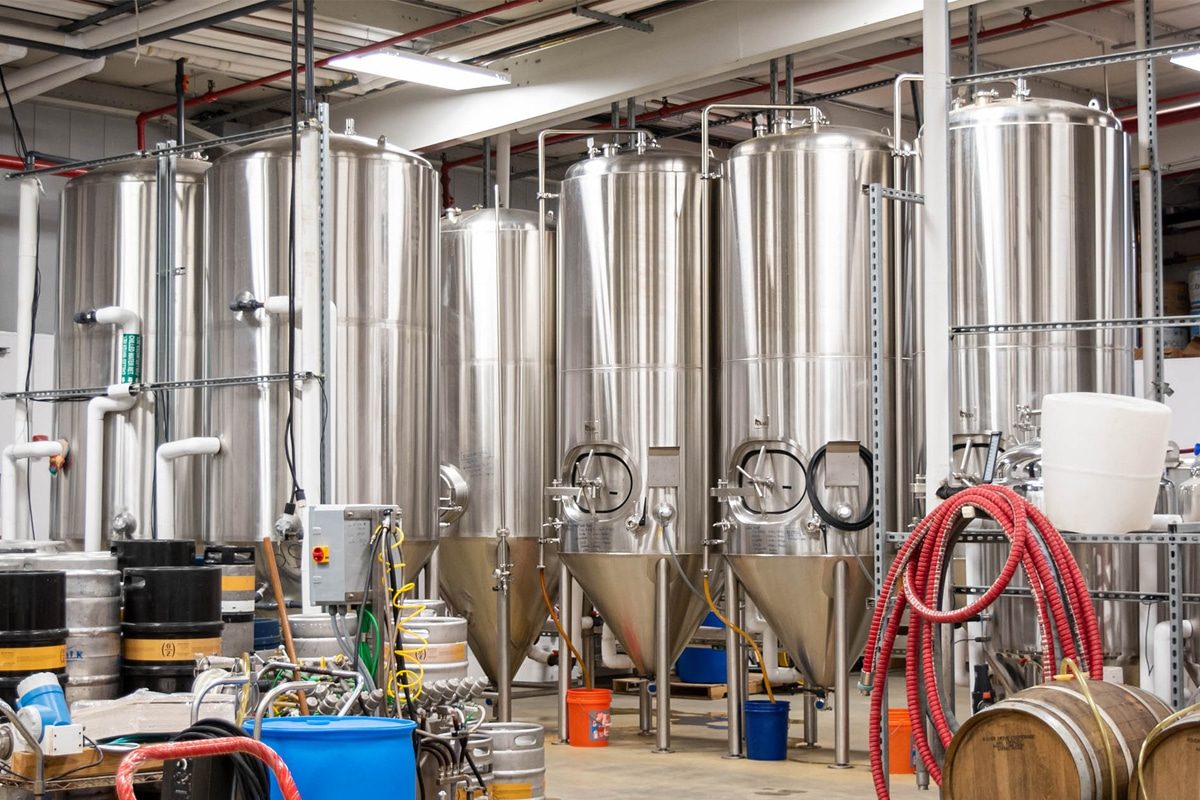
Fermentation Tank And Unitank: The Comprehensive Comparison
In the complex world of brewing, the choice between a Fermentation Tank and a Unitank is a critical decision, and each choice has its own advantages and complexities. Understanding these vessels involves not only understanding their physical structure, but also gaining insight into their impact on flavor, efficiency, and scalability. To brew the perfect beer, brewers navigate a maze of equipment choices. Fermentation Tank and Unitank are at the forefront of this decision-making process, transforming humble ingredients into delicious beers.
In this comprehensive exploration, we’ll take a journey into the heart of the brewing process, dissecting the features, capabilities, and benefits of Fermentation Tank and Unitank. As brewers continue to push the boundaries of their craft, understanding the differences between these two fundamental building blocks of brewery becomes critical. This article aims to illuminate the complexities, providing detailed comparisons that go beyond superficial similarities to enable winemakers to make informed decisions that resonate with the essence of their winemaking philosophy.
The Comprehensive Comparison
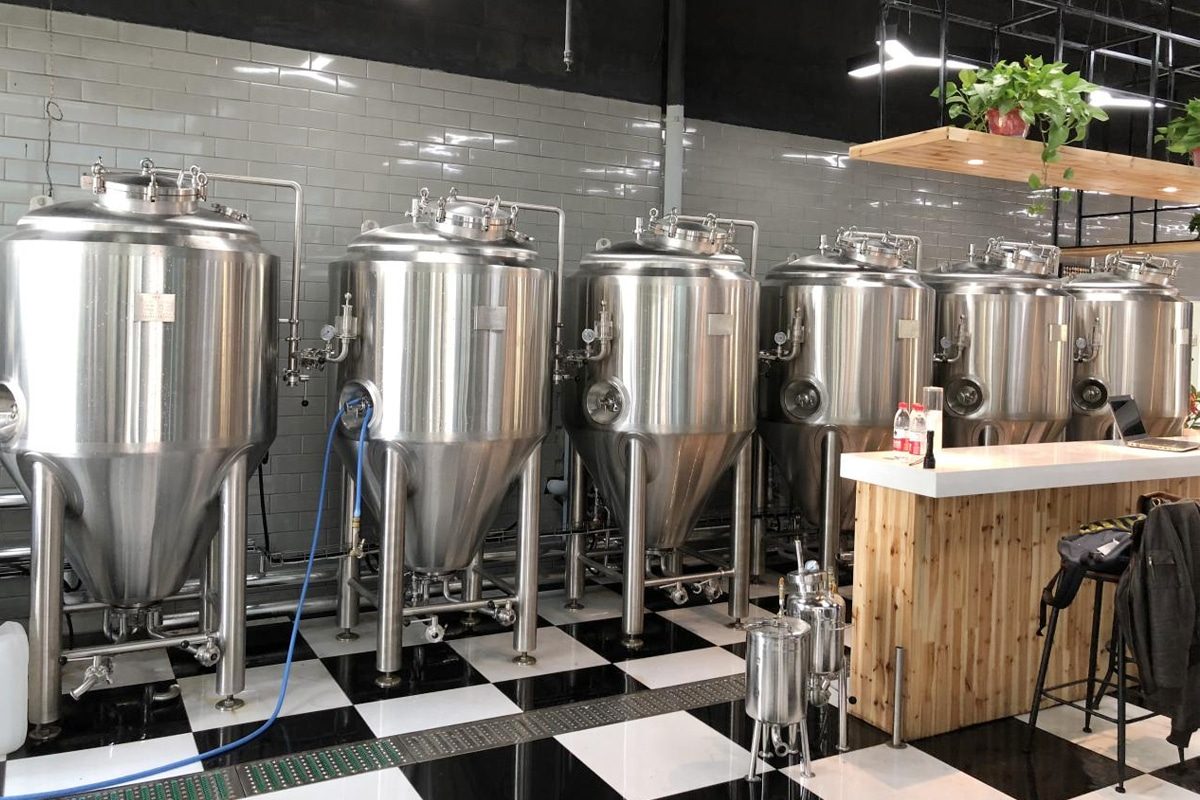
Fermentation Basics
Fermentation is a natural biochemical process in which microorganisms (usually yeast or bacteria) convert sugar into alcohol, acid, or gas. Whether brewing beer, craft wine, or fermenting other delicacies, understanding the basic principles of fermentation is key to mastering the art.
Microbial Players
The core of fermentation is yeast. Yeast is a living organism that typically plays a central role in brewing. Yeast consumes the sugar and converts it into alcohol and carbon dioxide through the fermentation process, while bacteria such as lactobacilli provide acidity and unique flavor.
Sugar Conversion
Fermentation begins with the introduction of sugar, usually from sprouted grains or fruits. During fermentation, yeast feeds on the sugars in the grain or fruit, producing alcohol and carbon dioxide. This process is called glycolysis and is central to alcohol production.
Temperature Control
Temperature is a key factor in fermentation and affects the speed and characteristics of the fermentation process. While higher fermentation temperatures generally result in faster fermentation, off-flavors may also occur. Temperatures that are too low may slow or stop the fermentation process. Therefore, the fermentation process needs to reach a delicate balance.
Flavor Features
Fermentation involves not only the production of alcohol but also the creation of flavor. The interaction of yeast and other microorganisms produces compounds such as esters and phenols that give the final product its unique aroma and taste. The choice of yeast strain and fermentation conditions affects beer flavor characteristics.
Fermentation Vessel
The vessel in which fermentation takes place is an important aspect of the brewing process. Traditional Fermentation Tank and Unitank each have their advantages. Fermentation Tanks are simpler, more cost-effective, and often used for specific types. In contrast, Unitank offers versatility and precise control over a variety of fermentation parameters, appealing to those looking for a more nuanced approach.
Time
Patience is the virtue of fermentation, and the process takes time. Fermentation duration varies based on factors such as yeast strain, temperature, and desired characteristics of the final product. Rushed fermentation can result in bad flavors, so the microbes need to be allowed to work their magic at their own pace.
Monitor
Brewing the perfect beer requires careful monitoring. Gravity readings can track the progress of fermentation, pH levels can affect flavor and stability, and other parameters such as oxygen exposure and cleanliness play a vital role in ensuring a successful fermentation.
In the world of brewing, fermentation is the magical alchemy that transforms raw materials into delicious beer. Whether you’re a home brewing enthusiast or a professional brewer, mastering the basics of fermentation will open the door to a world of possibilities and create delightful beverages. It’s a delicate balance of science and art, and every decision affects the flavor and character of the final product.
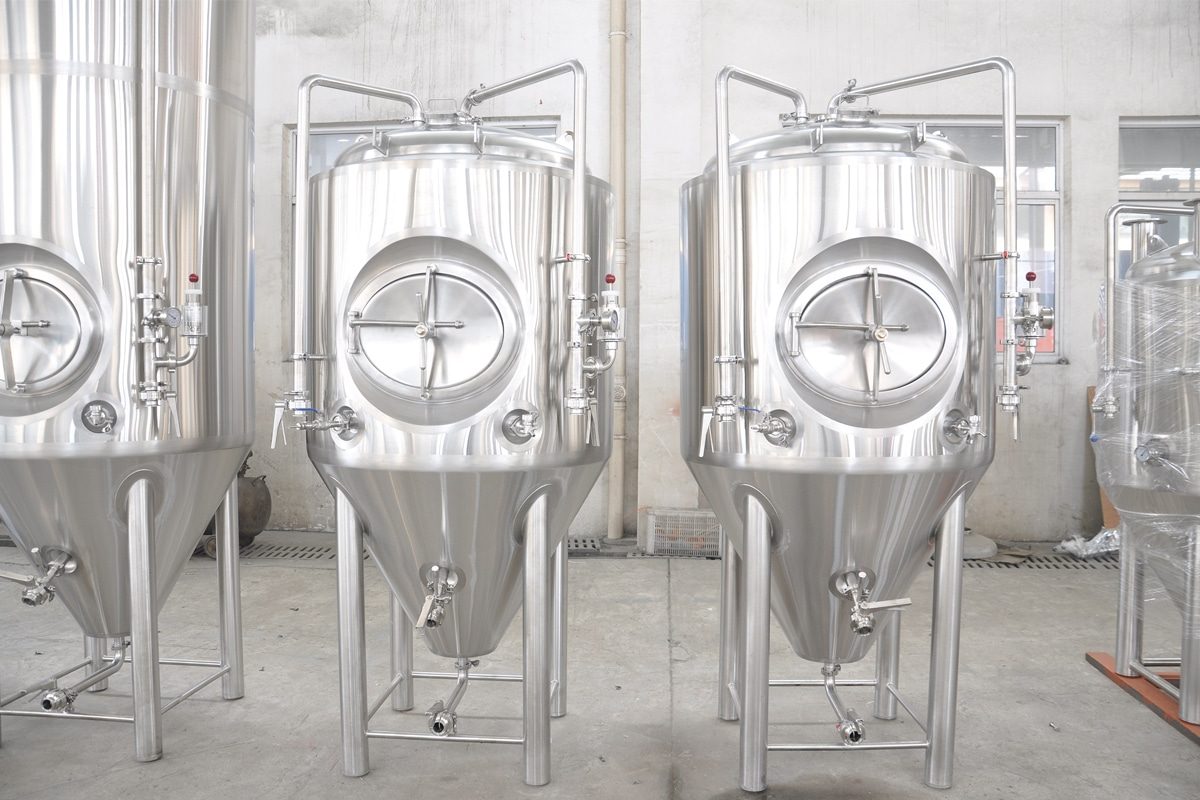
Learn About Fermentation Tank
Definition And Purpose
Fermentation Tanks are vessels designed for use in a controlled environment to facilitate and control the fermentation process in the production of a variety of beverages, including beer, wine, and spirits. The main purpose of a Fermentation Tank is to provide an environment conducive to the growth and activity of yeast or bacteria, allowing sugar to be converted into alcohol and other flavor-enhancing compounds.
Types of Fermentation Tank
Open Fermentation Tank:
- Description: Open fermenters expose the fermentation liquid to the surrounding environment. It has minimal control over environmental factors and is commonly used in the production of certain types of beer and wild ales.
- Purpose: Allow unique microorganisms in the environment to contribute to the brewing of beer, thereby cultivating complex flavors.
Closed Fermentation Tank:
- Description: Closed fermenters provide greater control over environmental conditions, including temperature, pressure, and exposure to contaminants.
- Purpose: Commonly used in modern brewing to maintain consistency, reduce the risk of contamination, and control fermentation parameters.
Conical Fermentation Tank:
- Description: These tanks have a tapered bottom that collects yeast and other sediments, simplifying the separation process.
- Purpose: Suitable for fermentation and conditioning, providing convenience and space efficiency.
Open Top Fermentation Tank:
- Description: Similar to open vessels, but with the advantage of control. Open-top tanks allow for manual hole punching and better management of fermentation lids.
- Purpose: Commonly used in brewing and certain beer styles to provide a compromise between open and closed systems.
Fermentation Process in Fermentation Tank
Vaccination:
- Description: The fermentation process begins with the introduction of yeast or bacteria into the wort or must.
- Purpose: Inoculation triggers the conversion of sugars into alcohol and flavor compounds.
Primary Fermentation:
- Description: Primary fermentation occurs during the initial stages of most fermentations. Yeast consumes large amounts of sugar, producing alcohol and carbon dioxide.
- Purpose: Primary fermentation provides the basis for a beverage’s alcohol content and essential flavor.
Temperature Control:
- Description: Maintaining a constant temperature helps control the speed and flavor characteristics of fermentation.
- Purpose: Temperature control affects yeast activity, flavor, and overall quality of the final product.
Harvesting And Filtering:
- Description: Once fermentation is complete, the beer is harvested and frequently filtered to remove remaining solids.
- Purpose: Harvest separates the final product from spent yeast and sediment, ensuring a clean, refined beverage.
Understanding the intricacies of fermentation tanks and the fermentation processes within them is key to mastering the art and science of brewing and winemaking. Each type of fermenter has its advantages that uniquely affect the final product.
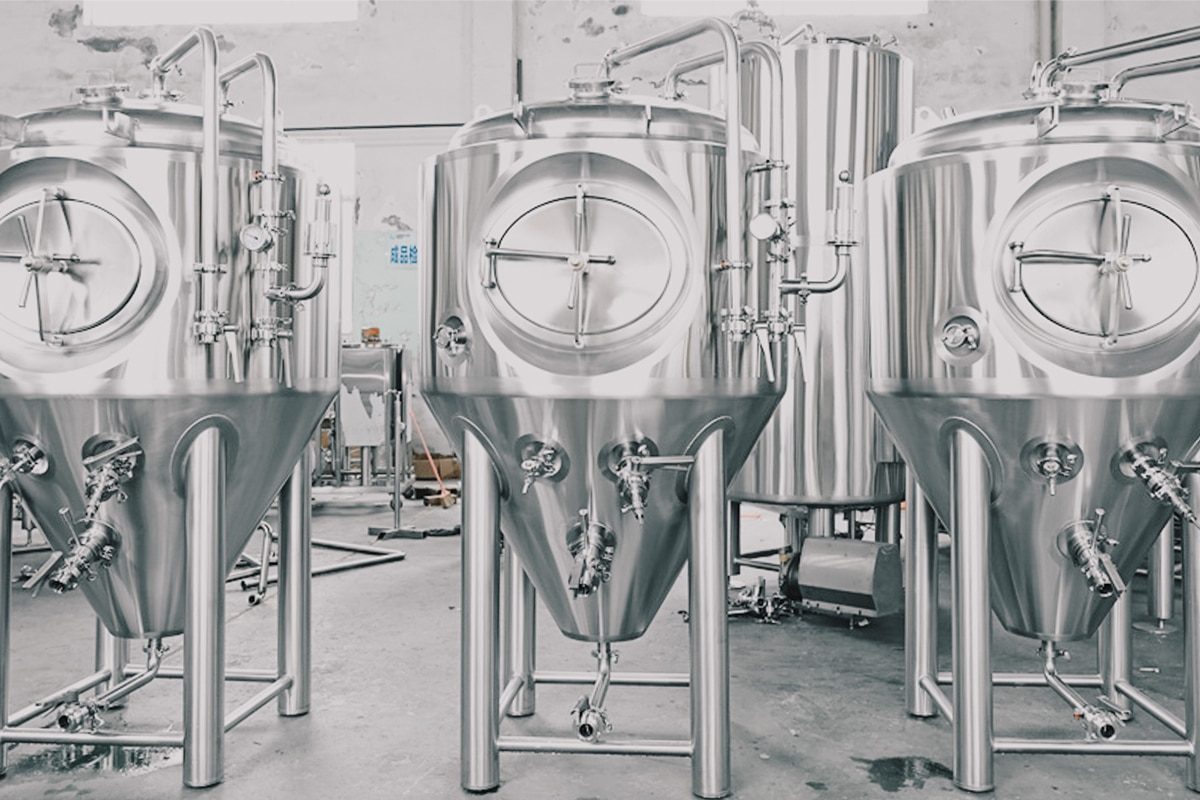
Learn About Unitank
Definition And Purpose
Unitank, short for “Universal Tank,” is a versatile fermentation vessel designed to perform multiple functions within a single vessel. Its main purpose is to provide a single vessel for the fermentation and conditioning processes. Unlike traditional fermenters, unit tanks allow brewers to conduct all stages of beer production, including fermentation, carbonation, and maturation, in one closed vessel.
Design And Features
Single Vessel Design:
- Description Unitanks are cylindrical stainless steel vessels that optimize space utilization and are easy to clean.
- Purpose: The single-vessel design simplifies the brewing process, minimizing the need to transfer beer between vessels and reducing the risk of contamination and oxidation.
Pressure Capacity:
- Description: Unitank is able to withstand pressure, allowing carbonation to occur naturally during fermentation or through forced carbonation.
- Purpose: This feature enables brewers to control and adjust carbonation levels within the same vessel, eliminating the need for an additional Bright Tank.
Temperature Control:
- Description: Unitank is equipped with a temperature control system (such as a cooling jacket or coil) to accurately regulate fermentation temperature.
- Purpose: Maintaining a specific temperature range helps control yeast activity and achieve the desired flavor.
Tapered Design:
- Description: The Unitank’s tapered bottom easily collects yeast and sediment, simplifying harvesting and cleaning.
- Purpose: The conical design helps separate yeast and other particles, simplifying the clarification process and reducing odors.
The Fermentation Process in Unitank
Inoculation And Fermentation:
- Description: Unitank begins its journey by receiving inoculated wort or grape juice and begins fermentation.
- Purpose: Unitanks are designed to precisely control fermentation parameters, ensuring consistent and ideal results.
Primary Fermentation:
- Description: Unitank supports the primary fermentation stage, where yeast consumes sugar and produces alcohol.
- Purpose: This stage determines the alcohol content and lays the foundation for the beer’s flavor.
Temperature And Pressure Control:
- Description: Unitank’s temperature control system maintains precise temperatures throughout the fermentation process, while the vessel’s pressure control capabilities allow for controlled carbonation.
- Purpose: Ensure consistency, influence yeast behavior, and control carbonation levels according to desired specifications.
Ripening And Conditioning:
- Description: After initial fermentation, Unitank can be used for maturation, allowing flavors to develop and the drink to clarify.
- Purpose: Combine fermentation and maturation in the same vessel, simplifying the brewing process and reducing the need for additional equipment.
Carbonation:
- Description: Unitank usually comes with carbonated stone, allowing brewers to introduce carbon dioxide directly into the beer.
- Purpose: This integrated carbonation approach simplifies the process and increases control over carbonation levels.
Harvesting And Packing:
- Description: After fermentation and conditioning, the beer is harvested directly from the Unitank.
- Purpose: To streamline the process, minimize the risk of contamination, and simplify packaging procedures.
Unitank is praised for its efficiency, versatility, and ability to streamline the brewing process. Its design and functionality cater to brewers seeking precise control over fermentation parameters and final product quality.
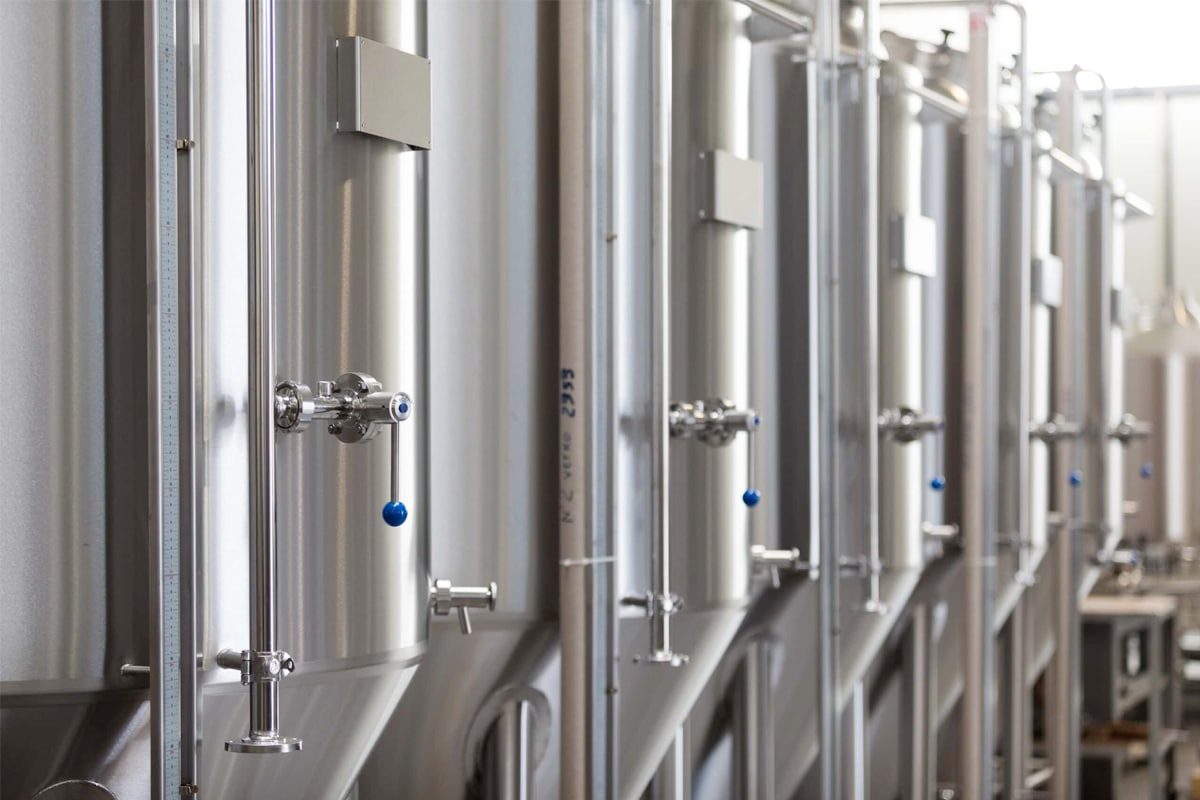
Key Differences Between Fermentation Tank And Unitank
The choice between a Fermentation Tank and a Unitank is a critical decision for brewers and plays a key role in shaping the brewing process and the characteristics of the final product. Here are the main differences between Fermentation Tank and Unitank:
Function
- Fermentation Tank: Usually used only for primary fermentation. Once fermentation is complete, the beer can be transferred to another vessel for conditioning and maturation.
- Unitank: combines fermentation and ripening processes in one vessel. It allows brewers to complete all stages of beer production, including fermentation, conditioning, and carbonation, in one tank
Design
- Fermentation Tank: Its design can vary, but generally has a simple cylindrical shape with a tapered bottom, without the special features of a Unitank.
- Unitank: adopts a cylindrical design and tapered bottom, which is beneficial to the collection of yeast and sediment. It comes with additional features such as pressure capability, a cooling jacket, and a temperature control system.
Pressure Treatment
- Fermentation Tank: Typically not designed to handle significant pressure. Carbonation is usually accomplished in a separate conditioning tank or by forced carbonation.
- Unitank: Designed to handle pressure, allowing controlled carbonation during fermentation. In many cases, this eliminates the need for a separate Bright Tank.
Temperature Control
- Fermentation Tank: This may have basic temperature control options. Limited accuracy compared to Unitank.
- Unitank: Equipped with advanced temperature control systems (such as cooling jackets or coils) to provide breweries with precise control of fermentation temperature.
Space Efficiency
- Fermentation Tank: An additional Bright Tank is required for conditioning and maturation, which takes up more space.
- Unitank: Consolidate multiple brewing stages into one vessel to optimize space utilization in the brewery.
Complexity And Cost
- Fermentation Tank: Generally simpler in design and operation, and potentially more cost-effective.
- Unitank: More complex design, but allows precise control of fermentation variables, which increases initial investment. However, it provides a comprehensive solution with the potential to reduce the need for additional storage tanks and associated costs.
The choice between a Fermentation Tank and a Unitank ultimately comes down to the brewer’s preference, the scale of production, and the level of control desired over the brewing process. The Fermentation Tank is simple and cost-effective, while the Unitank provides a more integrated and controlled brewing environment.
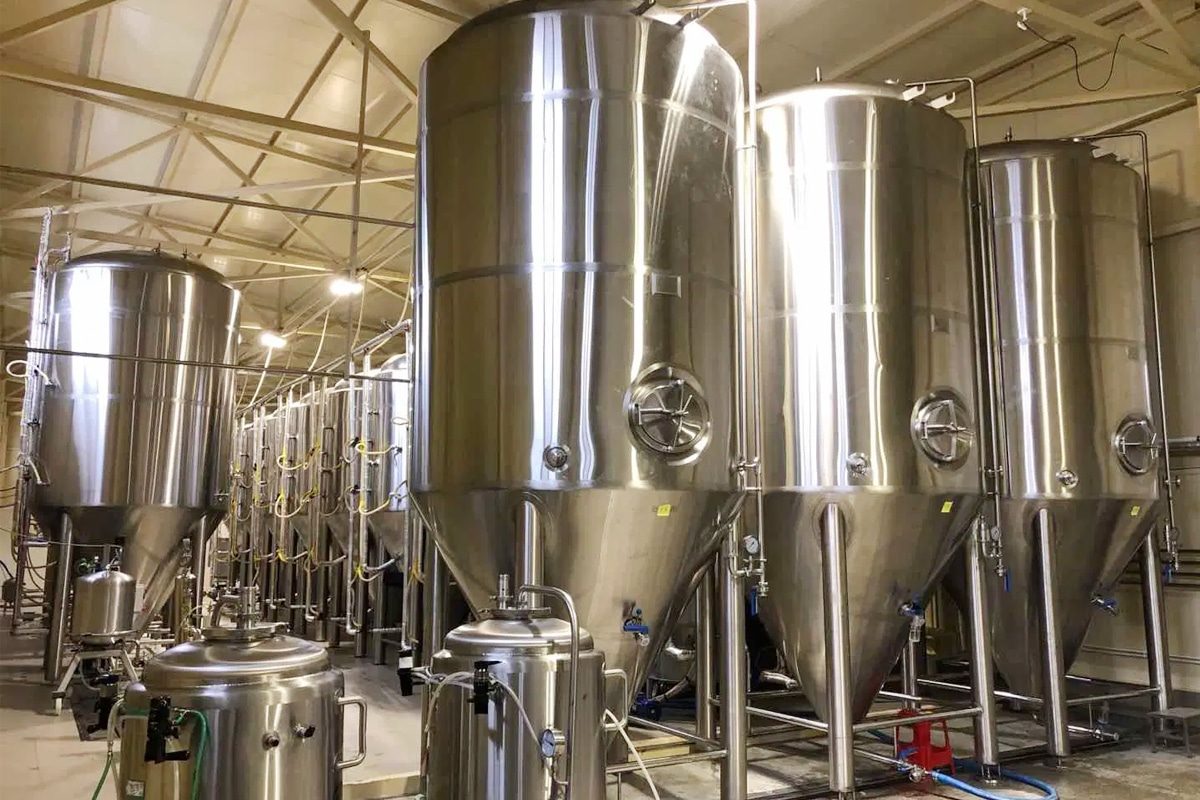
Application and Suitability of Fermentation Tank And Unitank
The choice of Fermentation Tank and Unitank in brewing depends on a variety of factors, such as the scale of production, the level of control required, and the specific needs of the brewing process. The following is an overview of the applications and suitability of Fermentation Tank and Unitank:
Fermentation Tank
Application:
- Large-Scale Brewing Operations: Fermenters are often used in large-scale brewing operations, where multiple tanks can be dedicated to different stages of the brewing process.
- Traditional Brewing: Fermenters are ideal for traditional brewing methods that focus on simplicity and cost-effectiveness.
- Basic Fermentation: Ideal for primary fermentation processes, brewers aim for direct fermentation without the need for advanced controls or conditioning within the same vessel.
- Small Breweries: This is especially beneficial for small breweries as they may not need complex equipment or invest in more advanced equipment.
Adaptability:
- Cost-Effectiveness: Fermenters are generally more affordable and suitable for breweries looking for a simpler setup without the need for extensive control features.
- Simplicity: For brewers who prioritize simplicity and produce beer styles that don’t require a lot of conditioning or maturation.
Precautions:
- Space Requirements: Breweries with sufficient space and the ability to use separate vessels for fermentation and conditioning may find fermenters Suitable.
- Beer Styles: Ideal for beer styles that don’t require a specific conditioning process or precise carbonation control.
Unitank
Application:
- Modern Brewing Practices: Unitank is ideal for breweries adopting more modern brewing techniques that require precision, control, and efficiency of the brewing process.
- Versatile Brewing: Ideal for breweries that produce a variety of beer styles and want flexibility in their brewing process.
- Complex Flavor Profile: Ideal for producing a variety of beer styles with different flavor profiles, where precise control of fermentation variables is critical.
Adaptability:
- Space Efficiency: Ideal for breweries with limited space as unit tanks consolidate multiple brewing stages into a single vessel.
- Precision And Control: For brewers who prioritize precise control of fermentation variables, including temperature, pressure, and carbonation.
- Versatility: Unitank’s versatility allows brewers to conduct multiple stages of the brewing process within a single vessel, reducing the need for additional tanks.
- Consistency and Quality: Unitank maintains consistency in product quality by minimizing the risk of contamination during transfers between tanks.
Precautions:
- Initial Investment: Due to its advanced features and capabilities, Unitank may have a high initial cost.
- Production Scale: While suitable for craft breweries, large-scale operations may require multiple Unitanks to meet production needs.
Choose The Right Option
- Brewing Goals: Consider the specific goals and style of beer the brewery intends to produce. Certain styles may benefit from the precision and control Unitank provides, while others may not require such complexity.
- Control Requirements: The level of control required to evaluate fermentation variables such as temperature, pressure, and carbonation. Unitank offers more advanced control options.
- Space Availability: Assess your brewery’s available space. The Unitank is beneficial for breweries with limited space, while the Fermentation Tank may be suitable for larger facilities.
- Budget Constraints: Consider the initial investment budget. Fermentation Tanks are generally more affordable, while Unitank may require a higher upfront cost.
- Brewing Philosophy: Breweries focused on traditional methods may prefer the Fermentation Tank, while those seeking precise control and efficiency may gravitate towards the Unitank.
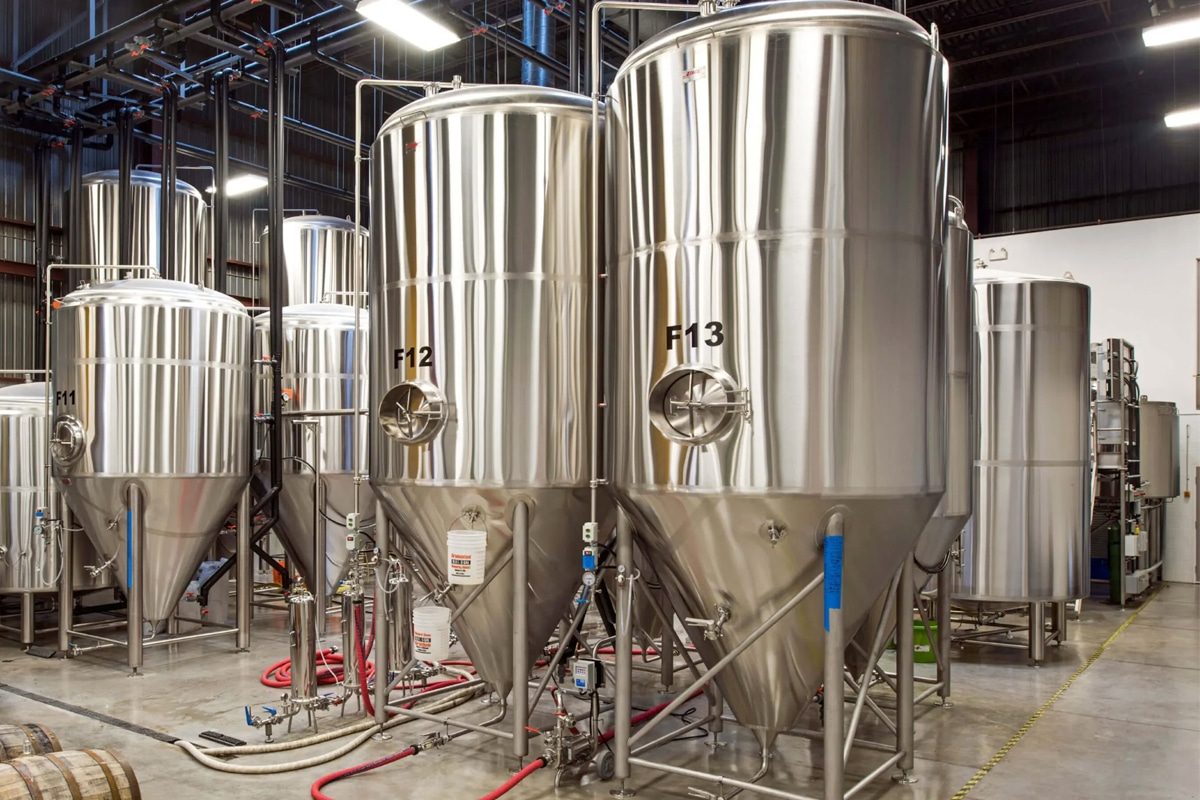
Summarize
In the complex world of brewing, the choice between a Fermentation Tank and a Unitank is a critical decision. The Fermentation Tank is a symbol of tradition and simplicity, providing a cost-effective approach to basic fermentation. Instead, Unitank is the epitome of modern brewing technology, integrating multiple stages into one vessel, ensuring precision and versatility.
In the end, the choice between these vessels is a symphony of craftsmanship, scale, and desire. Fermentation Tank honors the roots of brewing, while Unitank symbolizes the evolution toward precision and efficiency. Whether one prefers tradition or embraces innovation, each vessel plays a decisive role in shaping the winemaker’s journey. Ultimately, the choice depends on the brewer’s philosophy, production scale, and desire for control. As this comparison draws to a close, hopefully, brewers will find inspiration, understanding, and guidance in utilizing the Fermentation Tank and Unitank for a rich brewing process.
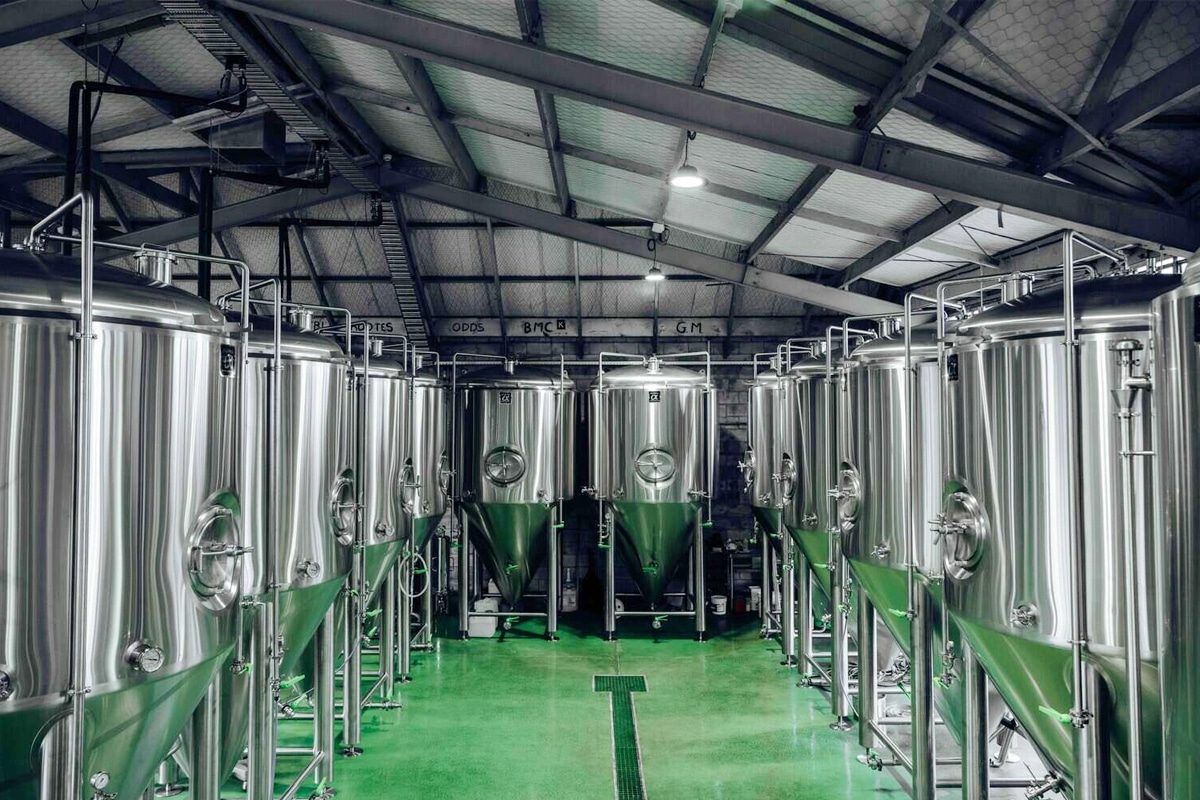
Brewery Turnkey Solutions
At ZYB Craft, we know that the choice between Fermentation Tanks and Unitanks is only one aspect of the complex brewing process. That’s why we offer complete turnkey solutions, guiding our customers from the initial brewing consultation to the completion of their first batch of beer. Our expertise extends beyond recommending the ideal vessel to provide a comprehensive brewing journey. We invite our customers to consult us, not only for an in-depth understanding of fermentation vessels but also for a holistic approach to brewing excellence. With our guidance, expertise, and support, we ensure a seamless transition from concept to completion, allowing brewers to start their brewing careers confidently and successfully.