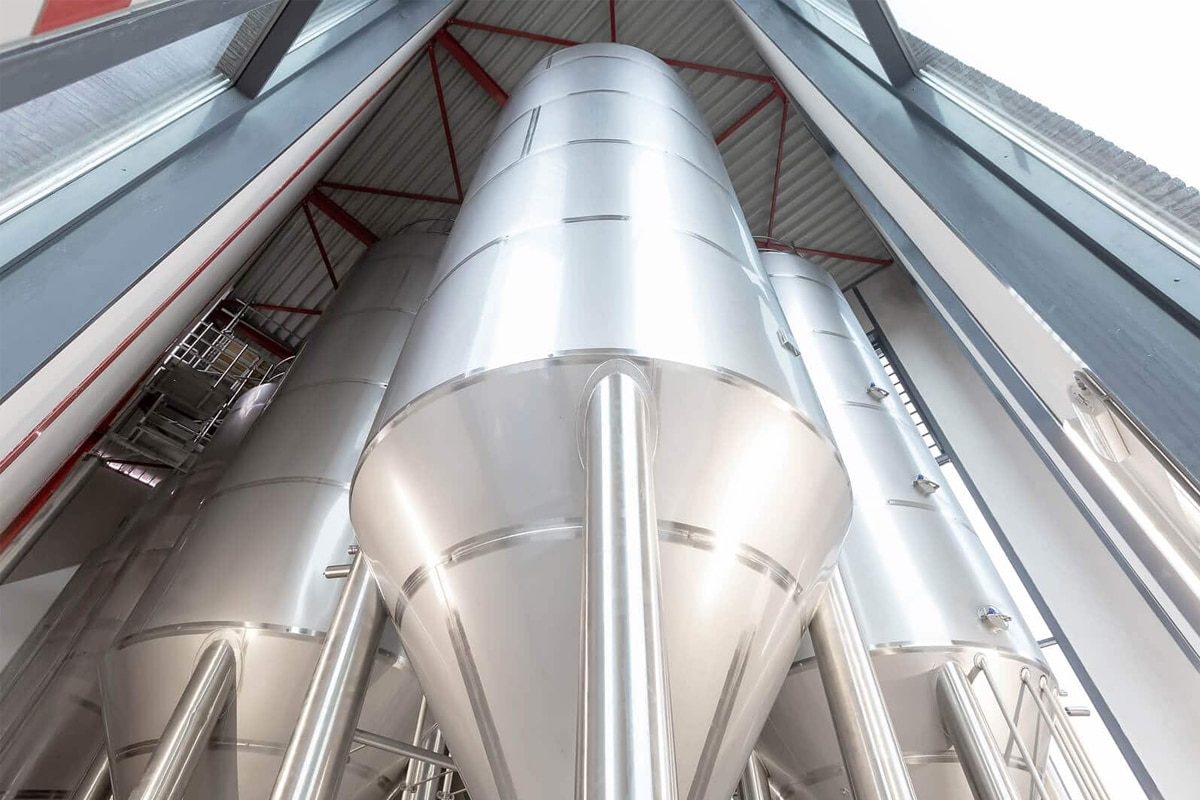
Decoding Conical Fermentation Tanks: A Comprehensive Evaluation of Brewery Equipment
In the dynamic world of home brewing, art meets science, and every step of the brewing process is meticulous, contributing to the symphony of flavors that defines great beer. Among the many devices available to brewers, the conical fermentation tank stands out as a complex and interesting tool that promises to take the brewing experience to new heights. As we began to dissect the complexities of this equipment, we found ourselves at a crossroads, pondering a key question: Are conical fermentation tanks worth the investment?
The art of brewing has evolved tremendously, reflecting the passion and dedication of those who strive for perfection in every pint. From the humble beginnings of traditional fermentation tanks to the emergence of cutting-edge technology, brewers are always looking for tools that enhance their process and final product. With their unique shape and numerous features, conical fermentation tanks are gaining attention as potential game-changers in the pursuit of excellence in brewing.
In this exploration, we delve into the heart of the brewing process, taking a closer look at the benefits and considerations of adopting a conical fermentation tank. As we explore the intricate landscape of brewery equipment, our goal is to demystify the mysteries surrounding this special vessel and provide insights that will allow brewers to make informed decisions about the next step in their beer journey.
Comprehensive Evaluation of Brewery Equipment
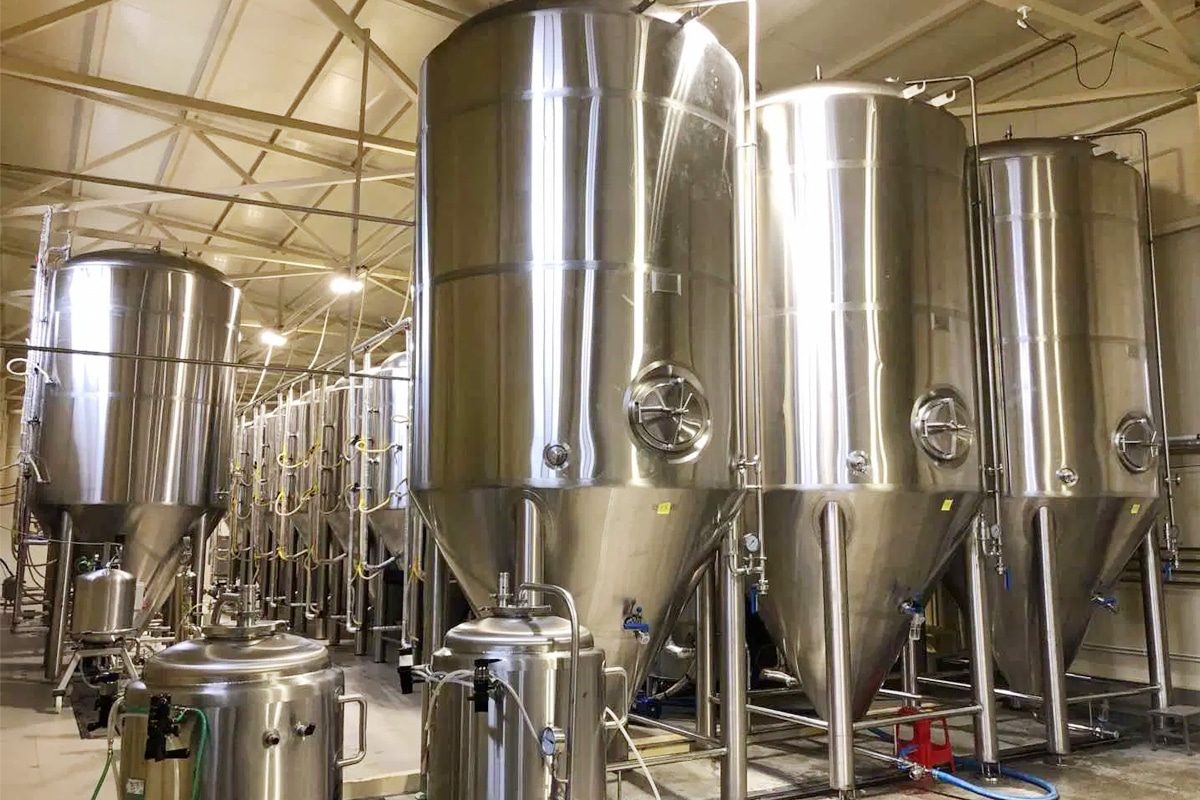
The Evolution of Fermentation Tanks
The vessels used to alchemize wort into beer have undergone significant evolution in the ancient art of brewing. From the humble clay amphora of the past to the sleek, purpose-designed stainless steel fermentation tanks of today, the journey of the fermenter is a testament to the ingenuity and passion of brewers for their craft. This evolution reached its zenith with the advent of the conical fermentation tank, a design that embodied both functionality and sophistication.
The history of fermentation vessels goes back to the origins of brewing itself. Early brewers relied on natural materials such as wood, clay, and even animal hides to contain and ferment their blends. These crude vessels often lack precise temperature control and sanitation, but are the crucibles where the magic of fermentation is revealed.
With the advent of the industrial age, the brewing industry transformed. Fermentation vessels were converted from traditional materials to clinically attractive stainless steel. This significant improvement results in better sanitation, temperature control, and equipment longevity. Stainless steel fermenters have become emblematic of modern winemaking practices as winemakers seek to improve their processes.
Against the backdrop of this progress, the conical fermentation tank emerged as a revolutionary design. Its signature feature is a conical shape that tapers toward the base, unlike the cylindrical tanks that dominate the brewing world. This innovative design is more than just an aesthetic choice, it offers practical benefits that will redefine the brewing experience.
The conical shape of these fermentation tanks allows sediments, including yeast and residue, to settle on the bottom. This separation simplifies the process of harvesting yeast for future batches, reduces the risk of off-flavors, and improves the overall quality of the beer. Temperature control, a key aspect of fermentation, has also been upgraded, with many conical fermentation tanks having built-in cooling systems, giving brewers unprecedented control over their beer.
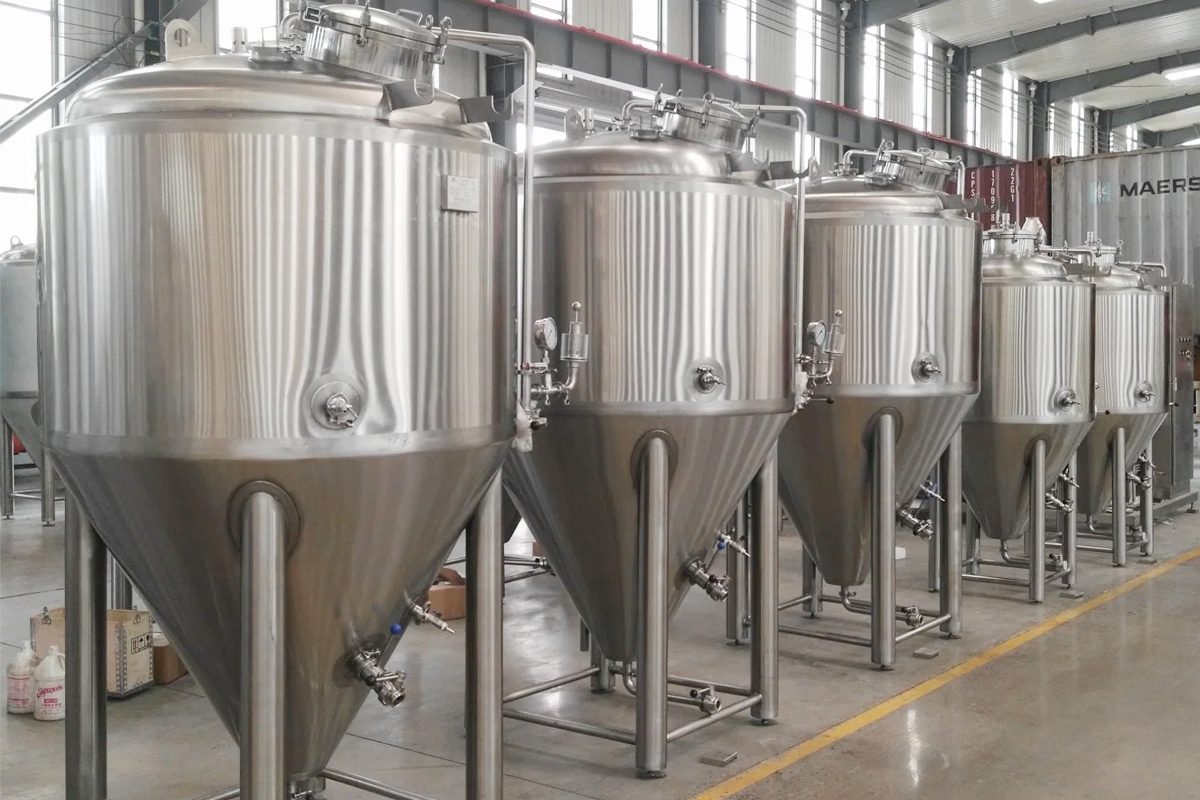
Learn About Conical Fermentation Tanks
In the hustle and bustle world of commercial brewing, where every jar, valve, and vessel contributes to the symphony of flavors poured into glasses from around the world, equipment selection becomes an art in itself. Among the many fermentation tanks available, the conical fermentation tank stands out as a sophisticated and versatile vessel that attracts the attention of discerning winemakers. To truly understand the importance of this type of brewing equipment, let’s embark on a journey to understand the intricacies of conical fermentation tanks in the commercial brewing world.
Define Conical Fermentation Tank
Essentially, a conical fermentation tank is a specialized vessel designed to facilitate the fermentation process in its unique conical shape. Unlike traditional cylindrical fermentation tanks, the conical design offers unique advantages from yeast management to temperature control.
Craftsmanship And Design
Conical fermentation tanks are usually made of materials such as stainless steel and are durable, hygienic, and easy to clean. The defining feature of the conical shape is not only an aesthetic choice, but also a functional one. As fermentation proceeds, the conical shape allows sediment, including yeast and residue, to settle at the bottom. This separation helps maintain the clarity and purity of the beer, ensuring that every sip is a testament to the brewer’s artistry.
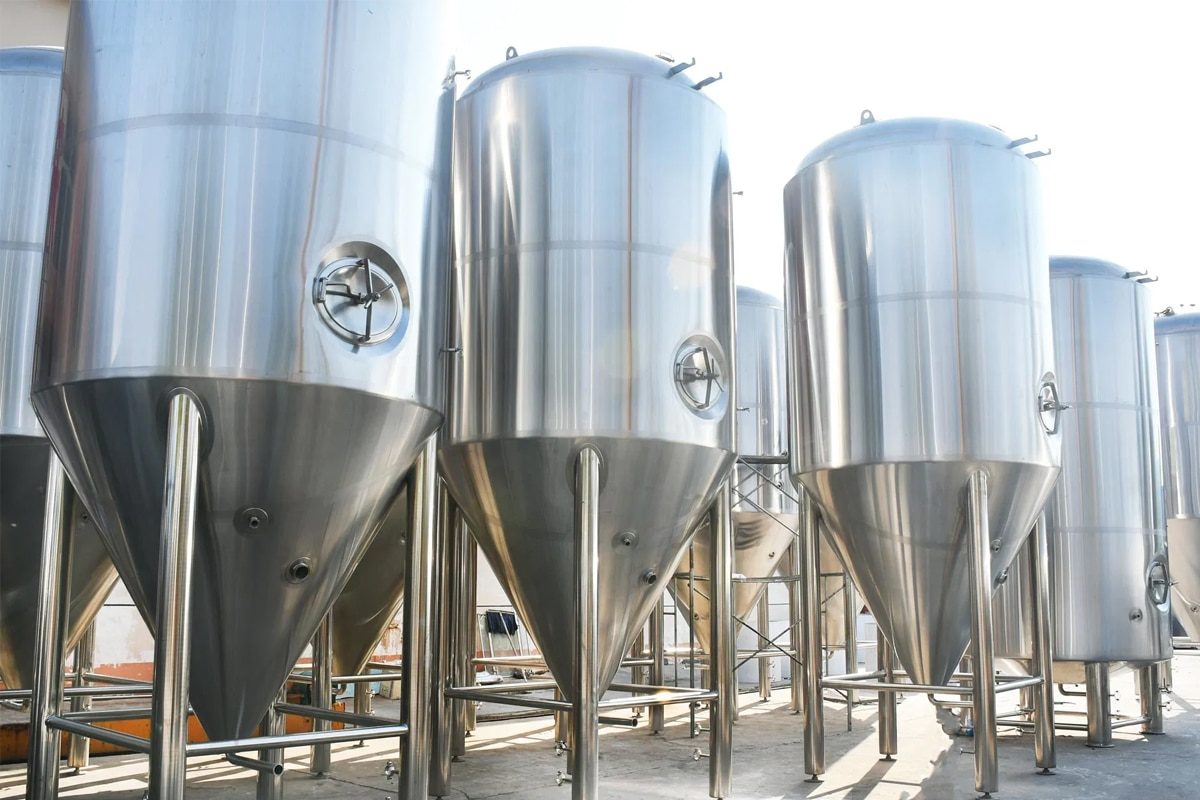
Advantages of Conical Fermentation Tanks
In the dynamic landscape of commercial brewing, where precision and innovation determine success, equipment selection is a critical factor in shaping the essence of the beverage produced. Of the countless tools at a brewer’s disposal, the conical fermentation tank serves as a beacon of efficiency and craftsmanship. Let’s delve into the complex benefits conical fermentation tanks offer and demonstrate their transformative impact on the brewing process in the commercial brewing world.
Strengthen Yeast Management
The fermentation tank’s conical shape facilitates excellent yeast management. As fermentation proceeds, the yeast cells that are critical to the fermentation process settle to the bottom due to gravity. The design makes it easy to collect and separate yeast from beer. This feature simplifies the process of harvesting and reusing yeast for subsequent batches, ensuring consistent flavor profiles and reducing costs associated with yeast procurement.
Improved Residue Removal
Conical fermentation tanks excel at separating lees, the undesirable sediment of hop particles and proteins, from beer. The tapered bottom guides these particles downward, separating them from the liquid above. This effective method of removing residue produces a clearer, more visually appealing beer that minimizes off-flavors and delivers a smoother taste.
Temperature Control Accuracy
Temperature control is a key aspect of fermentation, affecting yeast activity and therefore the flavor profile of the beer. Many commercial-grade conical fermentation tanks are equipped with advanced temperature control mechanisms. Whether through an integrated cooling system or an external control unit, brewers can fine-tune and maintain optimal fermentation temperatures. Precise temperature control mechanisms allow breweries to fine-tune and regulate the fermentation process, ensuring batch-to-batch consistency and achieving desired flavor profiles, helping to enhance brand image and consumer expectations.
Simplify Sampling And Testing
Sampling ports in the conical fermentation tank facilitate easy access to beer during fermentation without compromising the integrity of the entire batch. Brewers can monitor fermentation progress in real-time by taking small samples for tasting or analysis. This feature allows for timely adjustments and interventions to ensure the beer meets the desired flavor profile.
Space Efficiency
Conical fermentation tanks optimize space utilization in commercial breweries with their efficient design. Compared with traditional fermentation tanks, it has a compact footprint and can utilize the floor space more efficiently. For breweries where space is at a premium, this space-saving approach becomes a valuable asset to install more equipment in the brewing area or streamline workflow.
Improve Oxygen Control
Exposure to oxygen during fermentation can cause beer off-flavors and reduced quality. The conical fermentation tank has a sealed design that minimizes the risk of oxygen ingress. This sealed environment not only enhances the beer’s stability but also extends its shelf life, a key factor in commercial beer competition.
Facilitates Dry Hopping And Flavor Addition
For breweries experimenting with innovative hop characteristics or flavor additions, conical fermentation tanks provide a convenient platform. The tapered shape allows hops or other flavor-enhancing elements to be added directly to the fermentation tank. This allows for a seamless integration of flavors, helping to create a unique and memorable beer.
Versatility And Flexibility
Conical fermentation tanks typically come in a variety of sizes and configurations to suit different production volumes. This versatility allows breweries to scale up production without compromising quality. Additionally, some fermentation tanks may include customizable features or accessories that provide flexibility to the brewing process and accommodate various beer styles or experimental brews.
Increase Hygiene And Cleaning
The construction of conical fermenters is usually made of durable and easy-to-clean materials such as stainless steel, which facilitates strict sanitation procedures. The fermenter’s shape and accessibility make it easier to reach and clean every nook and cranny, reducing the risk of contamination and ensuring a hygienic brewing environment.
Efficient CIP (cleaning in place) Process
Maintaining impeccable cleanliness is an aspect of commercial brewing that cannot be ignored. Conical fermenters are often designed with accessibility in mind, making the clean-in-place (CIP) process more efficient. Winemakers have easy access to all surfaces, ensuring thorough cleaning and sanitation between batches.
The advantages of conical fermentation tanks in commercial brewing are significant. It simplifies key aspects of the brewing process, from yeast management and residue removal to temperature control and space efficiency. These fermentation tanks not only contribute to stable and high-quality beer production but also provide brewers with greater control, flexibility, and cost-effectiveness in their operations.
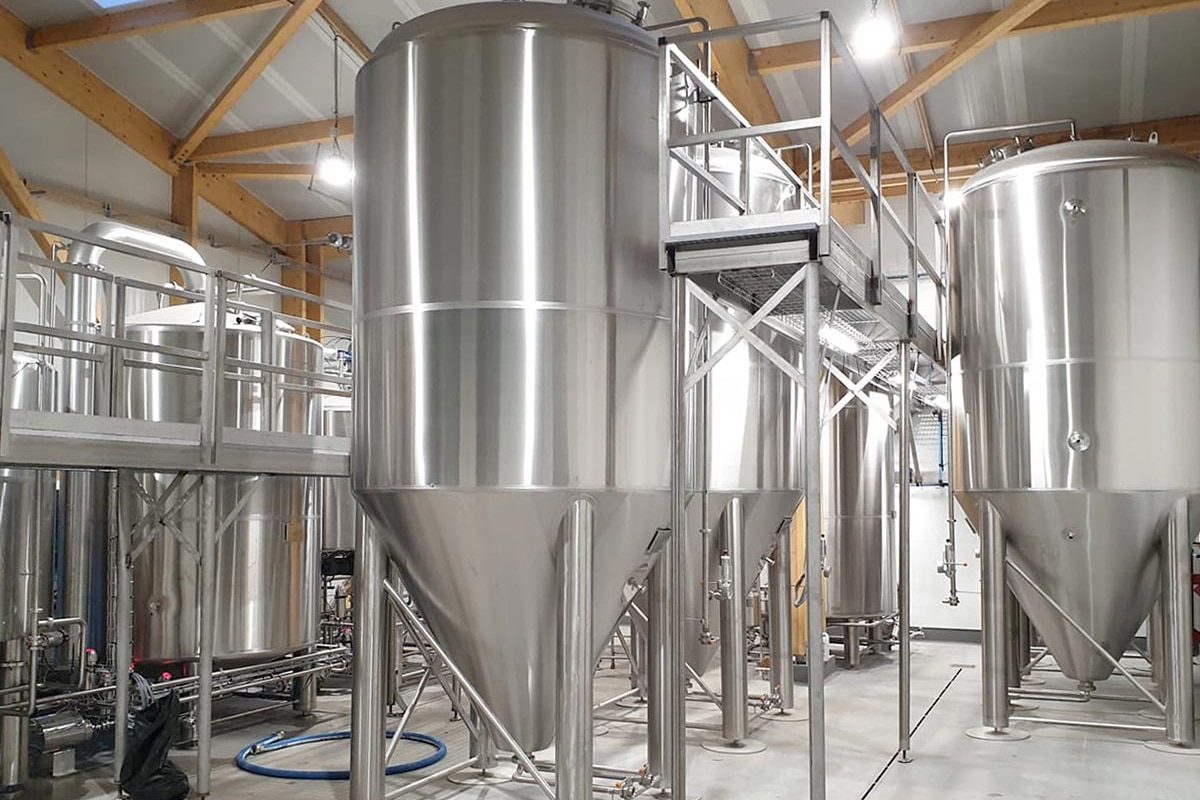
Disadvantages of Conical Fermentation Tanks
Exploring the potential disadvantages of conical fermentation tanks can help give you a full picture. While these containers offer many advantages, it is also crucial to weigh their disadvantages, especially in the context of commercial brewing. Here’s a closer look at the potential drawbacks:
Higher Initial Cost
One of the main disadvantages of conical fermentation tanks is their higher upfront cost compared to traditional fermentation tanks. Exquisite design, materials, and additional features drive the price up. For small or start-up breweries with a limited budget, this initial investment can present significant financial challenges.
Design Complexity
The complex design of the conical fermentation tank, while providing advantages, can also be a double-edged sword. Additional features such as built-in temperature control systems and sampling ports add to the complexity. This complexity may require more comprehensive training for brewery staff, which may result in a steeper learning curve, especially for those accustomed to simpler fermentation vessels.
Increased Cleaning And Maintenance
The complex design of conical fermentation tanks, with their curved surfaces and specialized fittings, can make cleaning and maintenance more labor-intensive than simpler fermenter models. This complexity can require additional time and effort for thorough cleaning, potentially resulting in increased labor costs and downtime during maintenance.
Limited Scalability
While many conical fermentation tanks can accommodate different batch sizes, some models may have limitations in scalability. Smaller units may not be able to accommodate the volume growth of a rapidly expanding brewery. This limitation requires careful consideration during the selection process to ensure that the selected fermentation tank meets current and future production needs.
Space Constraints
While conical fermentation tanks are generally space efficient, some larger models or configurations may require sufficient headroom for installation and operation. When considering these larger fermentation tanks, the brewing facility’s limited vertical space or ceiling height may pose a challenge, limiting their suitability for some breweries. Brewers must evaluate whether the benefits of space efficiency outweigh any potential space challenges.
Possibility of Oxygen Exposure
Some conical fermentation tanks, especially those with larger openings or longer exposure times during sampling, may pose a risk of increased oxygen contact with the beer. Exposure to oxygen can cause oxidation, affecting the flavor and shelf life of your beer. Brewers need to implement strict procedures to minimize the ingress of oxygen at all stages of brewing.
Potential Yeast Stress
Despite the advantages of conical fermentation tanks for yeast management, conical fermentation tanks, especially those with steep cones, may subject the yeast cells to greater stress and stress as they settle to the bottom. This stress can affect yeast viability and performance, affecting the consistency of subsequent batches.
Learning Curve And Training Needs
For breweries transitioning from traditional fermentation tanks to conical fermentation tanks, there may be a learning curve for brewing staff. Training and familiarity with the operation, maintenance, and specific functions of these fermentation tanks may be required, resulting in a potential adjustment period and additional resource allocation for education and training.
Customization Cost
While versatility is an advantage of conical fermentation tanks, customization to meet specific brewing requirements may require additional costs. Breweries looking for highly specialized features or configurations tailored to unique brewing processes may find that the price tag of custom options adds to the overall investment.
Limited Availability of Some Features
Not all conical fermentation tanks are equipped with the same features. Some entry-level or budget-friendly models may lack advanced features, such as integrated temperature control systems or sophisticated sampling mechanisms. Brewers must carefully evaluate whether the available features fit their specific brewing needs and goals.
While conical fermentation tanks offer significant advantages in terms of yeast management, temperature control, and efficiency, it is also important to consider these potential disadvantages. Each brewery’s unique circumstances, operational needs, and budget constraints should be carefully evaluated when determining whether an investment in a conical fermentation tank is consistent with its brewing goals and resources.
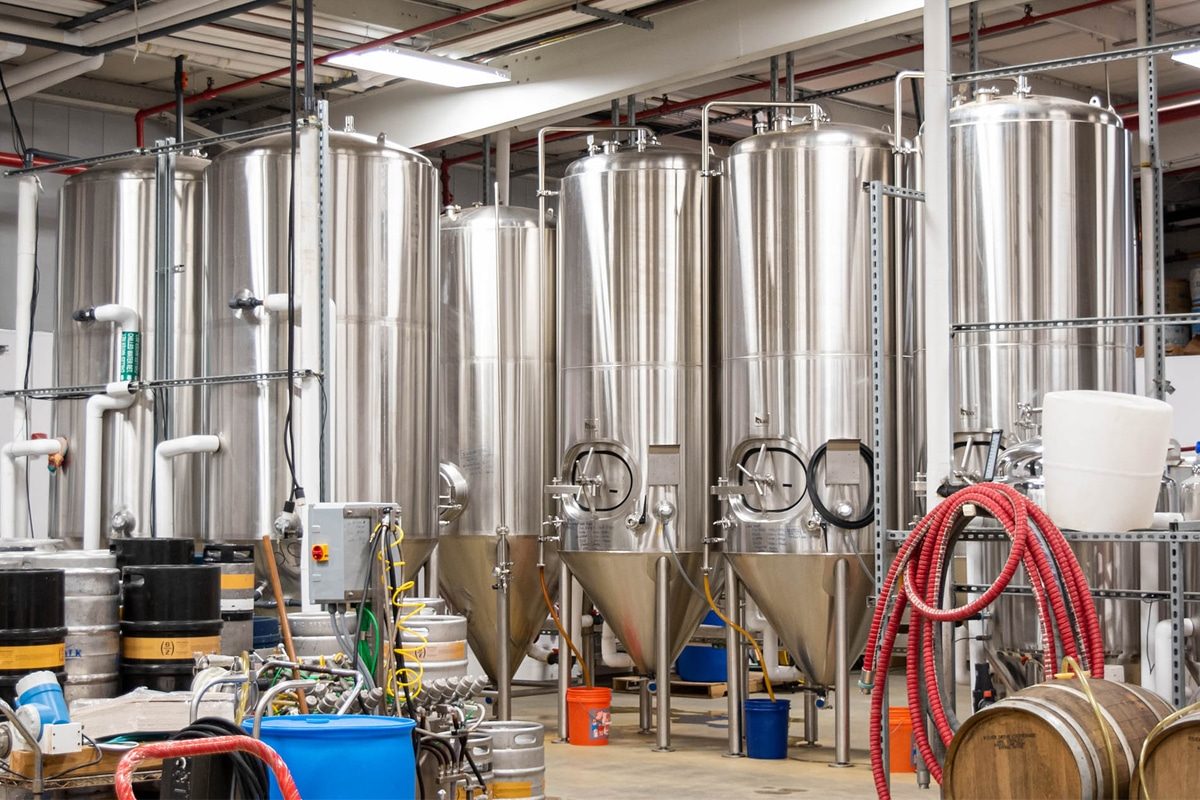
Things To Consider Defore Investing in A Conical Fermentation Tank
The decision to invest in a conical fermentation tank is a critical moment for any brewery that requires a thorough evaluation of a variety of factors to ensure compliance with brewing goals, operational needs, and financial constraints. Before entering the world of conical fermentation tanks, brewers should carefully consider several key factors to make an informed strategic decision.
Scalability And Batch Size
Conical fermentation tanks come in a variety of sizes, and breweries must carefully match the fermentation tank’s capacity to their typical batch size and scalability goals. Investing in fermentation tanks that match your brewery’s output ensures optimal efficiency and utilization of your equipment.
Budget Constraints
For any brewery considering purchasing a conical fermentation tank, financial aspects are usually the first consideration. These containers come with advanced features and sturdy construction at a premium price. Breweries must conduct a detailed cost-benefit analysis, weighing the initial investment against the long-term advantages that conical fermentation tanks will bring to their brewing process.
Cleaning And Maintenance Requirements
The complex design of conical fermentation tanks may require more meticulous cleaning and maintenance procedures than traditional fermentation tanks. Brewers should evaluate their willingness and ability to invest time, energy, and resources to keep their equipment in optimal condition. Cleaning regimen, frequency, and potential downtime during maintenance should be considered.
Available Space
The physical space of the brewery is a key consideration, especially for larger conical fermentation tanks. Breweries should evaluate whether their facility has the necessary space for installation, operation, and potential expansion. Vertical space considerations, especially for fermentation tanks with taller designs, are critical to preventing brewing area restrictions.
Device Compatibility And Integration
Ensure compatibility and integration of conical fermentation tanks with existing brewing equipment and infrastructure. Compatibility with pumps, hoses, temperature control systems, or other ancillary equipment facilitates seamless operation and workflow.
Consider Local Regulations
Depending on the region or country, there may be specific regulations for the use of certain brewing equipment. Breweries should ensure that the selected conical fermentation tank complies with local standards and regulations to avoid potential legal or operational complications.
Experience Level of Brewing Staff
The complexity of conical fermentation tanks, especially those with advanced features, can present challenges for less experienced brewers. Breweries should evaluate their team’s experience level and consider whether additional training or support is needed to take full advantage of the benefits of conical fermentation tanks.
Brewing Process Flexibility
Breweries with a diverse brewing portfolio or who tend to experiment should evaluate whether their chosen conical fermentation tank supports the flexibility needed for a variety of brewing processes and beer styles. Customizable features or accessories can enhance adaptability to different brewing scenarios.
Supplier Reputation And Support
Choosing a reputable supplier is crucial. Breweries should research potential suppliers thoroughly, evaluating their reputation, customer reviews, and after-sales support. Reliable customer support and readily available spare parts are important components of a successful long-term relationship with your equipment supplier.
Long-Term Brewing Strategy
The decision to invest in a conical fermentation tank should be consistent with a brewery’s long-term brewing strategy. Breweries should envision how fermentation tanks will fit into their future expansion plans, brewing goals, and the evolving landscape of the craft beer industry.
Staff Training And Expertise
Evaluate the brewing team’s familiarity and expertise with conical fermentation tanks. Consider the need for training or educational resources to ensure staff are skilled in operating, cleaning, and maintaining fermentation tanks to maximize their efficiency.
Temperature Controls And Features
Evaluate the specific features required for conical fermentation tanks, such as built-in temperature control systems, cooling jackets, insulation, or sampling ports. Combine these capabilities with the brewing process, the level of control required, and the consistency to achieve a specific flavor profile.
By carefully considering these factors before purchasing a conical fermentation tank, breweries can make an informed decision that maximizes potential advantages. At the same time, this also helps mitigate any challenges or limitations associated with integrating the equipment into your brewing operation.
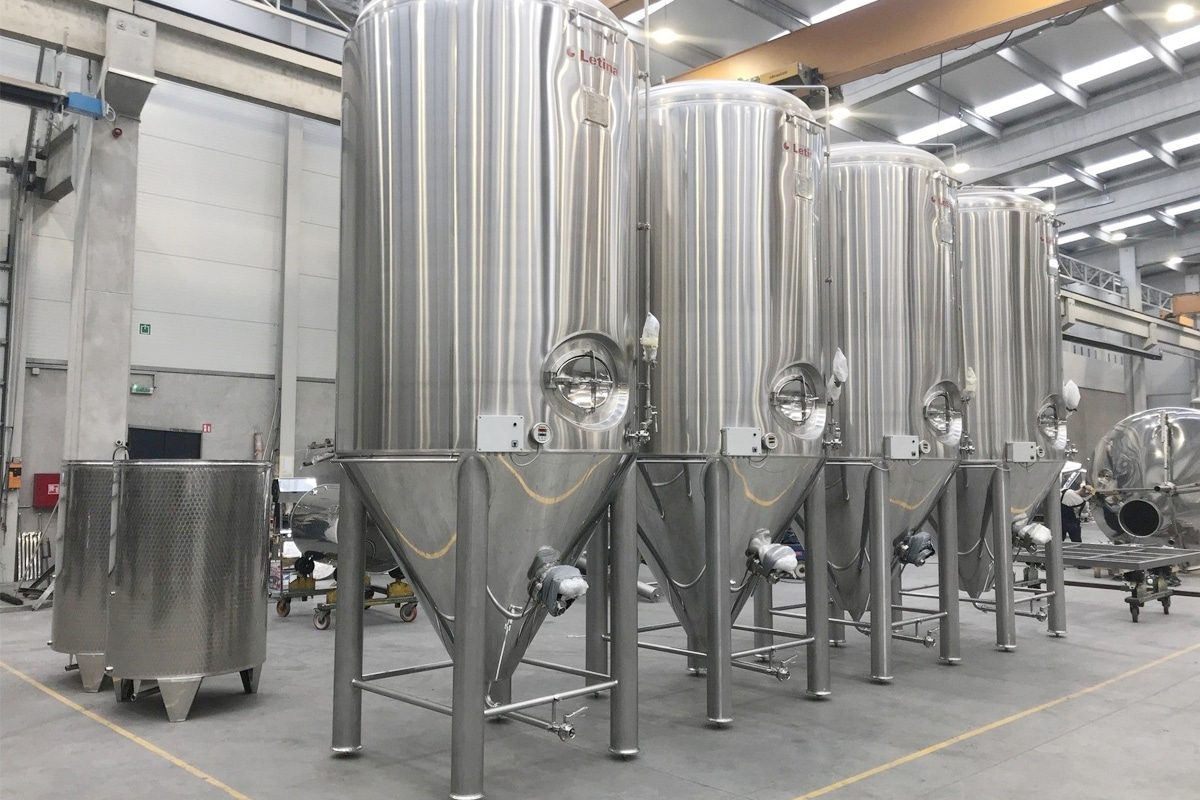
Summarize
In the maze of brewing decisions, the conical fermentation tank is both a beacon of innovation and a strategic investment. From precise yeast management to streamlined operations, the benefits paint a compelling picture for commercial brewers seeking excellence. However, as with any transformative tool, the decision to adopt a conical fermentation tank requires careful consideration.
During this exploration, we learned about its advantages and potential disadvantages, recognizing that the value of the container depends on the dynamics of the individual brewery. The temptation to improve quality, scalability, and efficiency is undeniable, but access to conical fermenters requires a balance between desire and pragmatism.
Ultimately, the decision comes down to a combination of the brewer’s vision, production scale and budget, and the capabilities of the fermentation tank. As the brewing industry continues to evolve, the conical fermentation tank becomes a testament to the ongoing pursuit of perfection. Whether it becomes an indispensable asset or a strategic choice, it’s the story of every brewer’s crafting as they navigate the intricacies of flavors and challenges in the brewing world.
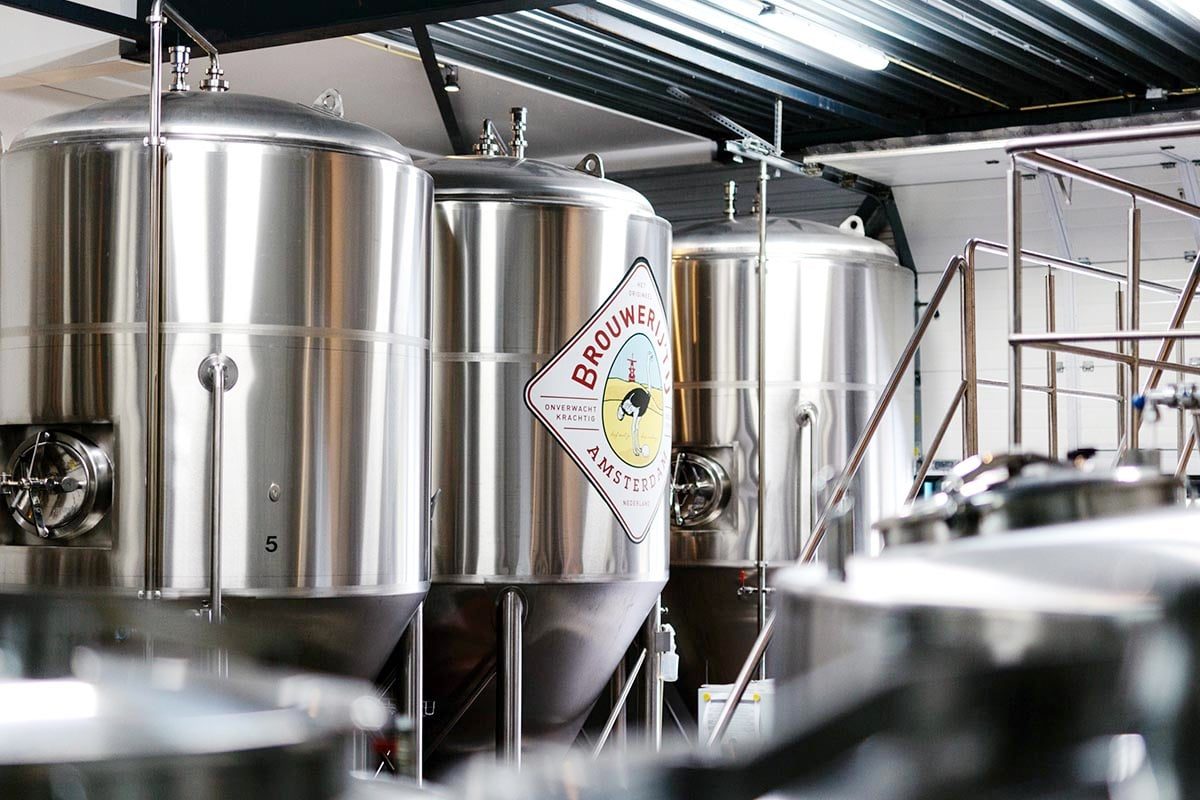
Get A Quote For Fermentation Tanks
ZYB Craft is a major supplier of fermentation tanks, offering a variety of designs to meet the unique needs of brewers. When you think about the importance of investing in a conical fermenter, ZYB Craft can guide you through the decision-making process. Our fermentation tanks are engineered to enhance yeast management, ensure precise temperature control, and simplify brewing operations. We understand the importance of this strategic investment, and our team is dedicated to providing personalized consultation to help you select the ideal fermenter for your brewing goals. Ask us and let us embark on a journey to enhance your winemaking career.