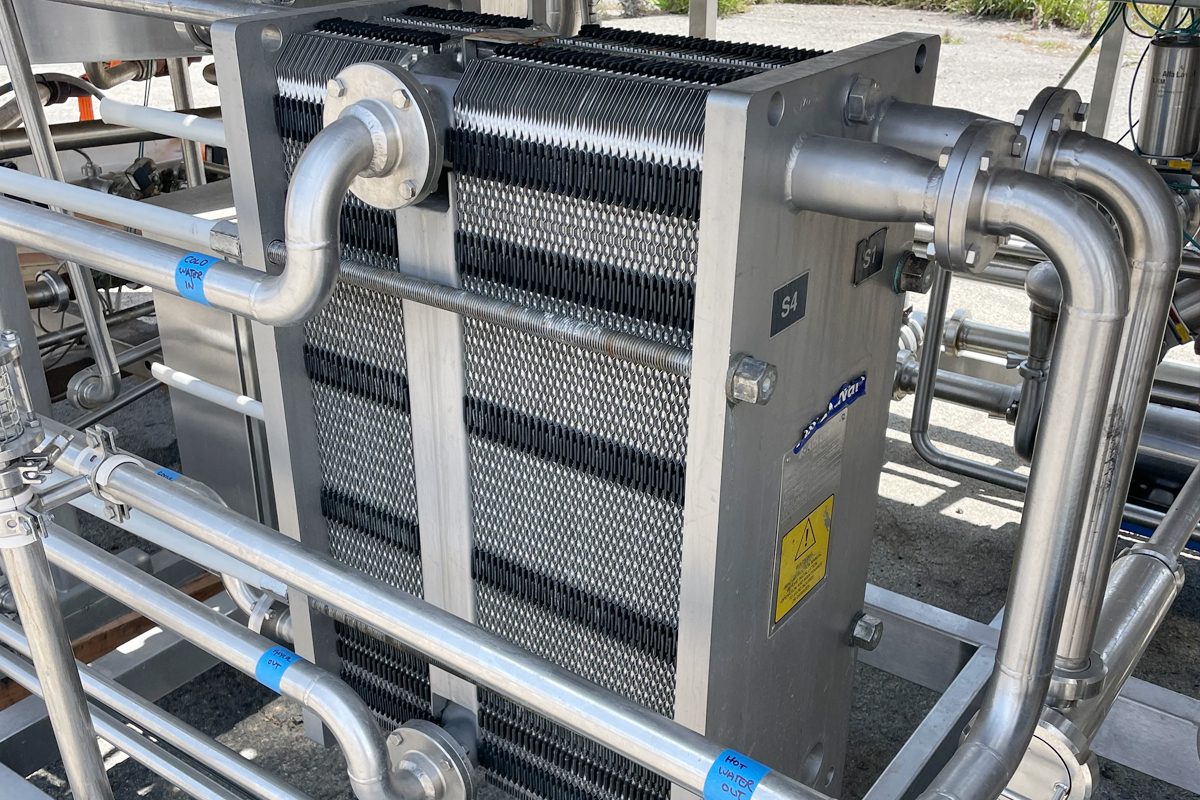
Reasons Why Breweries Choose Plate Heat Exchangers
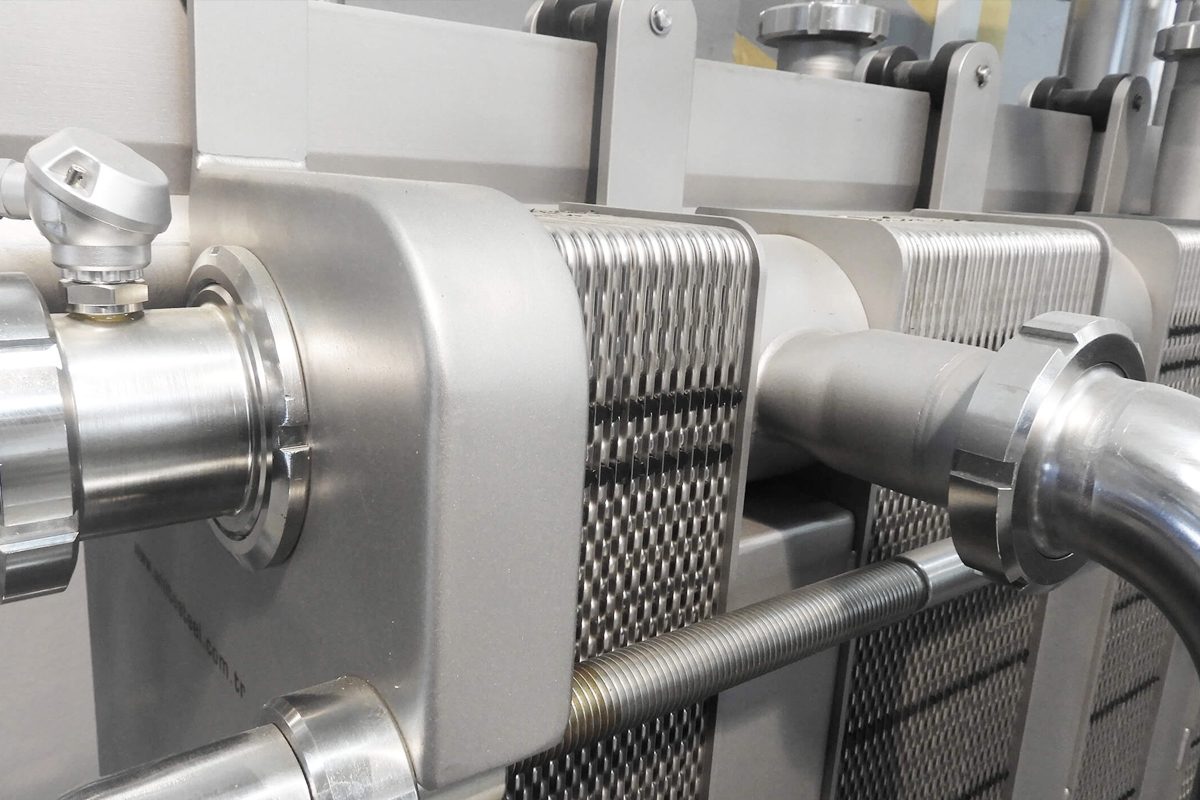
What are Plate Heat Exchangers?
Definition and Basic Principles
Types of Plate Heat Exchangers
- Gasketed Plate Heat Exchangers: They are the most common type used in various industries, including brewing. These units feature plates sealed with gaskets that are positioned between each plate. The gaskets ensure that the fluids do not mix and that the heat transfer occurs efficiently. One of the key advantages of gasketed plate heat exchangers is their ease of maintenance and cleaning. The gaskets allow for the disassembly of the unit, making it easier to access and clean the plates. This type is ideal for applications where frequent cleaning and maintenance are necessary, such as in the brewing industry.
- Welded Plate Heat Exchangers: They are designed for high-pressure and high-temperature applications. Unlike gasketed models, the plates in a welded heat exchanger are permanently sealed by welding, which eliminates the need for gaskets. This design provides a robust and leak-proof construction, making welded plate heat exchangers suitable for demanding processes. They are commonly used in applications where the fluids are highly corrosive or where high pressures are involved. However, the permanent sealing makes maintenance more challenging compared to gasketed models.
- Brazed Plate Heat Exchangers: They are characterized by plates that are bonded together through a brazing process. This method involves joining the plates using a filler metal with a lower melting point than the base metals. Brazed plate heat exchangers offer a compact and highly efficient design, with no gaskets or welding involved. The absence of gaskets makes them ideal for applications where space is limited and where the heat exchanger needs to be highly resistant to pressure and temperature fluctuations. They are commonly used in smaller-scale operations or where space and efficiency are critical factors.
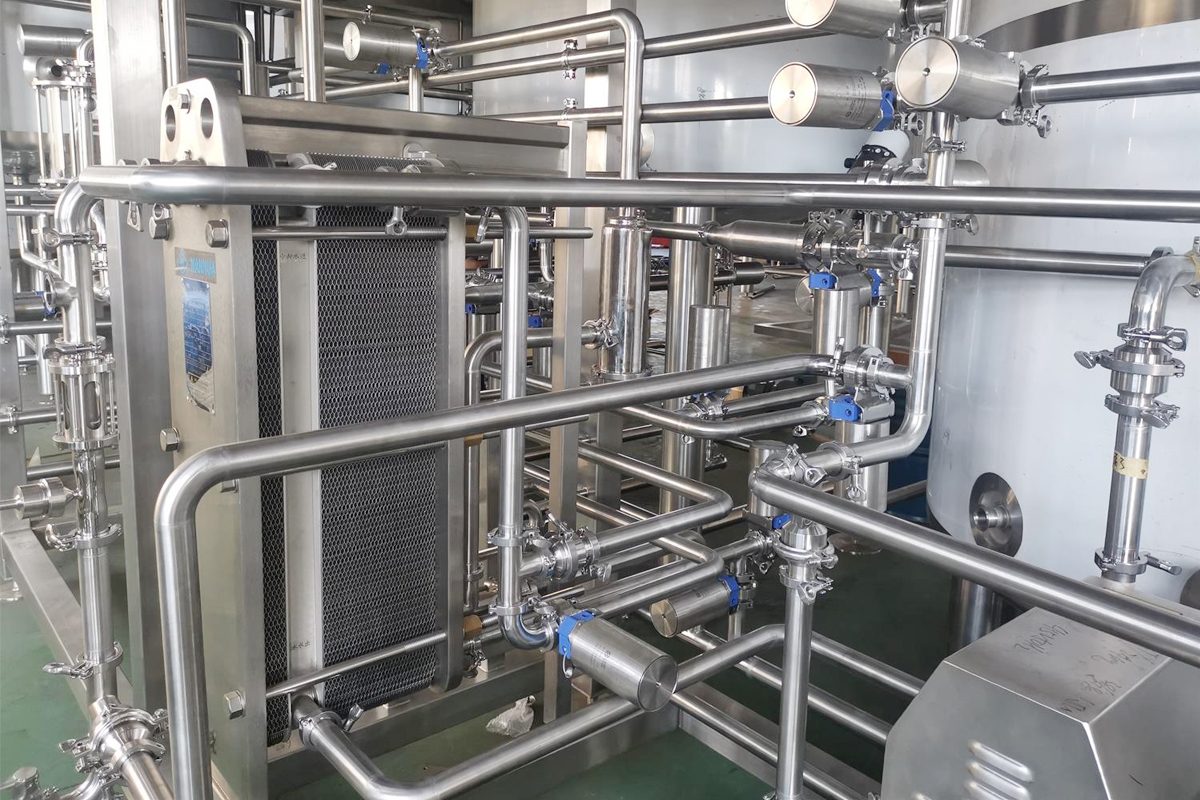
Advantages of Plate Heat Exchangers for Breweries
High Thermal Efficiency
Compact Design
Flexibility and Scalability
Easy Maintenance
Cost-Effectiveness
High Pressure and Temperature Tolerance
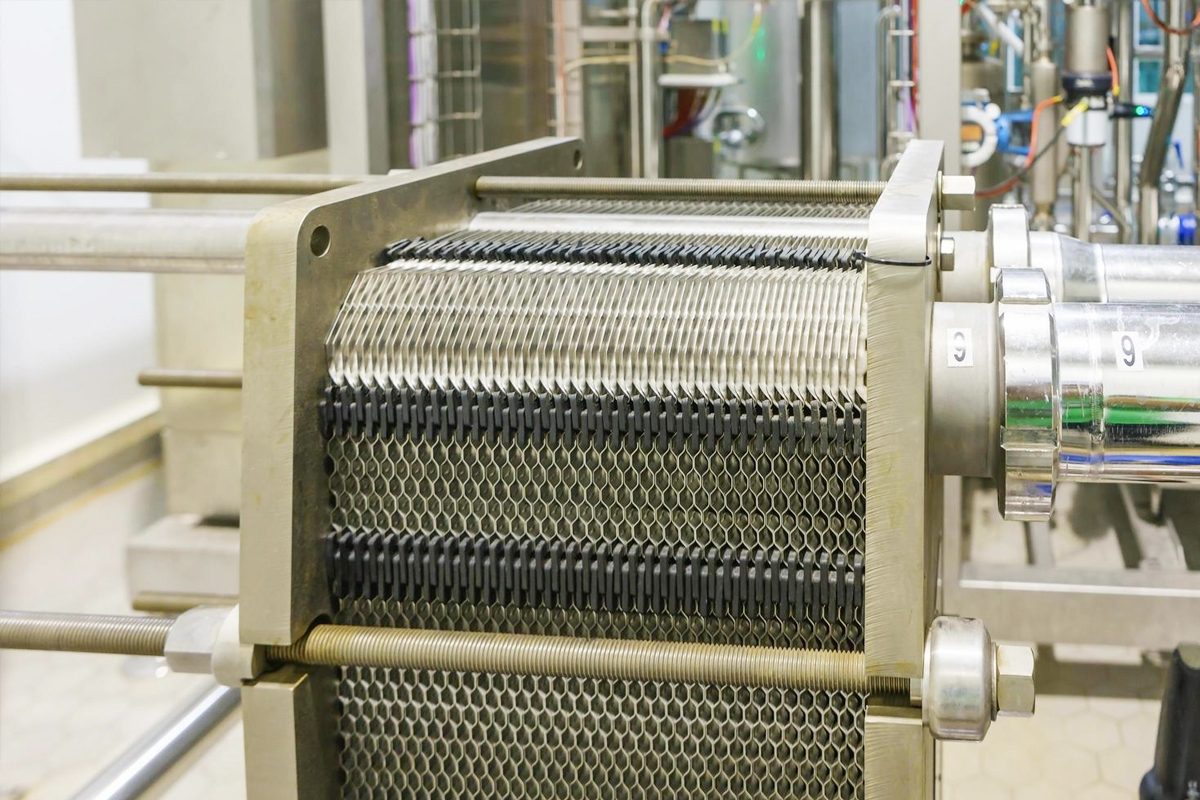
Applications in the Brewing Industry
Wort Cooling
Hot Water Heating
Pasteurization
Heat Recovery

Technical Considerations and Challenges
Design and Sizing
The design and size of a plate heat exchanger affect its performance and efficiency. Proper design involves selecting the right configuration and plate type based on the specific heat transfer requirements of the brewing process. Factors such as the flow rate, temperature difference, and the nature of the fluids being processed all influence the design.
- Flow Arrangement: Plate heat exchangers can be designed with various flow arrangements, including counterflow, parallel flow, and crossflow. The choice of flow arrangement affects the efficiency of heat transfer. Counterflow designs, where fluids flow in opposite directions, typically offer the highest heat transfer efficiency and are often preferred in brewing applications.
- Plate Type and Configuration: Different types of plates, such as chevron or semi-welded, provide varying levels of heat transfer efficiency and pressure drop. The selection depends on the specific needs of the brewery, such as handling particulate matter or high-viscosity fluids.
- Sizing: Accurate sizing ensures that the heat exchanger meets capacity requirements and does not cause excessive pressure drop or inefficient heat transfer. Oversized units can lead to unnecessary costs and space utilization, while undersized units may fail to deliver the required performance. Computational tools and manufacturer guidelines can assist in selecting the appropriate size.
Maintenance and Cleaning
Regular maintenance and cleaning can ensure the efficient operation of the plate heat exchanger and increase its service life. The design of PHEs facilitates easier maintenance compared to other types of heat exchangers, but some challenges still exist.
- Cleaning Procedures: Gasketed plate heat exchangers allow for disassembly, making cleaning relatively straightforward. However, breweries must establish effective cleaning procedures to remove residues, scales, and biofilms that can accumulate on the plates. Common cleaning methods include chemical cleaning and mechanical scrubbing.
- Fouling and Scaling: Fouling, which occurs when unwanted materials adhere to the heat exchanger surfaces, and scaling, which involves the buildup of mineral deposits, can reduce heat transfer efficiency and increase maintenance needs. Regular monitoring and cleaning schedules are necessary to manage these issues and maintain optimal performance.
- Access and Disassembly: While gasketed plate heat exchangers are designed for easy disassembly, the process of accessing and reassembling the unit can be labor-intensive. Breweries must ensure that maintenance staff are trained and equipped to handle these tasks efficiently to minimize downtime.
Material Selection
Selecting the appropriate plate heat exchanger material ensures compatibility with the fluids being processed and the operating conditions.
- Corrosion Resistance: Breweries handle various fluids, including acidic or alkaline solutions. Therefore, materials used in plate heat exchangers must exhibit good corrosion resistance to prevent degradation and maintain performance. Stainless steel is commonly used due to its excellent corrosion resistance, but other materials like titanium or specialized alloys may be necessary for more demanding conditions.
- Thermal Conductivity: The materials should have high thermal conductivity to ensure effective heat transfer. Stainless steel and other high-conductivity alloys are often chosen to maximize the efficiency of the heat exchanger.
- Compatibility with Cleaning Agents: The materials must also be compatible with cleaning agents used in maintenance procedures. Incompatibility can lead to material degradation and potential leaks or failures. Breweries should consult with manufacturers to ensure that the chosen materials will withstand the cleaning agents used in their processes.
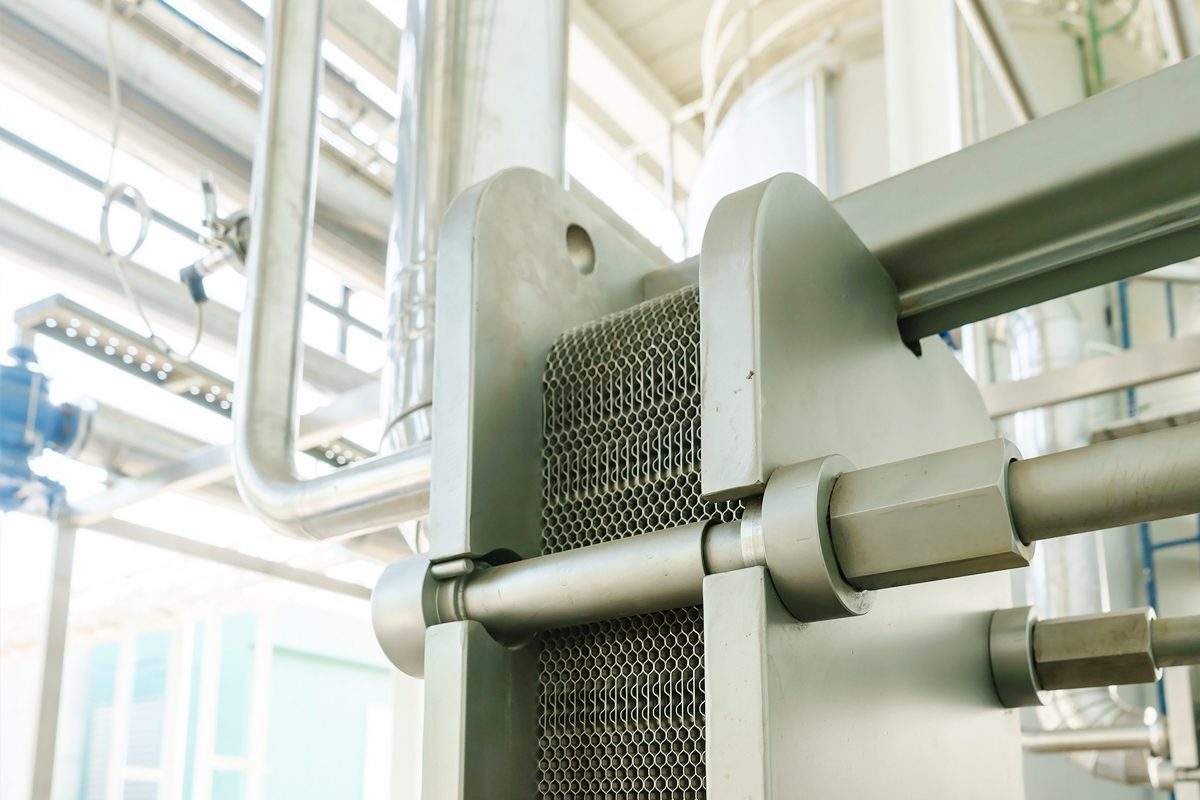
Considerations When Choosing a Plate Heat Exchanger
Material Compatibility
Material compatibility is a crucial factor when choosing a plate heat exchanger, as it directly impacts the unit’s durability and performance. The materials used in the construction of the plates and gaskets must be compatible with the fluids they will handle. In brewing applications, fluids may vary from wort to cleaning solutions, so materials need to be selected that are resistant to corrosion, erosion, and chemical reactions.
- Corrosion Resistance: Stainless steel is a popular choice due to its excellent corrosion resistance and durability. For more aggressive fluids or higher temperatures, specialized alloys or coatings may be required.
- Compatibility with Cleaning Agents: The selected materials must withstand the cleaning agents used in maintenance without degrading. Breweries should consult with manufacturers to ensure that the materials can handle the specific chemicals used for cleaning and sanitation.
Temperature and Pressure Requirements
Plate heat exchangers must be selected based on their ability to handle the temperature and pressure conditions of the brewing process. The unit must be capable of operating efficiently within the temperature and pressure ranges required for various applications such as wort cooling, hot water heating, and pasteurization.
- Temperature Range: Ensure that the heat exchanger can handle the maximum temperatures of the fluids involved. Different types of plate heat exchangers (e.g., welded or brazed) offer varying temperature tolerances.
- Pressure Rating: The heat exchanger should be designed to withstand the pressures of the process fluids. Overestimating or underestimating the required pressure rating can lead to equipment failure or inefficiencies.
Maintenance Requirements
The ease of maintenance is a significant consideration, as regular upkeep is necessary to ensure the long-term performance and efficiency of the plate heat exchanger.
- Ease of Access: Gasketed plate heat exchangers are designed for easy disassembly, which simplifies cleaning and maintenance. Ensure that the design allows for straightforward access to the plates for routine maintenance tasks.
- Cleaning Procedures: Consider the cleaning requirements of the heat exchanger. Choose a unit that can be effectively cleaned with the standard procedures used in the brewery to prevent fouling and scaling.
Energy Efficiency
Energy efficiency is a key factor in reducing operational costs and improving the overall sustainability of the brewing process. Plate heat exchangers are known for their high thermal efficiency, but it is essential to evaluate their performance in the context of the brewery’s specific needs.
- Heat Transfer Efficiency: Look for a heat exchanger that maximizes heat transfer between fluids while minimizing heat loss. Higher thermal efficiency translates to better energy utilization and cost savings.
- Operational Costs: Consider the impact of the heat exchanger on energy consumption. Efficient heat transfer can lead to reduced energy requirements for heating or cooling, resulting in lower utility bills.
Cost VS Performance
When selecting a plate heat exchanger, you need to balance cost and performance. The initial investment should be weighed against the long-term benefits and operational savings provided by the unit.
- Initial Cost: Evaluate the upfront cost of the heat exchanger, including installation and any additional components required. While higher-quality units may come with a higher price tag, they can offer better performance and longevity.
- Long-Term Value: Consider the total cost of ownership, including maintenance, energy consumption, and potential downtime. A more expensive unit with higher efficiency and durability may provide better value over time compared to a lower-cost option with higher operating costs.
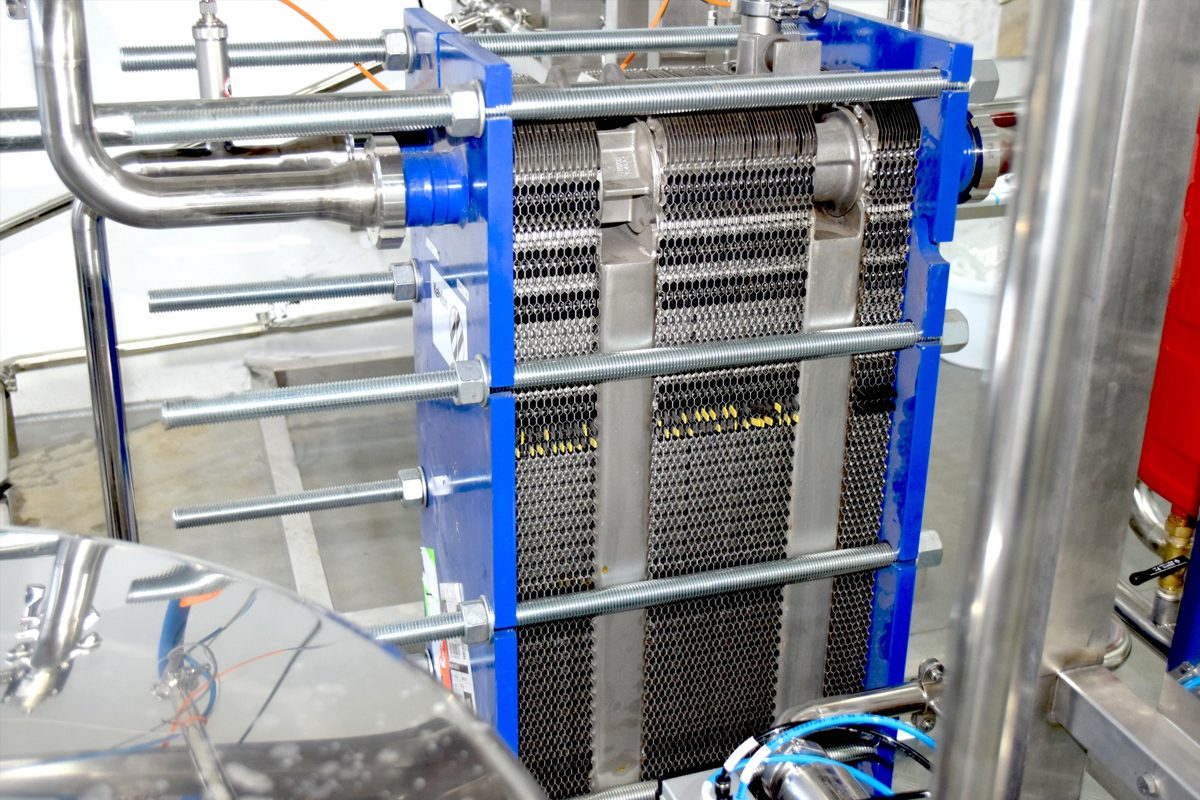
Summary
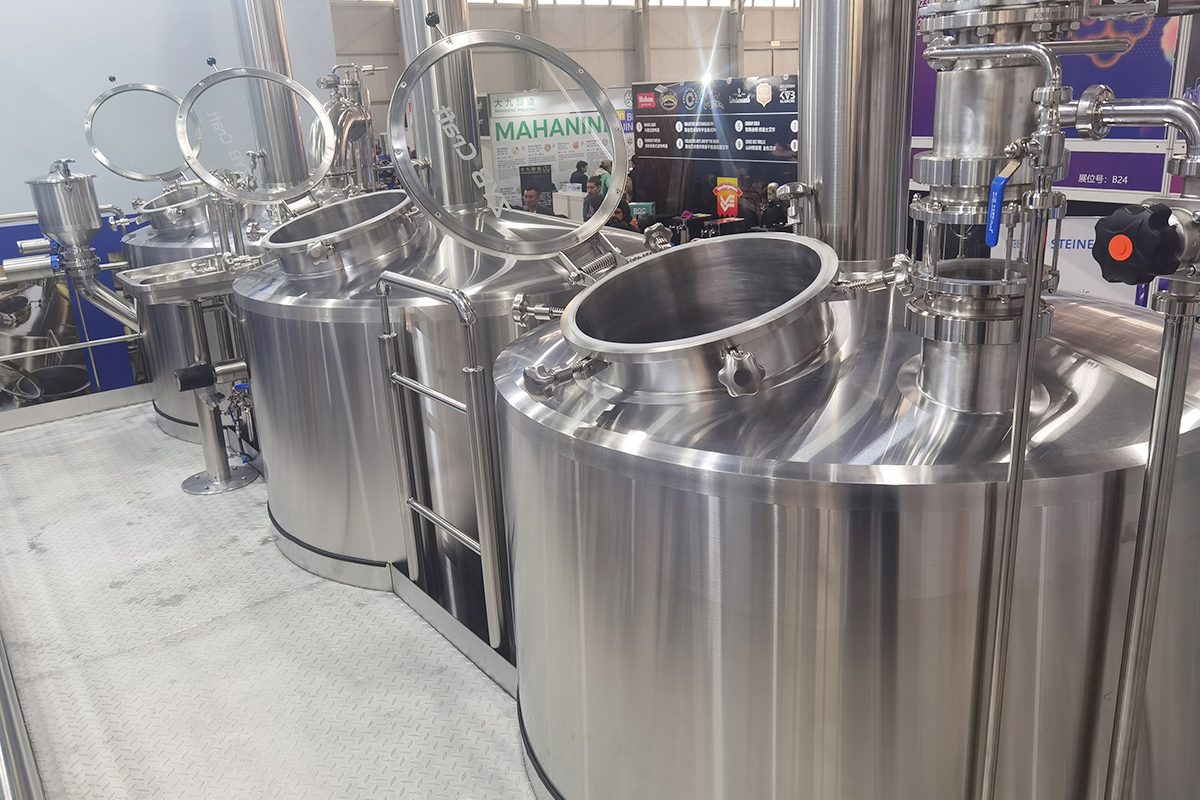