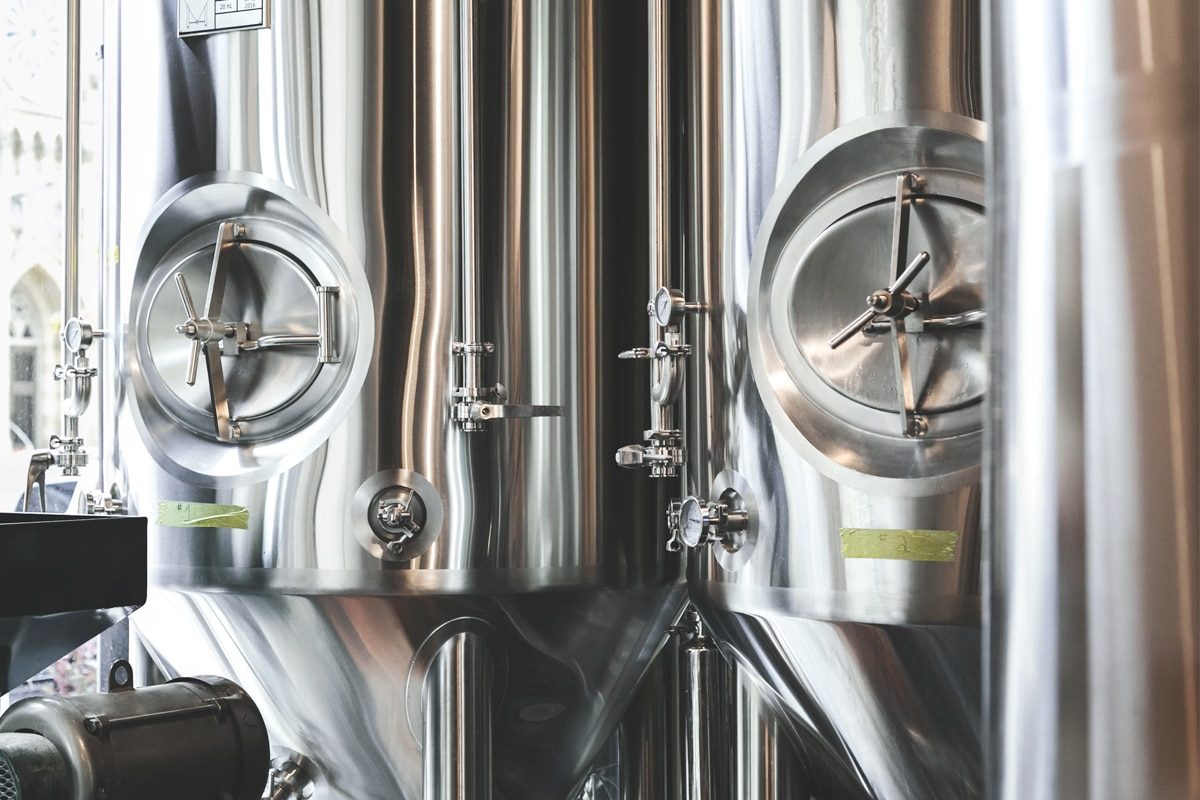
How Do Handle The Buildup of Scale and Mineral Deposits in Brewery Equipment?
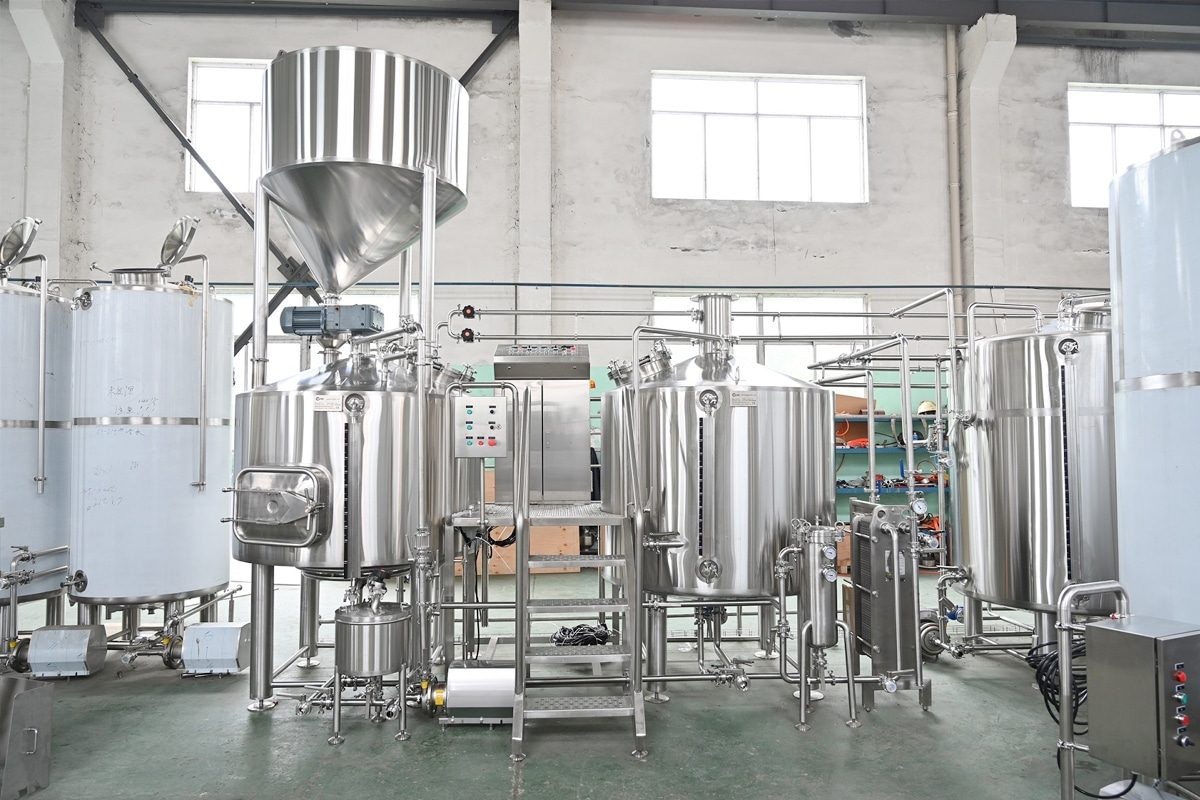
Understanding Scale and Mineral Deposits
Types of Scale and Mineral Deposits
Calcium Carbonate (CaCO3) Scale
- Formation: The calcium carbonate scale forms when calcium ions in the water combine with carbonate ions, especially at higher pH levels and temperatures.
- Appearance: It typically appears as a white, chalky deposit.
- Impact: This type of scale is prevalent in heat exchangers, boilers, and other heated surfaces, significantly reducing heat transfer efficiency and increasing energy consumption.
Calcium Sulfate (CaSO4) Scale
- Formation: Calcium sulfate scale forms when calcium ions react with sulfate ions in the water. Unlike calcium carbonate, it forms regardless of pH levels.
- Appearance: This scale appears as a hard, crystalline deposit.
- Impact: It is particularly troublesome in heat exchange surfaces and can be more challenging to remove due to its hardness.
Magnesium Hydroxide (Mg(OH)2) Scale
- Formation: Magnesium hydroxide forms when magnesium ions react with hydroxide ions, usually at high pH levels.
- Appearance: It appears as a whitish, gelatinous deposit.
- Impact: This type of scale is less common but can still cause significant issues in specific brewery equipment.
Silica (SiO2) Scale
- Formation: Silica scale forms from dissolved silicates present in the water, which precipitate out at high temperatures.
- Appearance: Silica deposits appear as hard, glassy scales.
- Impact: Silica scale is particularly problematic due to its hardness and resistance to conventional cleaning methods.
Iron and Manganese Deposits
- Formation: Iron and manganese can oxidize and precipitate out of water, forming reddish-brown and black deposits, respectively.
- Appearance: These deposits are often rust-colored or black.
- Impact: They can cause staining and affect the taste and quality of the beer.
Causes of Buildup
Water Hardness
- Description: Hard water contains high concentrations of calcium and magnesium ions. These ions are the primary precursors to scale formation.
- Impact: The higher the water hardness, the greater the potential for scale buildup, especially in equipment where water is heated.
Temperature
- Description: Higher temperatures facilitate the precipitation of minerals from the water.
- Impact: Equipment such as boilers, heat exchangers, and fermentation tanks, where water is frequently heated, are particularly prone to scale formation.
pH Levels
- Description: The pH of the brewing water influences the solubility of minerals. Higher pH levels can lead to increased precipitation of calcium and magnesium compounds.
- Impact: Maintaining an optimal pH range can minimize scaling.
Alkalinity
- Description: Alkalinity measures the water’s capacity to neutralize acids and is closely related to pH. High alkalinity can lead to increased carbonate and bicarbonate ions, contributing to calcium carbonate scale formation.
- Impact: Managing alkalinity is essential in preventing scale buildup.
Presence of CO2
- Description: Carbon dioxide (CO2) in water can form carbonic acid, which can then react with calcium to form a calcium carbonate scale.
- Impact: In breweries, CO2 is a common byproduct of fermentation, which can exacerbate scale formation if not properly managed.
Concentration of Silica
- Description: Silica is naturally present in some water sources and can precipitate out under certain conditions, especially at high temperatures.
- Impact: Silica scale is challenging to remove and requires specialized treatment methods.
Inadequate Water Treatment
- Description: Failure to properly treat brewing water before use can lead to increased mineral content and subsequent scale formation.
- Impact: Implementing an effective water treatment solution can effectively prevent scaling.
System Design and Maintenance Practices
- Description: Poor system design, such as sharp bends and dead zones in piping, can promote scale formation. Inadequate maintenance practices, such as infrequent cleaning, can exacerbate the problem.
- Impact: Ensuring optimal system design and rigorous maintenance routines can minimize the risk of scale buildup.
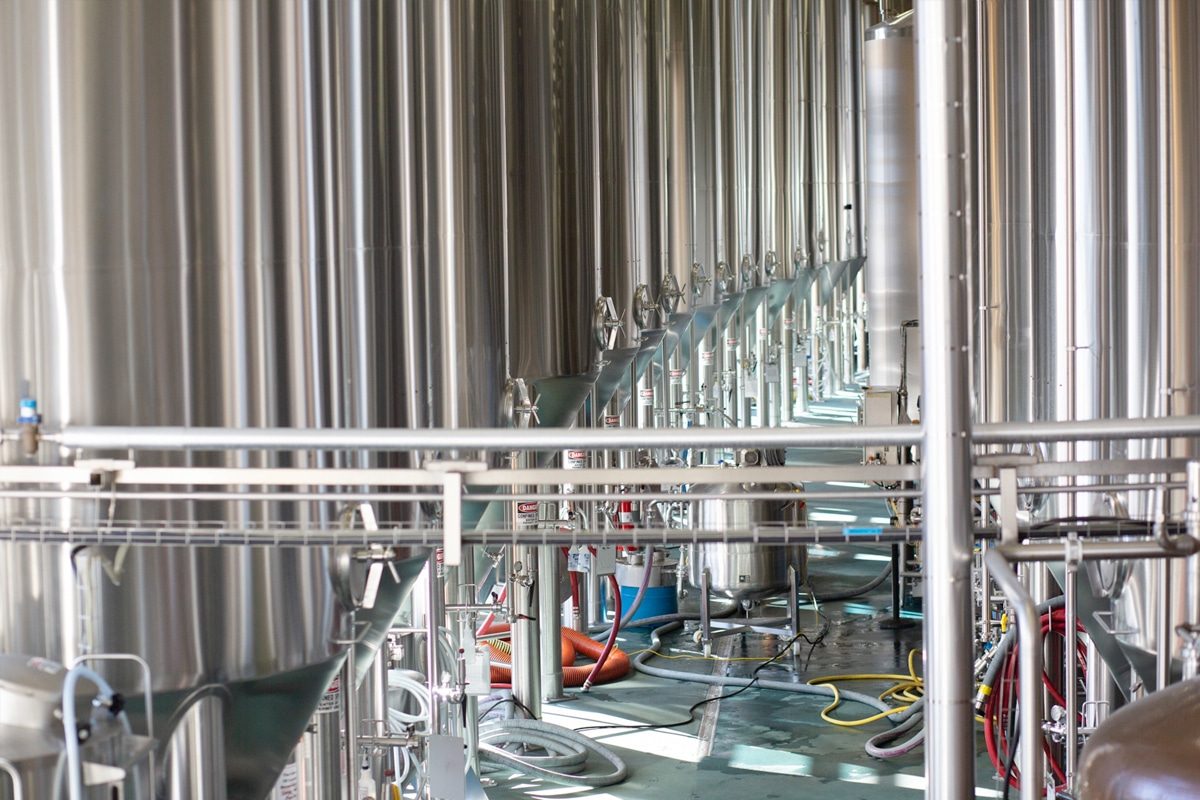
Impact of Scale and Mineral Deposits on Brewery Equipment
Impact on Heat Transfer Efficiency
One of the most immediate and significant effects of scale and mineral deposits is the reduction in heat transfer efficiency. This issue is particularly critical in equipment such as heat exchangers, boilers, and kettles, where efficient heat transfer is essential.
- Insulating Layer: The scale acts as an insulating layer, preventing efficient heat transfer between surfaces. For instance, in a heat exchanger, scale buildup on the heat transfer surfaces impedes the flow of heat, leading to longer heating times.
- Increased Energy Consumption: To compensate for the reduced efficiency, equipment must operate longer and at higher power, resulting in increased energy consumption. This not only raises operational costs but also impacts the brewery’s environmental footprint.
- Temperature Control Issues: During the brewing process, consistent and precise temperature control ensures the desired chemical reactions occur. Scale buildup can cause uneven heating, leading to temperature fluctuations that affect the brewing process.
Reduced Equipment Lifespan
Scale and mineral deposits can significantly shorten the lifespan of brewery equipment, leading to premature wear and tear.
- Abrasion and Corrosion: The abrasive nature of certain scales, such as calcium sulfate and silica, can cause mechanical wear on equipment surfaces. Additionally, deposits can create crevices that trap moisture and promote corrosion.
- Stress on Components: The buildup of scale increases the operational stress on components like pumps and valves, which must work harder to maintain flow rates. This additional strain can lead to more frequent breakdowns and the need for replacements.
- Blockages and Fouling: Scale can accumulate to the point of causing blockages in pipes and valves, disrupting the flow of liquids and gases. This fouling necessitates more frequent maintenance and cleaning, further reducing the equipment’s effective lifespan.
Quality Issues
The presence of scale and mineral deposits can have a direct impact on the quality of the beer produced, leading to potential issues with taste, safety, and consistency.
- Contamination: Scale deposits can harbor bacteria and other microorganisms that may contaminate the beer. This contamination can lead to off-flavors, spoilage, and potential health hazards.
- Altered Flavor Profile: Mineral deposits can leach into the brewing process, altering the water chemistry and subsequently affecting the flavor profile of the beer. For instance, high levels of calcium and magnesium can impart undesirable tastes.
- Inconsistent Product Quality: Scale buildup can cause variability in the brewing process, leading to inconsistent batch quality. For breweries striving for a consistent product, this variability can damage brand reputation and customer trust.
Increased Maintenance Costs
Dealing with scale and mineral deposits requires more frequent and intensive maintenance, which can significantly increase operational costs.
- Frequent Cleaning: Regular removal of scale and deposits will maintain the efficiency and hygiene of your equipment. This cleaning often involves both mechanical and chemical methods, which can be labor-intensive and costly.
- Chemical Costs: The use of specialized cleaning chemicals to dissolve and remove scale adds to the operational expenses. Over time, these costs can accumulate significantly.
- Downtime and Productivity Loss: Frequent maintenance and cleaning result in equipment downtime, which disrupts production schedules and reduces overall productivity. For commercial breweries, this downtime translates to lost revenue.
- Repair and Replacement: The need for more frequent repairs and eventual replacement of equipment due to scale-induced damage further adds to the long-term costs. Investing in new equipment prematurely because of severe scale damage represents a significant financial burden.
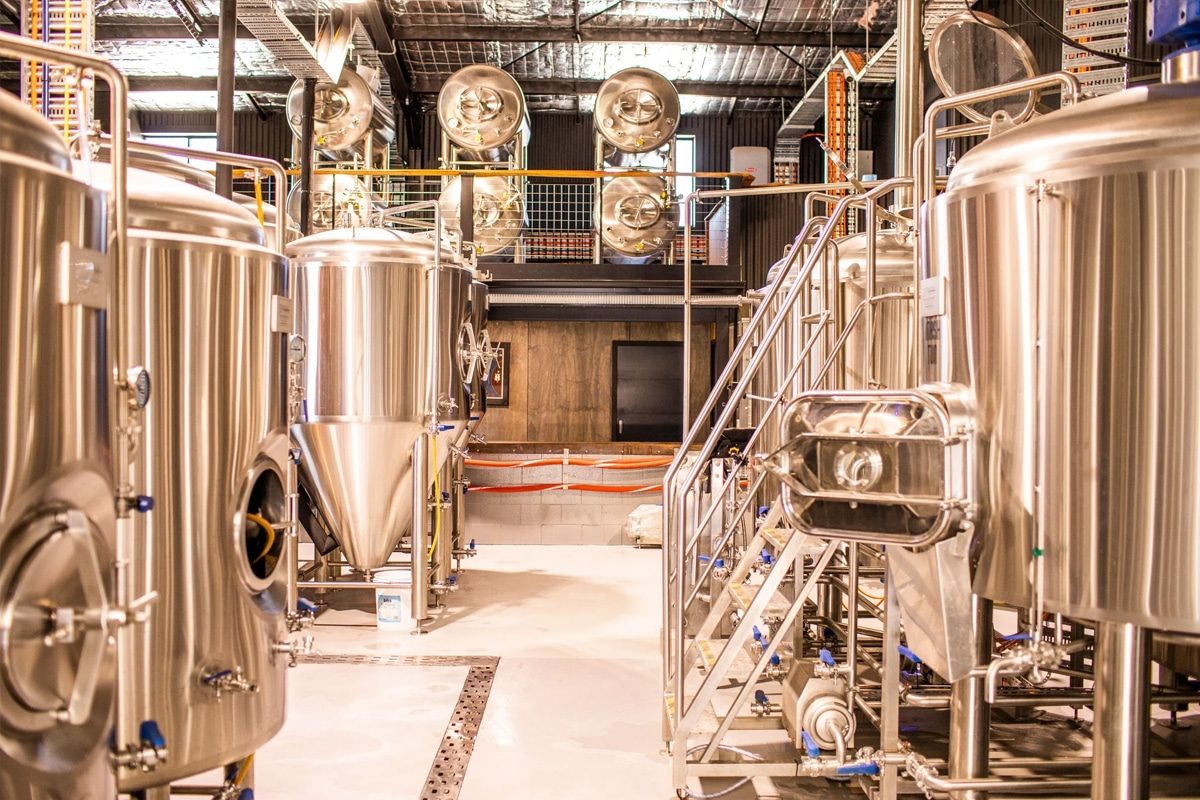
Preventing Scale and Mineral Deposits
Water Treatment
Water Softening
- Ion Exchange Systems: These systems replace calcium and magnesium ions in hard water with sodium ions, effectively reducing water hardness. This is achieved through the use of a resin bed that captures the hard minerals and releases sodium in their place.
- Benefits: Water softening is highly effective in preventing calcium carbonate and magnesium hydroxide scale. It also helps improve the efficiency and lifespan of brewery equipment.
Reverse Osmosis (RO)
- RO Systems: These systems use a semi-permeable membrane to remove up to 99% of dissolved solids, including calcium, magnesium, and silica, from the water. The process involves forcing water through the membrane under high pressure, leaving the impurities behind.
- Benefits: RO systems provide high-purity water, which is ideal for brewing. They also help in preventing a wide range of scale and mineral deposits.
Chemical Additives
- Chelating Agents: These chemicals bind to metal ions, preventing them from precipitating out of the water. Common chelating agents include EDTA (ethylenediaminetetraacetic acid) and phosphates.
- Scale Inhibitors: These chemicals interfere with the formation of scale by preventing the crystallization of minerals. Examples include polyphosphates and certain polymers.
- Benefits: Chemical additives are versatile and can be tailored to specific water compositions and brewing processes. They are especially useful in cases where other water treatment methods are not feasible.
Regular Cleaning and Maintenance
Cleaning Procedures
- Mechanical Cleaning: Regular mechanical cleaning involves the use of brushes, scrapers, and other tools to physically remove scale from accessible surfaces. This method is effective for large and easily accessible equipment components.
- Chemical Cleaning: Periodic chemical cleaning with descaling agents, such as acids (e.g., phosphoric acid, citric acid), can dissolve and remove stubborn deposits. Combining mechanical and chemical cleaning often yields the best results.
- Sanitization: Regular sanitization using appropriate sanitizing agents helps eliminate microbial contamination that can exacerbate scaling problems.
Maintenance Schedule
- Routine Inspections: Regular inspections of equipment can help identify early signs of scale buildup and address them before they become severe.
- Maintenance Logs: Keeping detailed maintenance logs ensures that all cleaning and maintenance activities are performed on schedule and helps track the effectiveness of preventive measures.
Temperature Control
Optimal Temperature Ranges
- Brewing Processes: Maintaining brewing processes within the optimal temperature ranges reduces the likelihood of mineral precipitation. For instance, keeping the temperature below the threshold where calcium carbonate tends to precipitate can help prevent scale buildup.
- Heat Exchangers and Boilers: Regular monitoring and adjustment of temperatures in heat exchangers and boilers can minimize scale formation. Using automated temperature control systems can help maintain consistent temperatures.
Heat Recovery Systems
- Usage: Implementing heat recovery systems can reduce the temperature differential that contributes to scale formation. By preheating incoming water with waste heat, breweries can achieve more stable temperatures.
- Benefits: These systems not only prevent scale but also improve energy efficiency and reduce operational costs.
pH Management
pH Monitoring
- Regular Testing: Frequent testing of water pH levels helps in maintaining them within the optimal range for brewing. Automated pH monitoring systems can provide real-time data and alerts for any deviations.
- Adjustment: pH levels can be adjusted using acids (e.g., lactic acid, phosphoric acid) or bases (e.g., sodium hydroxide) to maintain the desired pH range.
Optimal pH Range
- Brewing Water: Keeping the pH of brewing water within the range of 6.5 to 7.5 is generally recommended to minimize the risk of scale formation. The exact optimal range may vary based on the specific brewing process and water composition.
- Cleaning Solutions: Using pH-balanced cleaning solutions helps in effectively removing deposits without causing corrosion or damage to the equipment.
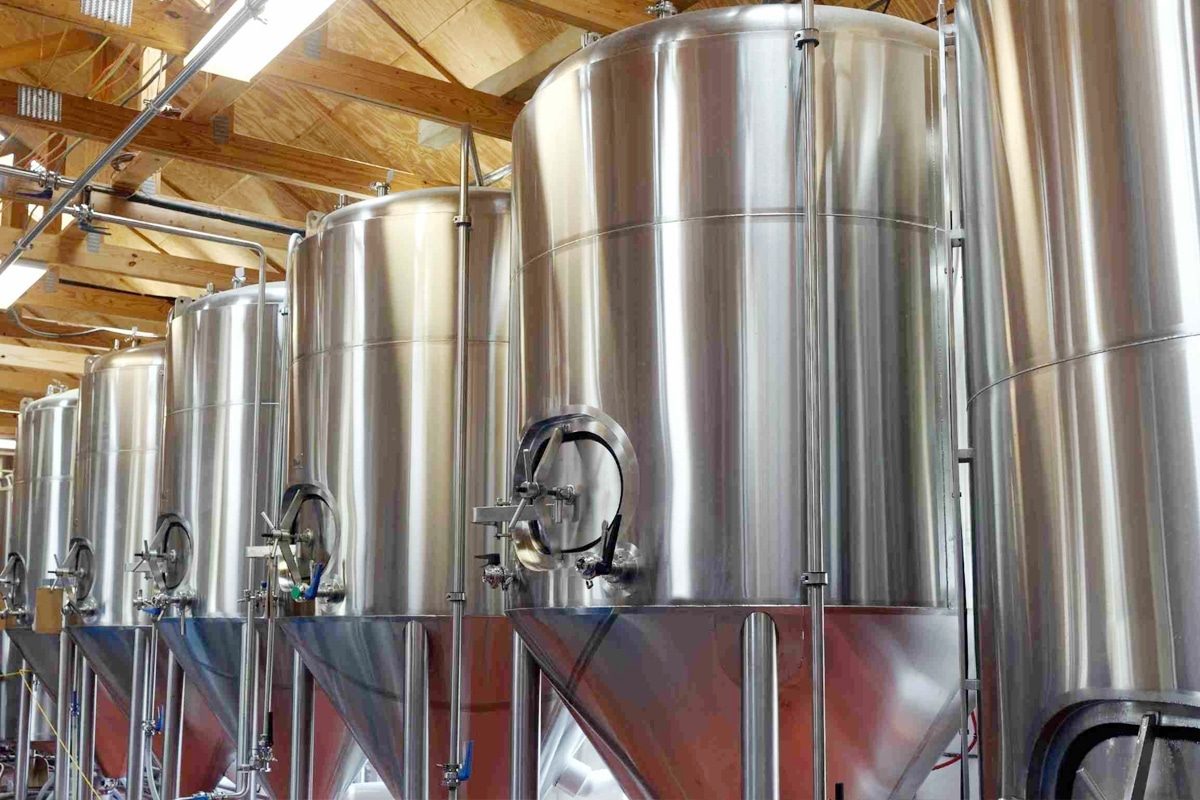
Removing Scale and Mineral Deposits
Mechanical Cleaning
Brushing and Scraping
- Tools: Brushes, scrapers, and abrasive pads are commonly used tools for mechanical cleaning. Stainless steel brushes and scrapers are particularly effective for tough deposits.
- Process: The process involves manually scrubbing or scraping the affected surfaces to dislodge and remove the scale. This method is suitable for equipment such as fermenters, kettles, and accessible pipework.
- Advantages: Mechanical cleaning is straightforward, does not require chemical use, and provides immediate visual confirmation of scale removal.
- Limitations: It can be labor-intensive, may not reach all areas of complex equipment, and can potentially damage surfaces if not done carefully.
High-Pressure Water Jets
- Tools: High-pressure water jetting systems use water at high pressure to blast away scale deposits.
- Process: The equipment directs a high-pressure stream of water at the scale, effectively dislodging and flushing it away. This method is particularly useful for pipes and heat exchangers.
- Advantages: High-pressure water jets can reach difficult-to-access areas and do not require chemicals, making them environmentally friendly.
- Limitations: This method requires specialized equipment and trained operators, and it may not be effective against very hard or thick deposits.
Chemical Cleaning
Acid Cleaning
- Chemicals Used: Common acids used in cleaning brewery equipment include phosphoric acid, citric acid, and hydrochloric acid. These acids effectively dissolve calcium carbonate and other mineral deposits.
- Process: The acidic cleaning solution is circulated through the equipment or applied directly to the affected surfaces. The solution reacts with the scale, breaking it down into soluble compounds that can be rinsed away.
- Advantages: Acid cleaning is highly effective at dissolving mineral deposits, especially in intricate and hard-to-reach areas. It is also faster than mechanical methods.
- Limitations: The use of acids requires careful handling and proper safety measures to prevent harm to personnel and equipment. Acidic residues must be thoroughly rinsed to avoid contamination.
Alkaline Cleaning
- Chemicals Used: Alkaline cleaners, such as sodium hydroxide and potassium hydroxide, are used to remove organic deposits and some mineral scales.
- Process: The alkaline solution is applied or circulated through the equipment, where it reacts with and breaks down deposits.
- Advantages: Alkaline cleaning can be effective for removing both organic and inorganic deposits, and it can be used in conjunction with other cleaning agents.
- Limitations: Similar to acid cleaning, proper handling and safety precautions are necessary. Alkaline cleaners may not be as effective on certain types of mineral scales.
Chelating Agents
- Chemicals Used: Chelating agents, such as EDTA (ethylenediaminetetraacetic acid), bind to metal ions in the scale, making them soluble in water.
- Process: The chelating solution is circulated through the equipment, where it binds to and removes the mineral deposits.
- Advantages: Chelating agents are effective at removing a wide range of mineral scales and do not pose the same corrosion risks as acids.
- Limitations: Chelating agents can be more expensive than other chemical cleaners, and their effectiveness may vary depending on the specific type of scale.
Combination Cleaning
Sequential Cleaning
- Process: This approach involves first using mechanical methods to remove the bulk of the deposits, followed by chemical cleaning to dissolve any remaining scale.
- Advantages: Combining methods ensures thorough cleaning, with mechanical cleaning addressing larger deposits and chemical cleaning reaching finer or residual scale.
- Limitations: Sequential cleaning requires careful planning and coordination, as well as additional time and resources.
Simultaneous Cleaning
- Process: In some cases, mechanical agitation is combined with chemical cleaning simultaneously. For example, circulating an acid solution through equipment while using brushes or agitators to enhance the cleaning action.
- Advantages: This method can significantly reduce cleaning time and improve the effectiveness of both mechanical and chemical actions.
- Limitations: It requires specialized equipment and careful monitoring to ensure the safety and effectiveness of the cleaning process.
Integrated Cleaning Systems
- Tools: Automated cleaning-in-place (CIP) systems can integrate both mechanical and chemical cleaning processes. These systems use programmed cycles to apply cleaning agents, perform mechanical agitation, and rinse the equipment.
- Advantages: CIP systems provide consistent and thorough cleaning, reduce manual labor, and enhance safety by minimizing direct contact with chemicals.
- Limitations: The initial investment in CIP systems can be high, and they require regular maintenance and calibration.
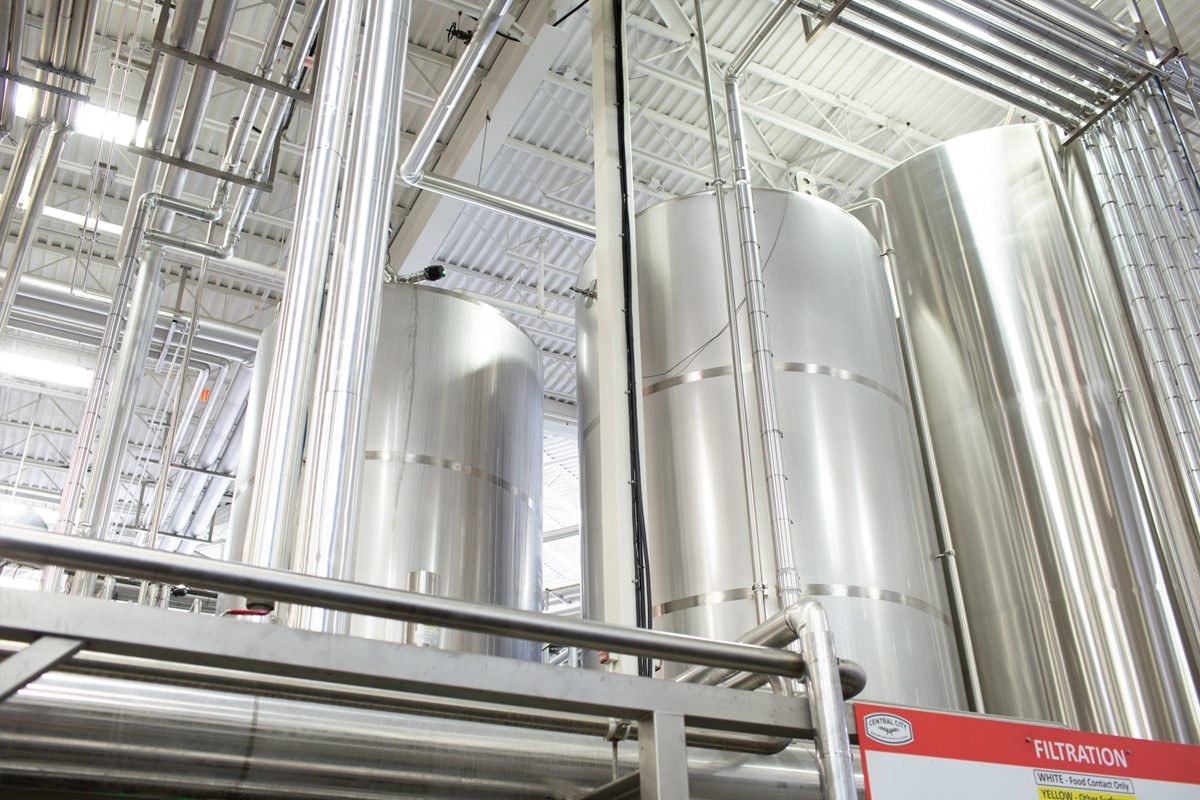
Summary
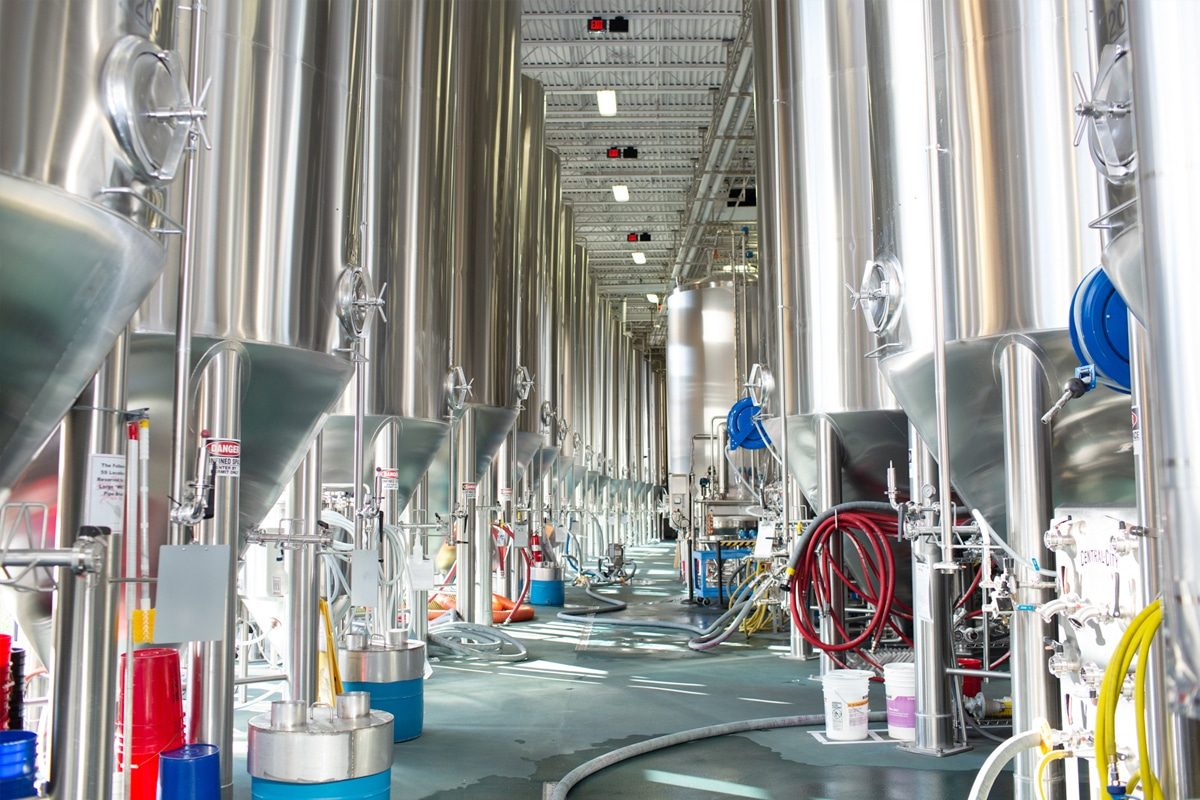