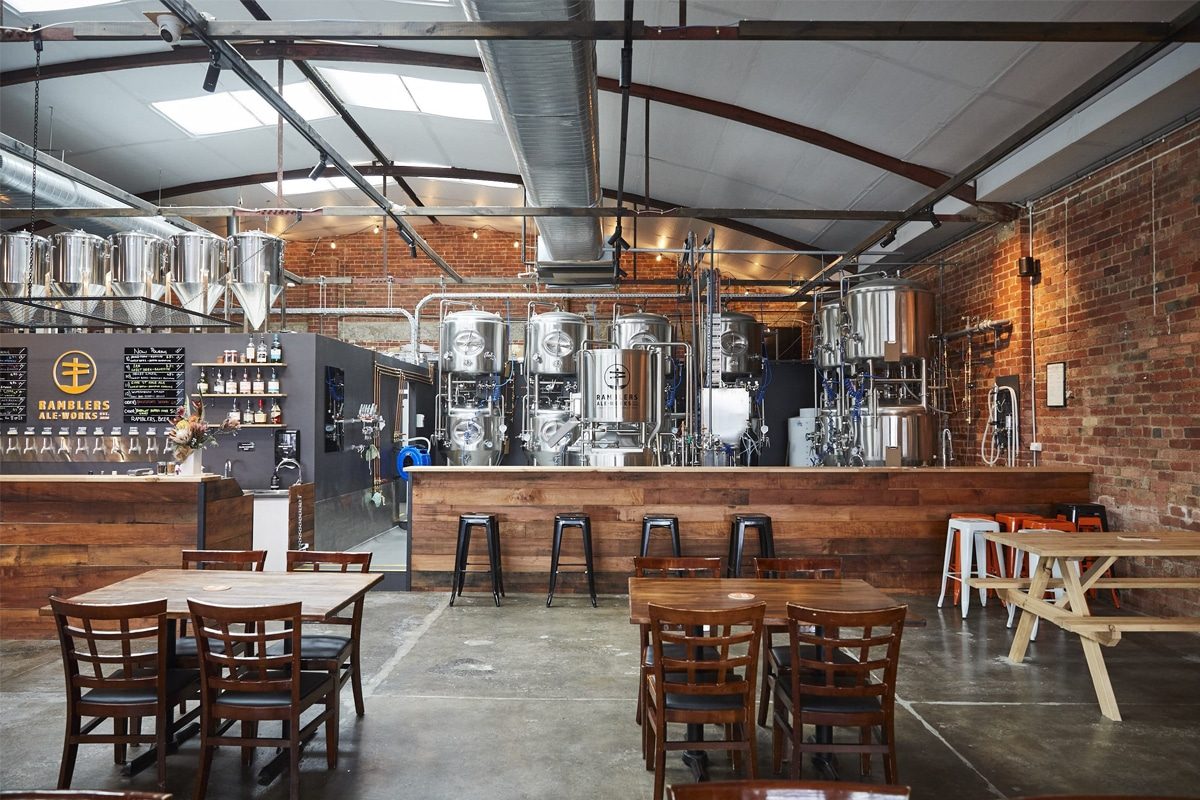
How Much Power Does A Brewery Need?
In the vibrant world of craft beer, where creativity flows as freely as the brews themselves, there’s a hidden force at work: power. Behind every crisp pint and bold flavor profile lies a symphony of machinery, all powered by the relentless demand for energy. From mashing to fermentation, the journey of beer from grain to glass is a power-hungry odyssey, with each step requiring its share of electricity or other forms of energy.
In this article, we embark on a journey to unravel the intricate web of power consumption within breweries. We’ll explore the various stages of the brewing process, dissect the factors influencing energy needs, and examine the challenges and solutions shaping the industry’s quest for sustainability. From small craft breweries to large-scale operations, understanding the power requirements of breweries is not just a matter of operational efficiency, it’s a cornerstone of sustainable brewing practices in an increasingly energy-conscious world.
Complete Guide

Learn About The Brewing Process
Brewing beer is a meticulous process that seamlessly blends art and science, requiring precise control at every stage to achieve the desired flavor, aroma, and texture. Let’s delve into the intricacies of the beer brewing process and explore how motivation plays an important role in the life of beer.
Milling
The journey begins with milling, breaking up the malted grains to expose their starchy interior. The process involves passing grain through a mill, usually powered by electricity or mechanical means. While grinding itself may not be the most energy-intensive step, it sets the stage for efficient starch extraction during mashing.
Mashing
After milling, the grains are mixed with hot water in a vessel called a mash tun. Here, naturally occurring enzymes in the grain break down complex starches into fermentable sugars, producing a sweet liquid called wort. Mashing requires precise temperature control, often achieved through electric or gas heating elements. Energy requirements during mashing depend on factors such as water volume, target temperature, and heating system efficiency.
Boiling
After mashing, the wort is transferred to a boiling pot where it is boiled. Boiling serves several important purposes, including sterilization, hop extraction, and flavor concentration. Maintaining a rolling boil for an extended period requires significant energy input, usually from a gas burner or an electric heating element. Energy requirements during boiling vary depending on factors such as batch size, required boiling duration, and environmental conditions.
Cooling
After boiling, the hot wort must be cooled quickly to prevent off-flavors and prepare it for fermentation. Cooling can be achieved using various methods, including immersion coolers, plate heat exchangers, or glycol jackets. Each method requires energy to operate efficiently, and larger breweries often employ more complex and energy-intensive cooling systems.
Fermentation
After the wort has cooled, it is transferred to a fermentation vessel where yeast is added to begin fermentation. During fermentation, yeast converts the fermentable sugars in the wort into alcohol and carbon dioxide, producing beer. Maintaining optimal fermentation temperatures helps maintain yeast health and flavor development. Many breweries use refrigeration or glycol cooling systems to control fermentation temperatures, increasing overall energy requirements.
Conditioning
After fermentation, some beer styles may be conditioned or aged to develop complexity and smooth flavor. Conditioning usually occurs in specialized tanks or barrels, where the beer is left to rest for some time under controlled conditions. While the conditioning itself does not consume large amounts of power, maintaining stable temperature and environmental conditions may require energy input, especially in large-scale operations.
Packaging
The final stage of the brewing process is packaging the finished beer into bottles, cans, or kegs for distribution and consumption. Packaging lines consist of a variety of machinery, including filling machines, capping machines, labelers, and packaging conveyors, all of which require electricity to operate efficiently. Additionally, refrigeration may be required to maintain the quality and freshness of packaged beer before it reaches the consumer.
The brewing process is an energy-intensive process spanning multiple stages, each requiring its share of energy input to achieve the desired results. From grinding to packaging, electricity plays a vital role in shaping the flavor, aroma, and quality of the beers we love. Understanding the power requirements at each stage helps breweries operate efficiently and sustainably in an increasingly energy-conscious world.
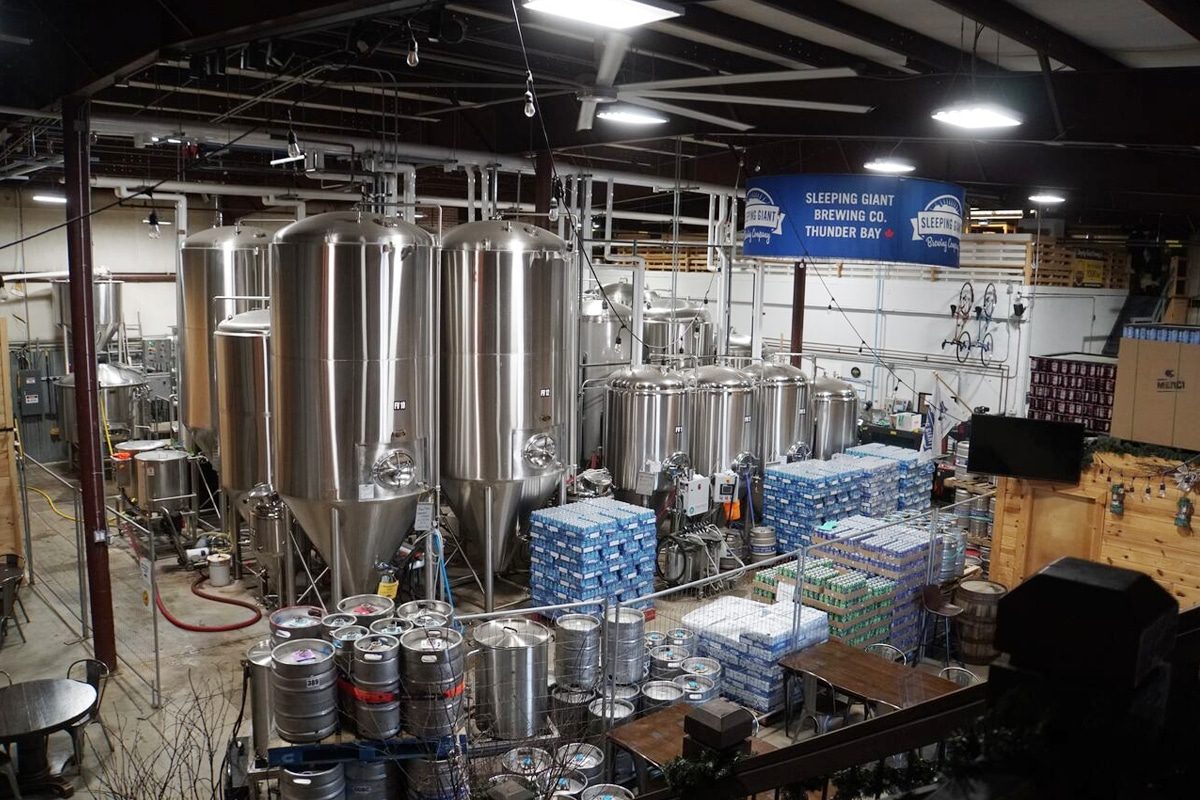
Factors Affecting Power Consumption
A brewery’s power needs are affected by a variety of factors, from size and scale to equipment efficiency and the use of renewable energy. Understanding these factors can help breweries effectively manage energy consumption and operate sustainably. Let’s examine each factor in detail:
Brewery Size And Scale
The size and scale of a brewery play an important role in determining its energy consumption. Larger breweries with higher production volumes naturally require more energy to run their equipment and facilities. Conversely, small craft breweries may have lower overall energy needs but may face challenges in optimizing efficiency due to smaller batch sizes and limited resources. Operation size is directly related to power requirements, as larger breweries typically use more equipment and resources, resulting in higher energy consumption.
Equipment Efficiency
The efficiency of brewing equipment directly affects energy consumption. Modern brewing equipment often features energy-efficient designs and technologies designed to minimize energy use without compromising quality. Over time, upgrading to newer, more efficient equipment can result in significant energy savings. Energy-efficient boilers, heat exchangers, pumps, and refrigeration systems are examples of equipment that can help reduce brewery energy consumption.
Process Optimization
Fine-tuning the brewing process can save significant amounts of energy without compromising product quality. Optimization strategies such as optimizing mash plans to reduce heating time, implementing heat recovery systems to capture and reuse waste heat, and optimizing fermentation plans to reduce energy consumption are effective ways to minimize electricity usage without sacrificing product quality. By continually evaluating and improving their brewing processes, breweries can identify energy-saving opportunities and improve overall efficiency.
Temperature Control System
Temperature control is critical at all stages of the brewing process, especially during mashing, boiling, fermentation, and conditioning. Breweries often rely on temperature control systems, such as refrigeration or glycol cooling systems, to maintain precise temperatures and control fermentation dynamics. The type and efficiency of the temperature control system used can significantly affect power consumption. Investing in energy-efficient temperature control systems and implementing smart temperature management strategies can help breweries reduce energy use while ensuring consistent product quality.
Renewable Energy Grid Integration
Many breweries are turning to renewable energy sources such as solar, wind, or biomass to offset electricity consumption and reduce environmental impact. Installing solar panels on brewery roofs, using wind turbines on brewery grounds, or investing in biogas digesters for organic waste management are all examples of renewable energy integration initiatives. By generating clean energy on-site, breweries can not only reduce their reliance on the grid but also reduce operating costs and improve their sustainability credentials.
Factors such as the size and scale of the brewery, equipment efficiency, process optimization, temperature control systems, renewable energy integration, etc. all play a vital role in the energy consumption of the brewery. By prioritizing energy efficiency and sustainability initiatives, breweries can minimize their environmental footprint, reduce operating costs, and contribute to the sustainability of the beer industry.
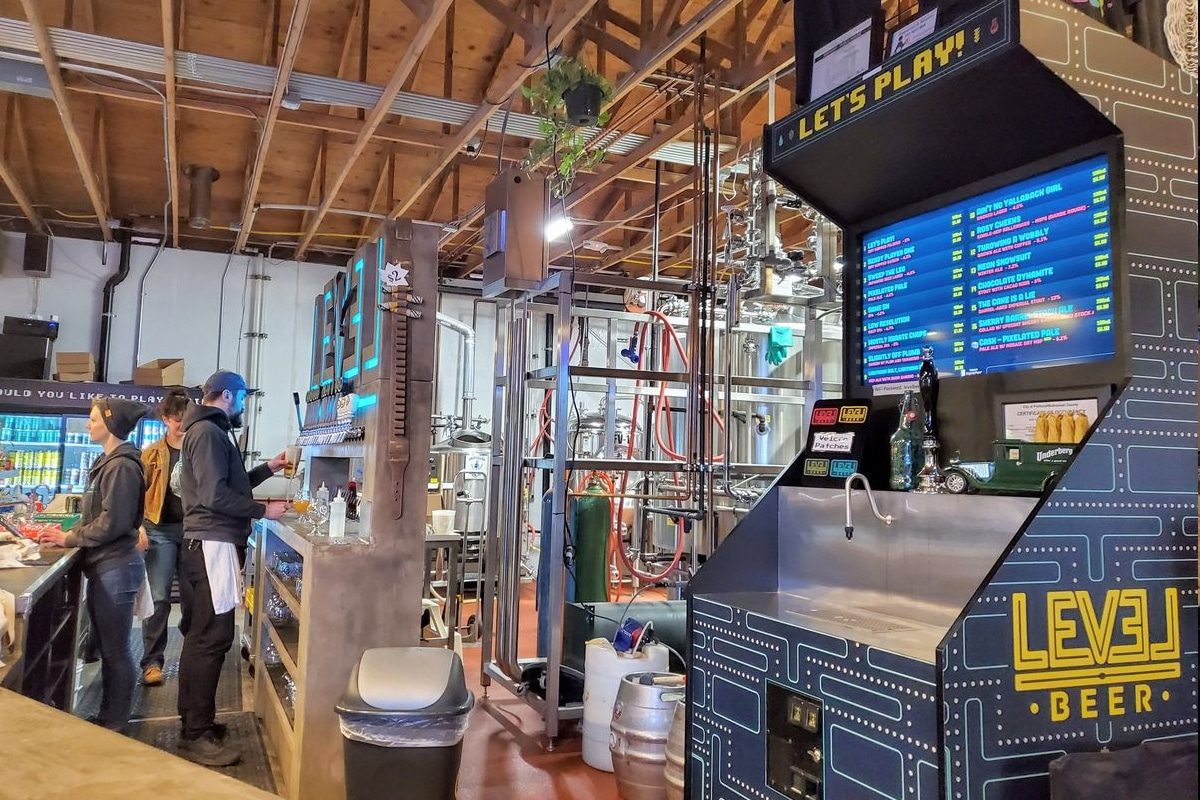
Challenges And Solutions
Navigating the complexities of power consumption in breweries comes with its fair share of challenges. From financial considerations to regulatory hurdles and cultural shifts, breweries must address these challenges head-on to optimize energy usage and operate sustainably. Here are some of the key challenges and potential solutions:
Cost Considerations
- Challenges: One of the primary challenges breweries face in optimizing energy consumption is the upfront cost associated with implementing energy-efficient equipment or renewable energy systems. Investing in new technologies or upgrading existing infrastructure can require significant capital expenditure, which may be prohibitive for smaller breweries or those operating on tight budgets. However, while the initial investment may seem daunting, it’s essential to consider the long-term benefits. Energy-efficient equipment and renewable energy systems can lead to substantial savings in operational costs over time, offsetting the initial investment and enhancing the brewery’s financial sustainability.
- Solutions: Breweries can explore various financing options, such as equipment leasing or financing programs, to spread out the cost of investments in energy-efficient technologies. Additionally, leveraging available incentives, grants, or rebates for energy efficiency upgrades can help offset upfront expenses and make sustainable investments more financially viable.
Regulatory Compliance
- Challenges: Breweries must adhere to various regulations related to energy usage, emissions, and environmental impact. Meeting regulatory requirements while optimizing energy efficiency can be challenging, particularly for smaller breweries with limited resources or expertise in regulatory compliance. Failure to comply with regulations can result in fines, penalties, or reputational damage, underscoring the importance of staying abreast of evolving regulatory frameworks.
- Solutions: Breweries can partner with energy consultants or industry experts to navigate regulatory requirements effectively and ensure compliance. Implementing robust monitoring and reporting systems can help breweries track energy usage, identify areas for improvement, and demonstrate compliance with regulatory standards. Engaging with industry associations or participating in sustainability initiatives can also provide valuable guidance and resources for navigating regulatory challenges.
Education And Awareness
- Challenges: Building awareness among brewery staff about energy conservation practices and fostering a culture of sustainability within the organization is essential for driving energy-saving initiatives forward. However, implementing behavioral changes and fostering a culture of sustainability may require overcoming resistance or apathy among employees.
- Solutions: Providing comprehensive training programs, workshops, or seminars on energy conservation and sustainability can empower brewery staff to identify opportunities for improvement and contribute to energy-saving efforts. Establishing clear goals, targets, and incentives for energy efficiency can also motivate employees to adopt sustainable practices and drive continuous improvement. Additionally, incorporating sustainability principles into the brewery’s mission, values, and corporate culture can foster a sense of ownership and responsibility among staff, encouraging active participation in energy-saving initiatives.
While challenges such as cost considerations, regulatory compliance, and cultural barriers can pose significant obstacles to optimizing energy consumption in breweries, proactive measures and strategic solutions can help overcome these challenges and pave the way for sustainable growth in the beer industry the way. By addressing these challenges head-on and embracing a culture of innovation and sustainability, breweries can improve operational efficiency, reduce their environmental impact, and position themselves as global leaders in the fight against climate change.
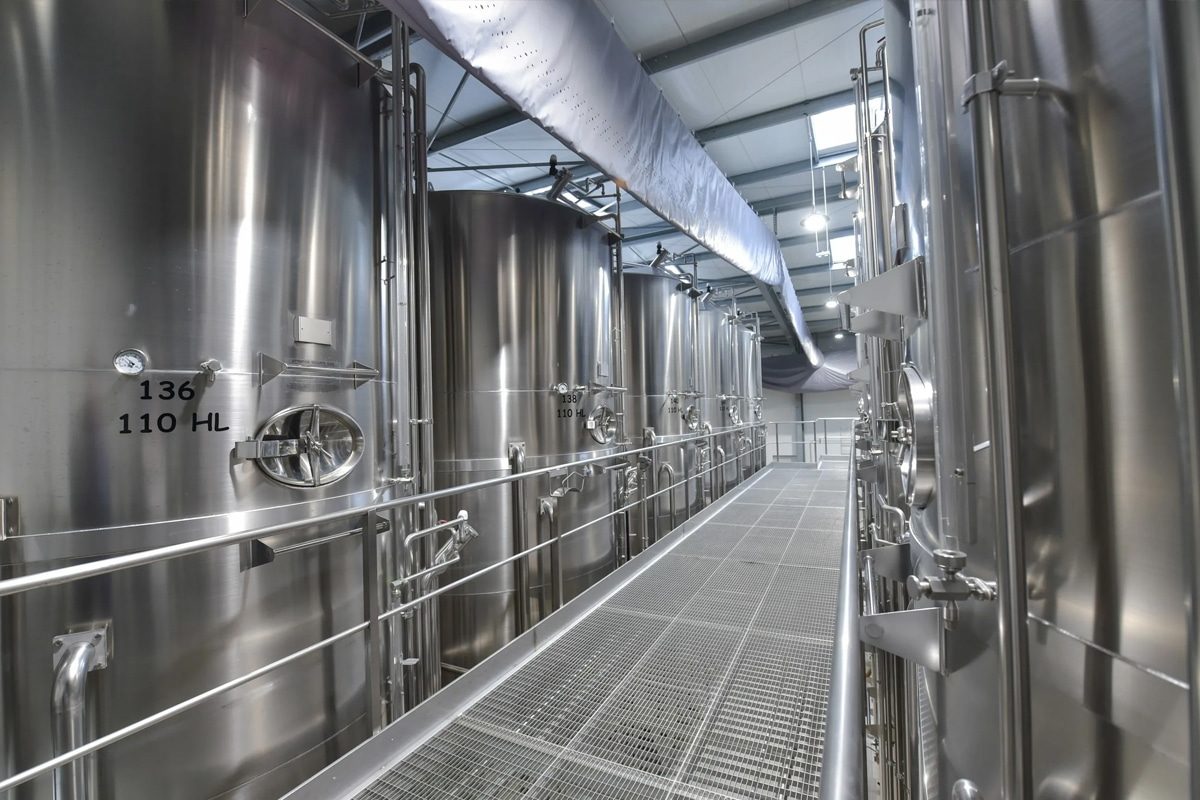
Summarize
The power requirements of a brewery are influenced by a multitude of factors, including brewery size and scale, equipment efficiency, process optimization, temperature control systems, and renewable energy integration. Understanding and managing these factors helps breweries operate efficiently and sustainably in an increasingly energy-conscious world.
From milling to packaging, every stage of the brewing process demands its share of energy inputs, making power management a critical aspect of brewery operations. By investing in energy-efficient equipment, optimizing processes, and integrating renewable energy sources, breweries can minimize their environmental footprint, reduce operating costs, and enhance their sustainability credentials.
Despite the challenges of cost considerations, regulatory compliance, and fostering a culture of sustainability, breweries have ample opportunities to implement innovative solutions and drive positive change within the industry. By prioritizing energy efficiency and environmental stewardship, breweries can continue to produce high-quality beer while minimizing their impact on the planet.
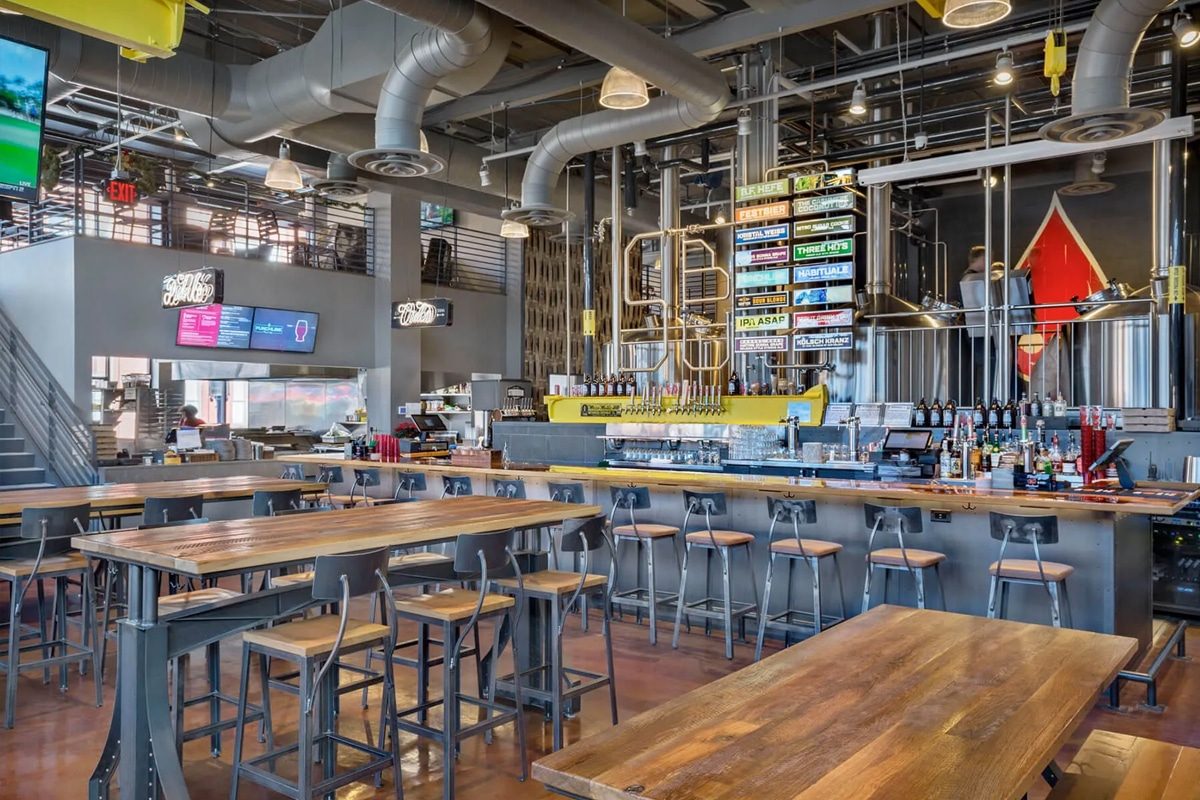
Get A Turnkey Brewery Solution
Navigating the complexities of power requirements in breweries can be daunting, but with ZYB Craft, breweries can streamline their operations and optimize energy usage effortlessly. As a professional brewery solution provider, ZYB Craft offers turnkey solutions tailored to meet the unique needs of each brewery, regardless of size or scale.
With ZYB Craft’s expertise in brewery design, equipment selection, and process optimization, breweries can maximize energy efficiency while minimizing costs. From energy-efficient brewing equipment to innovative temperature control systems and renewable energy integration, ZYB Craft provides comprehensive solutions to help breweries reduce their environmental footprint and achieve long-term sustainability goals.
By partnering with ZYB Craft, breweries gain access to a team of experts dedicated to delivering top-quality solutions that prioritize efficiency, sustainability, and profitability. With ZYB Craft as your brewery solution provider, you can rest assured knowing that your brewery is equipped to meet its power needs effectively and responsibly.