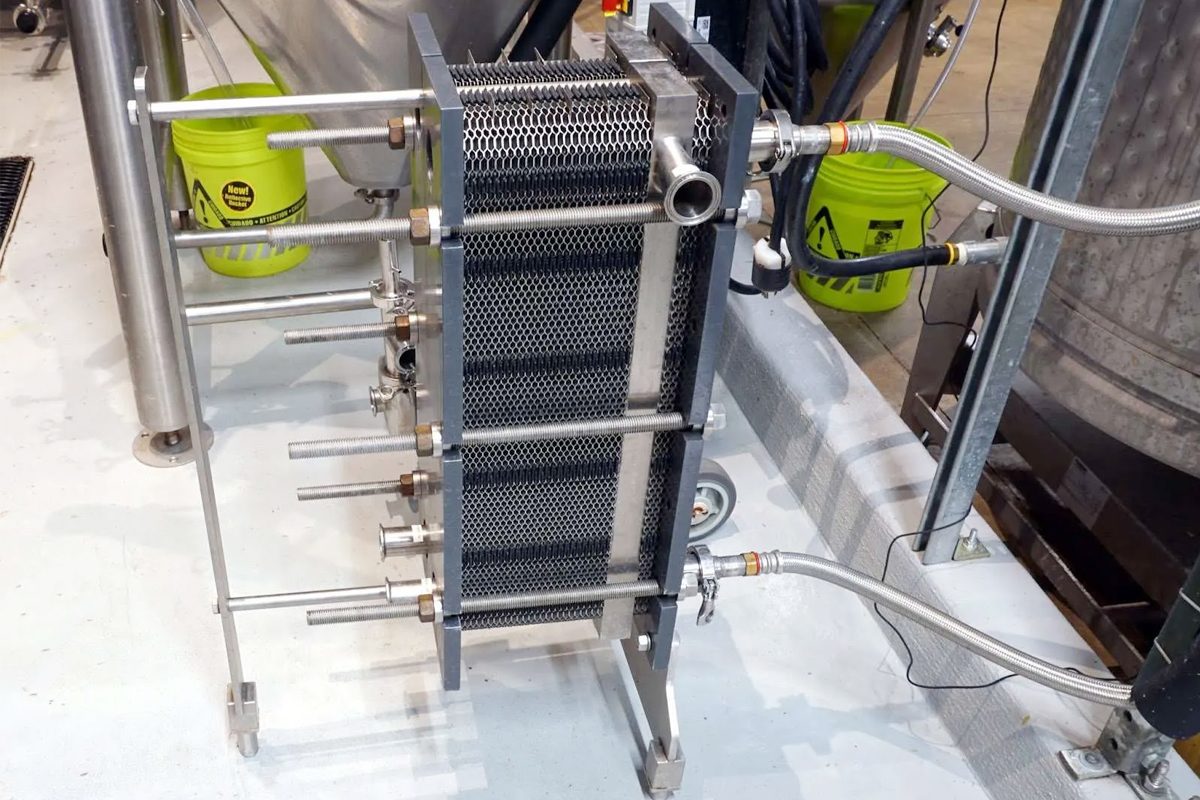
Guide To Brewery Plate Heat Exchangers
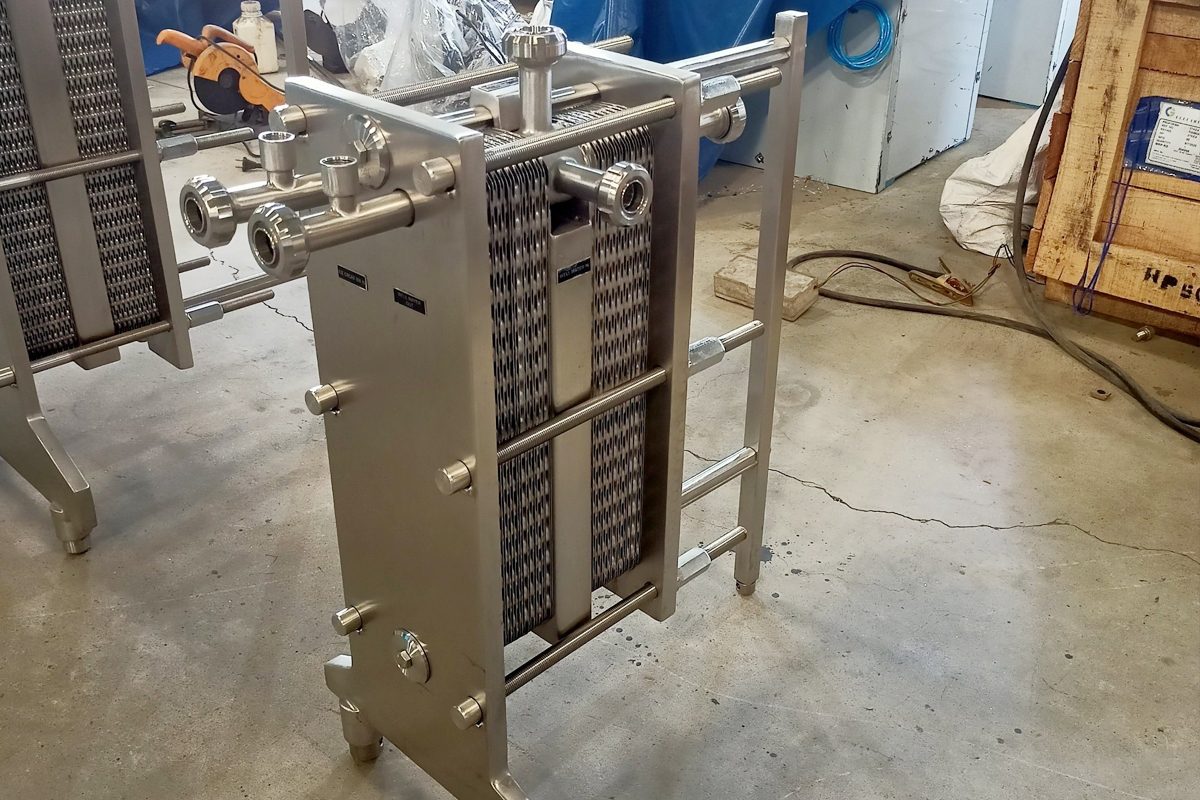
Introduction to Plate Heat Exchangers
What is a Plate Heat Exchanger?
Importance of Heat Exchangers in Brewing
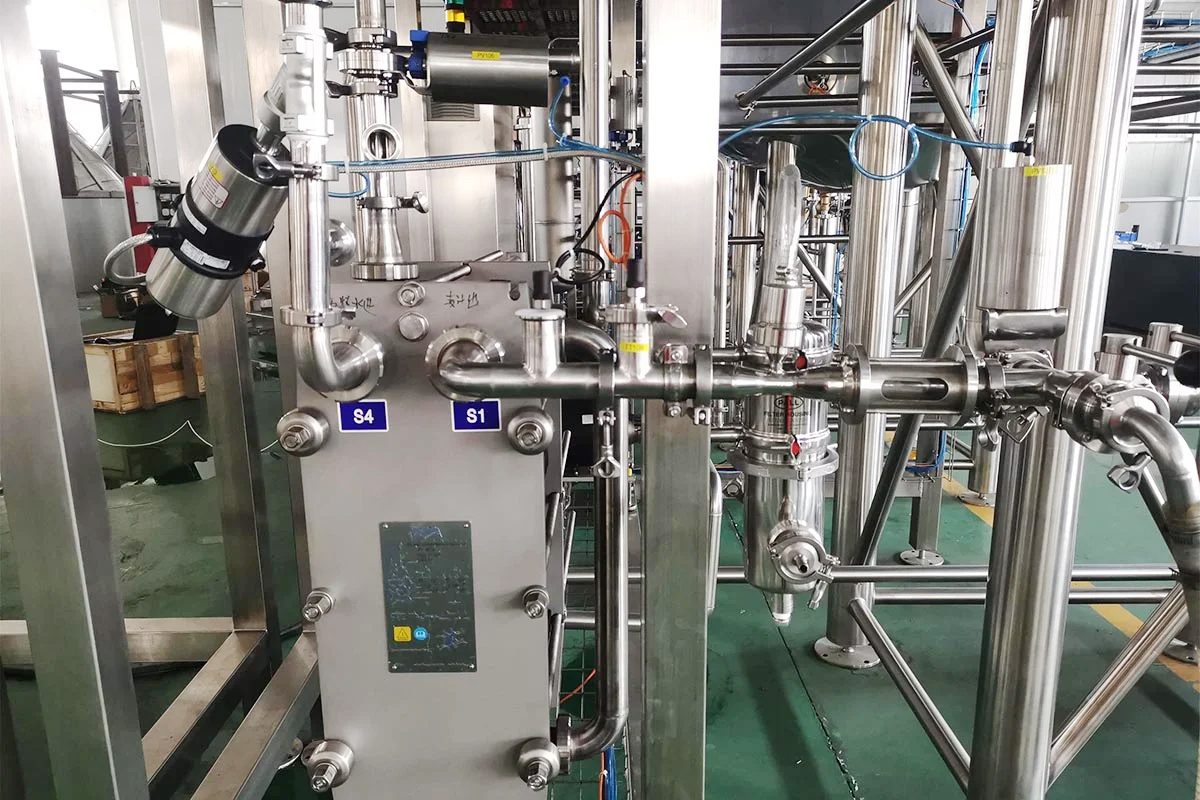
Types of Plate Heat Exchangers
Gasketed Plate Heat Exchangers
Gasketed plate heat exchangers are the most common type used in breweries. They consist of a series of thin, corrugated plates held together by a frame. Each plate is separated by a gasket, which seals the fluids and directs them into alternate channels. The modular design allows for easy expansion, maintenance, and cleaning.
- Flexibility: Easily customizable by adding or removing plates to adjust capacity.
- Maintenance: Plates can be removed and cleaned, and gaskets can be replaced.
- Application: Commonly used for wort cooling and pasteurization.
Brazed Plate Heat Exchangers
Brazed plate heat exchangers are compact, efficient, and highly durable. They are made by brazing thin stainless steel plates together using a filler metal, typically copper or nickel. This process creates a robust, leak-proof structure with no need for gaskets.
- Compact Design: Smaller footprint compared to gasketed PHEs, making them suitable for space-constrained breweries.
- Durability: Can withstand high pressure and high temperature.
- Application: Ideal for high-temperature applications and closed-loop systems.
Welded Plate Heat Exchangers
Welded plate heat exchangers offer the highest levels of durability and are typically used in applications where gaskets cannot withstand the operating conditions. The plates are welded together, eliminating the need for gaskets and making the unit highly resistant to corrosion and extreme temperatures.
- High Durability: Suitable for harsh conditions with high temperatures and pressures.
- Maintenance: Less maintenance is required compared to gasketed PHEs but harder to clean.
- Application: Often used in high-pressure pasteurization processes.
Semi-Welded Plate Heat Exchangers
Semi-welded plate heat exchangers combine the benefits of gasketed and welded PHEs. Some plates are welded together to form a sealed unit, while others are gasketed. This design allows for the handling of more aggressive fluids on the welded side while still permitting easy maintenance on the gasketed side.
- Versatility: Can handle a wider range of fluids and conditions.
- Maintenance: Easier to maintain than fully welded PHEs.
- Application: Used in applications requiring both durability and flexibility.
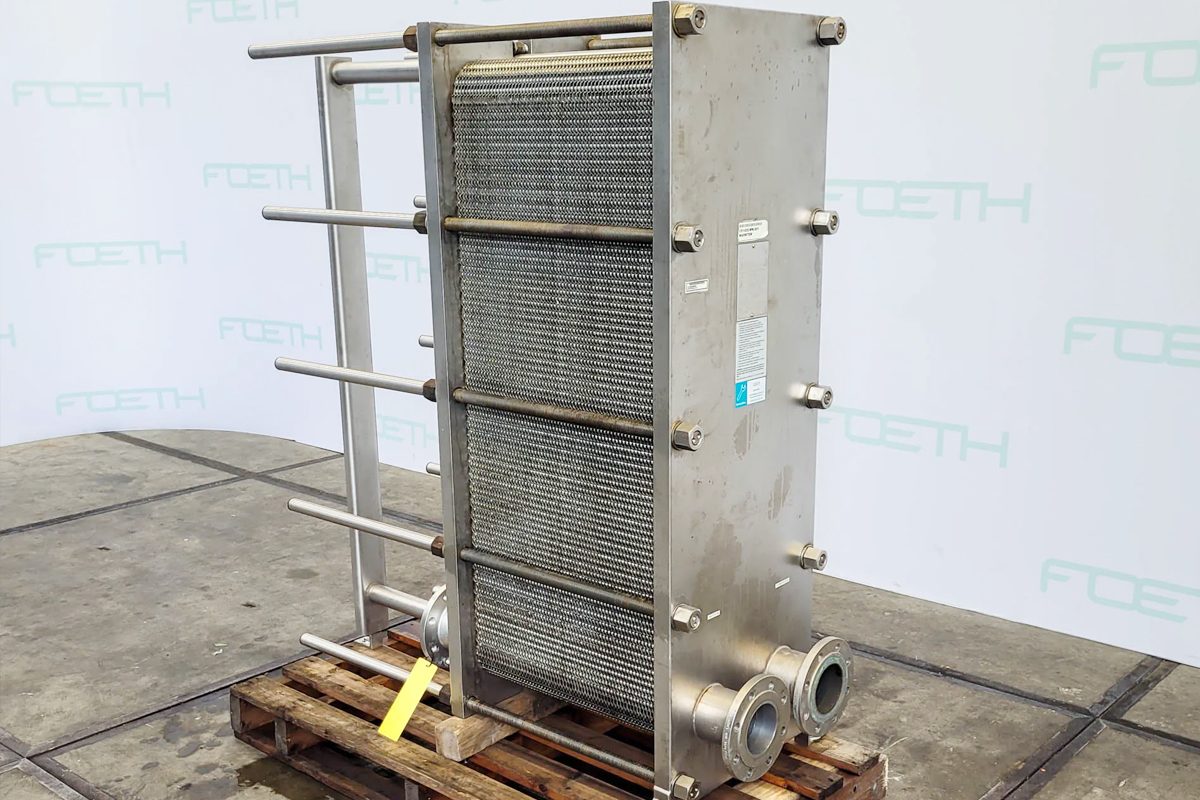
How Plate Heat Exchangers Work
Heat Transfer Mechanism
The primary function of a plate heat exchanger is to transfer heat from one fluid to another without mixing them. This is achieved by passing the fluids through alternating channels formed by the plates. As the fluids flow through these channels, heat is transferred from the hotter fluid to the cooler fluid through the thin metal plates.
- Counter-Flow Configuration: Most PHEs operate in a counter-flow arrangement, where the fluids flow in opposite directions. This maximizes the temperature difference across the plates, enhancing heat transfer efficiency.
- Thermal Efficiency: The corrugated design of the plates increases turbulence, which improves heat transfer by disrupting the boundary layer of fluid on the plate surfaces.
Flow Configuration
The flow configuration in a plate heat exchanger can be either single-pass or multi-pass, depending on the design and application requirements.
- Single-Pass Configuration: Both fluids pass through the heat exchanger once. This configuration is simpler and typically used in applications where the required temperature change is moderate.
- Multi-Pass Configuration: The fluids pass through the heat exchanger multiple times, increasing the temperature change capability. This configuration is used when a higher temperature difference is required.
Key Components of Plate Heat Exchangers
- Plates: The core component, typically made of stainless steel, with a corrugated design to increase the surface area and turbulence.
- Gaskets: Seals the plates and directs the flow of fluids into alternate channels.
- Frame: Holds the plates together and applies pressure to ensure a tight seal.
- Nozzles: Connect the heat exchanger to the brewery’s piping system, allowing fluids to enter and exit the unit.
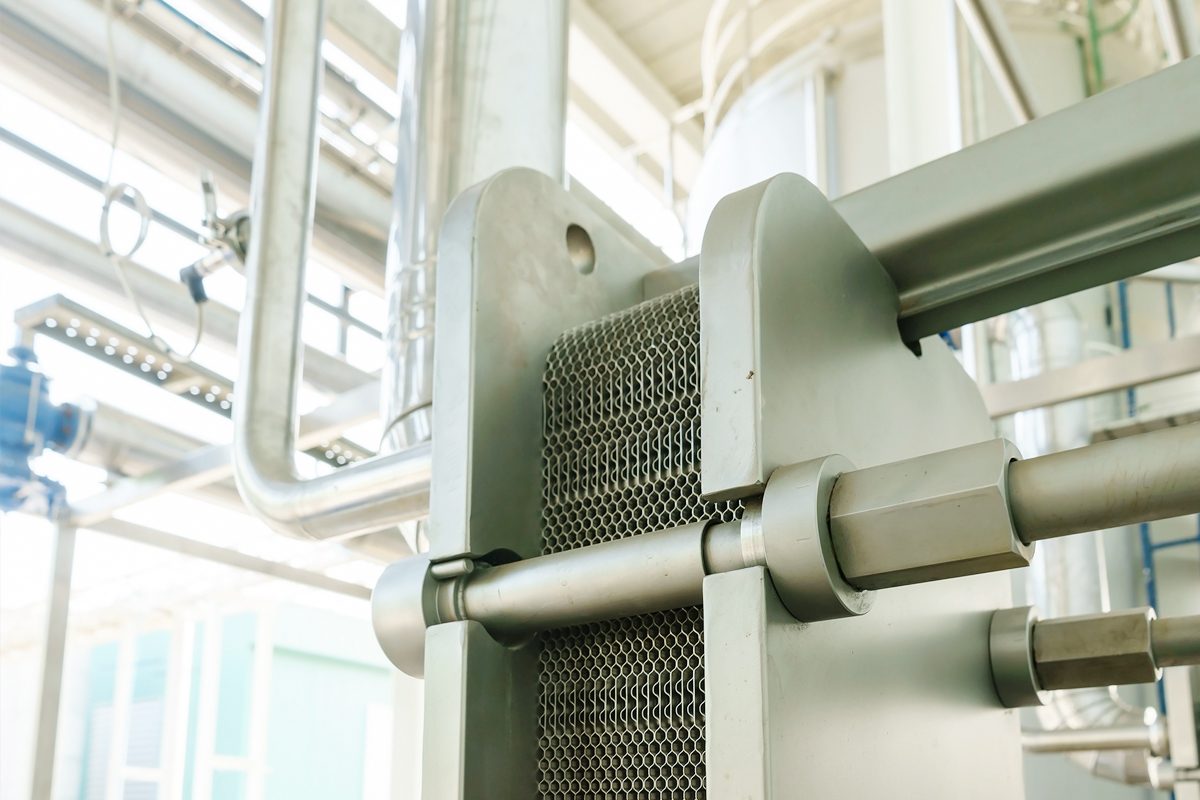
Design Considerations for Brewery Plate Heat Exchangers
Material Selection
Material selection is critical in brewery applications due to the need for corrosion resistance, hygiene, and durability. Stainless steel is the most common material used for plates due to its excellent corrosion resistance and ease of cleaning. The choice of gasket material also depends on the types of fluids used and the operating temperatures.
- Corrosion Resistance: Stainless steel is preferred for its ability to resist corrosion from wort and cleaning chemicals.
- Hygienic Design: Materials must meet food-grade standards to prevent contamination.
- Temperature and Pressure Compatibility: Materials should withstand the operating conditions of the brewery process.
Plate Design and Configuration
The design of the plates significantly impacts the efficiency of the heat exchanger. Plates are typically corrugated to increase turbulence, which improves heat transfer. The pattern of the corrugation can vary depending on the desired flow characteristics and thermal performance.
- Corrugation Pattern: Different patterns (e.g., chevron, herringbone) affect the turbulence and pressure drop.
- Plate Thickness: Thinner plates offer better heat transfer but may be less durable.
- Plate Spacing: The gap between plates affects the flow rate and pressure drop.
Flow Rate and Pressure Drop
The flow rate of the fluids through the heat exchanger and the associated pressure drop are critical considerations. A higher flow rate increases heat transfer but also increases the pressure drop, which can require more powerful pumps.
- Flow Rate: Must be balanced to achieve efficient heat transfer without excessive pressure loss.
- Pressure Drop: Should be minimized to reduce the energy required for pumping.
Heat Transfer Efficiency
The efficiency of a plate heat exchanger is determined by its ability to transfer heat between the fluids. This is influenced by the plate design, flow configuration, and the temperature difference between the fluids.
- Temperature Difference: A larger temperature difference between the fluids increases heat transfer efficiency.
- Surface Area: A larger surface area improves heat transfer but also increases the size and cost of the unit.
- Turbulence: Increased turbulence enhances heat transfer by reducing the boundary layer on the plate surfaces.
Sizing and Capacity
Proper sizing of the plate heat exchanger ensures it meets the needs of the brewery. The capacity of the unit must be sufficient to handle the required heat load without causing excessive pressure drop or flow restrictions.
- Heat Load: The amount of heat that needs to be transferred, determined by the brewery process requirements.
- Flow Rate: The rate at which fluids flow through the heat exchanger, affecting its size and capacity.
- Future Expansion: Consideration for potential future expansion or changes in brewery operations.
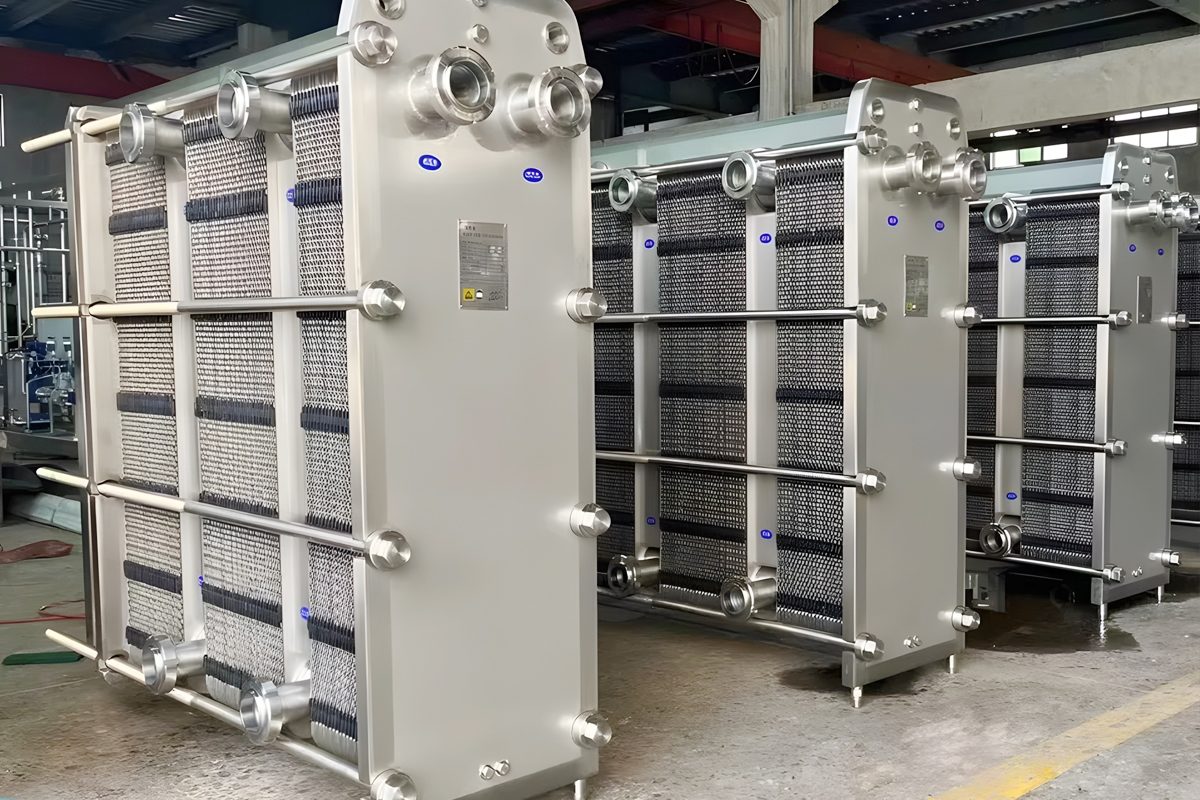
Applications of Plate Heat Exchangers in Brewing
Wort Cooling
One of the most critical applications of plate heat exchangers in brewing is wort cooling. After boiling, the hot wort must be rapidly cooled to a temperature suitable for fermentation. Plate heat exchangers are ideal for this process due to their ability to quickly transfer heat from the hot wort to a cooling medium, typically water or glycol.
- Rapid Cooling: Ensures that the wort reaches the desired fermentation temperature quickly, minimizing the risk of contamination.
- Energy Recovery: Heat from the hot wort can be recovered and used to preheat incoming water, improving energy efficiency.
- Consistent Cooling: Provides uniform cooling, ensuring consistent fermentation conditions.
Pasteurization
Plate heat exchangers are also used in the pasteurization process, where beer is heated to a specific temperature to kill any remaining microorganisms before packaging. This process ensures the stability and shelf life of the final product.
- Precise Temperature Control: Ensures that the beer is heated to the exact temperature required for pasteurization.
- Energy Efficiency: Heat from the pasteurization process can be recovered and reused, reducing energy consumption.
- Hygienic Design: Meets food safety standards, preventing contamination during the process.
Yeast Propagation
Yeast propagation is another critical process in brewing, where yeast cells are grown and multiplied before being added to the wort. Plate heat exchangers help maintain the optimal temperature for yeast growth, ensuring a healthy and active yeast culture.
- Temperature Control: Maintains the optimal temperature for yeast growth, improving fermentation performance.
- Consistency: Ensures a consistent environment for yeast propagation, leading to better fermentation results.
- Energy Efficiency: Heat exchangers can be used to recover energy from other processes, reducing overall energy consumption.
Energy Recovery
Energy recovery is a significant benefit of using plate heat exchangers in breweries. By recovering heat from hot processes like wort boiling or pasteurization, breweries can reduce their energy consumption and lower operating costs.
- Cost Savings: Reduces energy costs by recovering and reusing heat from brewing processes.
- Environmental Impact: Lowers the brewery’s carbon footprint by reducing energy consumption.
- Efficiency: Improves overall process efficiency by utilizing waste heat.
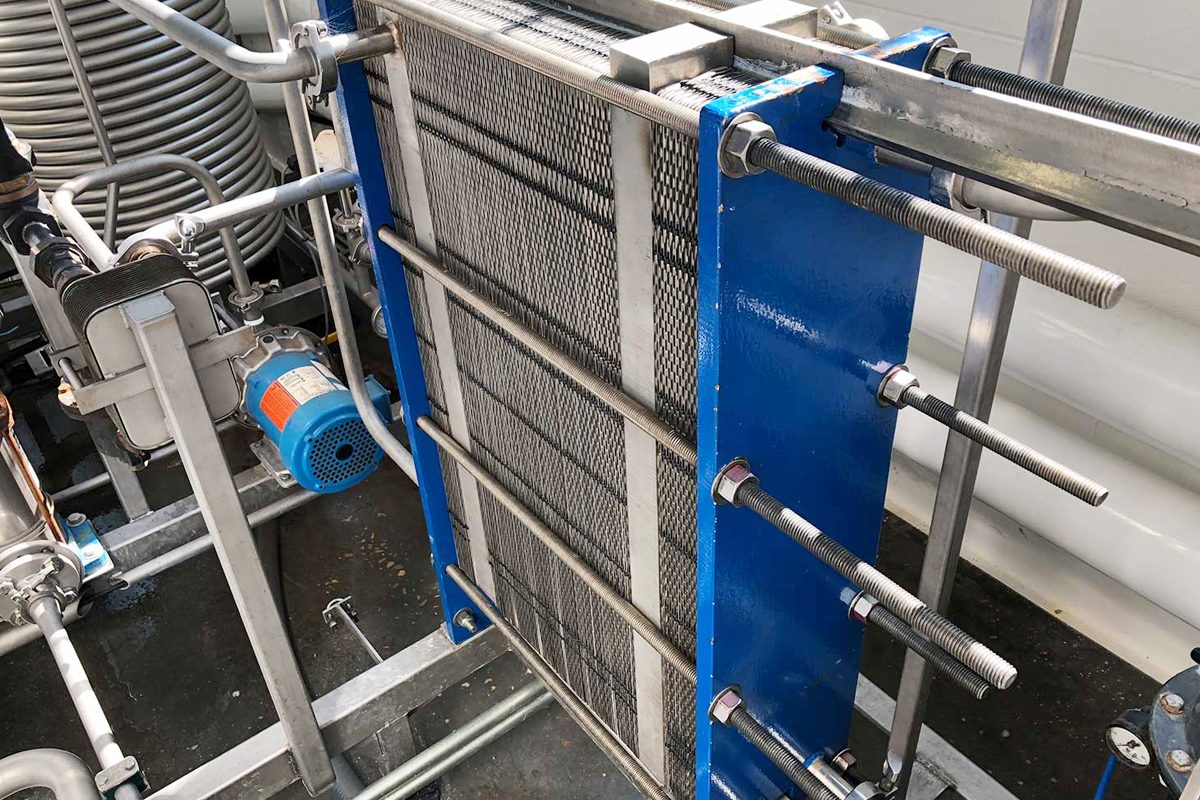
Benefits of Using Plate Heat Exchangers in Breweries
Energy Efficiency
Plate heat exchangers are highly energy-efficient, making them an ideal choice for breweries looking to reduce their energy consumption. By maximizing heat transfer and minimizing energy loss, PHEs help breweries achieve significant cost savings.
- Heat Recovery: PHEs can recover and reuse heat from hot processes, reducing the need for additional energy.
- Optimized Performance: High thermal efficiency ensures that heat is transferred effectively, minimizing energy waste.
- Sustainability: Energy-efficient equipment supports the brewery’s sustainability goals.
Cost-Effectiveness
In addition to energy efficiency, plate heat exchangers offer cost-effective solutions for breweries. Their modular design allows for easy expansion and maintenance, reducing downtime and operating costs.
- Lower Operating Costs: Reduced energy consumption leads to lower utility bills.
- Reduced Maintenance Costs: Modular design simplifies maintenance, reducing labor and replacement costs.
- Long-Term Savings: The durability and efficiency of PHEs provide long-term financial benefits.
Compact Design
The compact design of plate heat exchangers is another significant advantage, especially for breweries with limited space. PHEs offer a high heat transfer area relative to their size, making them ideal for space-constrained installations.
- Space Efficiency: Compact footprint allows for easy integration into existing brewery layouts.
- Scalability: Modular design allows for capacity expansion without requiring significant additional space.
- Installation Flexibility: Compact size and lightweight design make installation easier and more flexible.
Scalability
As breweries grow and expand their operations, the scalability of plate heat exchangers becomes increasingly important. The modular design of PHEs allows breweries to increase capacity by adding more plates, accommodating higher heat loads as needed.
- Modular Design: Easily scalable by adding or removing plates to match changing production needs.
- Adaptability: This can be customized to meet the specific requirements of different brewing processes.
- Future-Proofing: Provides flexibility for future expansion without needing to replace the entire unit.
Hygienic Design
Hygiene is a top priority in brewing, and plate heat exchangers are designed to meet stringent hygiene standards. The materials and construction of PHEs are chosen to prevent contamination, ensuring the quality and safety of the beer.
- Food-Grade Materials: Stainless steel and other food-grade materials are used to prevent contamination.
- Easy Cleaning: Plates can be easily removed and cleaned, ensuring that hygiene standards are maintained.
- Sanitary Design: Smooth surfaces and minimal crevices reduce the risk of bacterial growth.
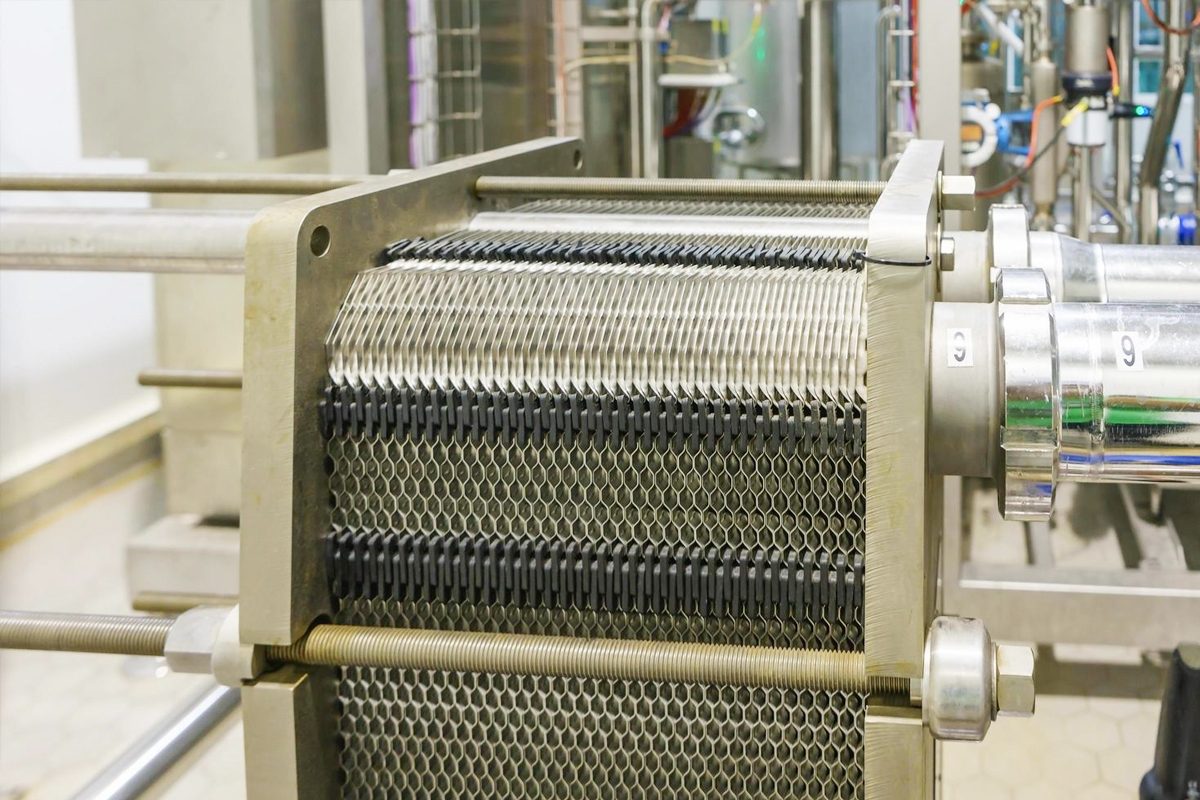
Maintenance and Cleaning of Plate Heat Exchangers
Routine Maintenance Practices
Regular maintenance ensures the long-term performance and efficiency of your plate heat exchanger. Routine maintenance practices include inspecting gaskets, checking for leaks, and monitoring the performance of the unit.
- Regular Inspections: Check gaskets, plates, and frames for wear and damage.
- Performance Monitoring: Track temperature differentials and pressure drops to identify potential issues.
- Proactive Maintenance: Replace worn components before they cause failures or reduce efficiency.
Cleaning Methods (CIP, Manual Cleaning)
Cleaning is a critical aspect of maintaining plate heat exchangers in a brewery. Two common cleaning methods are Clean-In-Place (CIP) and manual cleaning.
- Clean-In-Place (CIP): CIP systems allow for automated cleaning without disassembling the heat exchanger. This method is efficient and minimizes downtime.
- Manual Cleaning: For heavily fouled units or when CIP is not available, manual cleaning involves disassembling the heat exchanger and physically cleaning the plates.
Key Considerations:
- Frequency: Cleaning frequency depends on the type of fluids processed and the brewery’s operating conditions.
- Chemical Compatibility: Ensure that cleaning agents are compatible with the materials used in the heat exchanger.
- Thoroughness: Ensure that all surfaces are cleaned to prevent contamination and maintain efficiency.
Troubleshooting Common Issues
Common issues with plate heat exchangers include fouling, scaling, and leaks. Understanding how to troubleshoot these problems can help prevent downtime and maintain efficiency.
- Fouling: Accumulation of organic matter or minerals on the plates, reducing heat transfer efficiency. Cleaning is the primary solution.
- Scaling: Buildup of mineral deposits, particularly in hard water areas. Descaling solutions or water softeners can be used to prevent scaling.
- Leaks: Caused by worn gaskets or damaged plates. Regular inspection and prompt replacement of components can prevent leaks.
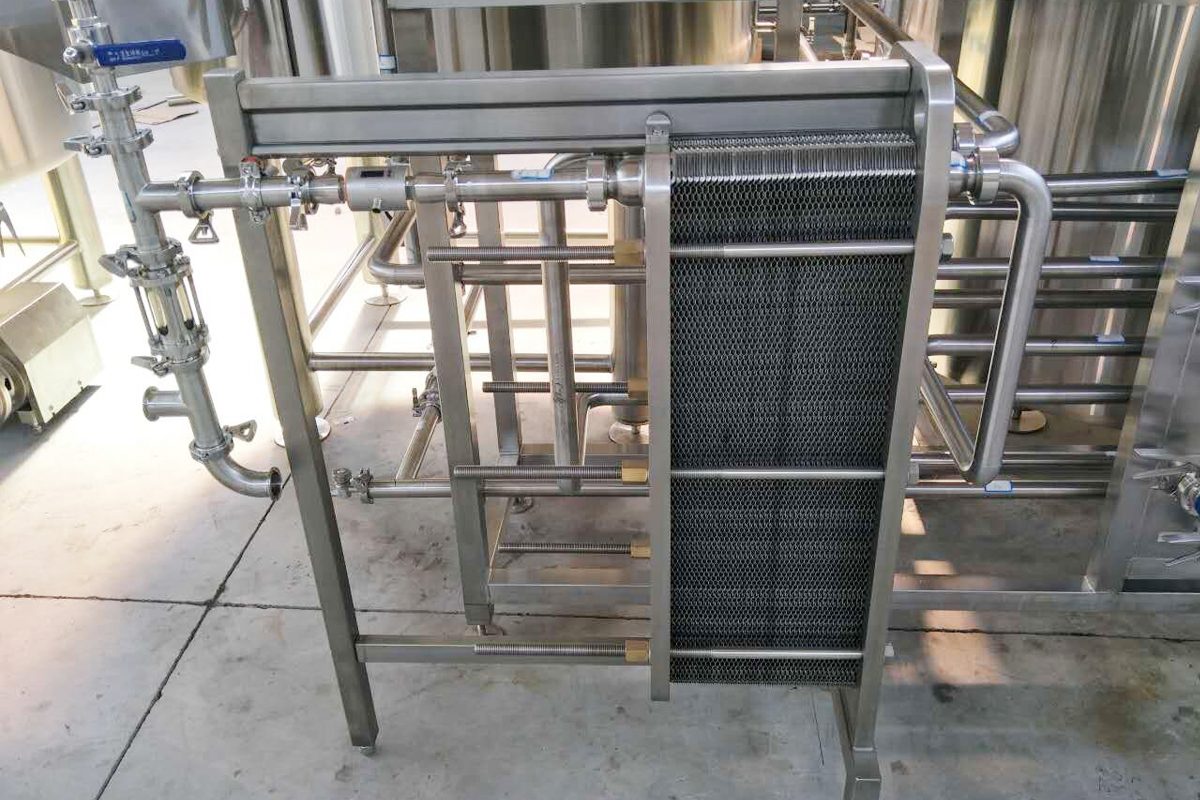
Challenges and Considerations
Fouling and Scaling
Key Considerations:
- Preventive Maintenance: Regular cleaning and maintenance can help prevent fouling and scaling.
- Water Quality: Using treated water or installing water softeners can reduce scaling.
- Monitoring: Regularly monitor the performance of the heat exchanger to detect fouling or scaling early.
Corrosion and Material Compatibility
Key Considerations:
- Material Selection: Choose materials that are resistant to the specific fluids used in the brewery.
- Corrosion Inhibitors: Consider using corrosion inhibitors if the heat exchanger is exposed to corrosive environments.
- Regular Inspection: Monitor for signs of corrosion and address any issues promptly.
Performance Monitoring
Key Considerations:
- Temperature Monitoring: Track inlet and outlet temperatures to ensure efficient heat transfer.
- Pressure Monitoring: Monitor pressure drops to detect any flow restrictions or blockages.
- Efficiency Tracking: Regularly assess the overall efficiency of the heat exchanger to identify potential issues.
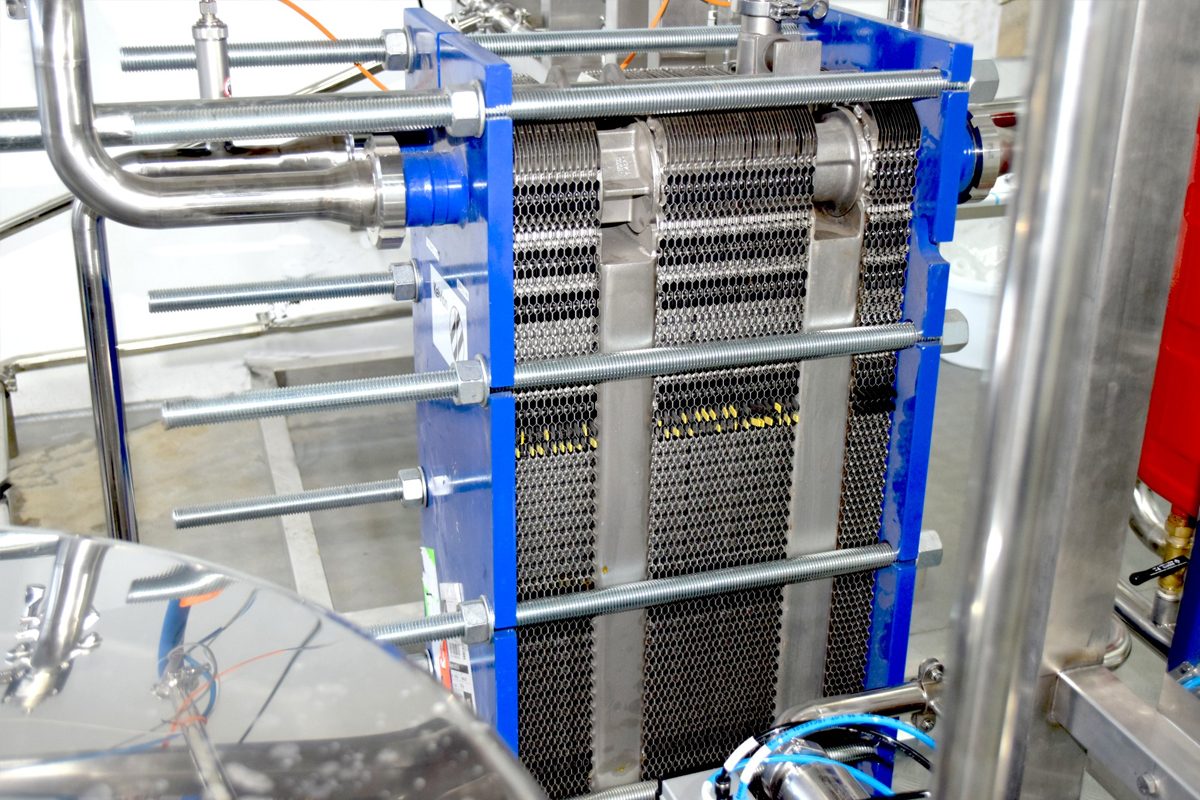
Summary
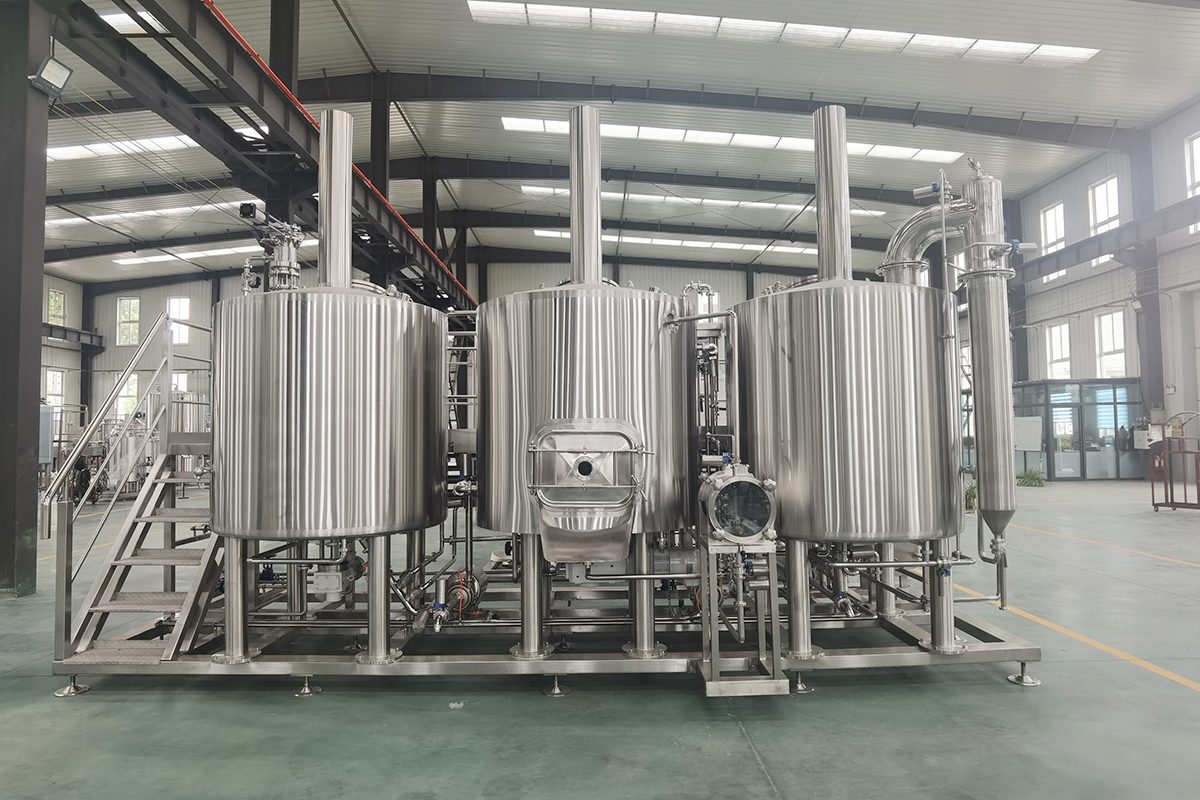