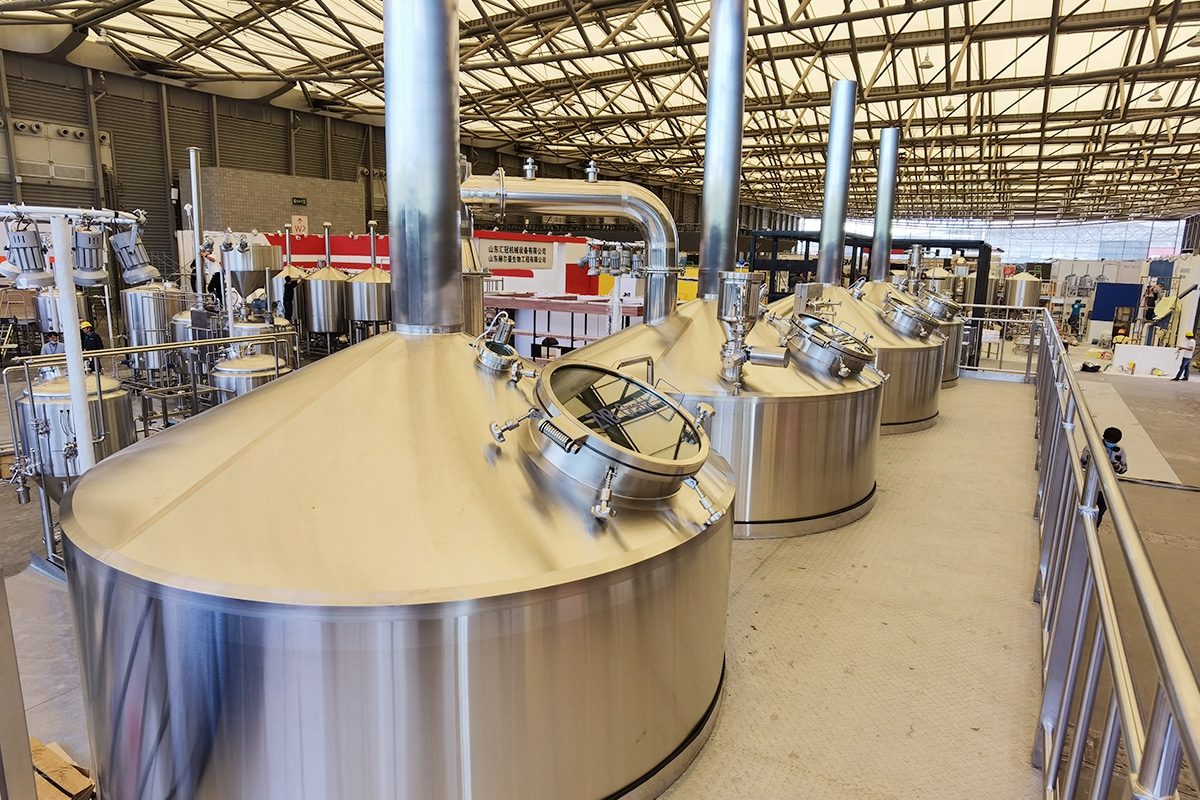
2-Vessels VS 3-Vessels VS 4-Vessel Brewhouse
In the alchemical world of brewing, where art meets science, at the heart of every brewery is the brewhouse. The choice of brewhouse configuration is a critical decision that greatly affects the brewing process. These configurations hold the secrets of efficiency, precision, and mastery. The 2 vessel setup champions simplicity, and mixing functionality to create streamlined processes. Meanwhile, the 3-vessel configuration achieves balance and separates brewing stages for enhanced control and versatility. And in the realm of ultimate precision, the 4-vessel brewhouse reigns supreme, with separate vessels for each critical step, guaranteeing unparalleled control and continuous brewing.
Join us as we explore the maze of brewing techniques, dissecting the role of each vessel and uncovering the brewhouse’s intricate tapestry, where every choice echoes the symphony of flavors poured into every pint. Whether you’re an experienced brewer or an aspiring enthusiast, this exploration is designed to illuminate the path to brewing excellence and assist you in selecting the ideal brewhouse configuration for your brewery.
Complete Guide
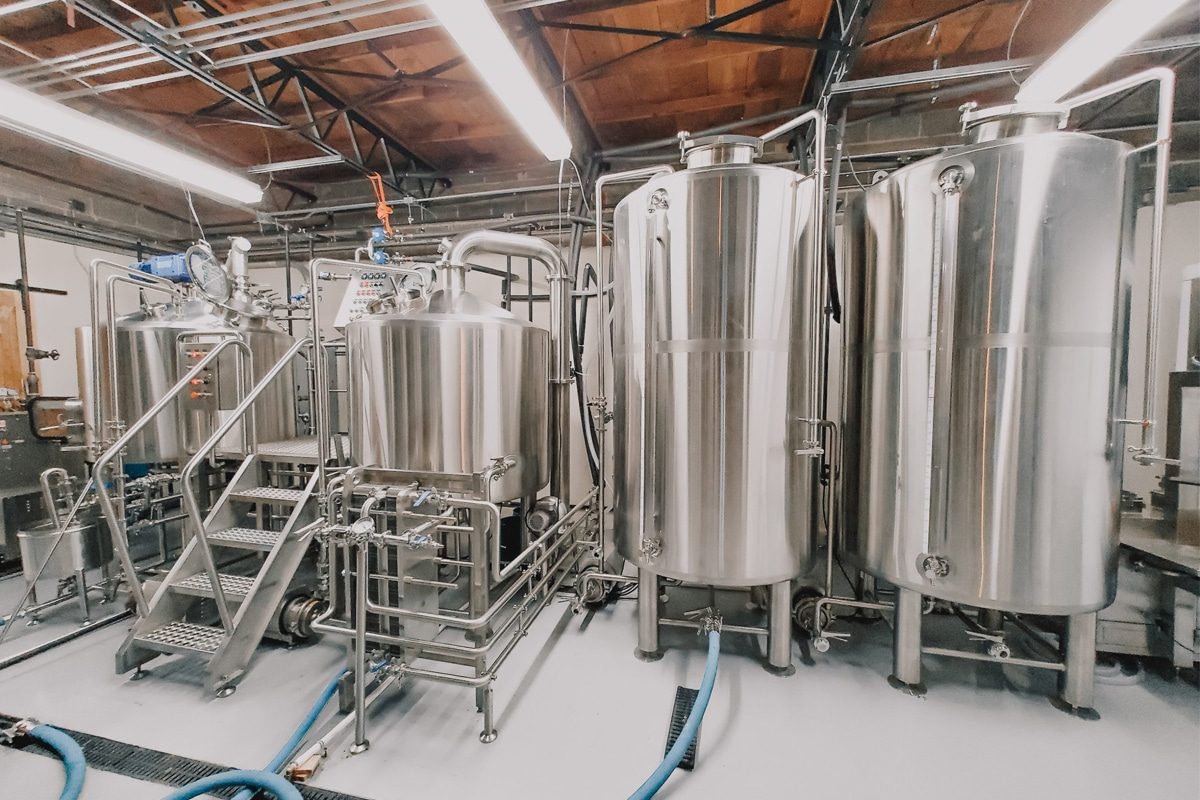
The Importance of The Brewery in The Beer Brewing Process
The Brewhouse is not only the center of beer brewing but also the key link where raw materials are transformed into liquid gold, gracing beer glasses around the world. Its importance in the brewing process is unparalleled, shaping the flavor, quality, and consistency of every beer. In essence, brewhouse orchestrates an exquisite revue of precise temperatures, meticulous timing, and expertly coordinated stages.
From mashing to filtering, boiling, and whirlpooling, every vessel in a brewery plays a key role. The brewhouse is responsible for extracting sugar from the grains, infusing hops to add bitterness and aroma, and separating the wort from the lees. It sets the stage for fermentation, determining the canvas on which yeast can work its transformative magic.
Brewhouse’s influence goes beyond technical details. It can shape the character of every beer, whether it’s a crisp lager, a stout, or an aromatic IPA. Brewers pour into their designs, seeking the perfect configuration to embody their brewing ethos, ensuring every pint poured reflects their vision and craftsmanship.
In the world of brewing, a brewhouse is more than just a space, it is a beating heart, a laboratory, and a canvas for the art of brewing. Its importance resonates with every sip of beer, so choosing between 2, 3, or 4 vessels is a complex decision that resonates throughout the brewing process.
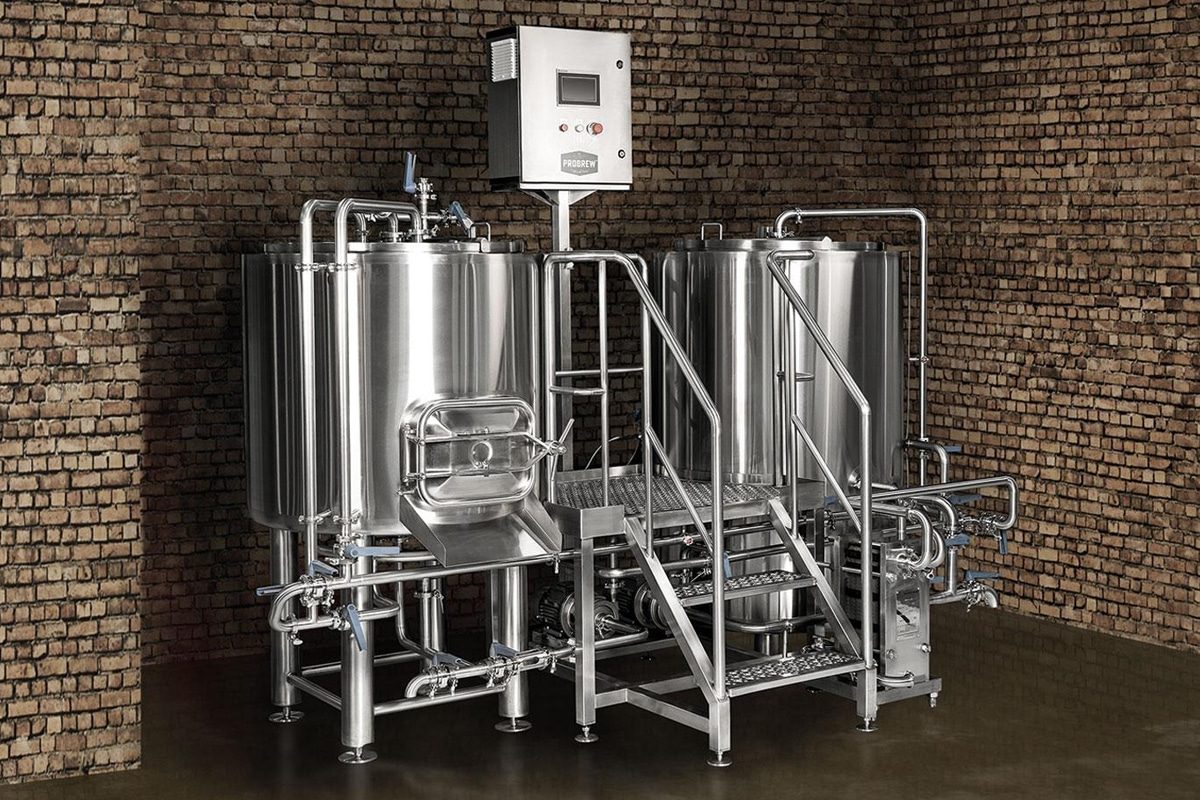
2-Vessel Brewhouse
Configuration
2 vessel brewhouse simplifies the brewing process by combining essential functions into two key vessels. The first vessel (usually a mash/lauter tun) has the dual purpose of mashing the grains and filtering to separate the wort from the spent grains. The second vessel (usually a kettle/whirlpool) is responsible for boiling the wort and facilitating the whirlpool process.
Advantages
- Space Efficiency: The 2-vessel setup has a compact footprint that maximizes available brewing space, making it ideal for small breweries with limited space.
- Cost-Effectiveness: Fewer vessels means reduced initial investment and maintenance costs, attractive to small breweries or start-ups.
- Simplified Operations: As the number of vessels is reduced, the process is simplified, allowing for simple management and workflow.
Disadvantages
- Process Limitations: Combined vessel functionality may limit simultaneous process flexibility, requiring careful planning and attention during the brewing process.
- Flexibility Limitations: A shared vessel can create challenges in adjusting brewing methods or trying different recipes at the same time.
Considerations
- Brewing Size: 2 vessels are great for smaller production sizes, but as production increases, scalability challenges may arise.
- Brewing Style: Consider the specific brewing style and planned recipe, as the simplicity of a 2-vessel configuration may be better suited for certain beer types.
- Process Management: Careful planning and sequencing of brewing steps contribute to smooth operations.
- Flexibility Needs: Evaluate whether the constraints of synchronized processes are consistent with the brewery’s production goals and recipe experiments.
The simplicity and cost-effectiveness of this configuration make it an attractive option for smaller breweries, but careful consideration of process flow and flexibility can help optimize brewing efficiency and versatility.
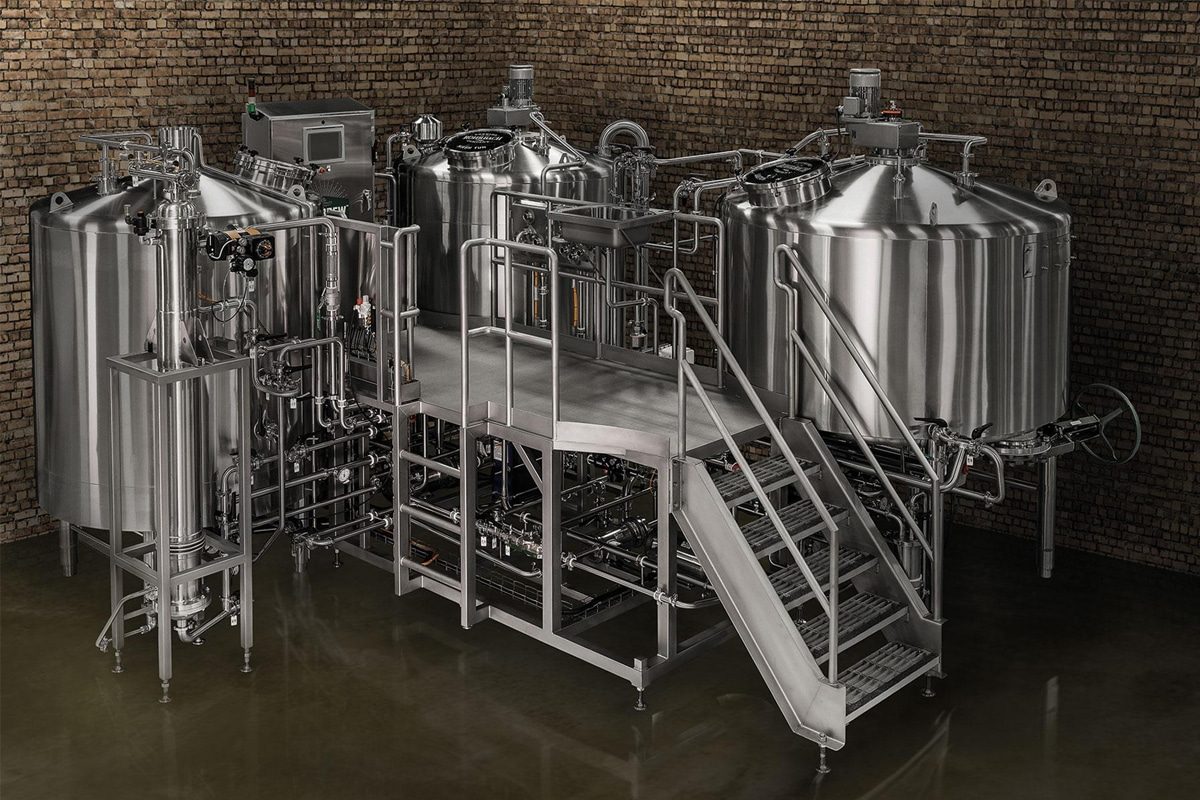
3-Vessel Brewhouse
Configuration
The 3 vessel brewhouse divides the brewing process into three dedicated vessels: the mash/lauter tun, the kettle, and the whirlpool. Each vessel is dedicated to a specific stage of the brewing process.
- Mash/Lauter Tun: Responsible for mashing, the conversion of starches to sugars, and lautering, separating the liquid wort from the spent grains.
- Kettle: Handles the boiling of the wort, allowing for the addition of hops and other flavoring agents.
- Whirlpool: Dedicated to the whirlpooling process, where the wort is gently stirred to collect trub (solid particles) in the center for later removal.
Advantage
- Enhanced Process Control: Each vessel has unique features that allow for precise control and meticulous management of the various brewing stages.
- Versatility And Synchronized Brewing: The synchronized brewing process allows for greater flexibility, allowing for multi-tasking during mashing, filtering, boiling, and swirling.
- Reduces The Risk of Cross-Contamination: Separating the stages into different vessels reduces the risk of flavor transfer from one stage to another, thus maintaining the integrity of each process.
Disadvantages
- Space Requirements: More space is required compared to a 2-vessel setup due to the need for an additional dedicated vessel. This can present challenges for smaller breweries or those with limited space.
- Higher Initial Investment: The increased number of vessels may result in higher upfront costs compared to a 2-vessel configuration. This makes it less cost-effective for some breweries, especially startups or small businesses.
Considerations
- Production Size: Suitable for mid-range production-size breweries, balancing space efficiency and versatility.
- Budgeting And Long-Term Planning: Brewers must weigh initial investment against increased control and flexibility, considering long-term growth and production goals.
- Space And Budget Constraints: Evaluate whether the brewery has enough space to accommodate additional vessels.
- Process Flexibility And Control: Evaluate the balance between increased control over each stage and the need for flexibility in the process at the same time, based on brewing goals and production needs.
Compared to a 2-vessel setup, a 3-vessel configuration provides greater control, and flexibility, and reduces the risk of cross-contamination. However, breweries must weigh these advantages against the space requirements and initial investment to determine if it’s suitable for their operations.
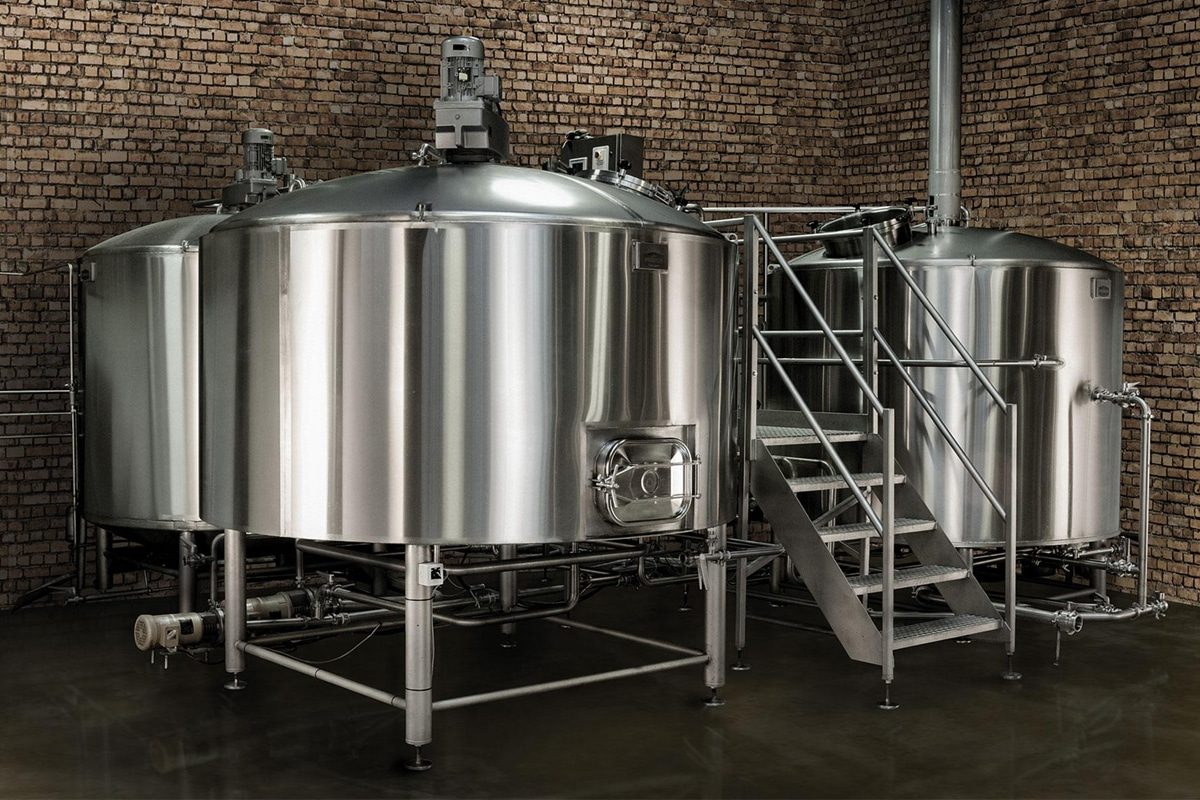
4-Vessel Brewhouse
Configuration
The 4-vessel brewhouse divides the brewing process into four separate vessels: mash tun, lauter tun, kettle, and whirlpool. Each vessel serves a different purpose in the brewing process. The mash tun is responsible for the mashing process, converting grains into fermentable sugars. The lauter tun performs the filtration stage, separating the liquid wort from the spent grains. The kettle is dedicated to boiling the wort, while the whirlpool is responsible for the clarification and separation of solids.
Advantages
- Precise Temperature Control: The addition of a dedicated Hot Liquor Tank (HLT) allows for precise temperature control throughout the brewing process, ensuring optimal conditions at every stage.
- Continuous Brewing Capability: The independent vessel enables continuous brewing, allowing for a seamless transition from one stage to another without downtime.
- Improved Efficiency And Process Control: The unique vessel allows for meticulous control of every brewing stage, reducing the risk of off-flavors and ensuring consistent quality.
- Reduces The Risk of Cross-Contamination: Similar to a 3-vessel setup, separating each stage into a dedicated vessel minimizes the risk of unwanted flavor carryover between processes.
Disadvantages
- Larger Footprint: A 4-vessel brewhouse requires more space than a 2-vessel and 3-vessel setup, which can present challenges for small breweries or breweries with limited space.
- Increased Investment: Adding a hydrothermal tank and another vessel increases the initial investment, making it a more significant financial commitment.
- Operational Complexity: Managing 4 separate vessels brings operational complexity and may require more advanced control systems and skilled personnel.
Considerations
- Space Planning: Evaluate whether the brewery has enough physical space to accommodate the larger footprint of a 4 vessel brewhouse.
- Budget Considerations: Assess the brewery’s financial ability to invest in additional vessels and related equipment.
- Operational Expertise: Consider the skill level of brewery personnel, as operating a 4-vessel system may require a higher degree of technical expertise.
- Production Scale And Goals: Determine if continuous brewing capabilities and enhanced control are appropriate for the brewery’s production scale and beer style.
- Brewing Precision: Consider whether the increased precision in the brewing process meets the quality standards required by the brewery.
The 4-vessel brewhouse configuration provides unparalleled control, continuous brewing capabilities, and unparalleled control over every brewing stage. However, breweries must carefully evaluate space, budget, and operational considerations to determine whether this configuration meets their specific needs and goals.
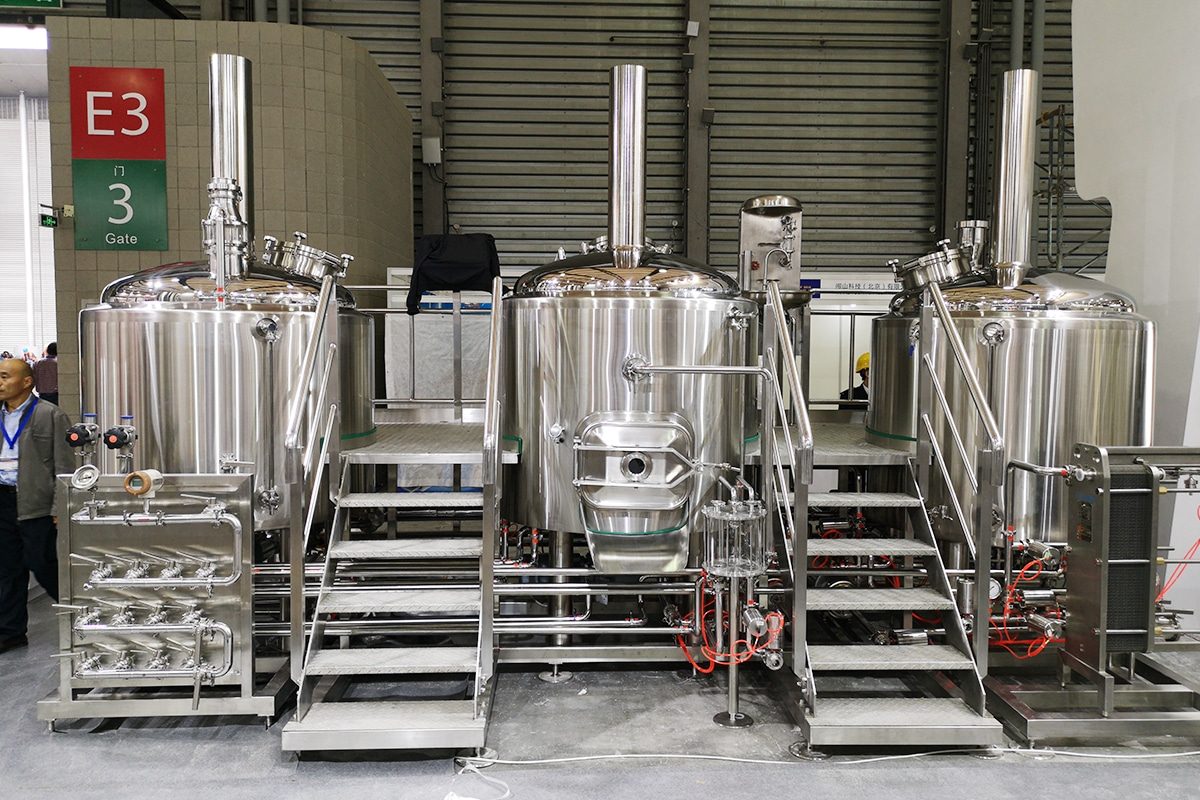
2-Vessel VS 3-Vessel VS 4-Vessel Brewhouse Comparative Analysis
As the craft beer industry continues to evolve, the choice between 2-vessel, 3-vessel, and 4-vessel brewhouse configurations remains a critical decision for breweries looking for the perfect balance of efficiency, flexibility, and control.
Space Efficiency And Floor Space
2 Vessel Brewhouse Advantages
- The compact design is ideal for small breweries or limited space.
- Cost-effective both in terms of initial investment and operating space.
2 Vessel Brewhouse Considerations
- Limited synchronization processes may require strategic spatial planning.
3 Vessel Brewhouse Advantages
- Enhance process control with dedicated vessels for mashing, boiling, and whirlpooling.
- Versatility to handle multiple brewing stages simultaneously.
3 Vessel Brewhouse Considerations
- The footprint is larger compared to a 2 vessel setup, which can be challenging for smaller spaces.
4 Vessel Brewhouse Advantages
- Precise temperature control is achieved through a dedicated hot liquid tank.
- Continuous brewing function for optimal efficiency.
4 Vessel Brewhouse Considerations
- Largest floor area, suitable for large breweries with ample space.
Initial Investment And Operating Costs
2 Vessel Brewhouse Advantages
- Lower initial investment and maintenance costs.
- Simplifying operations reduces labor and training costs.
2 Vessel Brewhouse Considerations
- Limited synchronization processes can impact production capabilities.
3 Vessel Brewhouse Advantages
- Balance enhanced control with a modest initial investment.
- Versatility may help increase production capacity.
3 Vessel Brewhouse Considerations
- The initial investment is higher compared to a 2 vessel setup.
4 Vessel Brewhouse Advantages
- The precise and consistent brewing capabilities justify the higher initial investment.
- Over time, productivity is likely to increase.
4 Vessel Brewhouse Considerations
- The initial investment is the highest among the three brewhouse configurations.
Process Control And Flexibility
2 Vessel Brewhouse Advantages
- Streamlined processes lend themselves to simple recipes.
- Ideal for breweries focused on sustained, limited-scale production.
2 Vessel Brewhouse Considerations
- The synchronization process has limited flexibility and may limit recipe experimentation.
3 Vessel Brewhouse Advantages
- Increased control over each stage allows for experimentation with different formulations.
- Versatility supports the production of a variety of beer styles.
3 Vessel Brewhouse Considerations
- Complex processes may require skilled personnel to manage optimally.
4 Vessel Brewhouse Advantages
- Unparalleled precision and control at every brewing stage.
- The continuous brewing function provides maximum flexibility.
4 Vessel Brewhouse Considerations
- Operational complexity may require advanced control systems and skilled personnel.
Production Scale And Workflow
2 Vessel Brewhouse Advantages
- Suitable for small and medium-sized production.
- The streamlined workflow may appeal to entry-level brewers.
2 Vessel Brewhouse Considerations
- Limited scalability for larger production needs.
3 Vessel Brewhouse Advantages
- Balanced medium to large-scale production.
- Versatility supports different beer styles and production requirements.
3 Vessel Brewhouse Considerations
- Potential scale limitations for high-volume production.
4 Vessel Brewhouse Advantages
- Suitable for large-scale production with continuous brewing capability.
- Precision ensures consistent quality across different beer styles.
4 Vessel Brewhouse Considerations
- Might be overkill for smaller breweries with limited production needs.
In the dynamic brewing process, choosing a 2-vessel, 3-vessel, or 4-vessel brewhouse is a critical decision that determines the essence of every pint. Each brewhouse configuration offers a unique set of benefits and considerations, allowing brewers to tailor their options based on their production goals, space constraints, and budget considerations.
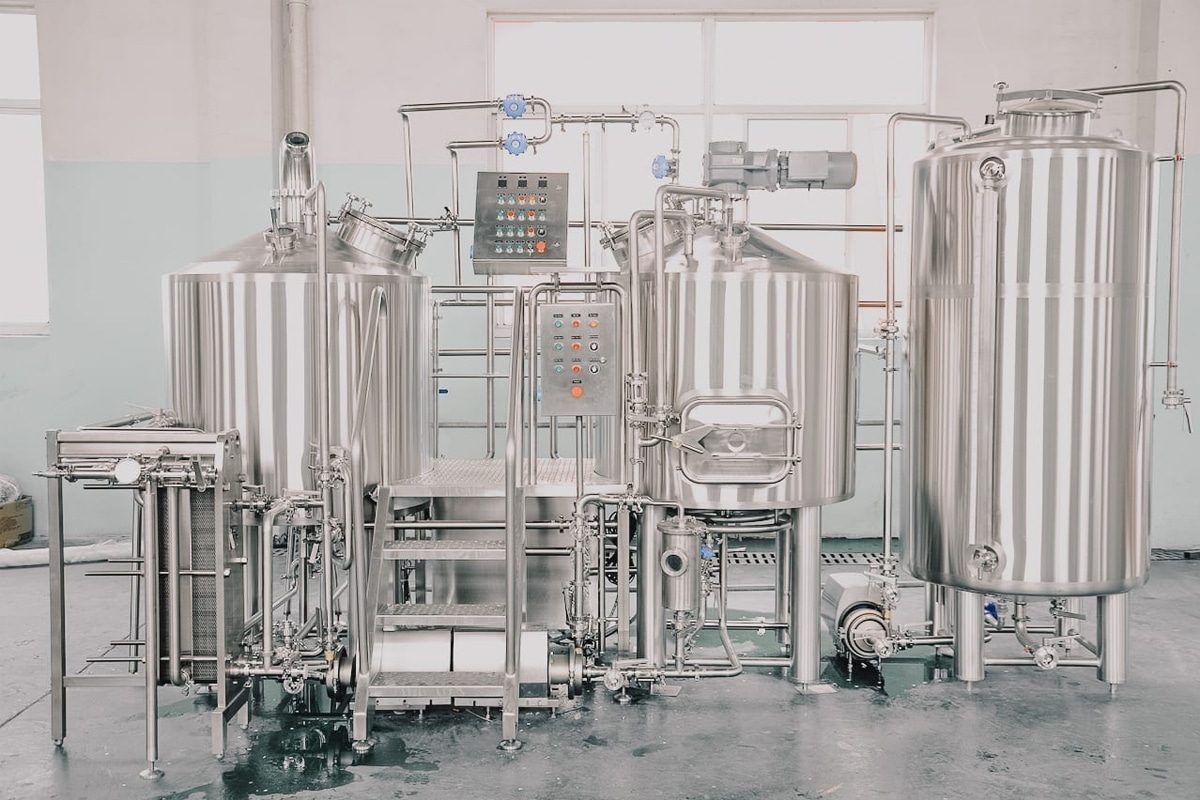
Factors Affecting Brewhouse Configuration Selection
Choosing the best brewhouse configuration is a critical decision for a brewery, influenced by a variety of factors from production size to personal preference. The following factors play an important role in guiding the choice of a 2, 3, or 4-vessel brewhouse configuration:
Production Scale
- Small Breweries: Due to space efficiency and cost-effectiveness, a 2-vessel configuration may be preferable for smaller production sizes.
- Medium To Large Breweries: 3 or 4-vessel setups provide enhanced control and versatility, meet higher production needs, and allow for simultaneous brewing processes.
Budget Constraints
- Initial Investment: 2-vessel brewhouses typically require a lower initial investment compared to 3- or 4-vessel configurations, making them more accessible to breweries on a budget.
- Long-Term Cost: While the initial cost of a 3- or 4-vessel setup may be higher, its increased efficiency and accuracy may reduce long-term operating costs and improve product consistency.
Winemaker Preference
- Personal Brewing Style: The brewer’s preferences and brewing philosophy greatly influence choices. Some may prefer the simplicity and cost-effectiveness of a 2-vessel setup, while others prioritize the precision and control of a 3 or 4-vessel configuration.
Brewing Goals And Styles
- Variety of Beer Styles: The choice of brewhouse configuration is inherently related to the variety of beer styles the brewery aims to produce. The 3 or 4-vessel setup provides greater flexibility to experiment with different brewing recipes simultaneously to meet a wider range of consumer preferences.
Brewery Space And Floor Space
- Floor Space Considerations: Physical space within the brewery is a key factor. Smaller breweries or those with limited space may find a 2 vessel brewhouse more suitable, while larger businesses can allocate the necessary space for a 3 or 4-vessel configuration.
Skill Improved
- Automation And Technology Integration: The level of technology integration required by a brewery is a key consideration. More advanced control systems are typically associated with 3 or 4-vessel setups, providing advantages such as precise temperature control and automated processes.
Sustainable Development Initiatives
- Energy efficiency and sustainability: Sustainability-focused breweries may consider the environmental impact of their breweries. Advanced configurations often have features designed to increase energy efficiency, consistent with a commitment to environmentally friendly practices.
Process Control And Flexibility
- Process Control: Breweries looking for precise control over each brewing stage may prefer a 3 or 4-vessel setup because they have dedicated vessels that allow for fine-tuning and consistency.
- Flexibility: Breweries seeking versatility and the ability to experiment with various recipes simultaneously may find advantages in a 3-vessel configuration that balances control with flexibility.
Operational Expertise
- Required Skill Level: Compared to 2 or 3 vessel configurations, 4 vessel setups typically require a higher level of technical expertise to manage the additional complexity. Breweries should consider their existing expertise when making their selection.
Future Expansion Plans
- Scalability: Consider future growth. Breweries planning an expansion can avoid frequent equipment upgrades by choosing a brewhouse configuration that can scale seamlessly as production needs increase.
The decision-making process for brewhouse configuration is multifaceted and requires careful consideration of production goals, budget constraints, personal preferences, and the brewery’s long-term vision. By weighing these factors, brewers can tailor brewhouse options to their unique needs, ultimately laying the foundation for successful, efficient beer production.
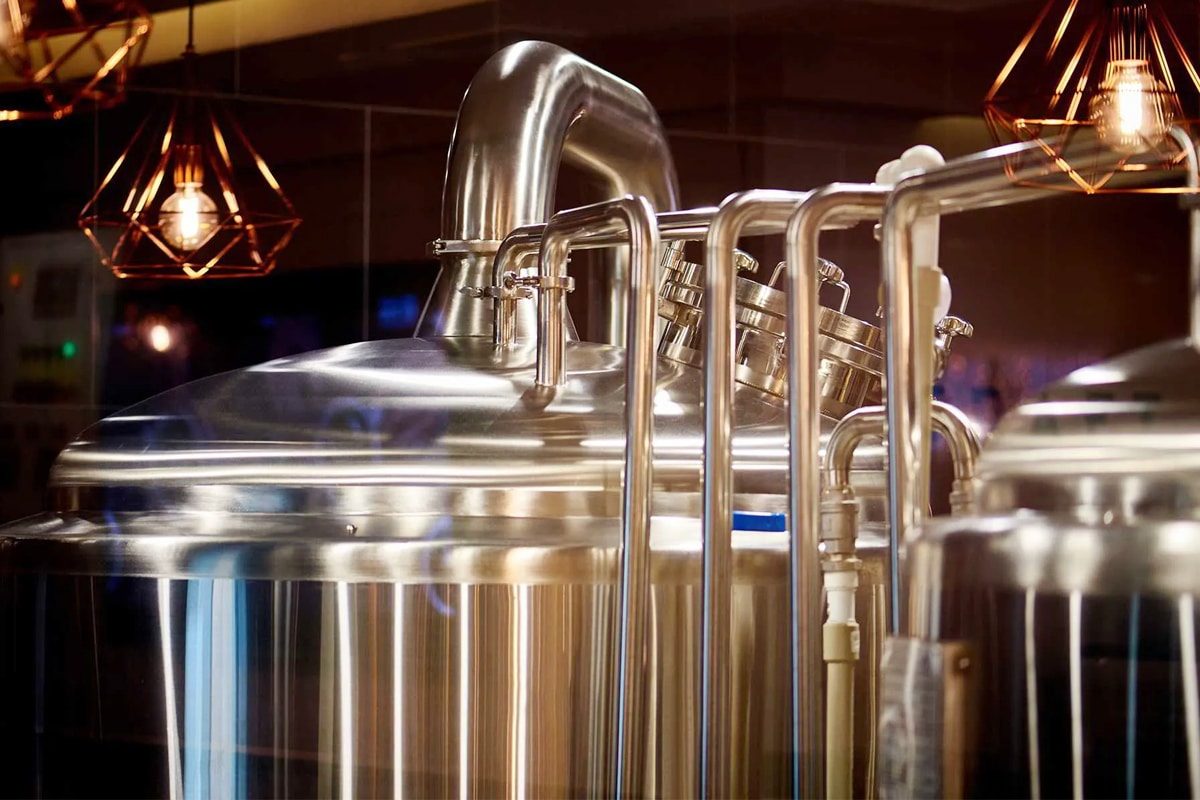
Summary
In the diverse landscape of brewing, the choice between 2, 3, or 4-vessel brewhouse configurations stands as a pivotal decision that shapes not just the brewing process, but the very essence of crafted libations. The 2-vessel setup, with its simplicity and cost-efficiency, appeals to smaller breweries seeking streamlined operations and economical solutions. In contrast, the 3-vessel configuration offers enhanced control, versatility, and reduced cross-contamination risks, making it an ideal choice for those balancing precision with flexibility. Meanwhile, the 4-vessel brewhouse, with its precision-driven control and continuous brewing capabilities, caters to the most discerning brewmasters aiming for utmost mastery.
Factors such as production scale, budget, space constraints, and brewing philosophy dictate the optimal choice. Smaller spaces and limited budgets might find solace in 2 vessels, while larger-scale operations craving precise control lean towards 3 or 4 vessels. But, amidst these complexities, the choice echoes the soul of the brewery, influencing everything from flavor profiles to operational efficiency. Ultimately, selecting the ideal brewhouse configuration is a profound journey, intertwining craftsmanship, innovation, and the unique aspirations of each brewer.
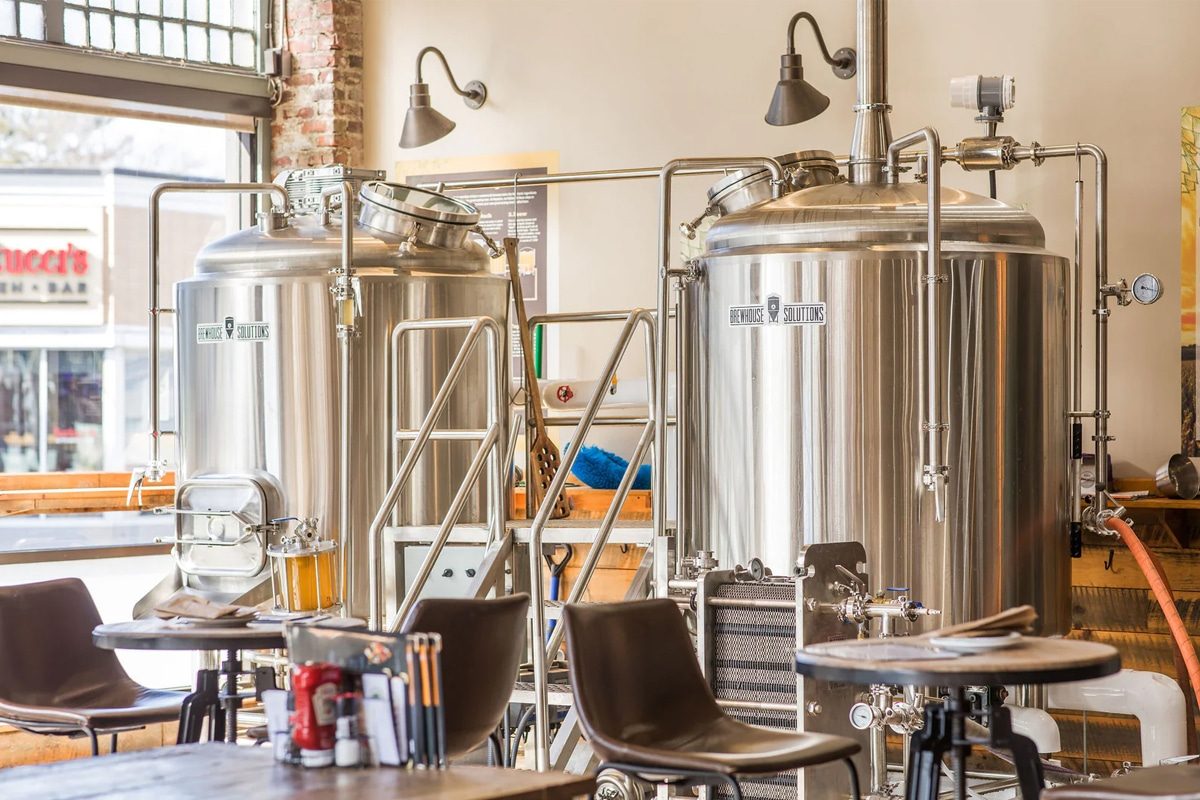
Personalized Brewhouse Turnkey Solution
At ZYB Craft, we recognize that the heart of brewing lies in the precision of your brewhouse setup. Whether you envision the simplicity of a 2-vessel system, the balanced control of a 3-vessel configuration, or the precision-driven mastery of a 4-vessel brewhouse, we understand that your brewing needs are as unique as the flavors you craft.
Our commitment extends beyond providing equipment, we offer personalized brewhouse turnkey solutions tailored to your specific requirements. ZYB Craft is not just a provider, we are your brewing partner, dedicated to empowering your vision. Our team of experts is ready to collaborate with you, guiding you through the intricacies of each configuration, and helping you make informed decisions that align with your production goals and brewing philosophy. Contact ZYB Craft today, and let’s embark on a journey to elevate your brewing experience.