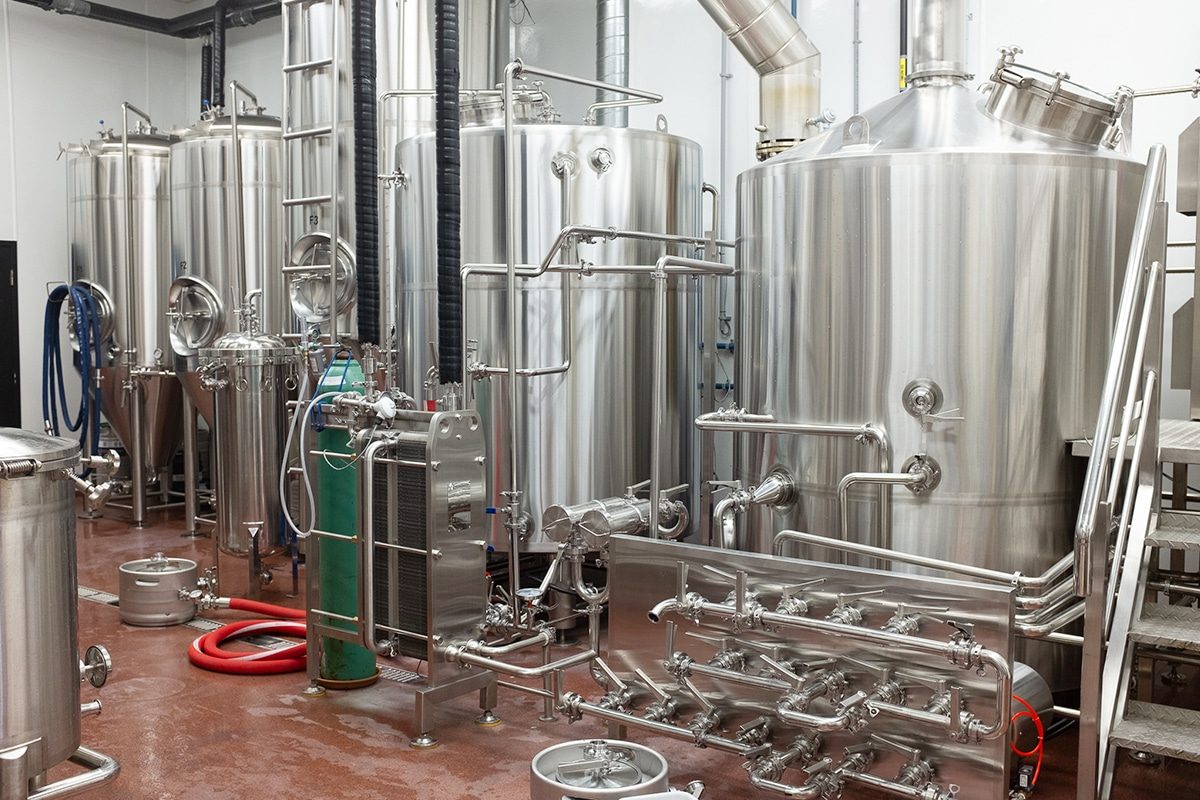
Operational Efficiency and Downtime
Increased Downtime
Increased downtime is a common challenge associated with second-hand brewery equipment. Older or refurbished equipment is more prone to breakdowns and malfunctions, leading to periods when production is halted.
- Unplanned Downtime: Unexpected equipment failures can occur more frequently with second-hand equipment, causing unplanned downtime. This can disrupt the brewing process, delay product deliveries, and impact overall production capacity.
- Production Losses: Each instance of downtime results in lost production time and potential revenue loss. For small breweries, even short periods of downtime can have a significant financial impact.
Repair Time
The repair time for second-hand equipment can be longer than for new equipment due to several factors, including the availability of parts and the complexity of the repairs needed.
- Parts Availability: Finding replacement parts for older or discontinued equipment can be challenging and time-consuming. Breweries may need to source parts from multiple suppliers or rely on custom fabrication, extending repair times.
- Complex Repairs: Older equipment may require more complex repairs, involving detailed diagnostics and skilled technicians. This can prolong the downtime and increase repair costs.
Scheduling Disruptions
Scheduling disruptions are a significant risk when relying on second-hand equipment. Frequent breakdowns and repairs can interfere with planned production schedules, leading to delays and inefficiencies.
- Production Planning: Consistent equipment performance is essential for effective production planning. Unreliable second-hand equipment can cause schedule slippages, making it difficult to meet production targets and customer demands.
- Bottlenecks: Breakdowns can create bottlenecks in the production process, where certain stages of brewing are delayed or halted, affecting the entire workflow.
Maintenance Demands
The maintenance demands of second-hand equipment are typically higher compared to new equipment. This includes more frequent maintenance checks, servicing, and part replacements to keep the equipment running smoothly.
- Preventive Maintenance: Breweries must implement rigorous preventive maintenance programs to mitigate the risk of unexpected breakdowns. This involves regular inspections, cleaning, lubrication, and part replacements.
- Corrective Maintenance: In addition to preventive maintenance, breweries must be prepared for corrective maintenance to address issues as they arise. This reactive approach can be costly and time-consuming.
Maintenance Frequency
The maintenance frequency for second-hand equipment is generally higher, necessitating more frequent interventions to ensure operational reliability.
- Increased Intervals: Older equipment often requires maintenance at shorter intervals due to wear and tear. This increases the workload on maintenance teams and can lead to higher operational costs.
- Inspection Program: A regular inspection program can help identify potential problems before they cause a major failure. This proactive approach helps in planning maintenance activities but requires dedicated resources.
Resource Allocation
Effective resource allocation can help manage the growing demand for used equipment maintenance. This includes allocating financial, human, and material resources to ensure the equipment remains operational.
- Financial Resources: Budgeting for higher maintenance and repair costs is crucial. This includes setting aside funds for unexpected repairs, spare parts, and potential equipment upgrades.
- Human Resources: Skilled maintenance personnel are needed to perform regular maintenance and repairs. Training staff to handle older equipment and troubleshooting issues can be resource-intensive.
- Material Resources: Stocking essential spare parts and consumables is necessary to minimize downtime. This requires efficient inventory management and supplier relationships.
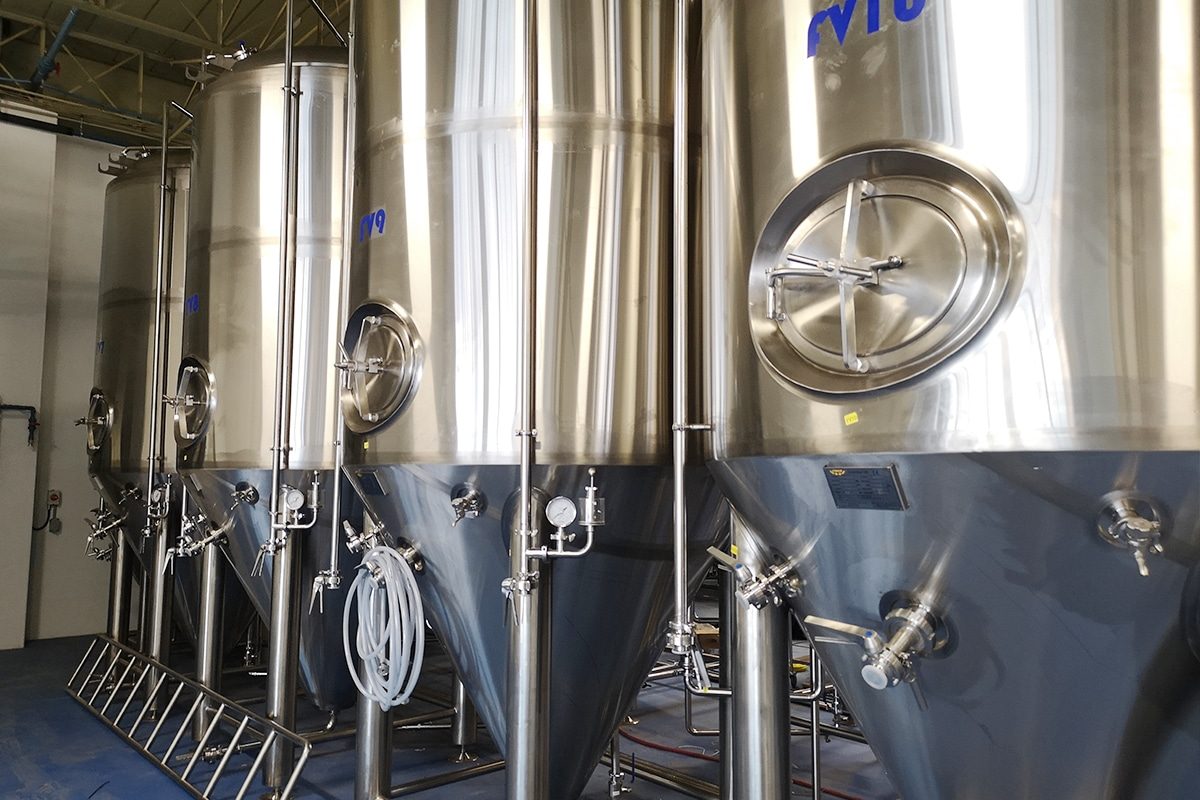
Strategies for Mitigating Risks
Thorough Inspection and Testing
Thorough inspection and testing of second-hand equipment are crucial steps before integration into your brewery operations. This process helps identify potential issues that could affect performance and safety.
- Initial Assessment: Conduct a detailed visual and operational inspection of the equipment to identify any visible signs of wear, damage, or corrosion. This initial assessment should include checking for leaks, assessing the condition of seals and gaskets, and ensuring that all components are intact.
- Functional Testing: Perform comprehensive functional tests to ensure the equipment operates as intended. This includes running the equipment through typical brewing cycles to check for any operational anomalies or inefficiencies.
- Third-Party Verification: Consider hiring third-party inspectors or consultants who specialize in brewery equipment to provide an unbiased assessment. These professionals can offer insights into the equipment’s condition and potential areas of concern.
Cleaning and Sanitization
Proper cleaning and sanitizing prevent contamination and ensure the safety and quality of brewed products.
- Deep Cleaning: Before use, perform a deep cleaning of all equipment surfaces that come into contact with brewing ingredients. Use appropriate cleaning agents designed for brewery equipment to remove any residues, oils, or contaminants.
- Sanitization Protocols: Implement rigorous sanitization protocols to eliminate any microbial contaminants. This involves using food-grade sanitizers and ensuring that all surfaces are thoroughly sanitized before each use.
- Regular Maintenance: Establish a regular cleaning and sanitization schedule to maintain hygiene standards. This routine should include cleaning after each use and periodic deep cleaning to prevent biofilm formation and persistent infections.
Custom Modifications
Custom modifications may be necessary to adapt second-hand equipment to the specific needs and standards of your brewery. These modifications can enhance compatibility, performance, and safety.
- Retrofits and Upgrades: Consider retrofitting the equipment with modern components or upgrades to improve efficiency and performance. This might include installing new control systems, upgrading heating or cooling elements, or adding safety features.
- Professional Modifications: Engage professional engineers or technicians who specialize in brewery equipment to perform any necessary modifications. This ensures that modifications are done correctly and safely, maintaining the integrity of the equipment.
- Customization for Fit: Modify equipment to fit seamlessly into the existing brewery layout and processes. This can involve adjusting connections, resizing components, or adapting the equipment to work with existing automation systems.
Budgeting for Maintenance
An effective maintenance budget can help manage long-term costs and ensure the reliability of used equipment.
- Maintenance Fund: Establish a dedicated maintenance fund to cover routine upkeep and unexpected repairs. This financial buffer helps prevent operational disruptions due to unforeseen equipment failures.
- Scheduled Maintenance: Implement a scheduled maintenance program to perform regular checks and preventive maintenance tasks. This proactive approach can extend the lifespan of the equipment and reduce the likelihood of major breakdowns.
- Spare Parts Inventory: Maintain an inventory of essential spare parts to minimize downtime during repairs. Stock commonly needed parts such as seals, gaskets, and bearings to enable quick replacements.
Ensuring Regulatory Compliance
Ensuring compliance with regulations can avoid legal issues and maintain operational standards.
- Compliance Audit: Conduct a compliance audit to ensure that second-hand equipment meets all relevant safety, health, and environmental regulations. This audit should be thorough and cover all aspects of the equipment’s operation.
- Documentation: Keep detailed records of inspections, maintenance activities, and compliance certifications. Proper documentation is essential for regulatory inspections and can help demonstrate compliance with industry standards.
- Regulatory Updates: Stay informed about updates to regulations and standards that affect brewery operations. Ensure that any second-hand equipment is upgraded or modified as needed to remain compliant with current regulations.
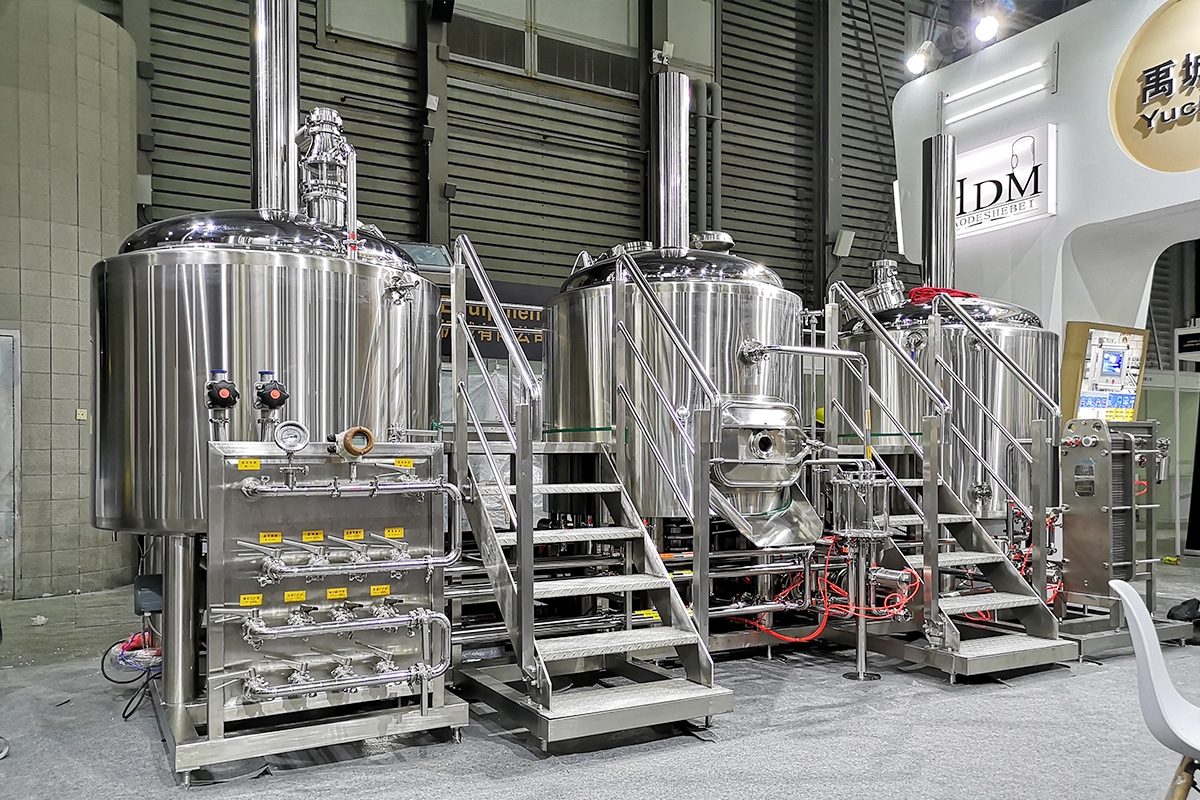
Summarize
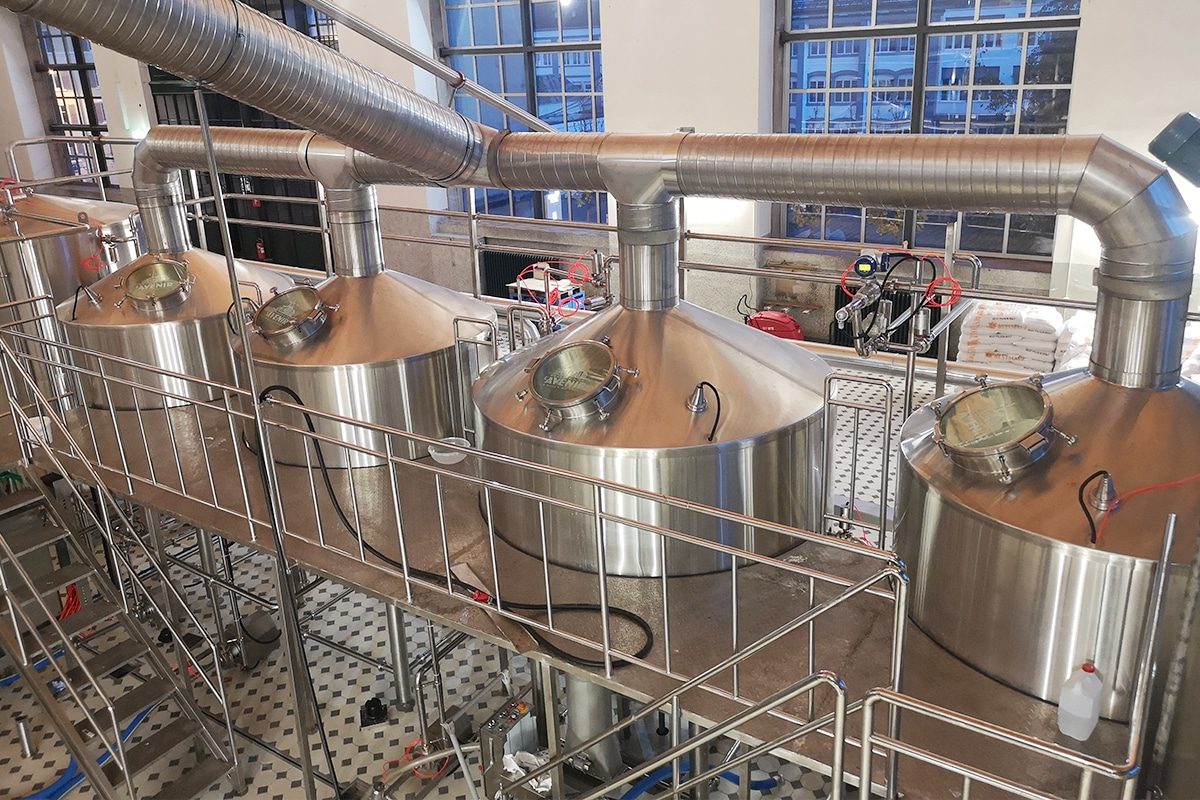