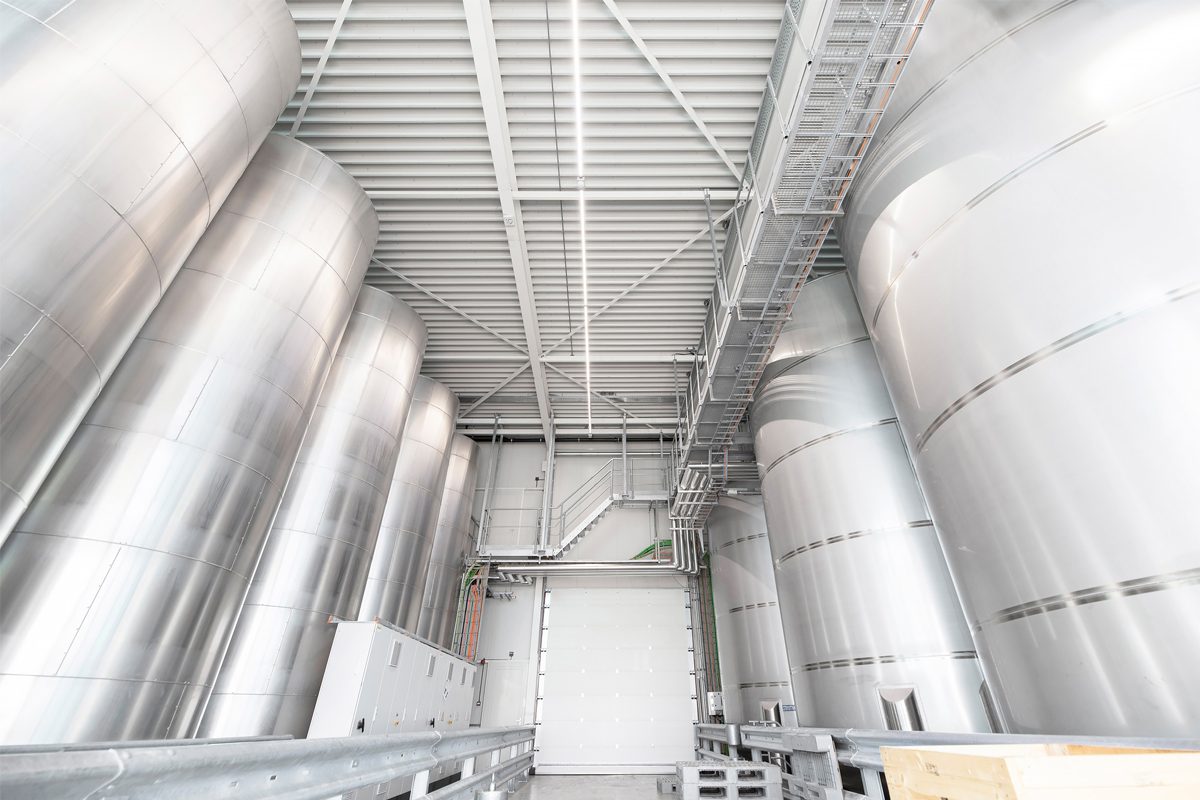
Horizontal VS Vertical Fermentation Tanks
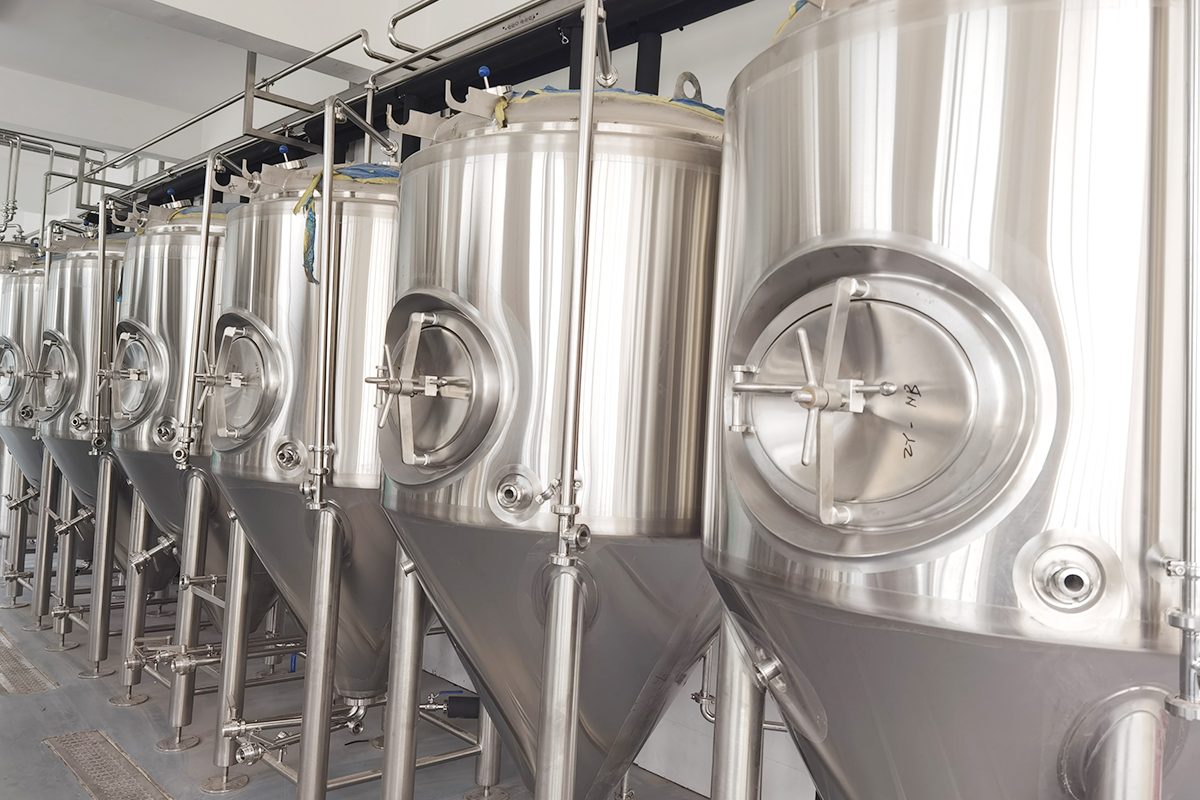
Overview of Fermentation Tanks in Brewing
The Role of Fermentation Tanks
Types of Fermentation Tanks
In the brewing industry, fermentation tanks come in various designs, each tailored to specific brewing needs. The two primary types are horizontal and vertical fermentation tanks.
- Horizontal Fermentation Tanks: These tanks are traditionally used in lager production and are characterized by their cylindrical shape lying on its side. Horizontal tanks offer a larger surface area for yeast to interact with the wort, promoting efficient yeast sedimentation and natural carbonation. They are often preferred for producing clear, crisp beers where yeast management is critical.
- Vertical Fermentation Tanks: Vertical tanks, which are more commonly used in modern brewing operations, are cylindrical vessels oriented upright. These tanks are favored for their space efficiency, allowing breweries to maximize their production capacity within a limited footprint. Vertical tanks are versatile, suitable for a wide range of beer styles, and are often integrated with advanced temperature and pressure control systems to ensure consistent fermentation results.
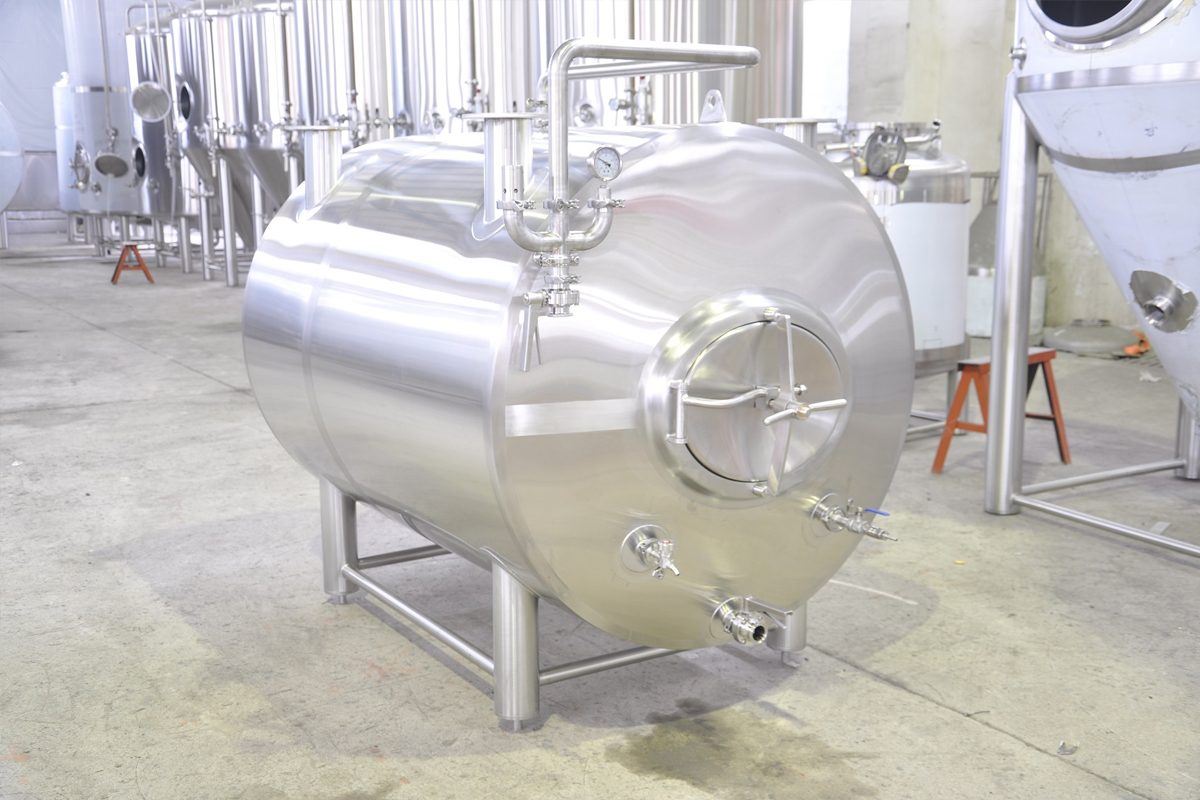
Horizontal Fermentation Tanks
Design and Structure
Advantages of Horizontal Fermentation Tanks
- Efficient Yeast Settling: The wide surface area of the horizontal tank promotes fast and efficient yeast settling, which helps produce clear, crisp lager.
- Improved Pressure Management: Horizontal tanks are particularly well-suited for managing pressure, making them ideal for beers that require natural carbonation.
- Stackability: The design allows for horizontal tanks to be stacked, saving valuable floor space in breweries with limited vertical height.
- Ease of Cleaning: The structure of horizontal tanks makes them relatively easy to clean and maintain, with accessible manways and ports.
Disadvantages of Horizontal Fermentation Tanks
- Space Requirements: Despite their stackability, horizontal tanks require more horizontal floor space, which can be a drawback in breweries with limited room.
- Limited Versatility: Horizontal tanks are less suitable for beer styles that benefit from prolonged yeast suspension, such as ales, where a more complex flavor profile is desired.
- Higher Initial Costs: The specialized design and construction of horizontal tanks can result in higher initial investment costs, particularly for larger-capacity tanks.
Specific Applications
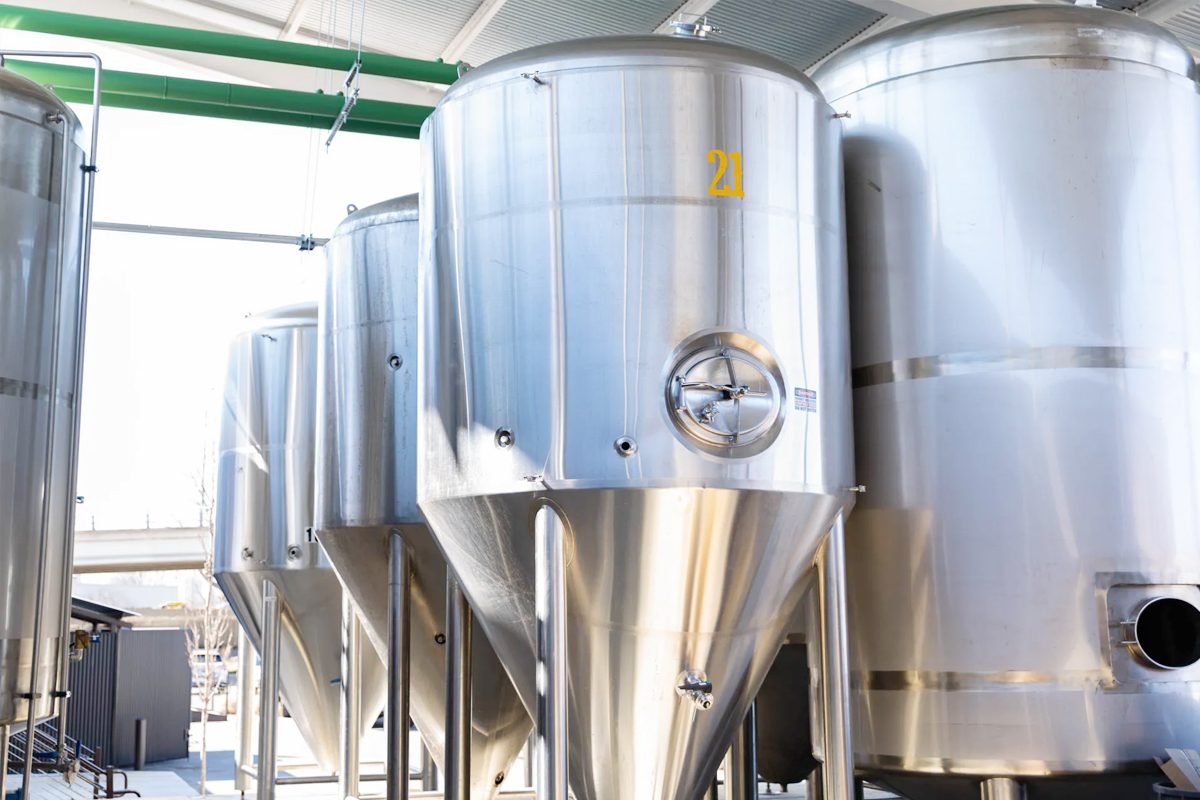
Vertical Fermentation Tanks
Design and Structure
Advantages of Vertical Fermentation Tanks
- Space Efficiency: Vertical fermentation tanks take up less horizontal space, allowing breweries to maximize production capacity in limited floor areas. This is particularly beneficial for large-scale operations.
- Versatility: The design of vertical tanks makes them suitable for a wide range of beer styles, from ales to lagers, providing flexibility in production.
- Improved Yeast Suspension: The taller design of vertical tanks helps keep yeast in suspension longer, promoting thorough fermentation and contributing to more complex flavor profiles in certain beers.
- Modern Integration: Vertical tanks are easily integrated with advanced brewing technologies, including automated temperature control, pressure management, and CIP systems, enhancing overall brewing efficiency and consistency.
Disadvantages of Vertical Fermentation Tanks
- Temperature Gradients: The tall structure of vertical tanks can lead to temperature gradients, especially in larger tanks, which may require advanced systems to ensure uniform temperature control throughout the tank.
- Pressure Variability: Due to the height of vertical tanks, there can be variations in pressure within the tank, which might affect the consistency of the fermentation process, particularly in high-volume productions.
- Cleaning Challenges: Cleaning vertical tanks can be more challenging due to their height, requiring specialized equipment or systems to ensure thorough maintenance.
Specific Applications
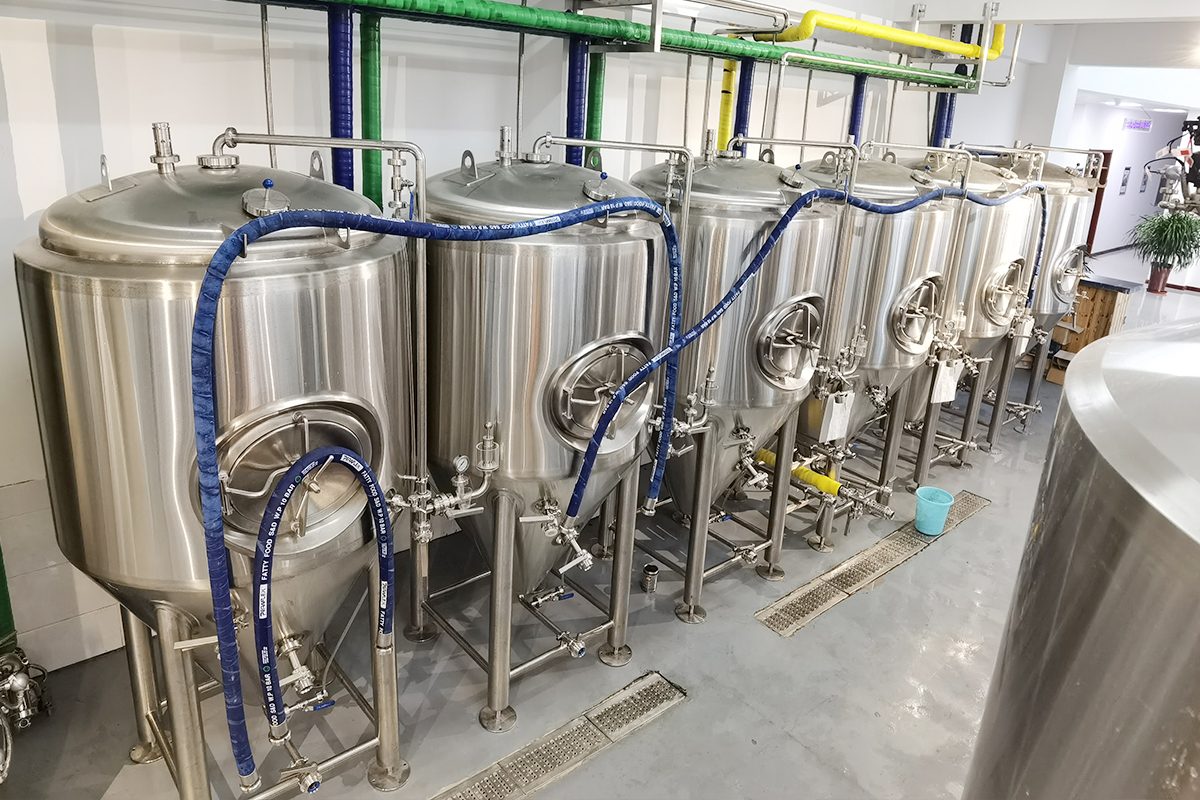
Comparative Analysis: Horizontal VS Vertical Fermentation Tanks
Impact on Beer Quality
When it comes to beer quality, the choice between horizontal and vertical fermentation tanks can significantly influence the final product’s characteristics.
- Horizontal Fermentation Tanks: These tanks excel in producing beers with a clean and crisp profile, particularly lagers. The larger surface area in horizontal tanks allows for efficient yeast sedimentation, which helps in producing a clear beer with minimal yeast flavors. This design also supports natural carbonation, enhancing the beer’s mouthfeel and overall quality. Horizontal tanks are ideal for breweries focusing on traditional beer styles that require precise control over clarity and carbonation.
- Vertical Fermentation Tanks: Vertical tanks, with their taller structure, encourage yeast suspension, which can result in a more complex flavor profile, especially in ales. The vertical design promotes thorough fermentation, which can enhance the development of esters and other flavor compounds, contributing to the beer’s depth and richness. Vertical tanks are versatile and can be used effectively for both ales and lagers, offering brewers the ability to produce a wide range of beer styles with distinct flavor characteristics.
Space and Cost Considerations
The spatial footprint and cost implications of fermentation tanks are critical factors for breweries, especially those with limited resources.
- Horizontal Fermentation Tanks: Horizontal tanks require more horizontal space, which can be a limitation for breweries operating in smaller facilities. While their stackable design offers some space-saving benefits, the need for a larger floor area may increase the overall operational footprint. Additionally, horizontal tanks can have higher initial costs due to their specialized design and construction, particularly for larger capacities.
- Vertical Fermentation Tanks: Vertical tanks are more space-efficient, requiring less horizontal floor space, making them ideal for breweries with limited area but high production demands. Their upright design allows for greater capacity within a smaller footprint, which can be a significant advantage in large-scale operations. In terms of cost, vertical tanks may be more economical in terms of space utilization and integration with existing brewing systems, although advanced features may add to the initial investment.
Operational Efficiency
Efficiency in the brewing process can help maintain production consistency and meet market demands.
- Horizontal Fermentation Tanks: Horizontal tanks offer efficient yeast management and pressure control, which can lead to a more consistent fermentation process, especially in lagers. However, their need for more space and potentially more complex cleaning processes can reduce operational efficiency in smaller or more automated breweries.
- Vertical Fermentation Tanks: Vertical tanks often provide better integration with automated brewing systems, enhancing overall operational efficiency. Their design supports efficient temperature and pressure control, which helps maintain consistency in high-volume production. Vertical tanks are also easier to clean with CIP systems, reducing downtime between batches and improving overall productivity.
Flexibility and Scalability
The ability to adapt to different production needs and scale operations is beneficial to the development of breweries.
- Horizontal Fermentation Tanks: Horizontal tanks are somewhat specialized, making them less flexible for breweries looking to produce a wide range of beer styles. They are best suited for specific applications like lager production, which can limit their use in more diverse brewing operations. Scaling with horizontal tanks can be challenging due to space constraints and higher costs associated with larger tank sizes.
- Vertical Fermentation Tanks: Vertical tanks offer greater flexibility, accommodating a wide range of beer styles from ales to lagers. Their design is conducive to scaling, as they can be easily integrated into existing production lines without significantly increasing the operational footprint. Vertical tanks’ adaptability makes them a preferred choice for breweries planning to expand their product range or increase production capacity.
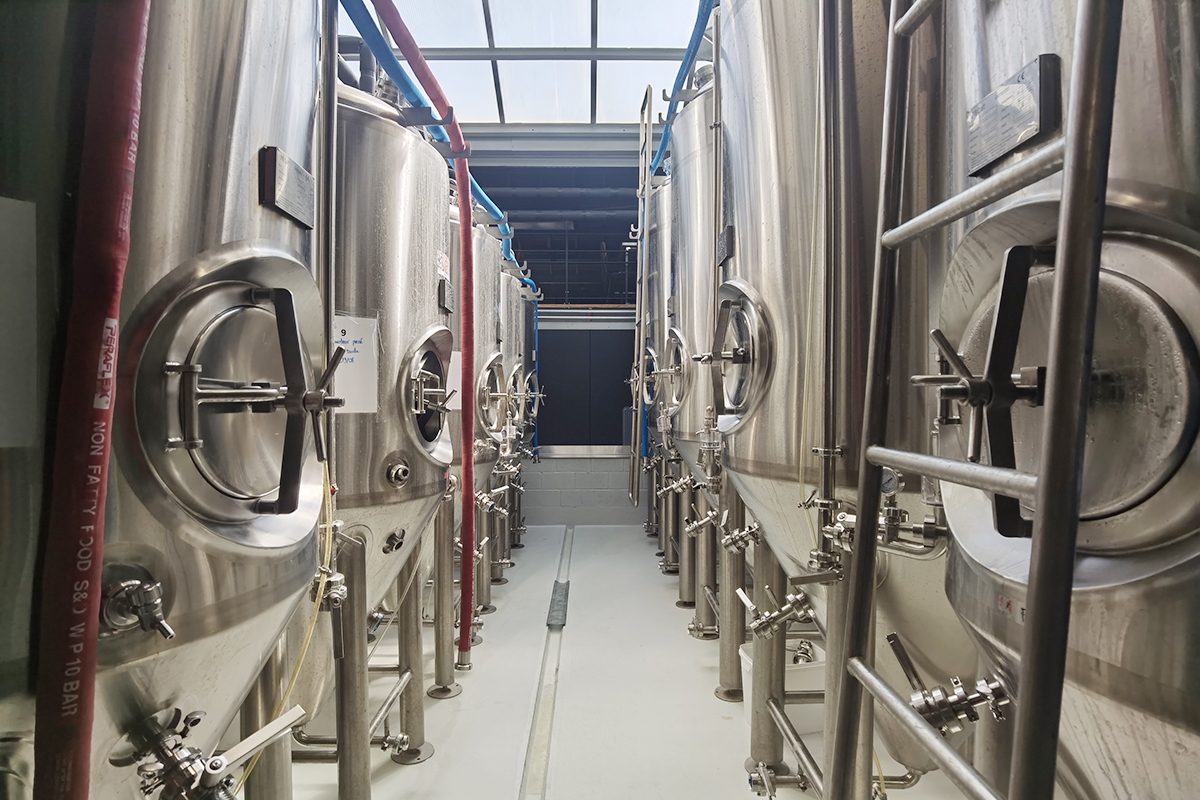
Choosing the Right Fermentation Tank for Your Brewery
Assessing Your Brewery’s Needs
Before deciding between horizontal and vertical fermentation tanks, it’s important to conduct a thorough assessment of your brewery’s unique requirements. Consider the following:
- Beer Styles: What types of beer do you primarily produce? Horizontal tanks are ideal for lagers due to their ability to promote yeast sedimentation and clarity, while vertical tanks offer versatility, suitable for both ales and lagers.
- Production Volume: Consider your current production capacity and future growth plans. Vertical tanks are generally more space-efficient, making them suitable for breweries with high production demands and limited floor space.
- Space Availability: Evaluate the available space in your brewery. Horizontal tanks require more horizontal floor space, while vertical tanks are better suited for facilities with limited area but ample vertical space.
- Operational Workflow: How do your brewing operations function? Vertical tanks integrate well with automated systems, enhancing efficiency and consistency, while horizontal tanks may require more manual intervention, particularly in cleaning and maintenance.
Cost and Budget Considerations
The financial aspect is a significant factor when choosing between horizontal and vertical fermentation tanks. Here’s how to approach it:
- Initial Investment: Horizontal tanks tend to be more expensive due to their specialized design and the need for more space, which could also lead to higher construction or renovation costs. Vertical tanks, on the other hand, may have a higher cost per unit due to advanced features but can be more economical in terms of space utilization and integration with automated systems.
- Operational Costs: Consider the long-term operational costs associated with each type of tank. Horizontal tanks might lead to higher utility costs due to their larger footprint and potential inefficiencies in space heating or cooling. Vertical tanks, with their space-saving design, can reduce overhead costs related to facility maintenance and energy consumption.
- Return on Investment (ROI): Evaluate the potential ROI based on your production scale and product range. Vertical tanks offer flexibility and scalability, which can lead to a quicker ROI if you plan to expand your product line or increase production capacity. Horizontal tanks, while more specialized, may offer a strong ROI for breweries focusing on high-quality lager production.
Long-Term Considerations
When selecting a fermentation tank, it’s essential to think beyond immediate needs and consider the long-term implications for your brewery:
- Scalability: Vertical tanks provide greater scalability, allowing you to expand production without significantly increasing your brewery’s footprint. This makes them a prudent choice for breweries with growth ambitions. Horizontal tanks, while excellent for certain styles, may limit scalability due to space constraints.
- Future-Proofing: Consider how your choice of tank aligns with industry trends and technological advancements. Vertical tanks, with their compatibility with automated systems, offer a future-proof solution as the brewing industry continues to innovate. Horizontal tanks may require additional adaptations or investments to keep up with technological changes.
- Resale Value: The resale value of your equipment can be a factor if you plan to upgrade or change your brewing setup in the future. Vertical tanks, due to their widespread use and versatility, may have a higher resale value and be easier to sell on the secondary market. Horizontal tanks, being more specialized, may have a more limited market, potentially affecting their resale value.
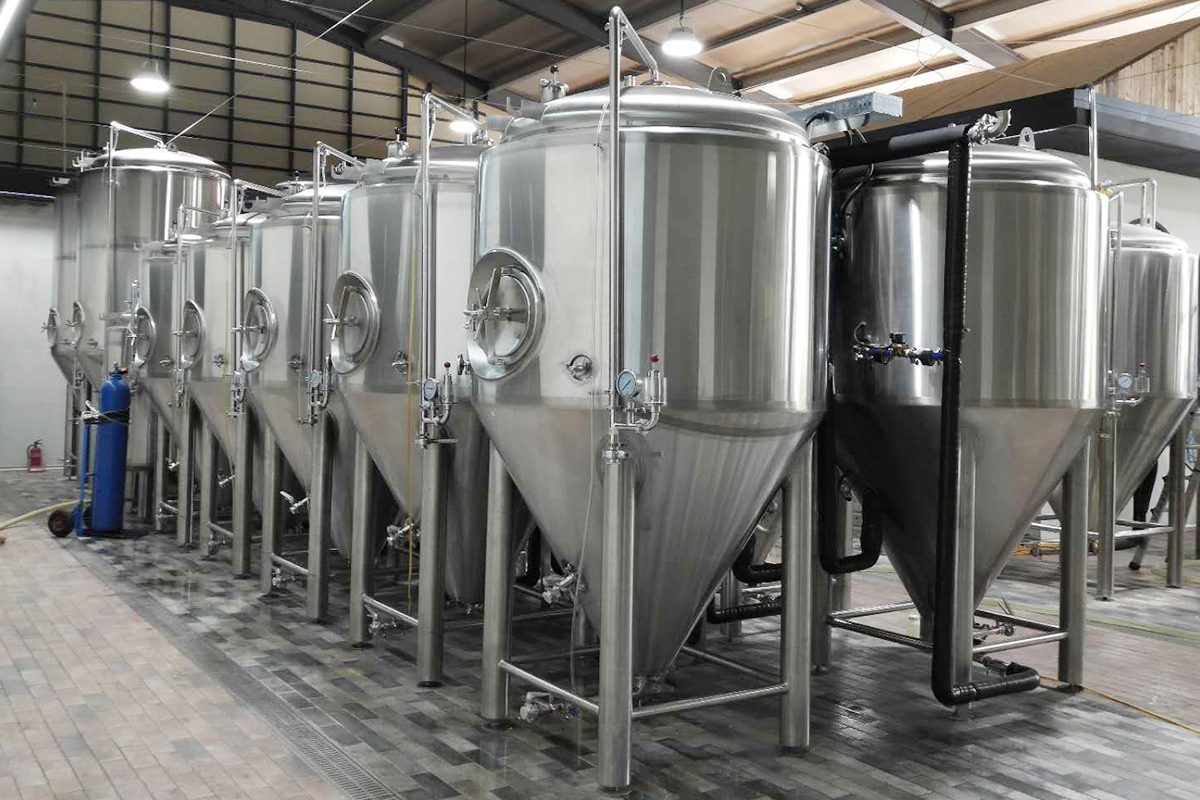
Summary
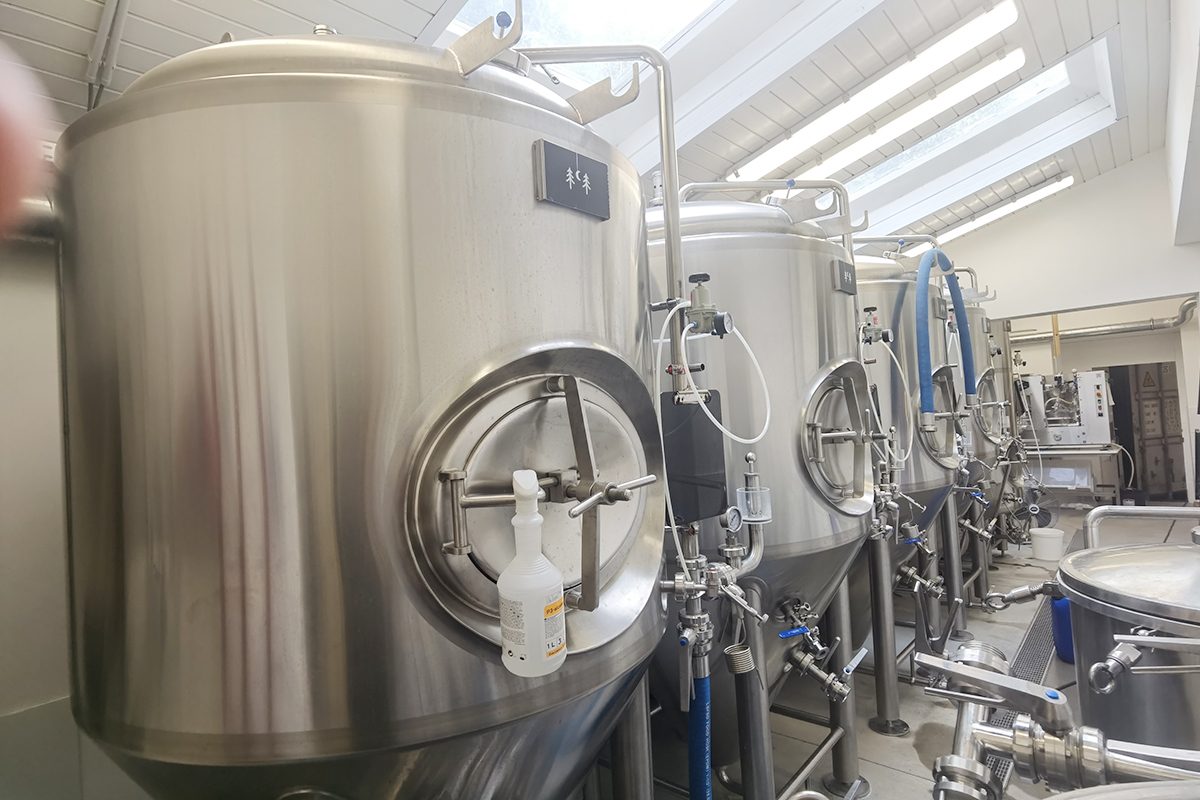