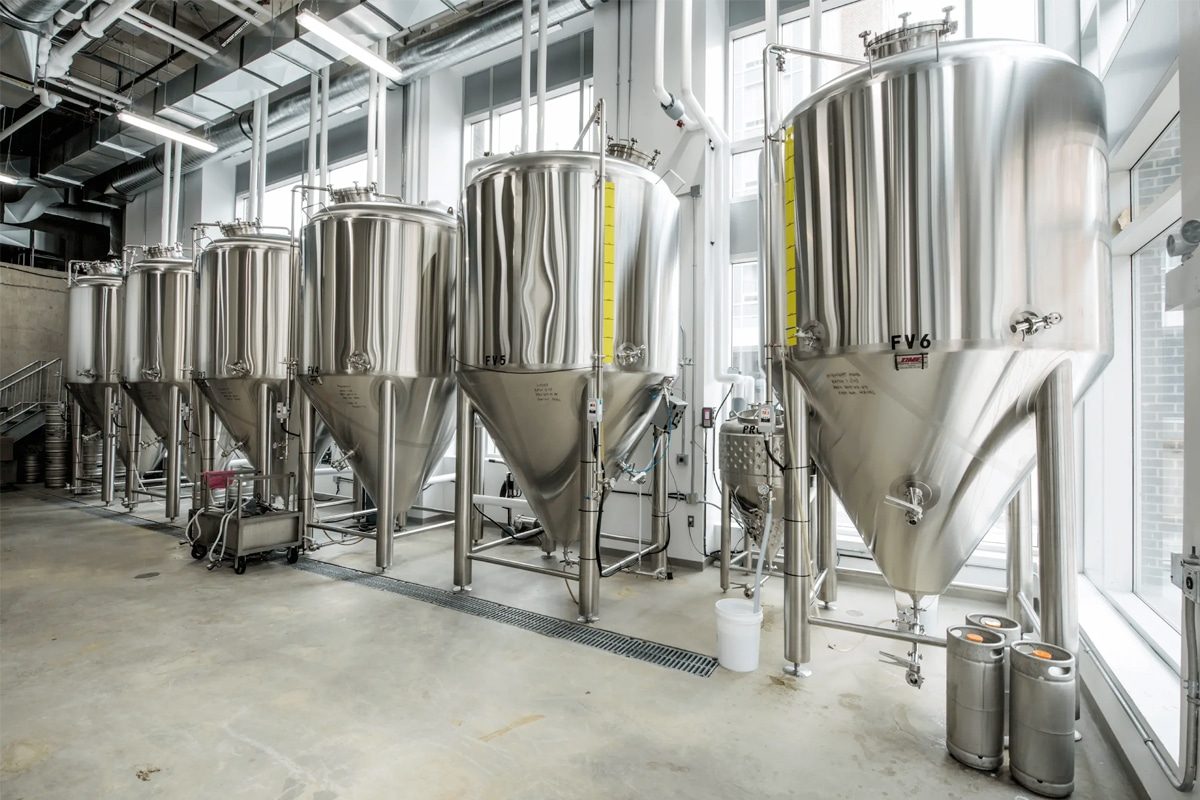
How To Manage CO2 Buildup in Fermentation Tanks?
Managing CO2 buildup in fermentation tanks is critical to modern brewing, directly impacting product quality, operational safety, and environmental responsibility. During fermentation, yeast converts sugars into alcohol and carbon dioxide, a natural byproduct essential for creating the carbonation and mouthfeel that define many beers. However, excessive CO2 accumulation within fermentation tanks can pose significant risks, including over-pressurization, potential tank damage, and safety hazards for brewery personnel.
Understanding how to control and utilize CO2 is not just a technical requirement but also a pathway to improving efficiency, ensuring consistency, and maintaining a safe working environment for breweries of all sizes. Effective CO2 management involves monitoring production rates, implementing pressure control mechanisms, and exploring technologies like CO2 recovery systems. This article delves into practical strategies and best practices to address CO2 buildup in fermentation tanks, helping brewers maintain safety standards while enhancing the brewing process and reducing environmental impact.
Complete Guide
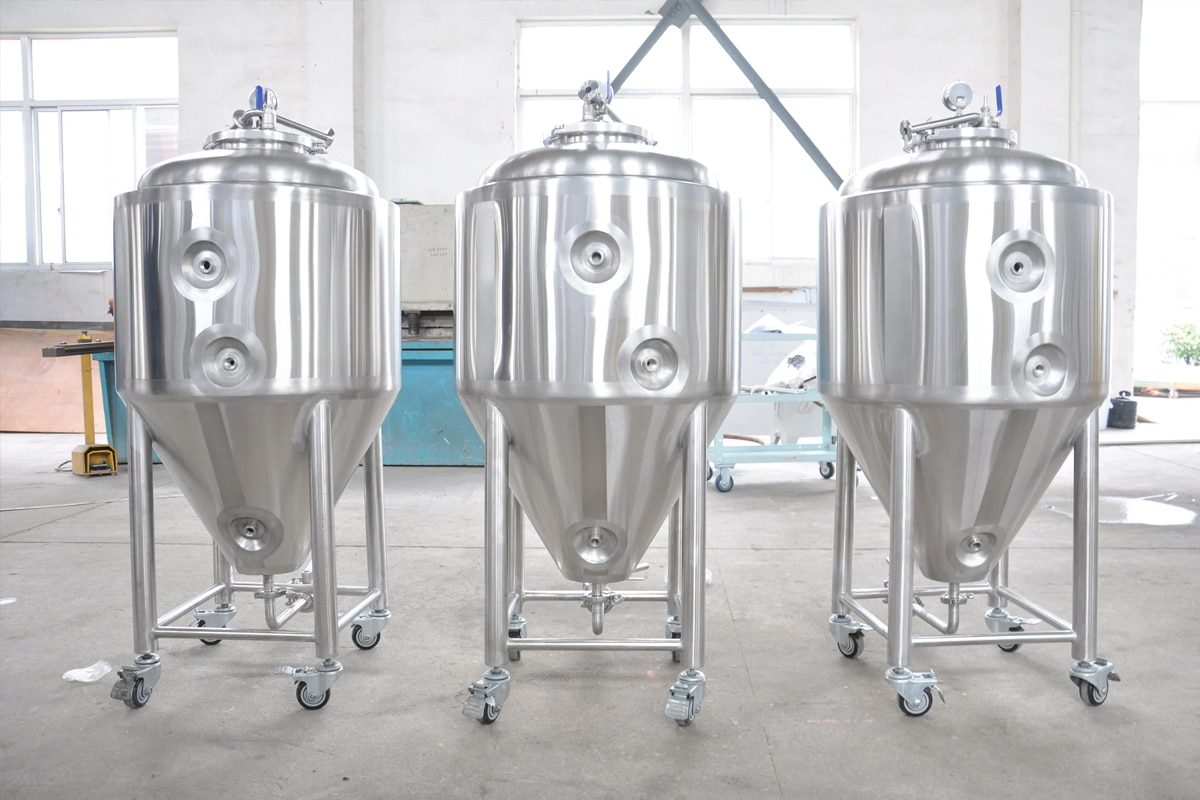
Understanding CO2 in Fermentation
The Fermentation Process
Fermentation is the heart of brewing, where yeast transforms the sugars in the wort into alcohol and carbon dioxide (CO2). This biochemical reaction is driven by yeast metabolism, producing ethanol and CO2 as its primary byproducts. The general equation for fermentation is:
C6H12O6 (glucose)→2 C2H5OH (ethanol)+2 CO2 (carbon dioxide)
This process occurs in distinct phases:
- Lag Phase: Yeast adapts to its environment, preparing for rapid reproduction.
- Exponential Phase: Active fermentation begins, with yeast cells multiplying and CO2 production accelerating.
- Stationary Phase: Fermentation slows as sugars are depleted and alcohol concentration rises.
- Final Phase: Yeast activity diminishes, with minimal CO2 production.
The rate and volume of CO2 generated depend on various factors, including the yeast strain, fermentation temperature, sugar concentration, and tank design.
Role of CO2 in Fermentation
CO2 plays a dual role in the brewing process, influencing both the beer’s quality and the fermentation environment.
- Carbonation: CO2 contributes to the beer’s characteristic carbonation, enhancing its mouthfeel and sensory appeal. The level of carbonation is crucial for certain beer styles, such as lagers and wheat beers, which demand a crisp, effervescent profile.
- Protection Against Oxidation: During fermentation, CO2 forms a natural blanket over the beer, reducing exposure to oxygen. This minimizes oxidation risks, which can cause off-flavors and spoil the beer’s freshness.
- Yeast Health and Fermentation Efficiency: CO2 concentration within the fermentation tank impacts yeast performance. While moderate levels are beneficial, excessive CO2 can stress yeast cells, slowing down fermentation and leading to incomplete sugar conversion.
- Pressure Control in Fermentation Tanks: Managing CO2 levels can help maintain optimal pressure within the fermentation tank. Controlled pressure can enhance specific flavor profiles, reduce undesirable byproducts, and support consistent brewing results.
Understanding the fermentation process and the role of CO2 allows brewers to effectively manage this byproduct, ensuring a balance between operational safety, beer quality, and production efficiency.

Risks Associated with CO2 Buildup
Proper management of CO2 in fermentation tanks is crucial, as unchecked buildup can lead to several risks that affect health, equipment, and beer quality.
Health Hazards
CO2 is a colorless, odorless gas that can accumulate to dangerous levels in enclosed brewing spaces. Its heavier-than-air properties mean it can settle in low areas, displacing oxygen and creating hazardous conditions. Health risks associated with CO2 buildup include:
- Asphyxiation: High concentrations of CO2 can displace oxygen, leading to symptoms such as dizziness, shortness of breath, unconsciousness, and even death in severe cases. Workers in confined spaces, such as fermentation rooms, are particularly vulnerable.
- Respiratory Irritation: Even at lower levels, CO2 can cause discomfort, including coughing, throat irritation, and difficulty breathing.
- Long-Term Exposure Risks: Prolonged exposure to moderate levels of CO2 can contribute to fatigue and reduced cognitive function.
Ensuring proper ventilation, gas monitoring systems and adherence to safety protocols is essential for protecting brewery personnel.
Equipment Damage
The buildup of CO2 can exert excessive pressure on fermentation tanks and associated equipment, leading to potential mechanical failures, including:
- Tank Ruptures: Over-pressurization from excessive CO2 can cause tanks to burst, posing serious safety hazards and costly repairs.
- Valve Failures: Pressure relief valves may become overburdened if CO2 levels are not properly managed, increasing the risk of malfunction.
- Stress on Fittings and Seals: Persistent high pressure can degrade tank components, reducing their lifespan and compromising the integrity of the system.
Proper pressure management, including the use of spunding valves and regular equipment inspections, helps mitigate these risks.
Impact on Beer Quality
CO2 levels directly influence the characteristics and consistency of the beer. Poor management of CO2 buildup can lead to:
- Over-Carbonation: Excess CO2 may result in overly fizzy beer, disrupting the intended mouthfeel and taste profile.
- Yeast Stress: High CO2 concentrations can stress yeast, leading to incomplete fermentation, undesirable off-flavors, or inconsistent alcohol content.
- Oxidation Risks: While CO2 protects against oxygen exposure, abrupt venting or poor pressure control can allow oxygen to enter the tank, negatively affecting the beer’s flavor and shelf life.
By maintaining optimal CO2 levels and implementing precise monitoring and control measures, brewers can ensure high-quality, consistent beer production while minimizing risks to both health and equipment.
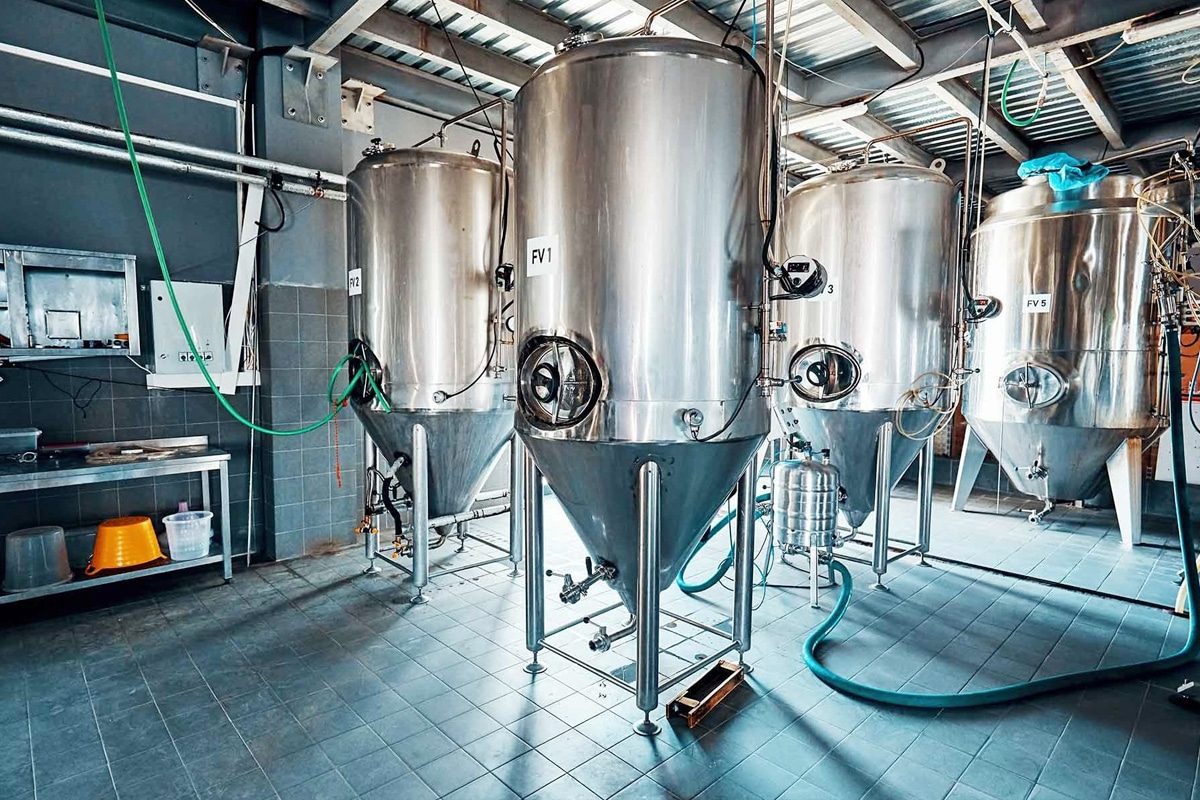
Methods to Manage CO2 Buildup
Managing CO2 buildup in fermentation tanks is a multi-faceted process that requires a combination of strategies to ensure safety, equipment efficiency, and beer quality.
Ventilation Strategies
Ventilation is a cornerstone of CO2 management in brewing facilities, ensuring that excess CO2 does not accumulate in dangerous concentrations. Because CO2 is heavier than air, it settles near the floor and can pose significant risks if not properly dispersed.
Natural Ventilation
- Strategic Layout: Position windows, doors, and vents to allow for natural air circulation. Openings at floor level are particularly effective at allowing CO2 to escape.
- Room Design: Incorporate high ceilings and open layouts in fermentation rooms to reduce the risk of CO2 buildup in confined spaces.
Mechanical Ventilation
- Exhaust Systems: Install mechanical fans near floor level to actively pull CO2 out of the fermentation area. Use industrial-grade exhaust systems for large-scale breweries.
- Airflow Optimization: Design airflow paths to maximize CO2 removal while preventing recirculation of the gas within the room.
- Backup Power: Ensure ventilation systems are connected to backup power sources to maintain functionality during outages.
Confined Space Management
- Equip confined areas with portable air circulation units to enhance airflow.
- Restrict access to high-CO2 areas and enforce the use of gas monitoring devices before entry.
Proper ventilation reduces the likelihood of hazardous CO2 concentrations, protecting workers and maintaining a safe environment.
Use of Spunding Valves
Spunding valves are an effective tool for regulating pressure and CO2 levels in fermentation tanks. These devices are essential for controlled fermentation and natural carbonation.
Controlled Pressure Fermentation
- Pressure Adjustments: Spunding valves allow brewers to maintain precise internal tank pressures by releasing CO2 at preset thresholds.
- Flavor Optimization: Controlled pressure helps manage yeast behavior, reducing the production of unwanted esters and fusel alcohols. This results in cleaner-tasting beer.
- Consistency: Maintaining a stable fermentation pressure ensures batch-to-batch consistency.
Natural Carbonation
- By partially retaining CO2 during fermentation, spunding valves allow brewers to naturally carbonate beer, reducing or eliminating the need for forced carbonation during packaging.
- Natural carbonation produces finer bubbles, enhancing the mouthfeel and sensory appeal of the beer.
Integration with Tank Systems
- Spunding valves are typically installed on fermentation tanks with pressure-rated fittings. They can be adjusted manually or connected to automated pressure monitoring systems for ease of use.
Spunding valves are particularly valuable for lagers and other beer styles where precise pressure and carbonation levels are critical.
CO2 Recovery Systems
CO2 recovery systems represent a sustainable and cost-effective solution for managing CO2 buildup. These systems allow breweries to capture, purify, and store CO2 produced during fermentation for reuse in various stages of the brewing process.
Collection
- Piping Setup: CO2 is collected directly from the headspace of fermentation tanks via dedicated piping systems.
- Tank Seals: Fermentation tanks must be sealed appropriately to prevent CO2 leakage during collection.
Purification
- Raw CO2 often contains impurities such as water vapor, ethanol, and residual sugars. Recovery systems filter and purify the gas to meet food-grade standards.
- Multi-stage filtration systems ensure the final product is suitable for direct use in carbonation or packaging.
Storage and Reuse
- Compression: The purified CO2 is compressed into storage tanks for later use in beer carbonation, kegging, or bottling.
- Efficiency: Recovery systems reduce dependence on external CO2 suppliers, saving costs and ensuring a steady supply.
Environmental Benefits
- Capturing and reusing CO2 lowers a brewery’s carbon footprint, contributing to sustainability goals.
- Some breweries integrate recovery systems into broader environmental initiatives, such as offsetting emissions through renewable energy use.
CO2 recovery systems are an investment that pays dividends in both financial and environmental terms, particularly for medium to large breweries.
Monitoring CO2 Levels
Accurate monitoring is crucial for effective CO2 management, as it provides real-time data to guide ventilation, pressure control, and safety measures.
CO2 Sensors
- Placement: Install sensors at critical points, such as fermentation rooms, tank headspaces, and near floor levels where CO2 tends to accumulate.
- Functionality: Sensors should be calibrated to detect CO2 concentrations in parts per million (ppm), with alarms triggered at hazardous levels (e.g., above 5,000 ppm for occupational safety).
Pressure Gauges
- Attach gauges to fermentation tanks to monitor internal pressures continuously.
- Pressure readings help identify early signs of over-pressurization, allowing for timely intervention.
Data Logging and Analytics
- Use digital monitoring systems to log CO2 data over time, enabling brewers to analyze trends and optimize processes.
- Integration with brewery management software enhances decision-making and predictive maintenance.
Portable Monitors
- Equip staff with portable CO2 detectors for use in confined spaces or during maintenance tasks.
Real-time monitoring ensures safety, compliance, and optimal brewing conditions.
Tank Design Considerations
The design of fermentation tanks has a direct impact on CO2 management. Investing inappropriately engineered tanks reduces risks and enhances efficiency.
Pressure-Rated Tanks
- Use tanks built to withstand the maximum pressures expected during fermentation, typically featuring reinforced walls and high-quality seals.
- Certification and testing ensure tanks meet industry safety standards.
Pressure Relief Valves
- Equip tanks with automatic pressure relief valves to release excess CO2 safely and prevent over-pressurization.
- Regular maintenance of these valves ensures reliability.
Headspace Design
- Tanks should include sufficient headspace to accommodate CO2 buildup and foam during active fermentation stages.
- Headspace capacity reduces the risk of overflow and pressure spikes.
Sanitary Features
- Smooth interiors, polished to food-grade standards, prevent contamination, and simplify cleaning.
- Sanitary fittings and connections minimize the risk of leaks during CO2 venting or recovery.
Customization for CO2 Management
- Incorporate fittings for spunding valves, blow-off tubes, and CO2 recovery systems.
- Tanks can also be outfitted with sensors and gauges for enhanced monitoring.
Properly designed tanks form the backbone of safe and efficient CO2 management.
These methods collectively provide a robust approach to managing CO2 buildup in fermentation tanks. By combining ventilation, pressure control, monitoring, and advanced systems like CO2 recovery, breweries can enhance safety, optimize efficiency, and produce high-quality beer while reducing their environmental impact. ZYB Craft offers brewery equipment tailored to these needs, ensuring that every brewer has the tools to excel.
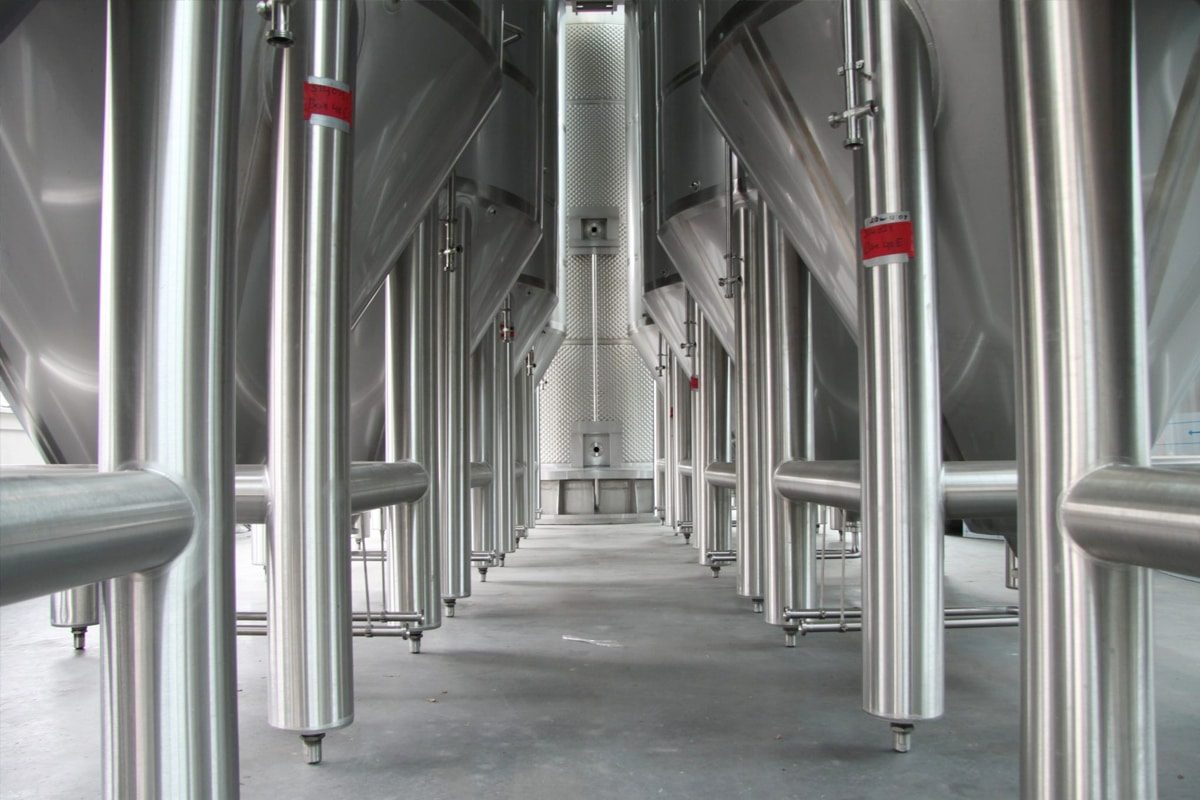
Equipment Considerations for Managing CO2 Buildup
Effective CO2 management in fermentation tanks requires the right equipment, robust safety measures, and consistent maintenance practices.
Selecting the Right Fermentation Tanks
Properly designed fermentation tanks are critical for controlling CO2 buildup. The materials, fittings, and valves used in tank construction directly impact their safety, durability, and functionality.
Materials
- Stainless Steel: The preferred material for fermentation tanks due to its durability, resistance to corrosion, and ease of cleaning. Grades such as 304 or 316 stainless steel are commonly used in brewing for their food-grade quality and strength.
- Alternative Materials: For smaller or less industrial setups, polyethylene or fiberglass tanks can be used, but they lack the durability and pressure resistance of stainless steel.
Fittings and Valves
- Pressure Relief Valves: Essential for releasing excess CO2 to prevent over-pressurization. Ensure these valves are adjustable and rated for the tank’s maximum pressure capacity.
- Sampling Ports: Allow brewers to take samples without opening the tank, minimizing CO2 escape and contamination risks.
- Tri-Clamp Fittings: Commonly used for their ease of disassembly, ensuring secure, sanitary connections that simplify maintenance.
- CO2 Vent Connections: Ports for attaching spunding valves, blow-off tubes, or CO2 recovery systems are vital for controlled pressure management.
Investing in well-designed fermentation tanks with these features enhances safety, efficiency, and consistency in CO2 management.
Safety Equipment
Managing CO2 buildup requires proper safety measures to protect brewery personnel and ensure compliance with safety regulations. Key safety equipment includes personal protective equipment (PPE) and ventilation systems.
Personal Protective Equipment (PPE)
- CO2 Monitors: Portable CO2 detectors should be worn by workers in fermentation areas to monitor gas levels in real-time.
- Respiratory Protection: Masks or respirators should be provided in areas with elevated CO2 concentrations or during tank maintenance tasks.
- Protective Clothing: Ensure staff are equipped with non-slip footwear, gloves, and safety goggles to prevent injuries in wet or high-risk environments.
Ventilation Systems
- Mechanical Ventilation: Install industrial fans or exhaust systems designed to remove CO2 from fermentation areas. Ensure airflow is directed from floor level, where CO2 tends to settle.
- Air Circulation Units: Portable air circulators can be used in confined spaces or smaller setups to disperse CO2 effectively.
- Backup Power Systems: Connect critical ventilation equipment to an uninterrupted power supply (UPS) to maintain functionality during outages.
Equipping your brewery with appropriate safety measures protects staff and ensures a safe working environment.
Maintenance and Inspection
Regular maintenance and inspection of equipment are essential for effective CO2 management. This ensures the longevity of your tanks and associated systems while preventing accidents or malfunctions.
Regular Inspections
- Pressure Relief Valves: Inspect and test valves periodically to ensure they function correctly and can handle the expected CO2 loads.
- Tank Integrity: Check for cracks, leaks, or signs of corrosion in the tank body, fittings, and connections.
- Monitoring Devices: Verify that CO2 sensors, pressure gauges, and spunding valves are calibrated and functioning properly.
Cleaning Protocols
- Sanitation of Tanks: Clean and sanitize fermentation tanks after every use to prevent contamination and maintain consistent beer quality. Automated CIP (Clean-In-Place) systems are recommended for efficiency.
- Valve and Fitting Maintenance: Disassemble and clean valves and fittings regularly to prevent residue buildup that can interfere with functionality.
- Ventilation Systems: Clean ventilation ducts and fans to ensure unobstructed airflow and optimal performance.
Implementing thorough maintenance and inspection routines not only ensures operational safety but also contributes to the longevity and efficiency of your brewery equipment.
By carefully selecting the right fermentation tanks, equipping your facility with adequate safety measures, and maintaining a rigorous inspection and cleaning schedule, you can effectively manage CO2 buildup in fermentation tanks.
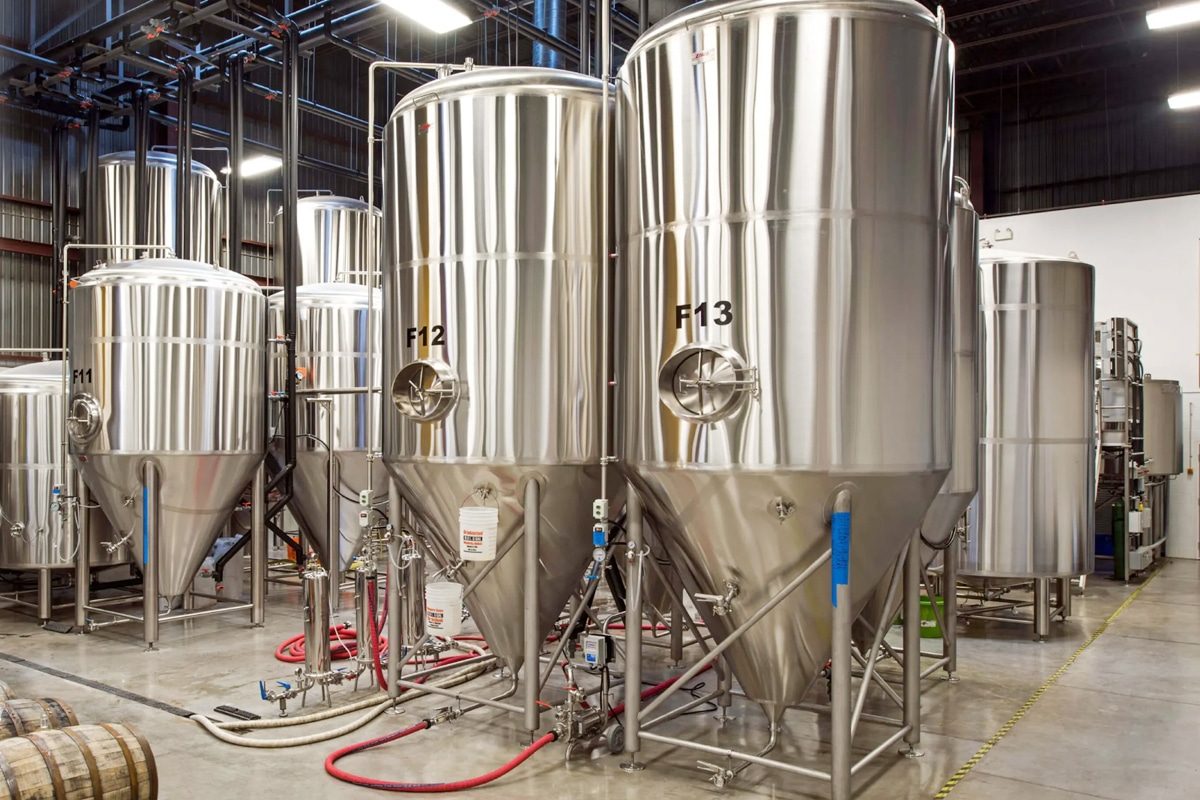
Best Practices for CO2 Management
Proper management of CO2 in fermentation tanks is critical for ensuring safety, maintaining high-quality production standards, and adhering to regulations. Implementing best practices helps breweries optimize processes, protect staff, and reduce risks. Below are detailed guidelines focusing on staff training, regulatory compliance, and operational procedures.
Staff Training
Well-trained staff are essential for effective CO2 management. Providing comprehensive training ensures employees understand the risks associated with CO2 and how to operate equipment safely and efficiently.
Safety Procedures
- Recognizing Hazards: Train staff to identify CO2 risks, such as the presence of low-lying gas, symptoms of exposure (e.g., dizziness, shortness of breath), and situations where CO2 buildup is likely to occur.
- Emergency Protocols: Establish clear procedures for handling CO2-related emergencies, including evacuation routes, first aid measures, and the use of gas detection devices.
- Confined Space Safety: Teach employees how to safely enter and work in confined spaces, emphasizing the importance of gas monitoring and ventilation.
Equipment Operation
- Tank Systems: Train staff to operate fermentation tanks, focusing on CO2 control mechanisms such as spunding valves, pressure relief valves, and CO2 recovery systems.
- Monitoring Devices: Provide training on using CO2 sensors and pressure gauges to maintain safe and efficient fermentation conditions.
- Maintenance Practices: Equip employees with the knowledge to inspect and maintain tanks, fittings, and safety equipment.
Regular training refreshers and updates ensure that staff remain knowledgeable about evolving safety standards and operational best practices.
Regulatory Compliance
Breweries must adhere to both occupational safety and environmental regulations to ensure legal compliance and promote a safe, sustainable operation.
Occupational Safety Standards
- CO2Exposure Limits: Follow guidelines set by organizations like OSHA (Occupational Safety and Health Administration), which recommend permissible exposure limits (PEL) for CO2 in the workplace. For example, OSHA sets a PEL of 5,000 ppm over 8 hours.
- Confined Space Regulations: Ensure compliance with standards for working in confined spaces, including the use of gas monitoring devices and safety harnesses when necessary.
- Inspection and Documentation: Maintain records of safety inspections, employee training, and equipment maintenance to demonstrate compliance during audits.
Environmental Regulations
- CO2Emission Reduction: Implement practices to minimize CO2 emissions, such as using recovery systems to capture and reuse gas.
- Waste Management: Adhere to local laws governing the disposal of byproducts and waste generated during the brewing process.
- Sustainability Initiatives: Many regions encourage breweries to adopt green practices, such as reducing greenhouse gas emissions and improving energy efficiency.
Staying informed about regional and international regulations helps breweries avoid penalties and contributes to industry leadership in sustainability.
Operational Procedures
Well-defined operational procedures form the backbone of effective CO2 management. Developing and implementing SOPs ensures consistency, safety, and continuous improvement in brewery operations.
Standard Operating Procedures (SOPs)
- CO2 Venting and Pressure Management: Document step-by-step guidelines for venting CO2, using spunding valves, and monitoring tank pressure during fermentation.
- Equipment Use and Maintenance: Create detailed procedures for operating and maintaining tanks, valves, monitoring devices, and CO2 recovery systems.
- Emergency Response: Include clear protocols for handling equipment malfunctions, gas leaks, or CO2 exposure incidents.
Continuous Improvement
- Performance Monitoring: Regularly review fermentation data, including CO2 production rates and tank pressure trends, to identify opportunities for optimization.
- Feedback Mechanisms: Encourage staff to provide feedback on SOPs and suggest improvements based on their experiences.
- Technology Upgrades: Stay updated on advancements in brewing technology, such as more efficient CO2 recovery systems or enhanced monitoring tools, to improve safety and efficiency.
Fostering a culture of continuous improvement not only enhances CO2 management but also supports broader operational excellence.
Implementing these best practices enables breweries to effectively manage CO2 buildup, ensuring a safe workplace, high-quality beer, and sustainable operations.
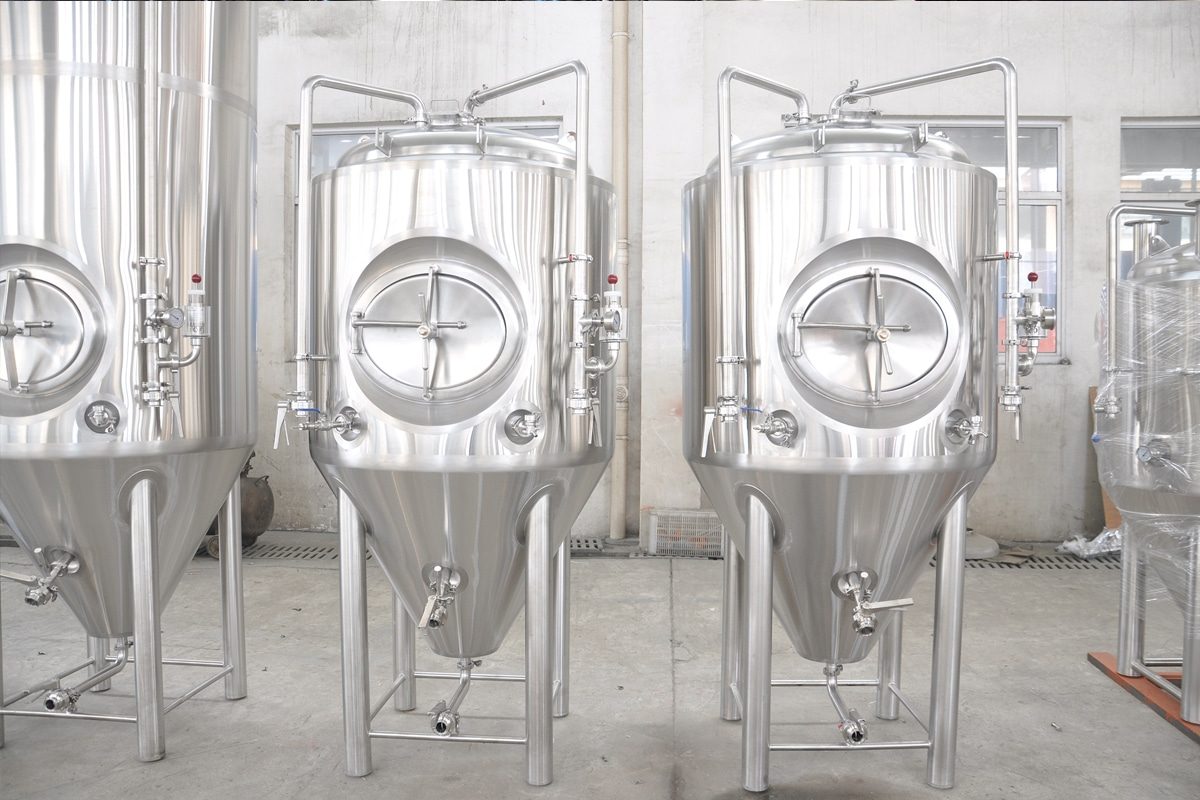
Summary
Managing CO2 buildup in fermentation tanks is critical to brewery operations, impacting safety, product quality, and operational efficiency. As yeast metabolizes sugars during fermentation, CO2 is naturally produced, requiring careful monitoring and control to prevent safety hazards, equipment damage, and product inconsistencies. Implementing a combination of strategies, such as proper ventilation, spunding valves, CO2 recovery systems, and advanced monitoring tools, helps brewers maintain optimal conditions within fermentation tanks.
Equally important is selecting the right equipment, including pressure-rated tanks with appropriate fittings and valves, and ensuring regular maintenance to uphold their functionality. Staff training, adherence to occupational and environmental regulations, and clear operational procedures are essential to safe and efficient CO2 management. By prioritizing these practices, breweries can enhance safety, reduce environmental impact, and ensure consistent, high-quality beer production.
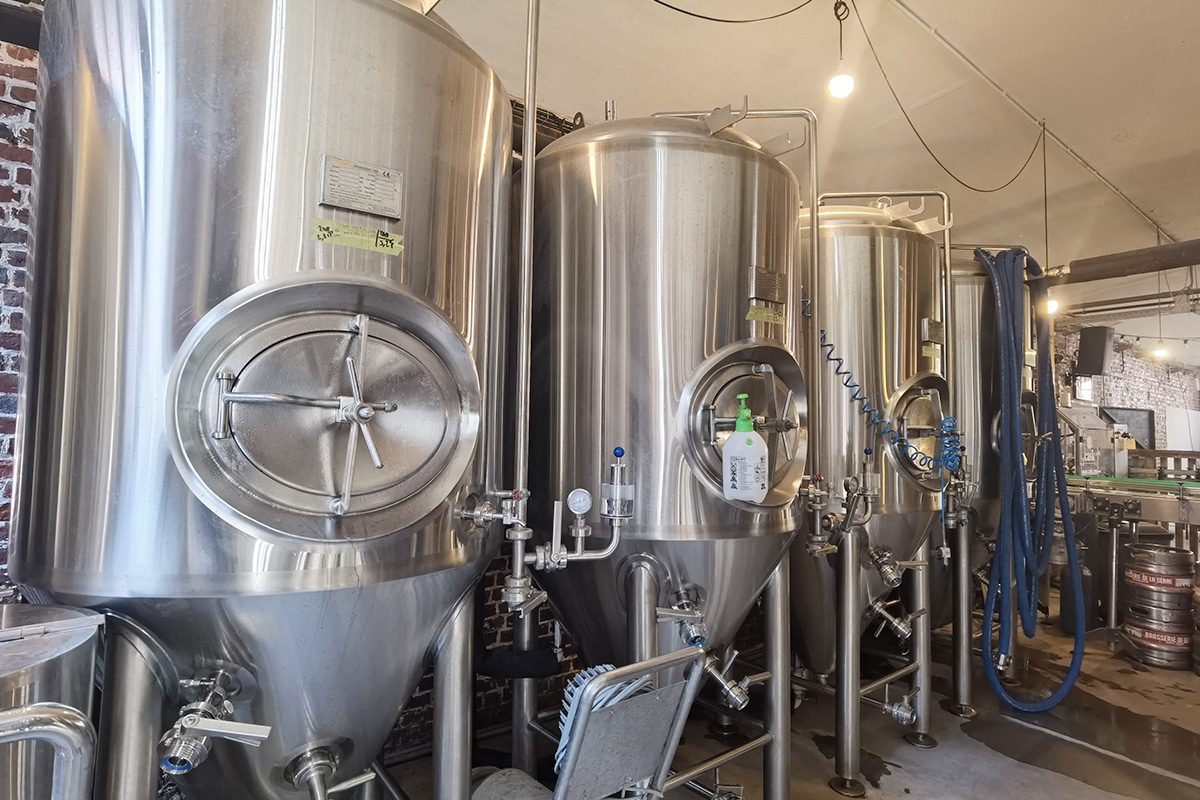
Get A Turnkey Brewery Solutions
Managing CO2 buildup in fermentation tanks requires more than just knowledge—it demands the right equipment and systems tailored to your brewery’s unique needs. At ZYB Craft, we specialize in providing professional, turnkey brewery solutions that streamline operations, enhance safety, and improve the overall brewing process. Our solutions include state-of-the-art fermentation tanks designed for optimal CO2 control, equipped with advanced features like pressure relief valves, spunding valve compatibility, and integrated CO2 recovery systems.
Beyond equipment, ZYB Craft offers comprehensive consulting services to help breweries implement effective CO2 management strategies, from ventilation system design to operational workflow optimization. Our team ensures every detail aligns with safety standards and regulatory requirements. Whether you’re building a new brewery or upgrading your existing setup, ZYB Craft delivers reliable, efficient solutions to help you achieve consistent, high-quality production. Contact us today to learn how we can support your brewery’s success.