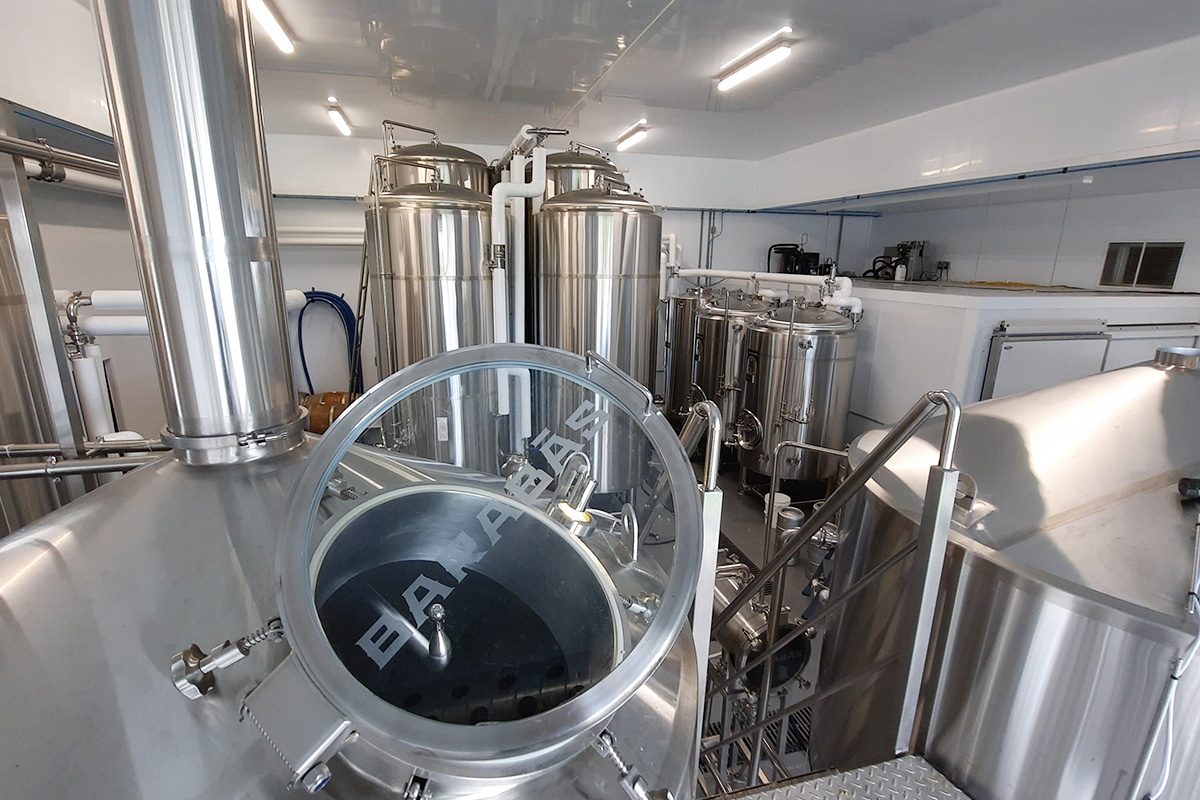
Brewhouse Buying and Maintaining Guide
Brewing beer is a timeless craft that combines science, art, and passion. At the heart of every brewery is the brewhouse, a carefully designed system made up of basic components such as mash tun, lauter tun, kettle tun, and whirlpool tun. These vessels work in harmony to transform raw materials into the beer we all know and love.
Aspiring winemakers and seasoned professionals alike face the precipice of a critical decision-making process that will determine the quality and consistency of their liquid products. Beyond the allure of brewing the perfect pint, the journey includes a detailed understanding of brewhouse equipment, financial considerations, and the meticulous care required for continued success. Join us on this adventure as we discover the art of capturing and preserving the beating heart of a brewery. From choosing the right equipment for your needs to implementing diligent maintenance practices, this guide will be your compass on your journey to brewing excellence.
Complete Guide
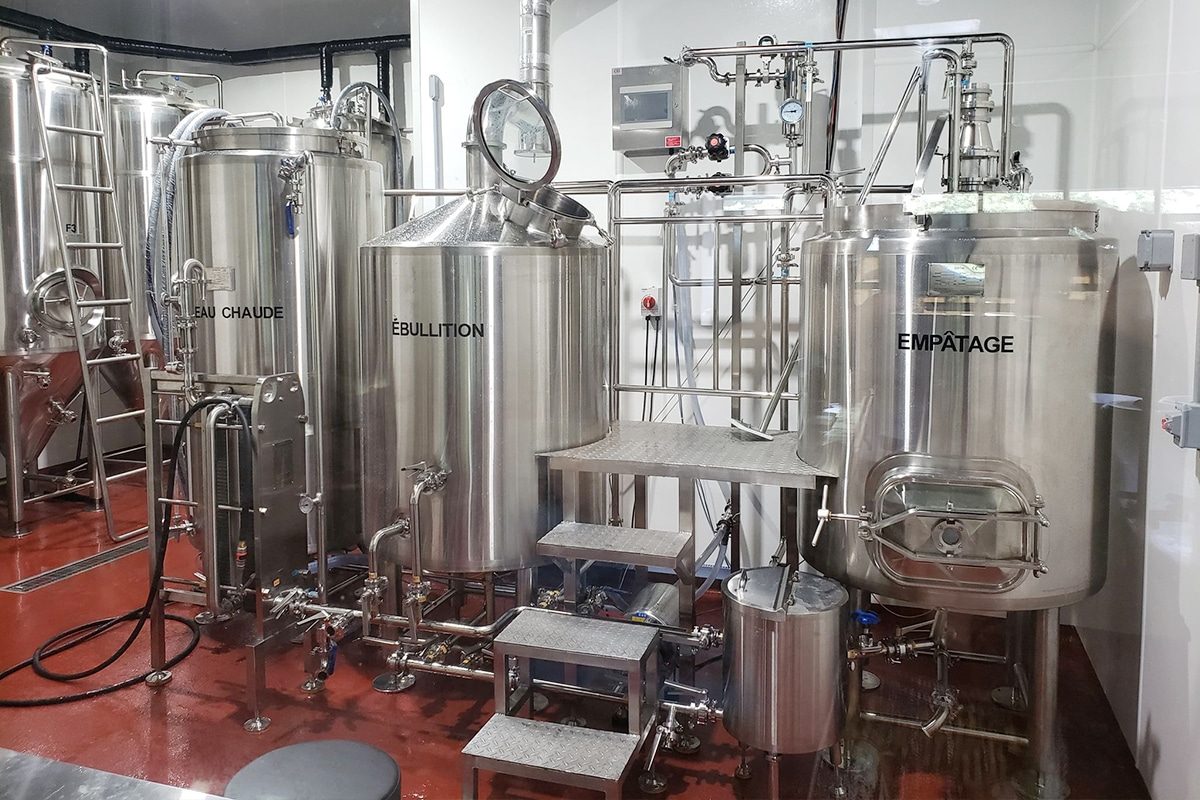
Understanding the Components of a Brewhouse
In the intricate dance of brewing, the brewhouse serves as the stage where raw ingredients transform into liquid gold. Comprising four essential components, the mash tun, lauter tun, kettle tun, and whirlpool tun, the brewhouse orchestrates each step of the brewing process with precision and finesse.
Mash Tun
The mash tun is where the alchemy begins, as milled grains meet hot water to initiate the enzymatic conversion of starches into fermentable sugars. This vessel serves as the incubator for the mash, maintaining specific temperatures to optimize enzymatic activity. Equipped with insulation and temperature controls, a well-designed mash tun ensures efficient saccharification, laying the foundation for a flavorful brew.
Lauter Tun
Following the mashing process, the liquid wort must be separated from the spent grain in the lauter tun. Here, a false bottom or grain bed acts as a natural filter, allowing the sweet wort to flow while retaining the grain husks. Proper filtration helps prevent grain particles from entering the cooking pot and ensures the clarity and purity of the final product.
Kettle Tun
Once separated, the wort journeys to the kettle tun, where it undergoes a vigorous boil with hops and adjuncts. The boiling process not only sterilizes the wort but also facilitates hop utilization and flavor development. Equipped with heating elements and safety features to prevent boil-overs, the kettle tun plays a pivotal role in shaping the beer’s character and aroma.
Whirlpool Tun
After boiling, the wort enters the whirlpool tun, where it undergoes a gentle whirlpooling motion to settle out solids such as hop debris and coagulated proteins. This centrifugal action creates a natural cone of trub at the center of the vessel, allowing the clarified wort to be drawn off for fermentation. Efficient trub separation in the whirlpool tun ensures a clean and pristine wort, setting the stage for a successful fermentation process.
In mastering the art of brewing, understanding the function and intricacies of each brewhouse component is essential. With the mash tun, lauter tun, kettle tun, and whirlpool tun working in harmony, brewers can unlock the full potential of their craft, producing exceptional beers that delight the palate and captivate the senses.
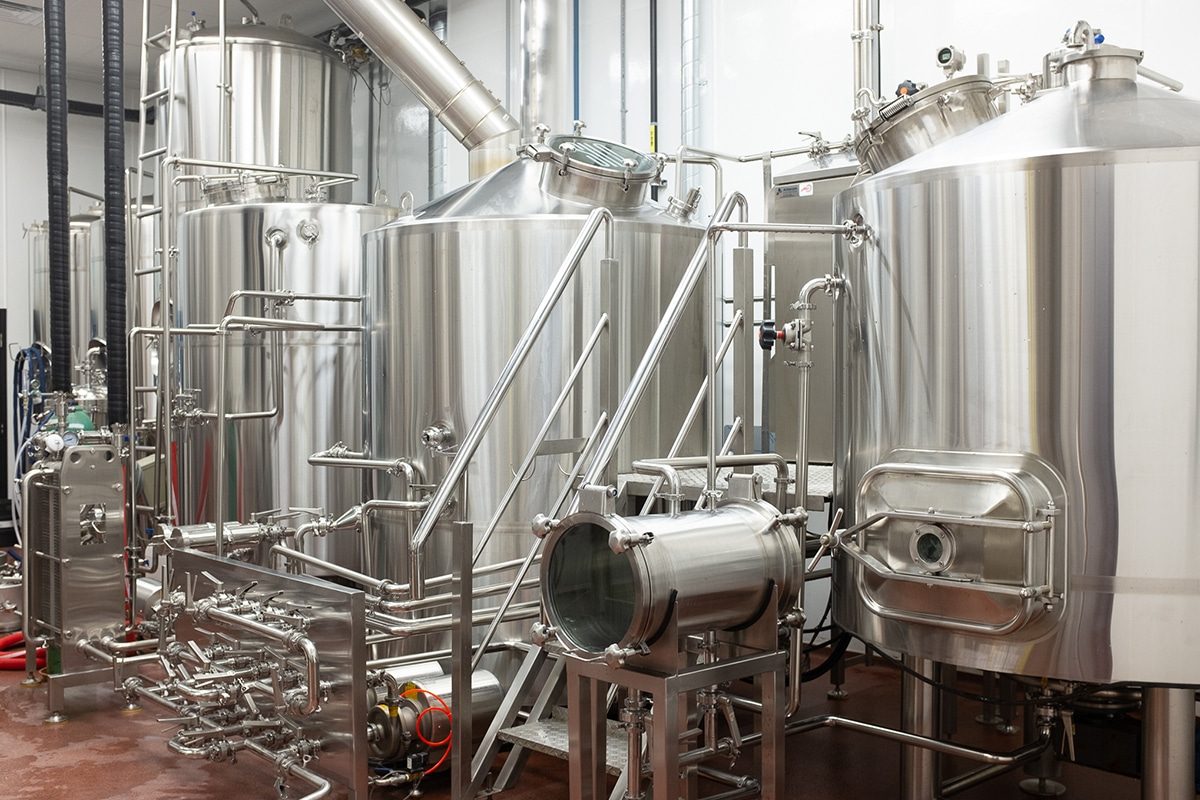
Assessing Your Brewing Needs and Budget
Investing in a brewhouse is a significant undertaking that requires careful consideration of your brewing needs and financial resources. Before diving into the buying process, you need to evaluate the size of your operation and budget constraints. Let’s explore how to effectively evaluate these factors to ensure you acquire a brewhouse that meets your requirements without breaking the bank.
Batch Size and Production Volume
- Determine the batch size that aligns with your production goals. Are you brewing small experimental batches or aiming for large-scale commercial production?
- Consider your anticipated production volume. Will you be brewing daily, weekly, or on a more sporadic basis?
Space Availability
- Evaluate the space available for installing your brewhouse. Ensure it’s sufficient to accommodate the equipment and provide room for operation and maintenance activities.
- Consider any spatial limitations or constraints that may impact the size or configuration of your brewhouse.
Frequency of Brewing
- Assess how frequently you plan to brew. This will influence the capacity and throughput requirements of your brewhouse.
- Determine whether your brewing schedule will be consistent or variable, as this may impact the size and design of the equipment needed.
Budget Considerations
- Establish a realistic budget for acquiring your brewhouse equipment. Consider not only the upfront costs but also ongoing expenses such as utilities, maintenance, and repairs.
- Research the market to understand the price range of brewhouse equipment that meets your needs. Be prepared to prioritize features based on their importance to your brewing operation.
Return on Investment (ROI)
- Evaluate the potential ROI of your brewhouse investment. Consider factors such as increased production capacity, efficiency gains, and the ability to produce higher-quality beer.
- Balance the upfront cost of the equipment with the long-term benefits it will provide to your brewery’s bottom line.
By carefully assessing your brewing needs and budgetary considerations, you can make informed decisions when purchasing a brewhouse. Whether you are a start-up brewery looking to establish yourself in the market or an established brewery looking to expand or upgrade, understanding these factors can help lead to a successful brewing career.
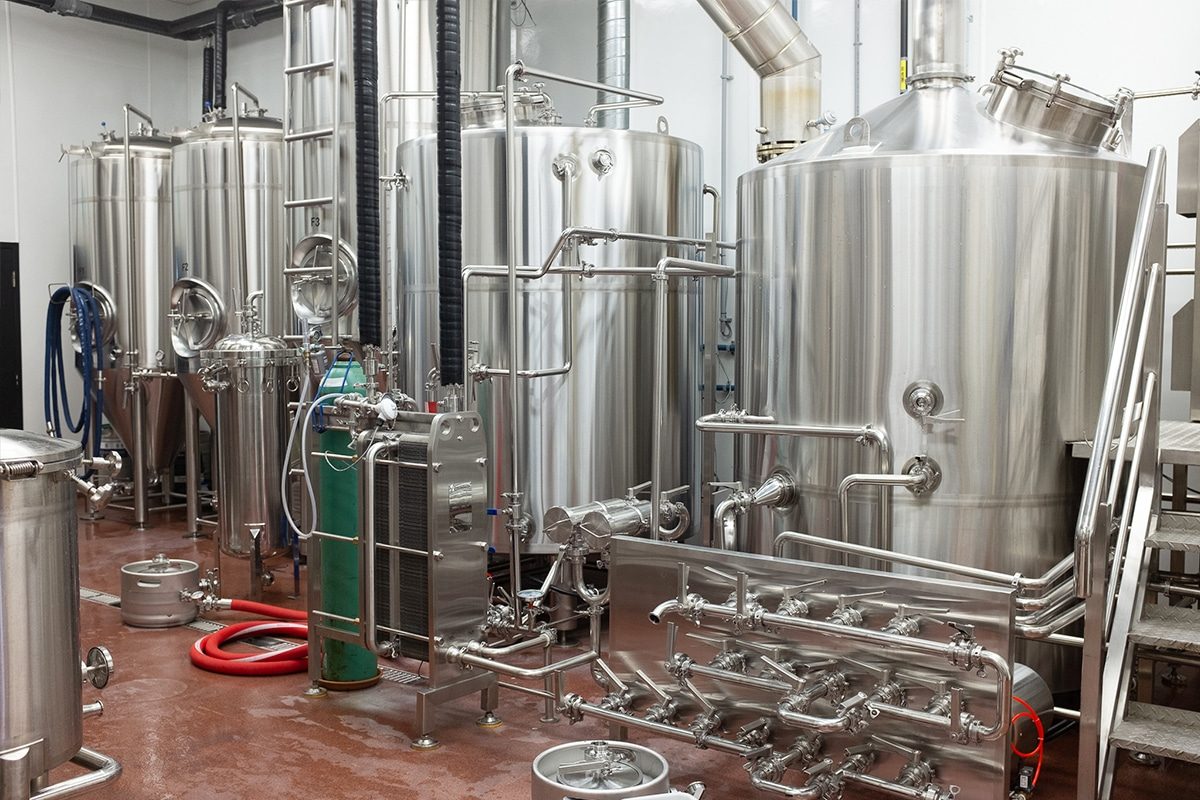
Selecting the Right Equipment Supplier
Choosing the right supplier for your brewhouse equipment is a critical decision that can significantly impact the success of your brewing venture. From ensuring product quality and reliability to providing ongoing support and service, the supplier plays a pivotal role in the acquisition and maintenance of your brewhouse. Here are some essential factors to consider when selecting an equipment supplier:
Reputation and Experience
- Research the supplier’s reputation within the brewing industry. Look for testimonials and reviews from other brewers who have worked with them.
- Consider the supplier’s experience in designing, manufacturing, and installing brewhouse equipment. An established track record indicates reliability and expertise.
Quality of Equipment
- Evaluate the quality of the brewhouse equipment offered by the supplier. Look for materials, construction methods, and manufacturing standards that ensure durability and performance.
- Inquire about certifications and compliance with industry standards, such as ASME (American Society of Mechanical Engineers) for pressure vessels.
Customization Options
- Assess the supplier’s ability to customize brewhouse equipment to meet your specific needs and preferences. Customization may include modifications to size, configuration, and features.
Technical Support and Service
- Ensure that the supplier offers comprehensive technical support before, during, and after the installation of the equipment. This includes assistance with design, installation, and troubleshooting.
- Inquire about the availability of spare parts and maintenance services to address any issues that may arise over time.
Warranty and After-Sales Support
- Review the supplier’s warranty policy to understand the coverage and duration provided for brewhouse equipment.
- Clarify the process for warranty claims and the availability of after-sales support, including repairs and maintenance.
Cost and Value
- Compare pricing and value propositions from multiple suppliers to ensure you’re getting the best deal without compromising on quality.
- Consider factors beyond the initial purchase price, such as long-term reliability, efficiency, and the total cost of ownership.
References and Testimonials
- Request references from the supplier and reach out to previous customers to gather insights into their experience.
- Ask for case studies or testimonials that demonstrate successful installations and satisfied customers.
Location and Logistics
- Consider the supplier’s location and its impact on shipping costs, delivery times, and installation logistics.
- Evaluate the supplier’s ability to handle logistics, including transportation, customs clearance (if applicable), and on-site installation.
In conclusion, selecting the right equipment supplier is a critical step in the process of acquiring and maintaining a brewhouse. By considering factors such as reputation, quality, customization options, technical support, warranty, cost, and references, you can make an informed decision that lays the foundation for a successful brewing operation.
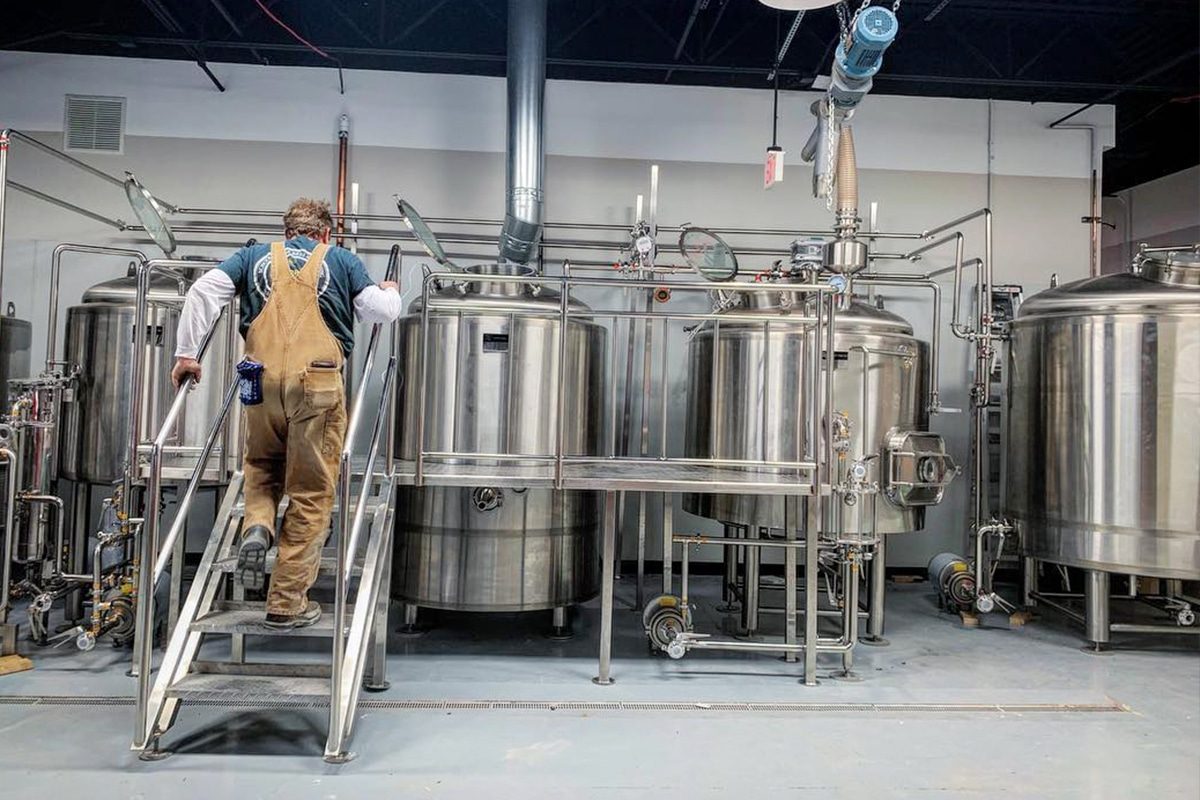
Installation and Commissioning
Once you’ve selected the right brewhouse equipment and supplier, the next crucial step is the installation and commissioning process. This phase sets the foundation for your brewing operations and ensures that your brewhouse functions optimally from the outset. Here’s a comprehensive guide to navigating the installation and commissioning of your mash tun, lauter tun, kettle tun, and whirlpool tun.
Pre-Installation Preparation
- Site Readiness: Ensure that the installation site is prepared according to the supplier’s specifications, including adequate space, ventilation, and utility connections. Clear any obstructions and ensure a clean, level surface for installation.
- Utility Connections: Coordinate with electricians, plumbers, and HVAC technicians to ensure proper connections for electricity, water, steam, and drainage. Verify that utility connections meet local building codes and safety standards.
Equipment Inspection and Acceptance
- Visual Inspection: Conduct a thorough visual inspection of each component, checking for any signs of damage during transportation. Ensure that all parts and accessories are accounted for.
- Documentation Review: Review the accompanying documentation, including manuals and certificates. Confirm that the equipment matches the specifications outlined in the purchase agreement.
Equipment Placement
- Layout Planning: Strategically position each brewhouse component to optimize workflow and efficiency. Consider accessibility for operation, maintenance, and cleaning purposes.
- Alignment and Leveling: Ensure that each piece of equipment is aligned and leveled correctly to prevent issues such as uneven heating or drainage. Use precision leveling tools to achieve optimal alignment.
Installation Process
- Assembly and Integration: Follow the manufacturer’s instructions for assembling and integrating each brewhouse component. Verify that all components are securely fastened and connected according to specifications.
- Testing and Calibration: Conduct thorough testing of each component to ensure proper functionality. Calibrate temperature, pressure, and other settings as per brewing requirements.
Commissioning and Start-Up
- Initial Startup Procedures: Gradually start up each component, following the recommended procedures provided by the manufacturer. Monitor for any anomalies or issues during the startup process.
- Performance Verification: Perform initial brewing trials to verify the performance and efficiency of the brewhouse. Monitor key parameters such as temperature, flow rates, and pressure to ensure consistency and quality.
Training and Handover
- Operator Training: Provide comprehensive training to brewing and maintenance personnel on the operation and maintenance of the brewhouse equipment. Ensure that operators are familiar with safety protocols and emergency procedures.
- Documentation and Handover: Compile all relevant documentation, including equipment manuals, schematics, and maintenance schedules. Conduct a formal handover process, ensuring that all stakeholders are informed and equipped to manage the brewhouse effectively.
Post-Installation Support
- Technical Assistance: Establish communication channels for ongoing technical support and troubleshooting with the equipment supplier. Address any post-installation issues promptly to minimize downtime.
- Continuous Improvement: Regularly evaluate and optimize brewhouse operations to maximize efficiency and quality. Implement feedback mechanisms to gather input from brewing staff and identify areas for improvement.
By meticulously following the installation and commissioning process outlined above, you can ensure a smooth transition from equipment delivery to full-scale brewing operations. Investing time and resources into proper installation and commissioning lays the groundwork for a successful and sustainable brewery venture.
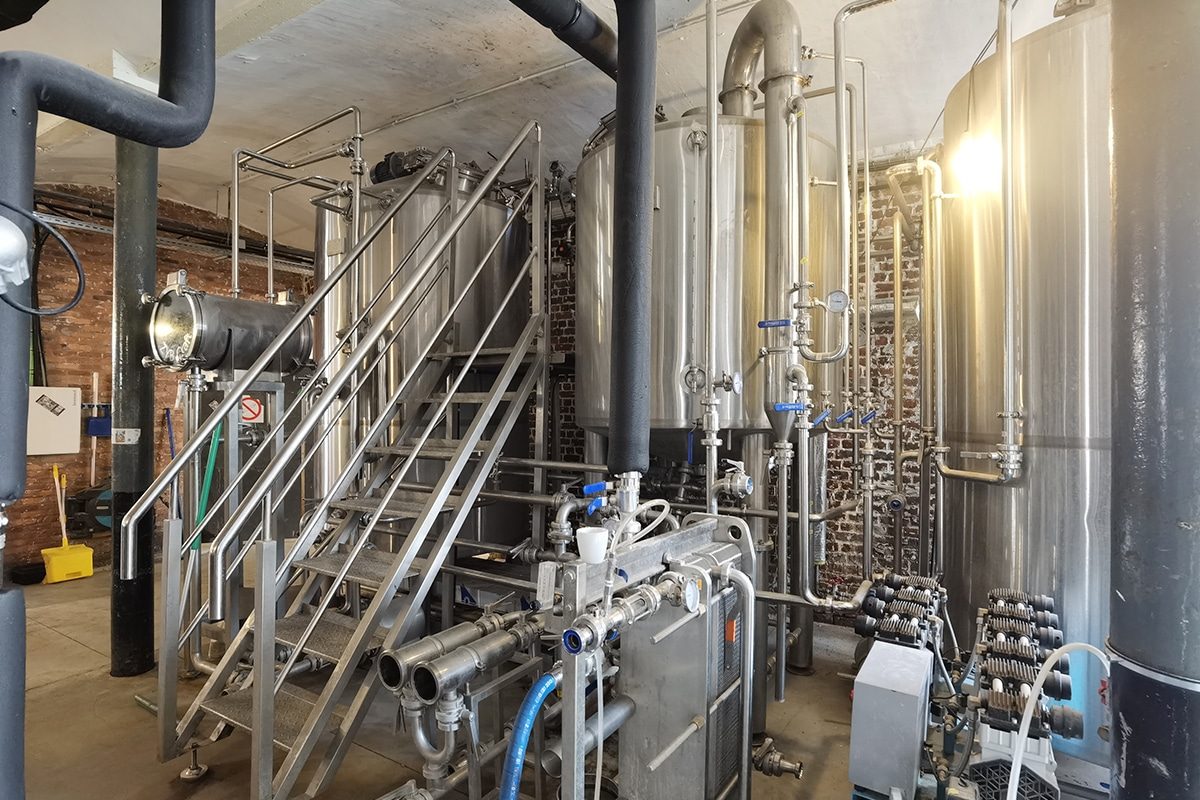
Implementing a Maintenance Plan
Maintaining a brewhouse is not just about ensuring smooth operations; it’s about safeguarding the quality and consistency of your beer. A well-executed maintenance plan is the cornerstone of preserving your investment and maximizing the lifespan of your brewhouse equipment. Here’s a comprehensive guide to implementing an effective maintenance plan for your mash tun, lauter tun, kettle tun, and whirlpool tun:
Developing a Maintenance Schedule
- Routine Cleaning Tasks: Establish a regular cleaning schedule for each component, addressing residue build-up and ensuring sanitary conditions. Use appropriate cleaning agents, following manufacturer guidelines to preserve equipment integrity.
- Inspection and Lubrication: Schedule routine inspections to identify wear, corrosion, or loose components. Lubricate moving parts, such as valves and agitators, to reduce friction and prevent mechanical issues.
- Calibration Checks: Regularly calibrate temperature and pressure gauges to maintain accuracy. Ensure that control systems are functioning correctly for precise brewing conditions.
Components-Specific Maintenance Tasks
- Mash Tun: Check temperature control mechanisms and insulation integrity. Clean false bottoms and screens to prevent clogging during lautering.
- Lauter Tun: Inspect filtration systems for efficiency and uniform drainage. Clean and sanitize all surfaces to prevent contamination of wort.
- Kettle Tun: Monitor heating elements for optimal performance and even heating. Remove trub and sediment buildup after each boil to prevent fouling.
- Whirlpool Tun: Ensure proper functioning of agitation mechanisms for trub separation. Clean whirlpool arms and drains to maintain efficient whirlpooling.
Preventative Maintenance
- Predictive Analysis: Implement predictive maintenance measures, such as vibration analysis and thermal imaging, to identify potential issues before they occur. Use data-driven insights to schedule maintenance tasks proactively.
- Replace Wearable Parts: Identify components prone to wear and plan for regular replacement, such as seals, gaskets, and O-rings. Keep spare parts on hand to minimize downtime in case of unexpected failures.
- Calibration and Adjustment: Periodically calibrate temperature and pressure gauges to ensure accuracy. Adjust control settings as needed to optimize brewing processes.
Documentation and Record-Keeping
- Maintenance Logs: Maintain detailed records of all maintenance activities, including inspections, cleanings, repairs, and replacements. Document any issues encountered and the steps taken to address them.
- Equipment Manuals: Keep equipment manuals and documentation readily accessible for reference. Update manuals with any modifications or customizations made to the equipment.
Training and Education
- Staff Training: Provide comprehensive training to brewing and maintenance staff on brewhouse operation and maintenance. Empower staff to identify potential issues and perform routine maintenance tasks.
- Continued Education: Stay informed about advancements in brewing technology and maintenance best practices. Attend workshops, seminars, or online courses to enhance knowledge and skills.
Emergency Preparedness
- Emergency Protocols: Develop and communicate clear protocols for handling emergencies such as equipment malfunctions, leaks, or power outages. Ensure staff are trained to respond quickly and effectively to mitigate risks.
- Emergency Contacts: Maintain a list of emergency contacts, including equipment suppliers, maintenance technicians, and utility providers. Ensure contact information is readily available in case of emergencies.
Collaboration with Equipment Supplier
- Scheduled Manufacturer Inspections: Arrange for scheduled inspections by the equipment supplier’s technicians to identify any issues not apparent during routine maintenance. Leverage the expertise of the supplier to optimize equipment performance.
- Software Updates: Stay informed about any software updates or improvements provided by the equipment manufacturer. Implement updates to benefit from the latest features and enhancements.
Continuous Improvement Initiatives
- Feedback Mechanisms: Encourage feedback from maintenance staff regarding equipment performance and potential areas for improvement. Implement continuous improvement initiatives based on insights gathered from the maintenance team.
- Periodic Assessments: Conduct periodic assessments of the maintenance plan’s effectiveness and make adjustments as needed. Stay adaptable to changes in brewery operations, scale, or equipment usage.
Implementing a comprehensive maintenance program can help maintain the integrity and performance of your brewhouse equipment. By establishing a proactive approach to maintenance, documenting all activities, providing staff training, and staying prepared for emergencies, you ensure the longevity and reliability of your brewhouse, ultimately safeguarding the quality of your beer.
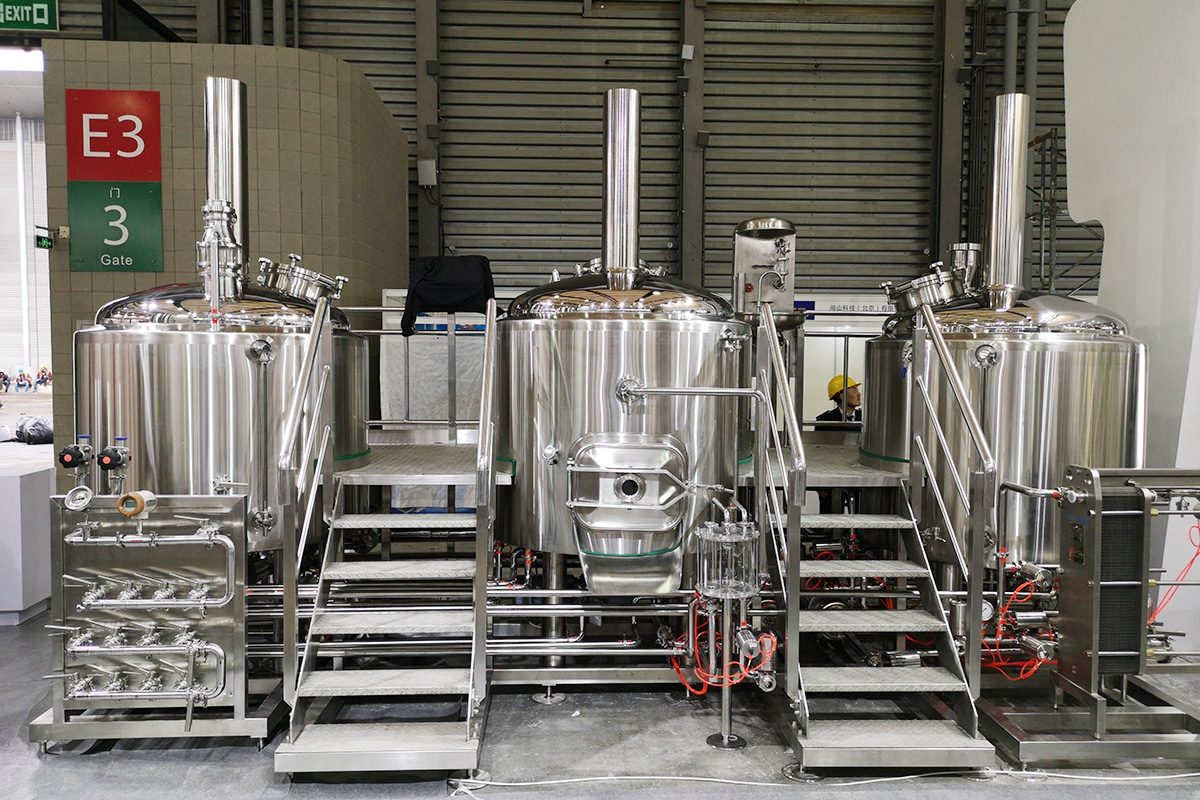
Troubleshooting and Repairs
Despite meticulous maintenance, occasional issues may arise with your brewhouse equipment. Prompt troubleshooting and effective repairs are essential to minimize downtime and ensure uninterrupted brewing operations. Here’s a comprehensive guide on how to tackle troubleshooting and repairs for your mash tun, lauter tun, kettle tun, and whirlpool tun:
Establishing a Troubleshooting Framework
- Diagnostic Procedures: Develop systematic diagnostic procedures for each brewhouse component to identify the root cause of issues. Include checks for temperature control, pressure levels, and mechanical components.
- Troubleshooting Team: Assemble a dedicated troubleshooting team comprising brewing and maintenance personnel. Clearly define roles and responsibilities to streamline the resolution process.
Common Issues and Solutions
Temperature Fluctuations
- Issue: Inconsistent mash or wort temperatures.
- Solution: Calibrate temperature sensors, check heating elements, and inspect insulation for any damage.
Clogging or Slow Drainage
- Issue: Slow drainage during lautering or whirlpooling.
- Solution: Investigate and clear any blockages in pipes, screens, or filters; inspect and clean pumps.
Leakages
- Issue: Fluid leakages from valves, seals, or connections.
- Solution: Tighten connections, replace damaged seals, and inspect for any corrosion or wear.
Agitator or Mixer Malfunctions
- Issue: Agitator or mixer not functioning correctly.
- Solution: Check the power supply, inspect for mechanical issues, and lubricate moving parts.
Control System Errors
- Issue: Malfunctions in the control system.
- Solution: Review error codes, check wiring and connections and ensure the software is up-to-date.
Troubleshooting Procedures
- Systematic Approach: Adopt a systematic approach to troubleshooting, starting with the most likely causes and progressing methodically. Refer to equipment manuals and documentation for troubleshooting guidelines specific to each component.
- Diagnostic Tools: Utilize diagnostic tools such as pressure gauges, temperature sensors, and flow meters to pinpoint issues accurately. Implement predictive maintenance measures to anticipate potential problems before they escalate.
Emergency Response Protocol
- Establish Clear Procedures: Develop clear and concise emergency response procedures for handling equipment failures or safety hazards. Train brewing and maintenance staff on emergency protocols to ensure a swift and coordinated response.
- 24/7 Technical Support Access: Maintain access to 24/7 technical support from the equipment supplier for immediate assistance during critical situations. Establish communication channels for rapid response and resolution of urgent issues.
Repair and Replacement
- Assess the Extent of Damage: Assess the extent of damage or malfunction to determine whether repairs can be performed on-site or if components need replacement. Consult with equipment suppliers or certified technicians for guidance on repair options.
- Spare Parts Inventory: Maintain an inventory of commonly used spare parts, such as seals, gaskets, and heating elements, to facilitate prompt repairs. Ensure that replacement parts meet manufacturer specifications and quality standards.
Collaboration with Equipment Supplier
- Technical Support Hotline: Establish a direct line of communication with the equipment supplier’s technical support team. Ensure 24/7 access to assistance during emergencies.
- Scheduled Maintenance Checks: Coordinate with the supplier for periodic maintenance checks, including assessments of wear and tear. Leverage the expertise of the supplier’s technicians to address complex issues.
Documentation and Reporting
- Record Maintenance Activities: Document all troubleshooting and repair activities, including observations, actions taken, and outcomes. Maintain a detailed log for each component to track maintenance history and identify recurring issues.
- Reporting to Management: Provide regular reports to brewery management on troubleshooting efforts, repair status, and recommendations for preventing future issues. Collaborate with management to implement corrective actions and improve equipment reliability.
Continuous Improvement Initiatives
- Root Cause Analysis: Conduct root cause analysis to identify underlying factors contributing to equipment failures. Implement corrective measures to address root causes and prevent recurrence.
- Training and Skill Development: Invest in ongoing training and skill development for maintenance staff to enhance their troubleshooting capabilities. Foster a culture of continuous learning and improvement within the maintenance team.
Integration with Preventative Maintenance
- Feedback Loop: Establish a feedback loop between the troubleshooting team and those responsible for preventative maintenance. Use insights from troubleshooting to enhance preventative measures.
- Predictive Analysis: Leverage data collected during troubleshooting for predictive analysis. Identify patterns or trends that may indicate potential issues before they manifest.
Budgeting for Repairs
- Emergency Repair Fund: Set aside a budget specifically for emergency repairs and unexpected equipment replacements. Regularly assess the fund to ensure it aligns with the brewhouse’s evolving needs.
- Insurance Coverage: Explore insurance options that cover equipment breakdowns and emergency repairs. Understand the terms and conditions of the coverage to make informed decisions.
The proactive and systematic approach to troubleshooting and repair helps maintain the reliability and efficiency of your brewery equipment. By establishing a comprehensive framework, collaborating with the equipment supplier, documenting issues, continuous improvement initiatives, and integrating troubleshooting with preventative maintenance, you ensure that your brewhouse remains a resilient and dependable asset throughout its operational life.
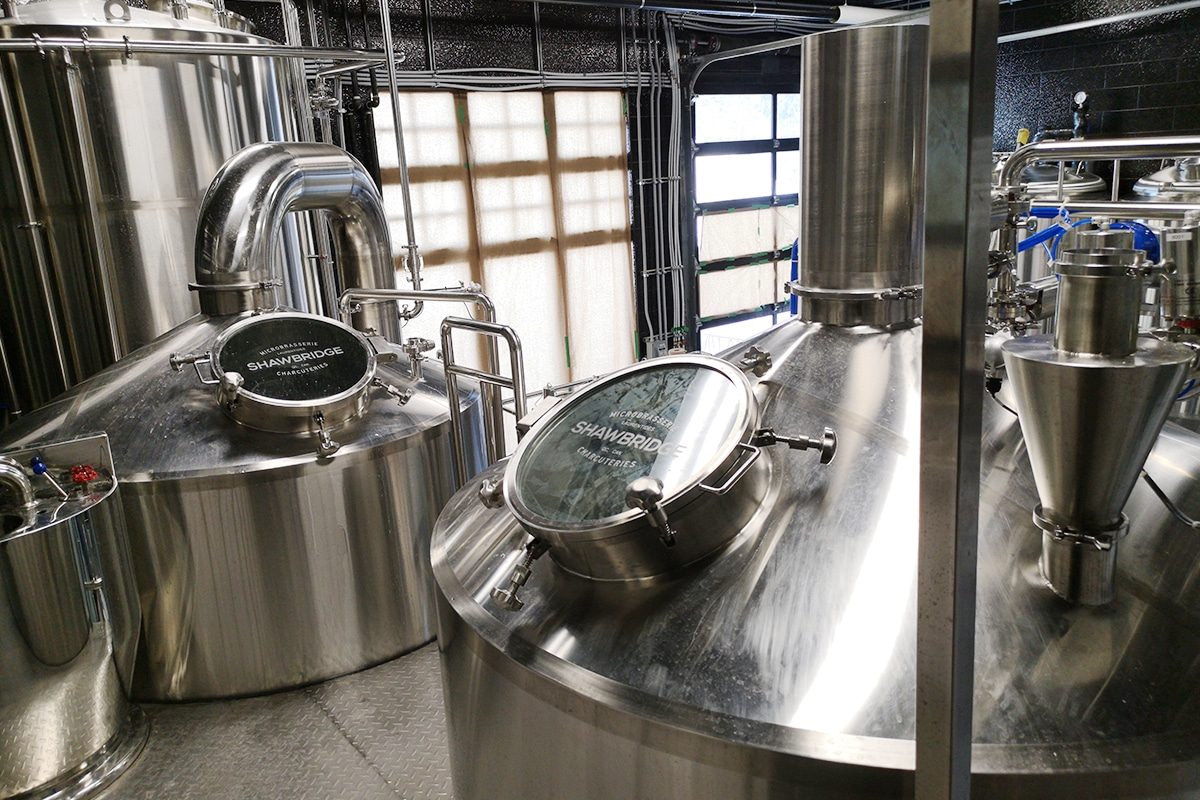
Continuous Improvement and Optimization
In the dynamic world of brewing, the pursuit of excellence is a journey rather than a destination. Continuous improvement and optimization are essential pillars that drive innovation, enhance efficiency, and elevate the quality of your brewing operations. This guide outlines key strategies to implement continuous improvement initiatives for your mash tun, lauter tun, kettle tun, and whirlpool tun, ensuring that your brewhouse remains at the forefront of brewing excellence.
Data-Driven Decision-Making
- Performance Metrics: Establish key performance indicators (KPIs) to measure the efficiency and effectiveness of brewhouse operations. Monitor metrics such as brewing cycle times, yield, energy consumption, and quality parameters.
- Data Collection and Analysis: Implement systems for collecting and analyzing data from brewhouse operations. Utilize data analytics tools to identify trends, patterns, and areas for improvement.
Regular Performance Reviews
- Periodic Assessments: Conduct regular reviews of brewhouse performance against established KPIs. Evaluate the effectiveness of maintenance procedures, brewing processes, and equipment utilization.
- Root Cause Analysis: Perform root cause analysis to identify underlying issues contributing to inefficiencies or quality deviations. Use findings to develop targeted improvement initiatives.
Staff Training and Empowerment
- Skills Enhancement Programs: Offer training programs to brewing and maintenance staff to enhance their skills and knowledge. Focus on areas such as equipment operation, maintenance best practices, and quality assurance techniques.
- Empowerment Initiatives: Encourage staff to contribute ideas and suggestions for process improvement. Foster a culture of empowerment and ownership, where employees feel valued and motivated to drive positive change.
Equipment Upgrades and Modernization
- Technology Adoption: Stay informed about advancements in brewing technology and equipment. Evaluate opportunities to upgrade or modernize brewhouse components to enhance performance and efficiency.
- Efficiency Enhancements: Explore innovations such as automated controls, energy-efficient heating systems, and process optimization tools. Implement upgrades that streamline operations and reduce resource consumption.
Process Optimization
- Workflow Analysis: Analyze brewing workflows to identify bottlenecks or areas of inefficiency. Optimize process sequences and resource allocation to maximize throughput and minimize downtime.
- Lean Manufacturing Principles: Apply lean manufacturing principles, such as value stream mapping and waste reduction strategies, to brewhouse operations. Eliminate non-value-added activities and streamline workflows for optimal efficiency.
Quality Assurance Initiatives
- Quality Control Measures: Implement rigorous quality control measures throughout the brewing process. Conduct sensory evaluations, lab analyses, and microbiological tests to maintain product consistency and integrity.
- Continuous Feedback Loops: Establish feedback loops between brewing, quality assurance, and maintenance teams. Use feedback to identify opportunities for process refinement and equipment optimization.
Sustainability Practices
- Resource Conservation: Implement sustainable practices to minimize water, energy, and raw material consumption. Explore options for wastewater treatment, heat recovery, and renewable energy sources.
- Environmental Stewardship: Commit to reducing environmental impact through initiatives such as waste recycling, carbon footprint reduction, and eco-friendly packaging. Engage with suppliers and partners who share your sustainability values.
Collaboration and Knowledge Sharing
- Industry Networking: Engage with the brewing community through industry events, conferences, and forums. Exchange knowledge, experiences, and best practices with peers and industry experts.
- Supplier Collaboration: Foster collaboration with equipment suppliers to stay abreast of new technologies and innovations. Leverage supplier expertise to address specific challenges and optimize brewhouse performance.
Continuous improvement and optimization contribute to the long-term success and sustainability of brewery operations. By embracing a culture of innovation, leveraging data-driven insights, empowering staff, adopting modern technologies, optimizing processes, ensuring quality assurance, prioritizing sustainability, and fostering collaboration, you position your brewery for ongoing success and growth in the dynamic brewing landscape.
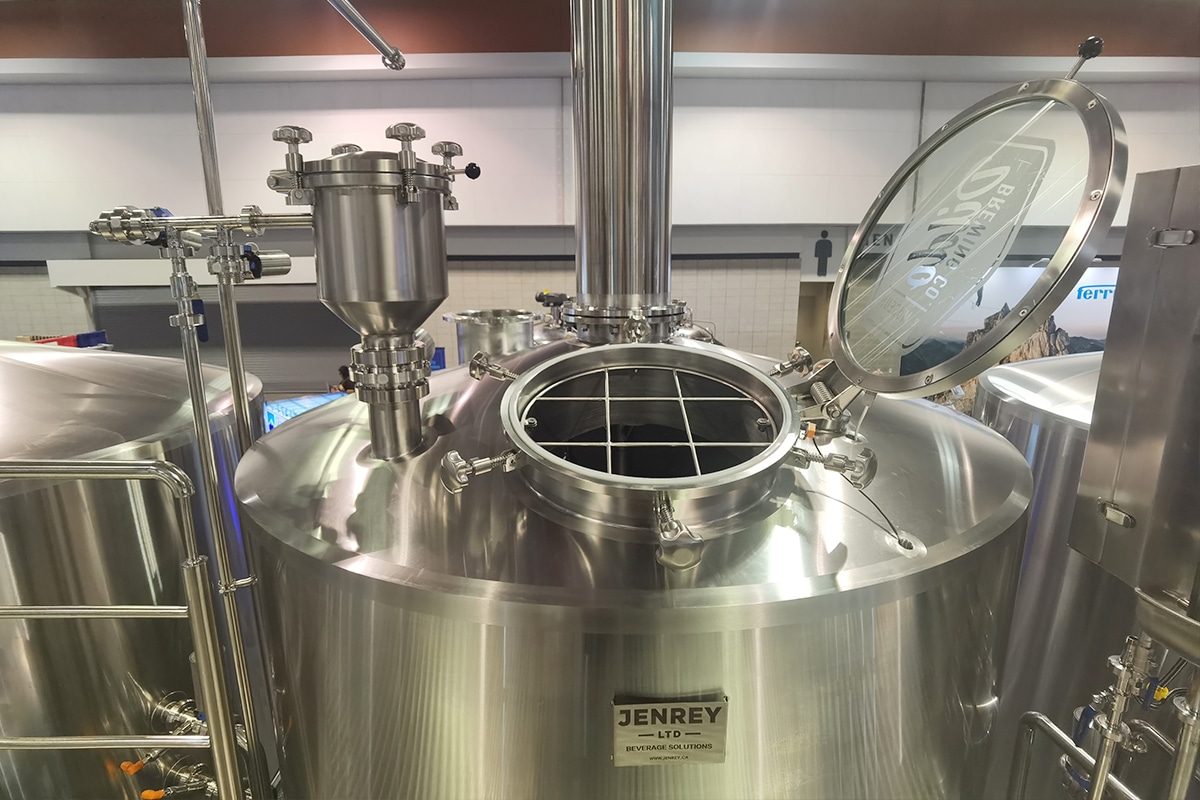
Summarize
In the journey of procuring and preserving a brewhouse, meticulous planning, and diligent maintenance are paramount. Selecting the optimal equipment supplier involves thorough research, considering factors like industry reputation, equipment customization options, and adherence to brewing regulations. Installation and commissioning demand careful coordination with suppliers to ensure seamless integration into your brewery space. Once operational, implementing a comprehensive maintenance plan is essential, encompassing regular cleaning, calibration, and staff training. Troubleshooting procedures and emergency response protocols should be in place to minimize downtime and ensure uninterrupted brewing operations. Additionally, fostering a culture of continuous improvement and sustainability ensures that your brewhouse remains at the forefront of brewing excellence. By investing in quality equipment, adhering to rigorous maintenance protocols, and embracing innovation, your brewhouse becomes not only a cornerstone of your brewery but also a symbol of craftsmanship and dedication to the art of brewing.
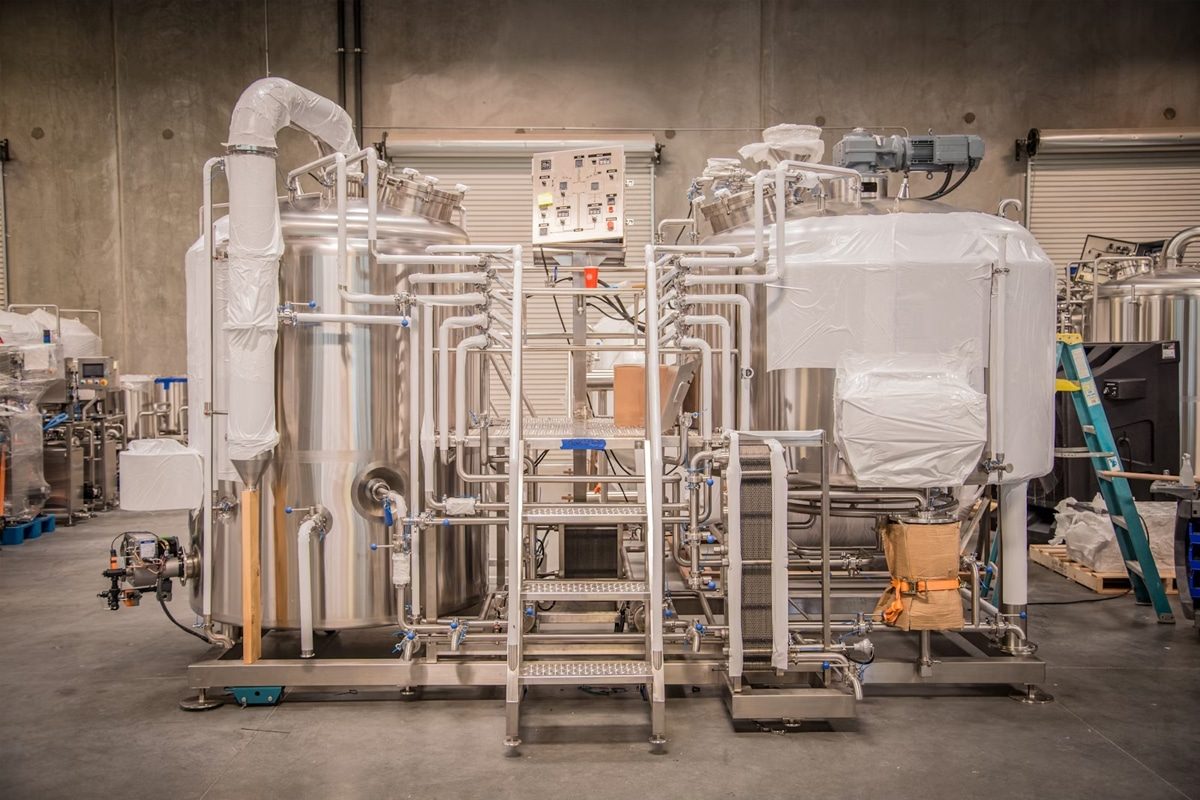
Get A Brewhouse Solutions
ZYB Craft specializes in providing comprehensive brewhouse solutions tailored to the specific needs of breweries. With expertise in brewhouse equipment, including mash tun, lauter tun, kettle tun, and whirlpool tun, ZYB Craft ensures that breweries are equipped with high-quality machinery designed for optimal performance.
Through ZYB Craft’s turnkey solutions, breweries benefit from a seamless purchasing process, from equipment procurement to installation and setup. Additionally, ZYB Craft offers ongoing maintenance and support services, ensuring that brewhouse equipment remains in top condition for years to come. With ZYB Craft as your partner, breweries can confidently invest in brewhouse solutions that lay the foundation for efficient brewing operations and long-term success.