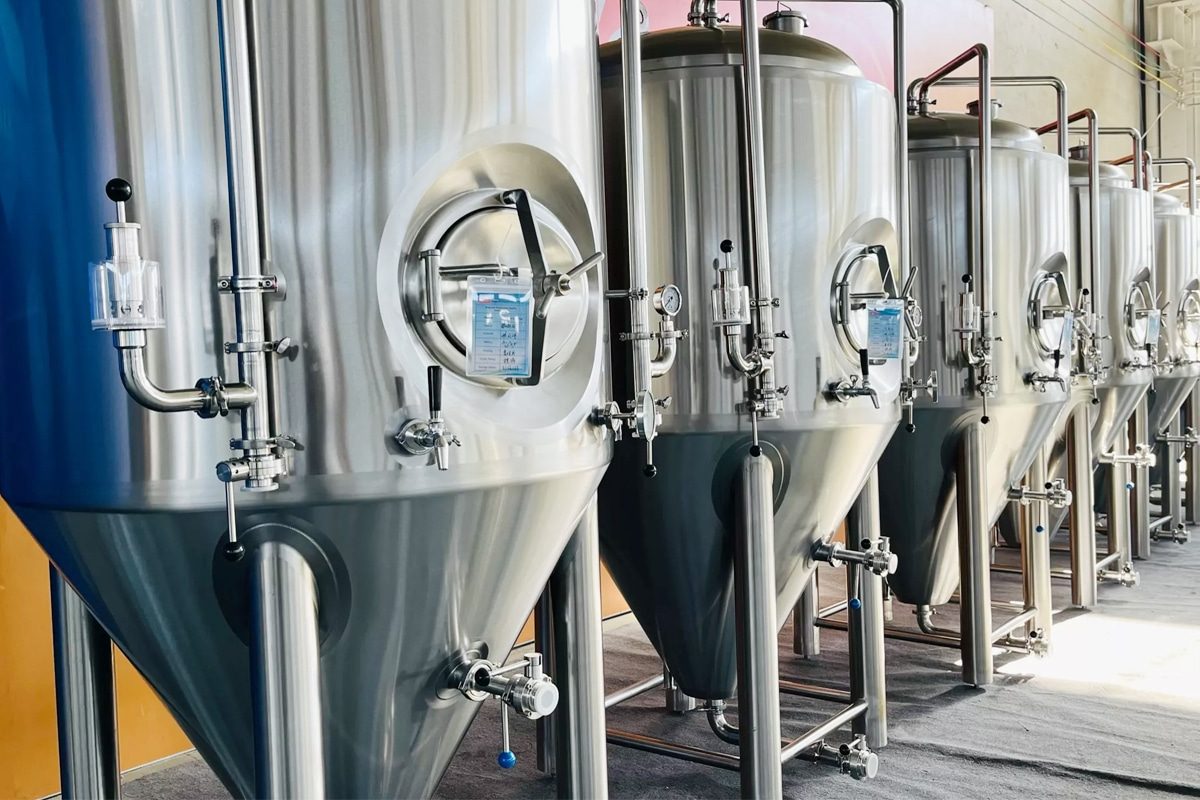
How To Prevent Corrosion in Fermentation Tanks?
Corrosion in fermentation tanks is a pervasive issue that can significantly impact the brewing and fermentation industries. The presence of corrosion not only compromises the structural integrity and longevity of the tanks but also poses a threat to the quality and safety of the products being fermented. This makes the prevention of corrosion a critical aspect of maintaining optimal operations. Understanding the various factors that contribute to corrosion, such as material composition, environmental conditions, microbial activity, and cleaning methods, can help develop effective prevention strategies. By employing appropriate material selection, design considerations, environmental controls, and advanced prevention techniques, industries can safeguard their fermentation processes. This article delves into the comprehensive methods for preventing corrosion in fermentation tanks, offering insights into best practices and innovative solutions to ensure the durability and efficiency of these vital pieces of equipment.
Complete Guide
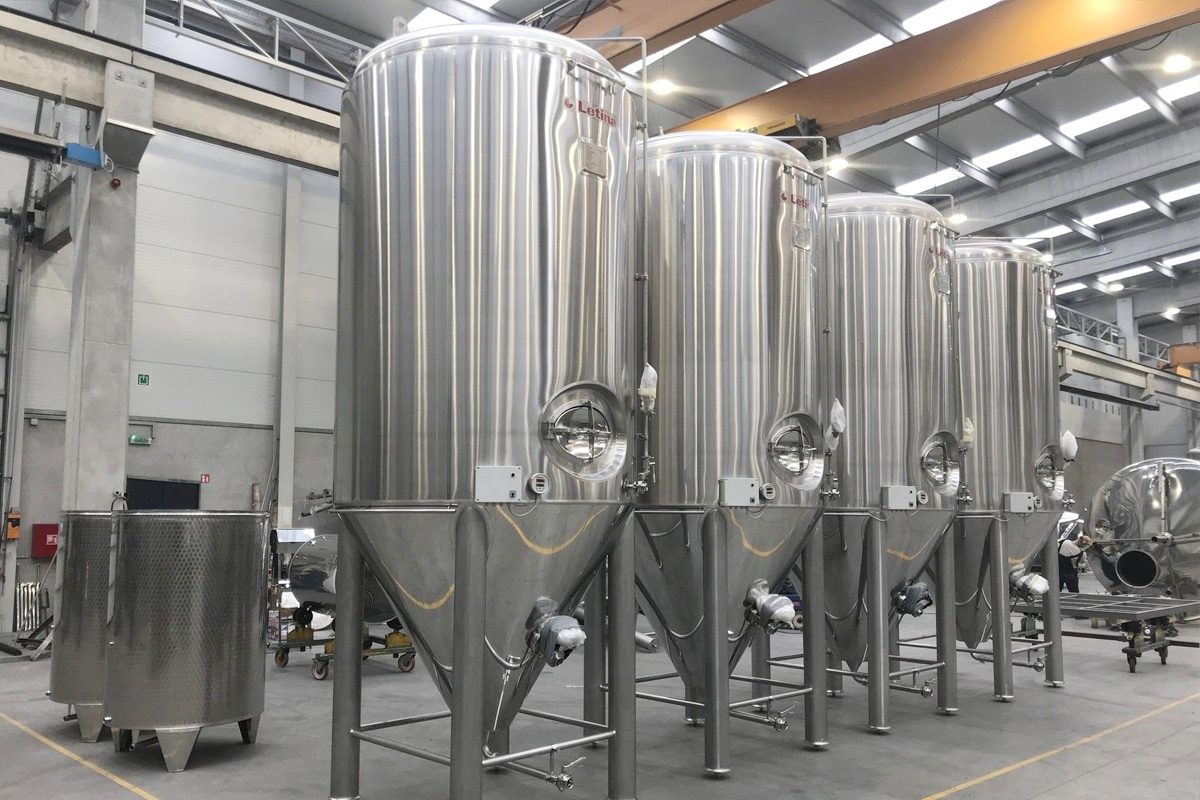
Understanding Corrosion
Corrosion is a natural process where metals deteriorate due to chemical reactions with their environment. In fermentation tanks, understanding the specific factors that cause corrosion can help develop effective prevention strategies. These factors include moisture, acidic environments, microbial activity, and chemical exposure. Each plays a unique role in the corrosion process and must be addressed to maintain the integrity of fermentation tanks.
Moisture
Moisture is one of the primary contributors to corrosion. Fermentation tanks are often exposed to high humidity levels and liquid contents, creating an environment conducive to corrosion. When metal surfaces are in constant contact with moisture, it can lead to the formation of rust, especially in tanks made of iron or steel. Even stainless steel, which is more resistant to corrosion, can suffer from pitting and crevice corrosion if moisture accumulates in small crevices or under deposits.
To mitigate moisture-induced corrosion, it is essential to ensure proper drainage and ventilation within and around the tanks. Regular inspections should be conducted to identify and eliminate areas where moisture can accumulate. Additionally, using desiccants or dehumidifiers in the storage and operational areas can help control humidity levels and reduce the risk of corrosion.
Acidic Environments
Fermentation processes often produce acidic byproducts, which can significantly accelerate the corrosion of metal surfaces. Acids react with metals, breaking down their protective oxide layers and exposing the raw metal to further corrosion. Stainless steel fermentation tanks are particularly susceptible to corrosion in acidic environments if the passive oxide layer is damaged or compromised.
To prevent corrosion in acidic environments, it is crucial to monitor and control the pH levels of the fermentation medium. Using corrosion-resistant materials, such as high-grade stainless steel (e.g., 316 stainless steel), can provide better protection against acidic conditions. Additionally, regular passivation treatments can help maintain the protective oxide layer on stainless steel surfaces, enhancing their corrosion resistance.
Microbial Activity
Microbial activity is another significant factor contributing to corrosion in fermentation tanks. Certain bacteria, known as sulfate-reducing bacteria (SRB), can produce hydrogen sulfide, which is highly corrosive to metals. These microbes thrive in anaerobic conditions, often found in the crevices and under deposits in fermentation tanks. The byproducts of microbial metabolism can create highly localized acidic environments, leading to pitting and crevice corrosion.
To control microbial-induced corrosion, it is essential to maintain stringent hygiene and sanitation practices. Regular cleaning and sanitization of the tanks can help prevent the buildup of microbial biofilms. Using biocides or other antimicrobial agents in the cleaning process can further reduce the risk of microbial activity. Additionally, monitoring the microbial load in the fermentation tanks and implementing strategies to control it can help mitigate corrosion caused by microbial activity.
Chemical Exposure
Chemical exposure, particularly to harsh cleaning agents and sanitizers, can significantly contribute to corrosion in fermentation tanks. Many cleaning agents used in the brewing and fermentation industries contain strong acids, alkalis, or oxidizing agents that can damage the protective oxide layer on metal surfaces. Repeated exposure to these chemicals can lead to the deterioration of the metal and increased susceptibility to corrosion.
To prevent chemical-induced corrosion, it is important to choose cleaning agents that are compatible with the materials used in the fermentation tanks. Opting for less aggressive cleaning solutions or those specifically designed for use with stainless steel can help minimize corrosion risk. Additionally, thorough rinsing of the tanks after cleaning to remove any residual chemicals can prevent prolonged exposure and potential damage.
Understanding the various factors that contribute to fermentation tank corrosion (moisture, acidic environment, microbial activity, and chemical exposure) can help develop effective prevention strategies. By addressing each of these factors through proper material selection, design considerations, environmental control, and maintenance practices, it is possible to significantly reduce the risk of corrosion and ensure the longevity and efficiency of fermentation tanks.
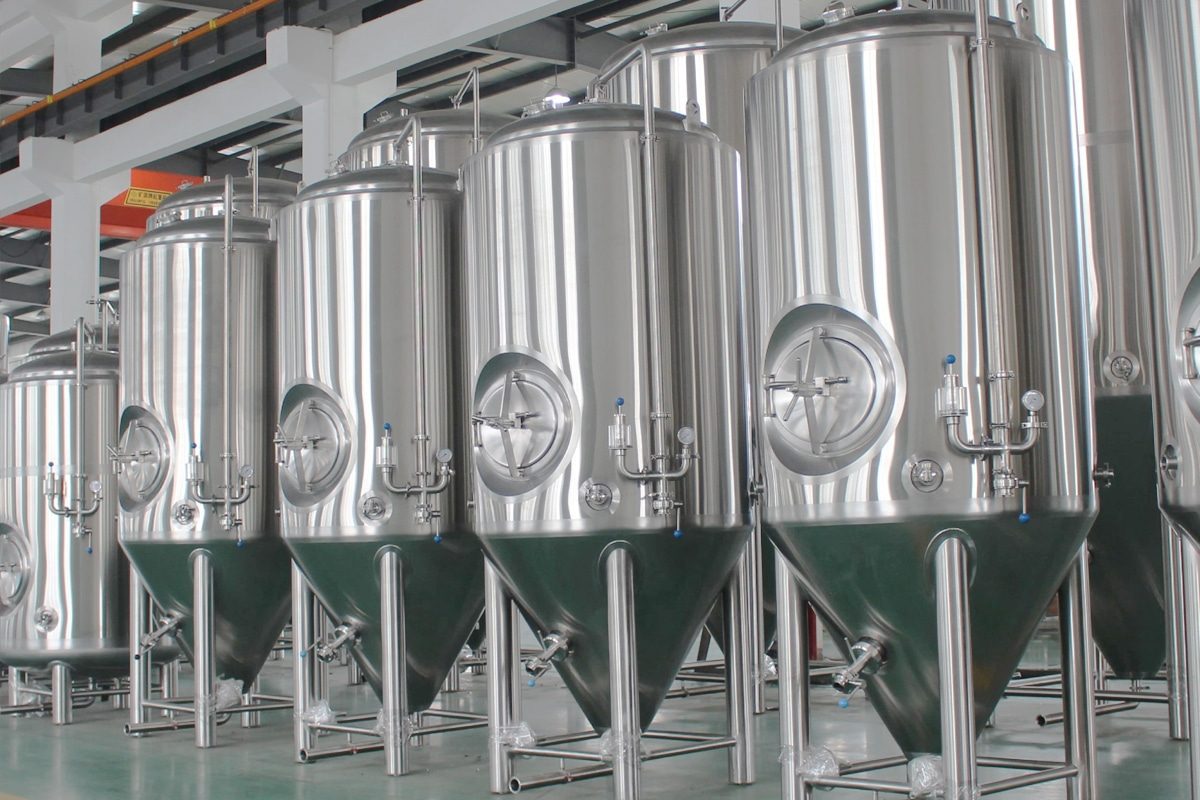
Types of Corrosion in Fermentation Tanks
Understanding the various types of corrosion that can affect fermentation tanks can help you prevent and maintain them effectively. Each type of corrosion poses unique challenges and requires specific strategies to mitigate. Here, we explore the five main types of corrosion commonly encountered in fermentation tanks: uniform corrosion, pitting corrosion, crevice corrosion, galvanic corrosion, and microbial-induced corrosion (MIC).
Uniform Corrosion
Uniform corrosion is the most straightforward form of corrosion, where the metal surface deteriorates evenly across its entire area. This type of corrosion occurs when the protective oxide layer on the metal surface is uniformly broken down, leading to a consistent and gradual loss of material.
Features
- Even thinning of the metal surface.
- Predictable and often easier to detect and measure.
- Typically occurs in environments where the metal is exposed to corrosive substances uniformly.
Prevention
- Use corrosion-resistant materials, such as high-grade stainless steel (e.g., 304 or 316).
- Apply protective coatings, like epoxy or polyurethane, to provide an additional barrier.
- Regular maintenance and inspection to monitor and address early signs of corrosion.
Pitting Corrosion
Pitting corrosion is a highly localized form of corrosion that results in small, deep pits or holes on the metal surface. It is one of the most dangerous types because it can penetrate deeply into the metal, leading to significant structural damage while remaining relatively undetectable until advanced stages.
Features
- Small, often hard-to-detect pits or holes.
- Can lead to severe damage with minimal material loss.
- Typically occurs in environments with chloride ions or other aggressive anions.
Prevention
- Use high-alloy stainless steel with enhanced resistance to pitting.
- Maintain clean surfaces to prevent the buildup of corrosive agents.
- Apply regular passivation treatments to reinforce the protective oxide layer on stainless steel.
Crevice Corrosion
Crevice corrosion occurs in confined spaces where the exposure to the environment is restricted, such as under gaskets, washers, or weld joints. This type of corrosion is driven by differences in oxygen concentration between the crevice and the surrounding environment, leading to an aggressive localized attack.
Features
- Localized to confined spaces.
- Can be challenging to detect due to its hidden nature.
- Often associated with areas where stagnant solutions can accumulate.
Prevention
- Design tanks with minimal crevices and ensure smooth welds and joints.
- Use non-absorbent gaskets and sealants to reduce crevice formation.
- Implement regular cleaning and inspection routines to detect and address early signs of crevice corrosion.
Galvanic Corrosion
Galvanic corrosion occurs when two dissimilar metals are electrically connected in the presence of an electrolyte, such as water or moisture. The more anodic metal corrodes faster than it would alone, while the more cathodic metal corrodes slower.
Features
- Occurs at the junction of two different metals.
- The less noble (anodic) metal corrodes preferentially.
- Common in systems where different metals are used nearby.
Prevention
- Avoid using dissimilar metals in close contact whenever possible.
- Use insulating materials or coatings to separate dissimilar metals.
- Apply sacrificial anodes to protect critical components from galvanic corrosion.
Microbial Induced Corrosion (MIC)
Microbial-induced corrosion (MIC) is caused by the presence of microorganisms, such as bacteria, fungi, or algae, which produce corrosive byproducts. Sulfate-reducing bacteria (SRB) are a common culprit, producing hydrogen sulfide, which is highly corrosive to metals.
Features
- Often occurs in localized areas where microbial colonies develop.
- Can produce pitting, crevice corrosion, and even uniform corrosion.
- Associated with environments rich in organic matter or stagnant water.
Prevention
- Maintain stringent hygiene and sanitation practices to prevent microbial growth.
- Use biocides or antimicrobial agents in cleaning processes.
- Monitor microbial activity regularly and implement control measures as needed.
Each type of corrosion presents unique challenges that require specific preventive measures. By understanding uniform corrosion, pitting corrosion, crevice corrosion, galvanic corrosion, and microbial-induced corrosion, industries can better protect their fermentation tanks from deterioration. Implementing comprehensive prevention strategies, including proper material selection, design considerations, and maintenance practices, is key to ensuring the longevity and efficiency of fermentation tanks.
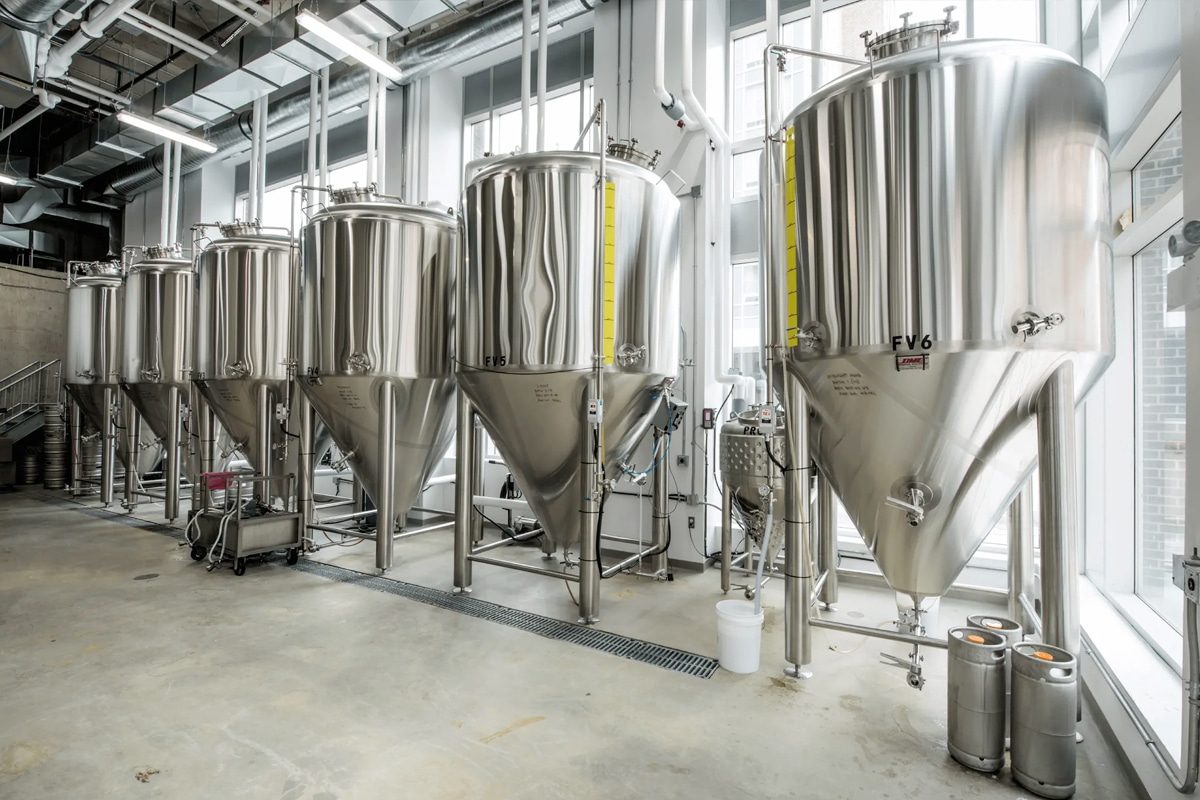
Factors Contributing to Corrosion
Corrosion in fermentation tanks is influenced by several key factors, each playing a significant role in the degradation of metal surfaces. Understanding these factors (material composition, environmental conditions, and microbial activity) can help determine the root causes of corrosion and develop effective prevention strategies.
Material Composition
The type of material used in the construction of fermentation tanks greatly affects their susceptibility to corrosion. Different materials respond differently to corrosive environments based on their chemical and physical properties.
- Stainless Steel: While commonly used for its corrosion-resistant properties, even stainless steel can be vulnerable under certain conditions. Stainless steels, such as grades 304 and 316, rely on a thin oxide layer for protection. If this layer is damaged or compromised, the underlying metal can corrode. The presence of chloride ions, often found in cleaning agents and the brewing environment, can particularly affect stainless steel, leading to pitting and crevice corrosion.
- Alloying Elements: The composition of the alloy can determine its corrosion resistance. Metals with high chromium content, like certain stainless steels, form a protective oxide layer that guards against corrosion. However, the presence of other elements such as sulfur, phosphorus, or carbon can introduce vulnerabilities, especially at grain boundaries or in welded areas.
Environmental Conditions
The environmental conditions within and surrounding the fermentation tanks can significantly influence the rate and severity of corrosion. Several environmental factors can help us understand the corrosion process:
- Moisture and Humidity: High humidity levels and the presence of moisture are primary drivers of corrosion. Fermentation tanks often operate in environments where condensation and liquid exposure are common. Moisture can facilitate the electrochemical reactions that cause corrosion, particularly when combined with other corrosive agents. This is especially problematic in areas where water can become trapped, such as under gaskets or in weld seams.
- Acidic Environments: The fermentation process can produce acidic byproducts, leading to a decrease in pH levels. Low pH environments are highly corrosive, especially to metals like stainless steel. Acids can dissolve the protective oxide layer on metals, exposing them to further corrosion. Frequent exposure to acidic substances, including organic acids produced during fermentation, accelerates the corrosion process.
- Temperature Fluctuations: Temperature variations can exacerbate corrosion. High temperatures generally increase the rate of chemical reactions, leading to faster corrosion. Moreover, repeated cycles of heating and cooling can cause expansion and contraction in the metal, leading to stress corrosion cracking or the formation of microcracks that facilitate further corrosion.
Microbial Activity
Microbial activity is a significant factor in corrosion, particularly in environments rich in organic material, such as fermentation tanks. Certain microorganisms can directly or indirectly contribute to the corrosion process.
- Sulfate-Reducing Bacteria (SRB): SRB are anaerobic bacteria that produce hydrogen sulfide as a byproduct of their metabolism. Hydrogen sulfide is highly corrosive to metals, particularly in anaerobic environments where oxygen is limited. These bacteria can thrive in the crevices and under deposits within fermentation tanks, leading to localized and often severe corrosion.
- Biofilm Formation: Microorganisms can form biofilms on the surfaces of fermentation tanks. Biofilms are complex communities of microorganisms that adhere to surfaces and produce extracellular polymeric substances (EPS). These biofilms can create microenvironments that are highly corrosive, trapping moisture and corrosive agents close to the metal surface and facilitating localized corrosion.
- Organic Acids: Certain bacteria and fungi produce organic acids during their metabolic processes. These acids can lower the pH of the environment, increasing the corrosive potential. Even small concentrations of these acids can lead to significant corrosion over time, particularly if they accumulate in crevices or other confined spaces.
Corrosion in fermentation tanks is driven by a combination of material composition, environmental conditions, and microbial activity. Each factor plays a distinct role in the corrosion process, contributing to the overall degradation of the metal surfaces. Understanding these factors can help determine the causes of corrosion and develop targeted strategies to mitigate its effects.
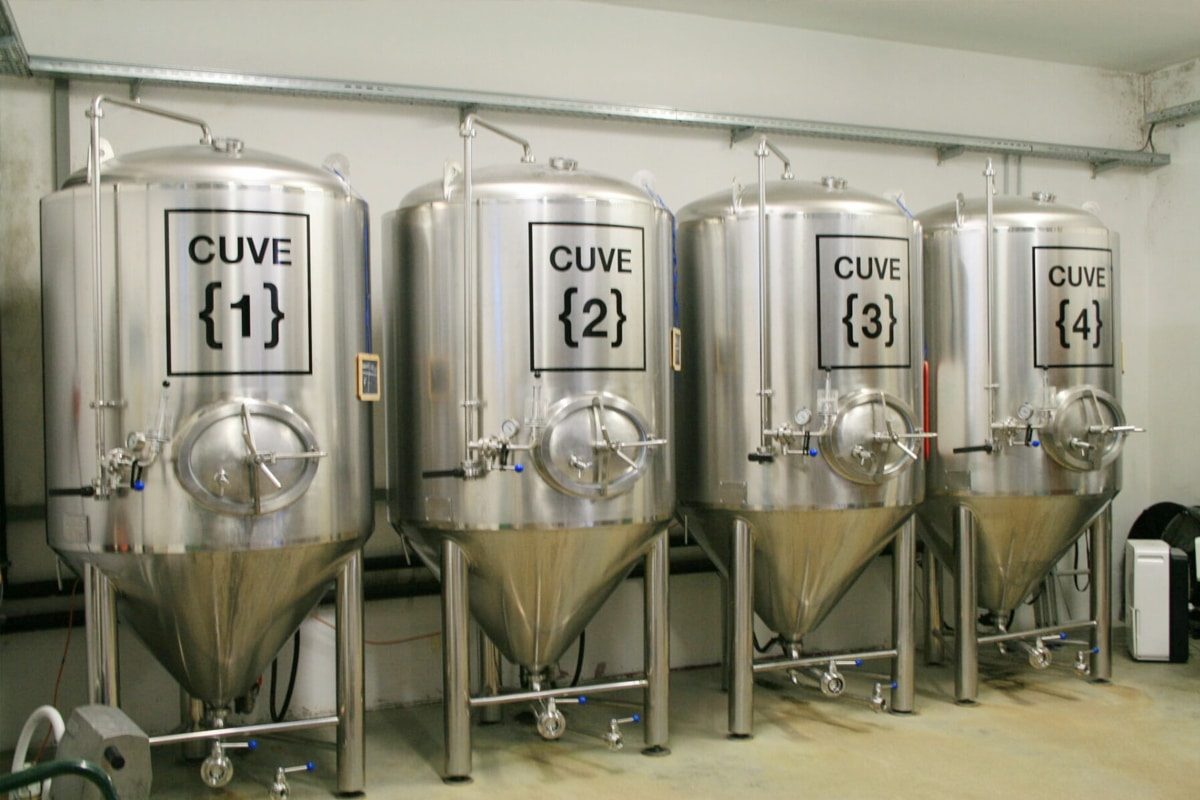
Types of Brewing Yeasts
Preventing corrosion in fermentation tanks requires a multifaceted approach that encompasses material selection, design and construction, protective measures, maintenance, environmental control, chemical treatment, monitoring, and training. Implementing these best practices can significantly enhance the longevity and performance of fermentation tanks, ensuring the quality and safety of the products being processed.
Material Selection
- Stainless Steel: Choose high-grade stainless steel such as 304 or 316 for fermentation tanks. 316 stainless steel contains molybdenum, which provides superior resistance to chloride-induced corrosion, making it ideal for environments exposed to salts and acids.
- Alloys and Composites: Consider using advanced alloys or composite materials that offer enhanced corrosion resistance. These materials can provide additional protection in highly aggressive environments.
- Compatibility: Ensure that all materials used in the construction and components of the tank are compatible to prevent galvanic corrosion. This includes fittings, pipes, and valves.
Proper Design and Construction
- Smooth Surfaces: Design tanks with smooth, rounded surfaces to minimize areas where corrosive agents can accumulate. Avoid sharp edges and corners.
- Weld Quality: Ensure high-quality welds that are smooth and free of defects. Poor welds can create crevices that are prone to corrosion.
- Drainage and Ventilation: Incorporate proper drainage and ventilation systems to prevent the accumulation of moisture and corrosive agents.
Protective Coatings and Linings
- Epoxy Coatings: Apply epoxy coatings to the interior and exterior surfaces of the tanks to provide a barrier against corrosive substances.
- Polyurethane Linings: Use polyurethane linings to protect the tank surfaces from chemical and microbial-induced corrosion.
- Periodic Reapplication: Regularly inspect and reapply protective coatings and linings as needed to maintain their effectiveness.
Regular Cleaning and Maintenance
- Appropriate Cleaning Agents: Use cleaning agents that are specifically designed for stainless steel and that do not contain harsh chemicals that can damage the protective oxide layer.
- Sanitization: Implement regular sanitization protocols to prevent microbial growth and biofilm formation. This can help mitigate microbial-induced corrosion.
- Scheduled Maintenance: Develop and adhere to a maintenance schedule that includes thorough cleaning, inspection, and repairs as needed.
Controlling Environmental Conditions
- Humidity Control: Use dehumidifiers or desiccants to control humidity levels in storage and operational areas. This helps reduce the risk of moisture-induced corrosion.
- Temperature Stability: Maintain stable temperature conditions to prevent thermal expansion and contraction, which can lead to stress corrosion cracking.
- Ventilation: Ensure proper ventilation to avoid the buildup of corrosive gases and vapors.
Chemical Treatment
- Corrosion Inhibitors: Add corrosion inhibitors to the fermenting medium or cleaning solutions to reduce the rate of corrosion. These chemicals work by forming a protective film on the metal surface or neutralizing corrosive agents.
- Passivation: Periodically passivate stainless steel surfaces using nitric or citric acid to restore the protective oxide layer. This enhances the metal’s resistance to corrosion.
- pH Control: Monitor and adjust the pH levels of the fermenting medium to avoid highly acidic or alkaline conditions that can accelerate corrosion.
Monitoring and Inspection
- Regular Inspections: Conduct regular inspections of the tanks to identify early signs of corrosion. Use tools like ultrasonic thickness gauges and borescopes to assess hard-to-reach areas.
- Corrosion Monitoring Systems: Install corrosion monitoring systems that provide real-time data on the condition of the tank surfaces. These systems can help detect changes in corrosion rates and identify potential issues early.
- Data Analysis: Analyze inspection and monitoring data to identify trends and adjust preventive measures accordingly.
Training and Awareness
- Staff Training: Train staff on the importance of corrosion prevention and the best practices for maintaining fermentation tanks. This includes proper cleaning techniques, material handling, and recognizing signs of corrosion.
- Standard Operating Procedures (SOPs): Develop and implement SOPs for all processes related to the maintenance and operation of fermentation tanks. Ensure that these procedures are regularly updated and followed by all personnel.
- Awareness Programs: Conduct regular awareness programs and workshops to keep staff informed about the latest developments in corrosion prevention and best practices.
Preventing corrosion in fermentation tanks is a comprehensive process that involves careful material selection, thoughtful design, and construction, protective coatings, regular cleaning and maintenance, control of environmental conditions, chemical treatment, diligent monitoring and inspection, and thorough training and awareness. By implementing these best practices, breweries and fermentation facilities can protect their investments, maintain product quality, and ensure the longevity and efficiency of their fermentation tanks.
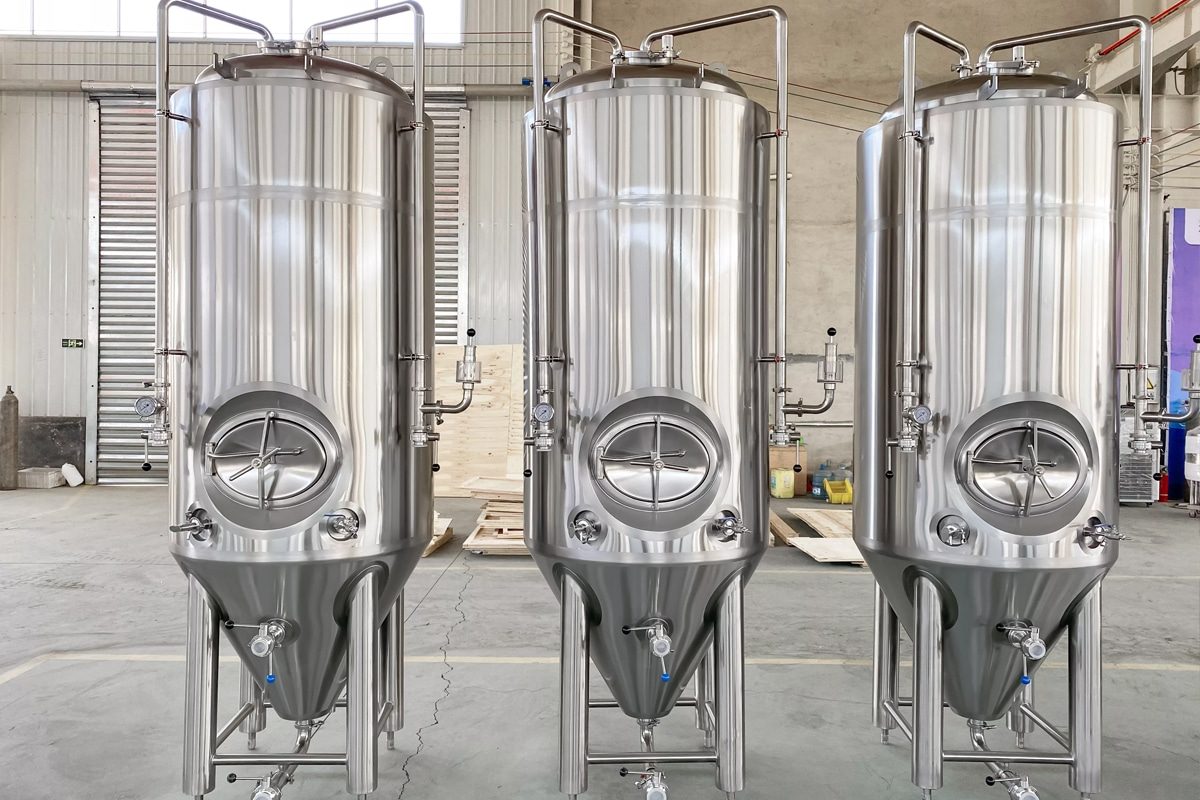
Summary
Preventing fermentation tank corrosion helps maintain the quality of your fermentation product, ensures the longevity of your brewery equipment, and reduces maintenance costs. Corrosion can be effectively managed by understanding the factors that contribute to it, including material composition, environmental conditions, and microbial activity. Implementing best practices such as selecting corrosion-resistant materials like high-grade stainless steel, designing tanks with smooth surfaces and proper drainage, and applying protective coatings and linings can significantly reduce the risk of corrosion. Regular cleaning, disinfection, and maintenance can prevent corrosion caused by microorganisms and ensure the effectiveness of protective measures. Controlling environmental conditions such as humidity and temperature, using chemical treatments like corrosion inhibitors and passivation, and conducting regular inspections and monitoring are vital steps in a comprehensive corrosion prevention strategy. Training staff and raising awareness about corrosion prevention practices further enhance the effectiveness of these measures, ensuring the integrity and efficiency of fermentation tanks over the long term.
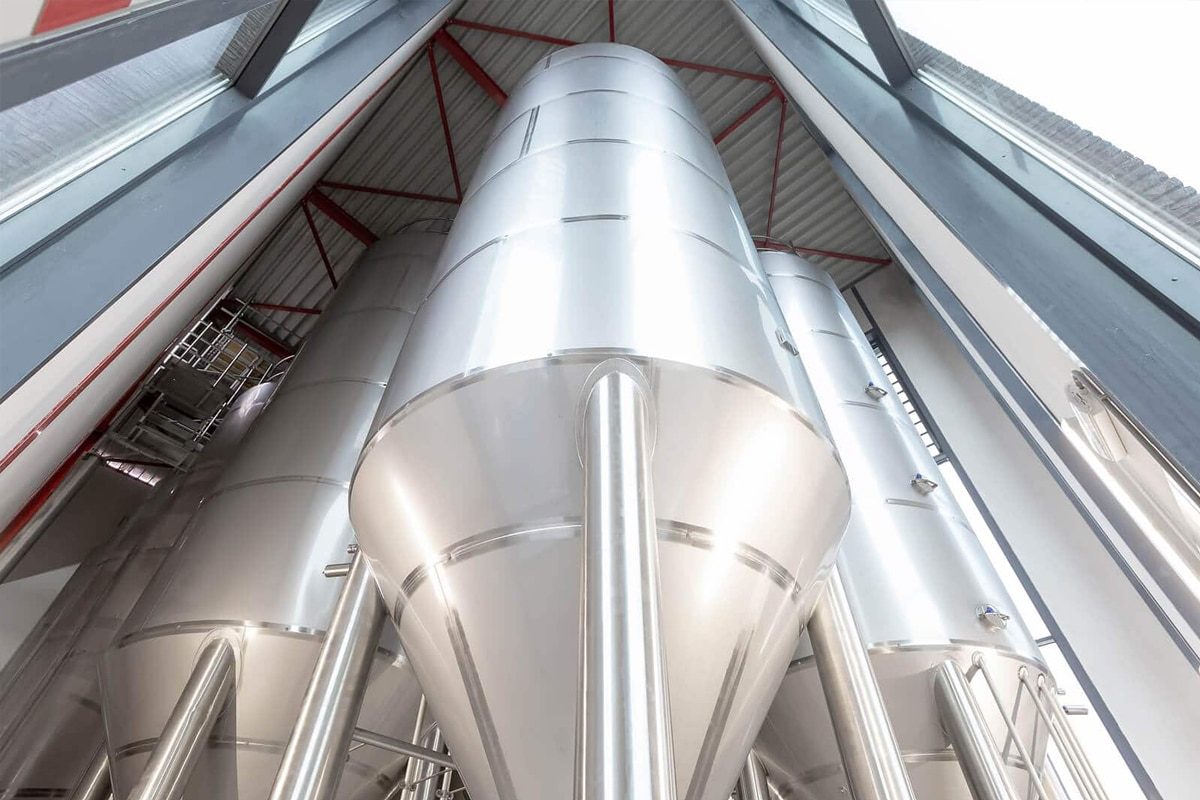
Get A Turnkey Brewery Solutions
Choosing a turnkey brewery solution from a professional provider like ZYB Craft can significantly simplify the process of preventing corrosion in fermentation tanks. Turnkey solutions offer comprehensive, end-to-end services, ensuring that every aspect of the brewery setup is optimized for performance and durability. ZYB Craft provides state-of-the-art fermentation tanks made from high-grade stainless steel, designed with corrosion resistance in mind. Their expert team ensures proper installation, incorporating features such as smooth welds, effective drainage, and ventilation systems that minimize corrosion risks. Additionally, ZYB Craft offers tailored maintenance programs and advanced protective coatings, further enhancing the longevity of your equipment. By opting for a turnkey solution, you benefit from professional expertise, reliable equipment, and ongoing support, allowing you to focus on producing high-quality brews while minimizing the challenges of equipment corrosion. Trust ZYB Craft to deliver a seamless and efficient brewery setup that stands the test of time.