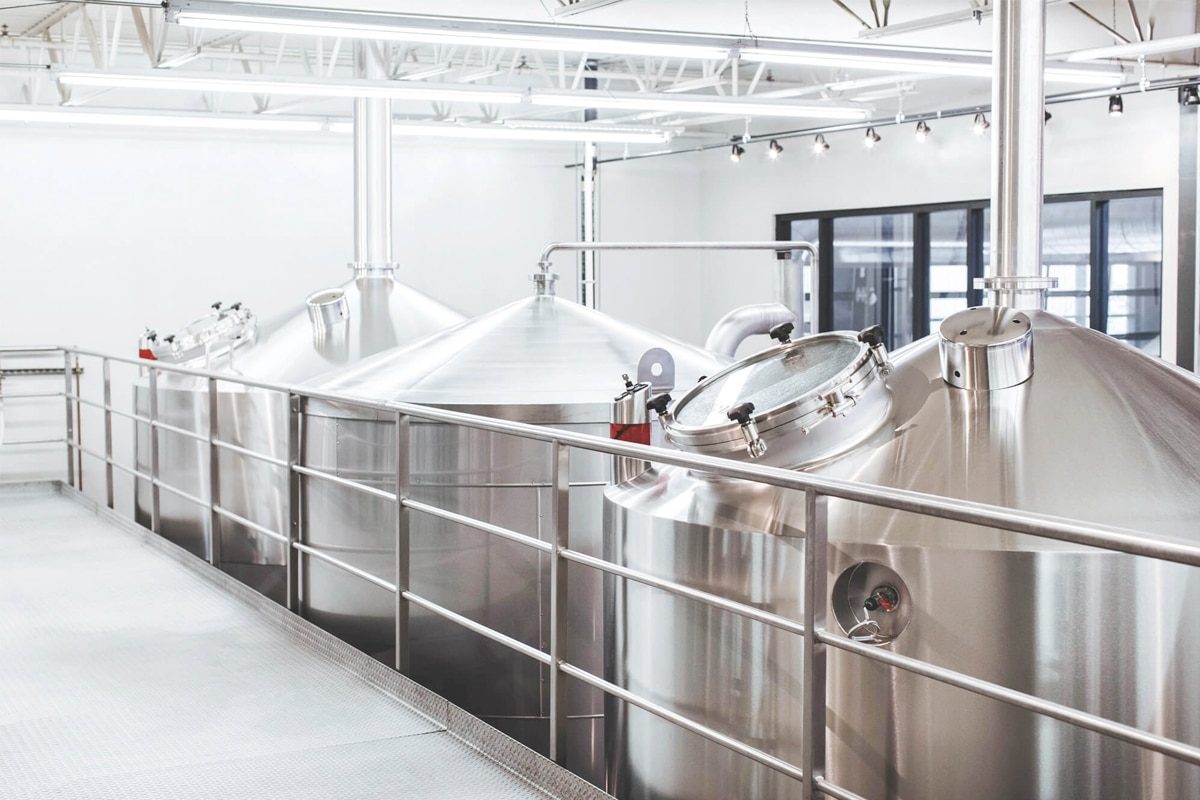
How Do You Calculate Brewery Capacity?
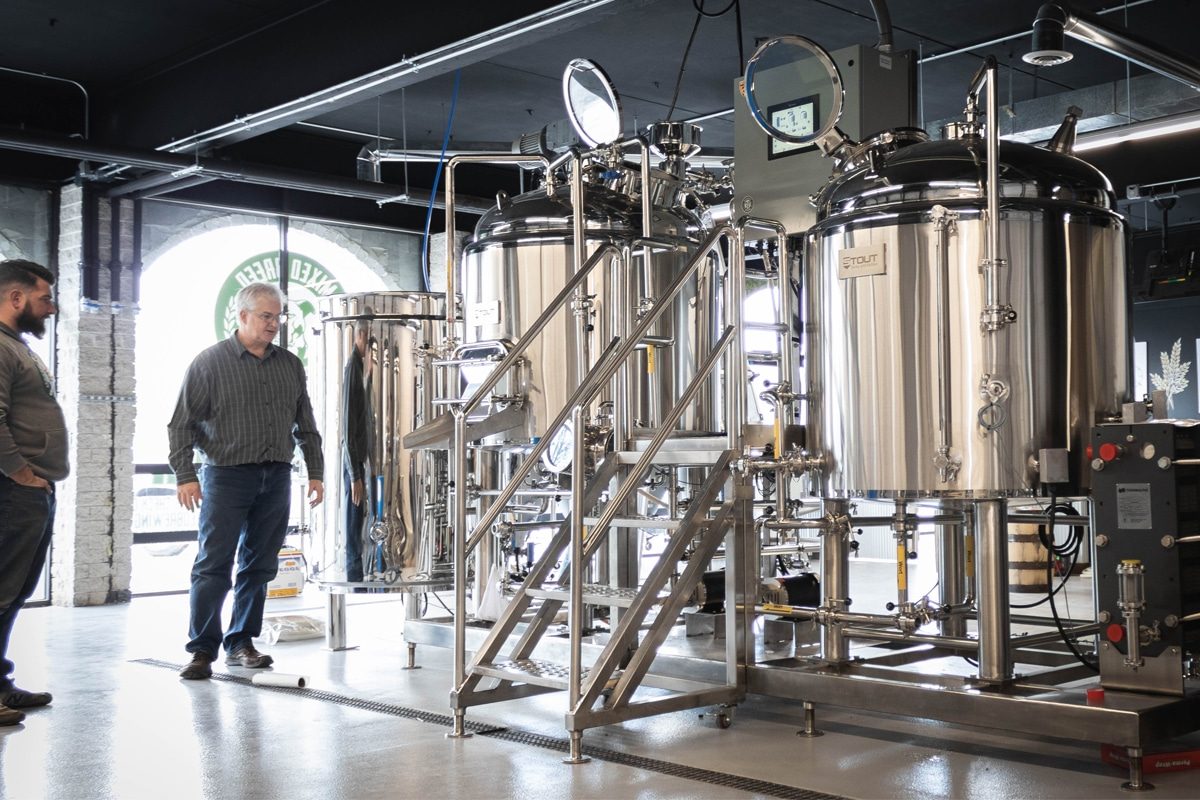
Understand Brewery Capacity
What is brewery capacity?
Factors Affecting Brewery Capacity
Several factors influence a brewery’s capacity, from physical infrastructure to operational efficiency. Key factors include:
- Equipment Efficiency: The size, capacity, and efficiency of brewery equipment significantly affect a brewery’s capacity. Factors such as brewery size, fermentation vessel capacity, packaging line speed, and equipment maintenance protocols all play a role in determining a brewery’s throughput.
- Brewing Process Duration: The duration of each stage of the brewing process, from mashing and boiling to fermentation and packaging, affects the overall brewery capacity. Knowing how long each step takes can help breweries optimize production plans and maximize output.
- Raw Material Availability: The availability of raw materials, including malt, hops, yeast, and water, affects brewery capacity. Fluctuations in feedstock supply, quality, and cost can impact throughput and scheduling decisions.
- Production Planning: Efficient production planning, including the number of brewing cycles per day, week, or month, plays a vital role in a brewery’s capacity. Balancing production with market demand and resource availability helps maximize capacity utilization.
- Staffing and Skill Levels: The availability of technicians and their efficiency in performing brewing tasks affects a brewery’s capacity. Well-trained employees optimize processes, reduce errors, and increase overall productivity.
- Operational Constraints: Various operational constraints, such as staffing levels, facility layout, regulatory compliance, and environmental considerations, can impact a brewery’s capacity. Identifying and addressing these limitations can help optimize brewery performance and efficiency.
Brewery capacity type
There are three main types of brewery capacity that breweries consider when planning and managing production:
- Actual Capacity: Actual capacity represents the maximum output a brewery can achieve under current operating conditions, taking into account factors such as equipment efficiency, downtime, and staffing levels. It provides a realistic estimate of a brewery’s production capacity and is used in daily planning and decision-making.
- Theoretical Capacity: Theoretical capacity represents the ideal maximum output that a brewery can achieve under perfect operating conditions, without any constraints or limitations. While theoretical capacity can serve as a baseline for performance evaluation and capacity optimization efforts, it may not always match actual conditions due to various operational constraints.
- Future Capacity: Future capacity considers the brewery’s potential for expansion or optimization efforts. It involves forecasting future production needs, investing in additional equipment or infrastructure, and planning for growth in market demand.
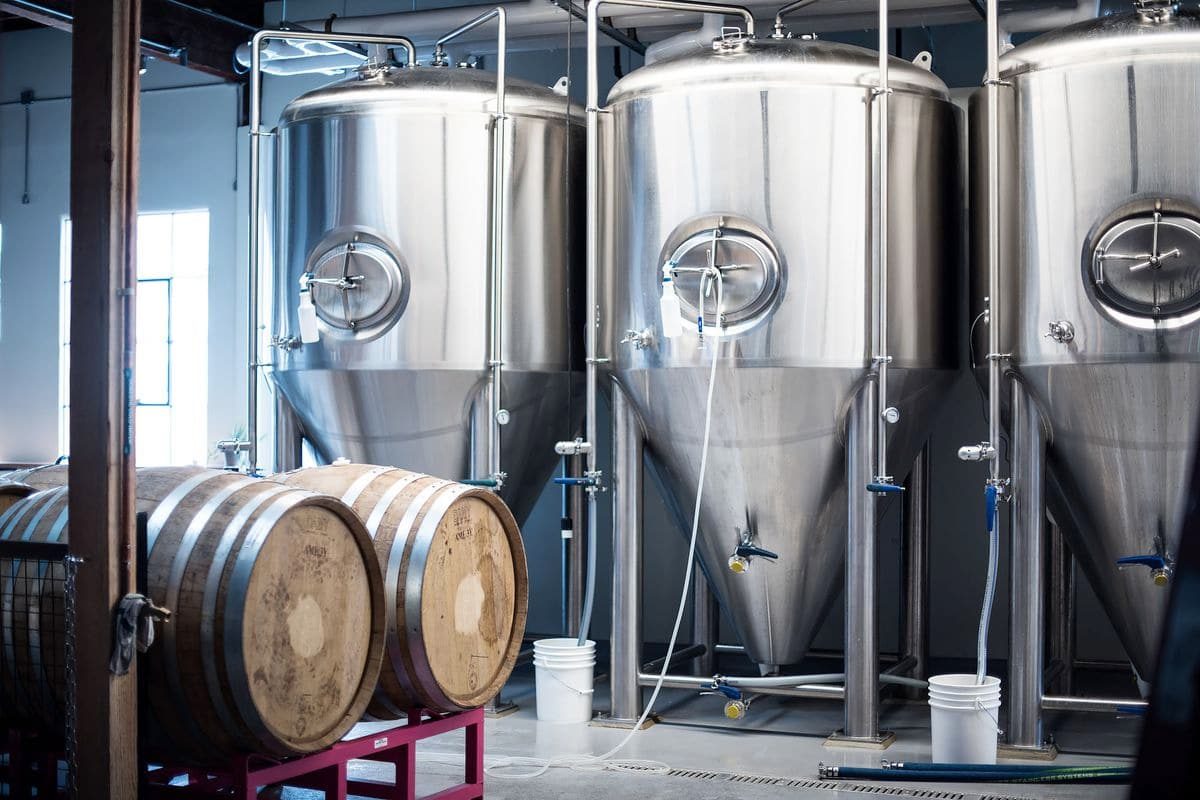
Factors Affecting Brewery Capacity
Equipment efficiency
The efficiency of brewing equipment is a major determinant of brewery capacity. Many factors affect equipment efficiency, including:
- Brewery Size and Configuration: The size and layout of the brewery determine the maximum amount of work that can be produced in a single batch. Larger breweries can accommodate larger volumes, resulting in greater production capacity per brewing cycle.
- Fermentation Tank Capacity: The capacity of the fermentation tank determines the amount of beer that can be fermented at the same time. Having a sufficient number of fermentation vessels of the proper size ensures smooth fermentation and maximizes brewery capacity.
- Packaging Line Speed: Packaging line speed and efficiency impact a brewery’s ability to package and distribute finished beer. Fast and reliable packaging equipment minimizes downtime and maximizes throughput, thereby increasing overall brewery capacity.
- Equipment Maintenance and Downtime: Regular maintenance and minimizing downtime are critical to maximizing equipment efficiency. Preventive maintenance programs and efficient repair protocols help minimize production interruptions and ensure optimal equipment performance.
Brewing process duration
The duration of each stage in the brewing process significantly affects the overall brewery capacity. Key factors that influence the duration of the brewing process include:
- Mashing and Boiling Times: The time required for mashing and boiling varies based on factors such as recipe complexity and equipment efficiency. Efficient mashing and boiling processes help simplify production and shorten the duration of the entire process.
- Fermentation and Conditioning Time: Fermentation and conditioning are critical stages and should not be rushed. The duration of fermentation and conditioning depends on factors such as yeast strain, beer style, and desired flavor profile. Optimal fermentation and conditioning times ensure high-quality beer production while maximizing brewery capacity.
- Packaging: The time required for packaging (including filling, labeling, and packaging) affects a brewery’s ability to effectively package finished beer. Efficient packaging operations minimize turnaround times and increase brewery throughput by reducing bottlenecks in the production process.
Production Plan
Production planning determines the frequency and timing of brewing cycles, directly affecting the brewery’s capacity. Key considerations for production scheduling include:
- Number of Brewing Cycles: The number of brewing cycles per day, week, or month determines the overall production capacity of the brewery. Efficient scheduling ensures a balance between meeting demand and avoiding overproduction or underutilization of resources.
- Batch Size and Turnaround Time: Optimizing batch size and turnaround time is critical to maximizing brewery capacity. Adjusting batch sizes to demand and minimizing downtime between batches helps maintain a stable production flow and maximize throughput.
- Seasonal Changes and Demand Fluctuations: Forecasting seasonal changes and fluctuations in market demand can help complete effective production scheduling. Scheduling flexibility allows breweries to adapt to changing demand patterns and optimize capacity utilization throughout the year.
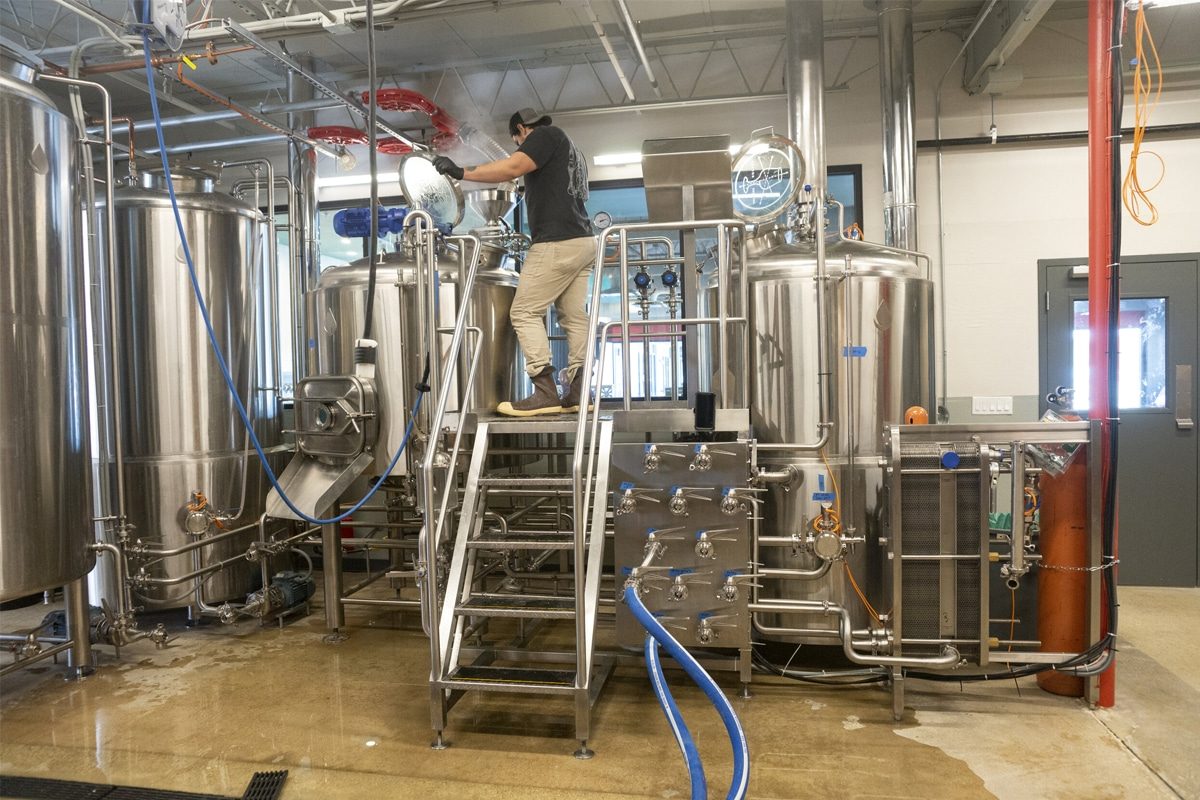
How To Calculate Brewery Capacity
Actual Ability
- Equipment Efficiency: Evaluate the efficiency and throughput of brewery equipment, including brewhouse equipment, fermentation vessels, and packaging lines. Consider factors such as equipment downtime, maintenance requirements, and production speed.
- Staffing and Skills: Assess the availability and skill levels of brewery personnel. Consider how staffing levels and skill sets impact productivity and overall capacity utilization.
- Production Constraints: Identify any operational constraints or bottlenecks that may limit production capabilities. This may include constraints on raw material availability, storage space, or facility layout.
Theoretical Ability
- Equipment Specifications: Determine the maximum throughput of your brewing equipment based on manufacturer specifications and design parameters.
- Optimum Process Efficiency: Assumes ideal operating conditions including minimal downtime, optimal staffing levels, and efficient production processes.
- No Production Constraints: Assume no constraints on raw material availability, storage space, or facility layout.
Utilization
- Determine Actual Production: Calculate the total amount of beer produced during a given period.
- Calculate Maximum Capacity: Determine the actual or theoretical capacity of the brewery for the same period.
- Actual Production Divided by Maximum Capacity: Divide actual production by maximum capacity and multiply by 100 to calculate utilization.
Future Expansion
- Demand Forecast: Forecast future market demand and consumption trends to provide information for capacity expansion plans.
- Infrastructure Investment: Evaluate whether additional equipment, facilities, or resources are needed to support increased production capacity.
- Risk Management: Assess potential risks and challenges associated with capacity expansion, such as capital investment, market volatility, and regulatory compliance.
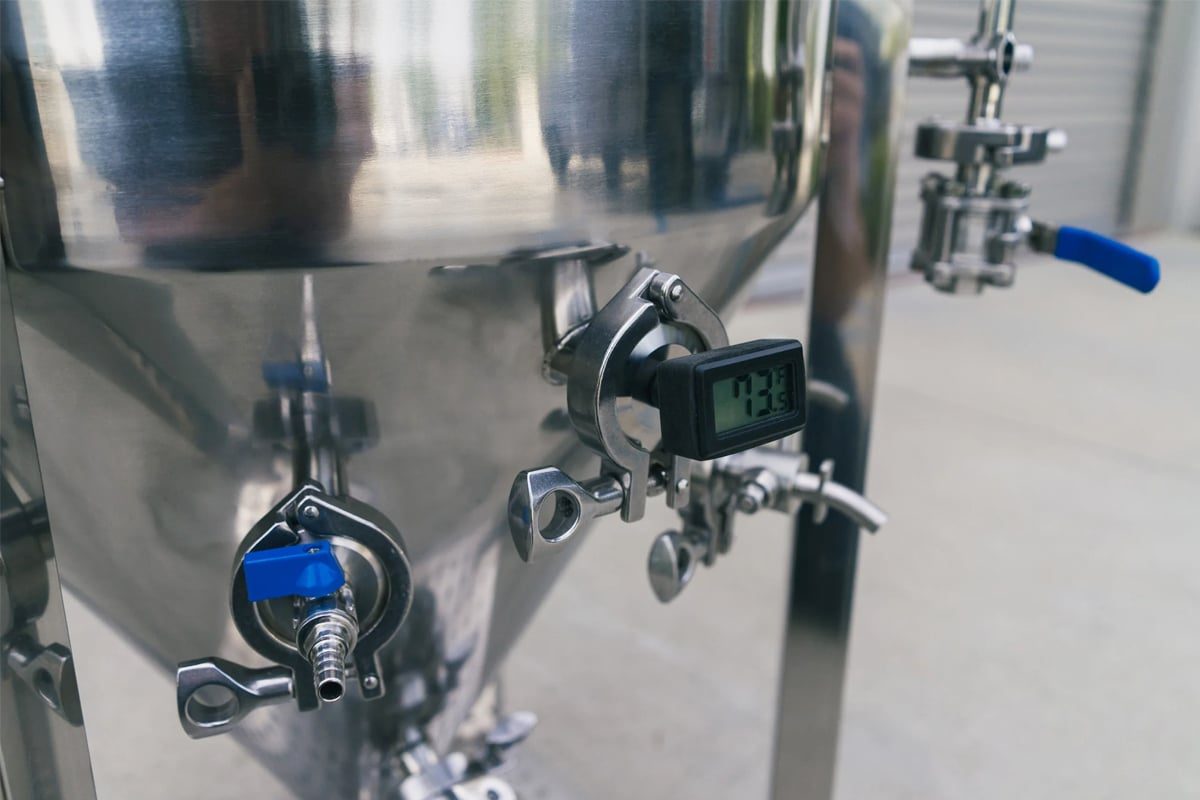
Sample Brewery Capacity Calculation
Step 1: Determine Equipment Specifications
First, we need to gather information about the brewery’s equipment specifications. Let’s assume our brewery has the following equipment:
- Brewhouse: 20-barrel capacity
- Fermentation Vessels: 10 fermenters, each with a capacity of 40 barrels
- Packaging Line: Can fill and package 60 barrels per hour
Step 2: Assess Production Processes
Next, we’ll assess the brewery’s production processes to estimate the time required for each stage. For simplicity, let’s assume the following process durations:
- Mashing and Boiling: 6 hours
- Fermentation and Conditioning: 2 weeks
- Packaging: 1 day (8 hours)
Step 3: Calculate Practical Capacity
- Brewhouse: 20 barrels per batch, producing one batch per day (Practical capacity: 20 barrels per day)
- Fermentation Vessels: 10 fermenters x 40 barrels each = 400 barrels total capacity, with a turnover of one batch every 2 weeks (Practical capacity: 20 barrels per day)
- Packaging Line: 60 barrels per hour x 8 hours = 480 barrels per day
Step 4: Calculate Theoretical Capacity
- Brewhouse: 20 barrels per batch, producing one batch per day (Theoretical capacity: 20 barrels per day)
- Fermentation Vessels: 10 fermenters x 40 barrels each = 400 barrels total capacity, with a turnover of one batch every 2 weeks (Theoretical capacity: 20 barrels per day)
- Packaging Line: 60 barrels per hour x 24 hours = 1,440 barrels per day
Step 5: Compare Practical and Theoretical Capacity
Step 6: Consider Future Expansion
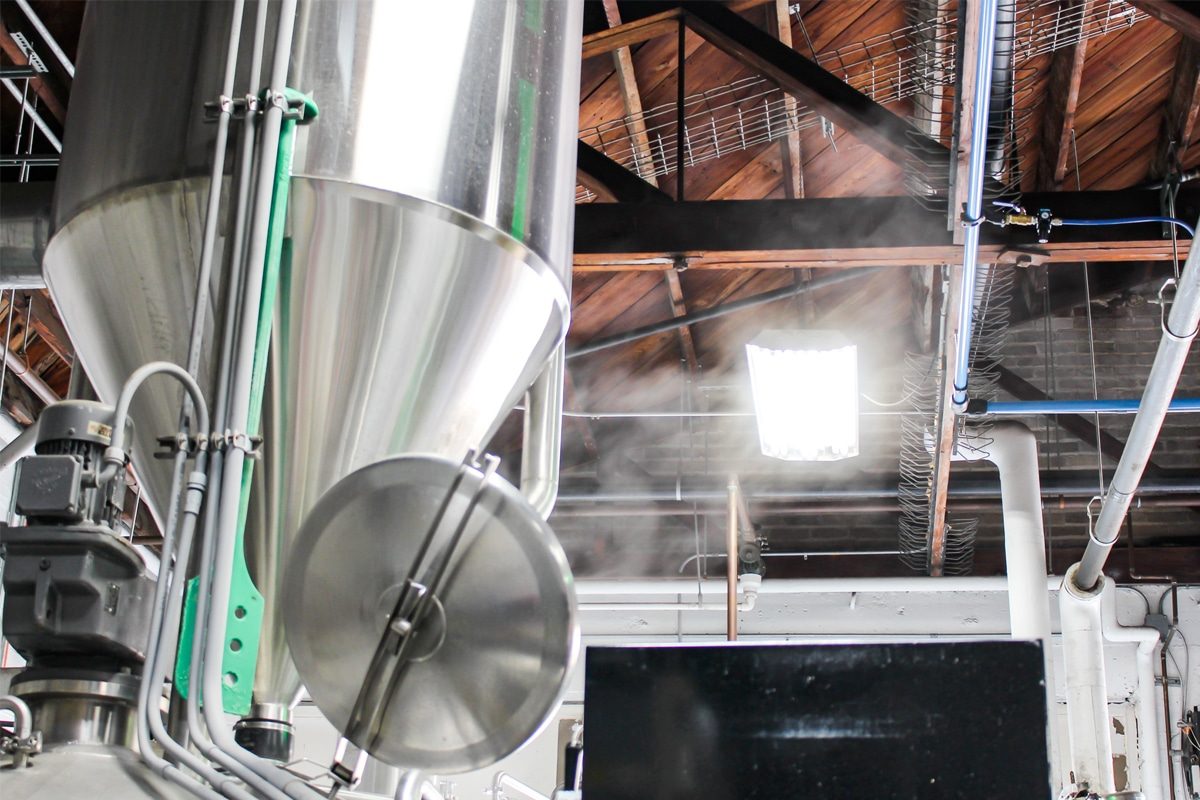
Brewery Capacity Optimization Strategy
Equipment optimization
Efficient and well-maintained equipment is the backbone of brewery operations. By optimizing equipment usage and performance, breweries can increase production capacity and minimize downtime. Key equipment optimization strategies include:
- Scheduled Maintenance: Implement a proactive maintenance plan to minimize downtime and ensure equipment is running at peak efficiency. Routine inspections, cleaning, and repairs help prevent costly breakdowns and production delays.
- Invest in Modern Equipment: Upgrade outdated or inefficient equipment to newer, more advanced models that provide higher throughput and improved performance.
- Automation and Integration: Employ automation technology and integrated systems to streamline brewery operations and reduce manual labor. Automated processes can increase production speed and consistency while reducing human error.
- Capacity Planning: Evaluate equipment capacity and identify opportunities for expansion or upgrades to support increased production needs and future growth.
Production plan optimization
Efficient production scheduling is critical to maximizing brewery capacity and meeting market demand while minimizing downtime and wasted resources. The main production plan optimization strategies include:
- Demand Forecasting: Use historical data and market trends to accurately predict future demand and adjust production plans accordingly to avoid underproduction or overproduction.
- Batch Scheduling: Optimize batch size and scheduling to minimize changeover time and maximize equipment utilization.
- Just-in-Time Inventory: Use a just-in-time inventory approach to reduce excess inventory levels and storage space requirements while ensuring the timely availability of raw materials and supplies.
- Flexibility and Adaptability: Maintain flexibility in production plans to accommodate changes in demand, raw material availability, and production priorities. Agile production processes enable brewers to respond quickly to market fluctuations and customer preferences.
Improved process efficiency
Improving process efficiency throughout the brewing process can significantly increase brewery capacity and productivity. Key process efficiency improvement strategies include:
- Standardization: Standardizing brewing processes and procedures to minimize variation, reduce errors, and increase the consistency and quality of the final product.
- Lean Manufacturing: Implement lean manufacturing principles to identify and eliminate waste, optimize workflow, and streamline production processes.
- Energy Efficiency: Implement energy-saving technologies and practices to reduce utility costs and environmental impact while maximizing production.
- Continuous Improvement: Establish a culture of continuous improvement and innovation to continuously identify and implement process improvements and efficiency gains.
Future expansion plans
For breweries looking to sustain long-term growth and success, proactive planning for future expansion is critical. Major future expansion planning strategies include:
- Market Analysis: Conduct market research and analysis to identify growth opportunities and emerging trends in the beer industry. Anticipate changes in consumer preferences, market demand, and regulatory requirements.
- Infrastructure Investment: Invest in scalable infrastructure and facilities to accommodate increased production capacity and future expansion. Consider factors such as facility layout, equipment scalability, and regulatory compliance.
- Scalable Solutions: Choose scalable brewing equipment and technology that can grow over time and adapt to your brewery’s needs.
- Strategic Partnerships: Explore strategic partnerships or collaborations with other breweries or beverage companies to leverage resources, expand distribution channels, and enter new markets.
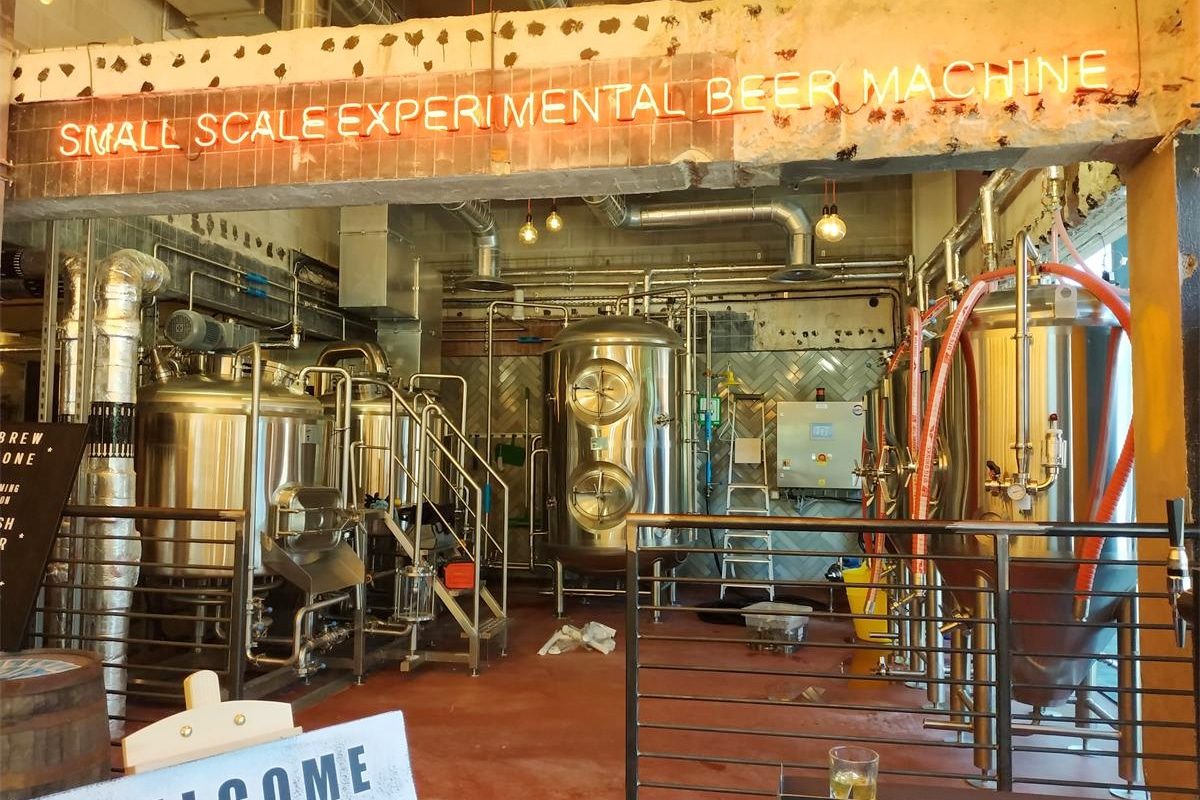
Summary
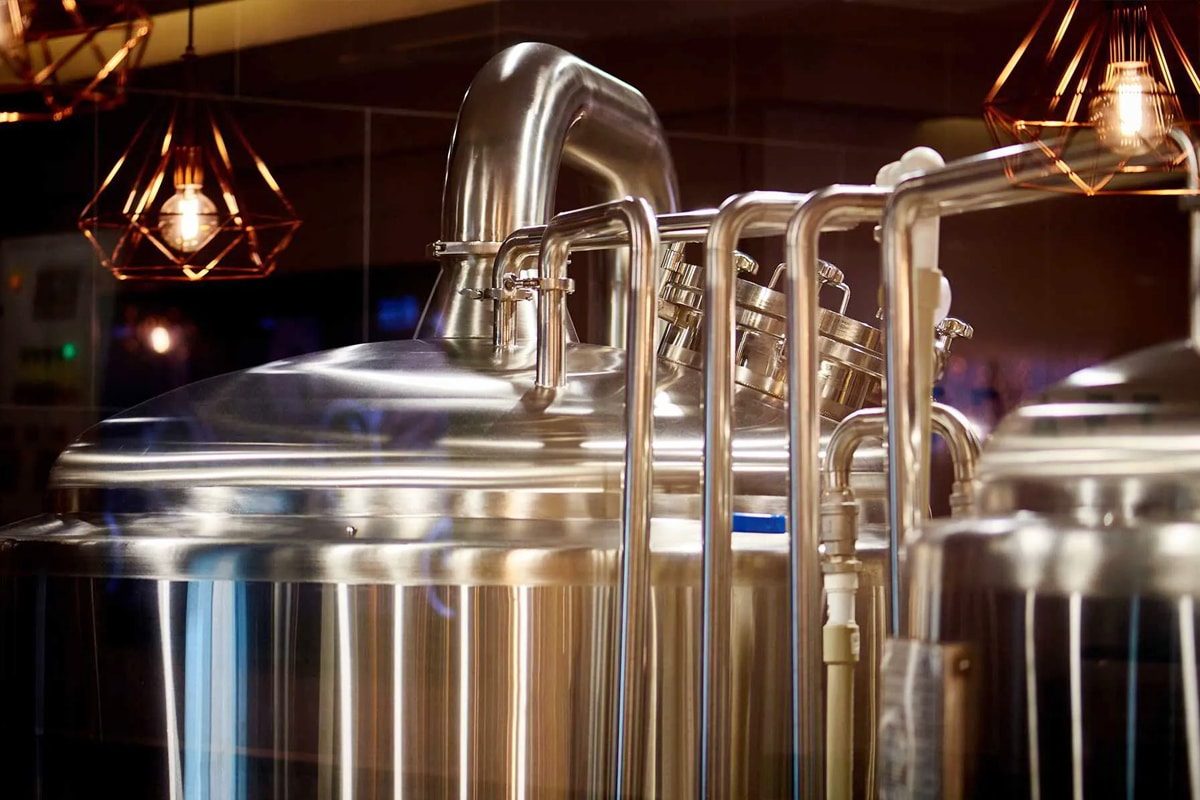