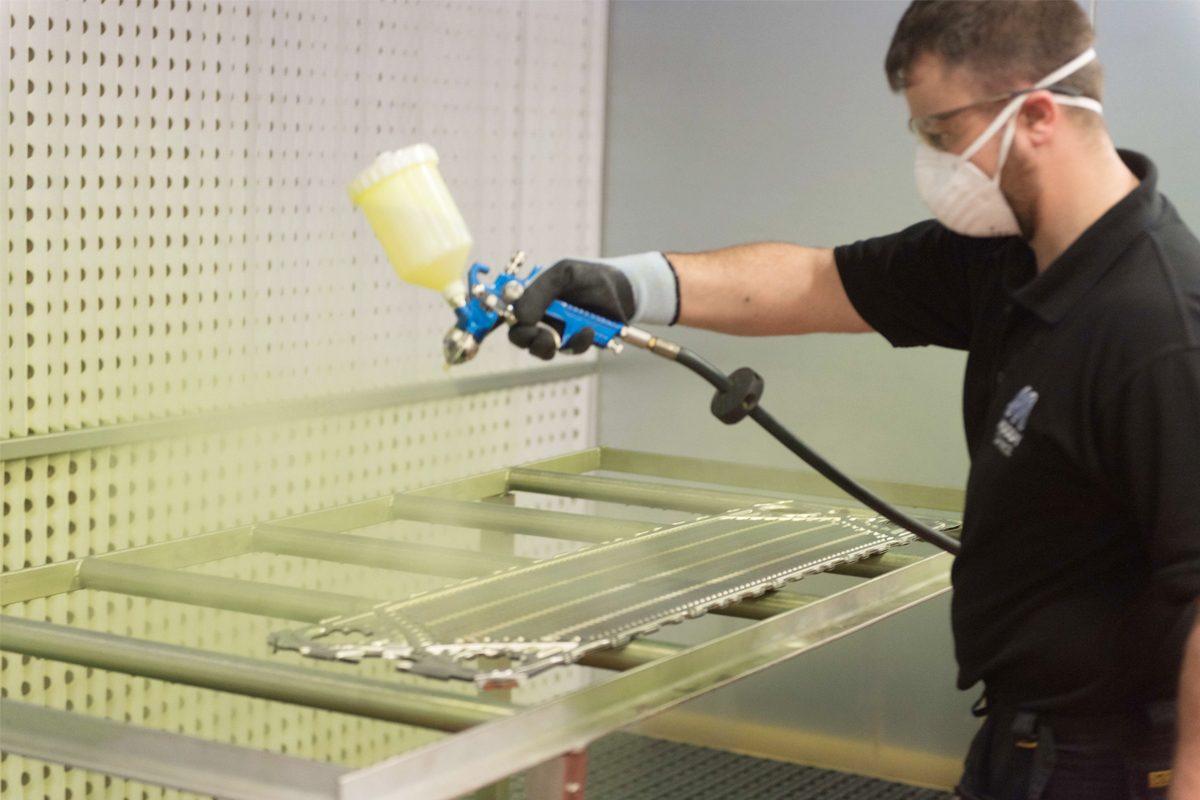
Heat Exchanger Plate Cleaning Method
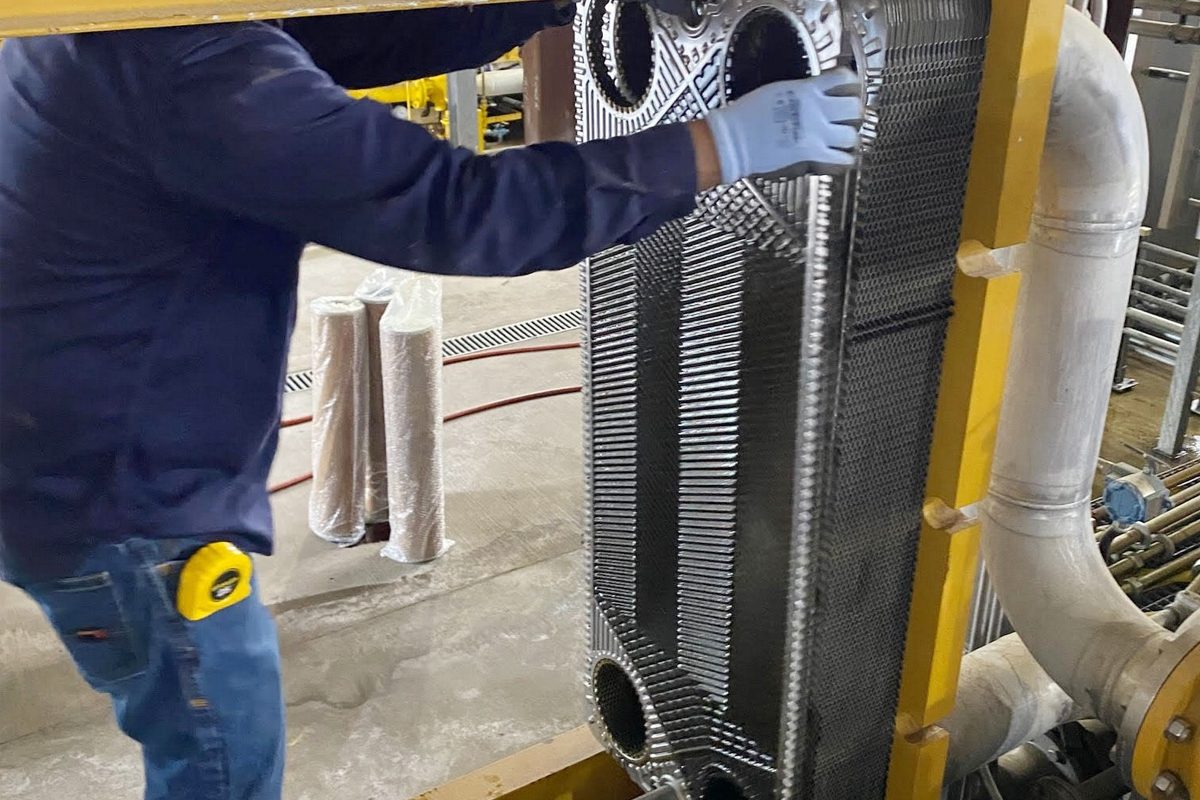
Understanding Alcohol Content in Beer
Maintaining Efficiency
Prolonging Equipment Life
Preventing Contamination
Reducing Downtime
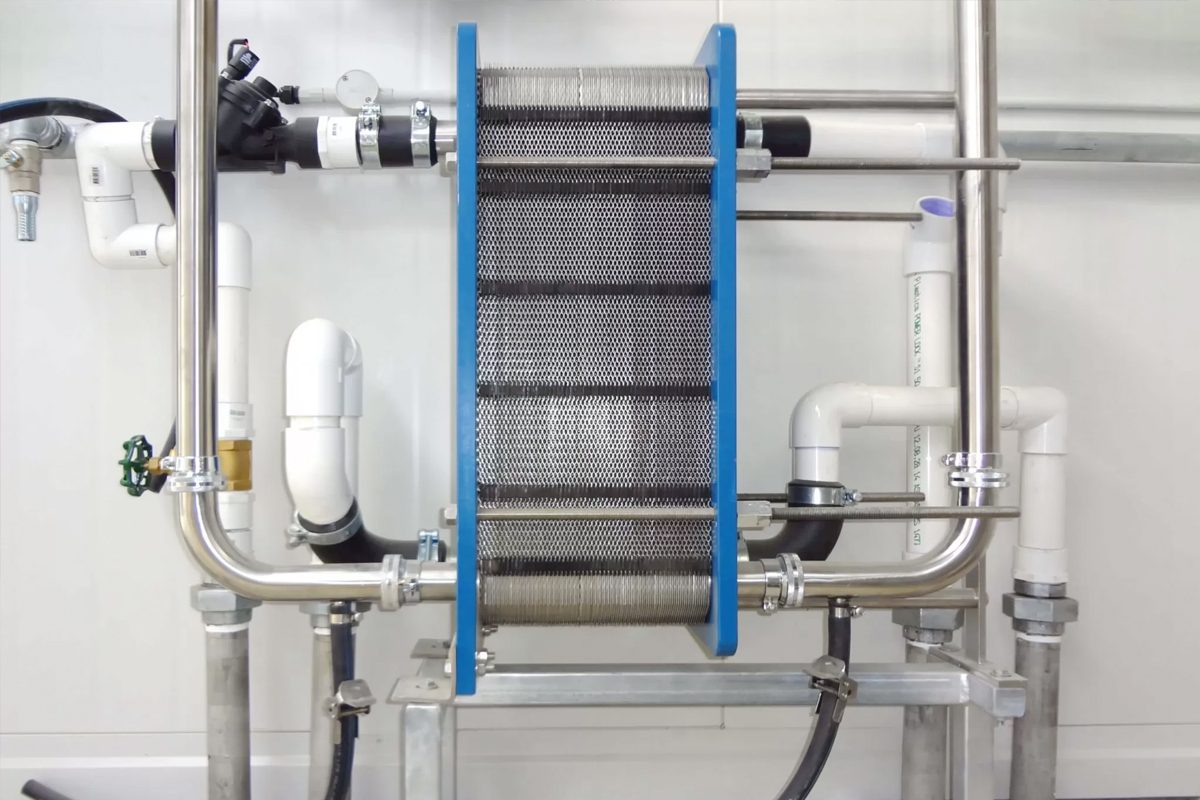
Types of Fouling in Heat Exchanger Plates
Scaling
Particulate Fouling
Biological Fouling
Chemical Fouling
Corrosion Fouling
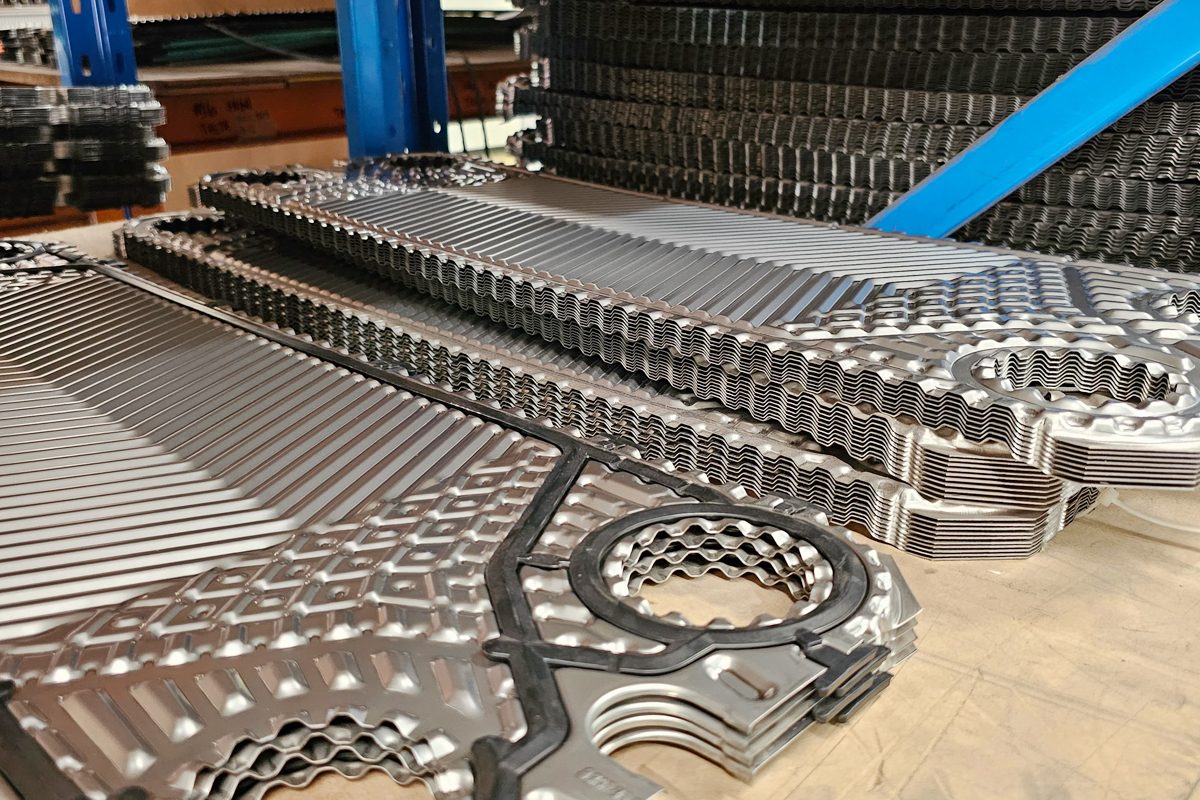
Common Heat Exchanger Plate Cleaning Methods
Mechanical Cleaning
Mechanical cleaning involves the physical removal of fouling deposits from the heat exchanger plates. This method is particularly effective for removing hard, stubborn scales and particulate deposits. Common techniques include:
- Brushing: Manual or motorized brushes are used to scrub the surfaces of the plates, dislodging and removing buildup. This method is effective for light to moderate fouling but may require care to avoid damaging the plate surface.
- Scraping: For more severe fouling, scrapers made of metal or plastic can be used to remove thick deposits. Care must be taken to avoid scratching or damaging the plate material during the process.
Chemical Cleaning
Chemical cleaning involves the use of specially formulated chemicals to dissolve or loosen fouling deposits, making them easier to remove. This method is particularly effective for dealing with scaling, biofouling, and chemical deposits. The process typically involves:
- Acid Cleaning: Acidic solutions, such as hydrochloric or citric acid, are used to dissolve mineral scale deposits like calcium carbonate. This method is effective for descaling but must be carefully controlled to avoid damaging the plates.
- Alkaline Cleaning: Alkaline solutions, such as sodium hydroxide, are used to break down organic fouling like grease, oils, and biological matter. This method is often used in combination with acid cleaning for a comprehensive cleaning process.
Cleaning-In-Place (CIP)
Cleaning-In-Place (CIP) is an automated cleaning method that allows heat exchanger plates to be cleaned without disassembly. In this process, cleaning solutions are circulated through the heat exchanger under controlled conditions, effectively removing fouling deposits. CIP system is commonly used in breweries due to its convenience and efficiency, particularly for:
- Routine Maintenance: CIP systems are ideal for regular, scheduled cleaning, minimizing downtime, and maintaining consistent operational efficiency.
- High-Volume Operations: For large-scale brewing operations, CIP offers a time-efficient solution that reduces labor costs and ensures thorough cleaning.
Ultrasonic Cleaning
Ultrasonic cleaning uses high-frequency sound waves to create microscopic bubbles in a cleaning solution. These bubbles implode upon contact with the fouled surface, effectively dislodging and removing deposits. This method is particularly advantageous for:
- Delicate Cleaning: Ultrasonic cleaning is gentle on the plates, making it suitable for removing fine particulate fouling and biofouling without damaging the plate surfaces.
- Complex Geometries: The ultrasonic process can reach into crevices and tight spaces that are difficult to clean mechanically or chemically.
Hydroblasting
Hydroblasting, or high-pressure water jetting, involves directing a powerful stream of water at the heat exchanger plates to remove fouling deposits. This method is particularly effective for:
- Removing Tough Deposits: Hydroblasting can effectively remove hard scales, corrosion products, and other stubborn fouling materials.
- Non-Chemical Cleaning: As a purely mechanical process, hydroblasting eliminates the need for chemicals, making it an environmentally friendly option.

Steps for Effective Heat Exchanger Plate Cleaning
Preparation and Safety Measures
Before beginning the cleaning process, thorough preparation is required and safety protocols are followed to protect personnel and equipment. Key steps include:
- System Shutdown: Ensure the heat exchanger is fully shut down and depressurized to prevent accidents.
- Personal Protective Equipment (PPE): Equip personnel with appropriate PPE, including gloves, goggles, and protective clothing, to safeguard against chemical exposure and physical hazards.
- Ventilation and Containment: Ensure proper ventilation in the cleaning area and set up containment measures to manage any chemical spills or water runoff.
- Tool and Equipment Setup: Gather all necessary tools, cleaning agents, and equipment, and ensure they are in proper working order before starting the cleaning process.
Inspection Before Cleaning
Conducting a thorough inspection before cleaning helps assess the extent and type of fouling present, as well as the condition of the heat exchanger plates. Important steps include:
- Visual Inspection: Examine the plates for visible signs of fouling, such as scaling, particulate deposits, or biofilm. Look for any signs of corrosion or damage that may require special attention.
- Performance Assessment: Review operational data, such as pressure drops and temperature differentials, to identify any performance issues that could be related to fouling.
- Damage Identification: Identify any plates that are damaged or corroded and may need to be repaired or replaced during the cleaning process.
Selection of Cleaning Method
Based on the findings from the inspection, select the most suitable cleaning method(s) to address the specific type of fouling and condition of the plates. Consider the following:
- Type of Fouling: Match the cleaning method to the type of fouling—mechanical methods for hard scales, chemical methods for mineral deposits, and ultrasonic cleaning for delicate or complex areas.
- Material Compatibility: Ensure that the chosen cleaning agents and methods are compatible with the material of the plates to avoid corrosion or damage.
- Brewery Requirements: Take into account the brewery’s operational requirements, such as the need for minimal downtime or the availability of specific cleaning equipment.
Execution of the Cleaning Process
With the cleaning method selected, the next step is to execute the cleaning process, following these guidelines:
- Mechanical Cleaning: If mechanical methods are chosen, use brushes, scrapers, or hydro blasting to physically remove fouling deposits. Ensure even coverage and avoid excessive force that could damage the plates.
- Chemical Cleaning: For chemical cleaning, carefully mix and apply the cleaning solution, following the manufacturer’s instructions. Allow the solution to circulate or soak as needed to dissolve the deposits before thoroughly rinsing the plates.
- CIP or Ultrasonic Cleaning: For CIP systems, set the appropriate parameters and allow the system to run its cycle. For ultrasonic cleaning, submerge the plates in the ultrasonic bath and monitor the process to ensure effective cleaning.
Post-Cleaning Inspection and Testing
After the cleaning process is complete, a thorough post-cleaning inspection and testing phase can help verify cleaning effectiveness and plate condition. Key steps include:
- Visual Inspection: Re-examine the plates to ensure all fouling has been removed and check for any signs of damage that may have occurred during cleaning.
- Performance Testing: Conduct operational tests, such as pressure and flow rate measurements, to confirm that the heat exchanger is functioning optimally.
- Documentation: Record the cleaning process, including the methods used, any issues encountered, and the results of the post-cleaning inspection and tests. This documentation is valuable for future maintenance planning.
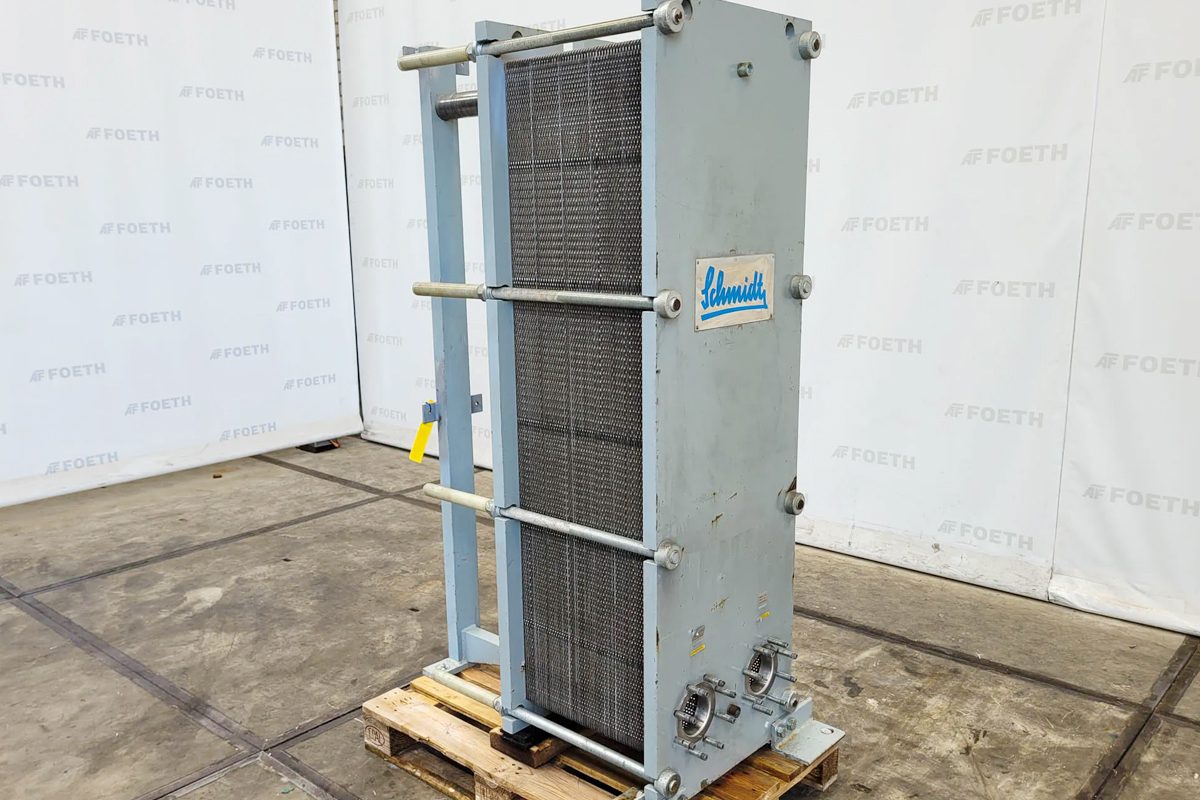
Maintenance Practices to Minimize Fouling
Regular Monitoring
Regular monitoring of heat exchanger performance can help detect early fouling and other problems that can affect efficiency. Key monitoring practices include:
- Performance Tracking: Continuously monitor key performance indicators (KPIs) such as temperature differentials, pressure drops, and flow rates. Sudden changes in these metrics can indicate the onset of fouling.
- Scheduled Inspections: Conduct periodic visual inspections of the heat exchanger plates to check for signs of fouling or wear. Early detection allows for timely intervention before the fouling becomes severe.
- Data Analysis: Use historical data to identify trends in performance degradation, which can help predict when fouling is likely to occur and schedule preventive maintenance accordingly.
Use of Anti-Fouling Coatings
Applying anti-fouling coatings to heat exchanger plates can significantly reduce the accumulation of deposits. These coatings work by creating a surface that is resistant to fouling, making it more difficult for scale, biofilms, and particulates to adhere. Key benefits of anti-fouling coatings include:
- Reduced Cleaning Frequency: With less fouling on the plates, the need for cleaning is reduced, lowering maintenance costs and downtime.
- Prolonged Equipment Life: Anti-fouling coatings protect the plates from corrosive substances and biological growth, which can extend the life of the equipment.
- Enhanced Efficiency: By preventing the buildup of insulating deposits, anti-fouling coatings help maintain the heat exchanger’s efficiency over time.
Optimizing Operating Conditions
Optimizing the operating conditions of heat exchangers is another effective way to minimize fouling. By carefully controlling variables such as fluid velocity, temperature, and pH levels, breweries can reduce the likelihood of fouling. Consider the following strategies:
- Increase Fluid Velocity: Higher fluid velocities can prevent the settling of particulate matter and reduce the formation of scale by minimizing the time fluids spend in the heat exchanger.
- Control Temperature: Maintaining appropriate temperatures can reduce the risk of scaling and biofouling. For example, operating at temperatures that discourage the growth of microorganisms can prevent biofilm formation.
- Adjust pH Levels: Managing the pH of the fluids can prevent chemical reactions that lead to fouling. For instance, keeping the pH at a level that prevents the precipitation of minerals can reduce scaling.
Water Treatment and Filtration
Water quality is a critical factor in preventing fouling in heat exchangers. Implementing effective water treatment and filtration systems can significantly reduce the introduction of contaminants that cause fouling. Key practices include:
- Filtration Systems: Installing filtration systems to remove suspended solids, such as rust, sand, and other particulates, from the water before it enter the heat exchanger can prevent particulate fouling.
- Water Softening: Using water softening systems to remove calcium and magnesium ions from the water can prevent scaling, which is a common type of fouling in breweries.
- Chemical Treatment: Implementing chemical treatments, such as corrosion inhibitors and biocides, can prevent chemical and biological fouling by neutralizing corrosive elements and controlling microbial growth.
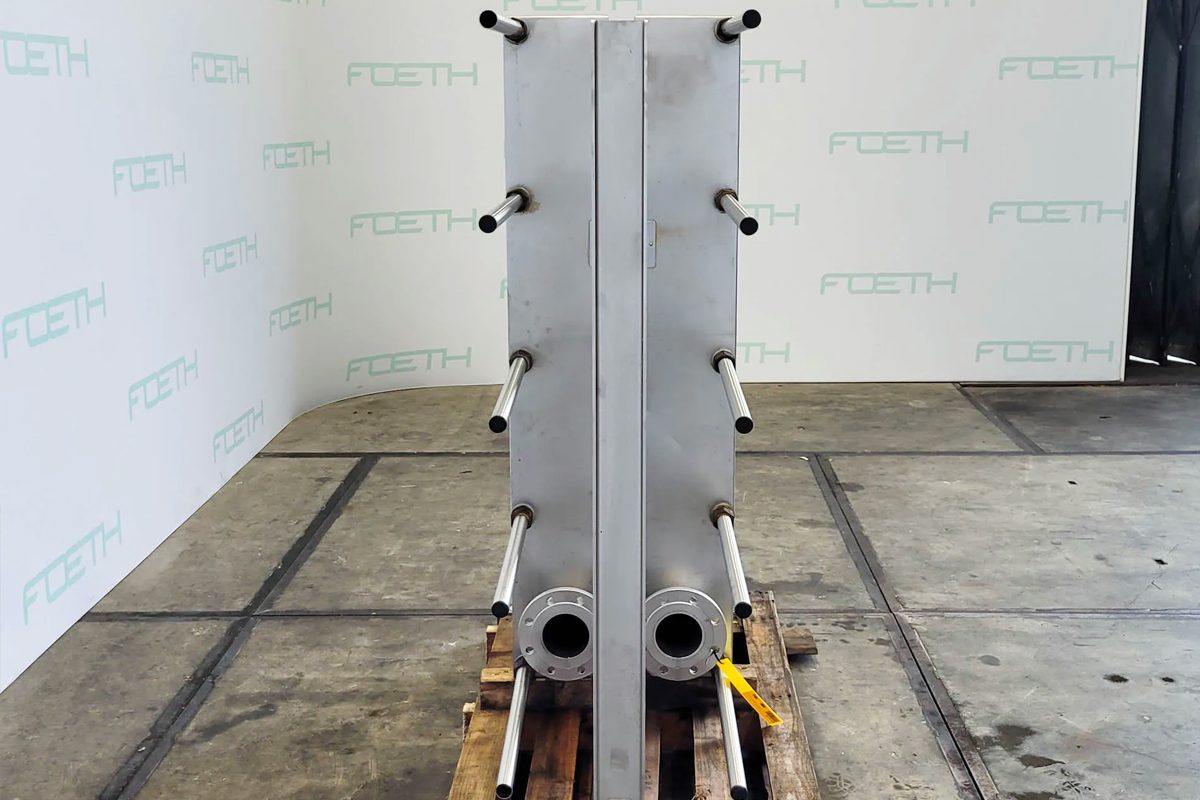
Best Practices for Extending Heat Exchanger Life
Scheduled Cleaning Intervals
Regularly scheduled cleaning intervals prevent dirt buildup on the heat exchanger plates. By adhering to a consistent cleaning schedule, breweries can ensure that the plates remain clean and functional, minimizing the risk of efficiency loss or equipment damage. Key considerations include:
- Customized Schedules: Develop cleaning schedules based on the specific operating conditions, such as the type of fluids used, temperature ranges, and historical fouling rates.
- Preventive Maintenance: Even if fouling appears minimal, adhering to the cleaning schedule prevents the accumulation of deposits that could lead to more significant issues if left unchecked.
- Efficiency Monitoring: Use performance data to adjust cleaning intervals as needed, ensuring that the heat exchangers are cleaned at the optimal frequency to maintain efficiency.
Proper Storage and Handling
Proper storage and handling of heat exchanger plates can also prevent damage to the equipment when not in use. This practice is particularly important for breweries that may have seasonal production cycles or periods of equipment downtime. Best practices include:
- Clean Before Storage: Always clean and dry the heat exchanger plates before storage to prevent corrosion, scaling, or biological growth during periods of inactivity.
- Controlled Environment: Store the plates in a dry, temperature-controlled environment to avoid exposure to moisture, extreme temperatures, or contaminants that could cause damage.
- Handling Precautions: Use appropriate tools and techniques when handling the plates to prevent physical damage, such as dents, scratches, or warping, which could affect the heat exchanger’s performance.
Documentation and Record Keeping
Maintaining thorough documentation and records of all maintenance activities, including cleaning, inspections, and repairs, can manage the long-term health of your heat exchanger. Key elements of effective documentation include:
- Maintenance Logs: Keep detailed records of all cleaning activities, including the methods used, dates of service, and any issues encountered. This information helps track the performance and condition of the heat exchangers over time.
- Inspection Reports: Document the findings of inspections, noting any signs of fouling, corrosion, or damage. This information is valuable for planning future maintenance and identifying trends that could indicate emerging problems.
- Historical Data: Maintain a comprehensive history of the heat exchanger’s performance, including pressure drops, temperature differentials, and other relevant metrics. This data can be used to optimize cleaning schedules and predict maintenance needs.
Training and Competency of Personnel
The knowledge and skills of those responsible for maintaining and cleaning the heat exchanger plates can help ensure that the equipment is properly maintained. Investing in training and competency development is essential to extending the life of your heat exchanger. Best practices include:
- Comprehensive Training: Provide thorough training on the various cleaning methods, safety protocols, and the specific requirements of the heat exchanger plates used in the brewery.
- Ongoing Education: Encourage ongoing education and skill development to keep personnel updated on the latest techniques, tools, and best practices in heat exchanger maintenance.
- Competency Assessments: Regularly assess the competency of personnel through evaluations or practical tests to ensure they can perform maintenance tasks effectively and safely.
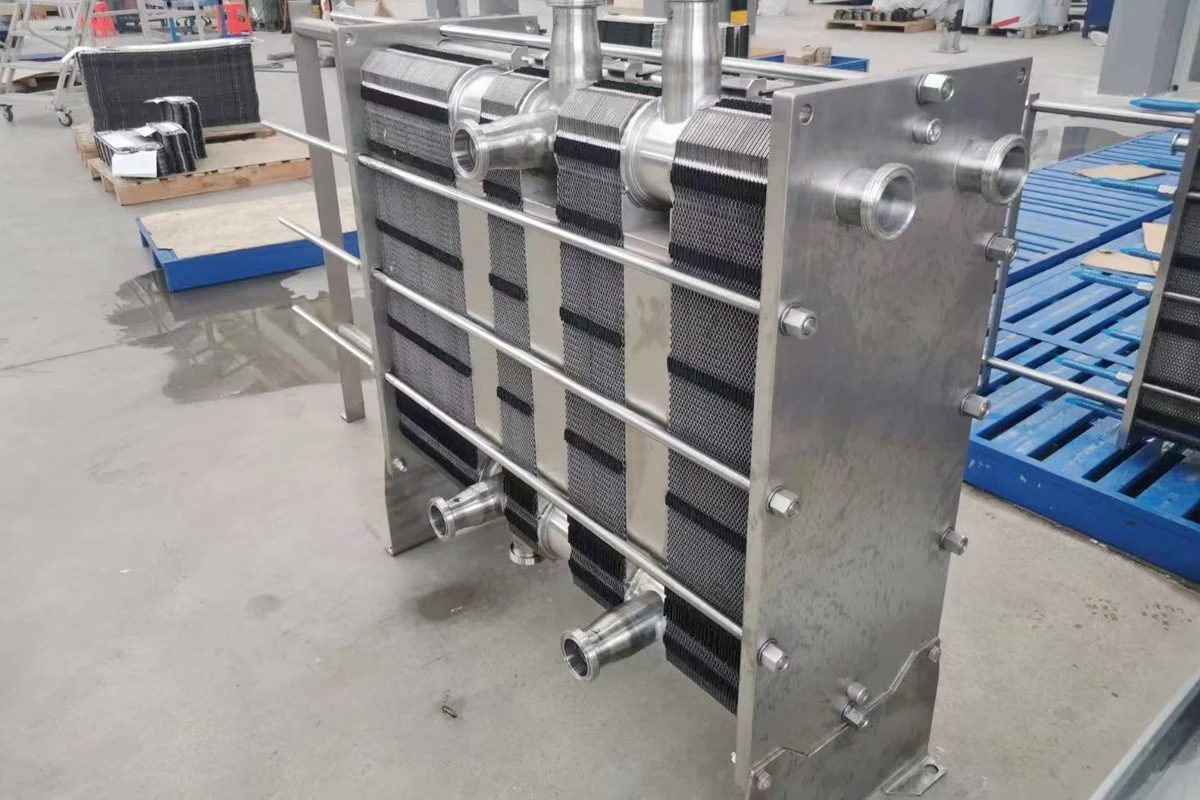
Summary
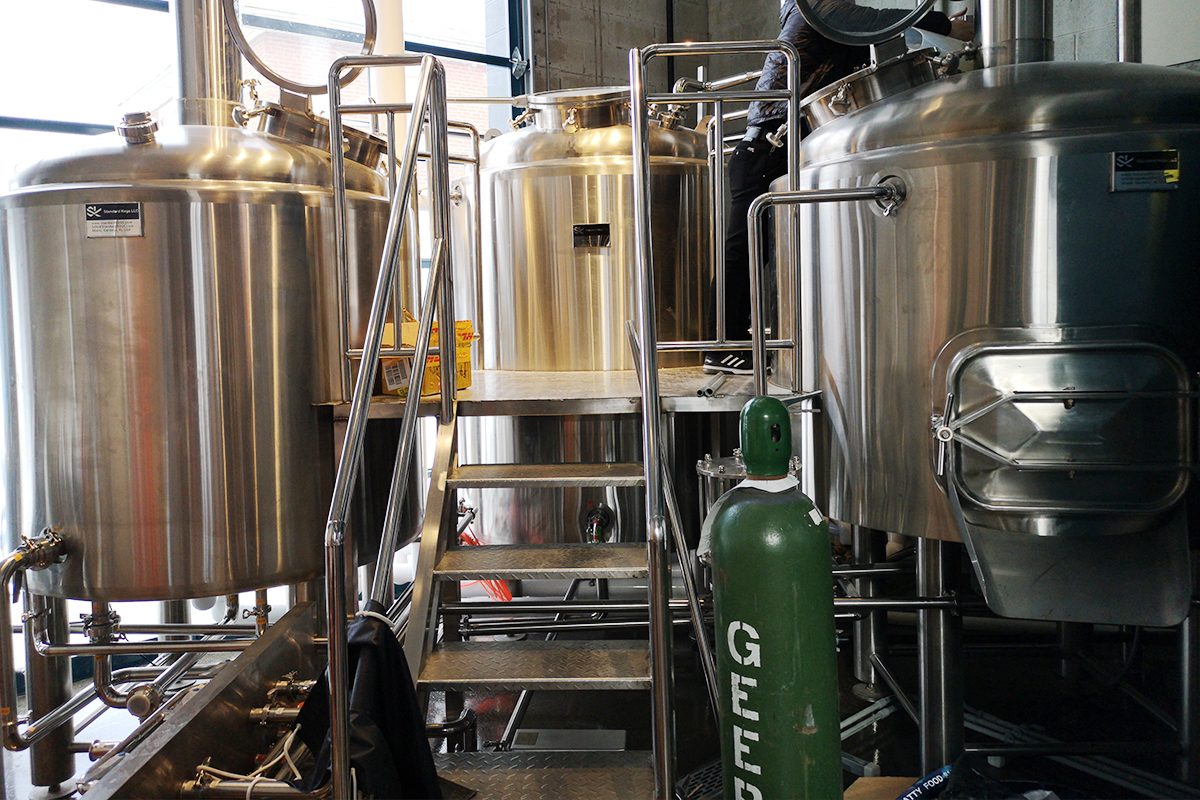