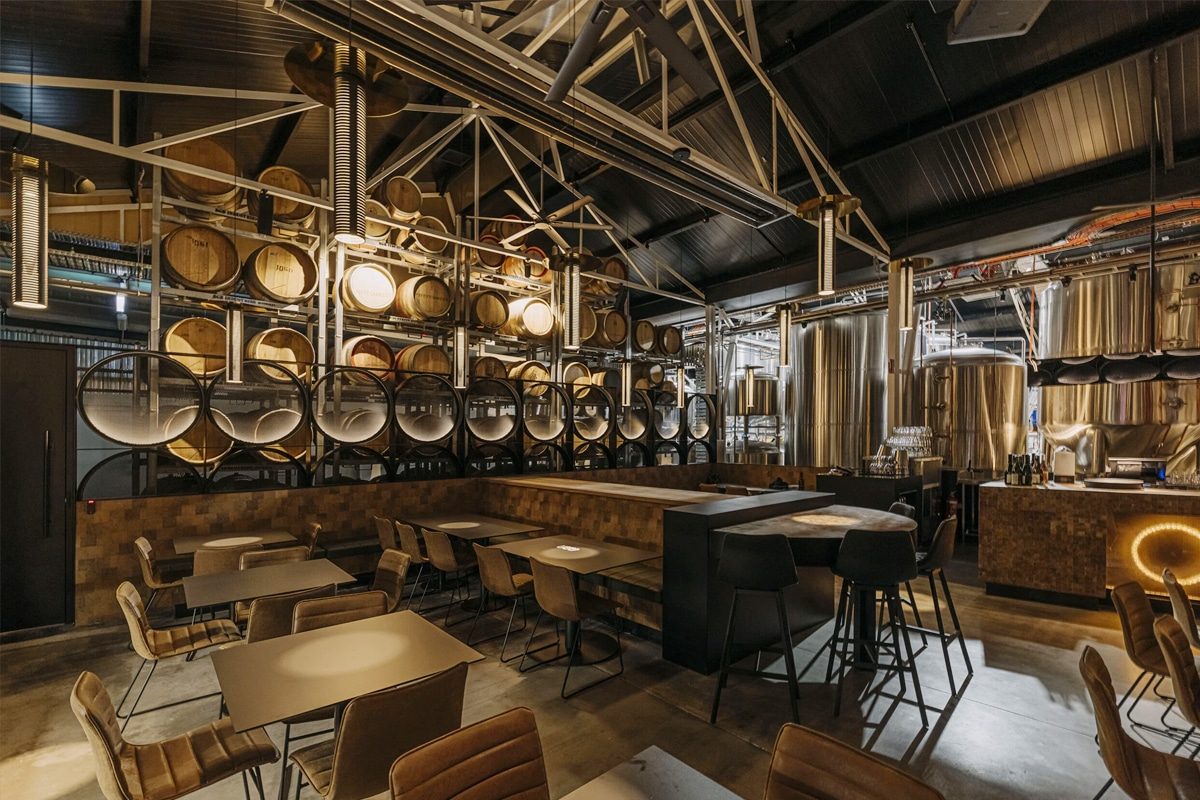
How Does The Layout of Brewery Equipment Affect Workflow And Efficiency?
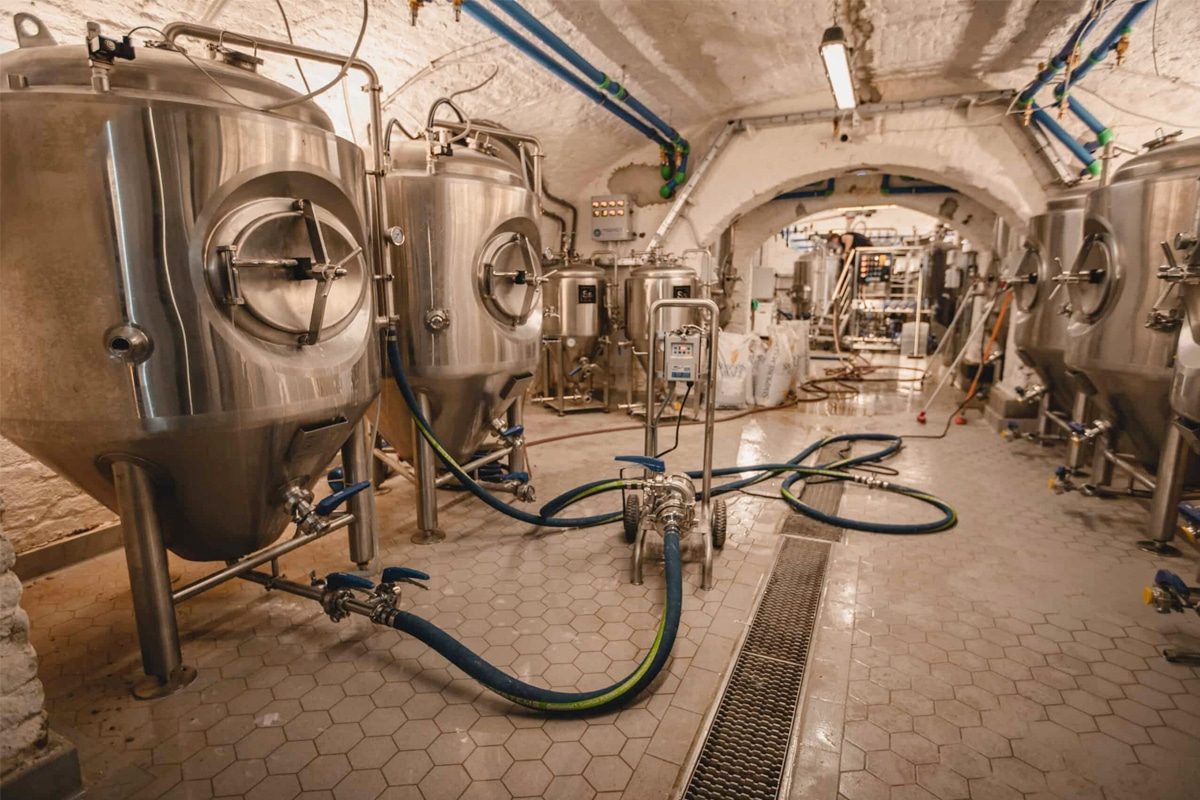
Importance of Brewery Layout
Space Utilization
Efficient use of space is a fundamental aspect of brewery layout. Breweries, whether small or large, must maximize their available space to ensure smooth operations and prevent congestion.
- Compactness VSAccessibility: Especially in small craft breweries, a compact layout is essential to make the most of limited space. However, equipment must remain accessible for cleaning, maintenance, and operation. Striking a balance between compactness and accessibility helps prevent operational inefficiencies and safety hazards.
- Vertical Space: Utilizing vertical space can significantly enhance space efficiency. Stacking fermentation tanks, placing equipment on elevated platforms, and using mezzanine levels for auxiliary processes can free up valuable floor space.
- Flexibility: A flexible layout that allows for easy reconfiguration can accommodate changes in production scale and process modifications. Modular designs that enable easy addition or removal of equipment can be particularly beneficial.
Process Flow
Seamless process flows enable efficient brewery operations. The layout should facilitate a logical and efficient progression of brewing activities from raw material intake to packaging.
- Linear Flow: Ideally, the process flow should be linear, with materials moving in a straight path through the different stages of production. This minimizes backtracking and cross-contamination, ensuring a smooth transition between each step.
- Logical Sequencing: Equipment should be arranged in the order of the brewing process. For example, raw materials should be stored near the brewhouse, wort should move directly from the brewhouse to fermentation tanks, and finished beer should flow easily from the conditioning tanks to the packaging area.
- Minimized Movement: Reducing the distance that materials and personnel need to travel between stages can significantly enhance efficiency. Well-placed conveyors, pumps, and pipelines can streamline the movement of liquids and raw materials.
Ergonomics
Ergonomics focuses on designing the workspace to fit the needs and capabilities of workers, minimizing physical strain and enhancing productivity.
- Equipment Height and Placement: Equipment should be positioned at heights that minimize bending, stretching, and lifting. Controls and monitoring devices should be within easy reach, reducing the need for awkward postures.
- Workstation Design: Workstations should be designed to support comfortable and efficient working positions. Adjustable work surfaces and seating can accommodate different tasks and worker preferences.
- Movement Efficiency: The layout should minimize unnecessary movements by placing frequently used tools, ingredients, and equipment close to the points of use. Reducing walking distances and repetitive motions can prevent fatigue and increase productivity.
Safety Considerations
Safety is paramount in brewery design, given the potential hazards associated with brewing operations, such as hot liquids, heavy machinery, chemicals, and pressurized systems.
- Clear Pathways: Pathways should be wide and unobstructed to allow safe movement of personnel and materials. Marked walkways and emergency exits enhance safety and facilitate quick evacuation in case of emergencies.
- Ventilation and Cleanliness: Proper ventilation can help control heat, humidity, and air pollutants. The layout should also facilitate easy cleaning and maintenance to ensure a hygienic environment, preventing contamination and ensuring product quality.
- Safety Equipment Accessibility: Safety equipment such as fire extinguishers, eye wash stations, and first aid kits should be easily accessible and strategically placed throughout the brewery. Safety signage should be visible and informative.
- Hazardous Material Management: Areas where hazardous materials are stored or used should be delineated and equipped with appropriate containment and ventilation systems to prevent accidents and exposure.
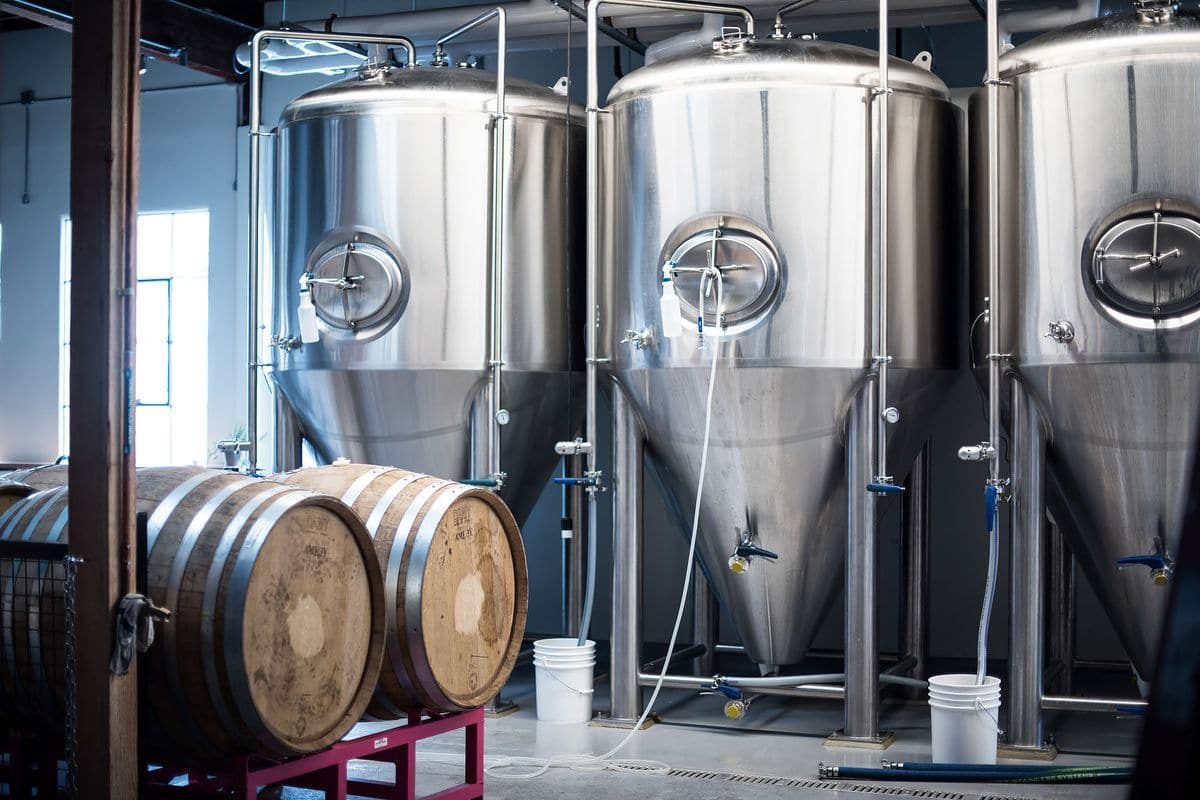
Key Areas of a Brewery and Their Layout Considerations
Raw Material Storage
Raw material storage is the starting point of the brewing process, where ingredients such as malt, hops, yeast, and adjuncts are stored until needed.
- Proximity to Brewhouse: Raw materials should be stored close to the brewhouse to minimize the distance they need to be transported, reducing the time and labor involved in moving ingredients.
- Climate Control: Proper temperature and humidity control helps maintain the quality of raw materials. For instance, malt should be kept dry to prevent mold growth, while hops may require refrigeration to maintain their freshness.
- Organized Storage: Ingredients should be organized in a manner that allows for easy access and inventory management. Shelving systems, bins, and labeled containers can help keep materials organized and readily available.
- Safety Measures: Storage areas should be equipped with safety measures such as spill containment for liquid adjuncts and proper ventilation to prevent dust accumulation from malt handling.
Brewhouse
The brewhouse is the heart of the brewery, where the initial stages of brewing—mashing, lautering, boiling, and whirlpooling—occur.
- Tank Arrangement: The arrangement of tanks should allow for an efficient flow of wort from one vessel to the next. Typically, this means placing the mash tun, lauter tun, brew kettle, and whirlpool nearby in a linear or circular pattern.
- Centralized Control Panels: Control panels should be centrally located and within easy reach of operators to monitor and adjust the brewing process effectively. This can streamline operations and reduce the need for operators to move frequently between different equipment.
- Accessibility: Equipment should be arranged to allow easy access for cleaning, maintenance, and ingredient addition. Platforms and walkways may be necessary to access the tops of tanks and other elevated equipment.
- Ventilation: Proper ventilation is crucial in the brewhouse to control heat and humidity generated during the brewing process. Exhaust fans and ductwork should be strategically placed to maintain a comfortable working environment.
Fermentation and Conditioning
Fermentation and conditioning are critical stages where the wort is transformed into beer, requiring precise temperature control and careful handling.
- Temperature Zones: Fermentation tanks and bright tanks should be grouped into zones based on their temperature requirements. This allows for more efficient cooling and temperature management.
- Access for Sampling and Maintenance: Tanks should be spaced adequately to allow for easy access for sampling, cleaning, and maintenance. Walkways and platforms may be necessary for accessing the tops and sides of tanks.
- Contamination Control: The layout should minimize the risk of contamination by ensuring that clean and sanitized areas are separated from areas where raw or unprocessed materials are handled.
- Safety Features: Safety features such as pressure release valves, proper ventilation, and secure tank racks can prevent accidents during fermentation and conditioning.
Packaging
The packaging area is where the finished beer is bottled, canned, or kegged. Efficient packaging operations can maintain product quality and meet production schedules.
- Flow of Materials: The packaging line should be arranged to allow for a smooth flow of materials from empty containers to filled, sealed, and labeled products. Conveyors and automated systems can help streamline this process.
- Quality Control: Designated areas for quality control checks should be integrated into the packaging line. This includes spaces for sampling, testing, and inspecting packaged products to ensure they meet quality standards.
- Storage of Packaging Materials: Adequate storage space for packaging materials such as bottles, cans, labels, and boxes should be provided. These materials should be easily accessible to the packaging line to avoid delays.
- Waste Management: Efficient waste management systems should be in place to handle packaging waste such as defective containers, labels, and excess materials. Recycling and disposal systems should be easily accessible from the packaging area.
Storage and Distribution
Once packaged, the beer needs to be stored before distribution. Efficient storage and distribution are crucial for maintaining product quality and meeting delivery schedules.
- Cold Storage: Finished beer often requires cold storage to maintain its quality and extend shelf life. Cold storage areas should be well-insulated and located close to the packaging line to minimize the distance the beer needs to be moved.
- Organized Inventory: An organized inventory system manages stock levels and ensures that products are easily distributed. This includes using shelving, pallet racks, and inventory management software.
- Loading Docks: The layout should include loading docks that are easily accessible for delivery vehicles. This minimizes the distance finished products need to be transported for shipping and facilitates efficient loading and unloading.
- FIFO (First In, First Out): Implementing a FIFO system ensures that older stock is distributed first, reducing the risk of product spoilage and maintaining freshness.
- Safety and Security: Storage areas should be secure and equipped with safety measures to prevent theft, damage, or contamination of the finished products.
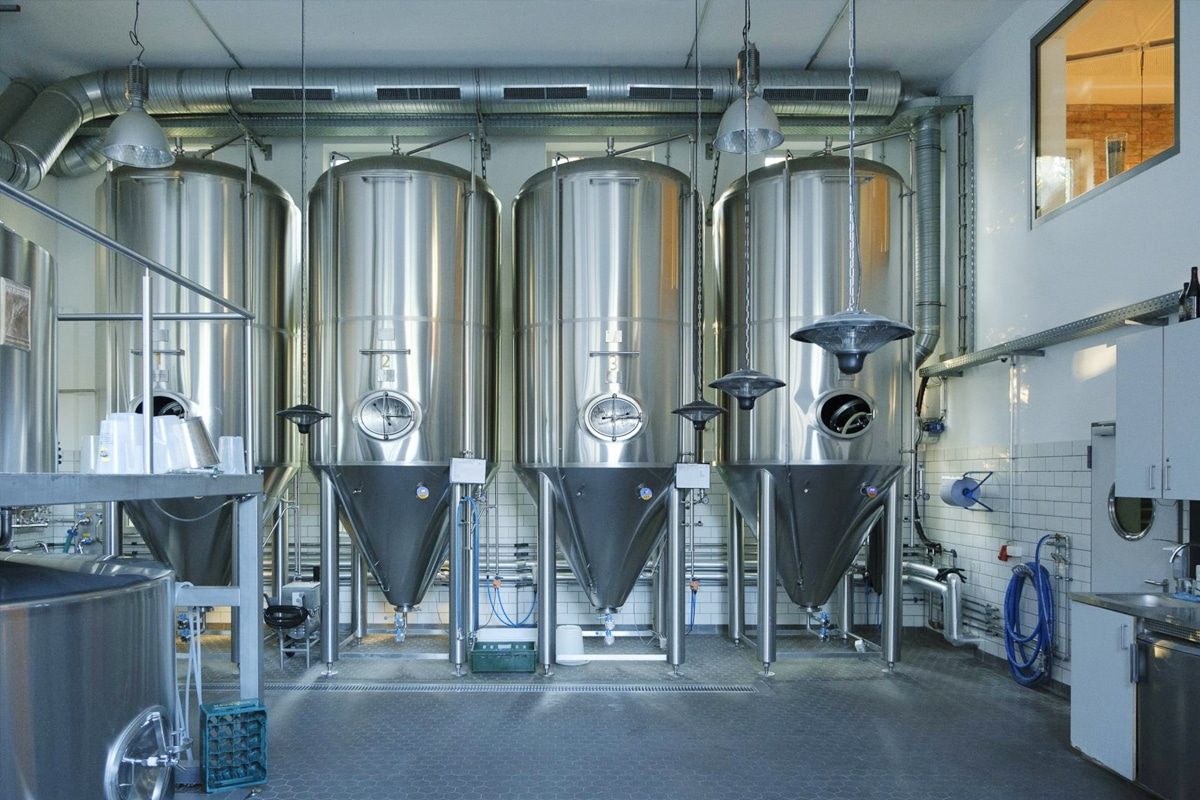
Technological Advancements and Their Impact on Layout
Automation and Robotics
Automation and robotics are becoming increasingly integral to modern brewery operations. They streamline processes, reduce manual labor, and enhance precision, leading to more efficient and consistent production.
- Automated Control Systems: Automated control systems centralize the monitoring and adjustment of brewing processes. These systems allow operators to control multiple aspects of brewing—from temperature regulation to ingredient dosing—from a single interface. This centralization reduces the need for operators to move between different pieces of equipment, enabling a more compact and efficient layout.
- Robotic Handling: Robotics can handle various repetitive tasks, such as moving raw materials, transferring wort between vessels, and packaging finished products. By integrating robotic systems, breweries can reduce the need for wide pathways and large handling areas, allowing for a more compact and efficient use of space. For example, robotic arms can automate the loading and unloading of bottles and cans, minimizing manual handling and reducing the risk of injury.
- Precision and Consistency: Automation and robotics enhance precision and consistency in brewing operations. Automated systems can precisely measure and add ingredients, ensuring consistent product quality. This reduces the need for rework and minimizes waste, leading to more efficient use of resources and space.
- Maintenance and Downtime: Automated systems can include predictive maintenance features, alerting operators to potential issues before they result in equipment failure. This reduces downtime and ensures that equipment is always operating at peak efficiency. The layout can be designed to facilitate easy access to automated systems for maintenance, further enhancing operational efficiency.
Data Analytics
Data analytics is transforming how breweries manage their operations, providing valuable insights into every aspect of the brewing process. By analyzing data collected from various stages of production, breweries can optimize their layouts and improve efficiency.
- Process Optimization: Data analytics allows breweries to identify bottlenecks and inefficiencies in their processes. By analyzing data on production times, ingredient usage, and equipment performance, breweries can make informed decisions about how to arrange their equipment to maximize efficiency. For example, if data shows that certain stages of the brewing process are consistently slower, the layout can be adjusted to reduce delays and streamline the workflow.
- Predictive Maintenance: Data analytics can be used to predict when equipment is likely to fail, allowing breweries to perform maintenance before issues arise. This proactive approach reduces downtime and ensures that equipment is always in good working condition. By integrating predictive maintenance into the layout planning, breweries can design spaces that facilitate easy access to equipment for repairs and maintenance.
- Inventory Management: Data analytics can optimize inventory management by providing real-time insights into stock levels and usage patterns. This helps breweries maintain optimal inventory levels, reducing the risk of stockouts or overstocking. Efficient inventory management systems can be integrated into the layout, ensuring that raw materials and finished products are stored in the most efficient manner possible.
- Energy and Resource Efficiency: Analyzing data on energy and resource usage can help breweries identify areas where they can reduce consumption and improve sustainability. For example, data may reveal that certain equipment is consuming more energy than necessary, prompting layout changes to enhance energy efficiency. By designing the layout to incorporate energy-efficient practices, breweries can reduce their environmental impact and operating costs.
Integration of Technology into Layout
Integrating automation, robotics, and data analytics into the brewery layout requires careful planning to ensure that these technologies enhance, rather than hinder, operational efficiency.
- Centralized Control Hubs: Establishing centralized control hubs where operators can monitor and control automated systems can streamline operations. These hubs should be strategically located to provide easy access to critical points in the brewing process.
- Flexible Layout Designs: Flexibility in layout design can help accommodate technological advances. Modular and reconfigurable layouts allow breweries to easily integrate new equipment and technologies as they become available. This flexibility ensures that the brewery can adapt to changing production needs and technological developments.
- Space for Growth: As breweries adopt more advanced technologies, they may require additional space for new equipment. Planning for future growth by including expandable areas in the initial layout design can save time and resources in the long run. This foresight allows breweries to scale up operations without significant disruptions.
- Training and Safety: Integrating advanced technologies requires staff training to ensure they can operate and maintain the new systems effectively. The layout should include dedicated training areas and clear signage to enhance safety and efficiency. Ensuring that staff are well-trained reduces the risk of accidents and improves overall productivity.
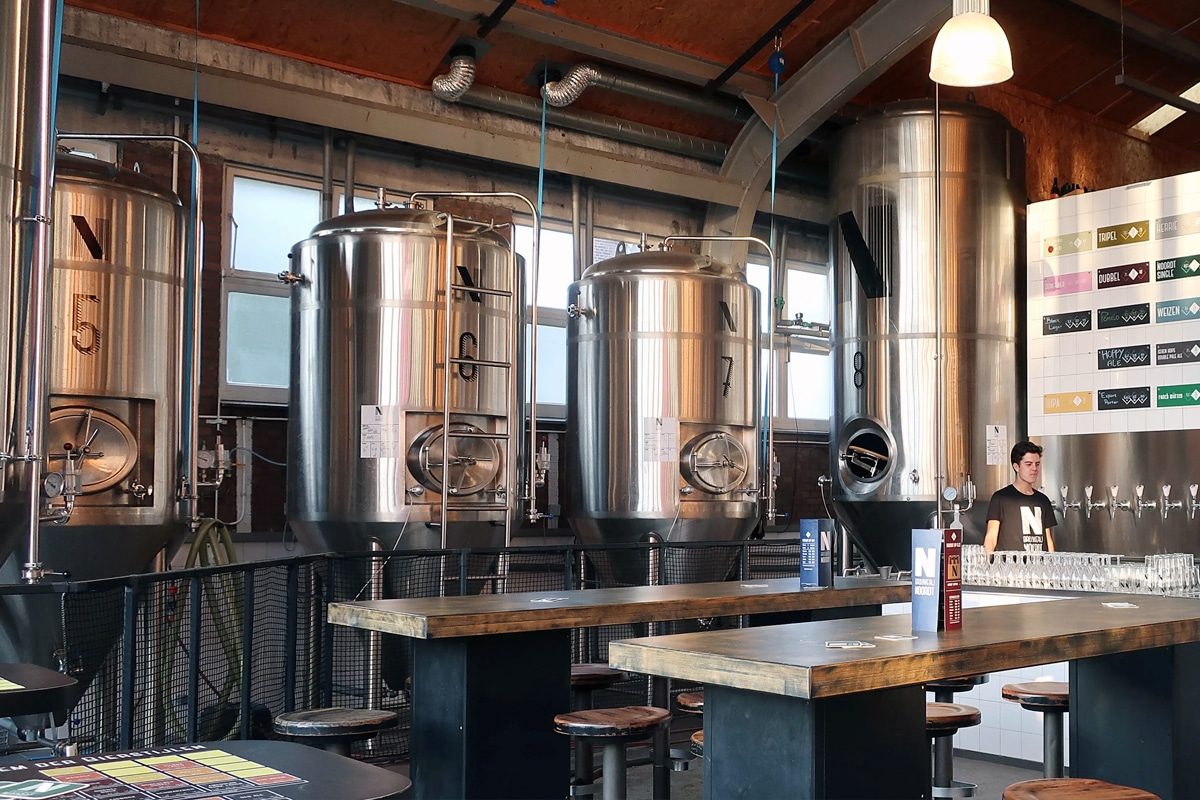
Future Trends in Brewery Layout Design
Sustainable Design
Sustainability is becoming an increasingly critical consideration in brewery layout design. Sustainable practices not only help protect the environment but also reduce operational costs and improve the overall efficiency of the brewery. Here are some key aspects of sustainable design in brewery layouts:
- Energy Efficiency: Designing layouts that optimize energy use is a central element of sustainable brewing. This includes the strategic placement of equipment to minimize energy loss, such as placing heat-generating equipment near areas that require heating or utilizing waste heat recovery systems. Implementing energy-efficient lighting, insulation, and HVAC systems also contributes to reducing the brewery’s energy footprint.
- Water Management: Water is a vital resource in brewing, and efficient water management is crucial. Sustainable layouts incorporate systems for capturing, recycling, and reusing water. This can include using greywater for cleaning purposes and integrating water-saving technologies in the brewing process. Proper drainage and wastewater treatment systems are also essential components.
- Renewable Energy: Incorporating renewable energy sources, such as solar panels and wind turbines, into the brewery layout can significantly reduce reliance on non-renewable energy. Positioning solar panels on rooftops or unused land within the brewery premises can generate a substantial portion of the brewery’s energy needs.
- Material Selection and Waste Reduction: Using sustainable building materials and designing for minimal waste generation are key considerations. This includes choosing recycled or low-impact materials for construction and ensuring that the layout facilitates efficient waste separation, recycling, and disposal processes. Breweries can also implement systems for composting organic waste and repurposing by-products, such as spent grain.
- Eco-friendly Transportation: Designing layouts that facilitate efficient logistics and transportation can further enhance sustainability. This includes optimizing the placement of loading docks and storage areas to reduce transportation distances and fuel consumption. Encouraging the use of electric or low-emission vehicles for distribution can also contribute to sustainability goals.
Modular Layouts
Modular layouts are becoming increasingly popular in brewery design due to their flexibility and scalability. This approach involves creating a layout with interchangeable and adaptable modules that can be easily reconfigured as the brewery’s needs change. Here are some key benefits and considerations of modular layouts:
- Scalability: One of the primary advantages of modular layouts is their ability to scale operations up or down without significant disruptions. As a brewery grows, additional modules can be seamlessly integrated into the existing layout. This scalability is particularly beneficial for small breweries with plans for future expansion.
- Flexibility: Modular layouts offer the flexibility to adapt to changing production requirements, new brewing techniques, or shifts in market demand. This adaptability allows breweries to experiment with different processes, products, and production volumes without extensive reconfiguration costs.
- Ease of Maintenance and Upgrades: Modular systems simplify maintenance and upgrades. Individual modules can be isolated and serviced without affecting the entire operation. This reduces downtime and ensures that equipment can be updated or replaced as needed without major layout changes.
- Standardization: Using standardized modules can streamline the design and construction process, reducing costs and lead times. Standard modules can also simplify staff training, as they become familiar with the consistent design and functionality across different parts of the brewery.
- Optimized Space Utilization: Modular designs allow for optimized space utilization, making the best use of available square footage. Equipment can be arranged in a way that maximizes efficiency while maintaining the flexibility to reconfigure the layout as needed. This is particularly advantageous for breweries operating in limited or unconventional spaces.
- Enhanced Collaboration and Workflow: Modular layouts can improve collaboration and workflow by grouping related processes and functions. This creates a more cohesive and efficient working environment, where teams can easily communicate and coordinate their activities.
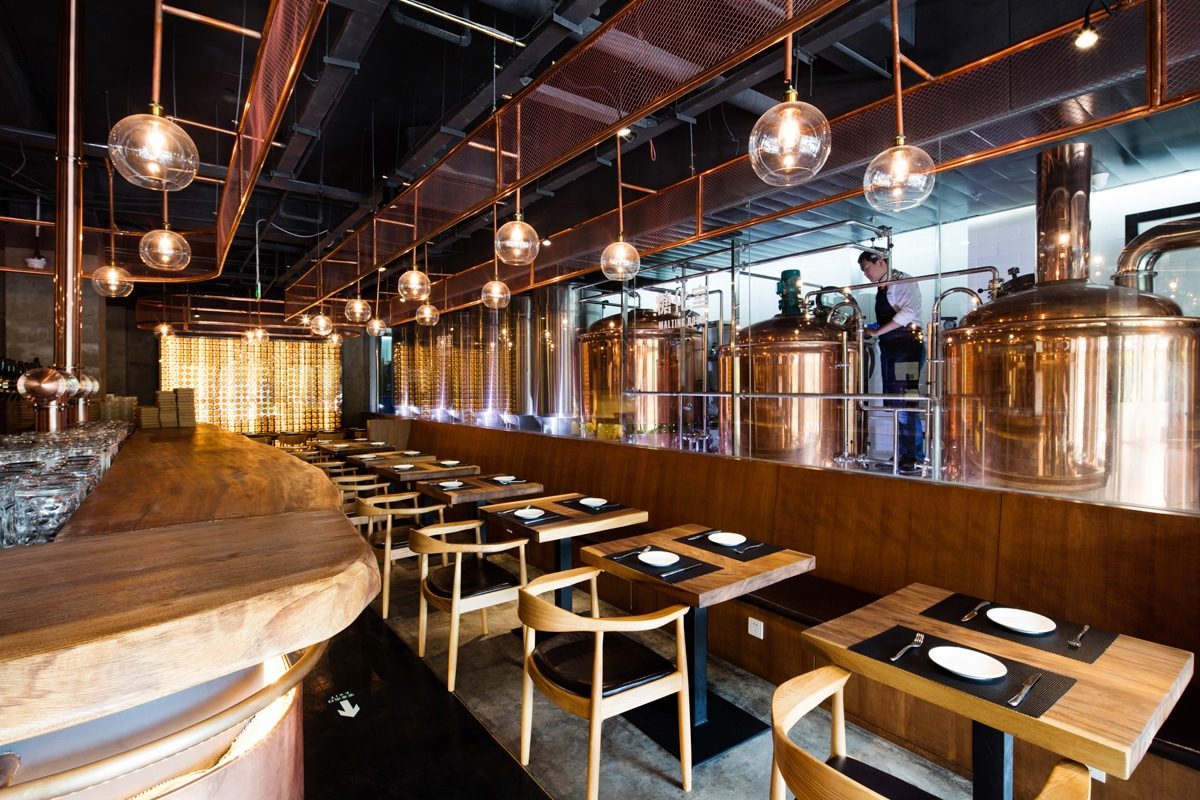
Summarize
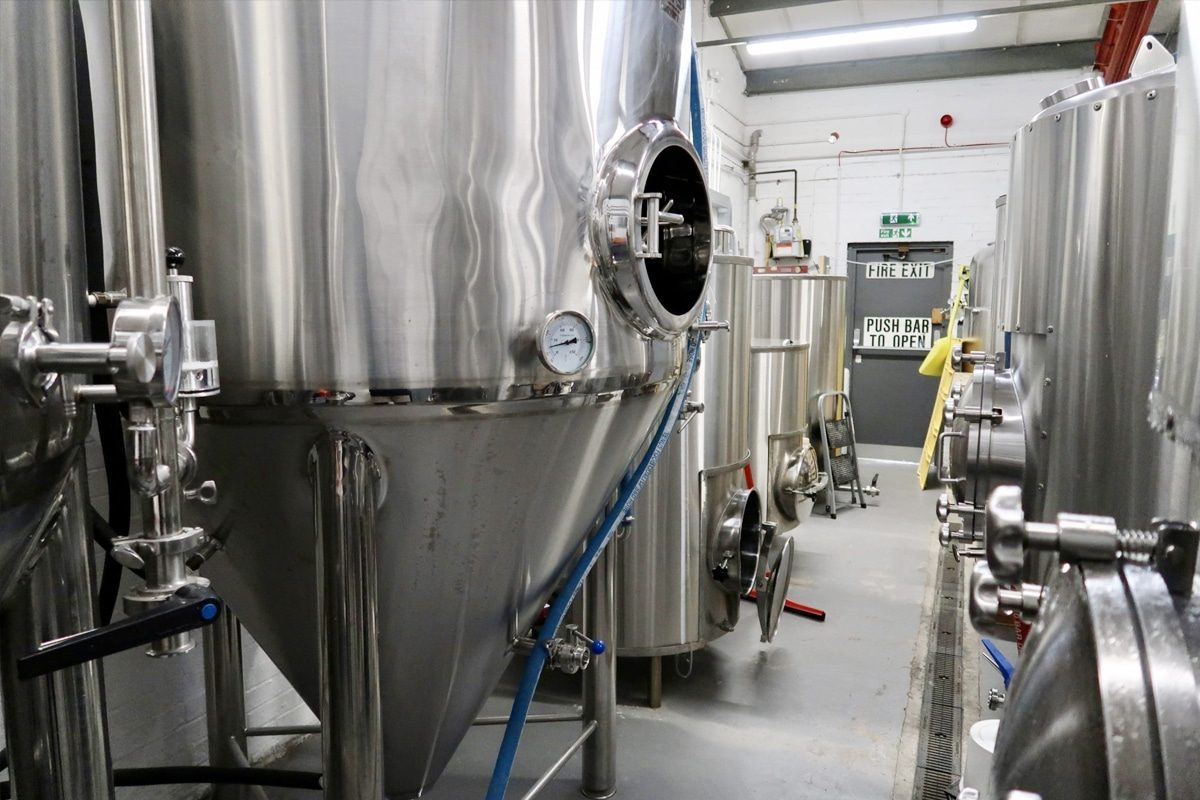