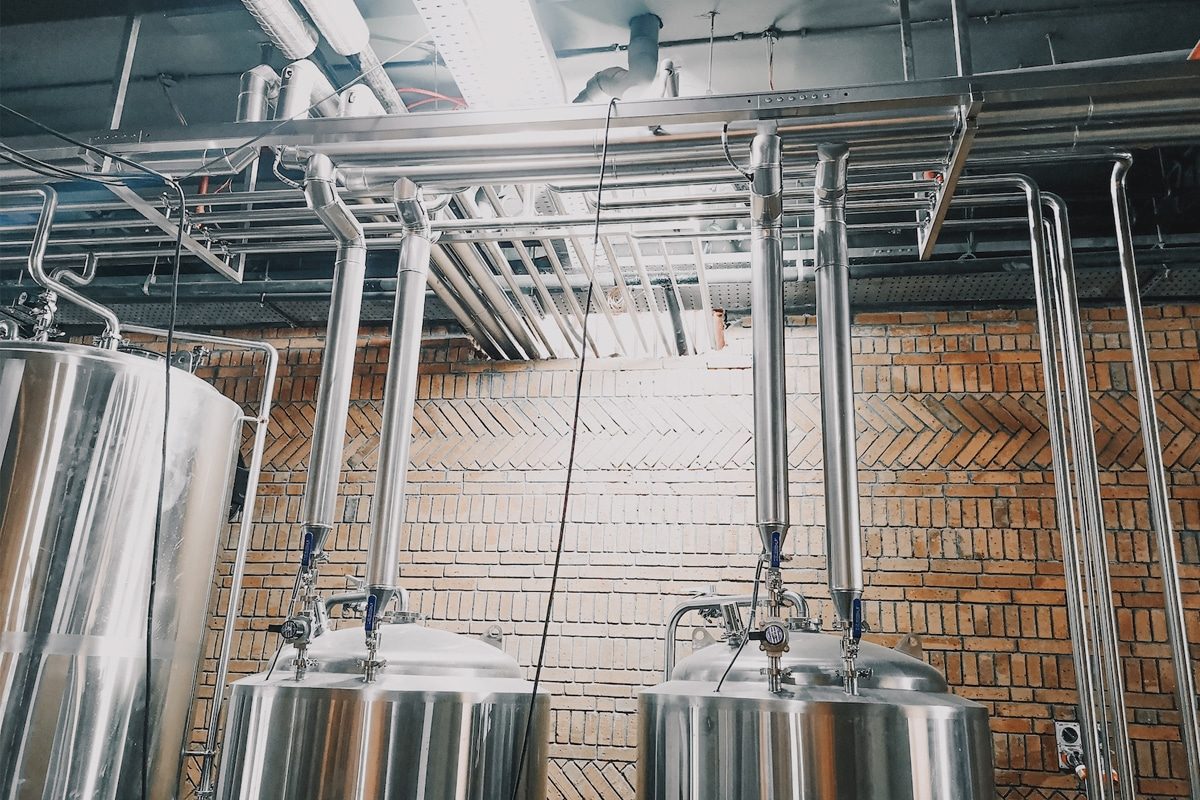
Mastering Brewery Chiller Sizing: A Comprehensive Guide for Brewers
Brewing beer is a multi-faceted endeavor that combines art and science to produce the perfect craft beer. Among the countless pieces of equipment essential to the brewing process, the brewery chiller acts as a silent guardian, ensuring the precise temperature control needed to brew quality beer. However, choosing the right size for a brewery chiller is not just a matter of guesswork, but a meticulous process that requires a thorough understanding of brewing dynamics and refrigeration principles.
In this comprehensive guide, we embark on a journey to demystify the art of brewery chiller selection. From understanding the nuances of cooling requirements to mastering the calculations needed to determine cooler capacity, we provide brewers with the knowledge and insights they need to improve their brewing operations. Whether you’re an experienced brewer or a novice hobbyist, this guide can serve as your compass in navigating the complex world of brewery chiller sizing.
Complete Guide
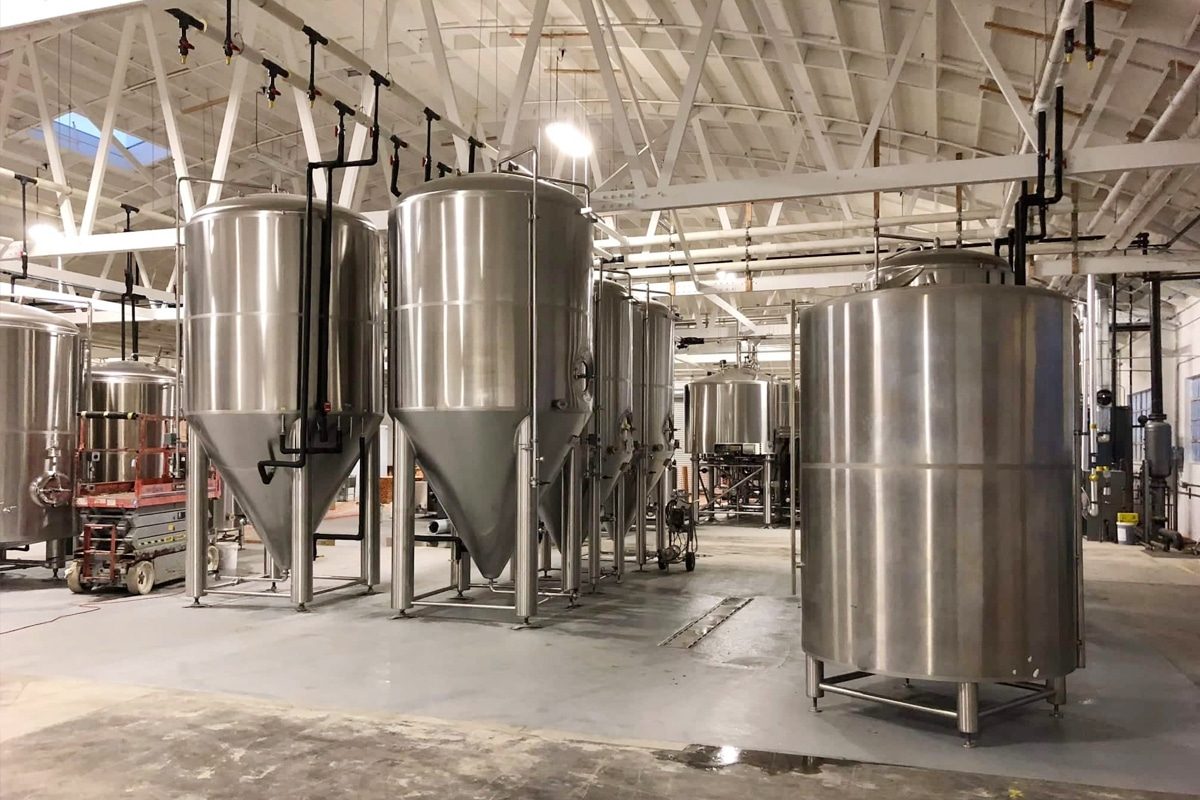
Learn About Brewery Chillers
Brewery chillers are an essential component in any brewing operation and are the cooling backbone that ensures the quality and consistency of the final product. Next, we’ll dive into what a brewery chiller is, its critical role in brewing, and the various types available in breweries.
What is A Brewery Chiller?
Brewery chillers are refrigeration systems specifically designed to regulate and control temperature throughout the brewing process. These systems utilize advanced cooling technology to remove heat from brewing media such as wort, fermenting beer, and refrigerated areas, allowing breweries to maintain precise temperature levels that are critical to producing high-quality beer.
The Role of Chiller in Brewing
The importance of a brewery chiller cannot be overstated, as temperature control is critical at every stage of the brewing process. Here is a detailed explanation of the key role played by chillers:
- Wort Cooling: After the boiling stage, the wort (unfermented beer) must be cooled quickly to a specific temperature to facilitate the fermentation process. Brewery chillers can accomplish this task effectively, preventing odors and ensuring an optimal fermentation environment for yeast.
- Fermentation Temperature Control: Maintaining consistent temperatures during fermentation helps keep yeast healthy and flavor development. Chillers regulate the temperature within the fermentation vessel, allowing the brewery to achieve the desired fermentation profile and produce consistent batches of beer.
- Chilling: Once fermentation is complete, the beer is refrigerated and stored to further develop its flavor and clarity. Brewery chillers maintain precise temperatures in refrigerated areas, ensuring beer remains stable and ready for packaging.
Types of Brewery Chillers
There are many types of brewery chillers, each tailored to specific brewing needs and production scale. The most common brewery chiller types include:
- Air-Cooled Chillers: These chillers use ambient air to dissipate heat and are ideal for breweries with limited space or limited water availability. Air-cooled chillers are generally more compact and easier to install but may be less efficient in hot climates or environments with poor airflow.
- Water-Cooled Chiller: Water-cooled chiller uses water as the coolant and is highly efficient. It is suitable for large breweries with high cooling requirements. It requires a reliable source of water for cooling, such as a water supply line or cooling tower. While a water-cooled chiller may have higher upfront costs and installation complexity, it provides superior efficiency and performance in the long run.
- Glycol Coolers: Glycol coolers utilize a mixture of water and food-grade ethylene glycol as a coolant that is circulated through insulated pipes to indirectly cool fermentation vessels and other equipment. This method is typically used in breweries or multi-stage brewing facilities where the fermentation tanks are located far from the main cooling unit. Glycol coolers provide flexible temperature control and prevent temperature stratification within the fermentator.
- Modular Chillers: Modular chillers are made up of multiple independent units that can be combined to provide scalable cooling capacity. It provides flexibility and redundancy, allowing breweries to expand their cooling infrastructure as needed without investing in a single large chiller.
Each type of brewery chiller has its benefits and considerations, and choosing the right chiller depends on factors such as throughput, space constraints, energy efficiency goals, and budget considerations. By understanding the functions of a brewery chiller, its critical role in brewing, and the various types available, breweries can make informed decisions when selecting the appropriate chiller system for their specific needs and production requirements.
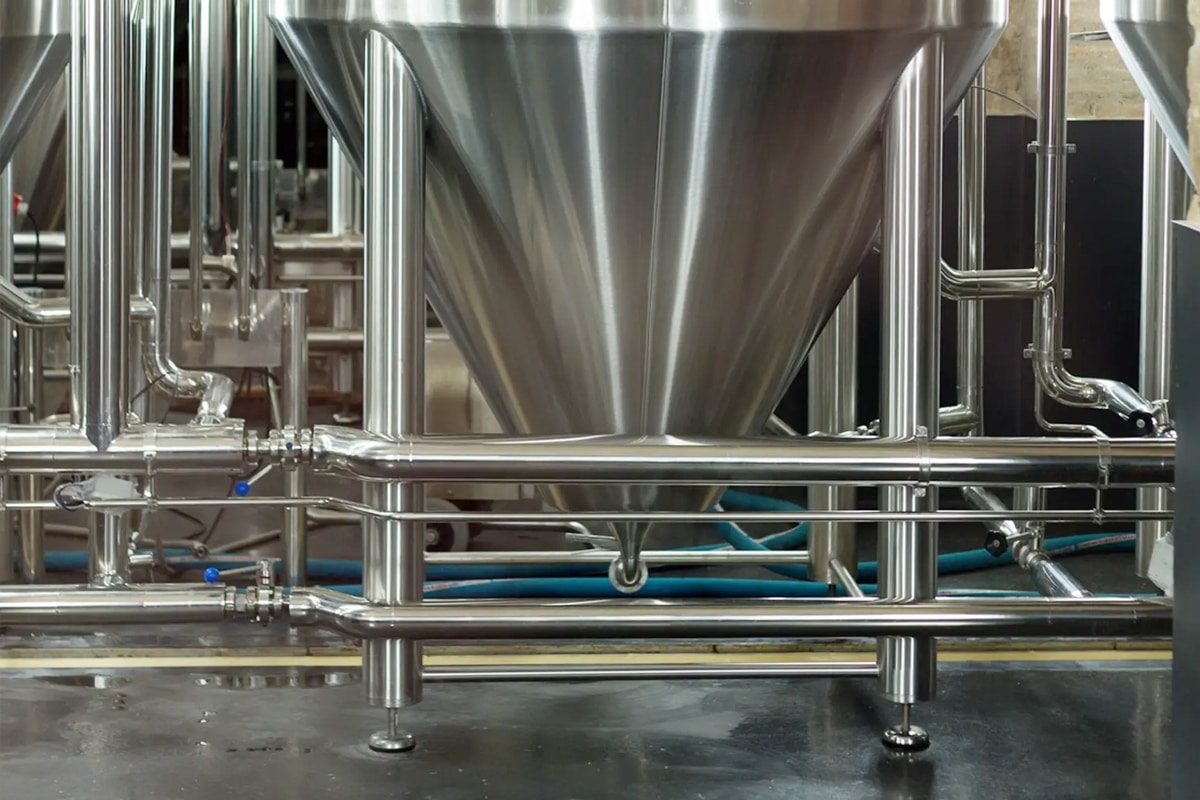
Factors Affecting The Selection of Chiller
Choosing the right size for your brewery chiller is a critical step in ensuring optimal performance and efficiency in your brewing process. Several key factors must be considered to accurately size a cooler to meet the specific needs of a brewery. Let’s explore these factors in detail:
Batch Size
The amount of beer produced per batch is the primary determining factor in cooler size. Larger batches require more cooling capacity to maintain consistent temperatures throughout the brewing process. Brewers must consider their typical batch sizes as well as any changes or fluctuations in output. Whether brewing small batches or large-scale production, matching cooler capacity to batch size helps achieve consistent brewing results.
Cooling Requirements
Different stages of the brewing process have different cooling requirements, so the specific cooling needs of each stage need to be carefully considered. For example, wort cooling typically requires a higher cooling capacity than fermentation or refrigeration. Brewers must evaluate the temperature differential required at each stage and select a chiller that can effectively meet these cooling needs. Understanding the intricacies of the brewing process allows breweries to tailor cooler sizes to meet the specific cooling requirements of their operations.
Environmental Conditions
Ambient temperature and humidity levels in a brewery environment significantly affect chiller performance. Higher ambient temperatures will increase the heat load on the chiller, requiring greater cooling capacity to effectively compensate. Likewise, humidity levels can affect the efficiency of evaporative cooling systems and the condensation rate of air-cooled chillers. Breweries operating in areas with extreme temperatures or seasonal changes must consider these environmental conditions when sizing their chillers to ensure reliable performance year-round.
Insulation And Heat Gain
The quality of the brewery’s insulation and any potential sources of heat gain will affect the chiller workload. A well-insulated brewery with minimal heat gain will need a smaller chiller to maintain the desired temperature, while a poorly insulated facility or a brewery with a lot of heat-generating equipment may need a larger chiller to offset the heat load. Evaluating the insulation performance of your brew space and implementing strategies to minimize heat gain, such as installing reflective roofing materials or insulating brew vessels, can help optimize chiller size and energy efficiency.
Future Expansion
When sizing your brewery chiller to accommodate potential growth and changing production needs, it is critical to consider future expansion plans. Choosing a chiller with a slightly higher capacity than your current requirements can provide room for expansion without the need for an immediate upgrade. Additionally, modular cooling systems or scalable solutions provide flexibility and scalability, allowing breweries to seamlessly adapt their cooling infrastructure to changing needs. By anticipating future growth and scalability requirements, brewers can make informed decisions when selecting the right chiller size for their operation.
By carefully evaluating these factors and taking into account the unique requirements of beer production, brewers can accurately size their coolers to achieve optimal performance, efficiency, and consistency in their beer production processes.
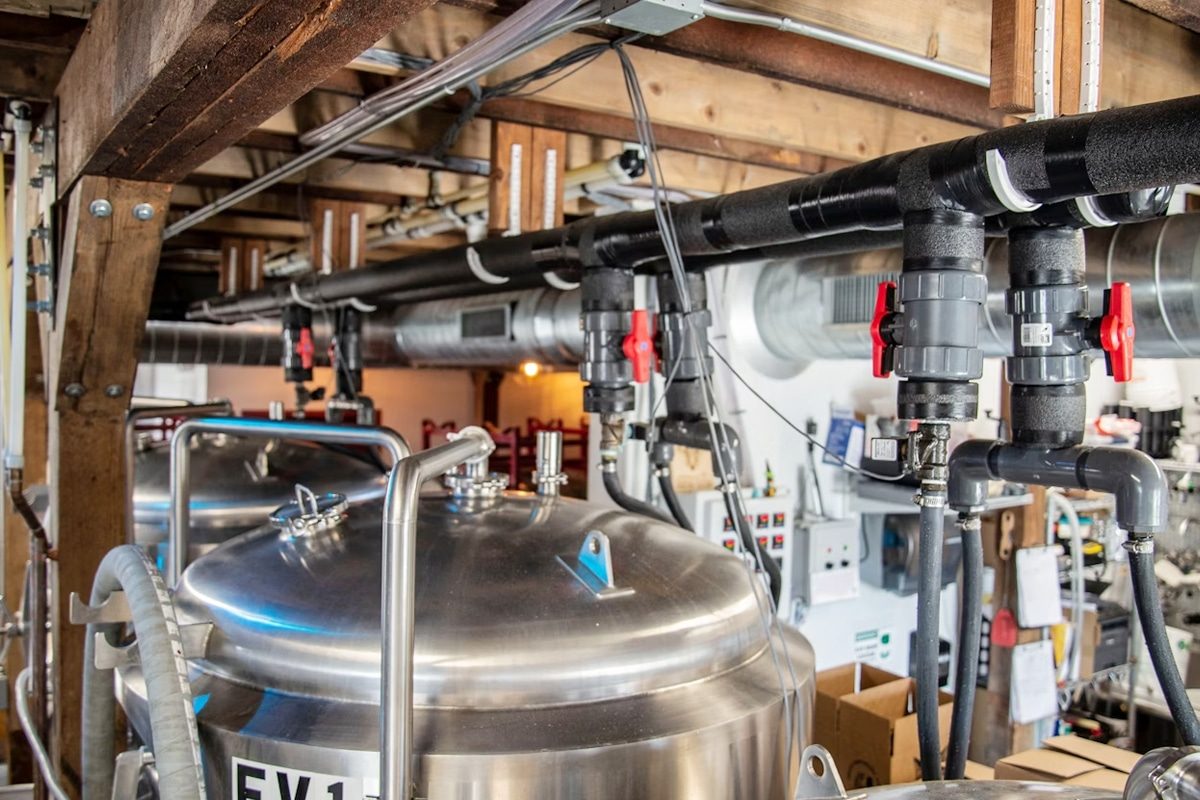
Calculating Chiller Size
Sizing a brewery chiller requires careful calculation and consideration of various factors to ensure it meets the specific cooling demands of the brewing process. Let’s explore the step-by-step process involved in determining the appropriate chiller size:
Determining Cooling Load
The first step in sizing a brewery chiller is to determine the total cooling load required for the brewing process. This involves estimating the amount of heat that must be removed to achieve and maintain desired temperatures at each stage, including wort chilling, fermentation, and cold storage. Factors such as batch size, cooling requirements, ambient conditions, insulation quality, and heat gain must be taken into account when calculating the cooling load.
Calculating Heat Transfer
Once the cooling load is determined, the next step is to calculate the heat transfer rate (Q) required to remove this heat. The formula for calculating heat transfer is:
Q = mcΔT
Where:
- Q represents the heat transfer rate (in BTU/hr or kW)
- m is the mass flow rate of the cooling medium (in gallons per minute or liters per minute)
- c is the specific heat capacity of the cooling medium (in BTU/lb°F or kJ/kg°C)
- ΔT is the temperature difference (in °F or °C) between the cooling medium and the desired temperature
Selecting Chiller Capacity
With the heat transfer rate determined, brewers can then select a chiller with a capacity that exceeds this calculated value to ensure sufficient cooling power. It’s essential to consider factors such as the chiller’s cooling capacity, efficiency, operating conditions, and compatibility with the brewery’s infrastructure and production requirements. Consulting with chiller manufacturers or HVAC professionals can provide valuable insights into selecting the most suitable chiller model based on the calculated cooling load.
Considering Redundancy
In addition to selecting the appropriate chiller capacity, it’s advisable to consider redundancy in the chiller system to minimize downtime in case of equipment failure. Incorporating backup chillers or implementing a modular chiller system allows for continued operation and ensures uninterrupted cooling capabilities, even in the event of a chiller malfunction. Redundancy measures provide added reliability and peace of mind, particularly in critical production environments where downtime can have significant financial implications.
By following these steps and considering factors such as cooling load, heat transfer, chiller capacity, and redundancy, brewers can accurately size their brewery chillers to meet the specific requirements of their brewing operations. Investing time and effort into proper chiller sizing ensures optimal performance, efficiency, and reliability in the beer production process, ultimately contributing to the success and quality of the brewery’s offerings.
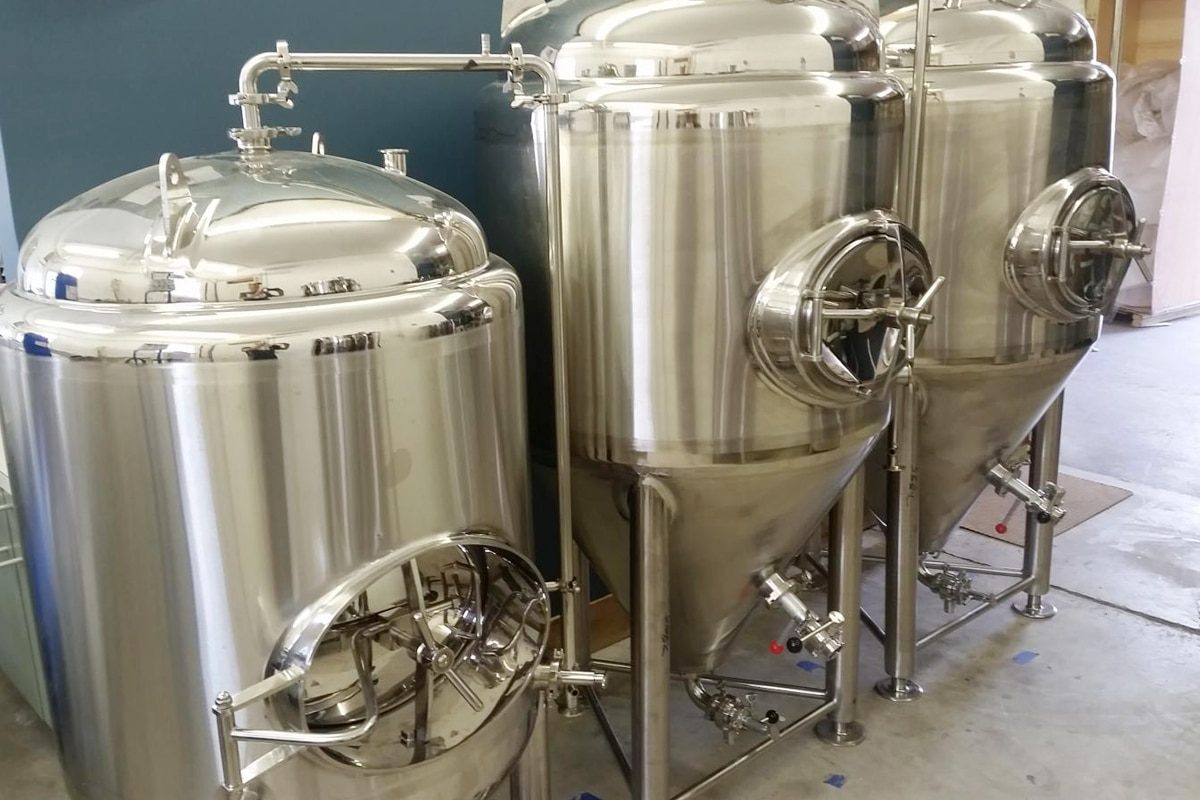
Advanced Sizing Considerations
While the basic principles of sizing a brewery chiller focus on meeting the immediate cooling requirements of the brewing process, advanced considerations delve deeper into optimizing performance, energy efficiency, and sustainability. Next, we explore several advanced factors that brewers should consider when sizing a brewery chiller.
Dynamic Load Profiles
Brewing operations often experience dynamic load profiles, with cooling requirements varying throughout the production cycle. Advanced chiller sizing takes into account these fluctuations in demand, ensuring that the chiller can adapt to changing conditions efficiently. By analyzing historical data and forecasting future cooling needs, brewers can optimize chiller sizing to match dynamic load profiles, maximizing energy efficiency and reducing operating costs.
Energy Efficiency
Energy efficiency is paramount in modern brewing operations, not only to reduce operational costs but also to minimize environmental impact. When sizing a brewery chiller, selecting energy-efficient models with advanced features such as variable speed compressors, thermal storage systems, and heat recovery technologies can significantly reduce energy consumption. By prioritizing energy efficiency during chiller selection, brewers can lower utility bills and decrease their carbon footprint without compromising performance.
Environmental Impact
Breweries are increasingly mindful of their environmental impact and strive to minimize resource consumption and emissions. When sizing a brewery chiller, considering the environmental impact of refrigerants and chiller operation is essential. Opting for chillers with low global warming potential (GWP) refrigerants or natural refrigerants such as ammonia or CO2 can reduce greenhouse gas emissions and align with sustainability goals. Additionally, implementing energy-saving practices such as waste heat recovery and water conservation measures further reduces environmental impact and enhances the brewery’s sustainability credentials.
Maintenance Requirements
Proper maintenance helps ensure the long-term performance and reliability of your brewery chiller. Advanced chiller sizing takes into account the maintenance requirements of different chiller models, including routine servicing, component lifespan, and availability of spare parts. Choosing chillers with low maintenance needs, durable components, and easy accessibility for service technicians can minimize downtime and prolong equipment lifespan, optimizing the return on investment.
Remote Monitoring and Control
Incorporating remote monitoring and control capabilities into the chiller system allows brewers to monitor performance, adjust settings, and diagnose issues remotely. Advanced chiller systems equipped with cloud-based monitoring platforms, real-time alerts, and predictive maintenance features provide brewers with greater visibility and control over their cooling infrastructure. By accessing real-time data and insights, brewers can proactively manage chiller operations, optimize energy usage, and prevent potential downtime, ultimately improving overall brewery productivity and profitability.
Incorporating these advanced sizing considerations into the chiller selection process enables brewers to not only meet their immediate cooling needs but also achieve long-term efficiency, sustainability, and operational excellence. By embracing innovative technologies and best practices, breweries can elevate their chiller systems to new heights, paving the way for a more sustainable and prosperous future.
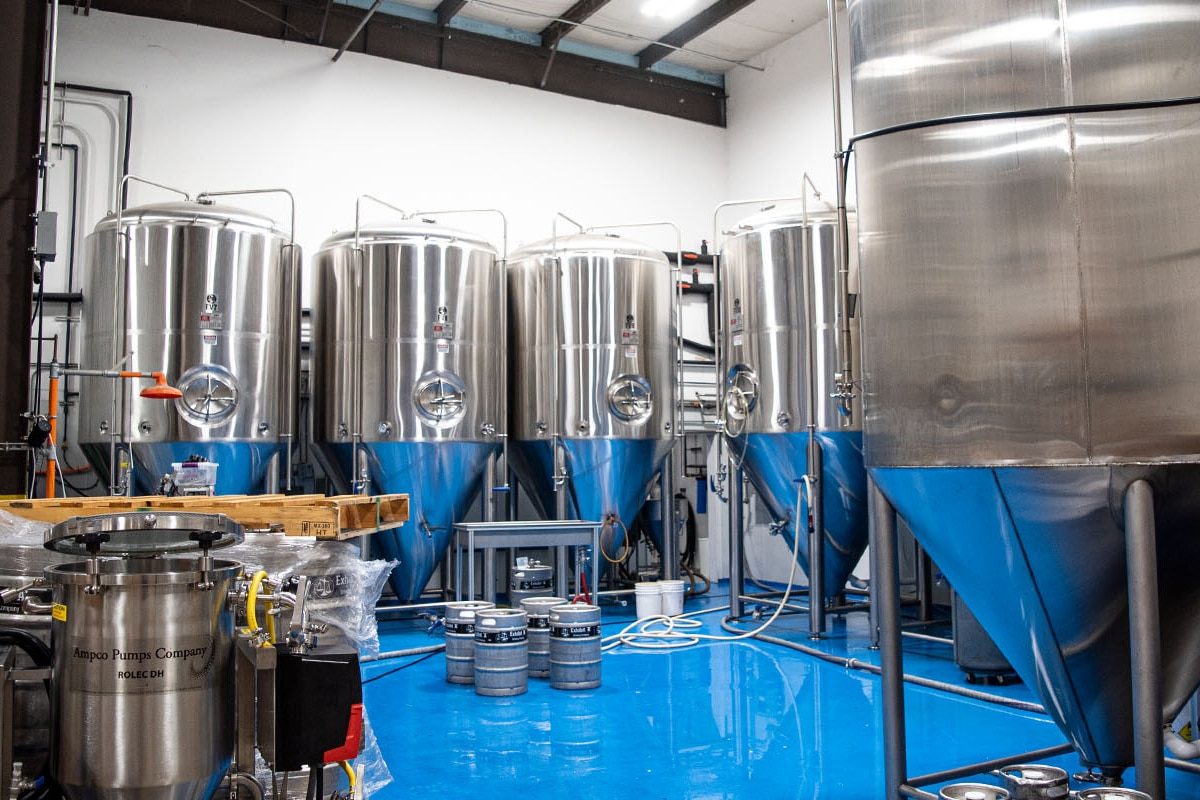
Summarize
Sizing a brewery chiller is a multifaceted process that requires careful consideration of various factors to ensure optimal performance, efficiency, and reliability in the brewing process. From assessing cooling requirements and environmental conditions to incorporating advanced sizing considerations, brewers must navigate a complex landscape to select the right chiller for their operations.
By understanding factors such as batch size, cooling requirements, ambient conditions, insulation, and future expansion plans, brewers can accurately determine the cooling load and select an appropriately sized chiller. Moreover, advanced considerations such as dynamic load profiles, energy efficiency, environmental impact, maintenance requirements, and remote monitoring and control further refine the chiller sizing process, enabling brewers to optimize performance and sustainability.
Ultimately, investing time and effort into proper chiller sizing pays dividends in the form of consistent beer quality, reduced operating costs, and enhanced environmental stewardship, positioning breweries for long-term success in an increasingly competitive market.
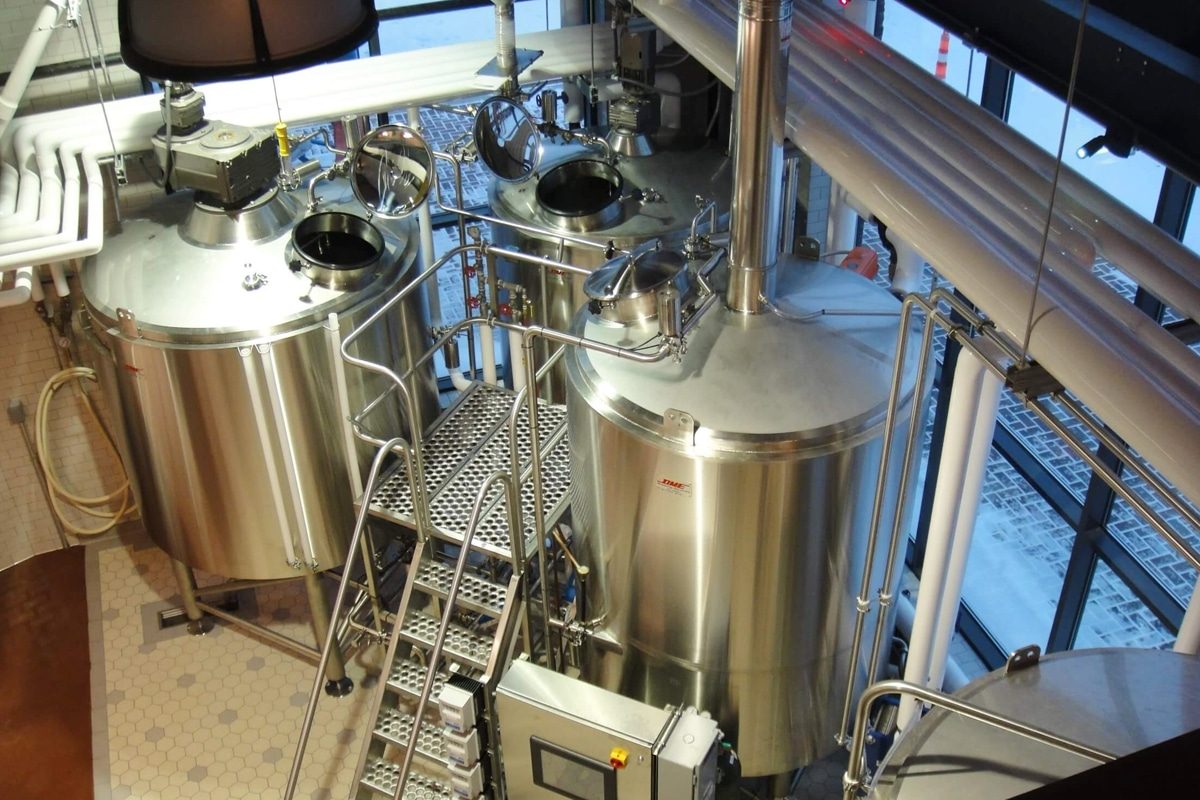
Get A Turnkey Brewery Solutions
At ZYB Craft, we understand the intricacies of brewery operations and the critical role that chiller systems play in ensuring the success of your brewing endeavors. As a professional brewery solution provider, we offer comprehensive turnkey solutions tailored to meet the specific needs of your brewery.
Our team of experts specializes in sizing brewery chillers to optimize performance, efficiency, and reliability. By leveraging our industry knowledge and technical expertise, we guide you through the chiller selection process, taking into account factors such as batch size, cooling requirements, ambient conditions, and future expansion plans.
With ZYB Craft’s turnkey brewery solutions, you gain access to top-of-the-line chiller systems equipped with advanced features such as energy-saving technologies, remote monitoring capabilities, and environmentally friendly refrigerants. From initial consultation to installation and ongoing support, we are committed to helping you achieve your brewing goals with confidence and peace of mind. Trust ZYB Craft for all your brewery chiller needs and unlock the full potential of your brewing operation.