Main Body Warranty
Auxiliary Warranty
Equipment Type
Brewery Control System Components
Temperature Control
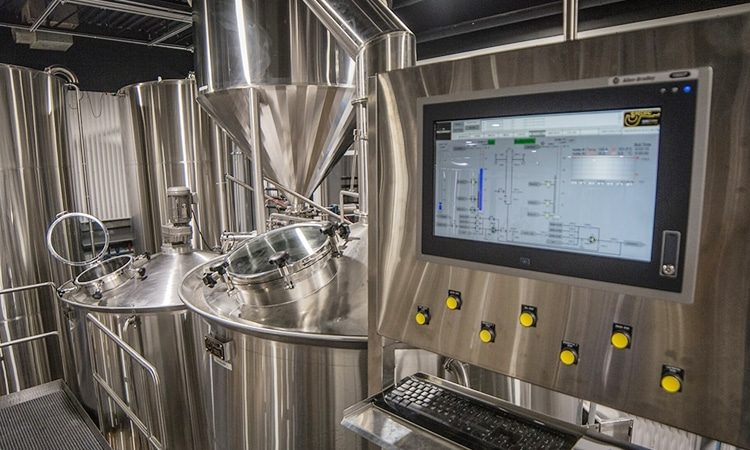
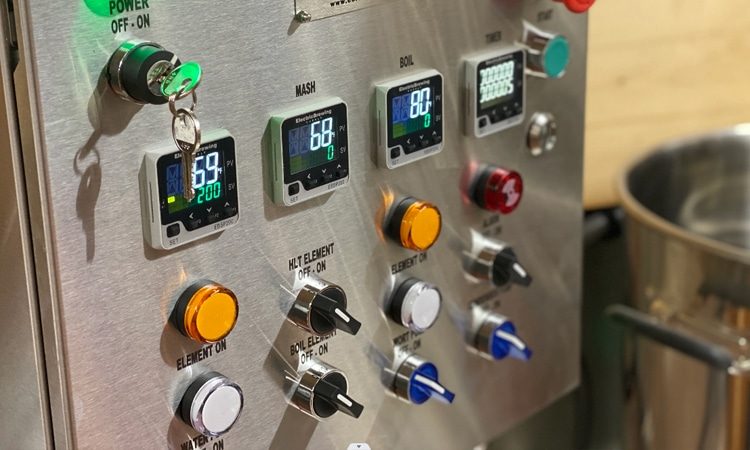
Flow Control
Pressure Control
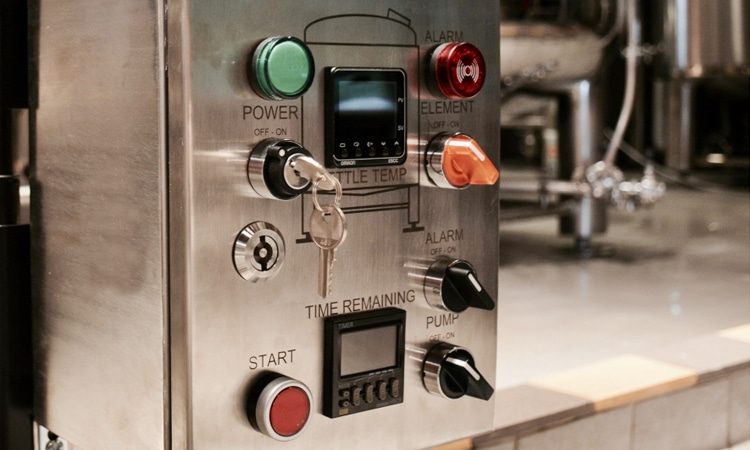
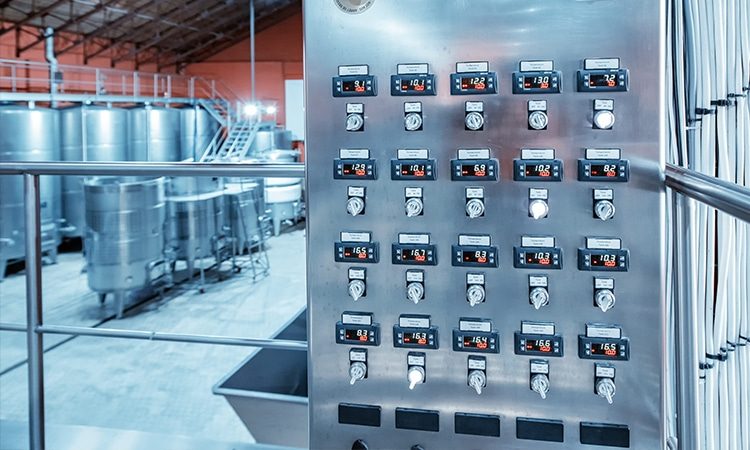
Automation
Advantages of Brewery Control System

Accuracy And Consistency
Get precise control of key parameters like temperature, pressure, and flow to ensure consistency in every batch you brew. With our brewery control systems, you can accurately replicate your recipes to produce a consistent product that meets customer expectations every time.

Improve Efficiency
Streamline your brewing process and reduce production time with automated controls and an intuitive interface. By automating repetitive tasks and optimizing workflows, our brewery control systems help you operate more efficiently, allowing you to focus on creativity and innovation in your brewing efforts.

Quality Assurance
Advanced monitoring and alarm features alert you to any deviations from set parameters, maintaining the quality and integrity of your beer. By proactively identifying and resolving issues in the brewing process, our control systems help you prevent quality defects and ensure every batch of beer meets your high standards.

Custom Made
Customize your brewery control system to meet the unique requirements of your brewery and brewing style. No matter what kind of beer you brew, our systems can be customized to meet your specific needs and preferences, ensuring a solution that's perfectly suited to your operation.

Data-Driven Decision-Making
Harness the power of data to optimize your brewing process and drive continuous improvement. Our systems feature comprehensive data logging capabilities that allow you to collect, analyze, and visualize brewing data, allowing you to fine-tune your recipes for better results.

Reliability And Support
Rely on ZYB Craft’s expertise and commitment to quality to deliver brewery control systems that operate reliably day after day. From initial consultation to installation and ongoing support, our dedicated team will help you every step of the way to ensure your brewery runs smoothly and efficiently.
Why Choose ZYB Craft
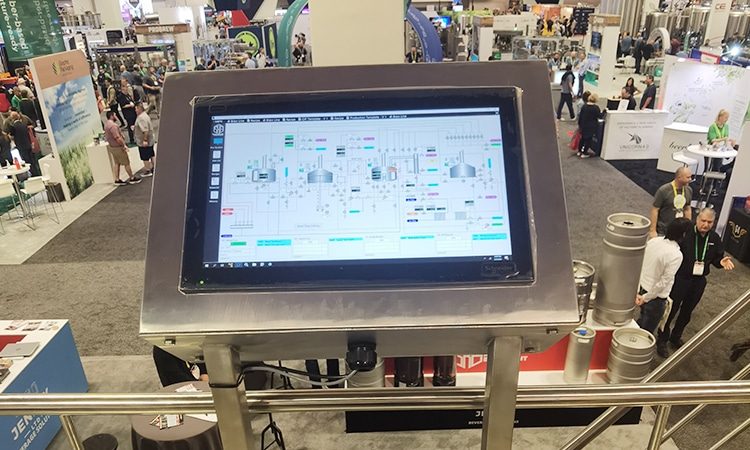
Expertise And Experience
Quality And Reliability
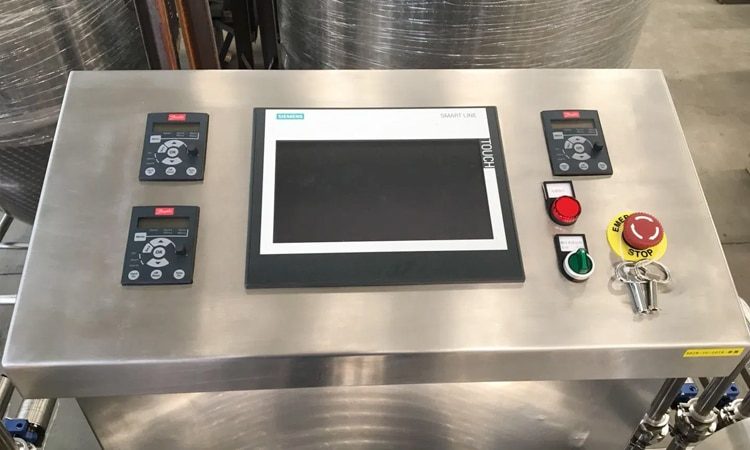
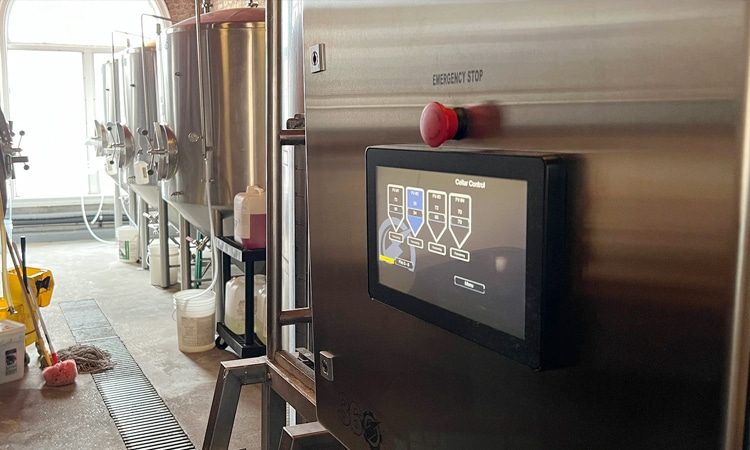
Comprehensive Support And Services
Customization And Flexibility
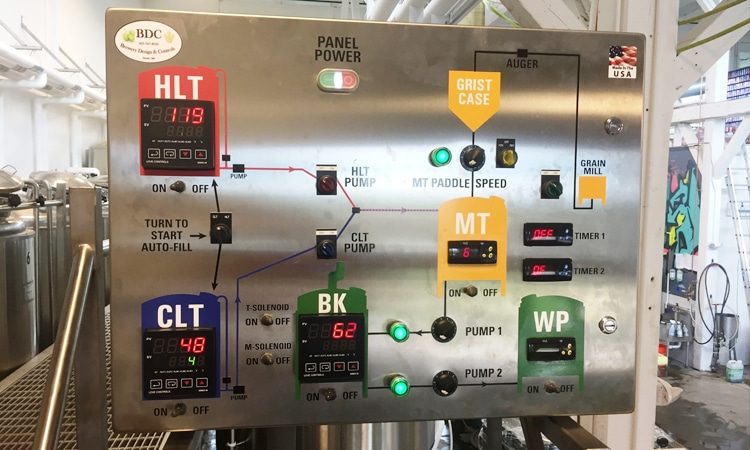
Get Brewery Control System Solutions
Frequently Asked Questions
Does The Brewery Control System Provide Real-Time Monitoring of Key Brewing Parameters?
Yes, many modern brewery control systems provide real-time monitoring of key brewing parameters. These control systems are designed to continuously monitor and display important variables in the brewing process. Here are some key brewing parameters that can be monitored in real-time:
- Temperature: The control system can monitor the temperature at each stage of the brewing process, including saccharification temperature, fermentation temperature, and tempering temperature.
- Pressure: The system can monitor the pressure within different vessels and piping systems (such as fermentation vessels or sake tanks) to ensure proper pressure levels and avoid any potential problems.
- Flow: Monitoring the flow of liquids such as wort or water helps maintain consistency and efficiency in the brewing process. The control system can display real-time flow for precise process control.
- pH: Monitoring pH is critical during certain brewing stages such as mashing or adjusting water chemistry. The control system provides real-time pH readings to ensure the desired pH range is maintained.
- Gravity: Gravity measurements such as specific gravity or Plato provide valuable information on the progress of fermentation and the alcohol content of beer. The control system can monitor and display real-time gravity readings.
- Dissolved Oxygen: Oxygen levels in beer can affect its flavor stability and shelf life. Some advanced brewery control systems can monitor dissolved oxygen levels in real-time to ensure proper oxygen management throughout the brewing process.
- Conductivity: Conductivity measurements can be used to monitor the concentration of certain ions or substances during brewing. For example, to monitor wort or beer clarity or to check specific salt concentrations.
- Timing And Sequencing: The control system tracks and displays the duration of each brewing step, ensuring correct timing and sequencing of the process. Real-time monitoring of time helps brewers maintain consistency and adhere to recipe specifications.
Real-time access to these parameters is invaluable for maintaining consistency, making timely adjustments, identifying deviations, and preventing potential problems in the brewing process. Data collected by the control system can be used for quality control, process optimization, and troubleshooting purposes, helping to improve the overall efficiency and quality of brewery operations.
Can The Brewery Control System Precisely Control The Timing And Sequence of The Different Brewing Steps?
Yes, brewery control systems are designed to precisely control the timing and sequence of the different brewing steps. The control system allows users to program and automate the brewing process, ensuring consistent and repeatable beer production. Here’s how brewery control systems can help in this regard:
- Recipe Management: Control systems often include recipe management functionality, allowing users to enter and store their brewing recipes. This includes specifying the timing and sequence of different brewing steps such as mash temperature and duration, hop addition, boil time, fermentation schedule, and conditioning time.
- Programmable Logic Controller (PLC): The control system is usually equipped with a PLC responsible for executing the programmed brewing steps according to the defined recipe. The PLC can precisely control the timing to ensure that each step starts and ends at the specified time.
- Automation And Integration: In advanced brewery control systems, automation and integration features allow seamless coordination between different components and systems. For example, the control system can automatically initiate the cooling process after boiling, transfer the wort to the fermentation vessel, and trigger the start of fermentation at the appropriate time and temperature.
- Sequencing And Interlocking: Control systems can enforce sequencing and interlocking, ensuring that certain steps or equipment operations do not occur until certain conditions are met. For example, the system can prevent the transfer of wort to the fermentation vessel until the boil is complete, or it can delay yeast dosing until the wort temperature reaches the desired level.
- Monitoring And Feedback: The control system continuously monitors the progress of each brewing step through sensors and feedback loops. This allows it to make real-time adjustments as needed, ensuring the timing and sequence of the brewing process remain on track and within desired parameters.
- Time-Based Alarms And Alarms: The control system can generate alarms or alerts based on predefined time thresholds to notify the user when a specific brewing step is complete or when the next step is to be started. This helps operators stay on track and adhere to brewing schedules.
By utilizing the capabilities of a brewery control system, breweries can precisely control the timing and sequence of the different brewing steps, ensuring consistent and reliable production of their desired beer recipe.
Can A Brewery Control System Track And Control The Flow of Ingredients During The Brewing Process?
Yes, a brewery control system can track and control the flow of ingredients during the brewing process. The control system precisely manages the flow of ingredients to ensure accurate and consistent addition of grain, hops, water, and other brewing ingredients. Here is how the brewery control system handles the raw material flow:
- Flow Sensors: The control system can be integrated with flow sensors installed in the piping system of the brewing equipment. These sensors measure the flow of liquids such as water, wort, and various solutions, as well as gases such as carbon dioxide.
- Flow Control Valve: The control system can control electric valves or solenoid valves that regulate the flow of ingredients. By adjusting the opening or closing of the valve, the system can control the rate at which ingredients are added to the brewing process.
- Recipe Management: The control system’s recipe management feature allows the user to enter the desired flow rate and when to add ingredients. This ensures an accurate and consistent flow of ingredients throughout the brewing process.
- Pump Control: Where a pump is used to transfer or circulate a liquid, a control system automates pump operation and controls flow. This allows precise control over the movement of ingredients through the brewing system.
- Automation And Precision: The control system is able to automatically control valves and pumps according to programmed recipes, ensuring a precise and consistent flow of ingredients throughout the brewing process. It minimizes human error and ensures accurate ingredient measurements, which contribute to the quality and consistency of the final product.
- Feedback And Correction: The flow sensor provides real-time feedback to the control system, allowing it to make adjustments during the brewing process and maintain the desired flow.
By tracking and controlling the flow of ingredients, brewery control systems help keep the brewing process consistent, accurate, and repeatable. It ensures that the right amount of ingredients are added at the right time, helping the resulting beer achieve the desired flavor profile and character.
Can The Brewery Control System Be Easily Expanded or Upgraded?
Yes, many brewery control systems are designed to be easily expanded or upgraded to accommodate changing brewery needs and technological advancements. Here are some considerations regarding the scalability and upgradeability of brewery control systems:
- Scalability: A good brewery control system is built with scalability in mind, allowing new equipment or processes to be added as the brewery expands. It should have the flexibility to integrate with additional tanks, pumps, valves, sensors, or other brewing equipment as needed.
- Modular Design: The control system adopts a modular design, which makes expansion and upgrades easier. Modular components can be added or replaced without disrupting the entire system. This allows incremental expansion of the system or incorporation of new functionality without extensive downtime or reconfiguration.
- Open Architecture: Control systems based on open architecture or industry standard protocols provide greater flexibility for expansion and integration. They can be easily connected with new or existing equipment, regardless of the manufacturer or technology used.
- Firmware And Software Updates: The control system shall have provisions for firmware and software updates. Regular updates from the manufacturer can add new features, enhance performance, and address any bugs or vulnerabilities. It would be beneficial if these updates could be easily installed without major disruption to brewery operations.
- Compatibility: A scalable control system should be compatible with a wide variety of equipment and peripherals commonly used in the brewing industry. This ensures that future additions or upgrades can be seamlessly integrated into existing systems without compatibility issues.
- Vendor Support: It is critical to select a control system from a reputable vendor that provides ongoing support and service. The supplier shall provide technical assistance, training, and consulting for system expansion or upgrade. They should also have a roadmap for future development, ensuring compatibility and continuity of the control system.
- Future-Proof: The well-designed control system takes into account future technological advances and trends in the brewing industry. It should adapt to emerging technologies or industry changes. Future-proofing ensures that the control system can be upgraded or integrated as new technologies emerge, allowing the brewery to remain competitive and keep up with the times.
It is important to consider these factors and discuss expansion and upgrade options with the control system supplier or manufacturer. They can provide guidance on system capabilities and limitations, and help determine the best way to meet the brewery’s changing needs.
Can Brewery Control Systems Be Accessed And Operated Remotely?
Yes, many brewery control systems offer remote access and operation capabilities, allowing breweries to monitor and control their brewing process from outside the brewery. Remote access brings benefits such as increased flexibility, convenience, and the ability to respond to issues or make adjustments while away from the brewery. Here’s how a brewery control system facilitates remote access:
- Network Connectivity: Brewery control systems are often connected to a local network or the Internet, allowing remote access. This connection can be established via a wired Ethernet connection, Wi-Fi, or cellular network, depending on the capabilities of the system and the brewery’s infrastructure.
- Secure Remote Access: Security is paramount when accessing control systems remotely. Control systems should employ security protocols, such as encrypted connections and user authentication, to prevent unauthorized access and ensure data confidentiality.
- Remote Monitoring: Remote access allows brewers to monitor the brewing process and key parameters from anywhere with an internet connection. They can view real-time data, check system status, and receive alerts or notifications if any parameter is out of range.
- Remote Control: Depending on the capabilities of the control system, the brewer may be able to remotely control various aspects of the brewing process. This can include adjusting set points, modifying recipe parameters, or activating/deactivating specific equipment.
- Alert Management: Remote Access enables brewers to receive and manage alerts remotely. If any serious situation or issue arises, they can be immediately notified and take appropriate action even if they are not on site.
- Flexibility And Convenience: Remote access offers greater flexibility and convenience to brewery owners and operators. Even when they are not at the brewery, they can monitor operations and respond to issues, making it easier to manage multiple locations or conduct off-site monitoring.
- Data Logging And Analysis: Remote access allows brewers to access historical data recorded by the control system. This data can be used for analysis, process optimization, and quality control purposes. Brewers can view and analyze brewing performance data remotely without having to physically access the control system.
- Troubleshooting And Support: Remote access enables technical support personnel or equipment vendors to remotely diagnose problems, provide troubleshooting instructions, and even perform software updates or maintenance tasks on the control system.
It is worth noting that the remote access capabilities of different brewery control systems may vary. Some systems may offer more advanced remote functionality, while others may have more limited functionality. Brewers should consult with the control system supplier or manufacturer to understand the specific remote access capabilities of the system they are considering and ensure that it meets their needs and requirements. Additionally, brewers should consider implementing appropriate security measures to protect remote access and protect against potential cyber threats.
Is The Brewery Control System Compatible With Various Brewing Styles And Techniques?
Yes, well-designed brewery control systems are usually compatible with a variety of brewing styles and techniques. Brewery control systems are designed to provide flexibility and adaptability to accommodate different brewing processes and recipes. Here’s how they support compatibility with various brewing styles and techniques:
- Recipe Management: Brewery control systems often include recipe management functionality that allows users to enter and store their brewing recipes. These recipes can be customized to suit different brewing styles, including traditional styles, modern craft beer styles, or experimental recipes. The control system can store and recall specific parameters and steps for each recipe, ensuring consistency and repeatability.
- Programmable Logic Controller (PLC): The PLC controlling the system can be programmed to perform the specific steps and actions required by different brewing techniques. Whether it is traditional brew mash, step mash, decoction mash, or alternative brewing methods such as acidification or barrel aging, the control system can be configured to control and monitor the process accordingly.
- Temperature And Time Control: The Brew Control System provides precise temperature control capability, which is critical for a variety of brewing styles. They allow the user to set and maintain specific temperatures for mashing, boiling, fermenting, and conditioning. In addition, the control system can control the duration of the different brewing steps, ensuring the precise timing of each style.
- Sensor Integration: The control system can be integrated with various sensors placed throughout the brewing facility to monitor and control key parameters. This includes temperature sensors, pressure sensors, pH sensors, and more. The ability to monitor and control these parameters is critical to achieving the specific flavor profiles and characteristics associated with different brewing styles.
- Customization And Flexibility: Well-designed control systems provide customization options to suit specific brewing techniques. It can allow users to configure specific processes such as step-by-step mash programs, hop additions, or special fermentation profiles. This flexibility allows brewers to experiment with different techniques and refine their brewing process.
- Data Logging And Analysis: Control systems often provide data logging and analysis capabilities, allowing brewers to examine and analyze brewing data. This capability is useful for evaluating the performance of different brewing styles and techniques, identifying trends, and making informed decisions for process optimization and recipe improvement.
Brewery control systems support compatibility with a variety of brewing styles and techniques by providing the necessary flexibility, customization options, and control over key brewing parameters. Whether brewing traditional styles, innovative craft beers, or experimenting with unique techniques, brewers can adapt the control system to their specific brewing process and achieve the desired results.