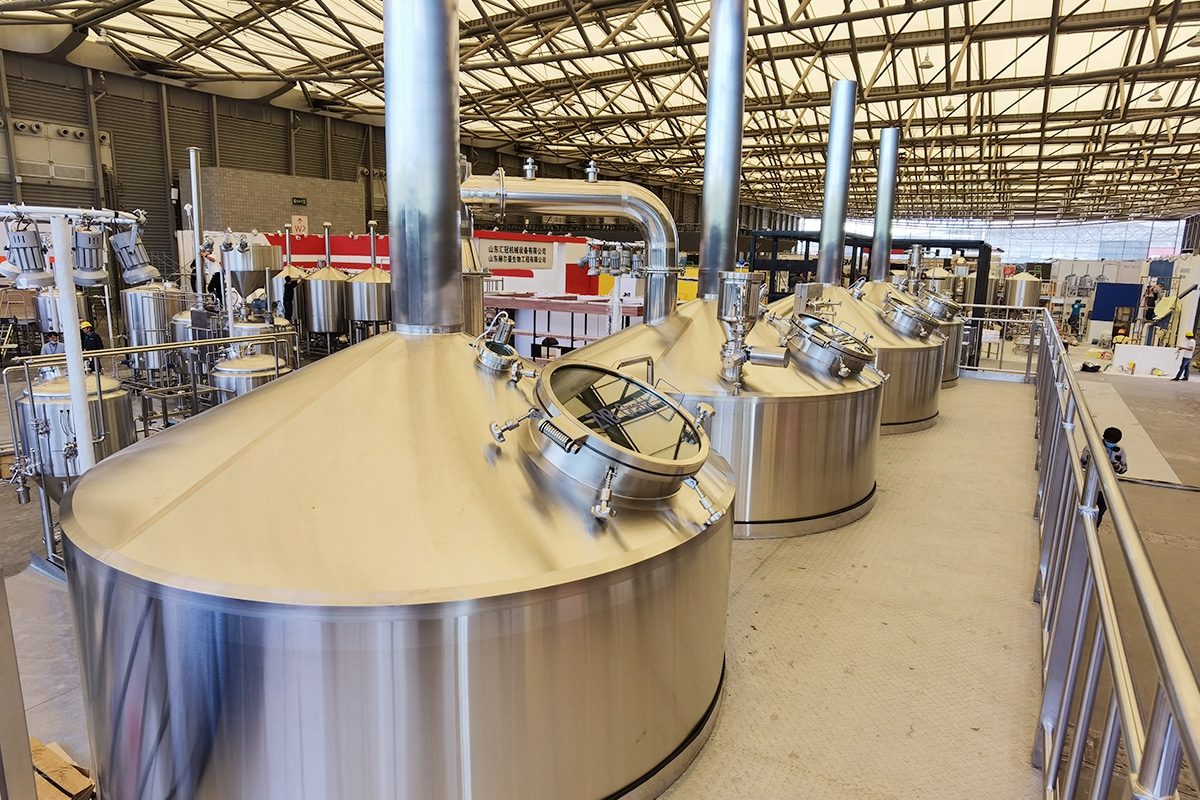
Brewhouse Heating Options: Electric VS Steam VS Direct Fire
In the fascinating world of brewing, alchemy meets art, and every decision shapes a symphony of flavors dancing in the pint. Among these key choices, the choice of the brewhouse’s heating method guides the harmony of malt, hops, and water into the perfect beer. In this exploration, we get to the heart of brewhouse heating, revealing the nuances of three different methods: electricity, steam, and direct fire.
The essence of a good beer lies not only in its ingredients but also in the careful management of heat during the brewing process. Electric heating, steam systems, and traditional direct fire all have a unique appeal, guaranteeing brewers precision, uniformity, or a nostalgic connection to brewing tradition. But this decision goes beyond technical details and is a harmonious interplay of science, tradition, and art.
This article serves as a compass to help you navigate the maze of choices, illustrating the complexities of electric, steam, and direct-fire heating methods. We’ll break down the pros, cons, and practical applications of each heating method so brewers can make informed decisions. These decisions will resonate not only with their brewing goals but with the soul of their craft.
Complete Guide
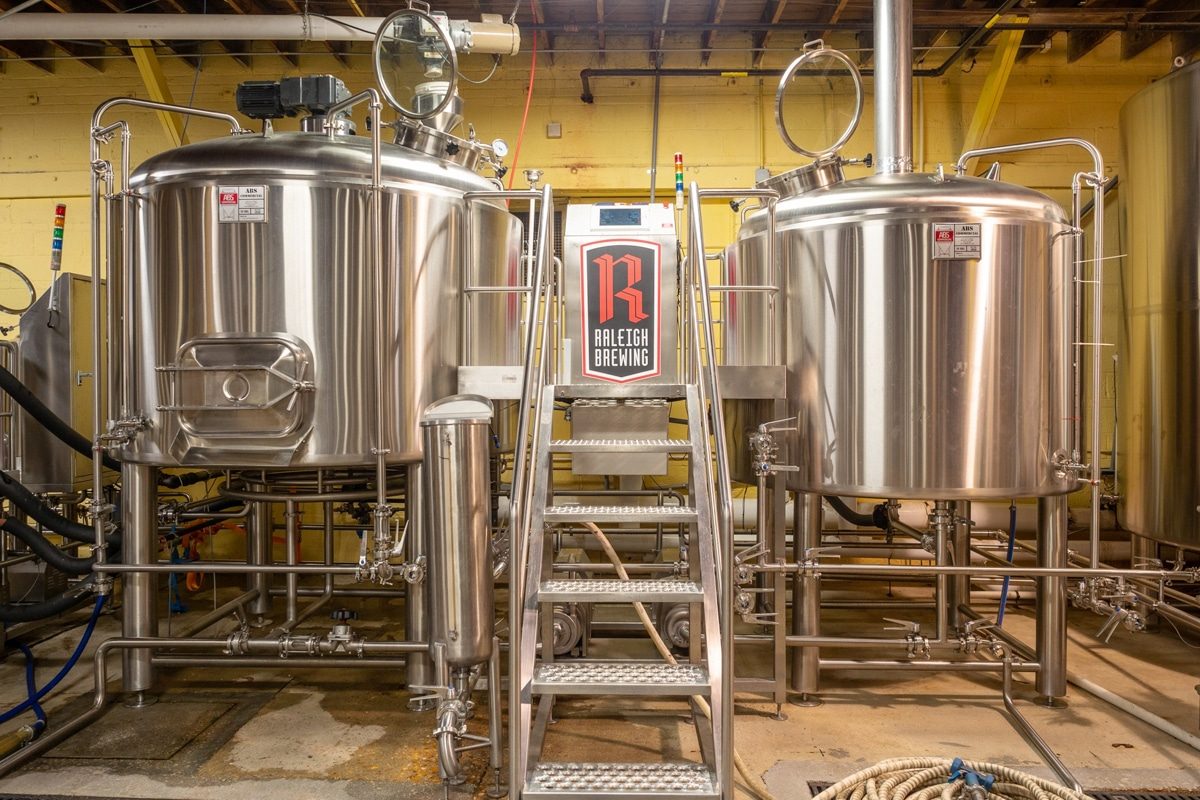
The Importance of Heating Systems
The choice of a brewhouse heating system is a fundamental cornerstone that shapes the entire brewing process, having a profound impact on the technical trajectory and sensory results of craft beer.
Impact on The Brewing Process
The type of heating system deployed determines the nature of the brew, determining how quickly and precisely each stage unfolds. Electricity, steam, and direct fire each bring a unique rhythm to the process, affecting everything from the mouthfeel to the clarity of the final product.
Temperature Accuracy And Control
The choice of heating system affects every stage of the brewing process, from mashing to boiling and fermentation. The precision and control these systems provide determine enzyme activation, sugar extraction, and flavor development.
Duration And Efficiency
The efficiency and speed with which target temperatures are reached significantly affect brewing time. The heating system affects the duration of the process, the extraction of flavor, aroma, and the overall character of the beer.
Impact on Beer Quality
The quality of beer is a combination of many factors, and the heating system plays a key role in shaping its sensory characteristics. The heating system is a master of directing chemical reactions, resulting in different beer aromas, flavor profiles, and overall sensory experience.
Consistency And Uniformity
The heating method chosen affects the consistency and evenness of heat distribution within the brewing vessel. Uniform heating ensures even flavor extraction and avoids local hot spots, improving beer quality.
Flavor Development And Complexity
The type of heating used can subtly or overtly affect the flavor profile of the final product. Precise temperature control and efficient heat distribution play a key role in creating subtle flavor and aromatic complexity in beer.
As we wade into the realm of electric, steam, and direct-fire heating options, it becomes clear that the importance of these systems goes beyond technical details. In the following sections, we’ll unveil the intricacies of each heating method, examining how they impact the brewing process and help define the unparalleled qualities of great beer.
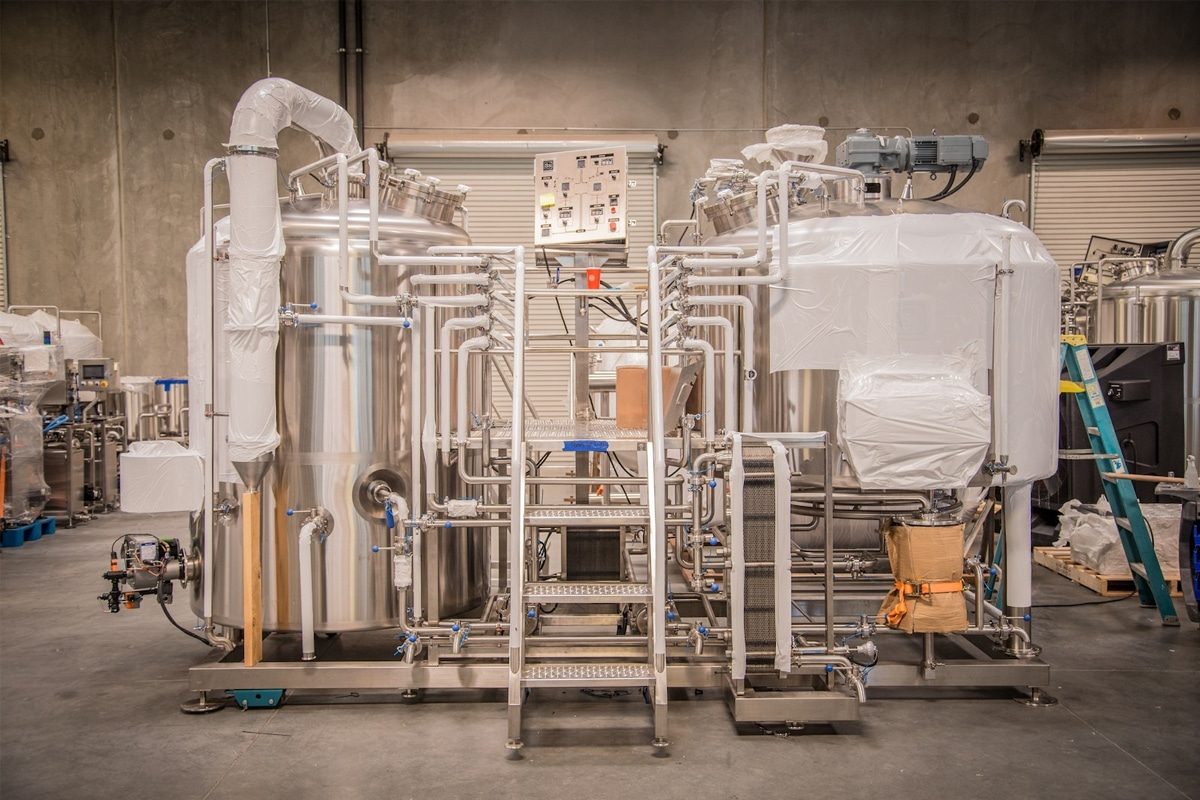
Electric Heating System
Overview
Electric heating systems are the brewhouse’s master craftsmanship. This method utilizes electronic components strategically placed within the brewing vessel to ensure meticulous control of temperature regulation throughout the brewing process. The fine precision of electric heating systems allows brewers to fine-tune temperatures at every brewing stage, from mashing to boiling and fermentation.
Advantages
- Precise Temperature Control: The power system is known for its ability to maintain sharp temperature control, a key factor affecting enzyme activity during mashing and achieving the boiling point required for hop utilization. This precision extends to fermentation, allowing brewers to have meticulous control over yeast activity.
- Energy Efficiency: Electrical systems are known for their efficiency, which often translates into lower energy consumption compared to some direct-fired alternatives. Brewers benefit from reduced utility costs and a greener footprint, in line with the growing focus on sustainable brewing practices.
- Cleanliness And Controllability: Electric heating is a clean process, with no open flames or waste gases produced. Brewers like the ease of control and lack of potential dangers associated with open flames, creating a safer, more controlled brewing environment.
Disadvantages
- High Initial Cost: The upfront investment in an electric heating system can be significant, especially for larger units. Specialty equipment such as heating elements and control panels can result in higher initial installation costs. This cost factor can present an obstacle for small breweries on a tight budget.
- Capacity Limitations: While electrical systems are ideal for small and medium-sized breweries, they may be less efficient for larger operations that handle high-volume production. Scaling up may require significant investments in additional power infrastructure.
- Maintenance Requirements: Although generally easier to maintain than other systems, electric heating does require regular attention to ensure optimal performance. Components may degrade over time, requiring replacement and occasional system inspections, which adds operational considerations.
Practical Application
Electric heating systems are favored by a range of beer businesses, from boutique craft breweries to innovative home breweries. Breweries such as Otway Brewing have successfully implemented electrical systems, touting the advantages of precise temperature control and the ease of adapting the method to small-scale operations. These real-world applications demonstrate the versatility of electric heating, proving its effectiveness in a variety of brewing environments. As we further explore brewhouse heating options, the electric system demonstrates the seamless integration of innovation with the age-old craft of brewing.
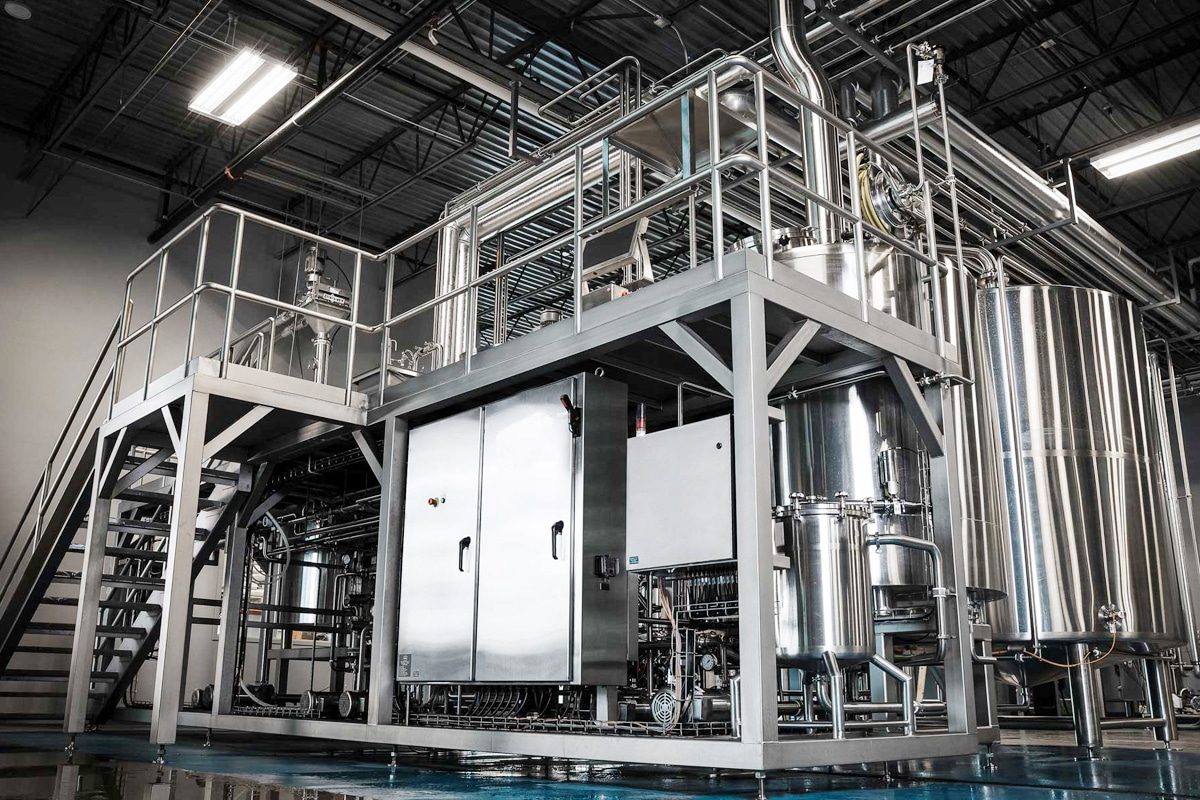
Steam Heating System
Overview
The steam heating system embodies the brewery’s combination of tradition and efficiency. This method uses steam as a heat conductor, allowing it to circulate within the brewhouse vessel to create an evenly warm environment. Known for its versatility and scalability, steam heating is the cornerstone of many commercial breweries.
Advantage
- Superior Heat Distribution: Steam’s ability to distribute heat within the brewing vessel minimizes temperature variations, eliminating hot spots and ensuring even temperature distribution during mashing, boiling, and fermentation. This consistency helps improve the overall quality and repeatability of your beer.
- Scalability: A defining feature of a steam system is its scalability. Whether in a small craft brewery or a large production facility, steam heating can be seamlessly adapted to handle varying quantities of beer. Its adaptability makes it a top choice for breweries experiencing growth and expansion.
- Energy Efficiency: Steam is known for its energy efficiency and is a cost-effective option, especially in large breweries. Its efficient heat transfer and ability to reuse condensed steam help reduce operating costs and reduce environmental footprint.
Disadvantages
- Complex Installation: The implementation of a steam heating system involves a more complex installation process than some other options. This complexity results from the need for steam boilers, extensive piping, and ancillary infrastructure, and results in higher upfront costs.
- Maintenance Costs: While reliable, steam systems require regular maintenance to keep them operating at peak efficiency. This includes boiler repairs, pipe inspections, and prompt resolution of potential issues. Maintenance costs can be high, especially for larger setups.
- Operational Expertise: Operating a steam system requires a certain level of expertise. Breweries require trained personnel to effectively manage and troubleshoot systems, which adds to the complexity of personnel requirements and may require specialized training.
Practical Application
Breweries like Backstory Brewery have seamlessly integrated steam heating into their operations, emphasizing the benefits of even heat distribution, scalability, and energy efficiency. These real-world applications highlight how steam systems are integral to the success of large breweries, playing a key role in ensuring consistent quality and efficient production. The advent of steam heating systems is a testament to the fusion of traditional methods with modern brewing practices, shaping the art of brewing on a massive scale.
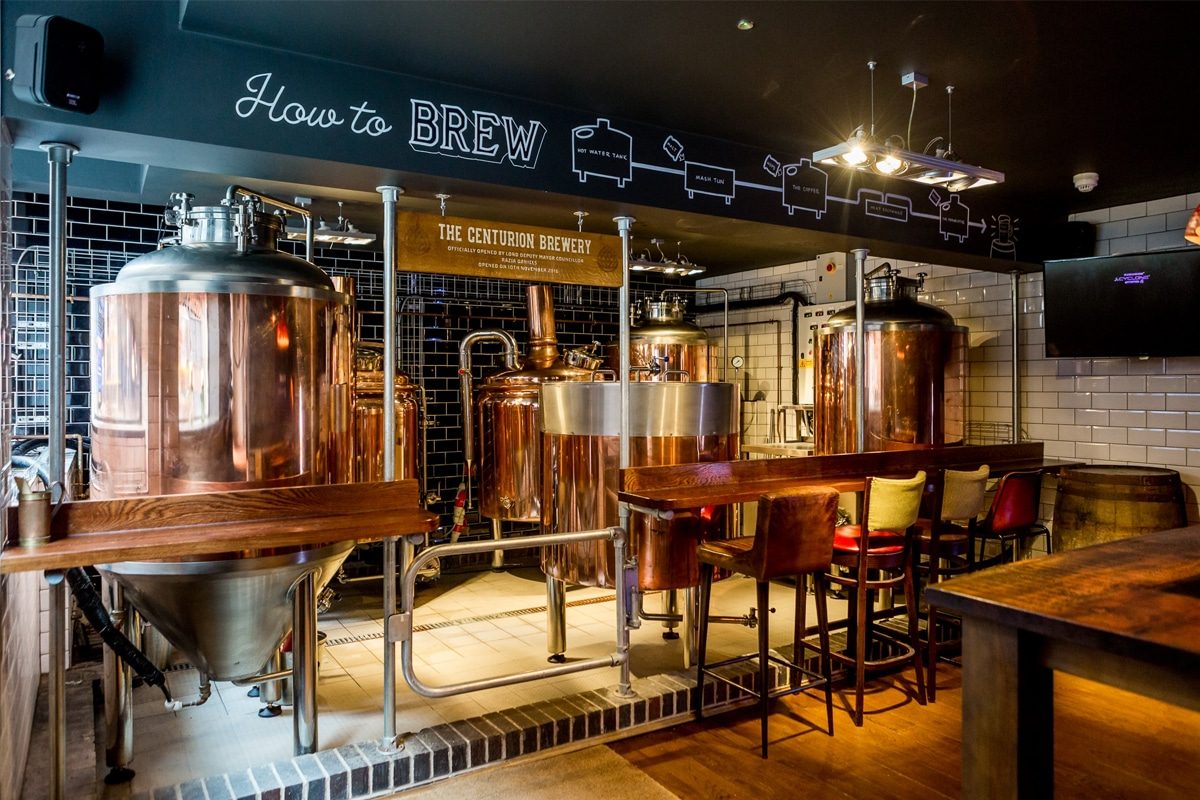
Direct Fire Heating System
Overview
The direct-fire heating system evokes the original essence of brewing, using an open flame beneath the brewing kettle to generate heat that transforms ingredients into liquid gold. This approach is rooted in historical practice, bringing a raw and elemental side to the brewery, and evoking a connection to the ancient art of craft beer.
Advantages
- Cost-Effectiveness: Direct-fired heating systems are often favored for their cost-effectiveness, often having a lower initial installation cost compared to some other heating methods. This cost-efficiency makes it an attractive option for small breweries on a budget.
- Setup Flexibility: The simplicity of a direct-fired system allows for greater flexibility in brewhouse design and layout. This adaptability gives brewers the freedom to configure the setup to their liking and is especially beneficial for breweries with unique space constraints or looking for a more customizable setup.
- Aesthetics And Tradition: In addition to functionality, direct-fire heating systems add an aesthetic dimension to the brewing experience. The visual spectacle of an open fire beneath the kettle not only recalls brewing tradition but also sets the ambiance of the brewery.
Disadvantages
- Limited Temperature Control: Direct-fire heating methods may provide less precise temperature control than electric and steam systems. The nature of the open flame can cause temperature fluctuations that may affect the consistency of the brew, and a high level of vigilance is required during the process.
- Energy Inefficiency: In some cases, direct-fired heating systems may be less energy efficient than electric or steam alternatives. The process of heating directly under the kettle may result in some heat loss, which may impact operating costs over time.
- Safety Issues: Open flames can pose some safety issues. Proper ventilation and safety measures can help mitigate the risks associated with using open flames in a brewing environment.
Practical Application
Breweries like Lost Rhino Brewery have demonstrated successful integration of direct-fire heating systems into their brewing processes. Their choices reflect an appreciation for cost-effectiveness and the unique aesthetic appeal this approach brings to craftsmanship. Direct-fire heating pays homage to the origins of brewing, embodying simplicity, flexibility, and a connection to tradition. Although less common in large-scale operations, direct-fire heating systems are still popular with craft brewers who want to inject a touch of elemental magic into their products.
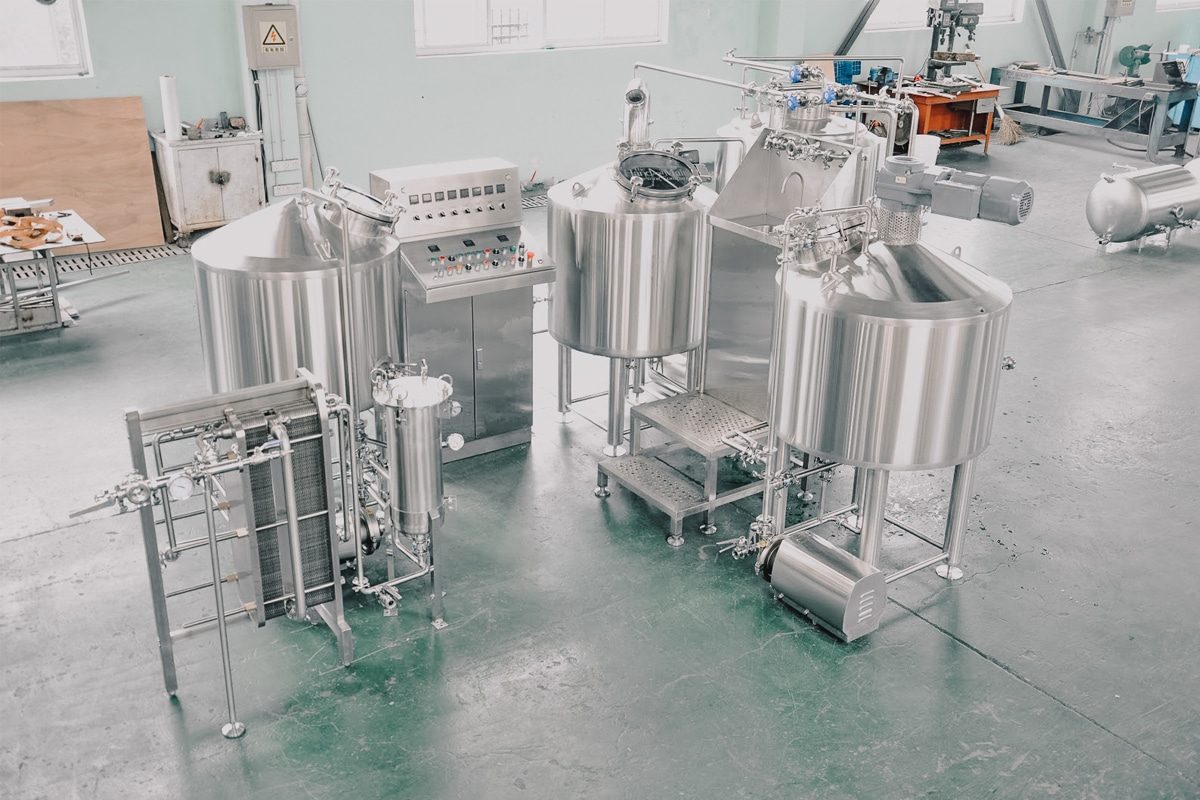
Comparative Analysis: Electricity, Steam, Direct Fire
Understanding the diversity of brewery heating options requires a thorough understanding of the relative advantages and disadvantages inherent in electric, steam, and direct-fired systems. Each method brings unique qualities to the brewing process, and a comprehensive analysis can guide brewers in choosing the option that best suits their specific needs.
Precision And Control
Advantages of Electric Heating
- Unparalleled precision and temperature setting control.
- Ideal for brewing recipes that require specific temperature profiles during mashing, boiling, and fermentation.
Precautions For Electric Heating
- Ideal for brewers who prioritize tight control of specific flavor profiles.
- High controllability may result in higher initial costs, especially for larger brewing capacities.
Advantages of Steam Heating
- Even heat distribution ensures a consistent temperature throughout the brewing vessel.
- Suitable for complex mashing programs and recipes that require precise control.
- Ideal for large-scale operations due to scalability and consistent performance.
Precautions For Steam Heating
- Ideal for those looking for a balance between precision and traditional brewing methods.
- Requires complex installation and additional infrastructure such as steam boilers and extensive piping.
- Maintenance requirements and repair costs may be higher than other methods.
- Expertise in steam system management is required.
Advantages of Direct Fire Heating
- The setup is simple and flexible, enabling a variety of brewhouse designs.
- Attractive to small breweries due to lower initial installation costs.
- Perfect for brewers who prefer the hands-on approach of traditional open-fire brewing.
Precautions For Direct Fire Heating
- Temperature control accuracy is lower compared to electric and steam methods.
- Safety concerns and potential energy inefficiencies due to heat loss.
- Offers flexibility, but may require extra vigilance to maintain consistent temperatures.
Energy Efficiency
Advantages of Electric Heating
- Often considered more energy efficient than direct combustion, resulting in possible long-term cost savings.
- Perfect for the environmentally conscious brewer.
- Suitable for small brewhouses with moderate energy requirements.
Precautions For Electric Heating
- Initial installation costs may be higher but are offset by energy savings over time.
- Ideal for those looking to minimize energy consumption without compromising performance.
Advantages of Steam Heating
- Known for its energy efficiency, especially in large setups, it helps reduce operating costs.
Precautions For Steam Heating
- Ideal for breweries focused on sustainability and scalability.
- Complex installations may incur higher upfront costs.
- Maintenance and occasional repairs can impact overall cost-effectiveness.
Advantages of Direct Fire
- Cost-effective heating method, especially for small breweries.
- A simplified setup may reduce initial costs.
Precautions For Direct Fire
- Energy efficiency may be lower due to potential heat losses during direct heating.
- Ideal for those who prioritize simplicity and cost-effectiveness over energy efficiency.
- Initial installation costs are relatively low but may impact long-term expenses.
Installation And Infrastructure
Advantages of Electric Heating
- Easier installation and fewer infrastructure requirements.
- Ideal for small breweries or breweries with limited space.
- Maintenance costs are generally lower compared to other heating systems.
Precautions For Electric Heating
- Capacity limitations may exist for large operations.
Advantages of Steam Heating
- Ideal for larger breweries capable of more complex setups.
- Efficient heat distribution minimizes the risk of hot spots.
Precautions For Steam Heating
- Involves a more complex installation process requiring steam boilers, extensive piping, and additional infrastructure.
- Regular maintenance is required for optimal performance.
Advantages of Direct Fire Heating
- Easier to install than steam and is often preferred for its flexibility.
- Ideal for breweries looking for a simple setup without extensive infrastructure.
Precautions For Direct Fire Heating
- Direct fire heating can cause some safety issues.
- Proper ventilation and safety measures are required to mitigate the risks of using open flames in brewing environments.
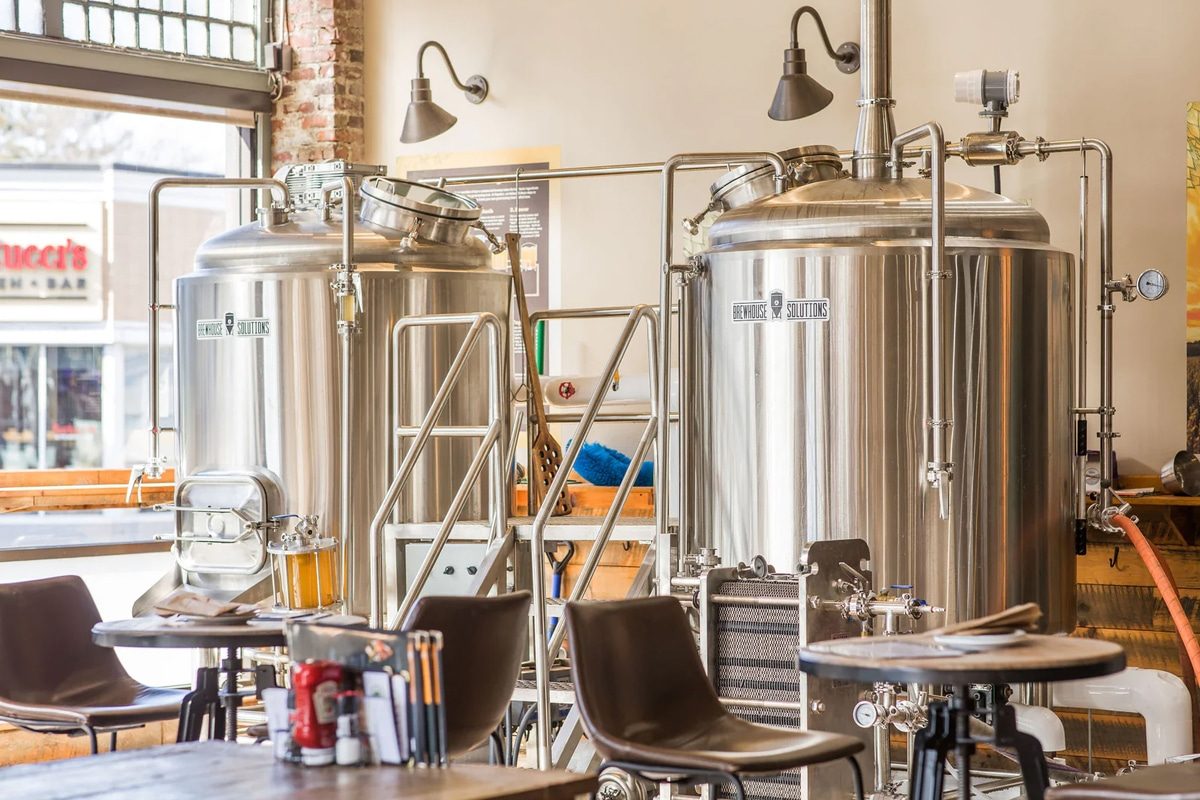
Factors Affecting The Choice of Heating Method
The choice of a brewery heating method is a multifaceted decision influenced by a variety of factors that combine to impact the brewing experience and the quality of the final product. Understanding these factors can help brewers seek the best heating solution for their specific brewing wishes and operational requirements.
Brewery Size And Scale
- Small Breweries: For small breweries, cost-effectiveness and simplicity of setup may prioritize options like electric or direct-fired systems.
- Medium To Large Breweries: Scalability becomes critical and it may be advantageous to have a steam system that can handle larger volumes efficiently.
Brewing Style And Recipe Complexity
- Temperature Control Precision: Brewing methods that require precise temperature management, complex mashing schemes, or specific boiling characteristics may favor electric or steam systems.
- Traditional or Experimental Brewing: Brewers who follow traditional methods or want to get their hands dirty may choose a direct-fire system for its rustic charm.
Budget And Operating Costs
- Initial Investment: Power systems may require a higher initial investment, while direct fire may be more cost-effective for smaller setups.
- Long-Term Operating Costs: Over time, efficiency and energy costs can impact operating budgets in favor of more energy-efficient systems such as electric or steam.
Maintenance And Expertise
- Maintenance Requirements: Direct-fired systems generally have lower maintenance requirements than steam systems, which may require specialized expertise.
- Access to Expertise: Availability of technical personnel or willingness to invest in training may influence the selection of systems that require specific operating expertise.
Brewing Philosophy And Aesthetics
- Aesthetic Appeal: The desire for a traditional, visually appealing brewing process may prompt brewers to turn to direct-fire heating, despite its limitations in control.
- Focus on Innovation: Breweries that emphasize innovation, precision, and a clean brewing environment may choose an electric system.
Compliance And Security
- Safety Measures: It is crucial to comply with safety regulations and implement necessary safety measures, especially for systems involving open flames or steam.
- Environmental Impact: Consideration of environmental regulations and sustainable practices may favor more energy-efficient options, such as electric or steam systems.
The choice of a brewery heating method is a delicate interplay between technical requirements, operational needs, brewing philosophy, and financial considerations. From the size of the brewery to the desired brewing aesthetics and regulatory compliance, every factor plays an important role in determining the most appropriate heating system. Understanding these influences allows brewers to make informed decisions that are consistent with their unique brewing vision, ensuring that each batch of beer reflects not only craftsmanship but also a harmonious blend of technology and tradition.
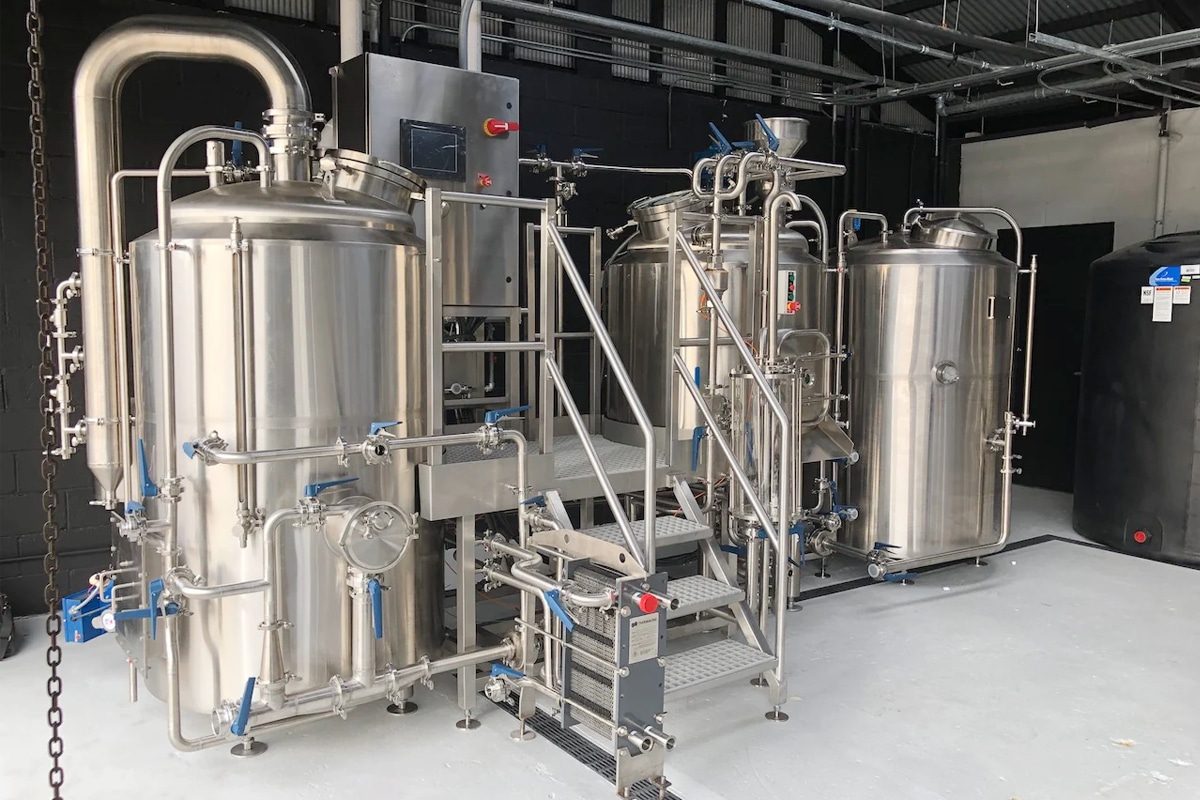
Summary
In the symphony of brewhouse heating options, the choice between electric, Steam, and direct fire emerges as a nuanced decision that encapsulates the essence of brewing craftsmanship. Each method weaves its unique narrative, shaping the flavor, aroma, and soul of the final brew. As we conclude this exploration, it becomes clear that the decision isn’t merely about heating vessels, it’s an orchestration of tradition, technology, and the brewmaster’s distinct vision.
In this symphony of choices, there is no one-size-fits-all solution. Instead, the brewmaster is an artist, blending the technicalities of heating methods with the canvas of their creativity. As the flames flicker, the steam rises, and the elements hum, the brewhouse becomes a crucible where the brewer’s passion is transmuted into every drop that fills the glass.
So, whether the path leads to the precision of electricity, the embrace of steam, or the elemental dance of direct fire, the journey is one of discovery, innovation, and the timeless pursuit of crafting the perfect brew. In the world of brewhouse heating, each method is a note in the grand symphony of beer, an ode to the art, the science, and the relentless pursuit of brewing perfection. Cheers to the choices, the craft, and the soulful symphony of brewing!
- Electric heating, with its precision and control, emerges as the maestro of temperature management, ideal for brewers seeking a harmonious blend of science and art. Yet, its upfront investment and potential limitations in larger operations necessitate careful consideration.
- Steam heating, a historical luminary, embraces efficiency and scalability, casting a timeless allure. Its heat distribution and energy efficiency make it the choice for those scaling up their brewing ambitions, even with the complex choreography of installation and maintenance.
- Direct Fire, the primal dancer with open flames, beckons to those who cherish tradition, simplicity, and a hands-on brewing experience. Cost-effective and flexible, it reverberates with the echoes of ancient brewing practices, though not without considerations of safety and limited temperature control.
In this symphony of choices, there is no one-size-fits-all solution. Instead, the brewmaster is an artist, blending the technicalities of heating methods with the canvas of their creativity. As the flames flicker, the steam rises, and the elements hum, the brewhouse becomes a crucible where the brewer’s passion is transmuted into every drop that fills the glass.
So, whether the path leads to the precision of electricity, the embrace of steam, or the elemental dance of direct fire, the journey is one of discovery, innovation, and the timeless pursuit of crafting the perfect brew. In the world of brewhouse heating, each method is a note in the grand symphony of beer, an ode to the art, the science, and the relentless pursuit of brewing perfection. Cheers to the choices, the craft, and the soulful symphony of brewing!
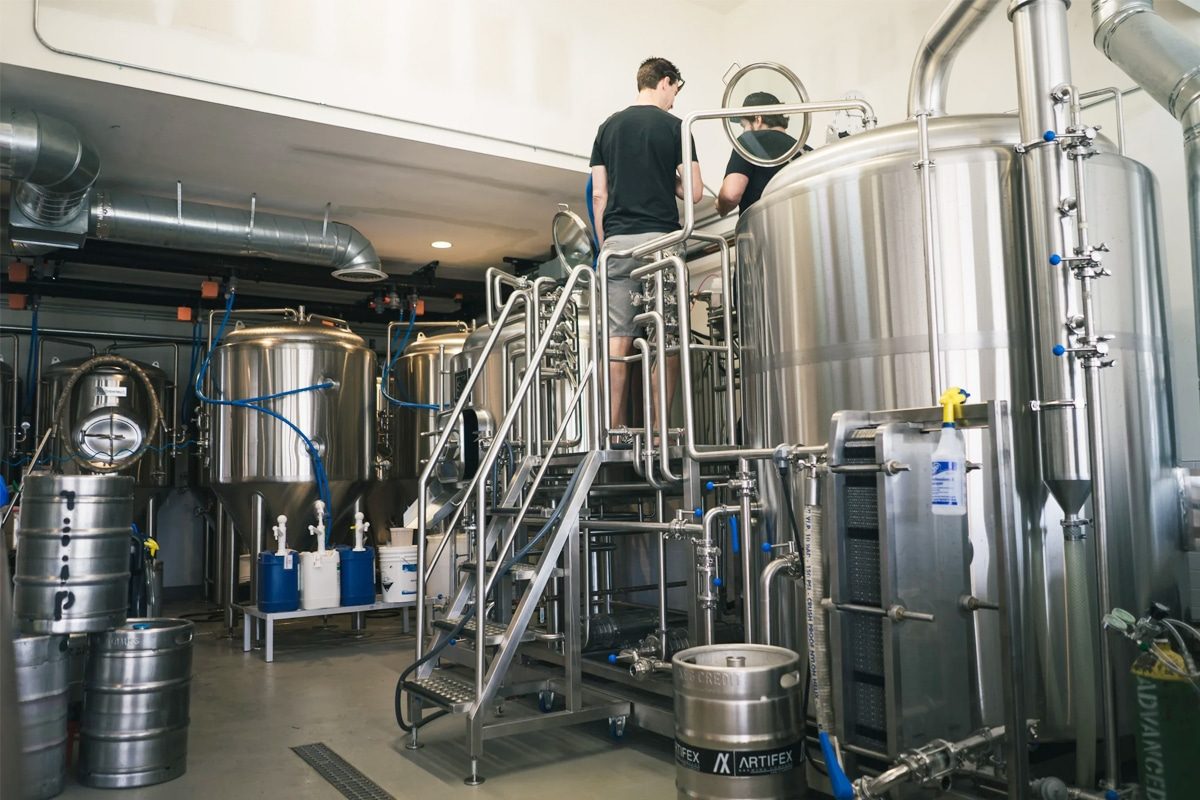
Personalized Brewhouse Turnkey Solution
In the intricate world of brewing, where every detail shapes the soul of your craft, the choice of a brewhouse heating solution is a pivotal decision. Enter ZYB Craft, your trusted partner in transforming brewing visions into reality through personalized turnkey solutions. Whether you lean towards the precision of Electric, the versatility of Steam, or the timeless appeal of Direct Fire, ZYB Craft specializes in curating turnkey solutions that align seamlessly with your brewing identity. Consult us now for a personalized brewhouse turnkey solution.