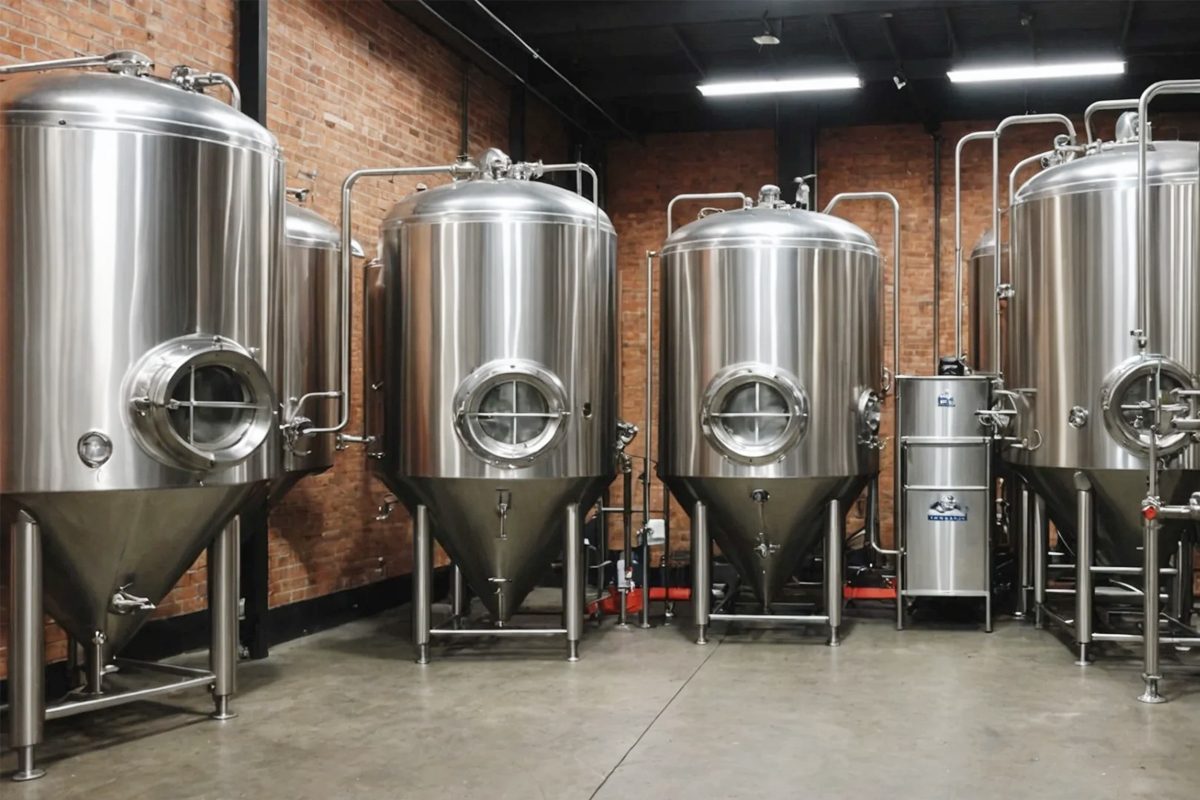
Factors Affecting the Initial Investment in Fermentation Tanks
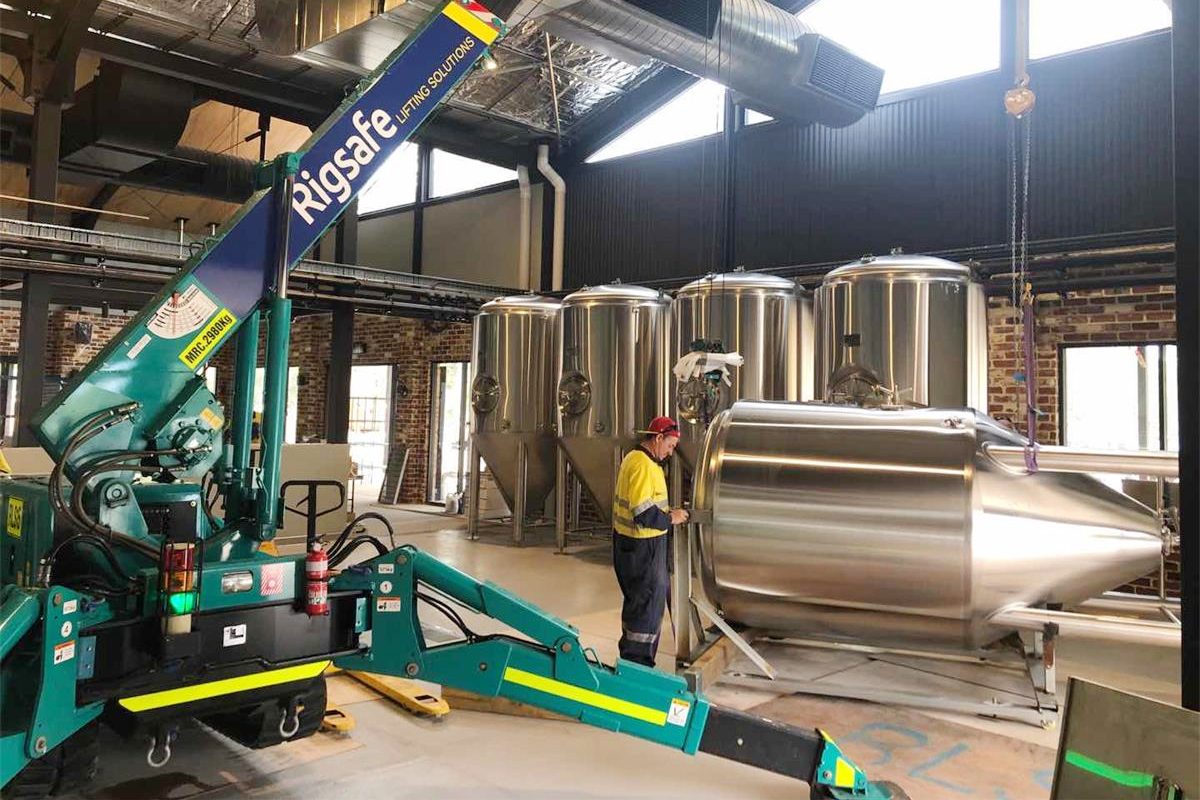
Material Selection
One of the primary factors influencing the initial investment in fermentation tanks is the material used in their construction. Selecting the right material helps ensure your fermentation tank’s durability, performance, and suitability for your brewing process. Typically, stainless steel is the preferred material for commercial fermentation tanks due to its robustness, resistance to corrosion, and ease of cleaning. However, the specific grade of stainless steel can significantly impact the cost.
- 304 Stainless Steel: This is the most common choice for fermentation tanks because it offers an excellent balance between cost and corrosion resistance. 304 stainless steel is suitable for most brewing environments and provides a long-lasting, durable solution without breaking the bank.
- 316 Stainless Steel: Known for its superior corrosion resistance, 316 stainless steel is often chosen when fermentation tanks are exposed to more aggressive or acidic environments. Although more expensive, it offers added protection, making it a worthwhile investment for breweries that handle particularly challenging ingredients or cleaning agents.
- Other Materials: For smaller breweries or homebrewers, materials like food-grade plastic or aluminum may be considered to reduce costs. However, these materials are generally not suitable for commercial-scale brewing due to durability concerns and the potential for imparting unwanted flavors to the beer.
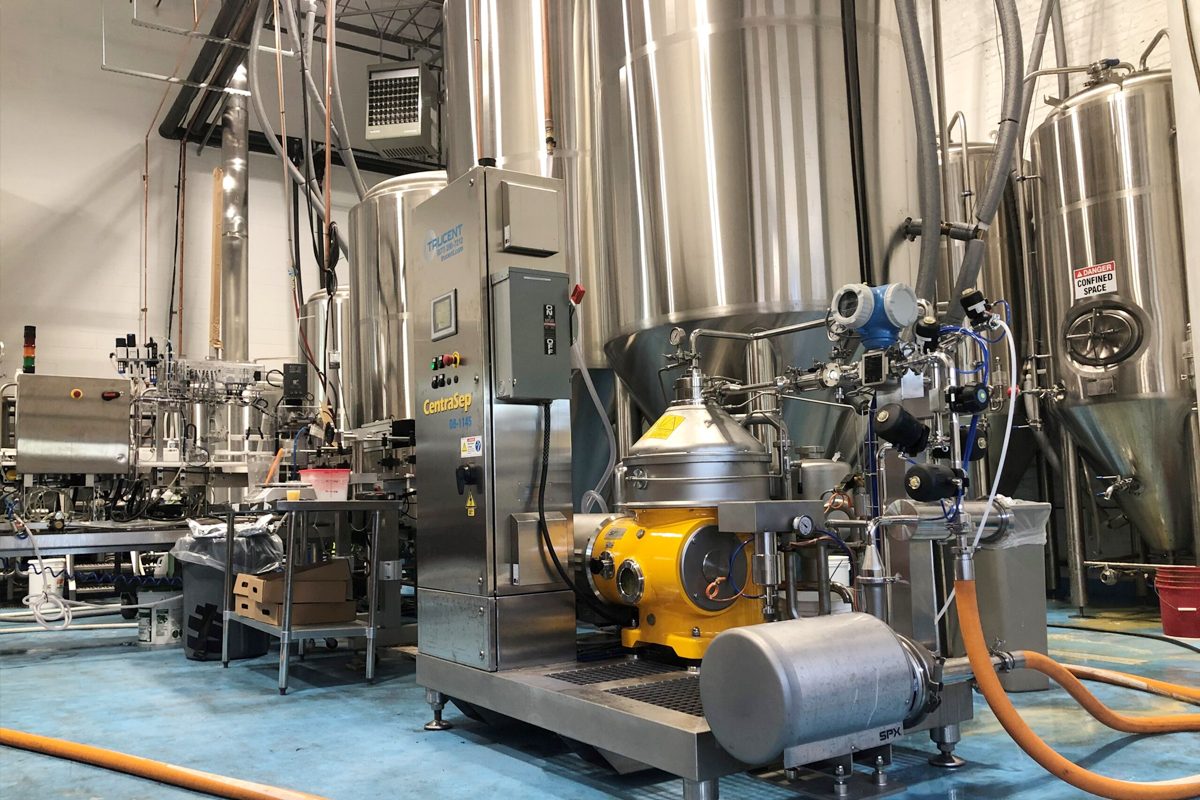
Tank Size and Capacity
The size and capacity of fermentation tanks are key factors that significantly impact the initial investment for any brewery. Tank size is typically measured in barrels (BBL) or liters, and it directly correlates with the brewery’s production volume. Larger tanks allow for higher production capacities, but they also require a greater upfront investment in both the tanks themselves and the supporting infrastructure.
- Small to Medium-Scale Breweries: For microbreweries or craft breweries, tanks in the range of 5 to 20 BBL are common. These tanks strike a balance between production capacity and initial cost, allowing for manageable production while still offering room for growth. Smaller tanks are also easier to install and maintain, making them suitable for breweries with limited space or budget constraints.
- Large-Scale Breweries: For breweries focused on high-volume production, tanks with capacities exceeding 20 BBL are typically required. These larger tanks come with higher costs, not only due to the increased material and manufacturing complexity but also because of the additional infrastructure required, such as reinforced floors, larger cooling systems, and increased space requirements.
- Scalability Considerations: While smaller tanks may be more affordable initially, breweries aiming for future growth should consider scalability. Investing in larger tanks upfront can reduce the need for frequent upgrades as demand increases. However, larger tanks also carry the risk of overcapacity if production levels do not meet projections, leading to underutilization and higher operational costs.
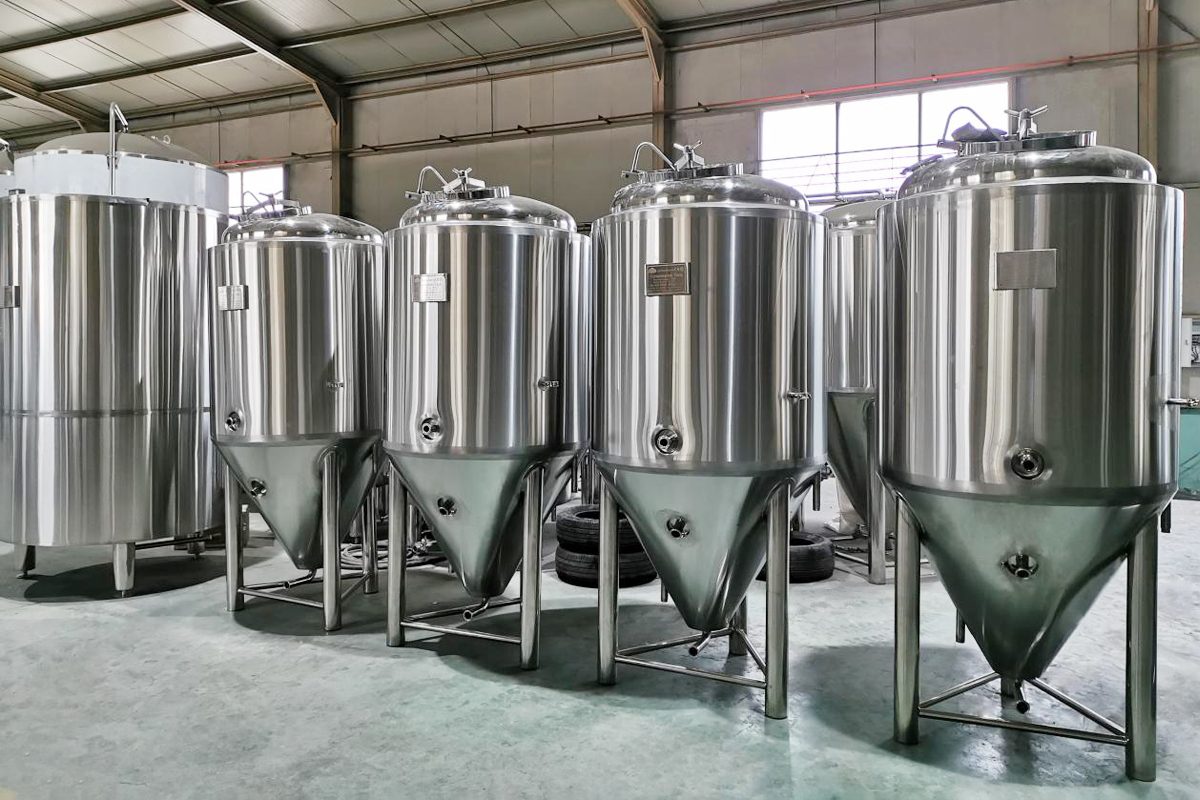
Customization and Design Features
Customization and design features are significant factors influencing the initial investment in fermentation tanks. Every brewery has unique requirements based on production scale, available space, and brewing processes, so customization helps optimize efficiency and ensure the fermentation tanks meet specific operational needs. However, the more customized the tank design, the higher the initial cost.
- Cylindroconical vs. Flat-Bottom Tanks: Cylindroconical tanks are the industry standard for most breweries, as their cone-shaped bottoms make it easier to separate yeast and sediment from the beer. This design improves both fermentation efficiency and the ease of cleaning. However, these tanks are typically more expensive than flat-bottom tanks, which are less efficient for commercial brewing but are often used by small breweries looking to save on costs.
- Horizontal vs. Vertical Tanks: Vertical tanks are more common in commercial brewing due to their ability to save floor space and accommodate larger volumes of beer. Horizontal tanks, often used in lager production, provide better yeast management and distribution during fermentation. However, they require more floor space and can increase installation and infrastructure costs.
- Custom Shapes and Sizes: Breweries with specific production or space constraints often require tanks in non-standard shapes or sizes. Custom-built tanks designed to fit into irregular spaces or designed for specialized brewing processes are more expensive due to the additional engineering and manufacturing involved. Tailored features, such as sloped floors for improved drainage, also add to the investment.
- Additional Features: Breweries often require tanks with added features like dry-hopping ports, multiple access points for cleaning, or specific pressure ratings for different brewing processes. These specialized design elements contribute to the increased cost but provide better functionality and safety.
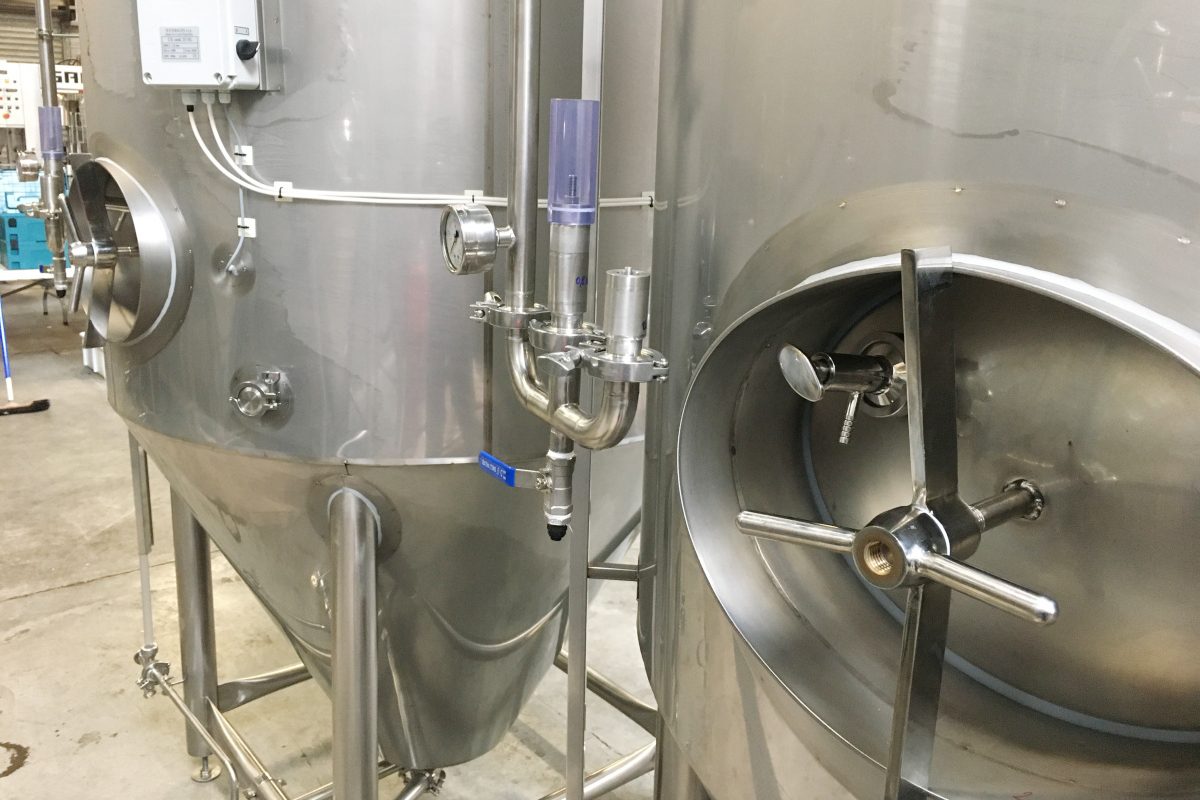
Cooling Systems and Temperature Control
Cooling systems and temperature control are critical factors in the performance of fermentation tanks and play a significant role in the initial investment. Fermentation is a temperature-sensitive process, and maintaining the right temperature is crucial for producing high-quality beer. The complexity and efficiency of the cooling system can have a considerable impact on both the cost and the long-term operational efficiency of the tanks.
- Cooling Jackets: Most modern fermentation tanks are equipped with integrated cooling jackets that allow for precise temperature regulation. These jackets, typically made from stainless steel, circulate cooling fluids (like glycol or water) around the tank to maintain the optimal temperature for fermentation. The size, complexity, and number of cooling zones in a jacket directly affect the cost of the tank. Tanks with multiple cooling zones allow brewers to control different sections of the tank independently, offering more precise temperature management but at a higher initial investment.
- Insulation: Insulated fermentation tanks help maintain a consistent temperature by minimizing the influence of external factors, such as ambient temperature fluctuations. While insulation adds to the upfront cost, it is a necessary investment for energy efficiency and reducing the load on the cooling system. The quality and thickness of the insulation material, such as polyurethane foam, can affect both the cost and performance of the tank.
- Advanced Temperature Control Systems: Breweries that require precise and automated temperature management may opt for tanks equipped with advanced temperature control systems. These systems often include digital temperature sensors, automatic controls, and real-time monitoring capabilities, allowing brewers to make quick adjustments during the fermentation process. Such systems offer better control but come with a higher price tag. Basic analog systems, while cheaper, provide less precision and may require more manual intervention.
- Energy Efficiency: Energy consumption is an important factor when considering cooling systems. Tanks with efficient cooling systems and insulation will reduce energy use over time, leading to lower operational costs. While these energy-efficient systems may require a larger initial investment, the long-term savings in electricity and maintenance can offset the upfront cost.
- External Chilling Units: In some setups, breweries may require external chilling units, such as glycol chillers, to support the cooling process. These systems add to the initial investment but are necessary for larger breweries or for those producing multiple beer styles that require different fermentation temperatures. The capacity and efficiency of these chilling units must match the size of the fermentation tanks to ensure adequate temperature control.
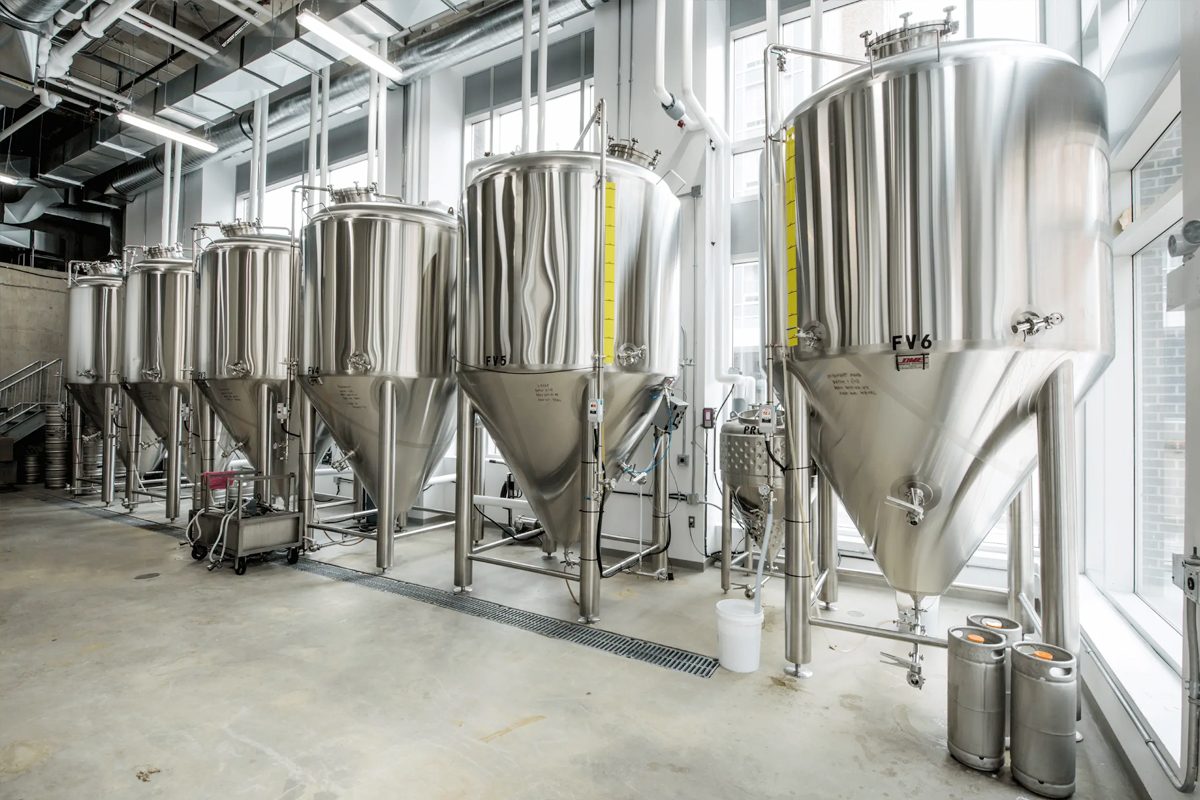
Cleaning and Maintenance Systems
Clean-in-place (CIP) systems are critical to the sanitation and operational efficiency of fermentation tanks, making them a key factor in the initial investment. CIP systems allow for automated cleaning without the need to dismantle the tank, ensuring a thorough, efficient, and repeatable cleaning process that minimizes downtime and reduces labor costs. The inclusion of a CIP system can increase the upfront cost of fermentation tanks, but the long-term benefits often outweigh this initial expense, particularly in larger or high-production breweries.
- Automated Cleaning Efficiency: CIP systems use a combination of cleaning solutions, water, and rinsing agents to sanitize the interior surfaces of the tank. Automated systems ensure that every part of the tank is cleaned consistently, reducing the risk of contamination between batches. This is particularly important for breweries that produce multiple beer styles or operate continuously. While manual cleaning systems may seem like a cost-saving option, they often require more labor and time, increasing operational costs over time.
- Cost-Saving Through Reduced Labor and Downtime: One of the main advantages of CIP systems is the reduction in labor required to clean tanks. Automated systems handle most of the cleaning process without needing human intervention, freeing up staff for other tasks. Additionally, the efficiency of CIP systems minimizes tank downtime, allowing for faster turnaround between batches and maximizing production. While the initial investment in CIP equipment is higher, the reduction in labor costs and downtime leads to significant long-term savings.
- Customizable Cleaning Cycles: Advanced CIP systems often allow breweries to customize cleaning cycles to fit their specific needs. For example, tanks used for high-alcohol or high-sugar beers may require longer or more aggressive cleaning cycles to ensure complete sanitation. Customizable cycles can enhance operational efficiency by optimizing the cleaning process based on the brewery’s specific production requirements.
- Chemical and Water Efficiency: Modern CIP systems are designed to minimize the use of cleaning chemicals and water, reducing ongoing operational expenses. Efficient use of resources not only lowers costs but also aligns with environmentally sustainable practices. Though these systems might come at a higher initial cost, the savings from reduced chemical and water consumption over time can help offset the initial investment.
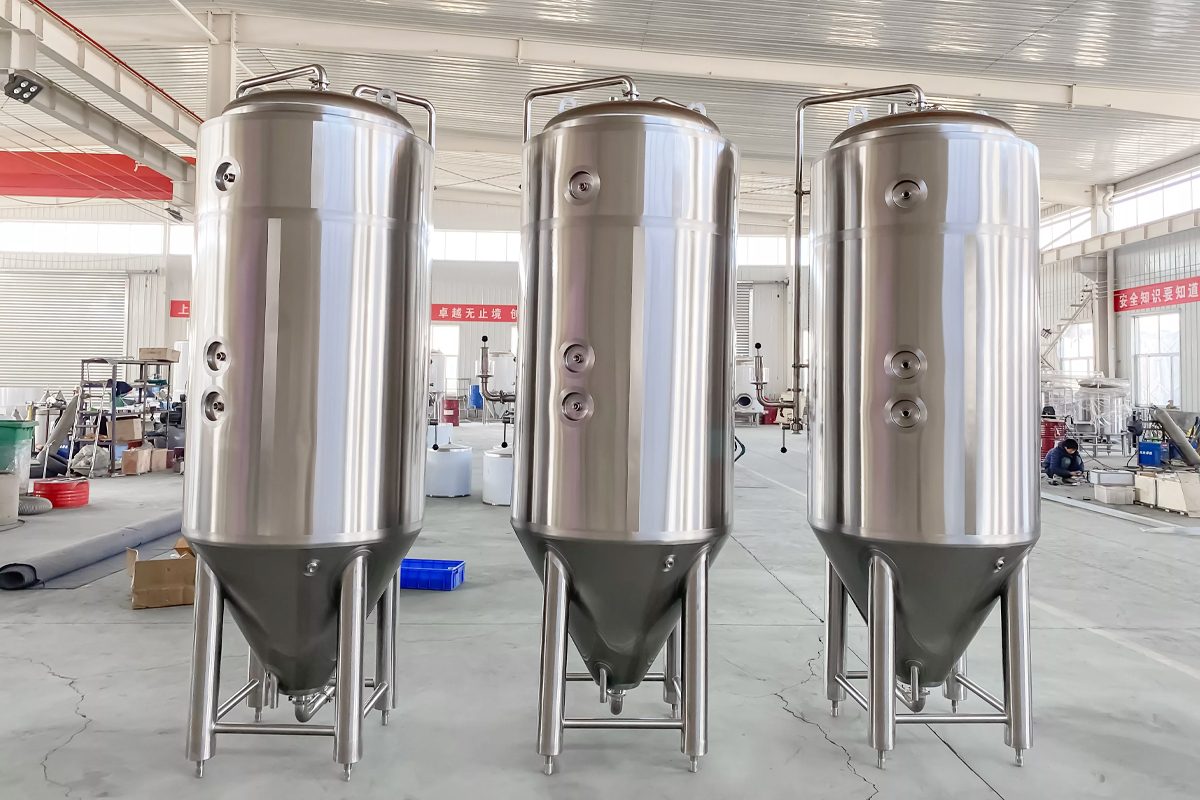
Automation and Control Systems
Automation and control systems are crucial elements that can significantly affect the initial investment in fermentation tanks. These systems provide precision in managing the fermentation process, optimizing efficiency, and minimizing manual intervention. While the inclusion of automation increases upfront costs, it also offers long-term benefits such as improved quality control, labor savings, and enhanced productivity, making it a valuable investment for breweries aiming to scale or improve consistency.
- Automated Temperature Control: Fermentation is a highly temperature-sensitive process, and automated control systems ensure that the desired temperature is maintained throughout the process. These systems typically include sensors that monitor the temperature inside the tank in real-time, automatically adjusting cooling or heating mechanisms as needed. Automated systems offer greater precision than manual methods, allowing brewers to focus on other tasks. Though these systems come at a higher initial cost, they reduce the risk of temperature fluctuations that could negatively impact beer quality, ensuring consistency across batches.
- Fermentation Process Monitoring: Advanced control systems can monitor various aspects of the fermentation process, such as pressure, CO2 levels, and yeast activity. These systems provide real-time data, enabling brewers to make informed decisions and quickly address any issues that may arise. While manual monitoring requires more labor and increases the risk of human error, automated systems allow for continuous oversight with minimal intervention. The ability to track fermentation in real-time reduces the likelihood of batch failure, making it a worthwhile investment despite the higher upfront costs.
- Remote Monitoring and Control: Many modern fermentation tanks come equipped with control systems that allow remote monitoring and management via computers or mobile devices. This level of automation is particularly beneficial for larger breweries or those operating multiple locations, as it enables brewers to oversee operations from anywhere. Although this advanced functionality increases the initial investment, it significantly improves operational flexibility and ensures that issues can be addressed quickly, minimizing downtime.
- Programmable Logic Controllers (PLCs): PLCs are commonly used in automated fermentation systems to control and coordinate various functions such as temperature, pressure, and timing. PLC-based systems are highly reliable and offer flexibility in programming custom brewing parameters. While they require a higher initial investment, their robustness and ability to automate complex brewing processes lead to improved production efficiency and product consistency. This is especially important for breweries that require repeatable precision across multiple batches.
- Labor Cost Reduction: Automation systems reduce the need for manual monitoring and adjustments, resulting in significant labor cost savings over time. By streamlining the fermentation process, these systems minimize human error and free up staff to focus on other critical tasks. Although this benefit comes at a higher upfront cost, it can result in considerable long-term savings, making automation a wise investment for breweries with plans to scale or improve efficiency.
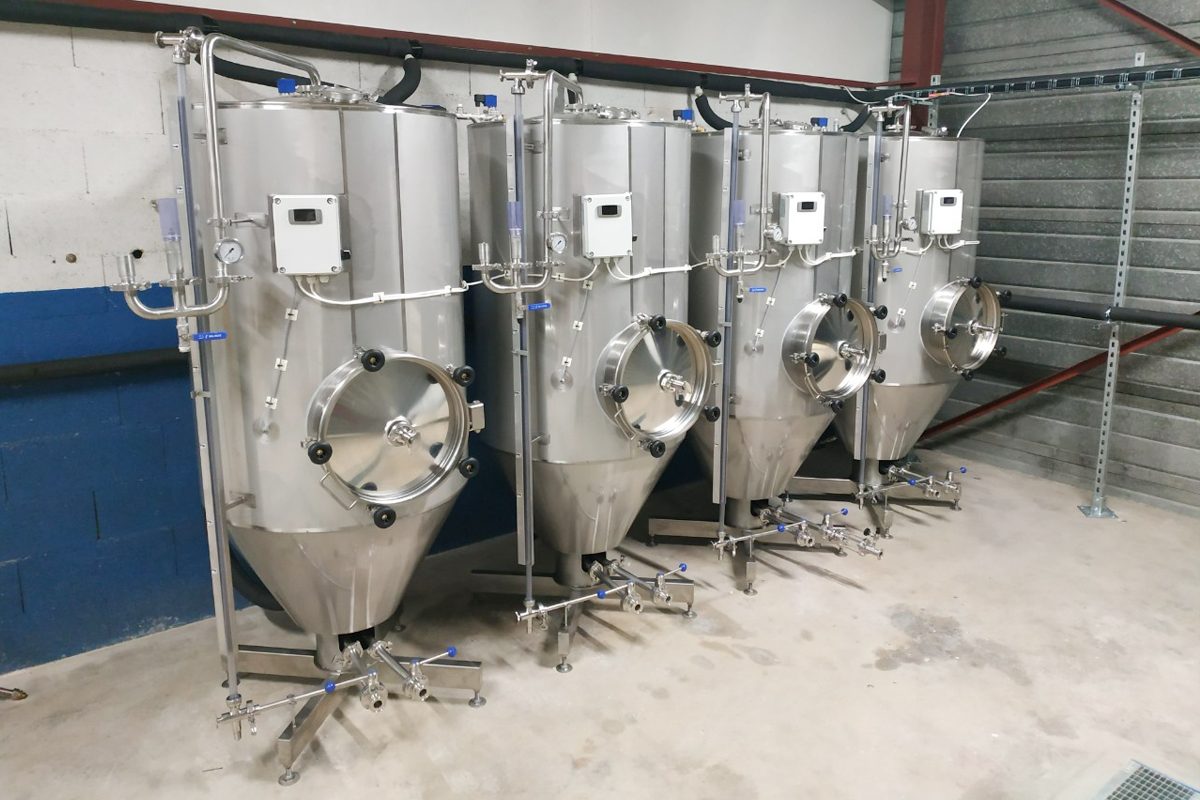
Installation and Site Preparation
Installation and site preparation are critical components that can significantly impact the initial investment in fermentation tanks. While the cost of the tanks themselves is important, breweries must also consider the expenses associated with preparing the site and installing the tanks. Factors such as the brewery’s infrastructure, available space, and required utilities play a major role in determining the overall cost of setup.
- Flooring and Structural Support: Fermentation tanks, particularly those with large capacities, can be extremely heavy, especially when filled with liquid. As a result, breweries often need reinforced flooring to safely support the weight. In many cases, this may involve upgrading or retrofitting existing floors with materials that can handle the increased load. For large-scale breweries, structural modifications may be necessary to ensure the building can support the installation of multiple tanks. This will increase the initial cost but will help ensure safety and durability.
- Space Requirements: The layout and available space within the brewery are important considerations when determining the type and size of fermentation tanks. Larger tanks may require more vertical space, which could necessitate adjustments to ceilings or roofs. Horizontal tanks, on the other hand, require more floor space and may need specialized support systems. Any spatial constraints or modifications needed to accommodate the tanks will influence the overall investment. Ensuring adequate space for both tanks and access to cleaning or maintenance areas is also important for long-term operational efficiency.
- Plumbing and Drainage: Proper piping aids in the operation and maintenance of fermentation tanks. Breweries must invest in drainage systems that allow for efficient cleaning, waste disposal, and management of excess liquid during the brewing process. Upgrading or installing new drainage systems to meet these demands can increase installation costs. Additionally, proper plumbing for Clean-In-Place (CIP) systems or water supply lines may need to be added or upgraded, depending on the brewery’s existing infrastructure.
- Electrical and Utility Setup: Fermentation tanks with advanced cooling systems, automated controls, or CIP systems require a reliable electrical supply to function properly. Breweries may need to upgrade their electrical infrastructure to support the energy demands of the tanks, cooling units, and automation systems. Larger tanks with more complex control systems may also need backup power sources or voltage stabilizers to ensure uninterrupted operation. Additionally, utility connections for water, cooling fluids, and waste disposal must be carefully planned and implemented, adding to the initial investment.
- Ventilation and Environmental Control: During fermentation, significant amounts of CO2 are produced, which must be safely vented from the brewery. Installing or upgrading ventilation systems to handle the byproducts of fermentation is a critical aspect of site preparation. Proper ventilation ensures a safe working environment and protects equipment from potential damage caused by excess moisture or gas buildup. In some cases, breweries may also need to install environmental control systems, such as air conditioning or humidity control, to maintain optimal brewing conditions.
- Installation Labor and Time: The complexity of installing fermentation tanks can vary depending on the size, design, and number of tanks being installed. For larger or more advanced tanks, specialized labor is often required to handle the installation, including fitting, welding, and aligning the tanks correctly. The cost of labor and the time required for installation should be factored into the overall budget, especially if delays in installation could affect the brewery’s production timeline.
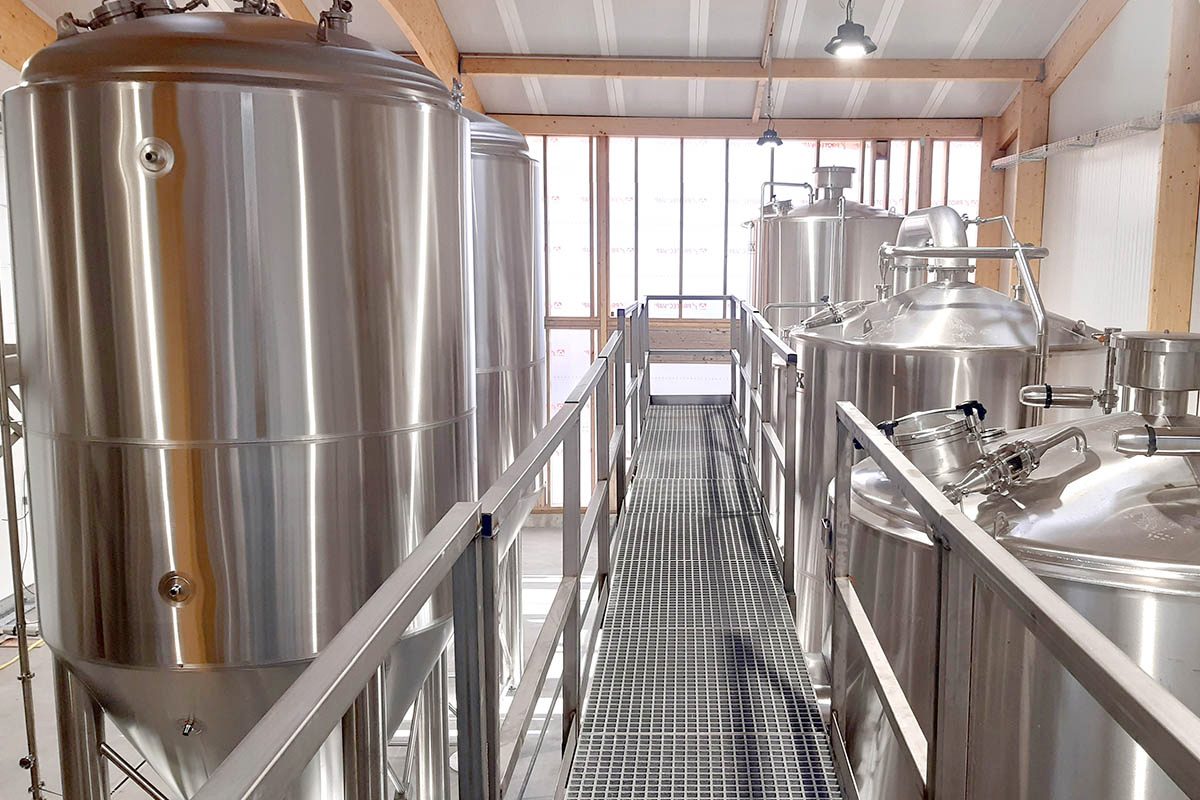
Branding and Aesthetics
Branding and aesthetics, while not directly related to the functionality of fermentation tanks, can significantly influence the initial investment for breweries that prioritize customer experience and brand identity. Particularly for breweries with public-facing operations, such as taprooms or tours, the appearance of fermentation tanks can play an important role in reinforcing the brewery’s image and creating a memorable experience for visitors. Although customization in design and branding adds to the upfront costs, it can be a worthwhile investment for breweries that want to differentiate themselves in a competitive market.
- Polished and Custom Finishes: Many breweries opt for polished stainless steel tanks to create a sleek, professional look. The highly polished finish is not only visually appealing but also easier to clean, enhancing both functionality and aesthetics. Custom finishes, such as mirror-polished or brushed textures, are often chosen to enhance the visual appeal of the brewing area. However, these options come with higher manufacturing costs due to the additional labor and materials required for the polishing process.
- Branded Logos and Design Elements: Incorporating a brewery’s logo or other branding elements into fermentation tanks can add a unique, personalized touch. Laser-etched logos, custom paint jobs, or wraps can transform standard tanks into a key part of the brewery’s brand identity. For breweries that host tours or use their brewing space as a customer-facing area, branded tanks serve as a marketing tool, reinforcing the brand and providing a visually cohesive experience for visitors. While adding logos or custom designs increases the initial cost, it enhances the brewery’s marketability and can have a lasting impact on customer engagement.
- Visible Tanks in Taprooms and Public Spaces: Many craft breweries position their fermentation tanks in areas visible to the public, such as taprooms, to create an immersive brewing experience. In these cases, the aesthetic appearance of the tanks becomes even more important. Investing in high-quality finishes and clean designs can make the brewery space more appealing to visitors, creating an inviting and professional atmosphere. Breweries that prioritize this customer experience often see a return on their investment through increased foot traffic, brand loyalty, and customer retention.
- Unique Shapes and Designs: In some cases, breweries may opt for tanks with non-standard shapes or custom designs to match the brewery’s theme or aesthetic. While this level of customization adds significantly to the initial investment, it can set the brewery apart from competitors by creating a one-of-a-kind environment. Unique tanks can become a talking point for customers, enhancing the brewery’s reputation and providing additional marketing opportunities.
- Impact on Brand Identity: The investment in aesthetically pleasing and branded fermentation tanks goes beyond mere appearance; it becomes part of the brewery’s identity. Breweries that invest in branding and aesthetics are more likely to leave a lasting impression on their customers, resulting in increased brand recognition and loyalty. While this may not directly impact the brewing process, the long-term marketing benefits can justify the higher initial costs.
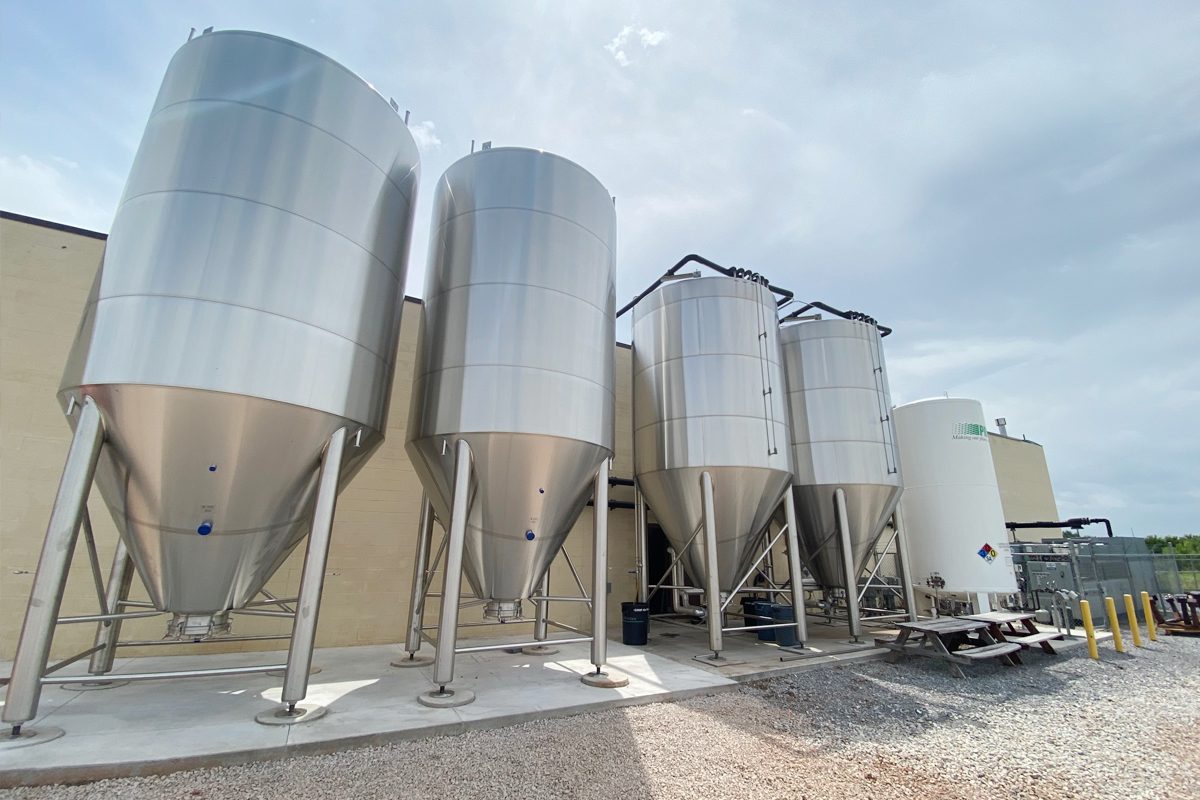
Infrastructure and Installation Costs
Infrastructure and installation costs are crucial considerations that significantly affect the initial investment in fermentation tanks. Beyond the cost of the tanks themselves, breweries must account for the expenses related to preparing the site, upgrading utilities, and ensuring that the facility can support the tanks and their operational requirements. These costs vary based on the size of the tanks, the complexity of the brewing process, and the existing infrastructure at the brewery’s location.
- Flooring and Structural Reinforcement: Fermentation tanks, especially large-capacity tanks, are extremely heavy, particularly when filled with liquid. Ensuring the brewery’s floor can handle this weight is essential. In many cases, the floor may need to be reinforced or upgraded to prevent damage or instability. This could involve using stronger materials, installing reinforced concrete, or retrofitting existing structures to support the weight. These upgrades increase the initial investment, but they help ensure the safety and longevity of the equipment.
- Utility Upgrades (Plumbing, Electrical, and Ventilation): Fermentation tanks require robust utility connections to function properly. This includes access to water, drainage systems for waste disposal, and electrical power for automated controls, temperature regulation, and cleaning systems. In many cases, existing utility setups are insufficient for the increased demands of new fermentation tanks, especially in large-scale operations. Upgrading plumbing systems, installing new drainage solutions, and ensuring the brewery has the appropriate electrical infrastructure can increase the initial investment considerably. Additionally, proper ventilation is necessary to safely manage the CO2 produced during fermentation, which may require upgrades to the building’s HVAC systems.
- Cooling Systems Installation: Fermentation tanks often rely on glycol cooling systems to maintain the optimal temperature for fermentation. Installing these systems involves connecting the tanks to a chiller, running piping, and ensuring that the refrigeration units are properly installed and sized for the brewery’s needs. The cost of this installation varies based on the complexity of the cooling system and the number of tanks. Breweries that invest in energy-efficient cooling systems may face higher upfront costs but will benefit from reduced operational expenses in the long term.
- Tank Delivery and Setup: The process of delivering and installing fermentation tanks can be a significant cost factor, particularly for larger tanks. The tanks may need to be transported in sections or require specialized equipment, such as cranes, for installation. Installation involves positioning the tanks, connecting utilities, and ensuring all systems are properly aligned and operational. For custom or large-scale tanks, installation may take several days or weeks, further increasing labor costs. Breweries located in areas with limited access or those that require special permits for tank installation may see even higher costs.
- Space Optimization: The layout of the brewery plays a significant role in installation costs. Breweries with limited space may need to invest in customized tanks or modify the facility to accommodate larger tanks. This could include raising ceilings, expanding floor space, or rearranging existing equipment to ensure proper workflow and safety. Space optimization work, including design consultation, may increase overall costs but can help maximize efficiency and ensure your brewery runs smoothly.
- Regulatory Compliance and Inspections: In many regions, installing fermentation tanks requires compliance with local building codes, safety regulations, and environmental standards. This often involves applying for permits, scheduling inspections, and ensuring the installation meets all legal requirements. The cost of these regulatory steps, along with any necessary adjustments to meet compliance, can add to the overall investment. Failure to meet these standards could lead to fines or delays in production, making it important to factor these costs into the initial budget.
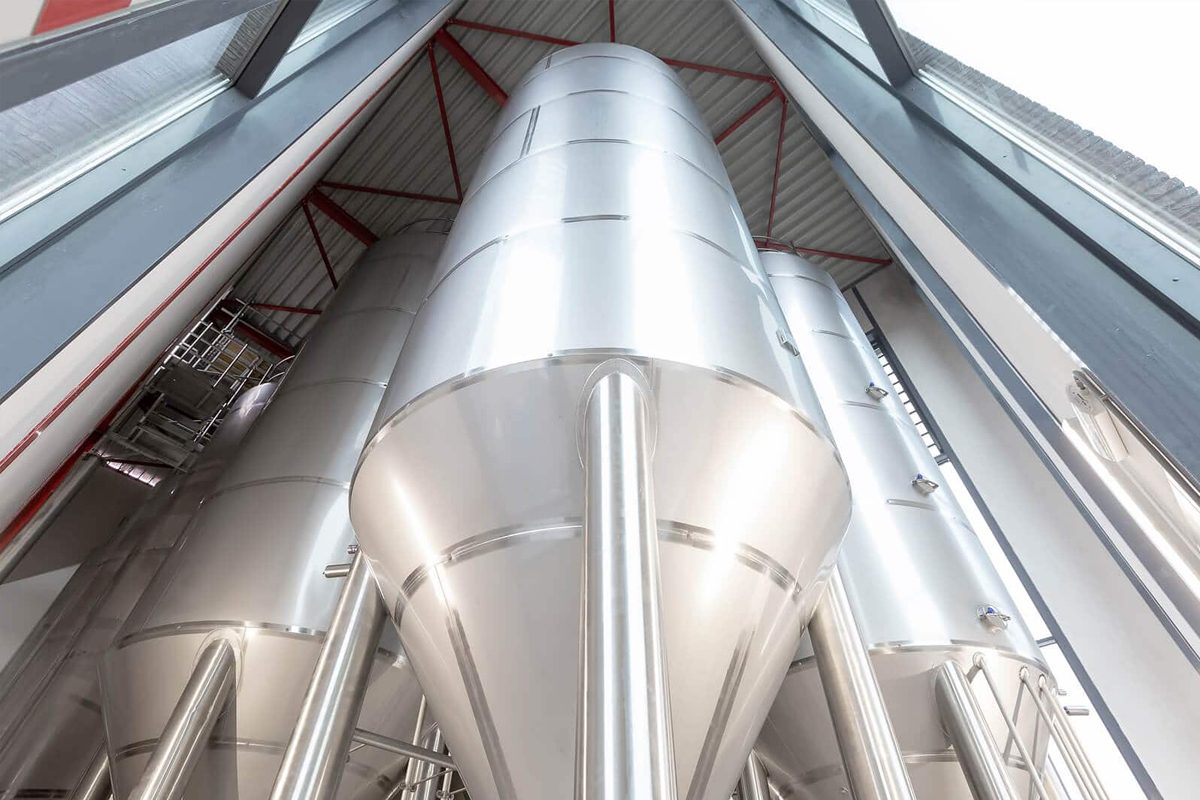
Vendor and Manufacturer Considerations
Choosing the right vendor or manufacturer is a crucial factor that significantly affects the initial investment in fermentation tanks. The reputation, reliability, and expertise of the manufacturer not only influence the upfront cost but also the long-term performance and durability of the tanks. Different vendors offer various levels of customization, support, and post-purchase services, all of which play a role in determining the overall investment.
- Manufacturer Reputation and Experience: Working with an established and reputable manufacturer ensures that you are purchasing high-quality fermentation tanks designed for long-term use. Experienced manufacturers typically have a track record of delivering reliable products that meet industry standards. They understand the specific needs of breweries and offer tanks that are optimized for different brewing processes. While tanks from a reputable manufacturer may come with a higher price tag, the investment is justified by the improved durability, performance, and lower risk of malfunctions.
- Customization Options: Vendors that offer tailored solutions, such as custom tank sizes, specialized shapes, or additional features (e.g., integrated CIP systems or cooling jackets), tend to have higher upfront costs. However, these customizations ensure that the fermentation tanks are optimized for the brewery’s specific requirements, improving operational efficiency and productivity. Manufacturers with extensive customization options can provide better solutions that are aligned with the brewery’s long-term goals, reducing the need for costly modifications or replacements in the future.
- Support and After-Sales Services: The level of support provided by the vendor or manufacturer can significantly affect the overall value of the investment. Vendors that offer comprehensive after-sales services, such as installation assistance, maintenance training, and troubleshooting, reduce the likelihood of costly downtime and operational issues. Additionally, ongoing technical support ensures that any issues with the tanks are quickly addressed, minimizing disruptions to production. Investing in a vendor with a strong support network may cost more initially, but it pays off through reduced maintenance expenses and improved equipment longevity.
- Warranty and Service Agreements: A manufacturer’s warranty and service agreement are important considerations that impact the total cost of ownership. Tanks with longer warranties or more extensive coverage tend to cost more upfront but offer better protection against defects or performance issues. Service agreements that include regular inspections, maintenance, or emergency repairs can further reduce long-term costs by ensuring that the tanks remain in optimal condition. Breweries should carefully review the warranty terms and service agreements offered by each vendor to understand what is included in the initial investment and what additional costs might arise in the future.
- Lead Times and Delivery Costs: The time it takes for a vendor to manufacture and deliver the tanks can affect both the initial investment and the brewery’s production timeline. Vendors with shorter lead times may charge a premium for expedited orders, while those with longer lead times may offer lower prices but delay the brewery’s operations. Additionally, delivery costs vary depending on the distance, tank size, and complexity of transportation. Breweries should balance the need for timely delivery with the associated costs and ensure that the vendor can meet their production schedule without significantly increasing the budget.
- Compliance with Industry Standards and Certifications: Ensuring that the vendor’s tanks comply with industry regulations and certifications is essential to avoid potential legal and operational issues. High-quality fermentation tanks should meet food-grade and safety standards, such as ASME (American Society of Mechanical Engineers) or PED (Pressure Equipment Directive) certifications. Tanks that meet these standards tend to have a higher initial cost due to the rigorous testing and quality assurance processes involved in their production. However, purchasing certified tanks reduces the risk of compliance issues, ensuring that the brewery operates legally and safely.
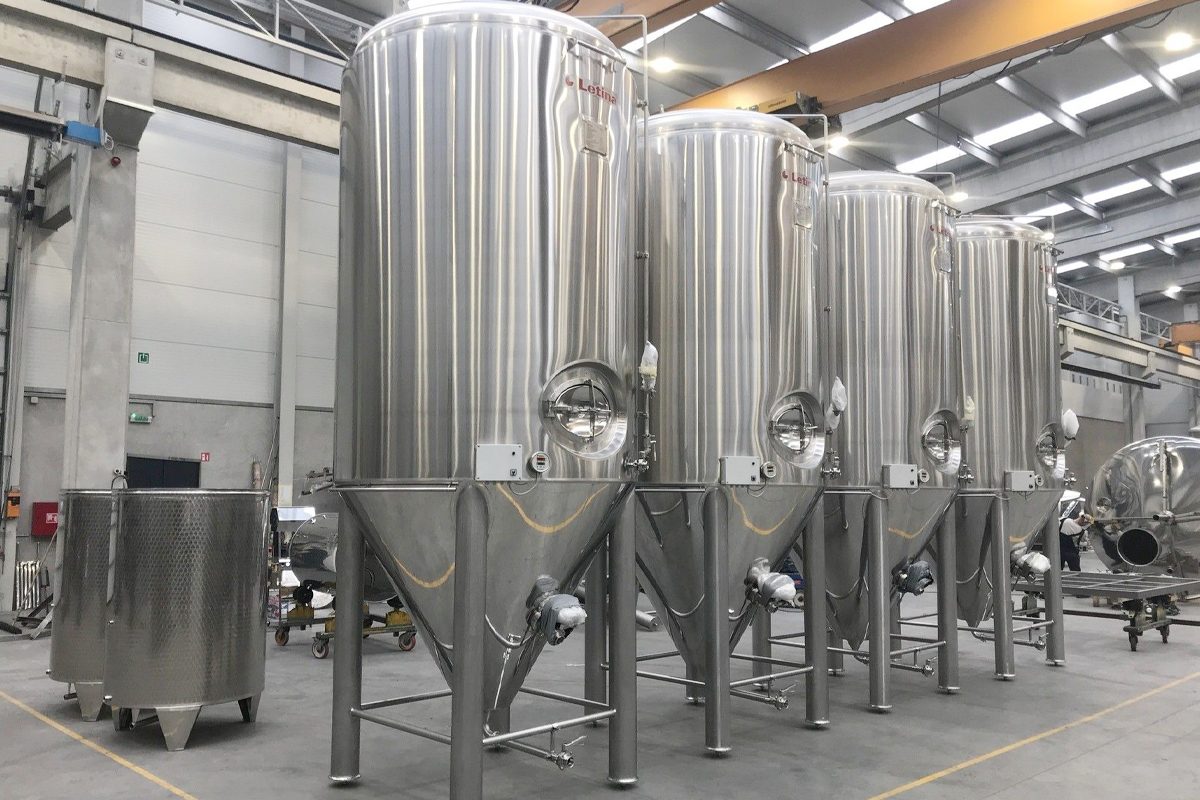
Summary
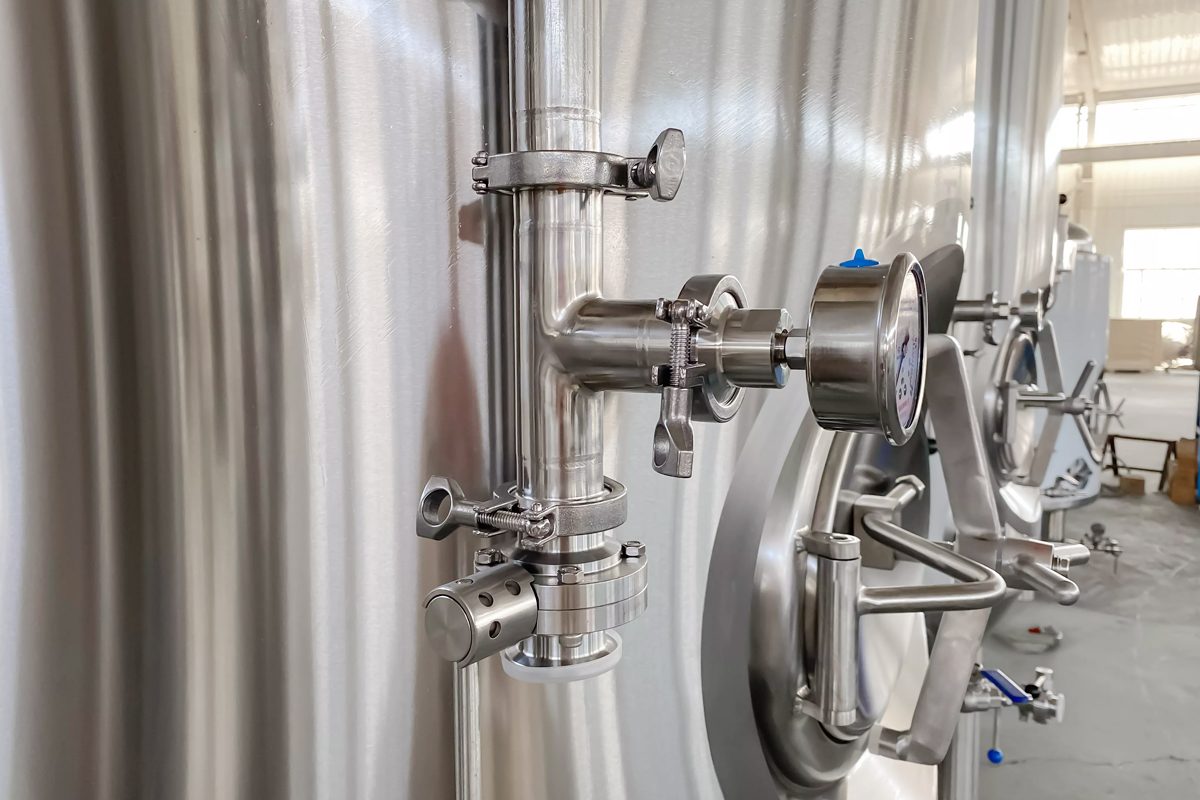