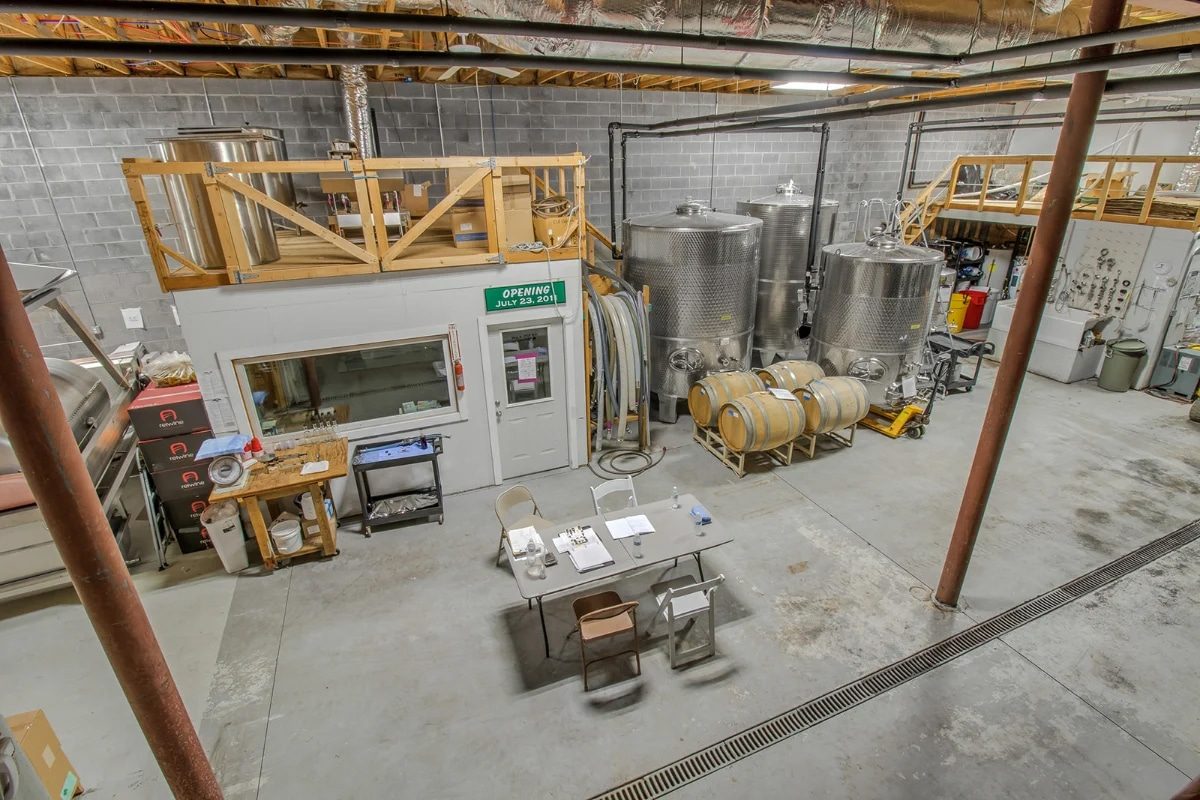
How To Develop The Best Brewery Floor Plan?
Creating the perfect brewery floor plan is a crucial step in turning your beer dreams into reality. In addition to the art of brewing great beer, there’s also the science and strategy of designing a space to optimize workflow, ensure safety, and accommodate future growth. A well-designed floor plan is more than just a layout, it’s a blueprint for efficiency, productivity, and innovation. It is the backbone that supports the seamless flow of raw materials during the brewing process, the orchestration of brewery equipment, and the packaging and distribution of craft beer.
In this comprehensive guide, we’ll dive into the essential elements of developing the best brewery floor plan, providing insights and practical advice to help you navigate the complexities of brewery design and create a space that sets the stage for brewing success. Whether you’re starting a new brewery or upgrading an existing facility, this guide will give you the knowledge and tools to design a brewery floor plan that meets your unique needs and fuels your passion for brewing great beer.
Complete Guide
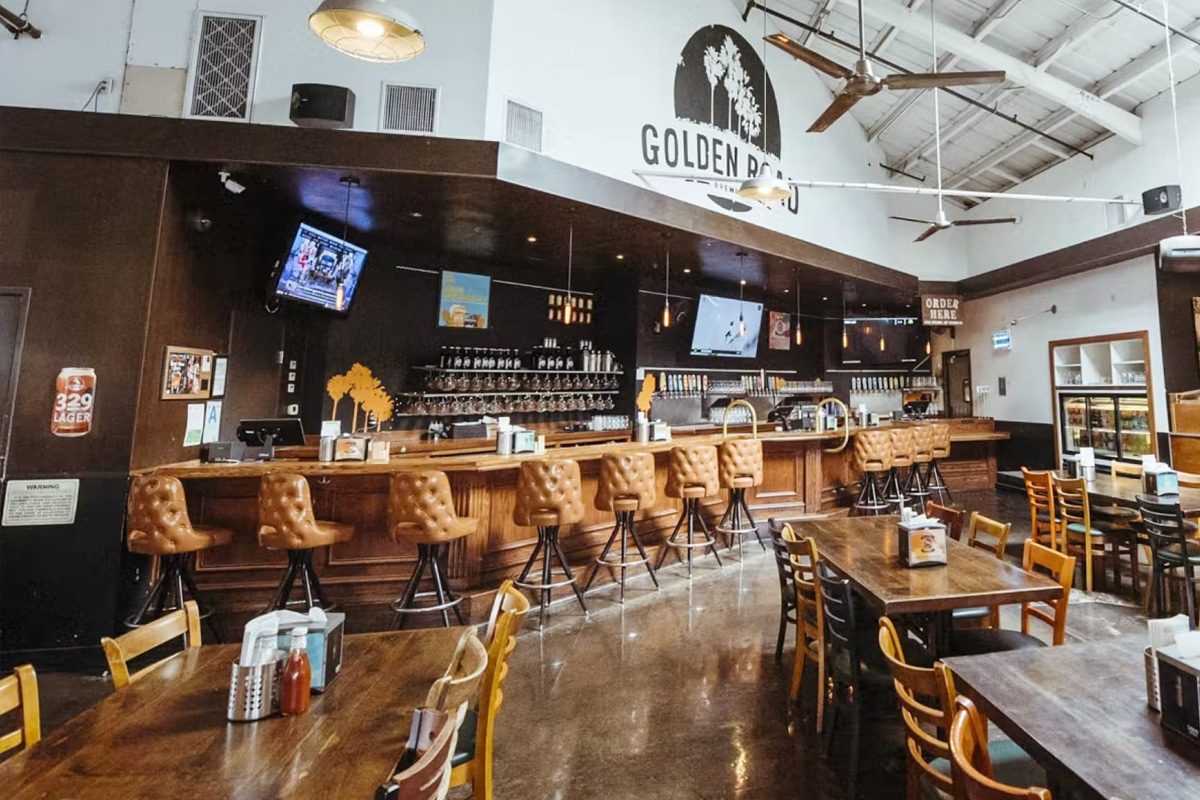
Understand your brewery’s needs
Developing the best brewery floor plan starts with a thorough understanding of your brewery’s unique requirements. By carefully evaluating every aspect of your operation, from production capacity to future growth potential, you can lay a solid foundation for designing an efficient and effective floor plan that suits your specific needs.
Assess production capabilities
Before delving into the intricacies of a brewery floor plan, it’s important to have a clear understanding of your production capacity requirements. Consider factors such as expected beer production, the type of beer you plan to brew, and any seasonal or specialty batches you plan to produce. This assessment will help determine the size and layout of your brewing equipment, fermentation vessels, and packaging lines to ensure they can meet your production goals.
Determine brewery equipment needs
Once you have determined your production capacity, the next step is to determine the brewery equipment needed to achieve your brewing goals. Evaluate the type and size of brewhouse equipment, fermenters, CIP systems, heat exchangers, and other basic equipment required for the brewing process. Consider specific requirements for brewing technology, such as hot and cold liquid tanks, grain handling systems, and filtration equipment. Choosing the right equipment can help optimize brewing efficiency, maintain product quality, and ensure scalability as your brewery grows.
Packaging and distribution planning
Packaging and distribution are critical components of a brewery operation and should be carefully considered when developing a floor plan. Determine your preferred packaging method, whether kegging, bottling, canning, or a combination thereof, and allocate space for packaging lines, labeling equipment, and storage of packaging materials. Consider logistics, such as finished product storage space, loading docks, and delivery vehicle access routes to ensure the packaging and delivery process is smooth and efficient.
Estimated storage requirements
Effective storage management maintains inventory levels and ensures product quality and freshness. Anticipate your storage needs for raw materials, packaging supplies, and finished goods, including grain storage, hops storage, yeast management, and refrigeration for kegs or packaged beer. Allocate enough space to each type of storage, considering factors such as accessibility, organization, and temperature control to optimize storage efficiency and product quality.
Consider future expansion
While focusing on your brewery’s current needs, it’s also critical to plan for future growth and expansion. Anticipate potential changes in production capacity, product offerings, and market demand, and consider scalability when designing floor plans. Leave room for additional equipment, storage capacity, or production lines to accommodate future growth without major renovations or facility expansions. By planning for future expansion now, you can save time and resources and ensure your brewery remains adaptable and competitive in the ever-evolving craft beer industry.
You can gain a complete understanding of your brewery’s needs by thoroughly assessing your brewery’s production capacity, determining your brewing equipment needs, planning packaging and distribution, forecasting storage requirements, and considering future expansion. These fundamentals will guide you in designing a brewery floor plan that meets your operational requirements, strategic goals, and long-term vision for brewing excellence.
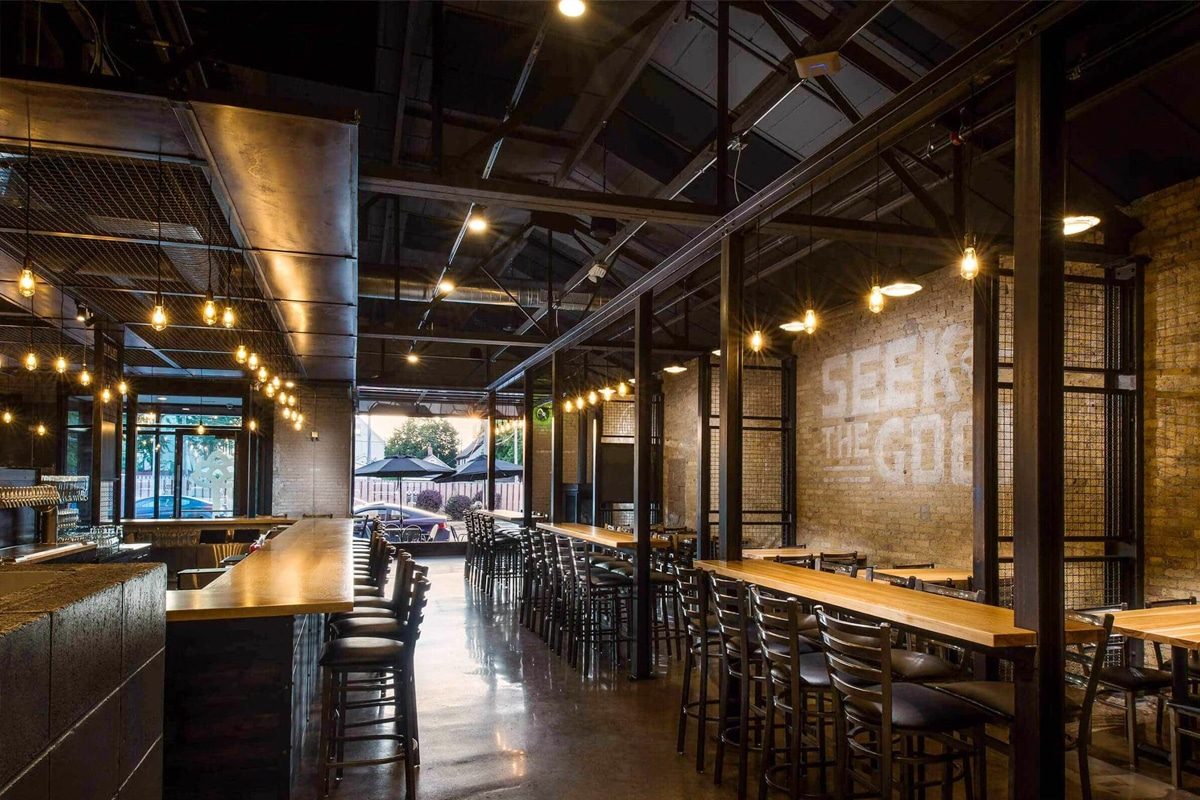
Workflow efficiency design
Creating an efficient brewery floor plan isn’t just about placing equipment in designated areas, it’s about coordinating the seamless flow of materials, people, and processes from raw materials to finished products. Well-designed workflows not only increase productivity but also ensure consistent product quality and safety. Here are key factors to consider when designing workflow efficiency:
Raw material storage and handling
Efficient storage and handling of raw materials is the basis for a smooth brewing process. Designate specific areas for receiving, storing, and managing ingredients such as malt, hops, yeast, and trimmings. Consider factors such as accessibility, organization, and FIFO (first in, first out) rotation to minimize waste and ensure fresh ingredients. Implement appropriate storage solutions, such as silos, bins, and racks, tailored to the specific needs and quantities of each raw material to streamline the brewing process and maintain inventory accuracy.
Brewery equipment layout
The layout of brewery equipment can help optimize the brewing process. Arrange brewhouse equipment, CIP systems, filtration equipment, and other important equipment in a logical sequence to minimize transmission distance and maximize operational efficiency. Consider factors such as equipment size, connection points, and workflow integration to create a cohesive and streamlined brewing system. Ensure adequate space around each piece of equipment for maintenance access, cleaning, and personnel movement to promote safe and efficient operations.
Fermentation and conditioning area
Fermentation and conditioning are critical stages in the brewing process and require careful planning to maintain product integrity and consistency. Designate dedicated areas for fermentation tanks, bright tanks, and conditioning vessels and arrange them to facilitate the smooth movement of beer between stages. Ensure proper temperature control, yeast management, and sampling, testing, and cleaning to optimize fermentation and conditioning efficiency. Consider integrating automation and monitoring systems to enhance process control and maintain product quality during these critical stages.
Packaging and bottling lines
Packaging and bottling are critical stages in the brewing process and require careful planning to ensure efficiency and product quality. Packaging areas should be designed with a focus on minimizing handling, reducing bottlenecks, and maximizing throughput. Arrange equipment such as filling machines, labelers, cappers, and conveyors to facilitate the smooth flow of products from packaging to palletizing. Ensure adequate space for packaging material storage, quality control checkpoints, and packaging line adjustments to accommodate various bottle sizes, labels, and packaging configurations. Integrate automation and quality assurance systems to improve packaging efficiency and product consistency.
Finished product storage
Proper storage of finished goods maintains product quality, ensures inventory accuracy, and facilitates timely distribution. Allocate dedicated storage areas for kegs, packaged beers, and seasonal or specialty products, considering factors such as product rotation, accessibility, and temperature control requirements. Implement efficient racking systems, racking and pallet storage solutions tailored to the specific needs of each product type to optimize storage density and retrieval efficiency. Monitor inventory levels, expiration dates, and product turnover to minimize waste and ensure timely delivery to customers.
By designing your brewery floor plan with careful consideration of workflow efficiencies, you can streamline operations, minimize production downtime, and ensure consistent quality throughout your brewing process. By optimizing the layout of raw material storage and handling, brewing vessels and equipment, fermentation and conditioning areas, packaging and bottling lines, and finished product storage, you can create a brewery floor plan that sets the stage for brewing success.
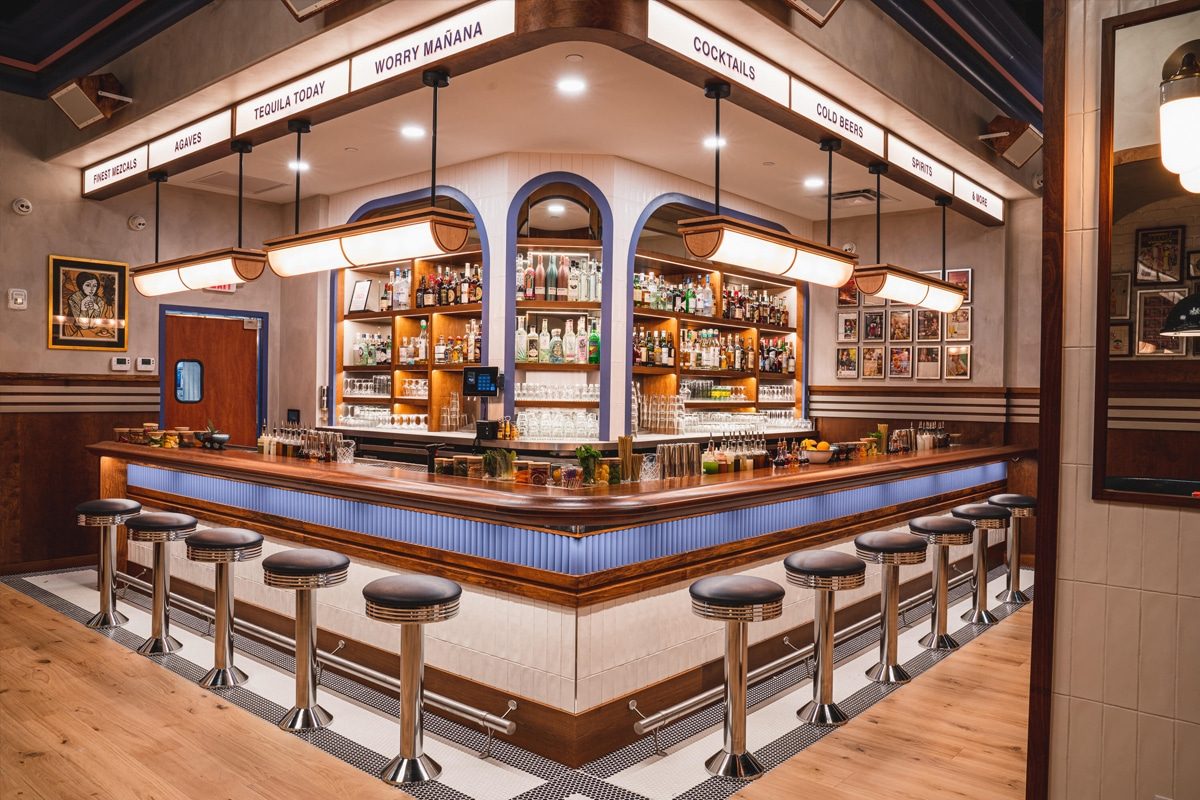
Maximize space utilization
Space optimization is critical for breweries of all sizes, whether operating in a compact urban location or a sprawling industrial facility. By maximizing the efficient use of available space, breweries can minimize overhead costs, improve workflow efficiency, and accommodate future growth. Here are key strategies for maximizing space utilization in brewery floor plan design:
Vertical space utilization
When floor space is limited, look for expansion opportunities in the vertical dimension. Utilize vertical space by installing mezzanine, aisle, or multi-level storage solutions to maximize storage capacity without increasing floor space. Consider using an overhead conveyor system to transport materials and products between different areas of your brewery. Effective use of vertical space can help declutter production areas, improve accessibility, and create additional workspace for administrative or support functions.
Device integration
Optimizing space utilization often involves consolidating equipment to minimize redundancy and maximize efficiency. Choose versatile equipment and flexible brewing systems that can perform multiple tasks within a compact footprint. Consider a modular brewing system that can be customized to meet your specific production needs while minimizing the overall space required. Consolidating equipment not only saves space but also streamlines workflows, reduces maintenance requirements, and improves overall operational efficiency.
Flexible layout design
Flexible design of brewery floor plans to adapt to changing production needs, technological advancements, and market demands. Take advantage of modular equipment, removable partitions, and adaptable workspaces that can be reconfigured as needed. Create flexible areas within your brewery that can easily accommodate different brewing processes, packaging requirements, or production lines. Flexible layout design allows your brewery to grow and expand without costly structural changes or facility expansions.
Efficient traffic flow
Minimizing congestion and optimizing traffic flow within the brewery can help maintain productivity and keep employees safe. Designate clean aisles, walkways, and staging areas to facilitate the movement of materials, personnel, and equipment throughout the facility. Implement one-way traffic patterns, color-coded areas, or signage to guide employees and visitors safely through different areas of the brewery. Consider ergonomic placement of equipment and workstations to reduce unnecessary movement and streamline workflow.
External Storage and Expansion
If space constraints prevent on-site expansion, explore options for off-site storage or satellite facilities to accommodate additional production capacity. Partnering with third-party logistics providers or contract brewers can provide access to external storage and production facilities as needed. Alternatively, consider leasing additional warehouse space or utilizing nearby facilities for overflow storage or specialized production processes. External storage and expansion options offer flexibility for scaling your brewery operations without compromising efficiency or requiring major facility modifications.
By implementing these strategies for maximizing space utilization, breweries can optimize workflow efficiency, minimize operating costs, and achieve sustainable growth and success in the highly competitive craft beer market. Whether operating in a compact urban environment or a sprawling industrial facility, breweries can leverage innovative design solutions to make the most of available space and create a vibrant, efficient brewing environment.
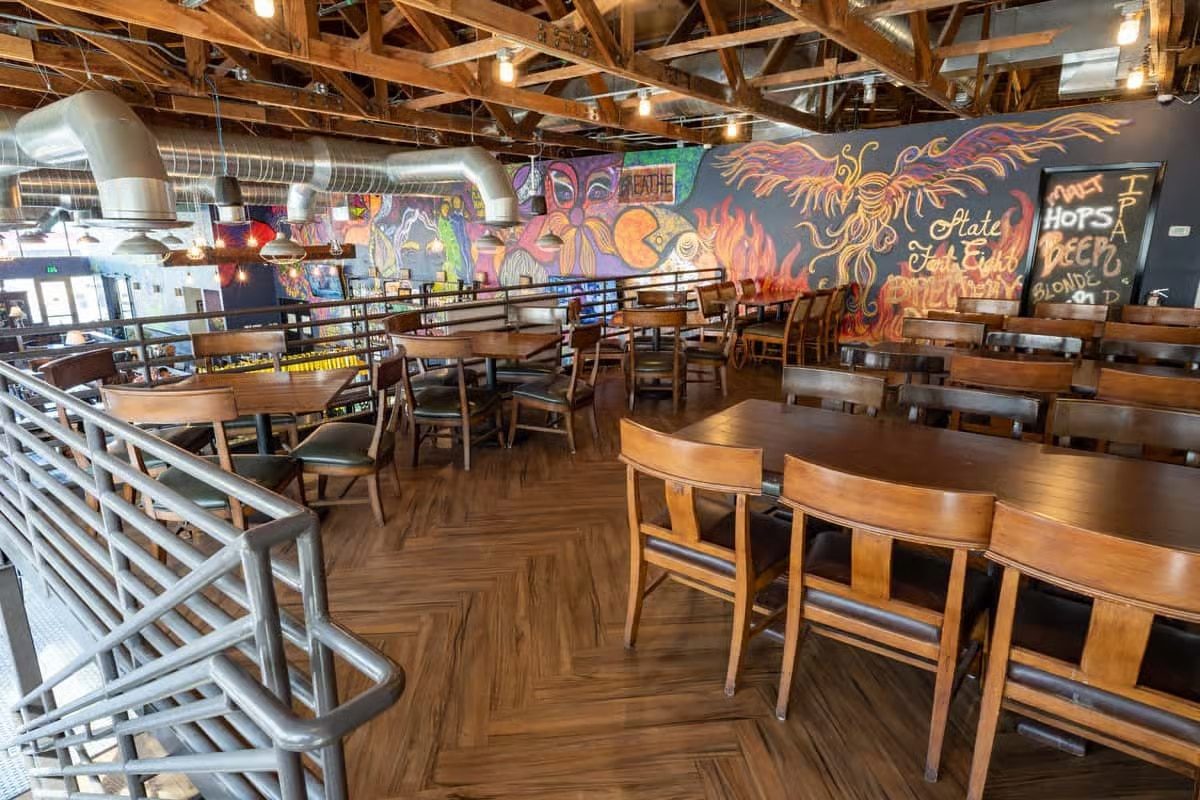
Safety first
Safety is paramount in brewery operations, with employees working with heavy machinery, pressure vessels, and potentially hazardous materials. Prioritizing safety in your brewery floor plan not only protects your employees, it also ensures compliance with regulatory standards and minimizes the risk of costly accidents or production disruptions. Here are key considerations for prioritizing safety in brewery floor plan development:
Mark path
Marked pathways and designated traffic areas are critical to preventing accidents and maintaining orderly movement within the brewery. Designate separate aisles for employees, equipment, and materials to minimize congestion and promote efficient workflow. Use floor markings, signage, and barriers to delineate aisles, loading zones, and restricted areas to ensure employees can move around the brewery safely and efficiently.
Ventilation and exhaust system
Install adequate ventilation and exhaust systems to remove smoke, dust, and air pollutants from the brewery environment. Proper ventilation helps maintain air quality, prevents the buildup of harmful gases, and reduces the risk of respiratory illnesses for brewery employees. Ensure ventilation systems are appropriately sized, regularly maintained, and equipped with appropriate filtration systems to mitigate health and safety risks associated with air contaminants.
Illumination
Provide adequate lighting in all work areas, storage areas, and walkways to ensure optimal visibility and prevent accidents. Use a combination of natural and artificial light sources to minimize shadows and reduce eye strain. Install shatterproof and waterproof light fixtures in areas prone to moisture or mechanical impact. Regularly inspect and maintain lighting systems to ensure consistent lighting and safe working conditions throughout the brewery.
Emergency Exit
Designate marked emergency exits and evacuation routes according to local building codes and safety regulations. Ensure emergency exits are easily accessible, clear of obstructions, and equipped with illuminated exit signs and emergency lighting. Conduct regular drills and training to familiarize brewery employees with emergency procedures and evacuation protocols. Always maintain clear access to emergency exits for quick evacuation in the event of an emergency.
Fire extinguishing system
Install appropriate fire suppression systems such as sprinklers, fire extinguishers, and fire alarm systems to prevent and mitigate the risk of fire in your brewery. Ensure fire suppression systems are installed in compliance with industry standards and regulatory requirements. Regularly inspect, test, and maintain fire suppression equipment to ensure proper operation and readiness in the event of a fire emergency. Train brewery employees on fire safety protocols, including fire prevention, detection, and evacuation procedures to minimize the risk of injury and property damage in the event of a fire.
By prioritizing safety in brewery floor plan design and implementation, breweries can create a safe and healthy work environment for employees while minimizing the risk of accidents, injuries, and code violations. Investing in safety measures such as marked pathways, ventilation systems, lighting, emergency exits, and fire suppression systems demonstrates a commitment to employee well-being and ensures the long-term success and sustainability of brewery operations.
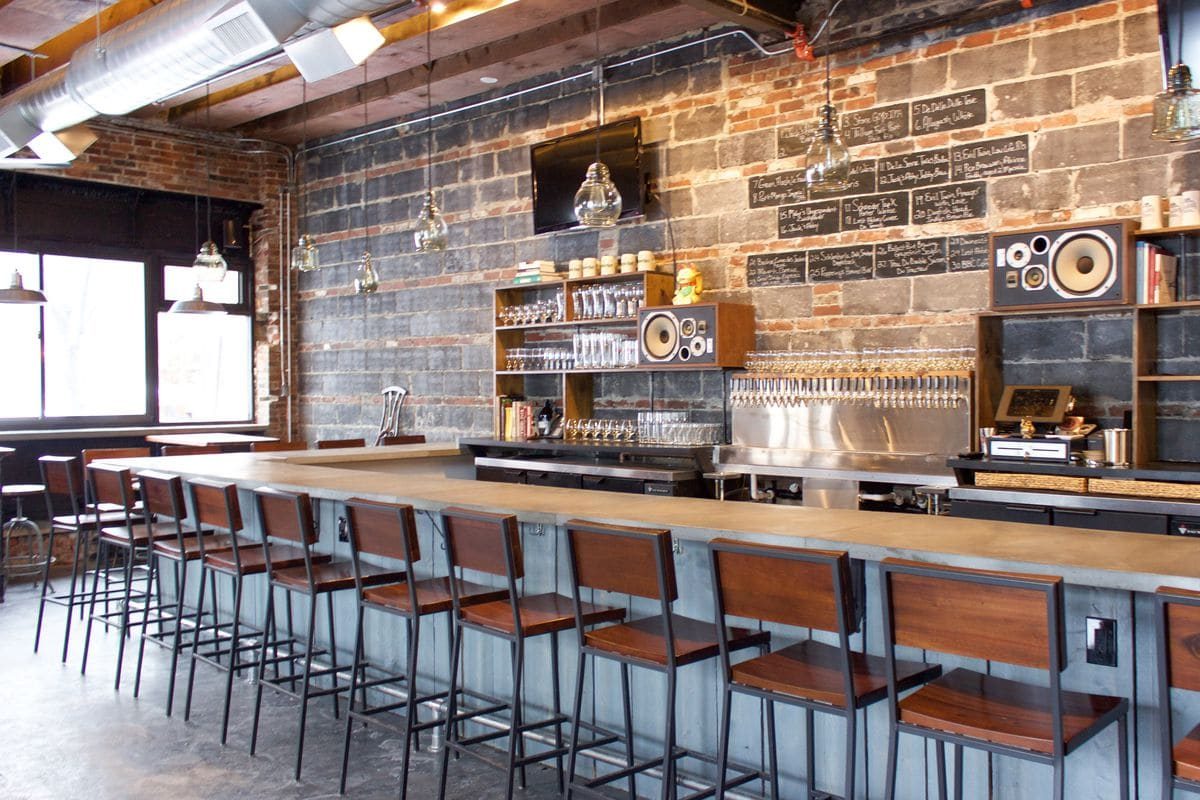
Consider ergonomics
Ergonomics plays a vital role in brewery operations as employees often perform repetitive tasks and use heavy equipment. By prioritizing ergonomics in brewery floor plan design, breweries can create a safer, more comfortable work environment that reduces the risk of injury and increases productivity. The following are key considerations for incorporating ergonomics into brewery floor plan development:
Optimal height and layout
Design workstations, equipment, and work surfaces to meet the ergonomic needs of brewery employees. Make sure brewing vessels, work surfaces, and storage racks are at optimal heights to reduce bending, reaching, and lifting. Consider the physical dimensions of your brewery employees when determining workstation height and layout to minimize strain and fatigue. Arrange equipment and workstations in a logical sequence to promote efficient workflow and minimize unnecessary movement.
Anti-slip floor
Choose flooring materials with adequate traction and slip resistance to prevent slips, trips, and falls in brewery work areas. Choose flooring materials with a textured surface or non-slip coating to provide grip in wet or greasy conditions. Install drainage systems and floor ramps to direct spills and liquids away from the work area and prevent standing water. Clean and maintain floor surfaces regularly to remove debris and ensure optimal slip resistance.
Ergonomic tools and equipment
Equip brewery employees with ergonomic tools and equipment designed to reduce stress and increase comfort during repetitive tasks. Choose tools with ergonomic handles, grips, and controls to minimize wrist, hand, and arm fatigue. Consider investing in ergonomic lifting aids, such as pallet jacks or lift tables, to assist with heavy lifting and material handling tasks. Provide adjustable seating options and anti-fatigue mats in work areas where employees may stand for long periods or perform repetitive tasks.
Incorporating ergonomic principles into the brewery floor plan demonstrates a commitment to employee well-being, safety, and productivity. By optimizing height and layout, choosing non-slip flooring, and investing in ergonomic tools and equipment, you can create a brewery environment that promotes employee health and efficiency, reduces the risk of workplace injuries, and increases overall job satisfaction and performance.
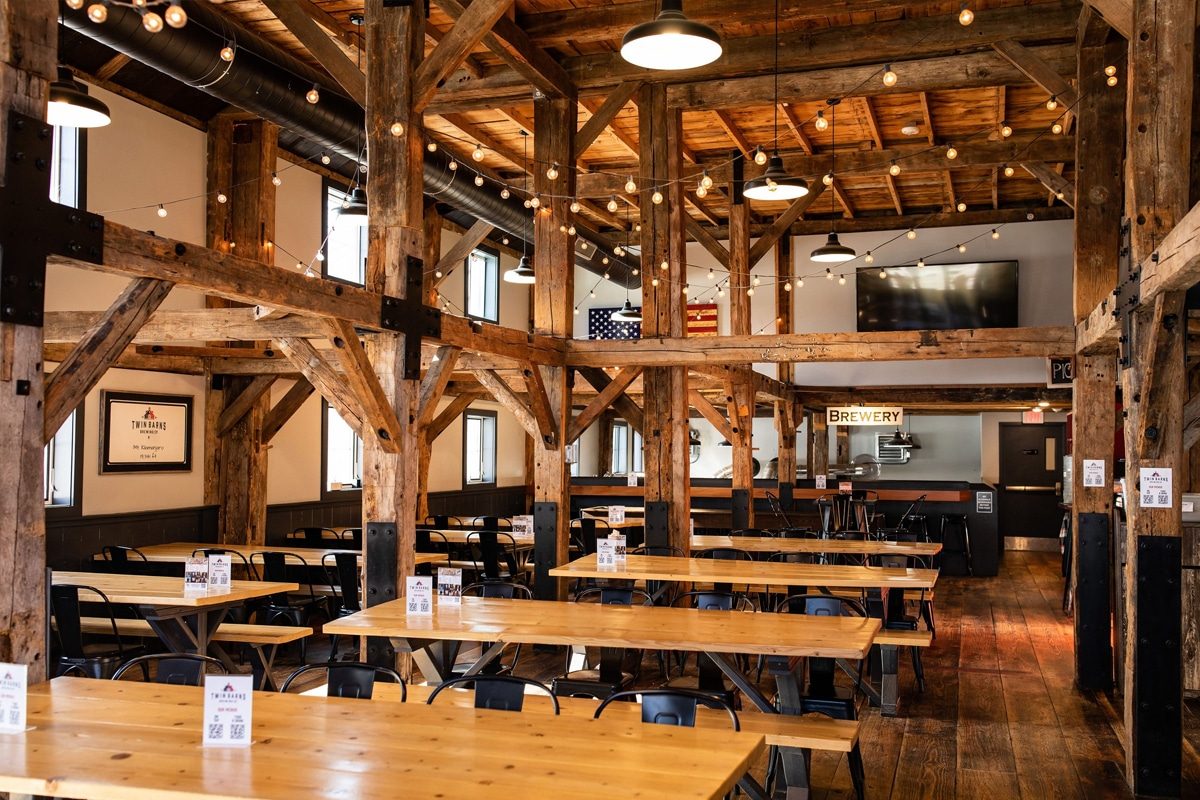
Plan for future growth and expansion
For breweries that want to thrive in the highly competitive craft beer market, anticipating future growth and expansion is critical. A well-designed brewery floor plan should be flexible and scalable, able to easily adapt to changing production needs, market trends, and business goals. Here are key considerations when planning for future growth and expansion in your brewery floor plan:
Scalable equipment and infrastructure
Invest in scalable brewery equipment and infrastructure that can accommodate future growth without major modifications or replacements. Choose from modular brewhouse equipment, scalable fermentation tanks, and flexible packaging lines for systems that can be easily upgraded or expanded as production needs increase. Scalable equipment allows breweries to adapt to changing market conditions and production requirements while minimizing capital expenditures and downtime.
Zoning and Permit Considerations
When planning future expansion, consider zoning regulations, building codes, and permitting requirements that may affect your brewery’s growth potential. Consult local authorities and zoning officials about land use restrictions, building height restrictions, parking requirements, and other regulatory considerations. By proactively addressing zoning and permitting issues, you can avoid potential roadblocks and speed up the expansion process when the time comes.
Financial planning and budgeting
Develop a comprehensive financial plan and budget for future growth and expansion plans. Consider factors such as equipment upgrades, facility renovations, staffing increases, marketing initiatives, and distribution expansion. Conduct regular financial assessments and cash flow forecasts to ensure brewery expansion projects are financially feasible and consistent with business goals. Explore financing options, grants, or investment opportunities to fund expansion projects and capitalize on market opportunities.
Collaboration and partnership opportunities
Explore collaboration and partnership opportunities with other breweries, suppliers, distributors, or industry stakeholders to facilitate brewery expansion. Co-brewing projects, contract brewing arrangements, or joint ventures can provide additional production capacity, distribution channels, and marketing support to accelerate brewery growth and market penetration. Collaborate with industry partners to leverage shared resources, expertise, and market coverage for mutual benefit.
Continuous improvement and adaptation
Embrace a culture of continuous improvement and adaptation within the brewery to stay ahead of industry trends, consumer preferences, and technological advancements. Regularly review and evaluate brewery operations, equipment performance, product quality, and customer feedback to identify areas for improvement and innovation. Invest in employee training, technology upgrades, and process optimization initiatives to increase efficiency, reduce costs, and maintain a competitive advantage in the dynamic craft beer market.
By incorporating these strategies for planning for future growth and expansion into your brewery floor plan, you can create a flexible and scalable brewing environment that can adapt to changing market conditions and business needs. By proactively addressing scalability, regulatory compliance, financial planning, collaboration opportunities, and continuous improvement, you can position your brewery for sustainable growth and long-term success in the dynamic craft beer industry.
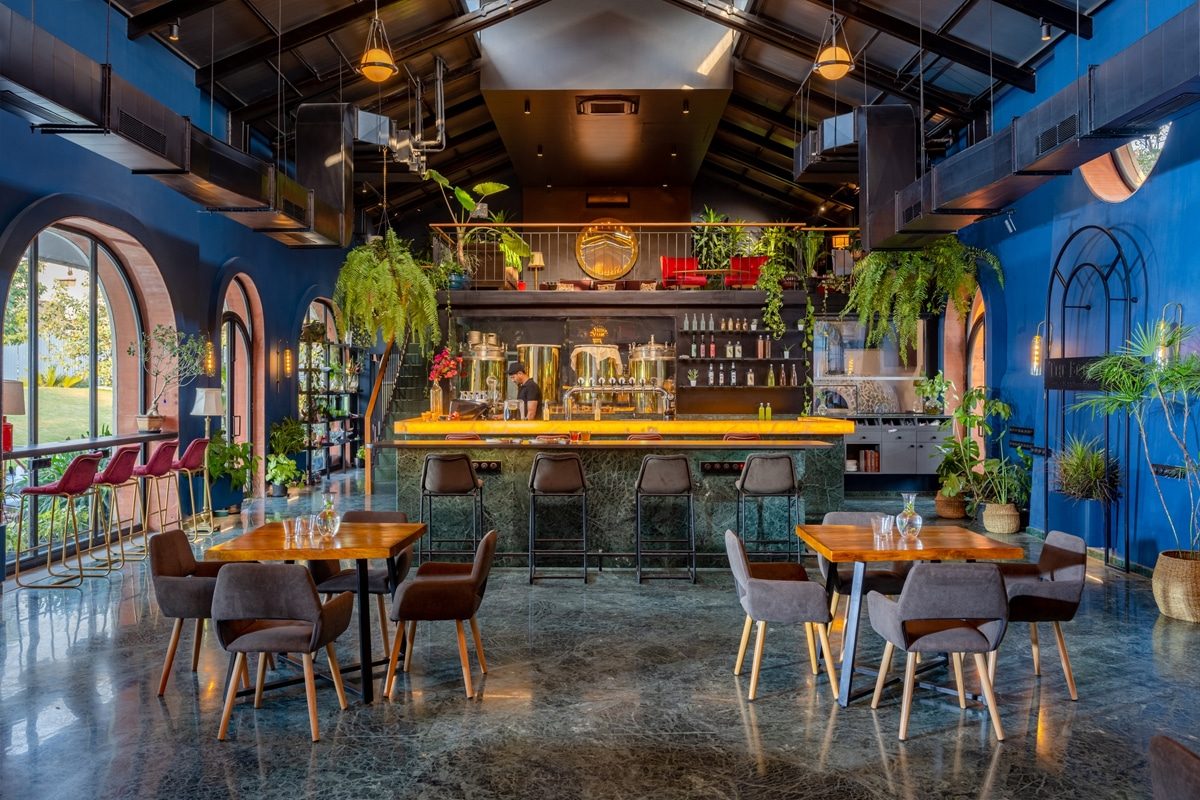
Seek professional guidance
Developing an optimal brewery floor plan is a complex and multifaceted process that requires expertise in brewery operations, facility design, regulatory compliance, and project management. While it can be tempting to handle the design and planning process independently, seeking professional guidance can provide valuable insight, reduce risk, and ensure the successful execution of your brewery floor plan. Here are the top reasons why you should consider hiring a professional to create a brewery floor plan:
Expertise and experience
Professional brewery consultants and architects bring expertise and years of experience. They understand the unique requirements of brewery operations and can provide valuable insights into efficient layout design, equipment selection, regulatory compliance, and industry best practices. By leveraging their knowledge and experience, breweries can avoid common pitfalls and make informed decisions, optimizing their floor plans for success.
Tailor-made solutions
Professional consultants work closely with breweries to understand their specific needs, goals, and constraints. They work with brewery owners and stakeholders to develop custom floor plans that fit their vision, budget, and operational requirements. Whether maximizing space utilization, ensuring ergonomics, or planning for future growth, professional consultants can customize solutions to meet each brewery’s unique needs.
Regulatory compliance
Complying with regulatory requirements and building codes can be a daunting task for brewery owners, especially those building their first facility. Professional consultants have in-depth knowledge of local regulations, zoning requirements, health and safety standards, and environmental considerations. They can guide breweries through the licensing process, ensure compliance with relevant regulations, and help obtain necessary approvals from regulatory agencies.
Project management and coordination
Managing a brewery floor plan development project involves coordinating various stakeholders, including architects, contractors, equipment suppliers, and regulatory agencies. Professional brewery consultants can oversee project management, ensuring seamless communication, timely execution, and quality control throughout the planning, design, and construction phases. Their project management expertise can help you stay on schedule and within budget while mitigating risks and proactively resolving issues.
Cost-effective solution
While professional guidance may require an upfront investment, it can lead to long-term cost savings by optimizing brewery design, minimizing operational inefficiencies, and preventing costly mistakes. Professional brewery consultants can help you identify cost-effective solutions, negotiate with suppliers, and prioritize investments to maximize return on investment (ROI) and ensure the financial sustainability of your brewery operations.
Seeking professional guidance in brewery floor plan development can provide you with the expertise, resources, and support you need to create a well-designed, efficient, and compliant brewery facility. Whether you’re an experienced brewer looking to expand or new to the craft beer industry, working with an experienced professional can help you navigate the complexities of a brewery floor plan and set you up for brewing success.
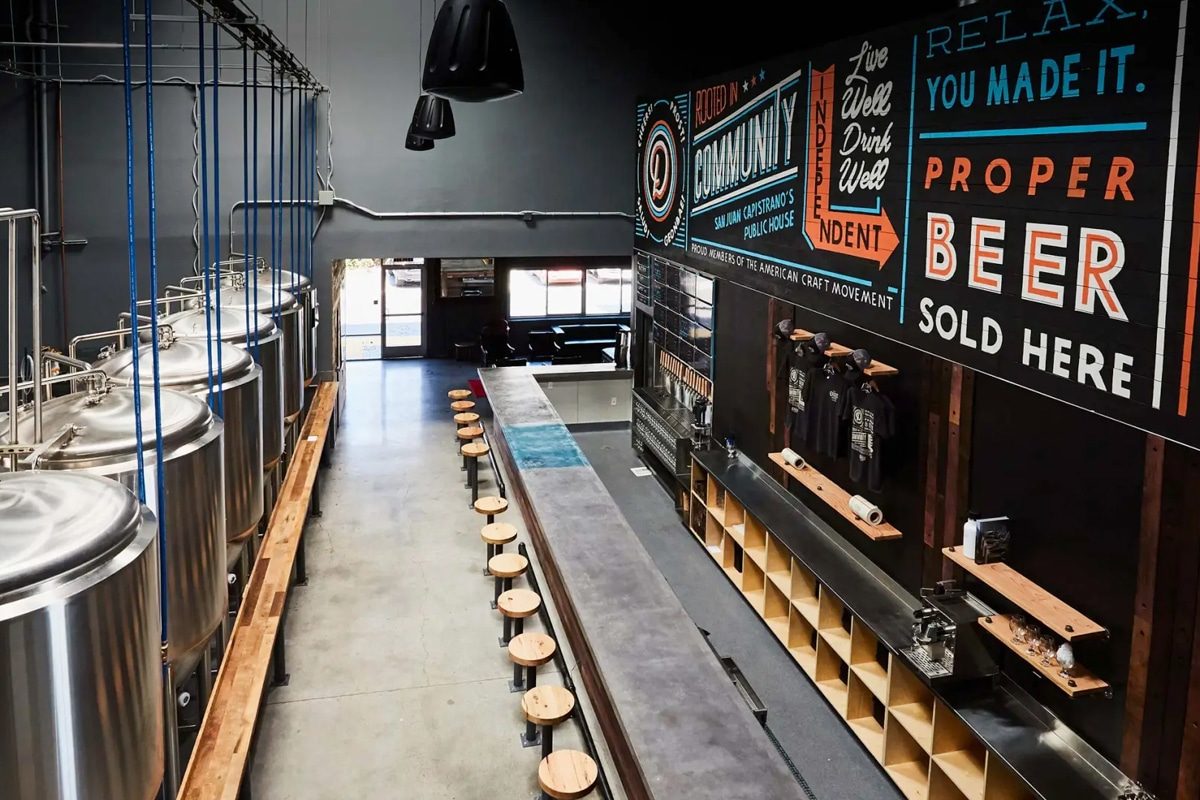
Summary
Developing the best brewery floor plan is a multifaceted process that requires careful consideration of various factors, including production capacity, workflow efficiency, space utilization, safety, and future growth. By following a systematic approach and incorporating key principles such as understanding brewery needs, designing for workflow efficiency, prioritizing safety and ergonomics, planning for future expansion, and seeking professional guidance, breweries can create floor plans that optimize operations, enhance productivity, and ensure long-term success. From assessing production requirements to implementing scalable equipment, considering ergonomics, and complying with regulatory standards, every aspect of brewery floor plan development contributes to the overall success and sustainability of the brewery operation. By prioritizing thoughtful planning and strategic decision-making, breweries can create floor plans that serve as the foundation for brewing excellence, innovation, and growth in the dynamic craft beer industry.
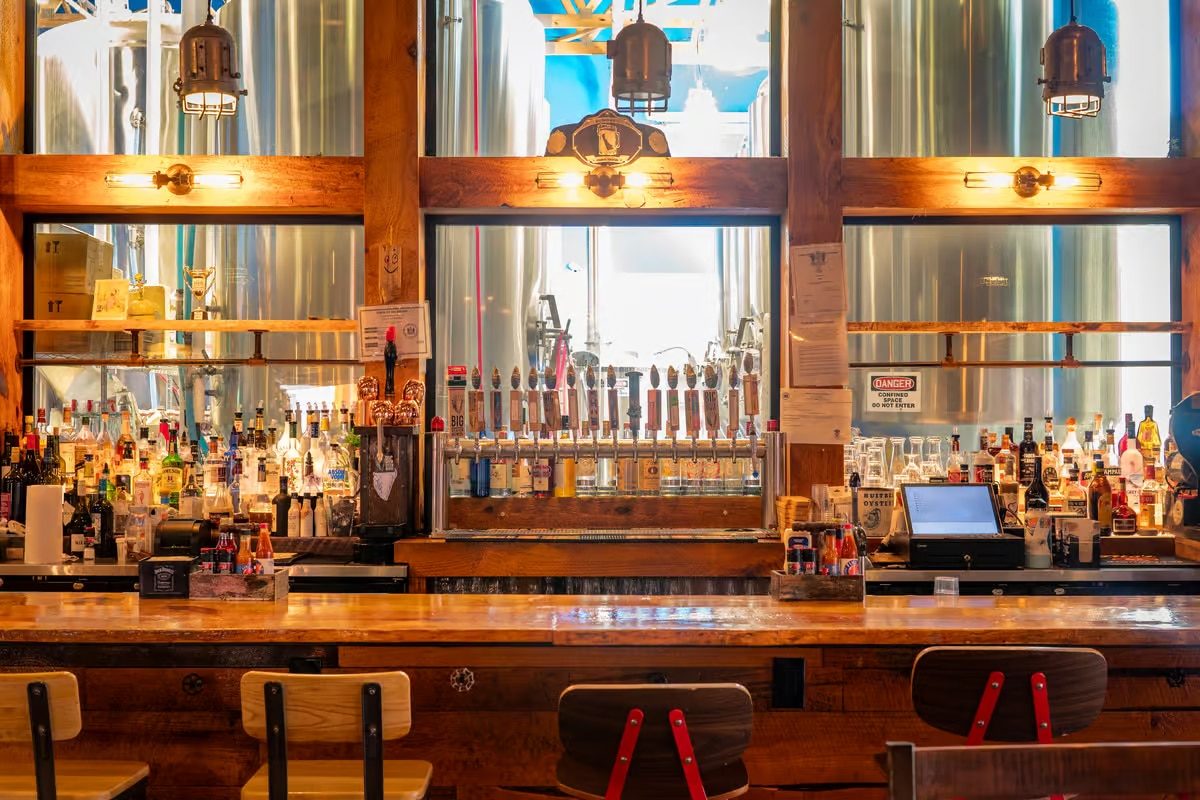
Get A Turnkey Brewery Solution
When it comes to developing the best brewery floor plan, partnering with a trusted industry expert can make all the difference. ZYB Craft specializes in providing comprehensive turnkey brewery solutions tailored to meet the unique needs and requirements of breweries of all sizes. With years of experience and a deep understanding of the craft beer industry, ZYB Craft offers end-to-end services that encompass everything from initial concept development and floor plan design to equipment procurement, installation, and ongoing support.
Choosing a turnkey brewery solution with ZYB Craft ensures seamless integration of all brewery components, optimized workflow efficiency, compliance with regulatory standards, and future-proof scalability. By entrusting your brewery project to ZYB Craft, you can rest assured knowing that you are partnering with a team of professionals committed to delivering excellence, innovation, and value at every stage of the brewery development process. Let ZYB Craft guide you in creating a brewery floor plan that sets the stage for brewing success and growth in the competitive craft beer market.